Reutilizar la información de ingeniería y el tratamiento de datos cerrado agilizan la fase de ingeniería y acortan los plazos de lanzamiento al mercado
El todo es más que la suma de sus partes: la modularización abre el camino hacia la Industria de proceso 4.0

La individualización es algo que no solo afecta a los vehículos, la ropa o los cereales del desayuno. También los sectores químico y farmacéutico se enfrentan a una creciente demanda de productos personalizados. Los ciclos de desarrollo y la vida útil de los productos son mucho más cortos, lo que supone todo un reto para los conceptos de las plantas industriales convencionales. En todo el mundo, las plantas modulares se perciben como la solución para dar respuesta a las cambiantes expectativas de los clientes. Estas plantas se caracterizan por su flexibilidad en términos de capacidad de producción (por ejemplo, mediante “adición” o paralelización), variedad de productos (cambiando los módulos de reacción o las fases de procesamiento aguas abajo), materias primas y ubicación (por ejemplo, módulos móviles). Los módulos estandarizados, profusamente disponibles, promueven la competitividad, en especial si son utilizados por un gran número de empresas. De este modo, es posible producirlos en grandes cantidades a menores precios.
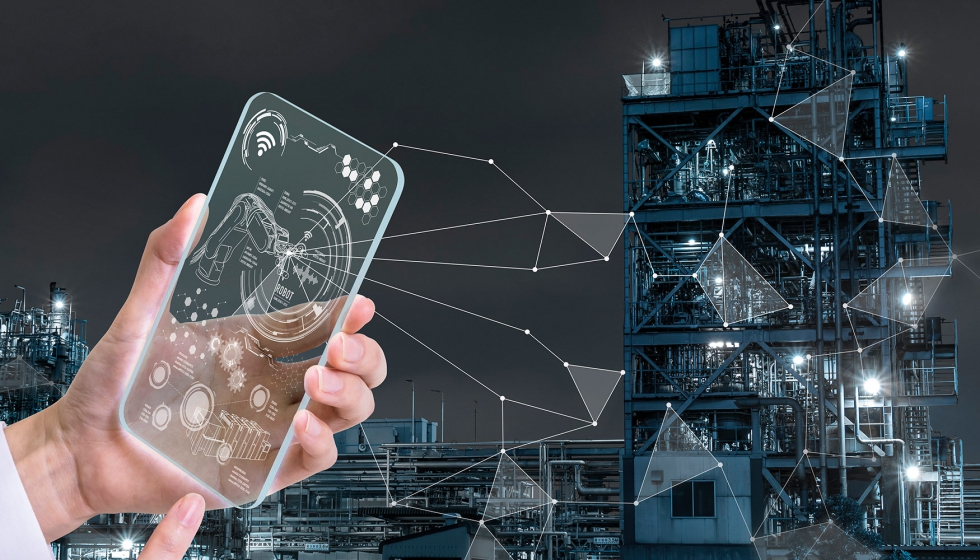
Modularización, desde la fase de planificación en adelante
Las ventajas de la modularización pueden aprovecharse desde la fase de planificación. La reutilización de la información de ingeniería y el tratamiento de datos cerrado en todas las fases del proyecto pueden agilizar la fase de ingeniería y acortar los plazos de lanzamiento al mercado. Para lograr este objetivo, es esencial contar con un flujo de trabajo de planificación modular estandarizado, antes de proceder a la modularización física.
Para conseguir unidades versátiles de producción continua y abrir la puerta a la producción descentralizada, se puede aplicar una modularización física de las plantas de procesamiento. El siguiente paso serán las definiciones de los módulos, de modo que se mantengan las funciones especificadas en una definición de PED. La modularización física puede realizarse in situ, a escala de máquinas, plantas o logística, así como en la red de producción. Cuando la modularización física es deseable, los módulos compatibles se construyen como unidades adaptables, ensamblándose para conformar plantas industriales polivalentes. Durante la explotación subsiguiente, la intercambiabilidad de los módulos individuales simplifica el mantenimiento y el servicio técnico, reduciendo además los tiempos de sustitución. Los datos operativos obtenidos durante la producción pueden ser empleados directamente por los ingenieros de plantas para definir estrategias de mantenimiento y optimizar los módulos ya planificados de cara a proyectos potenciales. Tras la fase de producción, la planta se desmonta, aunque la información y los componentes físicos pueden reutilizarse. Esto garantiza una mejora continua, así como la reaplicación de la experiencia operativa.
