Automatización y nuevas tecnologías en la fabricación de palas
A finales del año 2010, la Comisión Europea de la Energía Eólica, la Wind European Industrial Initiative Team, lanzaba todo un programa de actuación entre los años 2010 - 2020, por el que se instaba a las empresas eólicas a desarrollar turbinas con potencias de hasta 25 MW. Dicho así, de pronto, cuando en el mercado se fabricaban turbinas de escasamente 4 MW, parecía una utopía, pero la Comisión Europea daba plazos y por supuesto ayudas para poder llevar a cabo este Programa. Se fijaba el período 2010 - 2012 para comenzar con turbinas de 6 MW para alcanzar los 7 MW en el año 2013. Hay que decir que estos plazos se están cumpliendo y que en la actualidad, estamos con aerogeneradores de 7 MW de potencia que implican palas de 83,5 metros de longitud, lo cual las convierte en las mayores piezas jamás construidas en materiales compuestos, o composites, y por sus condiciones operativas, trabajando en cantiléver o voladizo, con enormes exigencias estructurales.
Por mi formación y dedicación durante más de cuatro décadas al estudio, desarrollo y aplicación de los materiales compuestos fui convocado para analizar si podía aportar ideas que tuvieran como objetivo alcanzar esas metas, palas que deberían trabajar off- shore, salvo en ciertas zonas polares y terrenos clasificados.
Si actualmente las palas de 7 MW alcanzan una longitud de 83 metros es fácil deducir que las palas de las que hablamos podrían fácilmente alcanzar los 150 metros de longitud. No contemplamos la fabricación de palas de esta longitud en secciones, lo cual sería muy interesante. En esas dimensiones, la introducción de pernos y tornillos de amarre, con una densidad cuatro veces superior a las fibras y resinas empleadas, hacen muy complejo no sólo el equilibrado, sino también el comportamiento elástico en piezas programadas para alcanzar los 20 años de longevidad.
La Comisión Europea hacía hincapié en que habría que tener en cuenta dos parámetros importantes, digamos que imprescindibles:
- Pensar en nuevas tecnologías de fabricación.
- Máxima automatización en todos los procesos de producción.
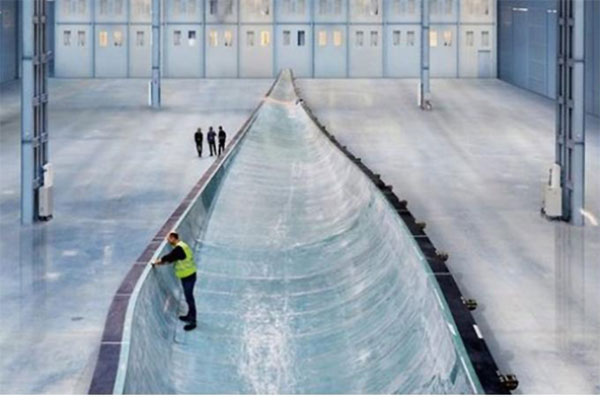
Fabricación de pala según un procedimiento actual. Corresponde a una de las conchas.
El desafío
Si bien en mi vida profesional he asumido en ocasiones verdaderos retos, éste en concreto, superaba todo lo imaginable. No olvidemos además que la Comisión Europea abre la puerta en años siguientes, a potencias de 40 MW, contemplando plataformas off-shore flotantes, con lo que la limitación de profundidad en fondos marinos no supone ya un obstáculo. De hecho, ya se está trabajando, incluso por empresas españolas, en este sentido.
Desde mi punto de vista, la inclusión del automatismo y robótica no ofrecía la mínima duda. En estudios llevados a cabo por empresas punteras, se demuestra que en los procesos actualmente en uso, el tiempo empleado en la colocación de refuerzos y unión de conchas y rigidizadores, alcanzan valores en torno al 60% en tiempo y mano de obra, a todas luces excesivo, eso sin tener en cuenta que en estos gigantes, la mano de obra lleva consigo:
- Baja capacidad de réplica
- Bajo control de proceso
- Costos elevados en la calidad
- Límites físicos en las personas.
