Validación del sistema INdeModular para palas segmentadas de mega aerogeneradores
La energía eólica se ha consolidado como la energía renovable de más rápido crecimiento en el mundo, propiciando el desarrollo de aerogeneradores de dimensiones cada vez mayores; de hecho, en la actualidad se están llevando a cabo varios proyectos para el desarrollo de máquinas de 10 MW con palas hasta 100 m de longitud. Esto está haciendo que los fabricantes de aerogeneradores se enfrenten a las limitaciones impuestas por las palas de gran longitud en relación a su fabricación, transporte y montaje.
Algunos fabricantes están desarrollando soluciones que permiten disponer de palas formadas por varias secciones, que son fabricadas y transportadas hasta el parque eólico por separado, procediendo a su ensamblaje in situ. Este tipo de palas, conocidas como segmentadas, facilitan la logística asociada a los procesos productivos y al transporte, posibilitando el acceso de palas de grandes dimensiones a parques eólicos con viales de acceso limitados, y evitando el traslado o duplicación de plantas de producción hacia otras zonas, tal y como ocurre en las aplicaciones offshore donde se tiende a localizarlas en zonas cercanas a puertos debido al tamaño de las palas.
Palas segmentadas
Las palas segmentadas son posiblemente la única solución para poder instalar parques eólicos en emplazamientos de acceso limitado como, por ejemplo, aquellos localizados en zonas de orografía compleja. Este tipo de palas dispone de un sistema de unión que le proporciona continuidad, tanto estructural como aerodinámica, en el empalme de sus segmentos. Como se muestra en la figura 1 si bien el coste de fabricación de una pala segmentada se ve incrementado respecto al de una monolítica debido a la incorporación del sistema de unión, es posible optimizarlo para que finalmente esté por debajo del 10%. Además, su impacto en el importe global de fabricación es menor, porque se ve compensado con una importante reducción en los costes de producción, ya que la pala segmentada requiere de moldes de menores dimensiones, cuya fabricación es menos costosa, se realiza en ciclos más cortos, y necesita una menor infraestructura en la planta de producción. En cuanto al transporte, la reducción de costes puede llegar a ser superior al 40% en las palas segmentadas dependiendo de su longitud. Por lo que, tras un análisis general, las palas segmentadas representan una solución técnica y económicamente viable con respecto a las palas monolíticas.