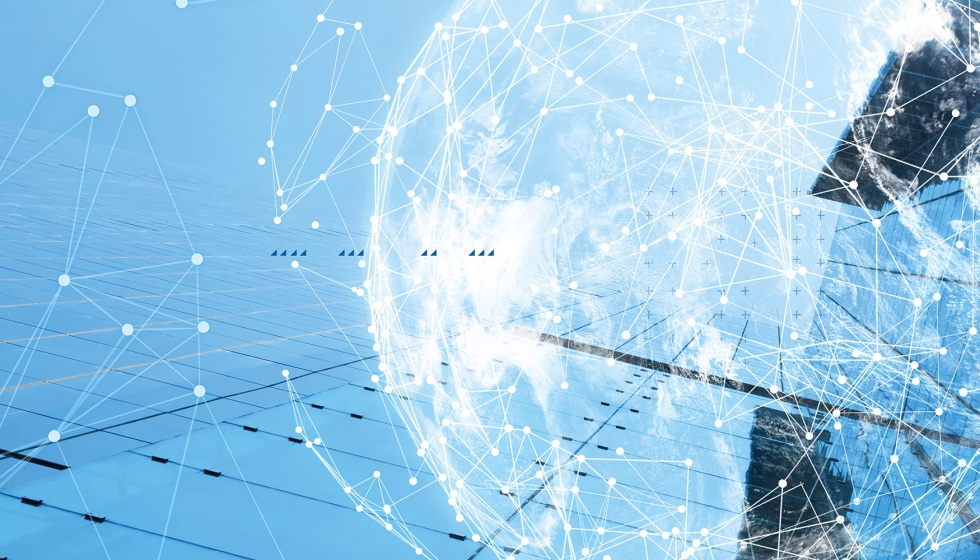
Modularización física: el módulo se ajusta a la función
Para implantar una metodología de modularización sistemática desde el desarrollo del proceso hasta el desmantelamiento de la planta, lo primero es dividir virtualmente un proceso en grupos de equipos pertenecientes a una misma parte del proceso. Esto reduce la complejidad y permite crear componentes básicos reutilizables. Todos los documentos de planificación necesarios para la construcción de estos módulos se combinan en unidades de procesamiento funcionales denominadas módulos de Diseño de equipos de proceso (Process Equipment Design, PED), y se guardan en bases de datos. Un PED incorpora al menos un equipo principal, capaz de realizar la operación unitaria deseada, conjuntamente con todos los componentes periféricos necesarios. Dentro de cada PED, es posible intercambiar los equipos principales para adaptarlos a diferentes condiciones operativas. Cada PED se guarda como un elemento de una base de datos que contiene toda la información y la documentación.
