DMG MORI, with eight innovations, goes back to surprise in Pfronten
Is an already traditional event in the diary of many. Same stage, same dates, same leading. But very far to cause flat feelings in the visitors, the Open House that
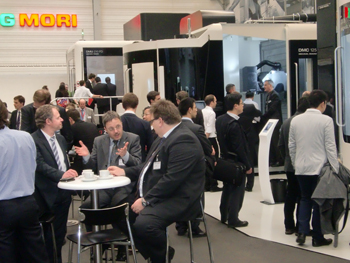
The first plane of the days of open doors was occupied by eight world-wide novelties with new corporate design Jealousies, that constitutes the most innovative road and fast to reflect an idea in a product finished. It offers a unitary interface for all the new machines of technology tip of DMG MORI and thanks to the app of Jealousies makes possible an administration, documentation and universal visualisation of data of requests, processes and machines. A total of 18 machines were instrumented with Jealousies.
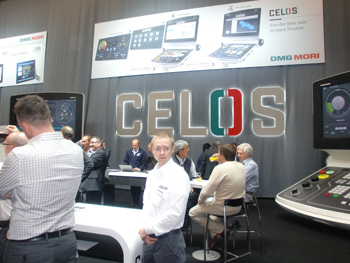
As already it has said , in Pfronten presented for the first time to the public eight world-wide novelties: the CTX beta 800 TC, the DMC 80 FD duoBlock, the DMC 80 H duoBlock (two machines more than the fourth generation duoBlock), the two new models DMC V 850 and DMC V 1150 to complete the series DMC V, the DMU 270 P, the DMU 70 ecoline and the Lasertec 65 AdditiveManufacturing. This last represents a technology that still is far to be strengthened in the industry but that offers some enormous possibilities. It is able to realizar milling demanding and a mechanised additive in an alone tie up of the piece. Common to all they was the corporate design Jealousies with ERGOline of 21,5 inches and control Siemens.
The Open House of this year centred fundamentally in the technologies and applications more advanced in the areas of matrices and moulds, mechanised of high speed and aerospace industry. Other thematic areas head offices were the mechanised XXL, the DMG MORI Automation and the Service Solutions.
Turning and milling in the CTX beta 800 TC
The new CTX beta 800 TC complete the program of machines “Turn&Mill” of DMG MORI in the area of small pieces until 500 mm of diameter and 850 mm of length of turning. The career of the axis And is of 200 mm. The central element of the machine is in the accionamiento direct of the axis B with a rank of twist in continuous of 110°. Said axis is instrumented with the new husillo of turning-milling ultracompacto, that, thanks to his compact construction and his integrated cylinder for decoupling of the baboon tool holders, allows to develop a pair of 120 Nm with his length of so only 350 mm. In comparison with a husillo conventional this gives place to a gain of space of work of 170 mm, having at the same time of a pair a 20 % upper. To this adds the saving of costs of tools, since it is possible to employ standard tools to the hour to mechanise surfaces and taladros oblicuos.
Of series, the machine with the Operate 4.5 on Siemens 840D solutionline is instrumented with the signpost of operator ERGOline of 19 inches. The options of application of the CTX beta 800 TC complete with 11 cycles of available exclusive technology like options. With his help can reduce the time of programming until 60% thanks to a simple programming.
Mechanised vertical with the special concept of the DMC 850 V / DMC 1150 V
After the presentation of the DMC 650 V in the fair EMO of Hannover, presented in Pfronten the DMC 850 V and the DMC 1150 V, two machines more than the third generation of this series of machining centres vertical. The powerful equipment includes a husillo of 14.000 min-1 and a table of fixed machine that in the case of the DMC 850 V admits a load of until 1.000 kg. The DMC 1150 V possesses even a maximum load of 1.500 kg. It can attain a mechanised productive thanks to his fast advances of 36 m/min in all the axles. Like novelty in this segment of machines stands out the refrigeration of the accionamientos and the guides. The nuts of the mechanisms of husillos of balls and the linear guides refrigerate by means of regletas of attack, evacuating of efficient way the heat of friction. The limits of route of the DMC 850 V situate in 850 x 520 x 475 mm. The DMC 1150 V has some limits of route of 1.150 x 700 x 550 mm and expands of practical way upwards, in particular with the 700 mm in the steering And, the range of machining centres vertical.
Can supply the two new machining centres vertical DMC V in his standard equipment with the ERGOline of 19 inches with control Heidenhain TNC640 as well as with Operate 4.5 on Siemens 840D solutionline.
The 4ª generation duoBlock: With 30% more than precision, performance and efficiency
With the successful universal centres of milling-turning of the series duoBlock, DMG MORI has forged of way determinant the development of the mechanised complete efficient. Likewise, the high percentage of models with cambiador of pallets has contributed to increase the degree of automation in the mechanised by start of shaving. This tendency is accompanied also by the fourth generation of the DMC 80 FD duoBlock. His cabezal of milling of the axis B again development offers a rank of twist expanded of 250°, with possibility to turn 70° in negative sense, whereas the greater dimensioning of the cojinetes of the axis increases in 20% the rigidity of the carcasa of the cabezal portafresa. Also the total rigidity of the DMC 80 FD duoBlock has increased in 30%, having reduced at the same time the necessary space. The new and innovative tool holders type films represents the most compact copy of the market. Like this, it has been able to reduce the width of the machine in until 41% in front of his predecessor.
Will be available with the numerical control Heidenhain TNC 640 or Operate 4.5 on Siemens 840D solutionline.