La mayor criticidad del sistema de unión se presenta en las zonas que otorgan una continuidad a los spar-caps, que son los componentes estructurales de la pala por los que se trasmiten las mayores cargas; este es el motivo por el que el desarrollo de los nuevos sistemas de unión se centran en esas zonas. La unión del resto de componentes, como conchas y largueros, es relativamente simple y conocida en la industria, estando resueltos en muchos de los casos mediante sistemas atornillados.
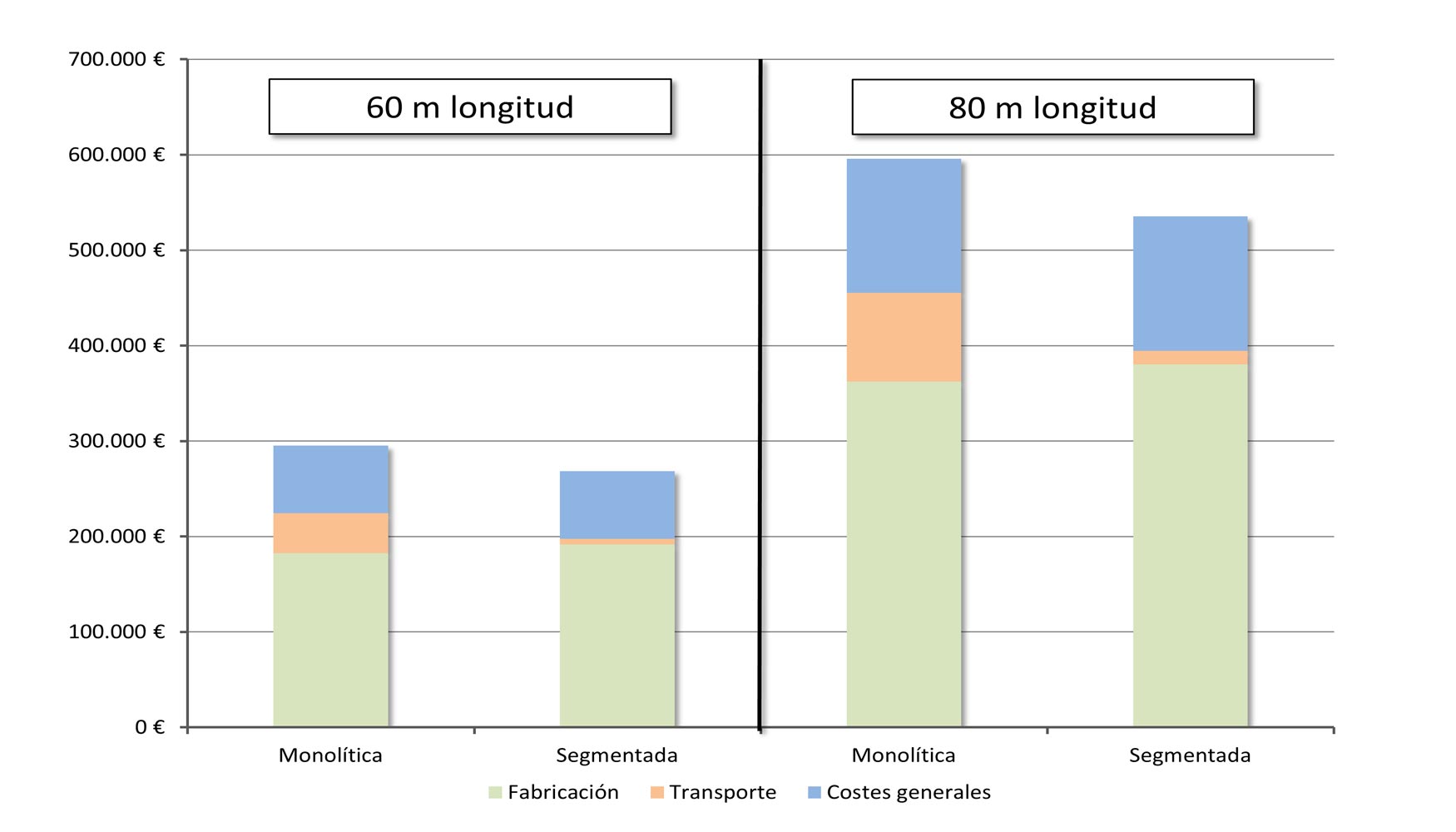
Existen dos grandes familias de palas segmentadas en función de la tecnología utilizada para unir los spar-caps (Figura 2). Por un lado, las que disponen de uniones atornilladas en las que el montaje se realiza mediante elementos metálicos roscados como espárragos, bulones o tuercas, siendo por lo tanto las más versátiles permitiendo, en caso de requerirse, el desmontaje completo de la pala; y por el otro, aquellas cuyas uniones son pegadas, donde las secciones se encolan entre sí. Las uniones pegadas suelen ser más ligeras que las uniones atornilladas, pero requieren el traslado al parque eólico de una compleja infraestructura para garantizar que el proceso de unión se realiza en condiciones controladas, alargándose el proceso de montaje y limitándose la capacidad de respuesta en caso de producirse algún tipo de problema durante el proceso, pudiendo ponerse en riesgo la integridad estructural y/o aerodinámica de la pala. A esto se une el hecho de que si a lo largo de la vida del aerogenerador se requiriera el desmontaje de la pala para su reparación en planta, ésta se tendría que cortar para poder ser trasladada, provocando que su reparación sea más costosa y de mayor dificultad técnica al tener que volver a unir sus componentes estructurales.
A la hora de decidir qué sistema de unión utilizar, el fabricante de palas debe considerar aspectos tales como la integración del mismo en el proceso de fabricación, el incremento en costes y la eficiencia en la transmisión de cargas a través de la unión, así como el efecto que tiene el aumento de peso en las cargas que soportará el aerogenerador y su posible impacto en la producción de energía eléctrica. También deberá asegurar que el sistema de unión garantiza la continuidad del sistema de protección contra rayos y deberá establecer los procedimientos para el montaje, la operación, el mantenimiento y el desmontaje de sus palas.