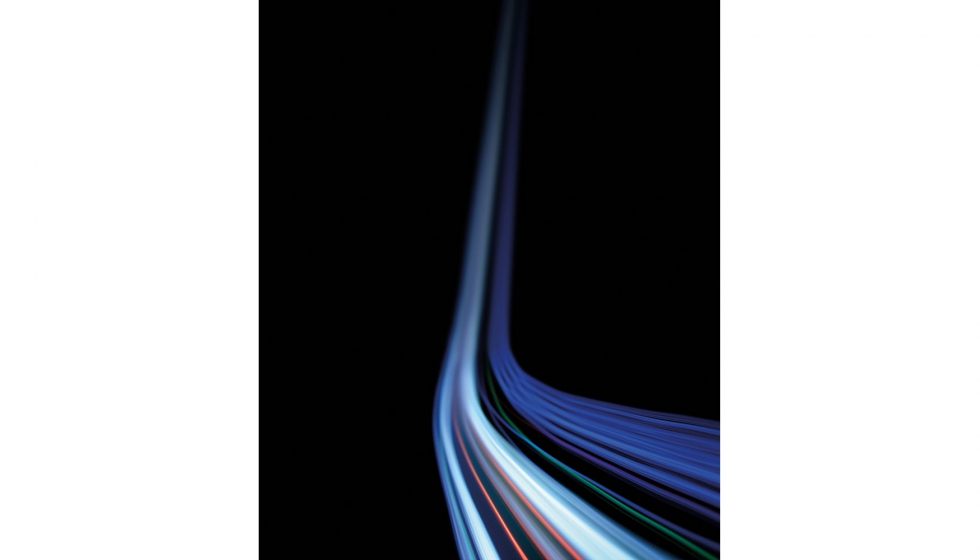
Los PED deben acompañarse de modelos de simulación, que facilitan la configuración de módulos a partir de una descripción de la funcionalidad del PED. Seguidamente, los PED se clasifican en unidades funcionales, unidades de procesamiento y unidades de servicio. Las unidades de procesamiento están en contacto directo con reactivos y flujos de procesamiento o de residuos (por ejemplo, almacenamiento y dosificación, reacción, tratamiento aguas abajo, formulación y envasado). Las unidades de servicio desempeñan funciones de apoyo a una o más unidades de proceso; por ejemplo, suministro de agua y electricidad, y no tienen contacto directo con los flujos de proceso. Esta diferenciación, así como las bases de datos relacionadas, suelen permitir escenarios de reutilización diferentes, capaces de agilizar el tiempo de lanzamiento al mercado.
Los PED individuales pueden combinarse para constituir un Diseño de planta de proceso (Process Plant Design, PPD). El PPD se adapta al ámbito de rendimiento de una planta modular, y consta de toda la documentación necesaria para una construcción y un funcionamiento efectivos. Entre otras cosas, define las posiciones y conexiones entre los PED y representa virtualmente el proceso deseado.
El núcleo son los equipos modulares
Para hacer posible un entorno de producción eficiente y versátil a la vez, un prerrequisito fundamental es la disponibilidad de equipos de proceso fiables para tareas de procesamiento industrial a pequeña escala. Esto incluye descripciones validadas de modelos de equipos de intensificación de procesos, así como dispositivos robustos y fiables, con calidad industrial. Un equipo individual puede definirse como “modular” si presenta al menos una de las siguientes características:
- Un diseño modular inherente, que posibilite la “adición” en serie o en paralelo de elementos básicos (por ejemplo, un reactor tipo canal preparado para sumar varios canales y longitudes), o bien otra función clave específica asociada a la reutilización de los equipos.
- Un diseño modular inherente con elementos configurables capaces de adaptarse a diversas condiciones operativas (por ejemplo, sistemas modulares de control de procesos que posibiliten la integración variable de módulos en un sistema principal).
- Series de equipos que proporcionen la misma funcionalidad a diferentes escalas operativas (por ejemplo, una serie de bombas con diferentes rangos de caudal volumétrico, empleando en todos los casos el mismo principio operativo).
