Se ha optado por la instalación de un sistema de bomba de calor con CO2 como refrigerante
Reforma de la instalación de producción de ACS en el Centro Deportivo Activa Club El Puerto de Santa María de Cádiz
El caso práctico que vamos a exponer es la reforma de la instalación de producción de ACS en el Centro Deportivo Activa Club El Puerto de Sta. María (Cádiz). La reforma ha sido estudiada y ejecutada por la empresa de Servicios Energéticos Cityhouse Spain, con sede social en Sevilla y para llevarla a cabo han elegido el sistema de bomba de calor Q-Ton de Mitsubishi Heavy Industries con CO2 como refrigerante.
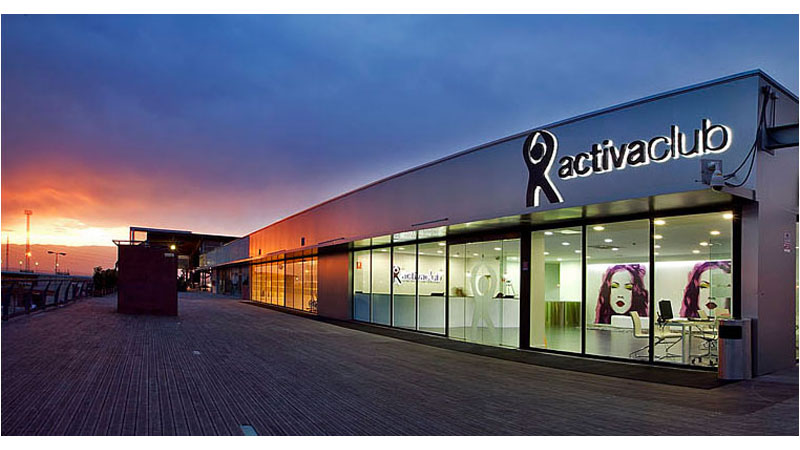
El Centro, antes de la reforma, disponía de un sistema de producción de ACS basado en dos depósitos de acumulación de 4.000 litros y 42 kW instalados de resistencias eléctricas.
El cliente buscaba una solución fiable, un ahorro en el consumo eléctrico de la instalación y un sistema de bajas emisiones de CO2 respecto al sistema actual.
