(parte 2) - Pasos a seguir, conclusiones, agradecimientos y bibliografía
INYECCIÓN
Paso I. Estética de la pieza
- tomando en cuenta la dificultad en la construcción del molde, la mejor opción siempre será inyectar la pieza desde la parte fija del molde,
- en caso de afectar la estética de la parte, se debe considerar colocar los puntos de inyección en alguna parte lateral donde las marcas no sean significativas y
- como ultima opción se debe considerar inyectar desde la parte móvil del molde.
Paso 2. Simetría en el punto de Inyección (empaquetamiento)
El software considera la resistencia geométrica de la pieza para evitar el empaquetamiento. Si una de las zonas se llena antes que la otra habrá empaquetamiento de tal forma que puede generar rebaba por ese lado del molde. Por lo tanto, la primera elección del punto de inyección debe hacerse considerando la simetría de la pieza. Si la pieza es simétrica con respecto a las direcciones XY, la mejor ubicación del punto de inyección será en el punto de simetría o centro de la pieza. La excepción a la regla es cuando la pieza tiene un agujero o una ranura en ese punto. Si este fuera el caso, deben considerarse las siguientes opciones, que serán solución sólo hasta alcanzar la igualdad en al menos el 95% del tiempo de llenado en las partes más alejadas:
- agregar otro punto de inyección y
- cambiar la geometría de la parte.
Paso 3. Presión en la cavidad
- mover el punto de lugar acercándolo hacia el centro de la pieza,
- incrementar el número de puntos de inyección (dos puntos de inyección se considera un número típico para solucionar este problema).
Paso 4. Comparación de regiones comunes
a11 a12 a13 a14
a21 a22 a23 a24
a31 a32 a33 a34
b11 b12 b13 b14
b21 b22 b23 b24
b31 b32 b33 b34
El impacto de las líneas de soldadura en las regiones con niveles de esfuerzo relativamente altos, se establece a través del siguiente índice (tomando la sumatoria total de cada una de las vistas).
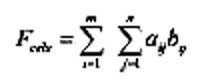
donde:
- aij = índice normalizado de concentración de esfuerzos en las plantillas (entre 0 al 1),
- bij = número de líneas de soldaduras identificadas dentro de cada región,
- m = renglones necesarios (comunes para cada plantilla en los análisis de esfuerzos y líneas de soldadura) y
- n = columnas necesarias (comunes para cada plantilla en los análisis de esfuerzos y líneas de soldadura)
Paso 5. Tiempo de ciclo
Conclusiones
- las condiciones de funcionalidad a las que se somete la pieza y
- las condiciones de proceso relativas a la manufacturabilidad. En este aspecto, se muestra la importancia de realizar un análisis de esfuerzos considerando las condiciones de carga bajo las cuales estará funcionando la pieza, de tal forma que permita identificar qué áreas son críticas debido a la concentración de esfuerzos.
Dichas áreas críticas se tomaron en cuenta en simulaciones de flujo para detectar cuál fue el mejor punto o puntos de inyección de la pieza, incluyendo la combinación de parámetros de proceso.Los avances tecnológicos y sistemas de CAE nos permiten llevar a cabo y poner en práctica este tipo de métodos con el fin de ahorrar tiempo de diseño, tiempo de proceso y tiempo de pruebas, con lo que el proceso de diseño global se convierte en un proceso más eficiente y económico. El impacto de este trabajo es evidente en el diseño de piezas de inyección de termoplástico, en la definición de aspectos geométricos, la localización y definición del punto o puntos de inyección y en la obtención de los parámetros adecuados de proceso.Con base en la revisión bibliográfica, se encontró que existen trabajos que consideran las condiciones de proceso [7] [6], pero sin tomar en cuenta las zonas críticas de esfuerzo dentro de la pieza. También hay estudios realizados sobre como afectan mecánicamente la existencia de líneas de soldadura a las partes inyectadas [14] [15]. Sin embargo, este trabajo se distingue por en considerar la integración de ambos fenómenos función vs. proceso, y de llegar a cuantificar la mejor opción o las mejores opciones de proceso con respecto a la funcionalidad de la pieza.
Se recomiendan las siguientes propuestas para mejorar y aplicar el presente trabajo:
- Implementación de la metodología en un software de simulación de proceso. La continuación de este trabajo estaría dirigida a la integración de la metodología dentro de un módulo en el software de simulación de flujo, de forma que permita importar el análisis de esfuerzos de la pieza y que también utilice regiones para calcular automáticamente lo que se realizó en este trabajo en hojas en de cálculo utilizando plantillas. De esta forma el software de simulación de proceso sería mucho más robusto ya que consideraría la funcionalidad de las piezas.
