Ámbito normativo y soluciones para el tratamiento de COV
El objetivo del presente artículo es explicar a los fabricantes de pintura y tintas, los problemas a los que se enfrentan a la hora de cumplir la normativa de emisiones en base al Real Decreto 117/2003 sobre limitación de emisiones de compuestos orgánicos volátiles debidas al uso de disolventes en determinadas actividades de producción de pinturas, tintas y recubrimientos.
Kalfrisa es una compañía con más de 50 años de experiencia en los sectores de la energía y el medio ambiente, y que cuenta con amplia experiencia implementando soluciones ambientales para los sectores siderúrgico, automoción, industria química y fabricación de pinturas, tintas y recubrimientos, especialmente en lo relacionado con el tratamiento y control de las emisiones de compuestos orgánicos volátiles.
Ecoimpress es una empresa con más de 20 años de experiencia en la implementación de soluciones tecnológicas a través de nuestros socios para la reducción de emisiones, la regeneración de disolventes y la implementación de equipos de apoyo a la producción de pinturas.
En este artículo se describen las soluciones técnicas y de ingeniería que pueden aportar Kalfrisa y Ecoimpress para solucionar todos los problemas derivados de la presencia de compuestos orgánicos volátiles en los procesos de fabricación de pinturas y tintas. Estas soluciones no solo se limitan al diseño y fabricación de un equipo de tratamiento y eliminación de estos compuestos, sino también en la definición, medición y caracterización de las emisiones para determinar la Mejor Técnica Disponible (MTD o BAT por sus siglas en inglés) para el cumplimiento de la normativa.
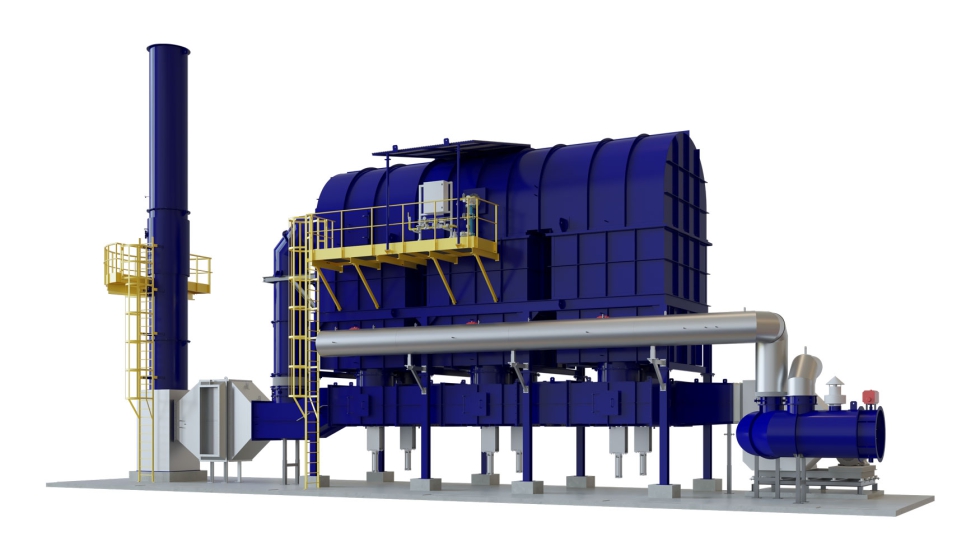
¿Qué son los COV y dónde están presentes en los procesos de fabricación de pinturas?
Los compuestos orgánicos volátiles (COV) son todos compuestos orgánicos formados principalmente por carbono y también otros elementos como hidrógeno, oxígeno, halógenos, azufre, fósforo, silicio o nitrógeno, y que tienen una presión de vapor > 0,01 kPa a una temperatura de 293,15 K. Dicho de una forma más sencilla, son todos aquellos hidrocarburos que se encuentran en estado gaseoso a temperatura ambiente o que son muy volátiles a dicha temperatura. Esto agrupa una gran cantidad de compuestos entre los que se encuentran los disolventes más frecuentes en las formulaciones de pinturas y tintas.
En el proceso de producción de pinturas existen diferentes zonas con generación de COV, tales como dispersores, mezcladores, procesos de limpieza, molienda, etc.
Idealmente se debería diseñar una estrategia de minimización de emisión en todos aquellos puntos donde sea posible, como por ejemplo en los procesos de aporte de producto y limpiezas automatizadas, y una vez minimizadas todas las fuentes se deben caracterizar en un parámetro de emisión total, que incluye la suma de emisiones residuales y emisiones difusas (pérdidas al aire o venteos).