Para el cálculo de la demanda energética para la producción de ACS se han tomado como referencia los datos de acceso para el día más desfavorable de todo el histórico del centro deportivo: un consumo por 21 litros/día ducha a 60°C y un factor de minoración a accesos medios del 80 %.
Este cálculo da como resultado una media diaria de 15.284 litros/día de ACS a 60°C con el siguiente perfil de consumo (figura 1):
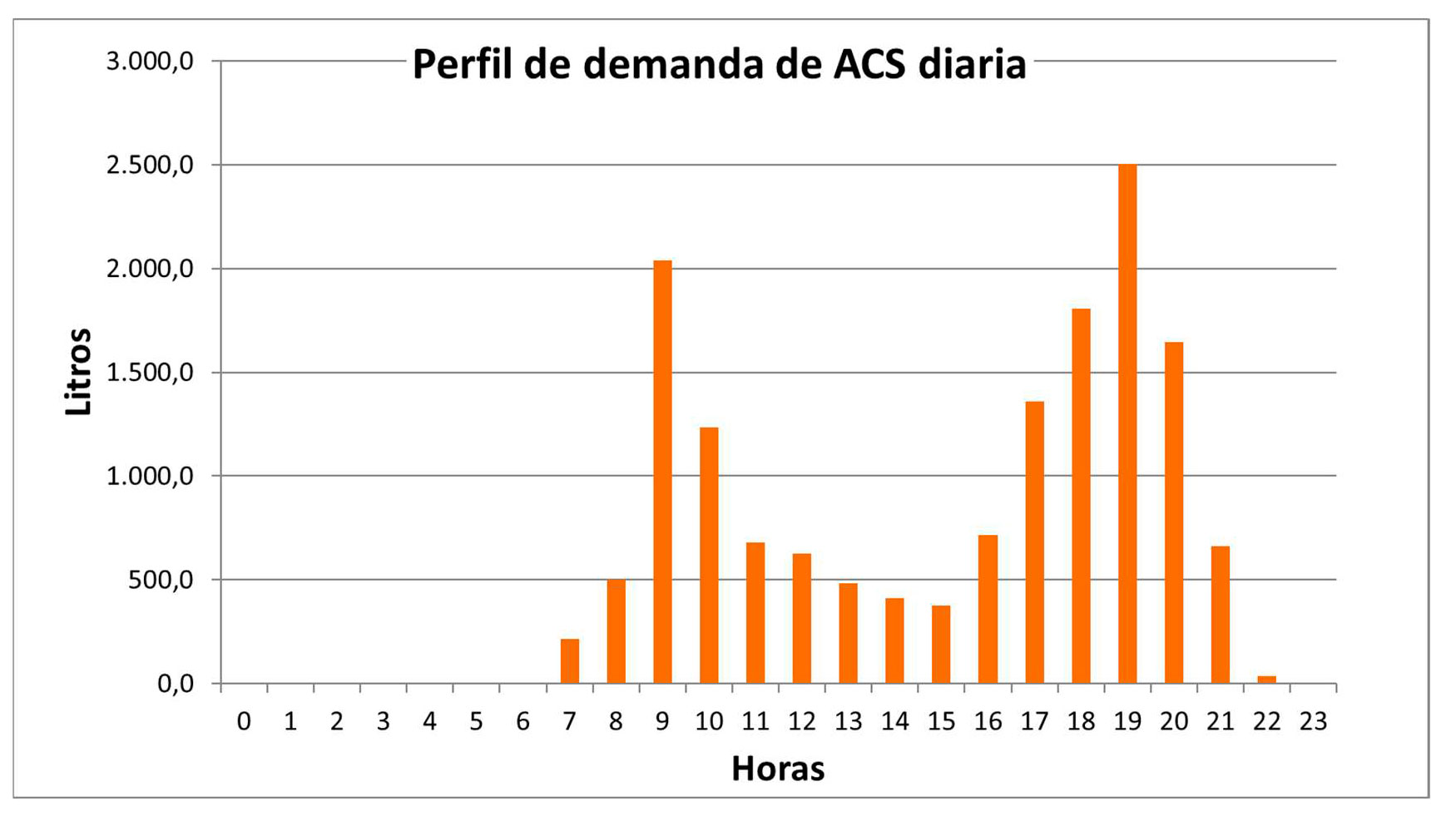
Figura 1
- Demanda de energía anual necesaria para el calentamiento de ACS: 288.531 kWh
- Pérdidas por distribución calculadas: 51.111 kWh
- Energía eléctrica anual consumida: 339.642 kWh
- Energía primaria anual consumida: 804.272 kWh
- Emisiones de CO2 anuales: 112.422 kg
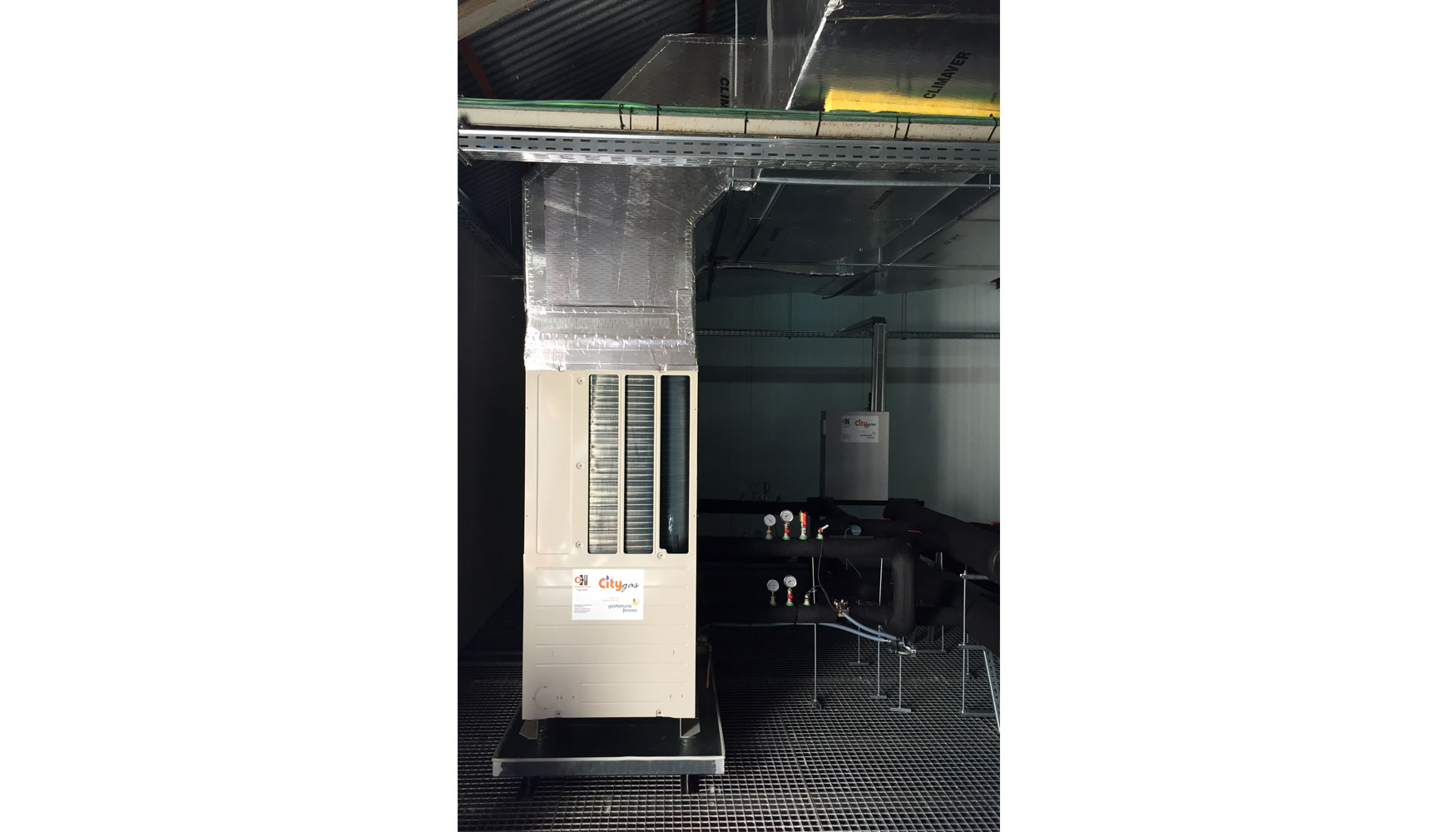
La empresa encargada de la instalación eligió el sistema bomba de calor Q-Ton de Mitsubishi Heavy Industries.