Esto sólo en lo que afecta a la fabricación pura y dura, sin contar con recanteado, repasado, pulido, equilibrado, pintado y cable antirrayo, entre otros.
Resultaba evidente la introducción de autómatas en todos y cada uno de los procesos de fabricación, pero… ¿cómo deberían ser estos?
Experiencia aeronáutica
Mi paso por la industria aeronáutica, y sobre todo, el uso continuo y exclusivo de un robot en los años ochenta, trazó la línea a seguir.
En las palas, actualmente, hablamos de la concha superior o extrados y la concha inferior o intrados y se fabrican por dos procedimientos: Infusión y Prepreg. Atrás quedaron los procedimientos manuales de impregnación. Recuerdo con nostalgia los inicios de los años setenta en el Centro de Aplicaciones donde trabajaba y en el que tuve el placer de crear y dirigir, la fabricación de palas hasta 6 metros de longitud; eran los comienzos.
La infusión, extraordinario avance en la fabricación de composites, tiene para estas grandes piezas que han de producirse en serie industrial, bastantes limitaciones. No es lo mismo fabricar un velero de competición que palas en serie industrial: el tiempo de colocación de las diferentes capas de refuerzo, elaboración de la bolsa de cierre, red de tubos, aireadores, selladores y verificación de estanqueidad, además del tiempo consumido en la infusión (con las consabidas incertidumbres en el correcto mojado) lo hacen inadmisible. El tiempo de mano de obra y utilización de molde, penalizan fuertemente el proceso.
No quedaba otra alternativa que utilizar la vía del prepreg o preimpregnado, es decir, seguir los pasos marcados por la industria aeronáutica.
Nuevas tecnologías
La tecnología que vamos a describir muy someramente y que constituye el núcleo de la patente, se basa en tres patas fundamentales: Moldes, Prepreg y Automatismo. Explicaremos brevemente las particularidades de los mismos.
Comenzamos por diseñar un nuevo sistema de fabricación. En lugar de partir de dos moldes, concha superior o extrados y concha inferior o intrados, partimos de molde con borde de ataque incluido y otro molde con borde de salida o fuga incluido. Esto nos lleva a varias ventajas importantes:
- Supresión de la unión en borde de ambas conchas.
- Eliminación del adhesivo de uniónen dicho borde: costoso, lento de aplicación y pesado.
- Indudable mejora estructural, eliminando la temida apertura de conchas. Hemos creado una viga-cajón.
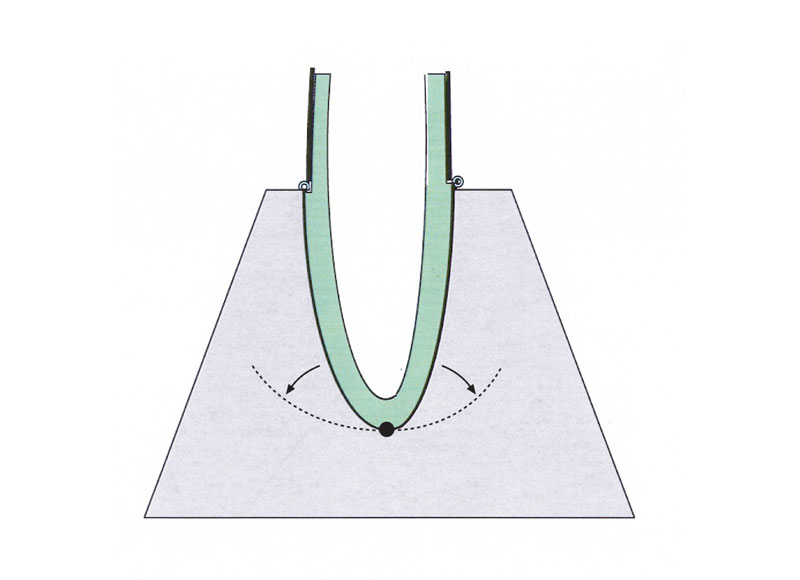
Elaboración de la parte correspondiente al borde de ataque de la pala.
