Una minicentral como alternativa 'limpia' de abastecimiento energético
15 de octubre de 2009
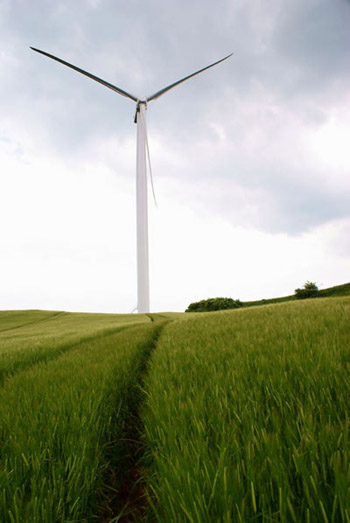
En un primer vistazo, el agotamiento de recursos en un plazo no compatible con la vida terrestre se presenta como una cuestión irresoluble. Por otra parte, las alternativas a contaminación del medio ambiente debido al quemado de combustibles carecen, por razones económicas y técnicas, de posibilidades de aplicación en la mayoría de los casos. Como es conocido, una solución a estas dificultades reside en el uso de fuentes renovables y limpias como la energía solar o la eólica. Fuentes sometidas a las condiciones de intermitencia propias de los fenómenos naturales. En consecuencia, para que la aplicación de las mismas sea universal se precisa disponer de un buen sistema de almacenamiento de los excedentes de energía. De esta manera, se puede desacoplar la producción del consumo con lo que se resuelve, por un lado, la dificultad que entraña la intermitencia en la producción de energía, y por el otro, el acoplamiento de estas fuentes a la red. Desde el departamento de física de la Universidad de Burgos se desarrolló un proyecto cofinanciado por la Comisión Europea en el programa 'Life Medioambiente 2004'. A través de esta experiencia piloto se pretendía mostrar la viabilidad de la refrigeración solar como la generación, almacenamiento y consumo en pila de combustible del hidrógeno producido mediante energías eólica y fotovoltaica.
Una minicentral de 70 kWp (kilovatios de pico) abastecía un edificio de 2.200 m2
La planta se ubicó en las inmediaciones del aeropuerto de Villafría (Burgos) en un terreno boscoso propiedad del ayuntamiento de la capital y sometido a diversos tipos de protecciones y servidumbres. En concreto, la servidumbre aérea limita la altura a la que se pueden elevar los aerogeneradores, mientras que la protección de la fauna del bosque obliga a situar dichos aerogeneradores en el exterior del perímetro del arbolado. Ambas limitaciones condicionan el desarrollo del proyecto, sin embargo ya que éste tiene un fin demostrativo, la ubicación de la planta junto al edificio de utilización proporciona una evidente ventaja en cuanto a su utilidad. En general, el emplazamiento disponible goza de buenas condiciones de insolación y de viento. Respecto a la insolación, el número medio anual de horas de sol en Burgos es de 2.183, se indican los valores medios de la irradiancia anual sobre superficie horizontal medidos en una estación situada en las inmediaciones de la ubicación de la planta de hidrógeno.Y en cuanto al potencial eólico, tras extrapolar las mediciones realizadas en la estación meteorológica del Departamento de Física de la UBU en Villafría para el año 2003, se obtuvo una velocidad media anual de 4,29 m/s.
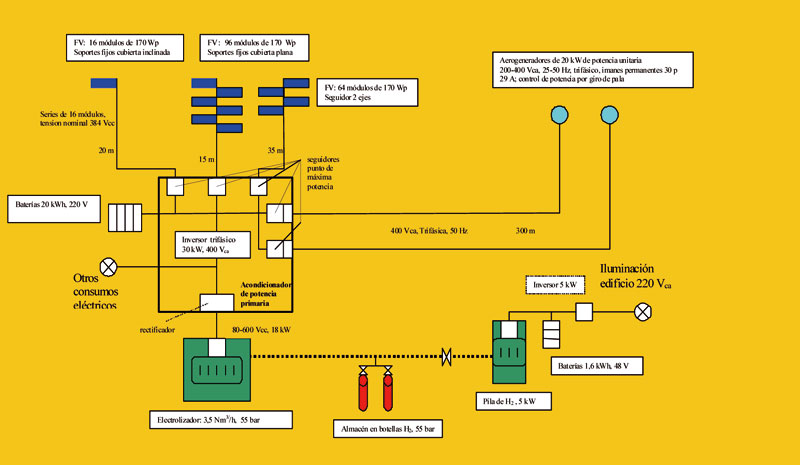
Objetivos de la instalación de hidrógeno
- Diseño y cálculo de una planta aislada para la generación de hidrógeno combustible mediante energías renovables limpias.
- Alimentación, de forma conjunta, del sistema mediante generadores eólicos y fotovoltaicos.
