Seguridad personal y protección medioambiental en el laboratorio
Las vitrinas convencionales provistas de conducto de evacuación al exterior fueron antiguamente importantes para la manipulación de grandes cantidades de productos o de productos difíciles de manipular. Sin embargo, estas ventajas se ven compensadas por desventajas como:
- La emisión de sustancias tóxicas a la atmósfera.
- Pérdida de aire calentado o enfriado por equipos de acondicionamiento.
- Necesidad continua de aire de reposición.
- Instalación difícil y costosa.
- La ausencia de movilidad y flexibilidad en la ubicación de la vitrina.
Para superar las desventajas anteriormente citadas es necesario considerar el uso de vitrinas de aspiración y filtración de gases –sin conducto de evacuación y con recirculación del aire– equipadas con filtros de carbón activo, que proporcionan protección a bajo coste sin emitir contaminantes a la atmósfera.
Las vitrinas de aspiración y filtración fabricadas por y con marca Cruma, empresa con más de 30 años de experiencia en el mercado nacional e internacional, están basadas en esta tecnología, garantizando la seguridad personal y la protección medioambiental en el laboratorio.
Para entender mejor los beneficios de las vitrinas de gases sin conducto de evacuación vamos a exponer cómo estas vitrinas filtran los vapores tóxicos, malolientes y/o contaminantes durante los procedimientos experimentales en el laboratorio.
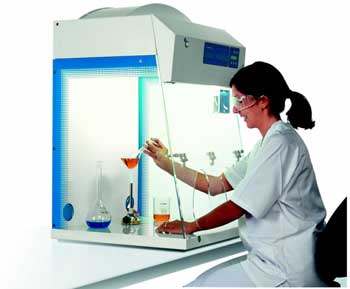
Tecnología de filtración
En general, se puede afirmar que moléculas con peso molecular superior a 30 y puntos de ebullición superiores a 60ºC son candidatos a la adsorción en filtros de carbón activo, aunque hay excepciones y combinaciones que deben ser particularmente evaluadas.
El principio fundamental en el que se basa la filtración de moléculas gaseosas es el concepto de adsorción. Los dos procesos que conforman la adsorción son la fisisorción y la quimiosorción.
La adsorción física (fisisorción) de las moléculas gaseosas se produce por difusión (Movimiento Browniano) o adsorción/condensación por Fuerzas de Van der Waals. Las moléculas gaseosas alcanzan los espacios vacíos entre las partículas de carbón activo y difunden hacia el interior de los poros de éstas. Atraídas y capturadas por las Fuerzas de Van der Waals, las moléculas penetran en los poros, chocan contra las paredes y son finalmente atrapadas. El número de poros presentes en el carbón activo es enorme y, en consecuencia, la superficie total que ofrece para el contacto es extremadamente elevada. La superficie específica es una medida del área superficial por unidad de masa, expresada en m2/g. Hay carbones que alcanzan los 2000 m2 /g.
El proceso físico en la adsorción es seguido por la adsorción química (quimisorción). Consiste en una reacción química entre el gas y el carbón activo cuyo producto de reacción queda unido por enlace químico al material activo. La impregnación química de carbones activos amplía el número de gases que pueden ser eliminados de la corriente de aire por este sistema.
Eficacia de adsorción o filtración
La temperatura de un gas es muy importante porque cuanto mayor es, menor es la capacidad de adsorción, especialmente en el caso de gases volátiles.
Además, las temperaturas altas pueden incluso propiciar una desorción parcial en la que el filtro “devuelve” a la corriente gaseosa parte de las moléculas previamente adsorbidas. Generalmente, la temperatura debe mantenerse por debajo de 40 ºC.
La humedad relativa es un factor importante que puede afectar a la eficacia del filtro. Las moléculas de gases con puntos de ebullición bajos serán peor adsorbidas porque en su lugar serán adsorbidas moléculas de agua dejando menos superficie libre en los poros para que las moléculas de gas puedan chocar y reaccionar. En general, la humedad relativa debe siempre mantenerse por debajo del 60 por ciento.
El tiempo de residencia es el tiempo que necesita el aire para cruzar el filtro durante el cual contacta con el carbón activo. O, dicho de otro modo, es el tiempo durante el cual las moléculas de gas pueden ser adsorbidas por los poros del carbón antes de abandonarlo. Este tiempo debería ser lo más largo posible. Para maximizarlo, el espesor del filtro debe ser suficiente y la velocidad del aire debe ser la mínima posible. Este mínimo está condicionado por la necesidad de asegurar que la velocidad en fachada garantice la contención y aspiración de los contaminantes.