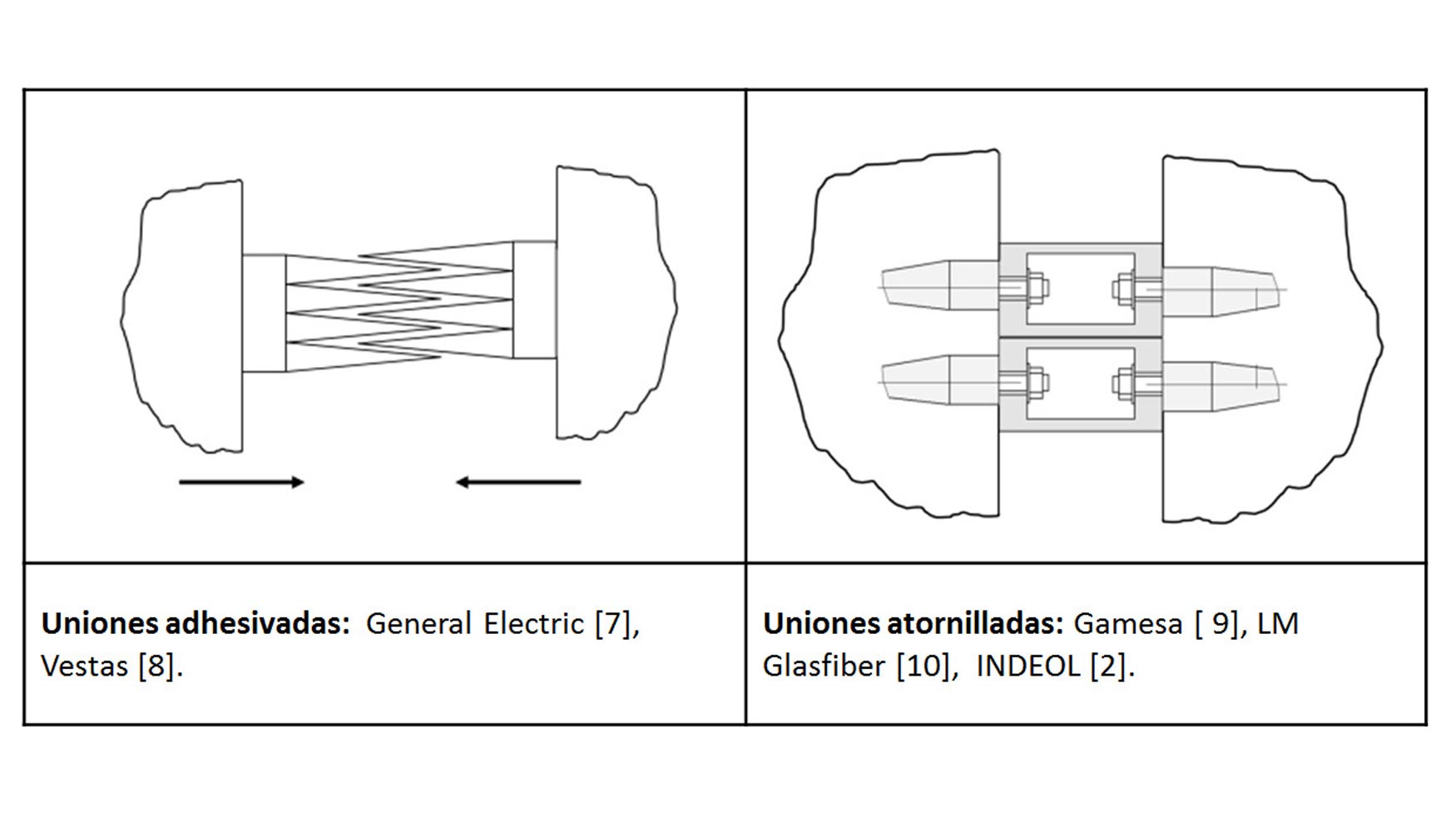
El sistema IndeModular
IndeModular es un sistema de unión atornillada para palas segmentadas. Fue creado y desarrollado para Indeol por el equipo técnico del Departamento de Energía Eólica del Centro Nacional de Energías Renovables (Cener). La tecnología IndeModular, que está patentada tanto en España como a nivel internacional, fue galardonada con el Premio Eolo de Innovación 2015 que concede la Asociación Empresarial Eólica española [1].
El sistema se localiza en el spar-cap de la pala y está basado en celdas unitarias que contienen placas intermedias y espárragos, con sus respectivos insertos, arandelas y tuercas. Los componentes de una celda unitaria se muestran en la figura 3. Los insertos, que se alojan en orificios practicados en el spar-cap a los que se fijan mediante adhesivo, tienen un agujero longitudinal con una zona roscada a la que se atornillan los espárragos. Éstos, a su vez, atraviesan la placa intermedia por sus respectivos agujeros, quedando el sistema asegurado mediante tuercas. La placa intermedia ha sido optimizada para acoger a los elementos de la celda y a la herramienta de apriete del sistema [2].