1. Sistema propuesto e instalado
La solución que propone la empresa de Servicios Energéticos es la instalación del sistema bomba de calor Q-Ton de Mitsubishi Heavy Industries con CO2 como refrigerante.
El estudio previo selecciona dos unidades Q-Ton de 30 kW para cubrir la demanda prevista de la instalación. El cliente exige una producción de 75°C para el agua caliente para eliminar cualquier riesgo de legionella en los tanques.
Con estas premisas el rendimiento anual estimado para el sistema propuesto es de: 3,86.
En la figura 2 vemos los rendimientos estimados por mes:
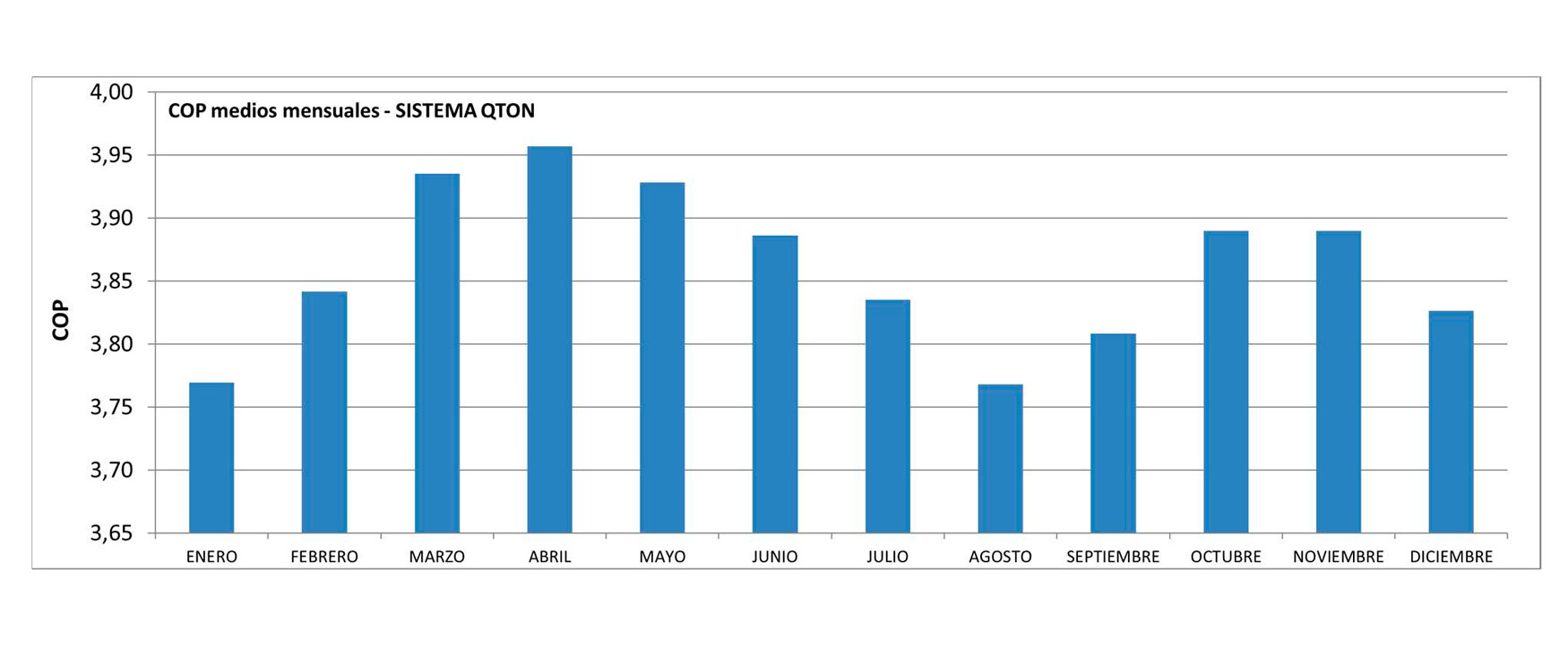
Figura 2.
El sistema estará formado por las dos unidades Q-Ton, un tanque estratificado de 4.000 litros que se sumará a los otros dos tanques de 4.000 litros existentes en la instalación, sondas y controles necesarios que se suministran junto a los equipos.