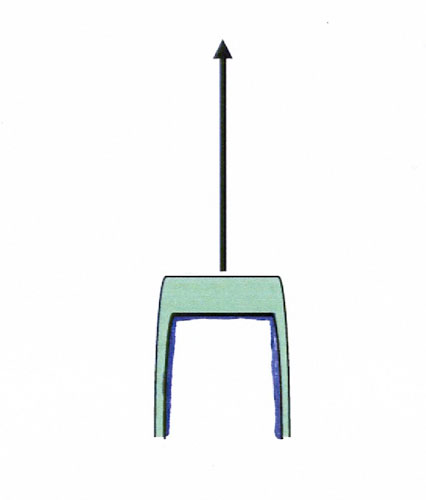
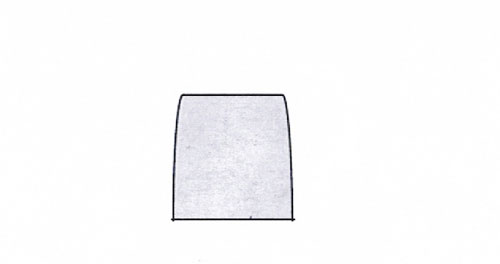
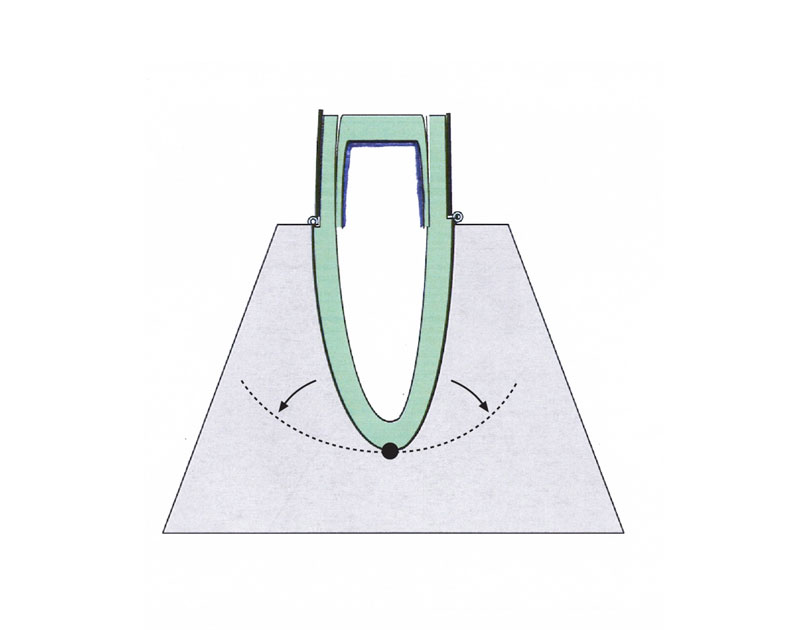
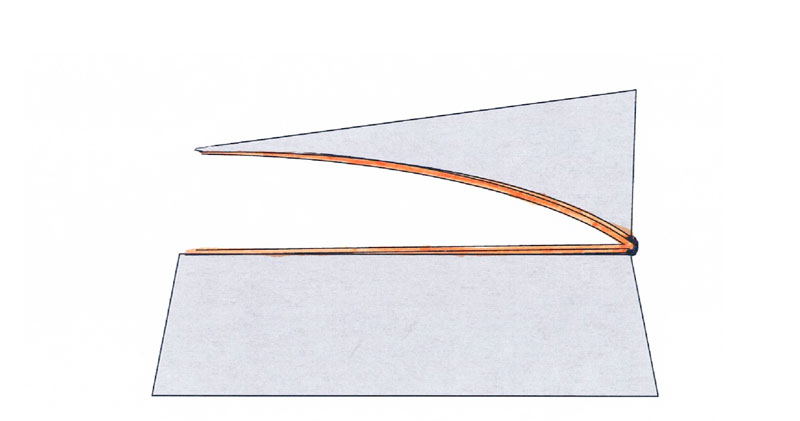
Forma final del prepeg que constituye el borde de salida todavía en su molde.