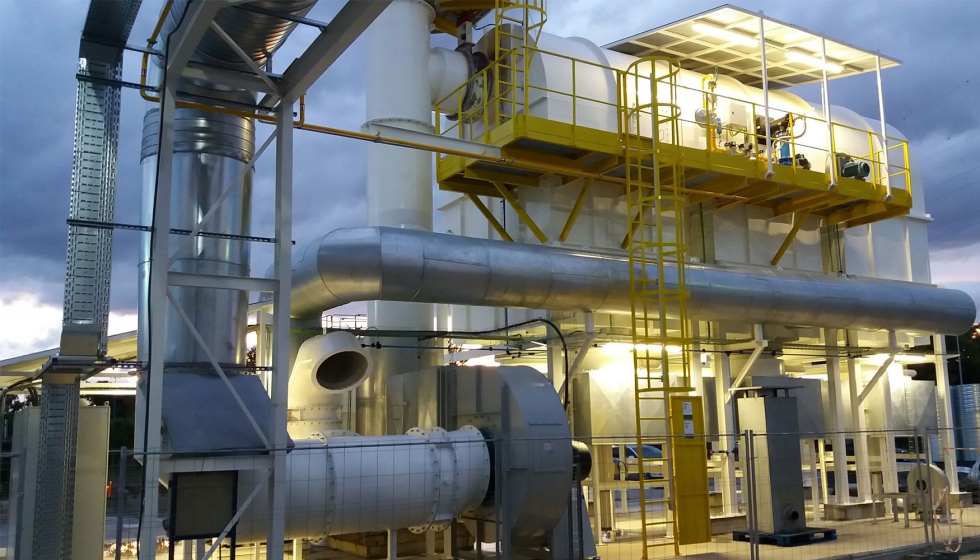
¿Qué normativa afecta a la actividad de mi industria? Interpretación del marco legal
Este RD dictamina que “El uso de disolventes en ciertas actividades da lugar a emisiones de compuestos orgánicos a la atmósfera que pueden ser nocivas para la salud y producir importantes perjuicios a los recursos naturales. Consciente de lo anterior, el Consejo de Ministros de la Unión Europea aprobó, el 11 de marzo de 1999, la Directiva 1999/13/CE, que tiene por objeto prevenir o reducir los efectos nocivos que para las personas y el medio ambiente pueden derivarse de algunas actividades que utilizan en sus procedimientos de fabricación o de trabajo disolventes orgánicos en cantidades importantes.
Esta directiva impone a los titulares de instalaciones en las que se realicen dichas actividades determinadas obligaciones, entre ellas, la de no superar los distintos valores límite de emisión que se especifican o la de reducir sus emisiones por otros medios. Asimismo, de conformidad con la citada norma, las autoridades competentes deberán comprobar el cumplimiento de las obligaciones impuestas, quedando obligados los titulares de las instalaciones a facilitar a aquéllas los datos e informaciones necesarios para el desarrollo de su labor”.
Este RD aplicado al sector 17 identificado como 'Fabricación de recubrimientos, barnices, tintas y adhesivos', identifica que empresas con consumos de disolvente superiores a 100 toneladas/año, tendrán un límite máximo de emisión de COV en concentración en gases residuales de 150 mgC/Nm3 y un valor de emisión difusa de entre el 5% y el 3% del parámetro de entrada de disolvente.
¿Qué se entiende por emisión difusa? ¿Cuándo puede considerarse que una emisión es confinada (Residual)?
Emisión Difusa: principalmente se engloba en esta definición toda emisión, no contenida en gases residuales, de COV al aire, suelo o agua, así como los disolventes contenidos en cualquier producto. Incluye también las emisiones liberadas al exterior a través de elementos como ventanas o puertas, respiraderos de depósitos …
La emisión difusa no se produce en un foco determinado, como si sucede en la emisión en los gases residuales, y por tanto no se puede determinar con una medición directa con instrumentación.
Emisión Residual (FOCO): son los procedentes de una chimenea o foco, y su contenido en COVs puede determinarse con instrumentación de medición correctamente calibrada.
Para conocer el límite de emisión y cumplimiento de los focos de emisión residual se debe realizar un estudio de emisiones que incluya una medición de diferentes parámetros para cada foco, entre los que se consideran caudal de emisión, partículas en suspensión COT, CO, NOx.