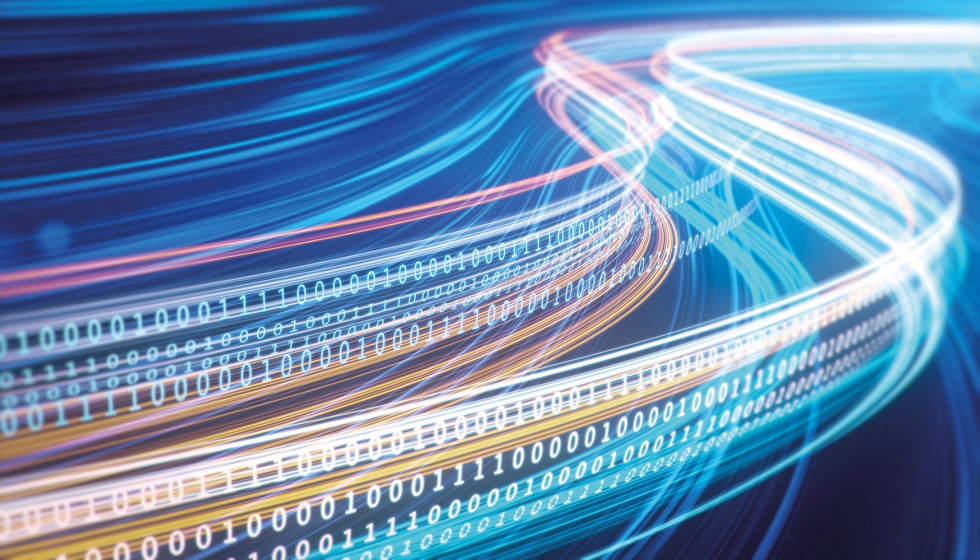
La modularización física es adecuada para plantas multiproducto/polivalentes, en las que es frecuente reconfigurar la estructura de procesamiento entre distintas tiradas de productos. Además, es posible integrar equipos de funcionamiento continuo de pequeña escala en plantas piloto o productoras de lotes polivalentes, para abrir la puerta a conceptos de producción híbridos de alta eficiencia. En este caso, la planta se compone de Bloques de equipos de proceso (Process Equipment Assemblies, PEA) individuales. Un PEA representa la ejecución física de un PED, siguiendo una serie de directrices de diseño adicionales, técnicas y geométricas, con el objeto de garantizar la compatibilidad entre módulos planificados de manera independiente. Durante la explotación subsiguiente, la intercambiabilidad de los módulos individuales simplifica el mantenimiento y el servicio técnico, reduciendo además los tiempos de sustitución.
Una planta industrial dentro de un contenedor
La conexión de diversos PEA a una planta de producción se describe en el Marco de equipos de proceso (Process Equipment Frame, PEF). El PEF contiene las condiciones geométricas y las especificaciones en materia de seguridad del entorno de instalación, e incorpora el suministro de todos los PEA. Al contener la totalidad del sistema de control de proceso de los PEA ordenados, el PEF se considera una unidad de producción independiente. En el caso de entornos de producción autónomos o descentralizados, la integración de los PEA en un PEF puede realizarse utilizando contenedores de transporte modificados, que pueden servir como una infraestructura totalmente integrada para construir un entorno de producción móvil y reconfigurable, que solamente requiere el suministro de servicios públicos básicos sobre el terreno.
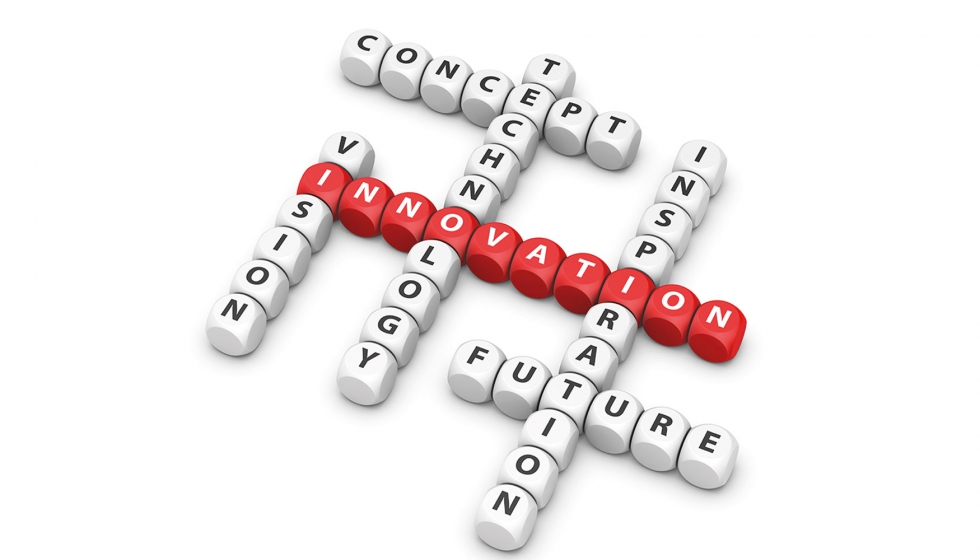
Para explotar al máximo los procesos continuos intensificados, deben adoptarse medidas fundamentales tendentes a una producción a largo plazo estable, perfectamente controlada y plenamente automatizada. En este contexto, desempeñan un papel fundamental las tecnologías analíticas de proceso (Process Analytical Technologies, PAT). Sobre la base de su información, es posible monitorizar, controlar y optimizar los parámetros críticos de proceso (Critical Process Parameters, CPP) para conseguir la calidad final de producto deseada o para detectar cambios en los atributos críticos de calidad (Critical Quality Attributes, CQA).