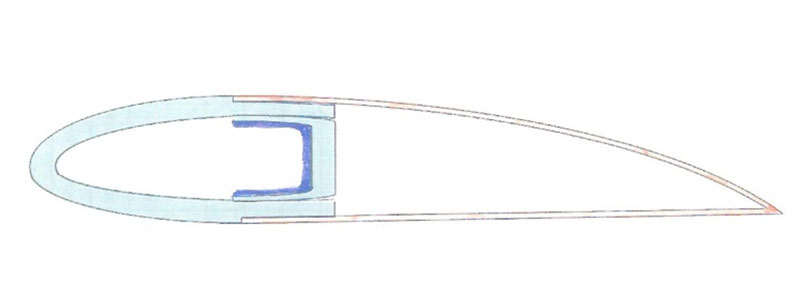
Vista en sección de una pala terminada. Obsérvense las tres piezas unidas por medio de la viga estructural.
Fabricamos además los girders o rigidizadores en sus respectivos moldes, que llevaremos a los dos moldes anteriores, borde de ataque y salida y curaremos el conjunto a un tiempo o cocurado.
Elementos innovadores
Este nuevo diseño incorpora elementos innovadores que expondremos muy brevemente:
- Diseño: la unión de las conchas no se hace en borde, sino en una parte de la sección de la pala, coincidente con el elemento rigidizador.
- Adhesivo: no se precisa. Eliminamos con ello tiempos, peso y costo.
- Prepreg: se extiende el prepreg con robot, eliminando tiempos de infusión con los riesgos de mojado y ganamos en volumen de fibra, siempre conveniente. Seguimos los pasos de la aeronáutica.
- Moldes: son de chapa metálica cortada con láser, conformada, pura calderería, calefactables, manipulables, en secciones, eternos.
- Automatismo: el proceso admite un elevado grado de automatización en las siguientes fases:
- Limpieza de moldes por láser,
- Desmoldeante,
- Gel coat,
- Lay up,
- Cierre de moldes,
- Desmoldeo,
- Mecanización de raíz de amarre,
- Lijado y limpieza superficial,
- Inspección,
- Medición,
- Pintado,
- Plataformas móviles para manipulación de palas.
- Estructura: no sólo eliminamos peso, sino que ganamos en estructura, evitándose el riesgo de separación de las conchas.
Medio ambiente
En el proyecto no hemos olvidado esta parcela, tan importante hoy en día. Desde hace unos años dedicamos tiempo y esfuerzo no sólo en resolver este problema, sino además, en resolverlo de forma rentable.
Las palas, sean del tamaño que sean, deben tener un final honroso y no depositarlas en vertederos o incluso enterrarlas. Si rindieron buenos servicios en vida, deben tener un final no menos digno y además aprovechable. Parodiando a nuestro querido Don Juan Tenorio: "Si buena vida os quité, mejor sepultura os di". Las palas que por las circunstancias que sean no sirvan, deben aprovecharse íntegramente y proporcionar beneficios. Lo primero que haremos es reducirlas de tamaño in situ, troceándolas, para seguidamente transportarlas a la unidad de aprovechamiento.
Diseñamos y patentamos una máquina que bautizamos con el nombre de 'Constrictor', móvil y autónoma, que reduce la pala en fragmentos transportables a una unidad de procesado. Esta unidad de procesado, es capaz de trocear y reducir a tamaños pequeños los composites y cualquier materia orgánica, los cuales generan en el caso de fibra de vidrio, material fundente en procesos industriales y en el caso de fibra de carbono, energía calorífica y sustrato carbonoso a emplear en procesos, hoy en pleno desarrollo. Los componentes metálicos como pernos, tornillos, cable de cobre, tienen muy buena aceptación en el mercado. Todo debe y puede ser reciclado con aprovechamiento económico.
Conclusión
Cuando un producto se presenta más ligero, repetitivo, fiable, con menor tiempo de uso de moldes y más económico, por fuerza ha de tener excelente acogida y perspectivas de mercado.
Esta tecnología expuesta que hay que desarrollar, comenzando como todo, por prototipos pequeños, puede aplicarse a otros campos de la ingeniería civil, como pasarelas, puentes, vigas, etc. puesto que su fundamento es muy simple.
Si Europa quiere ser competitiva frente a países emergentes, con mano de obra barata, no tiene otra alternativa que pensar en nuevas tecnologías y en automatización, ambas en nuestras manos.