La firma está especializada en el sector de sistemas de cierre mecatrónicos para automóviles
La técnica de secado y transporte Motan convence a Witte Automotive
En lo que se ha convertido un taller fundado en 1899 en Velbert (Alemania) por Ewald Witte para la producción de cerraduras de maletas hasta el día de hoy, es algo increíble. Hoy sigue siendo la empresa familiar Witte Automotive, que cuenta en Europa con 9 plantas distribuidas en Alemania, Suecia, Chequia y Bulgaria, con un total de 5.200 empleados en 2017 y un volumen de ventas de más de 670 millones de euros, y todo ello con el principio fundamental de 'Cerrar y echar el pestillo'. En la actualidad, Witte Automotive figura entre los líderes en tecnología en el sector de sistemas de cierre mecatrónicos para automóviles, como parte de soluciones sistemáticas para puertas, portones, interior y asientos. Witte Automotive está representada a nivel internacional en EE UU, México, Brasil, India, China, Japón y Corea, como parte de VAST, la alianza Vehicle Access Systems Technology. Con aproximadamente 12.000 colaboradores y un volumen de ventas de unos 1.700 millones de dólares nortamericanos, VAST figura entre los proveedores líderes a escala mundial en este sector de producción.
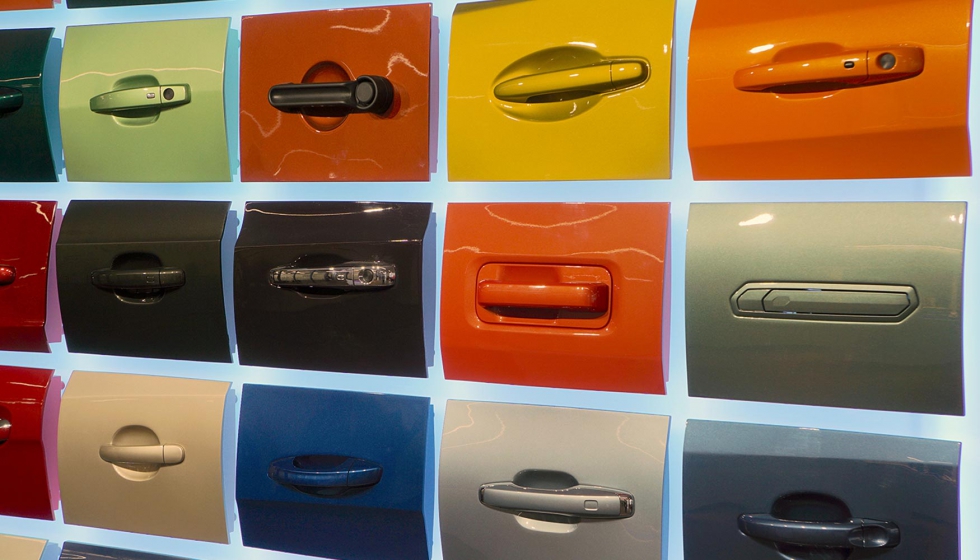
Fig. 1: Los tiradores de puertas de automóviles junto con los mecanismos de cierre, ubicados detrás de los mismos, constituyen los elementos principales de la fábrica de tiradores exteriores de puertas integrados, inaugurada en el año 2016, de Witte Automotive en la ciudad de Ostrov en Bohemia del Norte. El objetivo a medio plazo es alcanzar una producción anual de 20 millones de unidades. Foto: Reinhard Bauer.
La fábrica Witte inaugurada en 2016 en la localidad de Ostrov se ha especializado en la producción de unidades de tiradores de puertas junto con los módulos técnicos asociados con los mismos. En Ostrov se realiza particularmente la fundición inyectada de plástico, el barnizado y el montaje. Un componente importante de la instalación lo constituye la instalación de transporte centralizada y automatizada para granulados de plástico en las máquinas de fundición inyectada. Esta máquina fue suministrada por el grupo alemán Motan, representado en España por Coscollola.