La distribución hidráulica del sistema queda como se refleja en la figura 3:
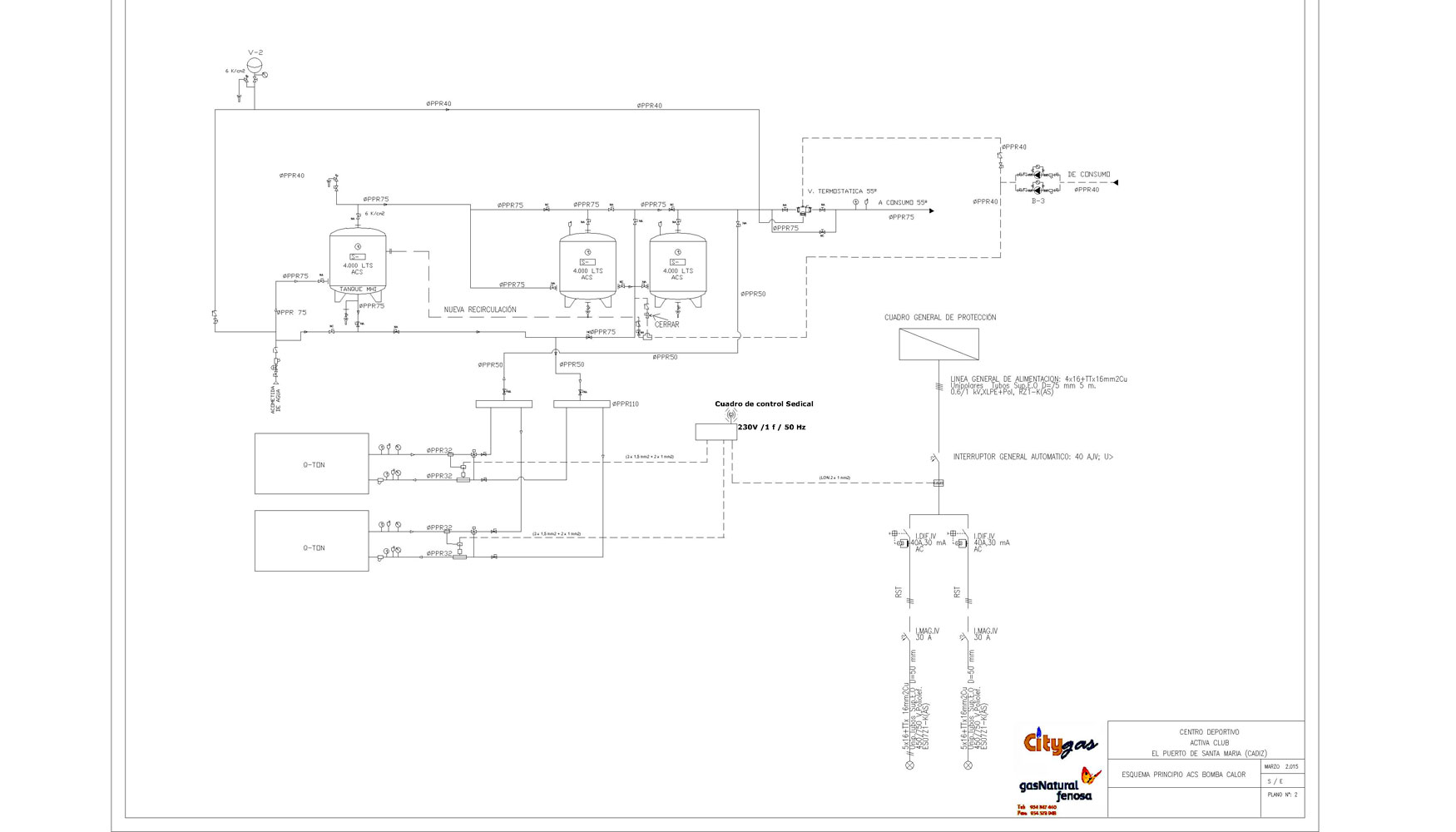
2. Energía anual consumida por la bomba de calor instalada:
- Energía eléctrica anual consumida: 87.990 kWh
- Energía primaria anual consumida: 208.360 kWh
- Emisiones de CO2 anuales: 29.125 kg
3. Balance final de consumos y emisiones de CO2
- Reducción de energía eléctrica anual consumida del 74 %.
- Reducción de energía primaria anual consumida del 74 %.
- Reducción de emisiones de CO2 anuales del 74 %.
4. Descripción de la tecnología
Tradicionalmente las calderas de gas o calderas de gasóleo han sido los principales sistemas para el calentamiento del agua caliente sanitaria, sobre todo para procesos donde la temperatura del agua oscila entre 70 y 90 °C.
Gracias a la nueva generación de bombas de calor de Mitsubishi Heavy Industries que utilizan como refrigerante el CO2 podemos alcanzar estas temperaturas de agua con un rendimiento global excelente y un potencial de calentamiento global (GWP) de 1.
En la Tabla 1 se compara las características del CO2 (empleado en este caso como refrigerante en bomba de calor para calentamiento de agua) junto con otro tipo de refrigerantes muy comunes en este tipo de instalaciones.
