Procesos de mezcla y granulación de sólidos
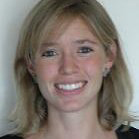
Uno de los problemas más evidentes de los materiales sólidos en forma granular o pulverulenta es la formación de polvo y su escape al medio ambiente. Así, uno de los retos de la industria es el diseño de plantas más limpias, minimizando las fugas de polvo y pérdidas de material. La formación de polvo además de la merma de producto y la formación de suciedad, tiene implicaciones en la salud laboral y en la temática Atex. Su progresiva resolución redundará en una mejor eficiencia y un aumento de la seguridad laboral y respeto del medio ambiente.
Otro reto es la consecución de sistemas de manipulación cada vez más automatizados y con una menor intervención humana. Se ha adelantado mucho en los últimos años, especialmente con el auge de los sistemas de transporte neumático, susceptibles de ser monitorizados, controlados y, por tanto, automatizados. También se ha avanzado en los sistemas de descarga de big bag, sacos y camiones cisterna.
El pesaje y la dosificación han conocido avances espectaculares los últimos años, con sistemas capaces de dosificar prácticamente en gramos y con el desarrollo de equipos que asegurar una dosificación continua y uniforme. Aquí el reto está localizado en conseguir que materiales muy poco fluidos, principalmente micronizados tipo harina, se puedan manipular tan fácil y eficientemente como un granulado tipo arena o azúcar.
En un orden de cosas más específico, nos queremos focalizar en dos procesos muy usuales y que han conocido desarrollos específicos durante los últimos años.
Mezcla
Uno de ellos es la mezcla de sólidos secos. Los retos en este proceso están mayormente relacionados con la eficiencia del proceso, la limpieza de los equipos y el consumo energético.
En términos de eficiencia, el advenimiento del mezclador neumático ha resuelto en gran manera las problemáticas relacionadas con el uso de mezcladores mecánicos convencionales. Uno es la capacidad del lote de fabricación, limitado en los sistemas mecánicos, debido a la configuración del depósito mezclador y de los elementos internos (palas, arador, etc) y las limitaciones en la motorización. El mezclador neumático puede realizar lotes de mezcla desde los 300 a los 50.000 kilos en el mismo depósito. Esta posibilidad de capacidad mezcladora conlleva ahorros de tiempo, al poder realizar la mezcla requerida en una sola operación en vez de dividirla en varias.
En cuanto a limpieza, el mezclador neumático es una alternativa óptima. Al ser básicamente un depósito (tipo silo o tolva) sin partes internas, una limpieza rápida y exhaustica se convierte en una tarea fácil. Esta característica es importante para la industria alimentaria y farmacéutica, pero también para la fabricación de pigmentos y aditivos alimentarios y cosméticos entre otros.
Para valorar el tema del consumo energético nos vamos a detener en el funcionamiento del equipo. Como hemos indicado, el mezclador neumático es un sistema que usa aire comprimido como fuerza motriz de la acción de mezclado, sin parte mecánicas internas en la cámara de mezcla.
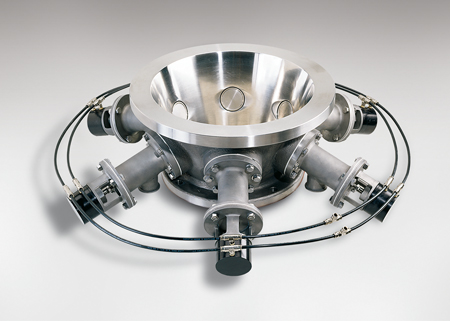
En el sistema mostrado en la imagen, la mezcla se realiza mediante pulsos de aire que se inyectan en el centro desde diversos ángulos, agitando los materiales suavemente en un movimiento convectivo, haciendo 'revolucionar' los materiales hasta conseguir el grado de mezcla deseado. Este sistema evita la instalación de un motor con una determinada potencia. El consumo energético está directamente relacionado con el consumo de aire comprimido. Como los pulsos de aire son a intervalos, la instalación de un depósito pulmón salva las puntas de demanda de aire, haciendo que el consumo energético sea altamente eficiente.