Ofrecen una gran variedad de formas, colores y funciones de los tiradores exteriores de puertas fabricados en Witte Automotive en Ostrov y sus unidades de bloqueo. Cumplen con los requisitos vigentes de seguridad y colisión, están realizados con y sin accionamiento a distancia, así como en forma de manejo 'Entrada pasiva/Salida pasiva' sin llave. Están hechos, en función del color específico del vehículo (Fig. 1 + 2). Las medidas 'antipicking' patentadas dan el toque final a la oferta en cuestión de protección antirrobo. En total, la oferta de Witte Automotive comprende además de los tiradores exteriores, también los arcos de cierre, los accionamientos interiores de la puerta, llaves y cerraduras, en aquellos casos necesarios, ayudas de cierre, fijadores de puertas y frenos de puertas, accionamientos de puertas, así como sistemas de protección de puertas.
El programa de suministro es también amplio para los portones delanteros y traseros. Además de cerraduras electromecánicas, también se emplean arcos de cierre eléctricos para portones traseros accionados o agarraderos de fácil montaje. Particularmente para los productos desarrollados para portones delanteros, las curvas sofisticadas de elevación se combinan con una construcción compacta y resistente. Forman parte, por ejemplo, del concepto del capó de motor 'activo' para aumentar la protección de los peatones que, en caso de colisión, se eleva mediante activación pirotécnica y, así, hace más blanda la zona frontal de absorción de impactos.
También para asientos de turismos hay disponible una amplia gama de productos. "Las cerraduras de respaldo absorbentes de energía y los arcos de cierre minimizan, en caso de colisión, la carga del respaldo. Forman parte del equipo de seguridad para la protección de los ocupantes. Los innovadores cerrojos en el fondo del asiento para la retirada y el montaje todo confort de los asientos, así como el sistema activo de respaldo de seguridad (ASR) dan el toque final al programa de Witte", así resume David Svoboda, jefe de sección Fundición Inyectada, en el curso de su presentación de la empresa.
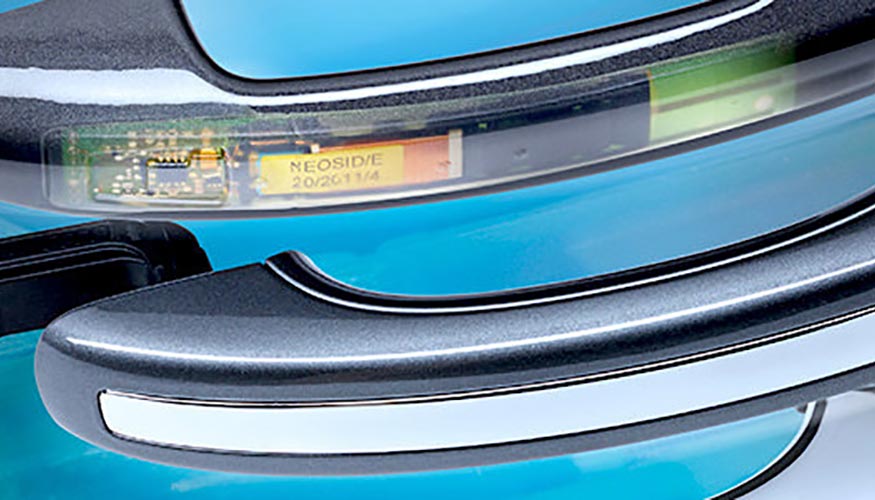
Fig. 2: Ejemplo de un módulo de tirador de puerta con electrónica integrada de emisión / recepción para la realización de un acceso sin llave. Foto: Reinhard Bauer. Foto: Witte Automotive
Piezas de plástico de una calidad inmejorable
Como los tiradores de las puertas y portones de un automóvil se encuentran en el área de visión y contacto del usuario, contribuyen en su forma y tacto considerablemente en la impresión de calidad de un automóvil.