- Consideración de cavidades múltiples. En el presente trabajo se consideró que el molde tenía una sola cavidad. Los moldes de piezas medianas y pequeñas normalmente tienen más de una cavidad. La metodología propuesta puede ser extendida a la consideración de cavidades múltiples para balancear el flujo en cada una de las cavidades.
- Evaluar la orientación de las líneas de soldadura tomando en cuenta la dirección de los esfuerzos principales. En la metodología planteada en este trabajo se normaliza el esfuerzo al que está sometido la pieza y se cuantifica el número de líneas de soldadura en cada elemento de la malla. Una opción de trabajo a futuro contemplaría tomar en cuenta la orientación de las líneas de soldadura con respecto a la dirección de los esfuerzos principales para evaluar si la línea de soldadura está orientada de tal forma que provoca la falla por fractura en la pieza.
- Automatizar el proceso de ubicar de las líneas de soldadura digitalizando la imagen. Se propone digitalizar la imagen para poder convertir el proceso de la localización de las líneas de soldadura en un proceso automático. La ubicación exacta de las líneas de soldadura, así como el ahorro del tiempo necesario para su ubicación serían los principales beneficios de automatizar el proceso.
Agradecimientos
Referencias
- Jesús Talavera, Metodología para la Evaluación Integral de Manufacturabilidad y Desempeño Funcional en Partes Inyectadas de Termoplástico, Tesis, Maestría en Sistemas de Manufactura, Instituto Tecnológico y de Estudios Superiores de Monterrey – Campus Monterrey, Mayo, 2002.
- M. Koc, T. Allen, S. Jiratheranat, T. Altan. "The use of FEA and design of experiments to establish design guidelines for simple hydroformed parts". International Journal of Machine Tools & Manufacture. Vol. 40 (2000), p. 2249-2266.
- D.C. Ko, D.H. Kim, B.M. Kim, J.C. Choi. "Methodology of preform design considering workability in metal forming by artificial neural network and Taguchi method". Journal of Materials Processing Technology. Vol. 80-81 (1998), p. 487-492.
- D.C. Ko, D.H. Kim, B.M. Kim. "Aplication of artificial neural network and Taguchi method to preform design in metal forming considering workability". International Journal of Machine Tools & Manufacture. Vol. 39 (1999), p. 771-785.
- J.N. Majerus, M.L. Mimnagh, J.A. Jannone, D.A. Tenney, S.P. Lamphear. "Blending hierarchical economic decision matrices (EDM) with FE and stochastic modeling II. Detailing EDM". Finite Elements in Analysis and Design. Vol. 30 (1998), p. 219-234.
- S. L. Mok and C. K. Kwong; "Review of Research in the Determination of Process Parameters for Plastic Injection Molding"; Advances in Polymer Technology. Vol. 18, No. 3, (1999), p. 289-291.
- B.H.M. Sadeghi, "A BP-neural network predictor model for plastic injection molding process"; Journal of Materials Processing Technology. (January 2000), p. 411-416.
- D. Su, M. Wakelam. "Intelligent hybrid system for integration in design and manufacture". Journal of Materials Processing Technology. Vol. 76 (1998), p. 23-28.
- B.N. Yetukuri, N.V. Yetukuri, G.W. Fischer. "SPAW: A design tool for planning a manufacturing process in a concurrent engineering environment". Computers in Industry. Vol. 32 (1996), p. 79-93.
- D.M. Bryce. "Plastic Injection Molding… Mold design and construction fundamentals. Vol. III: Fundamentals of Injection Molding Series". Society of Manufacturing Engineers. 1a Edición. Estados Unidos de América. (1994), p. 167-175.
- R. A. Malloy. "Plastic Part Design for Injection Molding". Hanser Publisers. 1a Edición. Alemania. (1994), p. 14-126.
- H. Rees. "Understanding Injection Mold Design". Hanser Publishers. 1a Edición. Alemania. (2001), p. 54-55.
- H. Rees. "Mold Engineering". Hanser Publishers. 1a Edición. Alemania. (1995), p. 27-28.
- R. Seldén, "Effect of Processing on Weld Line Strength in Five Thermoplastics"; Polymer Engineering and Science. Vol. 37, No. 1 (January 1997), p. 205-218.
- Val A. Kagan, "Optimized Mechanical Performance of Welding and Molded Butt Joints: Part II- Weld and Knit Lines Integrity". Honeywell International, Engineered Applications & Solutions. Morristown, New Jersey. Honeywell Plastics Technical Papers.