IndeModular se diferencia de otras soluciones en que, al alternar espárragos largos y cortos, permite reducir la distancia ‘d’ entre insertos (Figura 3) de tal manera que el sistema de unión puede acomodar un mayor número de espárragos y, en consecuencia, puede transmitir mayores cargas por ancho de spar-cap que las soluciones convencionales. Por otra parte, la placa intermedia presenta una alta capacidad resistente a fatiga ya que la precarga de los espárragos, gracias a su disposición alternada, hace que la misma trabaje principalmente a compresión [3].
![Figura 3: Diagramas de configuraciones de sistema de unión atornillada: IndeModular y solución convencional [3] Figura 3: Diagramas de configuraciones de sistema de unión atornillada: IndeModular y solución convencional [3]](https://img.interempresas.net/fotos/1179310.jpeg)
Figura 3: Diagramas de configuraciones de sistema de unión atornillada: IndeModular y solución convencional [3].
Diseño y cálculo estructural de la unión
a. Envolvente de cargas
Las cargas a transmitir por el sistema de unión fueron calculadas bajo la norma IEC61400-1 ed. 2 [4] sobre un aerogenerador de 5 MW viento clase II-A, con una torre de 120 m y palas de 61,5 m de longitud. Las cargas se obtuvieron en la sección de unión que, tomando en consideración criterios estructurales y logísticos, se situó a 30 m de distancia de la raíz de la pala.
Las cargas a extremas y a fatiga en los spar-caps, en la zona de unión, se obtuvieron a partir del máximo momento flector de solicitación y de la distancia entre las líneas medias de los mismos. A partir de las cargas por spar-cap, se obtuvo el máximo nivel de cargas a transmitir que se repartiría entre cada una de las celdas unitarias del sistema de unión. En la Tabla 1 se muestra la envolvente de cargas por celda unitaria.
Tabla 1: Envolvente de cargas por celda unitaria
Tipo de carga |
Envolvente de carga (kN) |
Extrema - Tensión |
+1.000 |
Extrema - Compresión |
-1.000 |
Fatiga (R=-1,0 // N=2E6 ciclos) |
+/-282,5 |
b. Cálculo estructural
Las cargas que soporta una pala se transmiten al sistema de unión a través de la capa de adhesivo que une los insertos al spar-cap, y desde allí se transfieren al resto de las piezas metálicas. Para el diseño del sistema de unión se llevó a cabo un cálculo estructural, tanto a carga extrema como a fatiga, sobre cada uno de sus componentes, utilizando la envolvente de cargas.
Las geometrías del inserto y del agujero en el spar-cap fueron diseñadas de manera que se redujeran los efectos de pelado que pudieran aparecer en la punta del inserto. Para el cálculo de las piezas metálicas se utilizaron tanto métodos analíticos como modelos de elementos finitos (FE). Estos modelos permitieron calcular el factor de reparto de los espárragos así como el efecto de flexión sobre los mismos debido a la forma de la unión. Además, se verificó la unión atornillada bajo los parámetros analíticos definidos en la norma VDI 2230 [5].
Los espárragos aseguran la continuidad de carga entre los insertos y la placa intermedia. Con objeto de evitar separaciones en los contactos entre estos componentes, con consecuencias críticas como pérdida de eficiencia en la transmisión de carga, los espárragos deben pre-tensionarse a un nivel de carga homogéneo y calculado de acuerdo a la norma VDI indicada. Para este caso, considerando las características de la herramienta de apriete, basada en torsión hidráulica, el nivel de precarga en los espárragos puede estar entre 470 y 564 kN.
Los resultados del análisis por FE del comportamiento de la placa intermedia frente a los valores máximos de fatiga se muestran en la figura 4, donde se observa concentración de tensiones en la zona del radio de acuerdo de la ventana interior de la placa, cuyo valor es cercano a 130 MPa. Teniendo en cuenta las prestaciones mecánicas de la curva de fatiga del material y las características superficiales obtenidas tras el mecanizado, este valor no resulta crítico tal y como se verificó durante el ensayo de validación del sistema.
