Contención en la ingeniería de procesos
En la actualidad se está produciendo un cambio de paradigma en la producción de sólidos en los sectores químico y farmacéutico. La tendencia hacia una mayor especialización y el uso de ingredientes activos más eficaces ha generado la necesidad de flujos de proceso herméticamente sellados. Las normativas gubernamentales también son cada vez más estrictas. Cada vez serán más los procesos de producción que deban diseñarse como sistemas de contención.
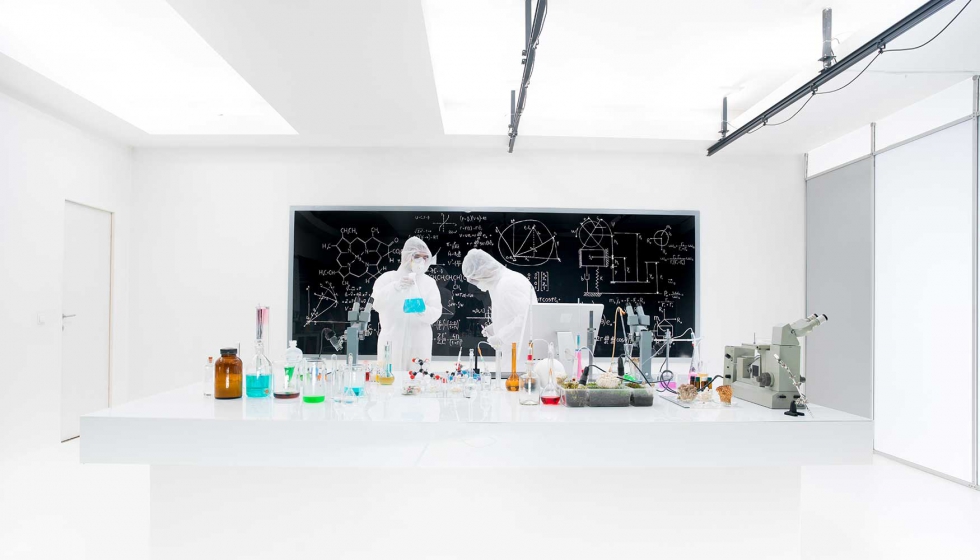
No hay comercialización sin registro. Este sucinto dictamen de Bruselas es un importante motivo de preocupación en muchas empresas del sector de los procesos. Todo viene a raíz de la directiva europea REACH, que exige el registro previo de todas las sustancias producidas o importadas en volúmenes de 1 t/a o superiores. La cantidad de información que una empresa debe presentar crece de forma proporcional a los volúmenes comercializados. Esto tiene repercusiones directas sobre el coste de las pruebas toxicológicas necesarias. Se estima que las pruebas cuestan 13.000 euros para volúmenes de hasta 1 t/a, pero que esta cifra puede elevarse por encima de los 900.000 euros en el caso de los volúmenes de 1000 toneladas métricas anuales o superiores. Y a pesar de que es caro, el registro no es precisamente una venta de bulas moderna. De hecho, solo constituye el primer paso.
Después, la ECHA o un organismo regulador nacional revisan la documentación presentada. La UE prefiere que se hallen sustitutivos de las sustancias peligrosas. Cuando esto no es posible, los operadores de la planta deben demostrar que pueden manipular las sustancias altamente activas de forma segura. Las estadísticas revelan que no son pocas las empresas a las que afectan estas políticas. Más del 50% de la totalidad de las NCE (nuevas entidades químicas) se consideran compuestos potentes (OEL < 10 µg/m3). La solución mágica para preservar la fluidez de los flujos de producción a pesar de estas circunstancias pasa por la contención.