- Acoplamiento de ambas fuentes al electrolizador mediante un subsistema de acondicionamiento de potencia.
- Acoplamiento del generador de hidrógeno a una pila de combustible mediante un sistema de almacenamiento.
- Estimación del rendimiento de la planta.
- Diseño del sistema de regulación y control de la planta.
- Optimización del funcionamiento global del sistema.
Aerogeneradores optimizados para trabajar a bajas velocidades de viento
Con el propósito de aprovechar los recursos eólicos de la zona, fue necesario utilizar aerogeneradores optimizados para trabajar a bajas velocidades de viento. Se efectuó un estudio de mercado de aerogeneradores en el rango de potencia menor de 100kW (kilovatios) y se comprobó la escasez de oferta de equipos existentes, y que muy pocos cumplían con la normativa CEI IEC 61400. Se debía tener en cuenta que en la zona de implantación debido a la proximidad del aeropuerto, la servidumbre aeronáutica limitaba la máxima altura alcanzable de la torre. Todos los condicionantes mencionados, unidos a la existencia de edificios próximos, llevaron a la elección del aerogenerador de 20kWe, modelo Jimp20 Plus de la marca Jonica Impianti. En consecuencia, el aerogenerador se instaló sobre una torre metálica de 18 metros de altura. El modelo seleccionado llevaba incorporado un generador síncrono de imanes permanentes y acoplamiento directo entre el rotor y el generador eléctrico. Esta unidad, provista de regulación de potencia por giro de pala, se orientaba por una veleta de cola. Cuando alcanzaba las 150 rpm se regulaba por cambio de paso y pérdida aerodinámica. En conjunto, se instalaron dos unidades lo que supuso una potencia total eólica instalada de 40kWe.
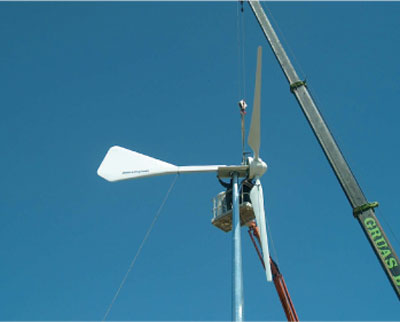
El sistema fotovoltaico disponía de módulos de silicio monocristalino colocados sobre un seguidor solar de doble eje, una cubierta y una marquesina. Se trataba de módulos del modelo A-170 W de la marca Atersa. La potencia total del sistema fotovoltaico fue de 30kWp. El seguimiento del sol se realizaba mediante un autómata que regulaba los movimientos de la estructura durante todas las estaciones en función de la hora solar, según la latitud del lugar en el que se instalaba el seguidor. Además contaba con un dispositivo de posicionamiento en bandera, para situaciones de emergencia por la acción de vientos moderadamente fuertes y huracanados.
La instalación también precisaba un electrolizador capaz de trabajar con fuentes de potencia variable. En el acople entre un sistema generador renovable intermitente y un electrolizador, se impide el buen funcionamiento del electrolizador en periodos de bajos niveles de potencia. En ese caso, también se incrementa el nivel de impurezas y se provoca la desconexión del mismo. Si se sobredimensiona el sistema generador respecto del equipo de electrólisis, aumentan la potencia media generada y el tiempo operativo de uso del electrolizador, con la consiguiente economía del sistema ya que se reduce el coste inicial del electrolizador. Para el proyecto de la Universidad de Burgos, se eligió un electrolizador de tipo alcalino por razones de coste y vida útil esperada. Se escogió un electrolizador alcalino bipolar de 3,5 Nm3/h (metros cúbicos normales por hora) de producción de hidrógeno entre 20-55 bar de presión de la marca Accagen. El rango posible de funcionamiento del electrolizador figuraba entre el 15-100% de su carga nominal. El electrolizador cumplía con la normativa europea para aplicaciones en atmósferas potencialmente explosivas (Atex), así como otras normativas relacionadas con equipos a presión y material eléctrico para emplazamientos peligrosos. En general, no existen muchos fabricantes de electrolizadores que garanticen la compatibilidad con fuentes renovables.