Granulación mediante Spry Dryer
Otro de los procesos que creemos que van a tener un gran desarrollo durante los próximos años es la granulación y secado por atomización mediante Spry Dryers. El secado por atomización, es una operación unitaria en la que una disolución o suspensión se transforma en un material granulado seco, manteniendo las propiedades físicas y químicas. Este proceso, tiene numerosas aplicaciones dentro de la industria química, farmacéutica y alimentaria entre otras. Para cada aplicación las características y propiedades del los materiales en polvo obtenidos son específicas y dependen de las condiciones en las que se lleva a cabo el proceso.
El principio básico de funcionamiento del Spry Dryer consiste en la dispersión de un líquido o slurry en una nube de pequeñas gotas a través de un disco giratorio o boquilla de inyección. Estas gotas se distribuyen en una cámara cilíndrica de secado donde se ponen en contacto con una corriente de aire caliente durante unos pocos segundos. Esto permite que se evapore el agua contenida en cada una de las gotas dejando la parte sólida diluida libre y preparada para ser recogida en forma de polvo.
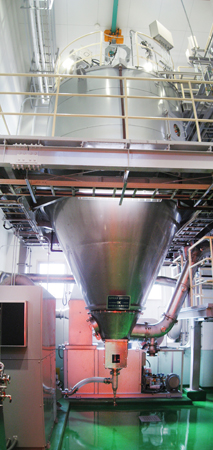
Spry Dryer.
Las diferentes características de materiales obtenidos varían según las características de la disolución de entrada, pero también, según las características del atomizador. La temperatura y la humedad relativa del aire de secado, el caudal, la presión de inyección, el diámetro de salida del inyector son variables que influyen en los resultados.
Las ventajas generales de este sistema de secado por atomización son, por un lado la garantía de que no existe deterioro en las propiedades del material debido a la temperatura y, por otro, la mayor uniformidad en el tamaño de las partículas obtenidas.
¿Qué hace que un Spry Dryer sea mejor que otro? La versatilidad de los atomizadores que permiten un rango mayor de resultados en un mismo equipo, la facilidad de mantenimiento y limpieza de los mismos y la posibilidad de poder trabajar en circuitos cerrados para solventes altamente inflamables.
Un ejemplo de conocimiento e innovación es el Spry Bag Dryer, puesto que la atomización, secado y filtrado de aire se realiza en un mismo depósito de tela de Nylon, fácilmente desmontable, reemplazable y lavable. Este sistema compacto tiene dos grandes ventajas frente a los sistemas convencionales. Por un lado, permite un claro ahorro de tiempo en el proceso de limpieza y por otro, la baja capacidad calorífica de la bolsa minimiza las pérdidas de energía y, por lo tanto, el ahorro energético se convierte en un factor destacable.
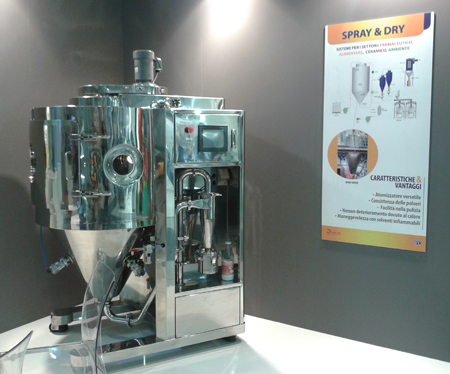
El objetivo común de todos los especialistas en el tratamiento de sólidos y pulverulentos es la óptima manipulación de los mismos, combinando la máxima eficiencia de proceso con la exigida calidad. Un enfoque orientado al valor proporciona eficiencias de producción y una fiabilidad de rendimiento a largo plazo. El equilibrio entre el conocimiento técnico y el pensamiento innovador es la estrategia para superar expectativas y obtener éxito.
Sobre Envisolid
La empresa Envisolid está especializada en soluciones para la manipulación de sólidos a granel y pulverulentos en los procesos de cribado, molienda, mezclado y valvulería. Su ámbito de actuación abarca todos los sectores industriales que manipulen sólidos granulados o pulverulentos, como la industria química, alimentaria, farmacéutica, de construcción, minera, energética, residuos y reciclaje, entre otras.