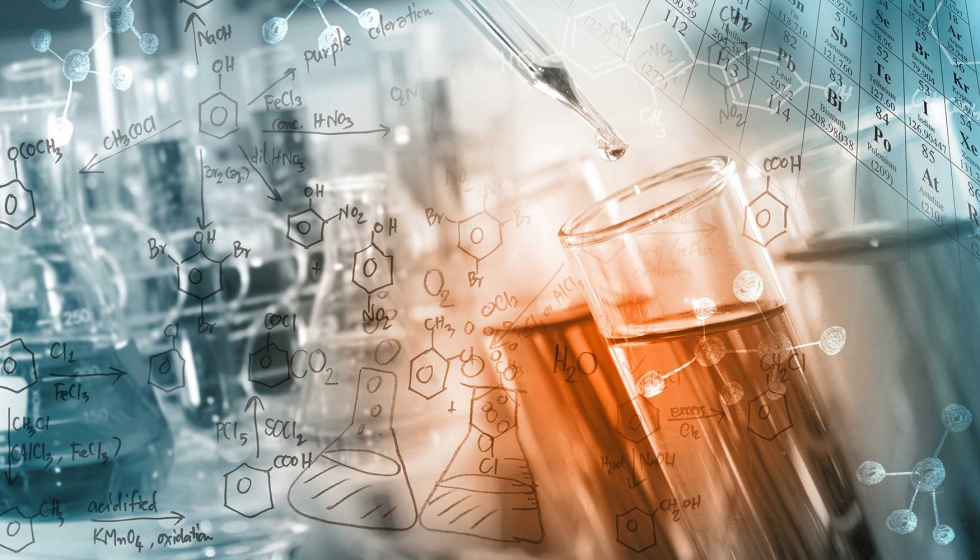
La necesidad de conocer íntegramente el proceso
“La contención implica proteger al operador del producto y también proteger al producto del operador”, señala Thomas Weingartner, CEO de Lugaia Deutschland, cuando explica el meollo de la cuestión. La contención (al menos en el sector farmacéutico) no es ninguna novedad. De hecho, se trata de una tendencia a largo plazo. No obstante, los conocimientos especializados en este campo no están repartidos de forma uniforme, señala Richard Denk, director de Ventas de Contención de Skan, empresa especializada en equipos de sala limpia, y fundador del Grupo de Expertos en Contención de ISPE, la International Society for Pharmaceutical Engineering. "En 2004 introdujimos la contención en el orden del día mediante la oferta de seminarios y cursos de formación en Alemania, Suiza y Austria. Han pasado 13 años desde entonces y aún tengo la sensación de que esto no es más que la punta del iceberg".
Sigue existiendo mucha incertidumbre. Uno de los motivos por los que las empresas poseen unos niveles de conocimientos técnicos en materia de contención tan dispares radica, sin duda, en el hecho de que el número de productos nuevos que se clasifican como extremadamente peligrosos está creciendo con mayor rapidez que el número de ingenieros y operadores de planta familiarizados con los problemas que conllevan. El déficit de conocimientos que se ha acumulado con los años se hace evidente en las conferencias y cursos de formación, que están registrando un gran número de inscripciones y matriculaciones. “El número de sustancias altamente activas no ha dejado de aumentar con los años y, en consecuencia, en la actualidad el nivel 5 OEB suele ser la norma". Las siglas OEB en inglés corresponden a 'Occupational Exposure Band' (banda de exposición ocupacional) y la asignación a una de estas bandas se basa en la potencia toxicológica de una sustancia.
El nivel OEB 5 equivale a una contaminación inferior a 1 µg/m3. Si equiparásemos esta cantidad al tamaño del Empire State Building de Nueva York, la proporción de la sustancia presente en todo el edificio no superaría una veinteava parte de una cucharilla. Naturalmente, no existe “una única solución” para lograr esto. Por el contrario, se pueden adoptar varios enfoques distintos. Por este motivo, según Claude Lefebvre, director de Desarrollo de Negocio del fabricante de equipos de trituración Frewitt, hay un aspecto que resulta esencial frente a todos los demás: un buen conocimiento del proceso.