![Figura 4: Modelo FE completo de la pieza intermedia para un nivel de carga de 282,5 kN (565/2 kN). Detalle de la zona crítica [6]... Figura 4: Modelo FE completo de la pieza intermedia para un nivel de carga de 282,5 kN (565/2 kN). Detalle de la zona crítica [6]...](https://img.interempresas.net/fotos/1179311.jpeg)
Validación del sistema
Para la validación del sistema de unión se fabricó un espécimen de ensayo que consistió en dos celdas unitarias cuyos insertos fueron pegados a dos paneles de laminado sólido que representaban el spar-cap de la pala. A continuación, para tener garantizada una superficie de contacto plana entre los insertos y las placas intermedias, se mecanizó la superficie exterior de los insertos quedando todos ellos incluidos en un plano.
Previo al montaje del espécimen, todos los elementos principales del sistema se instrumentaron usando galgas extensométricas; estos sensores permitieron obtener las deformaciones locales en determinadas zonas relevantes del sistema de unión, que habían sido previamente identificadas en el análisis por elementos finitos, con el objetivo de poder contrastar los valores de cálculo con los de ensayo.
Para validar el sistema de unión a cargas extremas y a fatiga, el ensayo se dividió en tres fases. En la fase 1 se aplicaron cargas de tracción y compresión hasta los 2 MN. A continuación, en la fase 2, se sometió el espécimen a una sucesión de ciclos de fatiga de +/-565 kN (R=-1) hasta llegar a los dos millones de ciclos. Finalmente, la Fase 3 consistió en una compresión hasta los 2,5 MN seguida por una tracción del espécimen hasta llegar a su rotura. El ensayo se realizó usando una máquina universal de ensayos de 3 MN y durante el ensayo se realizaron inspecciones, tanto visuales como con corrientes Eddy. En la figura 5 se muestra la configuración durante el ensayo de validación.
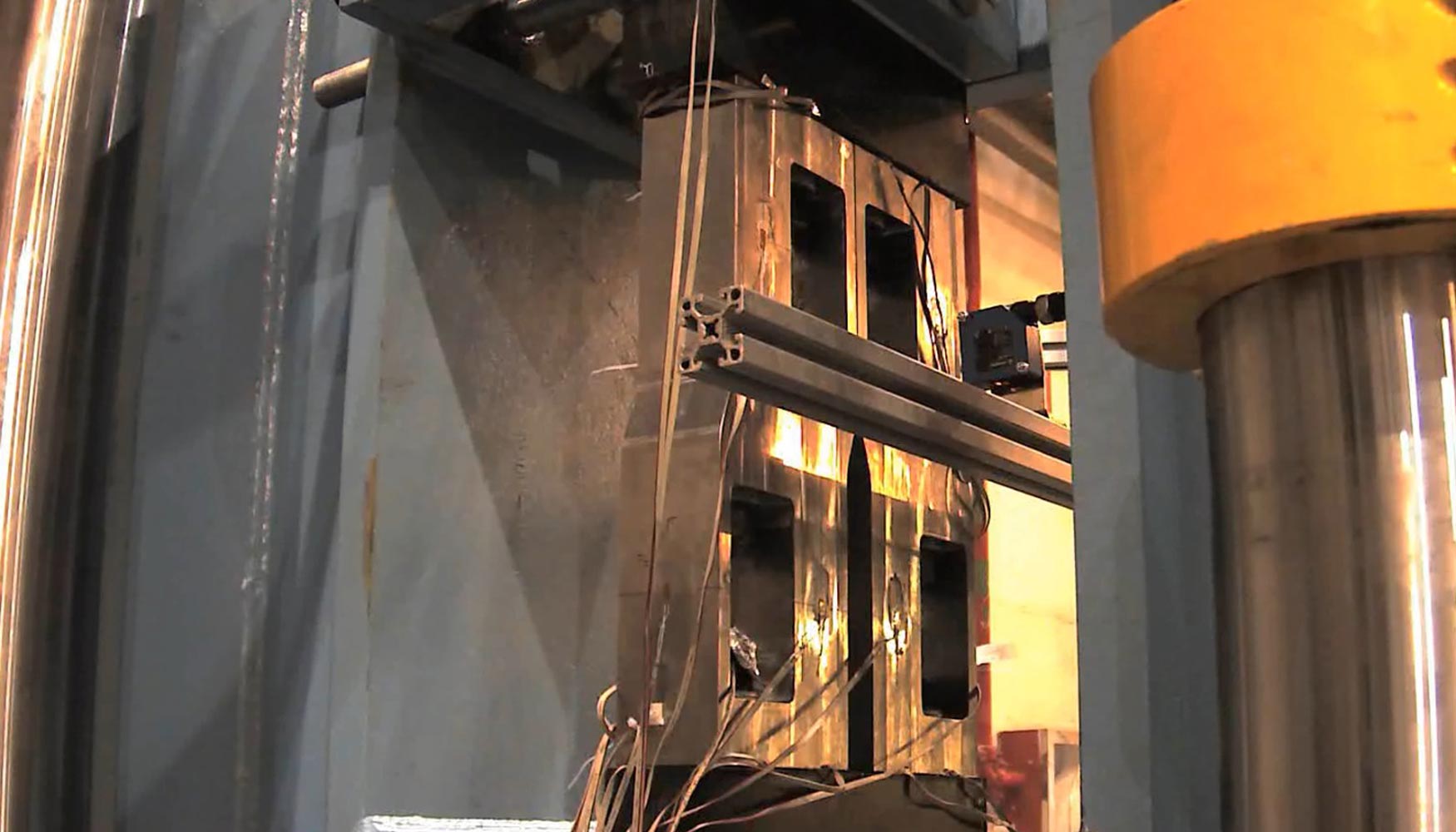
Conclusiones
El desarrollo y validación del sistema de unión atornillada IndeModular ha permitido obtener una solución competitiva para las palas segmentadas de aerogeneradores multimegavatio, resolviendo los retos tecnológicos asociados a la fabricación y transporte de palas de grandes dimensiones. El sistema facilita la fabricación de familias de palas, que únicamente se diferencian en zona de punta, y su fácil