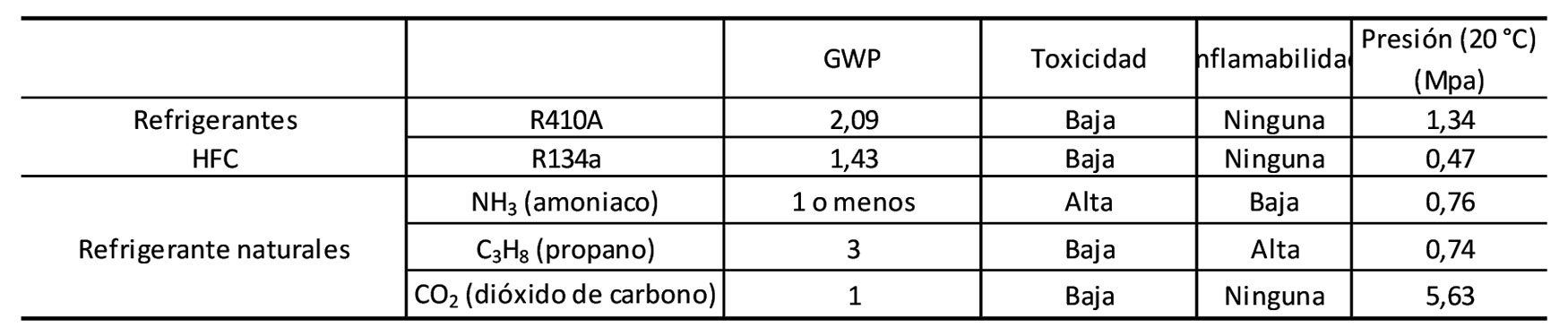
Según los datos mostrados en la tabla anterior, el CO2 utilizado como refrigerante presenta ventajas importantes: no es inflamable, baja toxicidad, temperaturas altas de trabajo que hacen posibles suministrar agua caliente hasta 90 °C y exento de tasas. Sin embargo, presenta el inconveniente de su alta presión de funcionamiento que provoca aumento de fugas internas y pérdidas mecánicas en su funcionamiento.
Este inconveniente se ha solucionado con el desarrollo de un nuevo compresor de dos etapas (compresores GSR) que mejora el rendimiento del equipo incluso con bajas temperaturas de aire exterior. El compresor se muestra en la Figura 4.
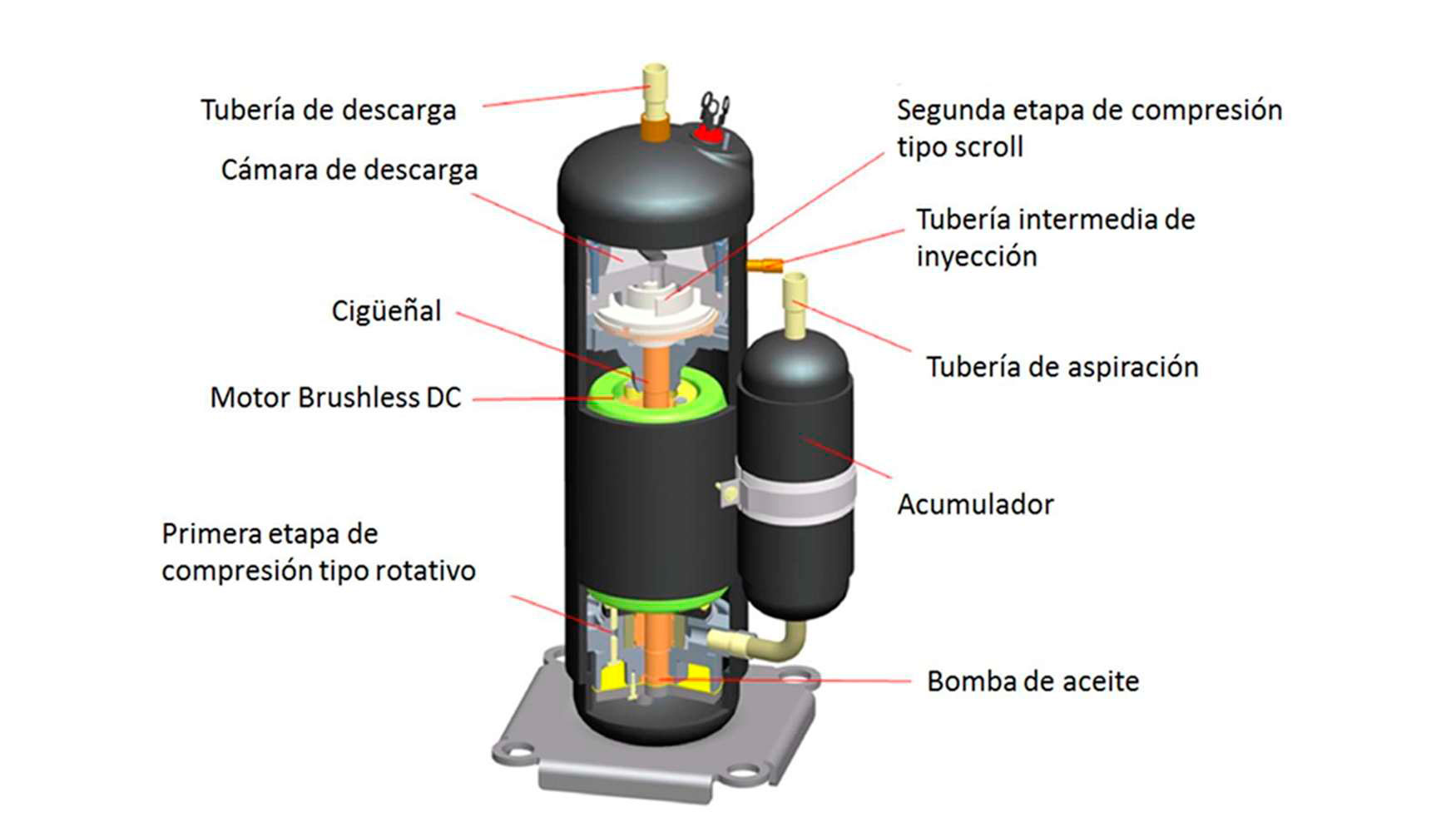
Figura 4
El compresor es accionado por un motor Brushless DC situado en el centro de éste con dos cámaras de compresión a ambos lados. La primera cámara, situada en la parte baja (aspiración del refrigerante), es un compresor rotativo que proporciona una eficacia de compresión alta a baja presión. La segunda cámara, parte superior del compresor (descarga del refrigerante), es un compresor scroll con gran eficiencia para relaciones de compresión elevadas.