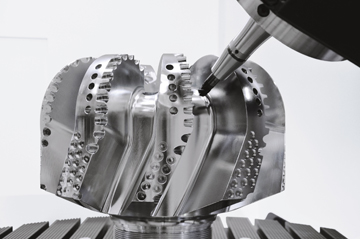
DMC 80 H duoBlock, for start of big volume of shaving and production in series
Also the most recent use of this robust base in the area of the machining centres horizontal again development shows the versatile that is the principle duoBlock of DMG MORI. The DMC 80 H duoBlock in his fourth generation has foreseen so much for the mechanised with start of big volume of shaving of high performance as for the manufacture of pieces in series with high productivity. The intense measures of refrigeration of all the accionamiento of advance ensure some values of precision with a provable improvement of 30%. Another advantage more than the principle duoBlock is the extensive and wide system modulate of complete solutions to measure that offer a wide fan of applications. Like this, the offer of husillos covers optimum variants for the start of big volume of shaving, standing out between these the husillo motorised powerMaster 1000, with a pair of 1.000 Nm to 9.000 min-1, and a husillo for multiplicador with a pair of 1.424 Nm to 8.000 min-1. To the equal that in the DMC 80 FD duoBlock, also in the DMC 80 H duoBlock employs the new warehouse tool holders type films with some very short times of change of tool of 0,5 seconds.
Is available with the control Heidenhain TNC 640 or with Operate 4.5 on Siemens 840D solutionline.
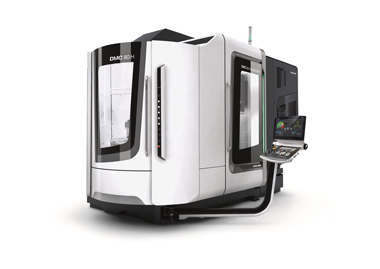
DMU 270 P: 235% more than space of work
In the series of machines of portico, the DMU 270 P constitutes a complement optimum with important advantages of space of work in front of the DMU 210 P of lower dimensions. His limits of route of 2.700 x 2.700 x 1.600 mm in the axles X / And / Z represent a plus of 50% in transversal steering and of roughly 30% in the longitudinal and vertical steerings. Therefore, the space of work sees increased in at all more and at all less than 235%. Likewise, they have optimised the outlines perturbadores since DMG MORI has developed a cabezal of milling totally new. In this way, the maximum size of piece situates in 3.000 of diameter and 1.600 mm of height with an admissible weight of 12.000 kg. The extremely elevated rigidity of the machine provides excellent values of precision.
DMU 70 ecoline – functionality and technology for mechanised in 5 faces
After the success of the DMU 50 ecoline, DMG MORI, in his segment of basic access, offers a new model of centre of mechanised in 5 faces of high precision DMU 70 ecoline. Therefore, the users that bet by price and quality have from this moment the possibility to mechanise by five sides also pieces of big dimensions: the DMU 70 ecoline offers visited of trip of 750 x 600 x 520 mm in X / And / Z. The round table giratoria controlled by CN (with a rank of twist of -10° until +95°) possesses a surface of tie up of 800 x 620 mm of diameter and admits a load until 350 kg. Besides, said table has of accionamientos digital and of an inmovilizador hydraulics of the table. His husillos motorised of 12.000 revolutions as well as fast advances of 24 m/min in his linear axles guarantee an impressesive development of power, whereas the warehouse of chain of tools, with 32 places for tools with carry SK40 and a double mordaza fast, offers the necessary versatility. To this adds that the DMU 70 ecoline is instrumented with a 3D quickSet for the review and correction of the cinematic of the machine and prepared for the automation.
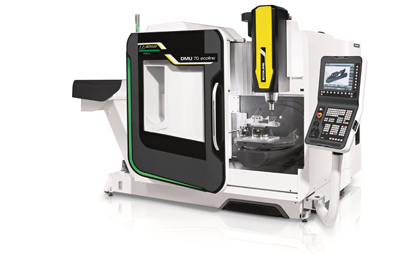
Mechanised by milling and additive in an alone tie up of the piece
The production generativa offers new options to face up to a high complexity and individuality in the production, having observed that the market of additive methods grows ininterrumpidamente. This hybrid machine of DMG MORI combines the milling with the welding of recargo by laser to make possible the mechanised additive. The conceptual study of the Lasertec 65 AdditiveManufacturing is based in a DMU 65 monoBlock and has been developed by Sauer Lasertec in Pfronten in collaboration with DMG MORI of United States. In this method employs a process of recargo by means of filter of metallic dust that it is until 20 faster times. The machine is besides instrumented with a laser of diodes of 2 kW for the welding of recargo by laser, combining in this way the milling compact in five axles with the welding of recargo with metal. They can process all the common metallic dusts like steel, nickel, alloys of cobalt or brass. Also it is possible recubrir the material sustrato with a protection antidesgaste harder. An advantage of this method is the possibility of recargar successively layers of different materials. To continuation, the distinct layers can mechanise by start of shaving with precision before the points in question, like consequence of the geometry of the piece, leave to be available for his mechanised with a strawberry or other tools.
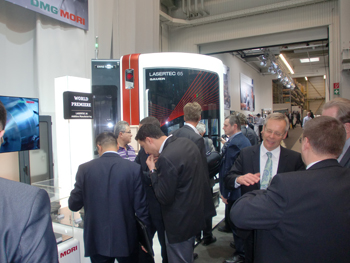
In the integral pieces, in which nowadays it starts by milling 95% of the material, can recargarse material by additive methods only there where need . Therefore, the loss of material reduces to 5%. The conceptual study showed can manufacture pieces until 500 mm of diameter, 360 mm of height and a maximum weight of 1 t. Nevertheless, it fits to imagine the production of pieces of dimensions even very upper. The start of the production in series of the Lasertec 65 AdditiveManufacturing is foreseen for autumn of 2014.