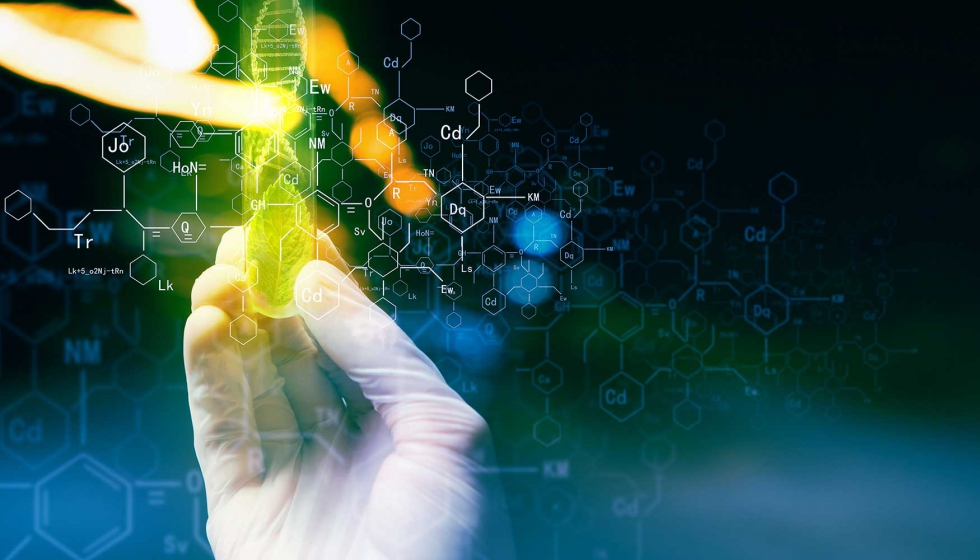
Protección del ser humano y del producto
Las dificultades comenzaron básicamente con las designaciones y las definiciones. En la actualidad, la clasificación OEB goza de una amplia aceptación, pero muchas empresas farmacéuticas poseen sus propias normas que, en cierta medida, superan los requisitos de las soluciones OEB 5. Por mencionar solamente un ejemplo, el equivalente a OEB 5 en Roche se denomina 3B. Precisamente estas empresas se consideran el principal factor de impulso del mercado de las soluciones de contención. “Durante los últimos años, la producción farmacéutica en masa se ha trasladado de Europa a Asia. En los países industrializados, las empresas se han visto obligadas a centrarse más en el desarrollo de productos de precio elevado, por ejemplo, para oncología”, explica Iris Barnstedt, CEO de Brinox Deutschland, empresa especializada en sistemas de procesamiento. El trabajo con estos productos de alta eficacia ha hecho necesaria una mejora de las normas en materia de seguridad ocupacional.
“Es esencial saber que, cuando se determina el nivel de equipamiento necesario y la eficacia de la contención, no basta simplemente con medir el valor límite de exposición profesional (OEL) del producto. Se trata de un error habitual que tiene como resultado una tendencia a la sobreespecificación en el sector. Si la solución elegida es demasiado compleja, el manejo, limpieza y mantenimiento del sistema se volverán más difíciles y los costes de aprovisionamiento obviamente serán superiores. Demostrar que una solución determinada es lo ”suficientemente buena" puede ser difícil, pero no imposible. Cuando se conocen bien el motivo que hace necesaria la contención y el producto y el operador y el equipo son objeto de la debida consideración, es posible desarrollar soluciones más sofisticadas y efectivas”.
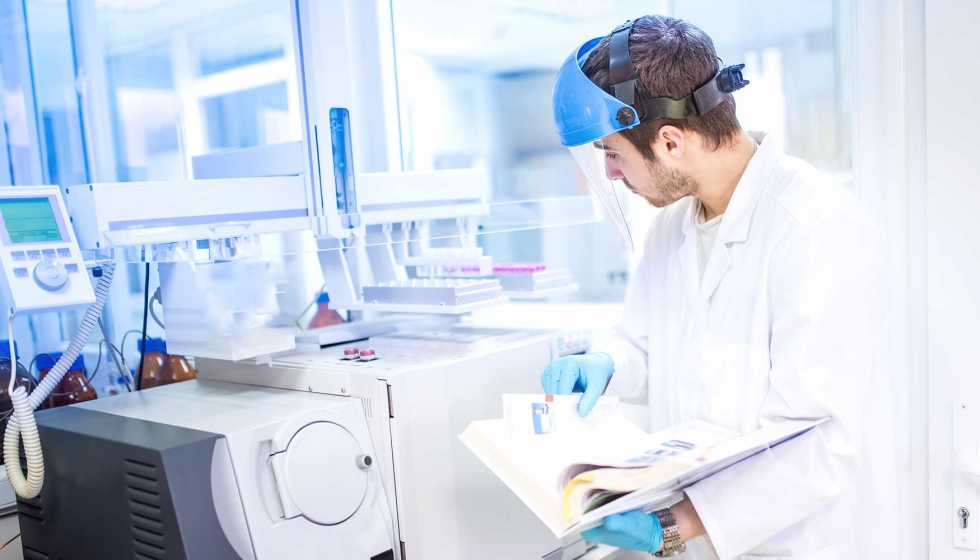
La demanda de los productos 'Made in Germany'
Puede que REACH esté obligando a los productores químicos a prestar gran atención a la seguridad ocupacional, pero el principal factor de impulso del mercado de las soluciones de contención es la industria farmacéutica, según Fred Lonzer, director de ventas y marketing del Grupo Müller, conglomerado especializado en sistemas de manipulación y envasado. La producción en masa se está viendo sustituida cada vez en mayor medida por una producción en lotes más pequeños más flexible que, naturalmente, ofrece máxima seguridad. “Estamos trabajando en estrecha colaboración con los fabricantes de aislamientos de este segmento en el desarrollo de unidades de envasado con dos interfaces. La reducción del número de interfaces hace el proceso más seguro”, explica Lonzer. Fritz Martin Scholz, director de producto de Hüttlin, filial de Bosch Packaging Technology, también comenta que la industria farmacéutica, en concreto, en el caso de los medicamentos contra el cáncer, por ejemplo, ha impulsado la demanda de sistemas de contención durante los últimos años.