La Figura 5 muestra el ciclo de refrigeración en el diagrama de Mollier utilizando un compresor del tipo GSR y en la Figura 6 mostramos el esquema frigorífico de los componentes y sus estados en el diagrama de Mollier.
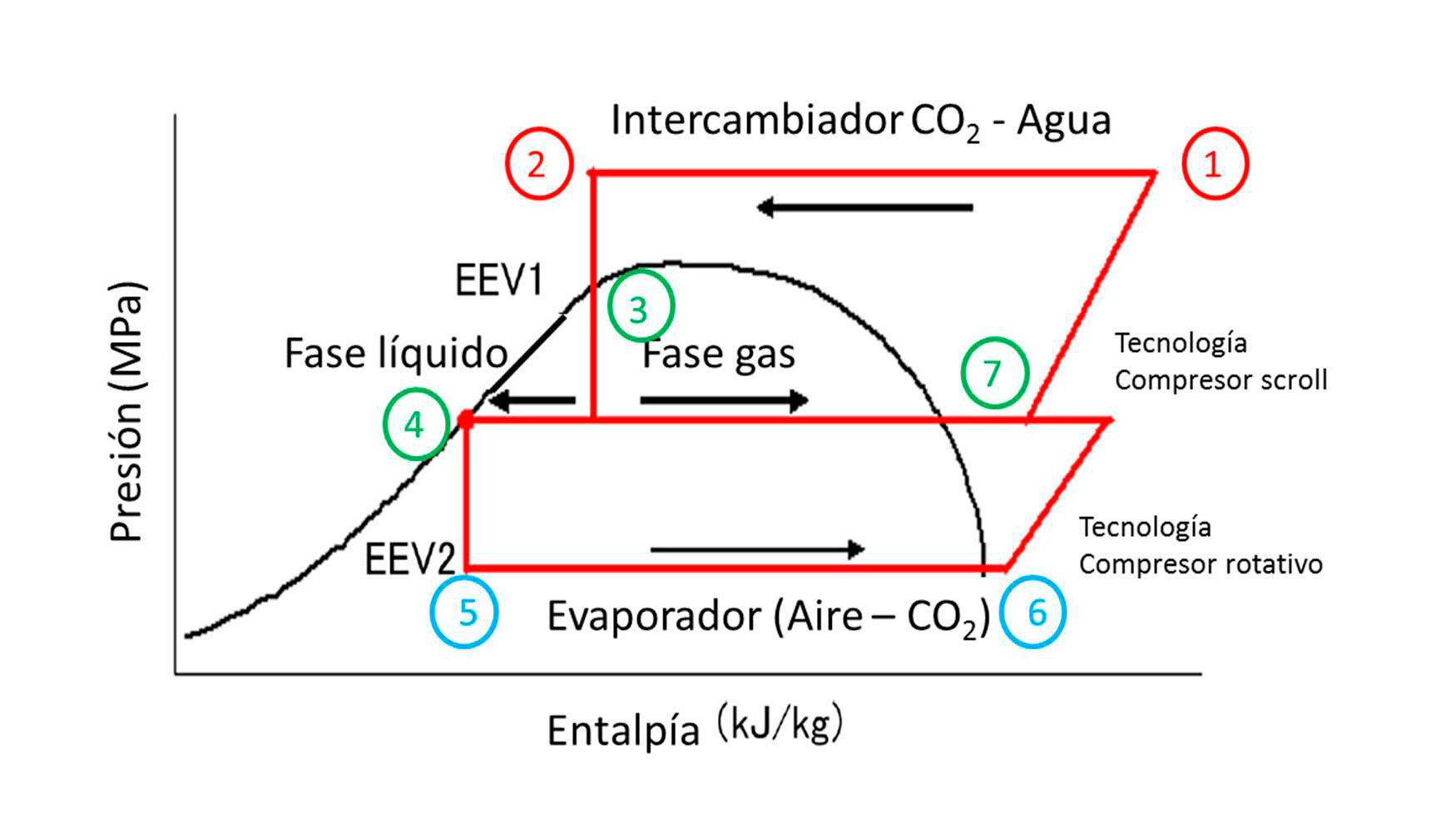
Figura 5.