Los módulos de los tiradores se fabrican como 'Car sets'. Un set comprende todos los tiradores de la puerta de un vehículo junto con las funciones relacionadas con los mismos. Las piezas estructurales se fabrican, por motivos de solidez, de PA6 con un 35% de fibras de vidrio, las cubiertas de un marco de PC/ABS. Se emplea sin excepción material coloreado previamente. Actualmente se produce en 12 máquinas de fundición inyectada, otras 10 ya se han planificado para su aplicación en un futuro próximo (Fig. 3).
Una gran parte de los tiradores se fabrica como cuerpos huecos mediante aplicación de técnica de inyección de gas. Lo que conlleva que, con cada ciclo de producción, una parte de material con una magnitud del 30 al 40% del volumen de plástico inyectado se desplace a una cavidad secundaria, que a continuación se separa, recolecta y, después de triturar, de nuevo se retorna a la corriente de material. "Para garantizar la calidad de la superficie, todos los materiales, tanto la mercancía nueva, como también el material reciclado tiene que secarse hasta alcanzar una concentración de humedad residual de un 0,1 a un 0,15% (PA6) o de un 0,02 a un 0,05% (PC/ABS)", explica Pavel Karas, jefe de departamento Fundición Inyectada en la fábrica de Ostrov. "Por este motivo, sólo podemos considerar una instalación con una estructura para la que se conducen todos los tipos de plástico tratado, inclusive cantidades de reciclado, a través de la instalación de secado central con aire seco hacia las máquinas".
La instalación de secado representa el 'corazón' técnico debido a la aplicación del sistema de suministro de material, en función de éste, se ha podido mantener sencilla la alimentación de material en la máquina de fundición inyectada. En la máquina se ha previsto un mezclador, para mezclar la materia virgen con la reciclada, así como con un aditivo. Debajo del equipo de dosificación se encuentra un detector de metales para separar las virutas de cuchillas posiblemente contenidas en el material molido.
La instalación completa se puede manejar claramente a través de un ordenador piloto de producción
Todos los componentes de la instalación, con excepción de los equipos de dosificación en las máquinas de fundición inyectada, se controlan y manejan por medio de módulos electrónicos desarrollados específicamente por Motan para este fin. Están conectados entre sí a través Ethernet o TCP/IP con un CONTROLnet al sistema de control centralizado. El cual está combinado con el amplio sistema de gestión de instalaciones LINKnet, que registra las etapas del proceso y datos de la aplicación, los protocola y a través de todo esto, todos los mandos conectados, así como también los equipos se pueden manejar y controlar. Además, se ha realizado una interfaz para el sistema ERP existente (Enterprise-Resource-Planning).
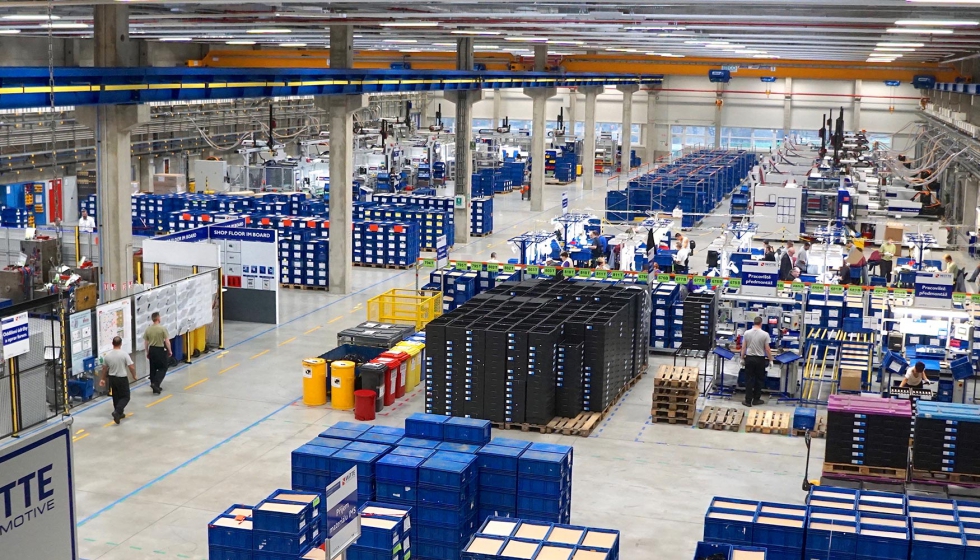
Éxito por medio de estrecha asociación
Para terminar, el jefe de sección Svoboda resume la puesta en marcha de la producción indicando el criterio principal de su elección por Motan: "En vista de la estrecha agenda de la que disponíamos durante la construcción y la puesta en marcha de nuestra nueva fábrica de producción, consideramos importante mantener lo más bajo posible el riesgo técnico en todos los componentes de la instalación. Tras toda una serie de visitas de referencia que nos convencieron por completo, nos decidimos por Motan-colortronic como proveedor de sistemas y Luger como planificador de sistemas y socio de servicio técnico, y desde entonces, seguimos convencidos de haber tomado la decisión correcta". (Fig. 4).