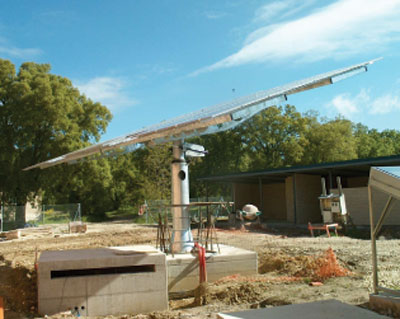
Pila de combustible, idónea para producir electricidad con fuentes renovables
La utilización de pilas de combustible para la generación eléctrica con fuentes renovables comporta beneficios en términos de nulas emisiones, menores ruidos y vibraciones. Las pilas de polímero sólido (Pem) son las más aptas para la aplicación con fuentes de este tipo, en caso de que se usen en re-electrificación. Es decir, cuando cesa la fuente renovable, debido a su naturaleza variable, tienen buen comportamiento ante las fluctuaciones que se producen y se ajustan desde el estado de 'parada en espera'. En esa situación, la respuesta es rápida para así satisfacer la demanda de carga que se requiere en ese momento. En este proyecto, la pila funcionaba en modo isla alimentando una carga de iluminación y el consumo de equipos auxiliares de la planta. Se empleó una pila tipo Pem, modelo Gencore 5 de la marca Plug Power. Dicha pila, podía generar 5 kW de potencia eléctrica nominal y gastar 4,5 Nm3/h de hidrógeno. La presión del hidrógeno almacenado en los bloques de botellas disminuía hasta la admisible en la pila de combustible, que operaba a 6 bar, tomando el combustible que necesitaba en cada momento, según la carga. Cuando se requieren pequeñas cantidades o su uso es variable, el hidrógeno se almacena como gas comprimido. El hidrógeno que no se gasta de forma inmediata, se confina en botellones comerciales de 50 l. Finalmente, el control de la pila inspeccionaba periódicamente la tensión de salida de la misma: si bajaba de un umbral de 49V la ponía en funcionamiento, por lo que podía trabajar del 0 al 100% de su potencia.
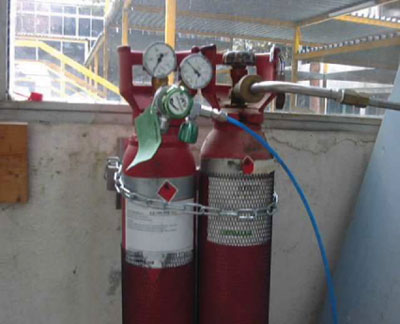
Una planta automatizada de producción de hidrógeno
Ya que la potencia primaria generada variaba, según el régimen de viento y la radiación solar, se debía indicar al electrolizador el hidrógeno que debía producir en dependencia de la potencia renovable producida. Así, se podía equilibrar la generación con la carga. Este control se realizaba con una señal de corriente 4-20 mA que regulaba la capacidad de producción de manera lineal entre el 15-100% de la nominal. Las medidas de tensión e intensidad dentro del equipo inversor servían para la elección de la intensidad de corriente de dicha señal de control, en cada instante. Esta medida se efectuaba con una frecuencia ajustada por experimentación. Entre los principales objetivos a la hora de elaborar un sistema de automatización figuraban: regular y controlar el funcionamiento de la instalación, teniendo en cuenta la gestión de seguridad; realizar mediciones y almacenar en forma de gráficos y tablas los datos obtenidos para apoyar labores de investigación y operar como medio didáctico que demostrara el funcionamiento de la instalación a los visitantes del recinto, así como facilitar material docente a los alumnos de la Universidad de Burgos.
Durante el proceso, se usaba como autómata programable un cPF de National Instrument, encargado de realizar las mediciones y de emitir las señales analógicas y digitales para el control de contactores y dispositivos de la instalación. Los datos de las mediciones realizadas se transmitían a un ordenador central que los almacenaba en tablas y gráficos útiles para el trabajo de investigación y la labor docente. En ese caso, la unidad de comunicación del cPF tenía cuatro ranuras para colocar los módulos de entrada / salida. A fin de realizar las medidas, se usaban diversos actuadores. Por ejemplo, cuatro sensores de efecto Hall para medir la intensidad de la corriente eléctrica, que se ubicaban a la salida de los generadores fotovoltaicos, a la entrada del inversor y a la entrada del electrolizador; un sensor de efecto Hall para medir la tensión de la corriente eléctrica a la entrada del equipo; tres sensores de temperatura, un anemómetro que establecía si la intensidad del viento era la adecuada para iniciar el funcionamiento del aerogenerador; dos sensores de insolación sobre los generadores fotovoltaicos respectivos y cuatro contactores que determinaban el suministro de potencia al electrolizador por parte de las fuentes de corriente. Y una salida analógica en el rango 0 – 20 / 4 – 20 mA que determinaba la intensidad de corriente con la que funcionaba el electrolizador, es decir, la producción de hidrógeno.
A finales de 2008, la producción eléctrica estimada a obtener por los generadores fotovoltaicos era de 42 MWhe (kilovatios por hora) y la de los generadores eólicos de 45 MWhe. La producción de hidrógeno electrolítico estimada rondaba los 1.000 kg anuales que traducida en producción de la pila suponía la generación de 10 MWhe anuales.