Normalmente, el filtro, si no ha sido adecuadamente almacenado antes de su uso, pierde eficacia con el tiempo a consecuencia del envenenamiento debido a la presencia de gases en la atmósfera así como al efecto de la humedad ambiental.
La velocidad a la que los contaminantes son evaporados dentro de la vitrina así como la concentración de dichos vapores son dos factores que afectan negativamente a la eficacia del filtro.
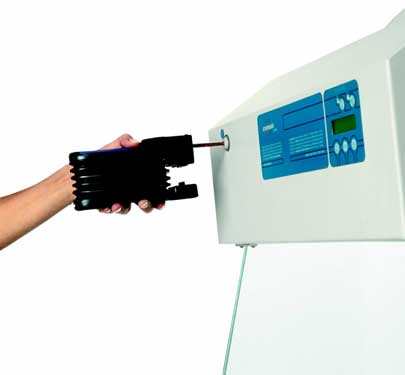
Seguimiento del filtro
- Control de la velocidad de flujo para asegurar que el prefiltro no está colmatado con polvo.
- Control químico del aire expulsado por la máquina para asegurar que el filtro principal de carbón activo no ha alcanzado la situación de “breakthrough” (aire que consigue atravesar el filtro sin que los contaminantes sean retenidos).
Las vitrinas Cruma van equipadas con un anemómetro que permite una lectura continua de la velocidad en fachada. Además, los cabezales llevan incorporado un sistema de toma de muestras que permite la extracción de aire filtrado para su análisis (fotografía 2)
La utilización de ventiladores centrífugos de alto rendimiento garantiza el mantenimiento del flujo cuando la pérdida de carga originada por el prefiltro aumenta.
La adsorción tiene lugar en una franja del lecho de carbón activo conocida como “zona activa de filtración”. A medida que el filtro va siendo usado y se carga de moléculas, la “zona activa” va desplazándose hacia arriba hasta que alcanza la parte superior del lecho, momento en el que se produce un “breakthrough” inicial a partir del cual el porcentaje de contaminantes gaseosos que escapan del filtro se incrementa. El seguimiento del filtro debería servirnos para detectar el periodo de “breakthrough” inicial y evitar así que se alcancen los Valores Límite de Exposición de los contaminantes implicados.
Filtros Hepa
El acrónimo Hepa procede del inglés “High Efficiency Particulate Air” y son conocidos como filtros “absolutos” por su elevadísima eficacia de filtración.
Están fabricados de papel de microfibras de vidrio en forma plisada o plegada. La técnica con la que se disponen estos pliegues es la que confiere la eficacia de separación de estos filtros. Los filtros Hepa empleados por Cruma son de clase H-14 según norma EN-ISO-1822, presentando una eficacia mínima, para partículas de 0,3 µm, del 99,995%. La categoría H-14 es la de mayor eficacia dentro del grupo Hepa. El siguiente filtro en eficacia es el U-15, que ya pertenece a la categoría de filtros Ulpa (ultraeficiencia), utilizados en aplicaciones muy especiales.
El tercer elemento filtrante es el prefiltro. Fabricado con biofibras sintéticas, de clase G4 (según norma En-1822) permite la retención del polvo atmosférico.
En la fotografía 3 se muestra la imagen de un cabezal de vitrina Cruma con todos los elementos que configuran el sistema de ventilación y filtración.
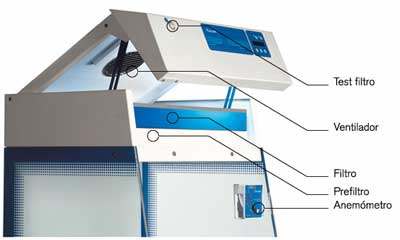
Tipos de carbón activo
- Tipo A: adsorción de vapores y disolventes orgánicos (cetonas, éteres, alcoholes, xilenos,…).
- Carbón activo sin impregnación.
- Tipo BE: gases ácidos inorgánicos como H2SO4, HCl, HNO3,… y compuestos volátiles de azufre (H2S, SO3,…). Carbón activo con impregnaciones de compuestos metálicos y sales neutralizantes.
- Tipo K: específico para vapores de NH3 y aminas. Carbón activo impregnado con complejos de sales metálicas.
- Tipo F: específico para formaldehído y derivados, impregnado con Cu.
- Tipo ABEK: tipo mixto entre los tipos A, BE y K teniendo la capacidad de retener moléculas pertenecientes a los 3 grupos. Impregnado con sales inorgánicas neutralizantes, sales y complejos metálicos y Cu.
- Tipos específicos: existe un filtro especial para Hg (tipo M).
Todos los filtros de carbón activo que equipan las vitrinas Cruma están impregnados, elaborados y testados de conformidad con la norma EN-141.