Fig. 4: El socio de proyectos Motan-colortronic, Luger y Witte Chequia echan una mirada retrospectiva sobre el trabajo exitoso realizado en común. De izquierda a derecha: Carola Wirth, Marketing Motan-colortronic, Thomas Luger, representante de Motan-colortronic para Chequia, David Svoboda, jefe de sección Fundición Inyectada Witte Chequia, Jaroslav Houska, coordinador de proyectos Fundición Inyectada, Pavel Karas, jefe de producción Fundición Inyectada en Witte-Ostrov y Zdenek Tesar, colaborador externo de la compañía Luger para la región de Bohemia.
Las instalaciones de un vistazo
Potencia para ocho materiales diferentes en 22 máquinas de fundición inyectada
Se tratan marcos de PC/ABS con y sin contenido de fibra de vidrio, PA 6 con 30% de fibra de vidrio en cantidades de consumo de 20 a 100 kg/h, con distribución flexible en varias máquinas respectivamente. Todos los materiales se alimentan desde la instalación de secado centralizada, por transporte de aire seco, hasta las máquinas de fundición inyectada.
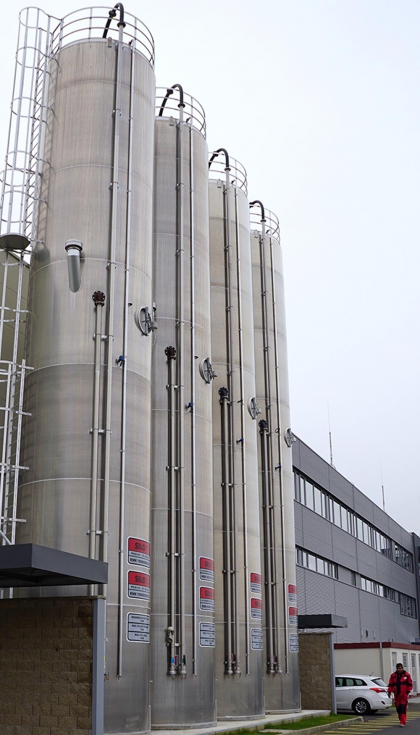
Fig. 1a: El material suministrado se almacena en cuatro silos de doble cámara. Fig. 1b: Las conducciones de llenado están aseguradas por finales de carrera contra un llenado erróneo. Fotos: Reinhard Bauer Secado de material Los tipos de material tratados en Witte se secan centralizados, antes de su transporte a las máquinas. Para este fin se emplean secadores de aire seco Luxor de Motan de la serie ETAplus. 'ETA' designa la letra griega con la que se representa en la técnica el grado de eficacia. (En Motan significa ETA-process la adaptación óptima de la temperatura de secado, la cantidad de aire seco alimentada, el punto de rocío y el tiempo de secado.) ETAplus combina la adaptación de la temperatura con una regulación adicional de la cantidad de aire. El sistema detecta por sí mismo las oscilaciones de rendimiento del material o las temperaturas modificadas de la entrada de material en el sistema de secado y adapta automáticamente la cantidad de aire a la energía necesaria de la tolva de secado.