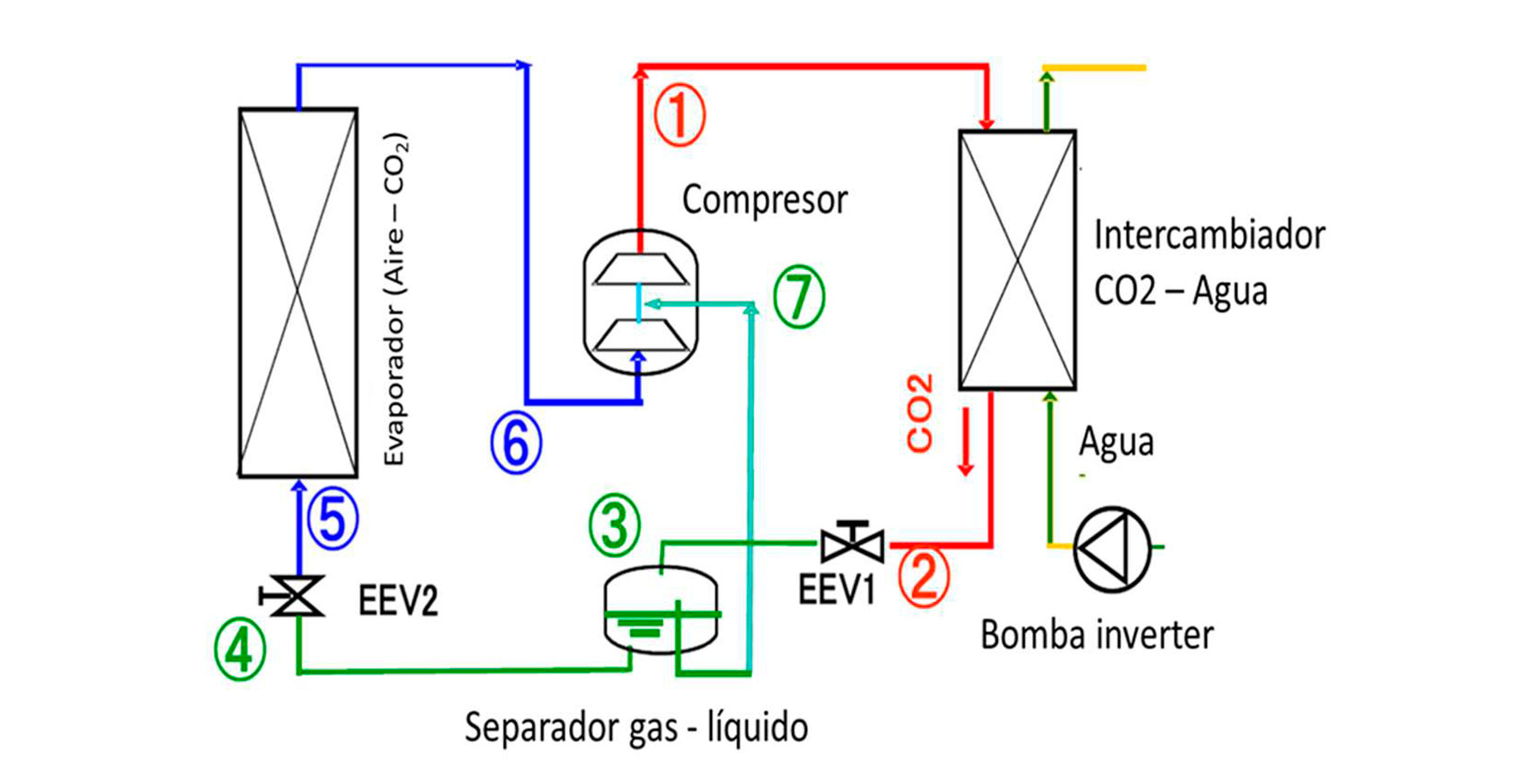
Figura 6.
El gas refrigerante procedente del evaporador se introduce en la cámara de compresión de la primera etapa a través del acumulador y es comprimido hasta una presión intermedia. El gas comprimido es entonces descargado dentro de la cámara de mezcla junto con el gas procedente de la expansión EEV1. Esta inyección de vapor tiene dos ventajas, por un lado, aumentar la capacidad del equipo en bomba de calor (incluso a bajas temperaturas) y otra ventaja que es la de disminuir la cantidad de refrigerante que pasa por el evaporador disminuyendo el consumo del compresor y por consiguiente el rendimiento del ciclo.
Esta mezcla es reconducida hacia la segunda etapa de compresión, donde se comprime hasta el valor de la presión de descarga.
La introducción de las dos etapas de compresión disminuye las diferencias de presión en cada etapa, aumentando de este modo la eficacia y fiabilidad.