“Para las empresas con operaciones de producción en regiones que están experimentando un alto crecimiento, el ingrediente activo y el mercado de venta son consideraciones importantes a la hora de decidir producir con equipos locales o europeos”. Scholz está convencido de que los sistemas de procesamiento 'Made in Germany' ofrecen la mejor calidad". Los sistemas de vanguardia cuentan con funciones que son importantes para la contención. Permiten, por ejemplo, detectar posibles fallos e interrupciones en el flujo del producto y emprender acciones correctivas sin necesidad de una intervención manual”, afirma Scholz. Con frecuencia son los pequeños detalles los que provocan problemas reales. Los operadores de las plantas suelen infravalorar el potencial del problema y esto hace que después se enfrenten a situaciones imprevistas. Por ejemplo, ¿a dónde va a parar el agua residual tras la limpieza? A este respecto debe tomarse una decisión crucial: ¿elijo aplicaciones de acero o de un solo uso? Empresas como Hecht comercializan sistemas de aislamiento con lámina desechable, pero la tecnología de “usar y tirar" no es la solución que prefieren algunos fabricantes”. Seguimos apostando por los sistemas de acero inoxidable. Naturalmente, seguimos de cerca las tendencias del mercado y, si se demandaran aplicaciones de un solo uso, actuaríamos en consecuencia”, destaca Lonzer.
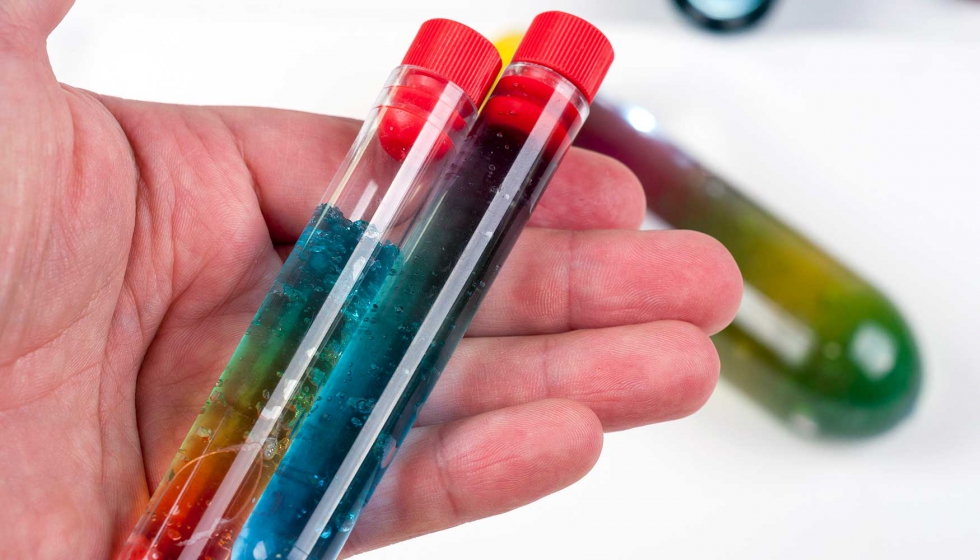
La contención por sí sola no basta
Los operadores de las plantas tienen que limpiar todos los componentes que se reutilizan. De nuevo, existen dos opciones o filosofías: retirada de todos los elementos con fines de limpieza o sistemas que se pueden limpiar en la línea, es decir, sistemas CIP/SIP o de limpieza manual. Andreas Bürckert, líder del equipo de ingeniería de diseño del fabricante de máquinas de envasado Bausch+Ströbel, señala las ventajas de este último enfoque: “Los sistemas CIP/SIP permiten validar el proceso porque las operaciones se llevan a cabo bajo el control de la máquina. El resultado es una calidad de limpieza uniforme y una secuencia de tiempo definida”. Además se requiere un menor número de intervenciones manuales por parte de los trabajadores que, de lo contrario, tendrían que retirar los componentes manualmente para su limpieza. Existen menos riesgos potenciales y se requieren un tiempo y esfuerzo menores. Bürckert destaca que, por motivos de eficiencia, cada vez son más los operadores de las plantas que ejecutan sus sistemas en paralelo. Mientras el programa CIP/SIP se ejecuta en uno de los sistemas, la producción continúa en el otro y esto reduce el tiempo necesario para el cambio. Si un operador de la planta opta por la limpieza automática, esto no significa necesariamente que la tecnología deba desplegarse en toda la línea de producción. “La tecnología CIP/SIP también se puede integrar en sistemas híbridos donde algunos de los equipos se limpian y otros son de un solo uso”.