Silos divididos para el almacenamiento de materias primas
Los 8 tipos más importantes de plástico se retiran del silo para su tratamiento. Los cuatro silos dobles se han adaptado a las cantidades consumidas y previsto con un contenido, en cada caso, de 2 x 47 m3 uno encima de otro para la separación de lotes (Fig. 1a). Los seguros de cerradura en los puntos de acoplamiento reducen el potencial de carga errónea. Entre los silos y la instalación de secado colocada posteriormente se transportan los materiales a través de un grupo de vacío con soplante de canal lateral con convertidor de frecuencia de alta eficiencia energética.
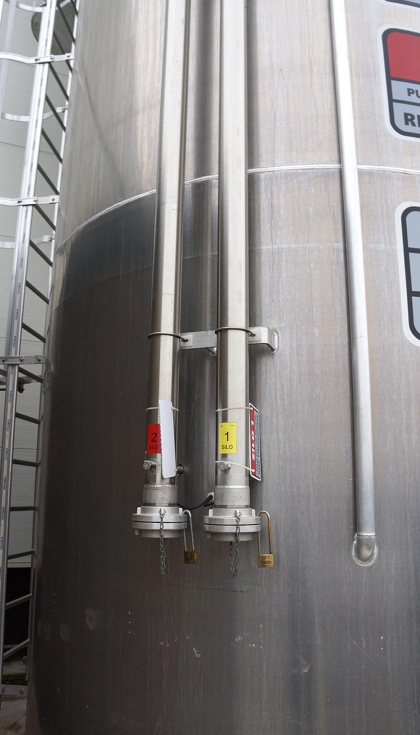
Foto: Reinhard Bauer Fig. 2: La serie Luxor A con el ETA-process de alta eficiencia energética y la tecnología de secado ETA plus comprende diez modelos con un rendimiento de aire seco de 80 a 2.400 m3/h. Están equipados con cartuchos de tamiz molecular fijos y aislados con procesos separados de secado y reciclado que generan un punto de rocío bajo constante para el proceso. Todas las instalaciones de secado Luxor A incluyen un controlador LUXORnet y se benefician de una tecnología moderna y flexible de BUS. El control de la instalación está en comunicación con el sistema de ordenador piloto LINKnet, a través del cual se vigila y controla toda la instalación.