montaje y desmontaje posibilita el recambio de las puntas de las palas para su reparación o sustitución por nuevos diseños, sin tener que dañar las palas como ocurriría en el caso de los sistemas de unión adhesivada. No penaliza la aerodinámica de la pala y, gracias a su concepto de diseño basado en la modularidad, satisface la versatilidad de aplicación en diferentes longitudes y configuraciones de pala (como mono-larguero, bi-larguero o viga cajón).
Agradecimientos
El proyecto de desarrollo del sistema de unión recibió financiación del programa Innocash-2009 del Gobierno de España a través de la Fundación Española para la Ciencia y la Tecnología (FECYT), y del Gobierno de Navarra. Parte de la financiación se ha realizado gracias al Fondo Europeo de Desarrollo Regional (Feder) de la Comisión Europea. Asimismo, la solicitud de la patente española de IndeModular, así como su extensión en el extranjero, ha contado con financiación de la Oficina Española de Patentes y Marcas (OEPM) dentro de su programa para el fomento de solicitudes de patentes en España y en el exterior.
Referencias
- Asociación Empresarial Eólica. http://www.aeeolica.org/es/new/aee-otorga-los-premios-eolo-de-innovacion-y-de-fotografia-a-cenerindeol-y-a-vicente-guill/.
- Montejo R., Amézqueta C., Lahuerta F., Nuin I., Guelbenzu J., Sanz M., del Río M., Fariñas A., Sáenz E. System for joining component portions of wind turbine blades. INDEOL patent WO 2012/156547 A1.
- Sáenz E., Maruri J.M. ‘Desarrollo de palas segmentadas con tecnología IndeModular’. Eolus 75 (Septiembre – octubre): 6-12. (2015).
- IEC61400-1 ed.3. ‘Wind Turbines. Part 1: Design Requirements’.
- VDI 2230. ‘Systematic calculation of highly stressed bolted joints. Joints with one cylindrical bolt’.
- Sáenz E., Nuin I., Montejo R., Sanz J. ‘Development and validation of a new joint system for sectional blades’. Wind Energy, 18(3), 419-428. (2015).
- Arelt R. Method for producing a rotor blade, a corresponding rotor blade and a wind power plant. GE patent US 2006/0127222A1.
- Bech A. Wind turbine blades made of two separate sections, and method of assembly. Vestas patent WO 2006/002621 A1.
- Sanz E., Arocena I., Arroz S. Blade insert. Gamesa patent EP 2 138 716 A1.
- Rajamani R. Blade section for a wind turbine blade. LM Glasfiber patent. WO 2010/020692 A2.