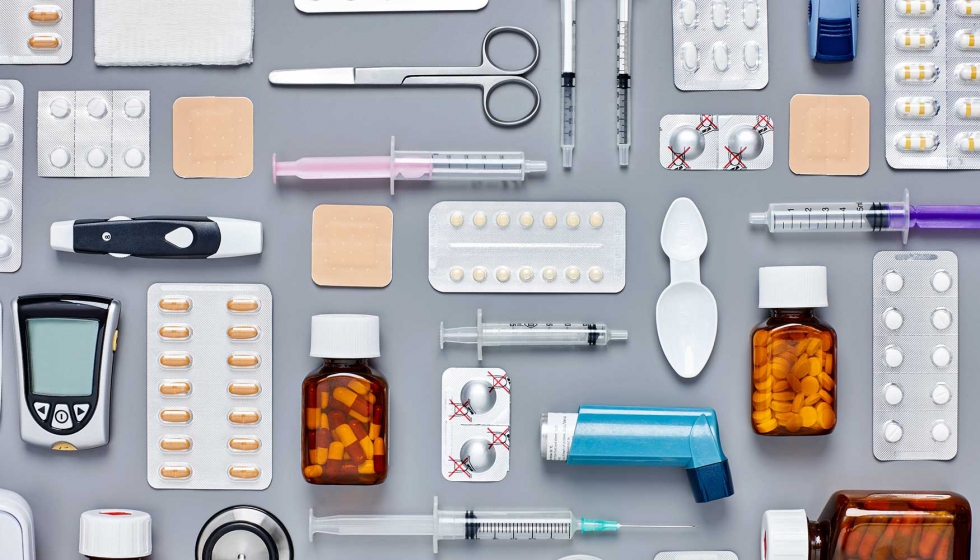
Validación de la instalación
Por muy bueno que sea el diseño de la solución, ningún sistema técnico proporciona contención al 100%. Es preciso adoptar las medidas adecuadas antes de la puesta en servicio para evaluar el cumplimiento de los límites especificados. La guía de buenas prácticas de la ISPE 'Assessing the Particulate Containment Performance of Pharmaceutical Equipment' (evaluación de la eficacia de la contención de partículas de los equipos farmacéuticos) explica cómo pueden los usuarios medir la concentración en el aire y la contaminación superficial y compararlas con los valores límite. Incluso con los que se consideran los mejores sistemas de contención del mundo, se recomienda precaución. Puede estar tranquilo, pero realice comprobaciones de todos modos.
Perspectivas
Nunca se hará suficiente hincapié en la idea de que la contención guarda relación principalmente con las interacciones o, para ser más exactos, con la forma de evitarlas. Cualquier interrupción en la contención durante el paso del producto de una fase del proceso a la siguiente supondrá un riesgo para los seres humanos y el producto final. Naturalmente, la ISPE se toma muy en serio esta posibilidad, como ha demostrado con la iniciativa Pharma 2025, que ofrece recomendaciones para futuros desarrollos: “Es esencial integrar la contención en el proceso y no adaptarla a este. En estos momentos, muchos de los sistemas de proceso no se descargan automáticamente y deben abrirse, lo que supone una interrupción en la contención. En este sentido se necesitan soluciones innovadoras”, comenta Denk.
Otra cuestión clave es el papel que el ser humano desempeñará en los entornos de producción del futuro en relación con las sustancias altamente activas. “Los valores de umbral se están acercando al límite actual de 1 ng/m3. Las actuales terapias contra el cáncer diseñadas para tratamientos localizados, que contienen sustancias extremadamente activas, se están acercando cada vez más al nivel de los nanogramos de un solo dígito. La especificación de dos nuevos productos recientemente lanzados en EE UU es de 0,1 ng/m3. Los métodos de medición también siguen mejorando y es cuestión de tiempo que se lleguen a detectar unos valores límite tan bajos. La posibilidad de encontrar sistemas de contención adecuados probablemente presentará las mismas dificultades. Los sistemas controlados mediante robots que no requieren supervisión son una opción posible”.