La empresa deberá realizar un plan de gestión de disolventes, para demostrar al órgano competente que sus focos de emisión cumplen con los valores límite establecidos en el Real Decreto. En el caso de incumplimiento, la empresa deberá establecer un sistema de reducción de emisiones o bien implementar un equipo de tratamiento de los focos con emisión basándose en el documente “Decisión de Ejecución (UE) 2020/2009 de la Comisión de 22 de junio de 2020 por la que se establecen las conclusiones sobre las mejores técnicas disponibles (MTD), con arreglo a la Directiva 2010/75/UE del Parlamento Europeo y del Consejo, sobre las emisiones industriales “.
Pero, ¿cuáles son las mejores técnicas disponibles? (BAT)
Entre otras cabe destacar: Oxidación térmica, Carbón activo, Condensación criogénica, absorción físico-quimica y biofiltración.
Una vez caracterizada la corriente, desde el departamento de Ingeniería de Kalfrisa se realiza el estudio de la mejor técnica disponible, junto con la ingeniería necesaria para realizar la conexión del equipo de tratamiento a las fuentes del cliente, realizando así una completa integración de todas las necesidades del cliente dentro de un proyecto llaves-mano.
Dada la extensa experiencia de Kalfrisa en el sector, la BAT más extendida para dar la mejor solución es la Oxidación térmica regenerativa (RTO).
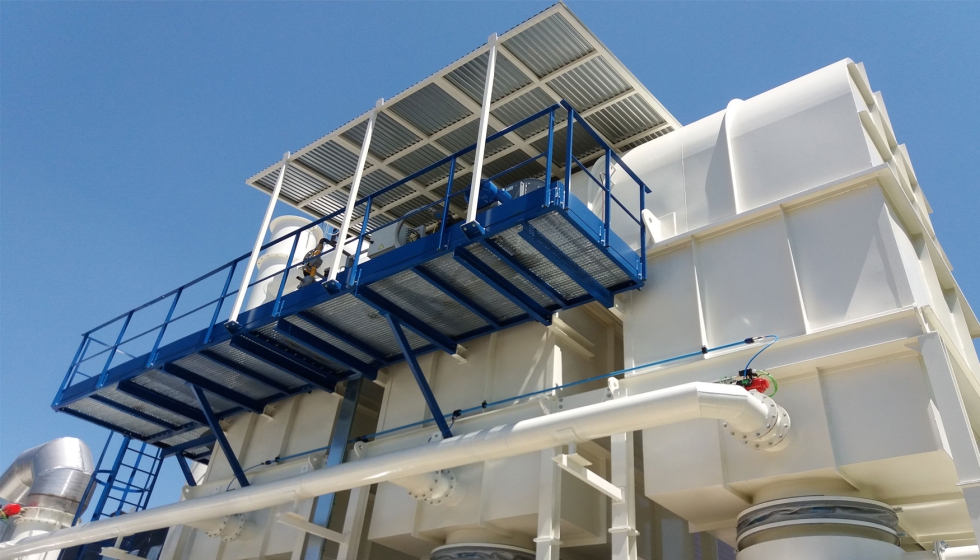
¿Por qué es la oxidación térmica regenerativa una de las BAT en el sector de la fabricación de recubrimientos, barnices, tintas y adhesivos?
Uno de los parámetros que determinan la viabilidad de una solución u otra es la relación Caudal/Concentración de COV, por los cuales, hacen que un sistema sea más rentable que otro.
Esta solución es óptima para bajos y altos caudales y/o concentraciones de COV. Es viable para el tratamiento para gases o líquidos. Esta técnica tiene una eficiencia de destrucción superior al 99% y eficiencia térmica del 95%
En resumen, la alta tasa de eliminación de COV así como las posibilidades de aprovechamiento energético posterior al proceso, junto con el bajo consumo y mínimas necesidades de mantenimiento, hacen de la oxidación térmica regenerativa la tecnología más adecuada para el sector.
El principio de este sistema (RTO) es la oxidación térmica, proceso mediante el que al calentar una mezcla de COV con aire y oxígeno por encima de su temperatura de autoignición y manteniéndola a alta temperatura durante el tiempo suficiente se produce de forma completa la reacción combustión-oxidación a dióxido de carbono y agua.
COV + O2 → CO2 + H2O + Calor
El equipo utilizado (RTO) se compone de tres (3) torres rectangulares verticales unidas por una cámara transversal de sección semi-cilíndrica colocada en la parte superior llamada cámara de oxidación. Cada torre contiene un lecho de elementos cerámicos que sirve de acumulador de calor. Este lecho cerámico se calienta o enfría dependiendo de la dirección del gas que lo atraviesa, durante un proceso de 3 ciclos.