Como ejemplo, destacar que con esta tecnología alcanzamos un COP de 4,2 con una temperatura exterior de 7 °C BS, una temperatura de agua de red de 5 °C y una temperatura de producción de 65 °C para el agua caliente sanitaria.
Etiquetado energético del sistema
Todos los productos relacionados con energía se han clasificado en LOTs por grupos de producto, con distintos criterios y plazos de aplicación. El LOT para la tecnología de ACS es el LOT 2 que engloba calentadores de agua a gas, calentadores instantáneos, termos eléctricos, bombas de calor de agua caliente, depósitos y sistemas solares.
El reglamento LOT 2 entró en vigor en fase voluntaria de transición el 26 de septiembre de 2013 y es obligatorio a partir del 26 de septiembre de 2015. Por tratarse de Reglamentos, son de obligado cumplimiento para todos los países de la UE. (No necesitan ser traspuestos a la reglamentación nacional).
Gracias a la tecnología del uso del CO2 como refrigerante combinado con la tecnología doble compresión descrita anteriormente, podemos encontrar en la etiqueta energética facilitada por el fabricante unos rendimientos COPDHW: Clima medio: 2,94 Clima cálido: 3,34 Valores que el usuario puede comparar con otras tecnologías de bomba de calor para producción de ACS.
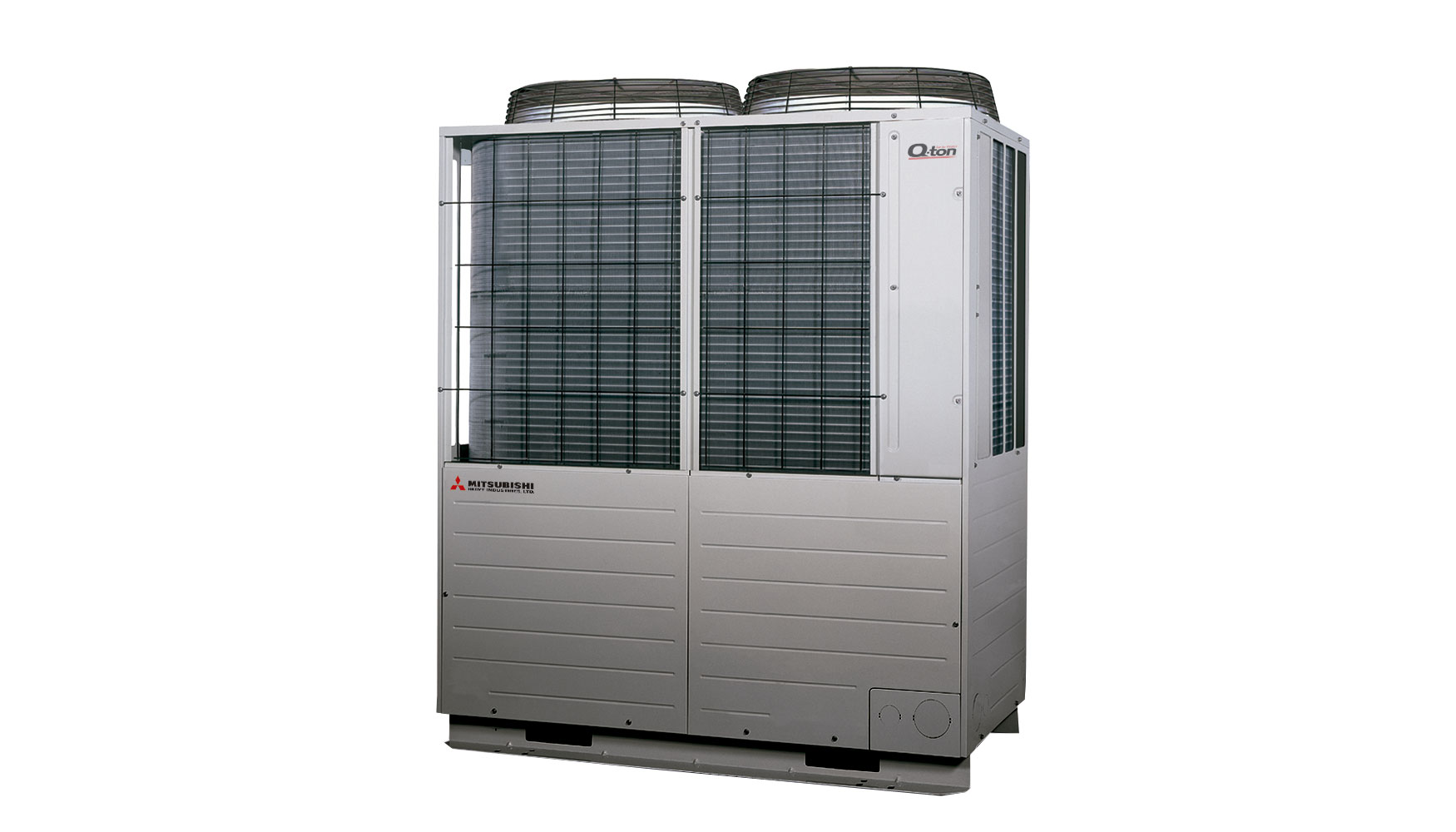