Para una implementación eficiente de las herramientas analíticas PAT, los métodos de medición requeridos (incluidos puntos de medición/muestreo adecuados) deben definirse en una fase temprana de la planificación. Lo ideal es que en todo el desarrollo del proceso se utilicen los mismos métodos de análisis, aumentando paulatinamente la escala desde el laboratorio hasta la planta piloto y la planta de producción. De este modo se agiliza la implantación de las herramientas PAT.
Los prerrequisitos de las plantas industriales modulares son: un conocimiento más profundo de la tecnología de microrreacción, la intensificación de los procesos y la producción continua. En todas estas áreas se han desplegado enormes esfuerzos de investigación y —lo que no es menos importante— financiación pública en los últimos años. Una serie de proyectos de investigación, tales como F3 Factory o la iniciativa ENPRO, han demostrado que el concepto de la modularización es viable y puede llevarse a la práctica. La visión del proyecto F3 Factory supuso un planteamiento modular radical para un desarrollo rápido de procesos y para la implementación de procesos novedosos flexibles y sostenibles, con una mejora de los índices de inversiones de capital y capital de explotación. El potencial de la intensificación y la modularización en el sector químico se ha demostrado en varios casos de estudio. En el diseño inicial del proyecto se aplicaron directrices y normas que optimizan la flexibilidad de una planta de producción mediante PEA intercambiables.
La visión se hace realidad
Además de proyectos con financiación pública, varias empresas químicas —y proveedores— ya han comenzado a adoptar la modularización en sus diferentes campos de aplicación. Ante la falta de una visión común sobre el grado de modularización y estandarización, se han empleado diversos métodos para llevar a la práctica la modularización según la empresa.
- BASF emplea contenedores personalizados para la producción a pequeña escala (dispone de talleres de construcción centralizados) y los transporta a los sitios de interés para la producción.
- Evonik usa contenedores como un tipo especial de plataforma de infraestructura móvil normalizada (Eco Trainer), con el fin de agilizar el desarrollo de los procesos y la posterior producción a pequeña escala. Este concepto se ha probado con éxito en el pasado en el segmento de productos químicas para el sector electrónico. Además, Evonik está estableciendo un concepto de marco modular similar al concepto de F3 Factory para el desarrollo de procesos en un entorno de planta piloto.
- Merck trabaja en un entorno en el cual el tiempo de llegada al mercado es el factor más sensible a la hora de lanzar nuevos productos. Las plantas de producción continua a pequeña escala siguen un concepto de planta multiproceso, que aporta un alto grado de flexibilidad combinado con la intensificación de los procesos.
- Clariant diferencia entre conceptos de planta modular que atienden necesidades específicas, como la llegada al mercado (rápida y fiable) y tipos de transferencia tecnológica (muestreo, proyectos piloto y formación). En este momento, Clariant trabaja en proyectos piloto centrados en formulaciones y reacciones químicas.