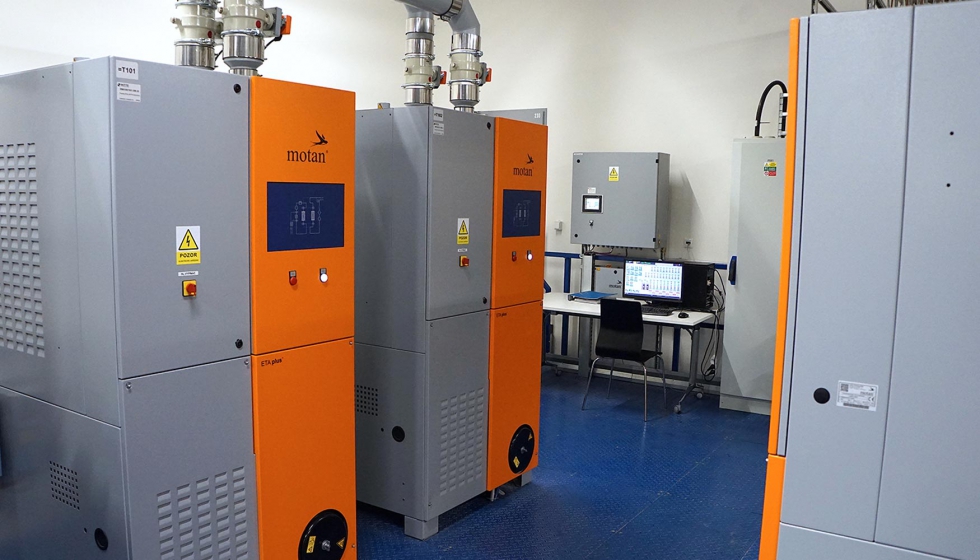
Fig. 3: Cada secador Luxor se puede combinar con toda flexibilidad con el volumen de la tolva de 15 a 2.400 litros. Todas las tolvas de secado están fabricadas en serie en acero inoxidable, totalmente aisladas y disponen de una calefacción y regulación de la temperatura individuales. Una característica importante de la instalación consiste en la geometría especial de la tolva, que con su relación altura/diámetro influye positivamente en el flujo de material por la tolva y así en el resultado del proceso de secado. Se pueden evitar tanto las zonas 'muertas', en las que el material se seca demasiado y, por lo tanto, se daña, como también el paso demasiado rápido del material por el centro de la tolva. Las dimensiones óptimas se han determinado realizando cálculos y ensayos prácticos. Foto: Reinhard Bauer Metroconnect. Sistema de acoplamiento C con codificación.
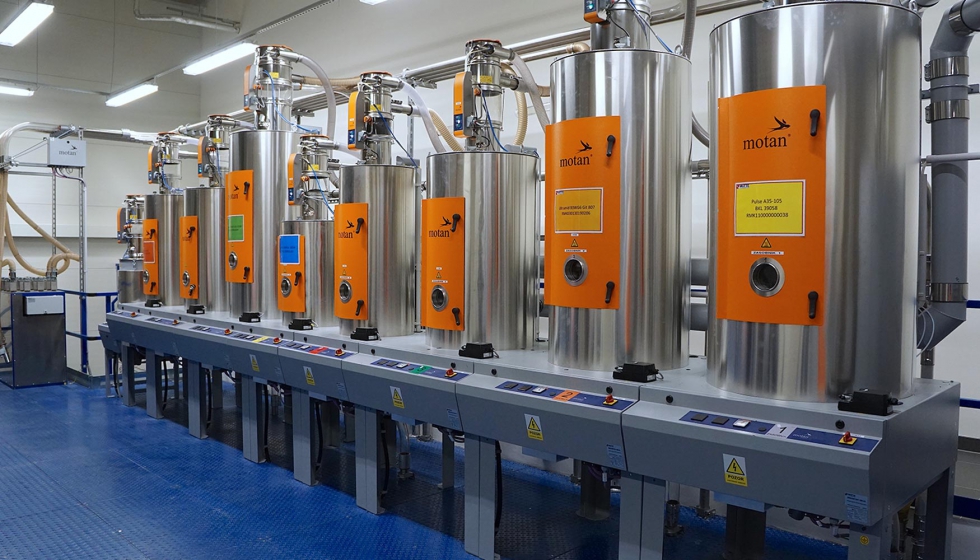
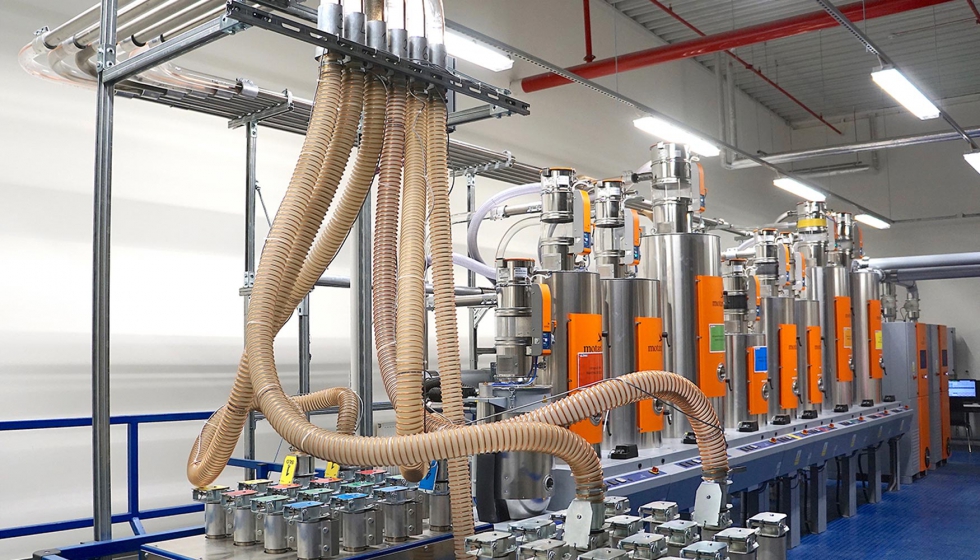
Fig. 5: La conducción de material entre la instalación de secado y las máquinas de fundición inyectada, consta de tubos de acero fino y codos de tubos de vidrio. Foto: Reinhard Bauer.