La corriente contaminada pasa a través de este lecho para aumentar su temperatura y de esta manera entrar en la cámara de oxidación, donde se produce la reacción de oxidación destruyéndose así los COV. Los gases generados en la reacción pasan al siguiente lecho con el fin de calentar la corriente de gas contaminado que entrara a dicha cámara en el siguiente ciclo. Finalmente, una vez depurados, los gases son evacuados por chimenea.
En los procesos de oxidación térmica regenerativa, gran parte de la energía revierte de nuevo en el propio proceso, disminuyendo drásticamente el consumo de combustible frente a otros procesos de oxidación directa. Pero además, en la mayor parte de los proyectos del sector se puede realizar un aprovechamiento energético adicional que permite una eficiencia energética aún mayor. Existen varias posibilidades, tales como el calentamiento de agua o aceite térmico, la generación de vapor de agua a presión en calderas de recuperación, o bien el calentamiento de aire para su aprovechamiento en el propio proceso productivo o para el calentamiento de estancias.
Ingeniería y proyectos llaves en mano
Desde la división de Ingeniería y oficina técnica se analizan las características de cada proyecto, para ofrecer la solución tecnológica que más se ajuste a las necesidades de cada proyecto.
La gestión completa del proyecto se realiza en todas sus fases, desde la confección y diseño general de la instalación, hasta el montaje y puesta en marcha.
Los equipos de Kalfrisa están diseñados y fabricados cumpliendo con toda la normativa aplicable.
Servicio post venta con la mejor garantía
Además, Kalfrisa cuenta con un Servicio de Asistencia con gran experiencia y un completo equipo de profesionales cualificados para prestarle servicio así como la realización de un diagnóstico de averías y servicio de guardias telefónicas 365 días al año.
También dispone de coordinación de visitas programadas con los clientes para evaluar y garantizar el correcto funcionamiento de los equipos, además de la posibilidad de atención prioritaria para resolución de averías.
Todos nuestros equipos incorporan sistemas de conexión remota que nos permiten supervisar el funcionamiento de estos en tiempo real, previendo y reparando las averías de manera inmediata.
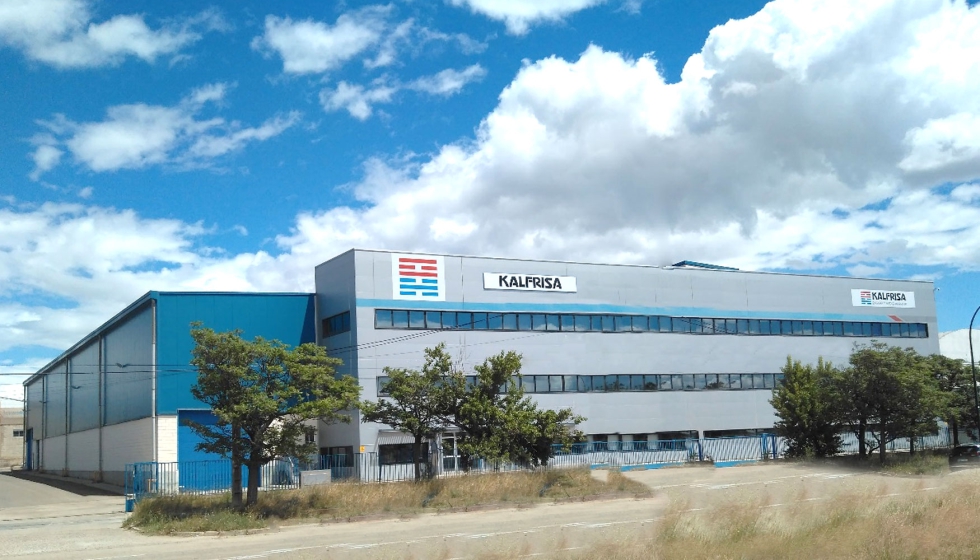
Kalfrisa 360
El conocimiento y experiencia adquirido durante más de 50 años en el sector de la energía y medio ambiente, nos permite ofrecer soluciones fiables y rentables a nuestros clientes
Kalfrisa es una compañía con facturación superior a 20M de € y dispone de un equipo de mas de 100 personas, que componen toda la estructura empresarial necesaria para integrar el proyecto con la máxima garantía y calidad.