- Invite ofrece servicios de ingeniería para plantas modulares según el concepto de F3 Factory. Sus servicios incluyen ingeniería básica y de detalle, así como ensayos en un centro técnico especialmente concebido para contenedores de proceso modulares.
Además de la implantación de estos conceptos en las empresas químicas, hay cada vez más proveedores que los aplican en sus actividades. ZETON construye plantas piloto, miniplantas y laboratorios modulares para diferentes segmentos del sector químico. Integrated Lab Solutions (ILS) construye laboratorios compactos y miniplantas especializados en experimentación de alto rendimiento con ME. Hte suministra tecnologías y servicios para mejorar la productividad de la I+D, poniendo el acento en las plataformas tecnológicas de altas prestaciones y los sistemas modulares para ensayos con catalizadores. Lonza y Ehrfeld ofrecen sistemas de microrreactores modulares para producción continua. Por su parte, HiTec Zang ha desarrollado un sistema de automatización de laboratorio que facilita la ejecución rápida de protocolos de secuencias por lotes. Sin embargo, estos conceptos modulares se siguen basando en conceptos de estandarización individuales y carecen de un enfoque de estandarización común.
Así encaja el puzle: estandarización
Sin embargo, la construcción de plantas modulares supone un enfoque totalmente nuevo. El diseño y la construcción de una planta industrial completamente modular todavía requiere un importante esfuerzo, en especial en lo relativo a la estandarización de equipos y a la tecnología de automatización.
Un requisito previo fundamental del enfoque modular es el desarrollo de soluciones estandarizadas para los problemas repetitivos, así como la definición de directrices para el diseño de los nuevos PED. Entre algunos ejemplos de aplicaciones estandarizadas cabe citar el almacenamiento, la dosificación o el mezclado. Típicamente, estas actividades no suponen conocimientos competitivos. Pueden ser desarrolladas mediante iniciativas conjuntas de varias empresas y la fabricación puede correr a cargo de proveedores. Esto podría reducir sustancialmente los costes de fabricación de plantas industriales. Por otra parte, los PED deben diseñarse individualmente o bien se deben modificar PED ya existentes, sea porque no se dispone de PED adecuados, o bien porque determinadas condiciones límite hacen inevitable el diseño individual.
Se necesitan interfaces para interconectar los PEA entre sí y con la infraestructura local. Estas interfaces deberán ajustarse a los requisitos de una gran variedad de procesos potenciales. Esto solo puede conseguirse con interfaces flexibles, adecuadas para adaptarse a condiciones límite locales. Aunque se normalicen las interfaces en función de las conexiones aplicadas con mayor frecuencia, seguirá siendo necesario un cierto grado de libertad para adaptarlas a los requisitos locales. Esto permitirá agilizar la instalación de los PEA y la reconfiguración del entorno, para conseguir plantas industriales polivalentes. En caso de intercambios frecuentes se requieren interfaces que posibiliten una conexión y desconexión rápidas de los PEA. Sin embargo, esto podría conllevar costes adicionales sustanciales. En consecuencia, sería importante encontrar un compromiso razonable entre estandarización y flexibilidad.
La modularización es una de las megatendencias que cubre la temática “Producción flexible” que se trató en la anterior edición de Achema, con fuerte cobertura tanto en la exposición como en el congreso.
Este informe de tendencias es un extracto del documento técnico “Plantas modulares”, preparado por el grupo de trabajo temporal ProcessNet sobre sistemas modulares, en estrecha cooperación la industria y centros de investigación. Este informe repasa la situación actual de las iniciativas conjuntas para perfeccionar la modularización de las tecnologías de plantas industriales en el sector químico. Puede consultar el informe completo en http://dechema.de/dechema_media/modularplants.pdf
Los informes de tendencias de Achema son compilados por periodistas internacionales especializados. Dechema declina toda responsabilidad por cualquier información incompleta o inexacta. Los informes de tendencias de Achema pueden ser utilizados gratuitamente para fines editoriales, citando la fuente (ver información más detallada en www.achema.de).