Dosificaciones de material en las máquinas de fundición inyectada
Todas las máquinas de fundición inyectada se han equipado con un separador de material y con un equipo de dosificación Gravicolor gravimétrico instalado encima con tres separadores de material. En las máquinas se trata material nuevo y material molido, pudiéndose ajustar la relación de la mezcla. El tercer componente es un aditivo.
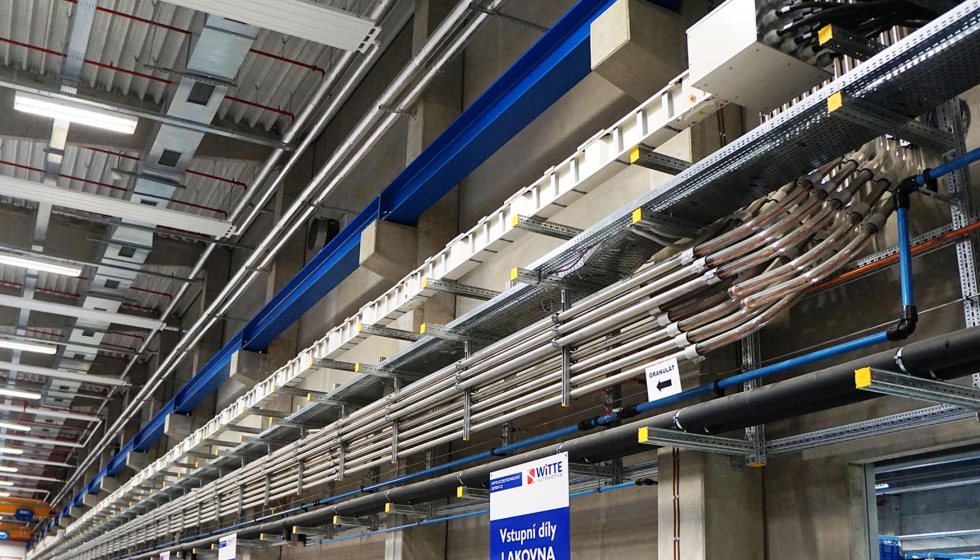
Ordenador piloto de producción
Todos los componentes de la instalación se controlan y manejan a través de módulos electrónicos que se pueden controlar a distancia y que están desarrollados específicamente para este fin. Los silos y la instalación de secado y transporte se vigilan y controlan a través de Motan CONTROLnet.
El concepto básico de la instalación ofrece más opciones de ampliación, las cuales incluyen también la gestión de instalaciones por medio de Motan LINKnet, al que se conectan todos sistemas de control aptos para la comunicación de Motan. Permite registrar todas las etapas del proceso y datos de la aplicación dentro de la instalación Motan, así como protocolar y manejar todos los equipos conectados. Con la protocolización completa de los procesos de la instalación se pueden relacionar los lotes de material tratados con los productos fabricados y realizar su seguimiento. (Fig. 7)
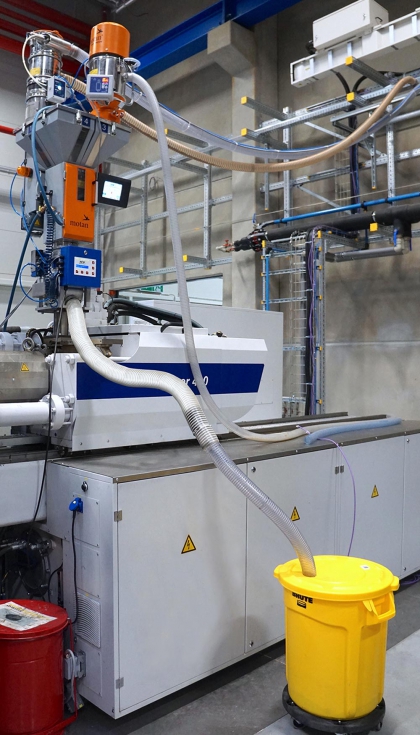
Fig. 7: Las funciones y los datos de ajuste de la instalación central se visualizan y controlan a distancia a través de Motan LINKnet. Foto: Reinhard Bauer
Sobre las empresas colaboradoras
Motan-Gruppe
El grupo Motan con sede en Constanza, a orillas del Lago de Constanza, en Alemania fue fundado en 1947. Como proveedor líder de sistemas para el manejo de materias primas, actúa en los sectores de moldeo por inyección, moldes de soplado, extrusión y compounding. En la gama de productos orientada por la aplicación figuran soluciones para sistemas innovadores y modulares para el almacenamiento, el secado y la cristalización, para el transporte, la dosificación y la mezcla de materias primas para las industrias de producción y tratamiento de plásticos. La elaboración se efectúa en las plantas de producción ubicadas en Alemania, India y China. En total, Motan actúa en más de 120 países en los sectores de ventas y servicio técnico. En la actualidad con más de 500 empleados se alcanza un volumen de ventas anual de unos 118 millones de euros.
Motan-colortronic gmbh Max-Eyth-Weg 42 D-88316 Isny im Allgäu Tel.: +49 7562 76-0 Internet: www.motan-colortronic.com
Luger Ges.m.b.H.
La compañía Luger Ges.m.b.H fue fundada en 1967 y por Willibald Luger como empresa de comercio y montaje, puesta en marcha para la venta de máquinas de fundición inyectada de plástico, instalaciones de extrusión y equipos periféricos en Austria, Chequia, Eslovaquia y Hungría y actúa de socio y asesor de proyectos. Luger es socio de Motan desde 1973.
Witte Automotive
En todas las marcas conocidas de vehículos se encuentran hoy en día productos Witte. Con soluciones innovadoras y unos amplios conocimientos tecnológicos, Witteentusiasma desde hace muchas décadas a sus clientes automovilísticos de todo el mundo. En la actualidad, Witte Automotive figura entre los líderes en tecnología en el sector de sistemas de cierre mecatrónicos para automóviles, y desarrolla junto con sus clientes soluciones sistemáticas innovadoras para puertas, portones, interior y asientos.
Los centros competentes y especializados en la técnica de plástico, estampado y fundición a presión garantizan resultados máximos desde el punto de vista funcional, cualitativo, ecológico y económico.
Con la inauguración de la fábrica de producción más moderna a escala mundial para tiradores exteriores de puertas barnizados en Ostrov/Chequia, Witte Automotive abre nuevos horizontes en el sector desde 2016 y consolida así su posición líder en el mercado. Junto a sus cuatro plantas dentro de Alemania, WITTE Automotive actúa en toda Europa, como en Chequia, Bulgaria, así como en Suecia. Por lo demás, Witte Automotive está representada a nivel internacional en los EE UU, México, Brasil, India, China, Japón y Corea, como parte de VAST, la alianza Vehicle Access Systems Technology.