Husky va más allá de las palabras en el moldeo por inyección
Husky15/09/2004
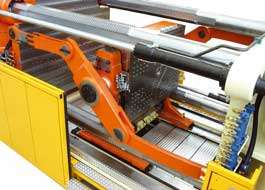
Máquinas Hylectric de 120 a 1000 toneladas
Combinan la eficiencia de un husillo eléctrico con la velocidad y la presión de una inyección hidráulica. Esto reduce los costes energéticos sin perjudicar el rendimiento de la máquina. Gracias al almacenamiento y al suministro de energía mediante acumuladores, el sistema hidráulico permite satisfacer los picos de energía exigidos y movimientos del plato a elevada velocidad, necesarios para una inyección económica.
La máquina Hylectric incorpora platos Reflex que permiten distribuir de forma uniforme las fuerzas de cierre en toda la superficie de montaje del molde. Ello permite reducir las fuerzas de cierre hasta en un 50 por ciento. La ubicación de las vigas de la unidad de cierre por fuera de las columnas aumenta la rigidez de la unidad, lo que permite mejorar el apoyo de los moldes pesados y reducir el desgaste de los mismos.
La mayoría de transformadores han invertido más en moldes y utillajes que en maquinaria. La Hylectric ha sido diseñada para espaciar más los intervalos de mantenimiento regular y prolongar la duración de vida de los moldes. Uno de los clientes de Husky consiguió reducir el mantenimiento del molde en por lo menos 12 veces respecto a una máquina de la competencia utilizada con anterioridad.
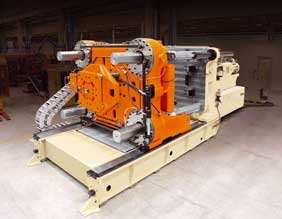
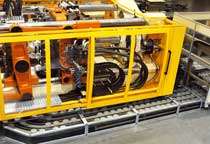
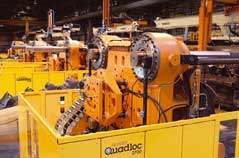
Máquinas Quadloc: de 1.350 a 8.000 toneladas
Las máquinas Quadloc pueden estar equipadas con el sistema de soporte multi-molde Tandem de Husky, lo que permite que dos moldes individuales puedan funcionar en una configuración de molde apilable.
El sistema Tandem ofrece varias ventajas:
- Permite casi doblar la producción de una máquina con una inversión inferior de capital que para la adquisición de dos máquinas
- Permite reducir el espacio en el suelo de aproximadamente el 40%
- Permite reducir la energía requerida por pieza producida
Además, racionaliza la producción para una gama de productos y consume generalmente un 15 por ciento menos de energía.
Automatización incorporada de SwingChutes
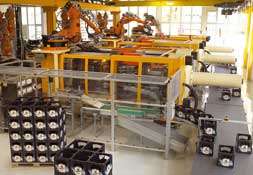
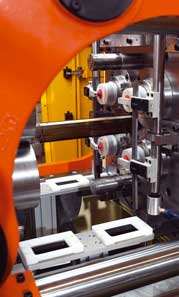
Un ejemplo de mejora de la productividad
Para demostrar su enfoque satisfactorio de soluciones, Husky propone un proyecto piloto que supone la integración en el sistema de una máquina de 600 toneladas con un molde apilado de 2x16 y un robot de entrada lateral para la producción de recipientes HIPS.
El objetivo principal consiste en probar la función y rendimiento del sistema como unidad completa. El tiempo de ciclo que había que conseguir tenía que ser inferior a los 5,2 segundos al 95% del tiempo de funcionamiento de la máquina sobre 24 horas. El proyecto también proporcionó una oportunidad de optimizar y establecer una ventana de proceso.
El tiempo de ciclo inicial era de 4,9 segundos. Sin embargo, se consideró que el sistema podía ser mejorado. El programa de la máquina fue actualizado para iniciar el cierre del molde antes del retroceso total de los expulsores. La lógica del expulsor ha sido cambiada para comprobar las posiciones del expulsor unos milímetros antes de que el molde esté totalmente cerrado. Mangueras hidráulicas de mayor capacidad para los expulsores han sido añadidas en el lado fijo. El tiempo de ciclo fue rebajado a 4,5 segundos.
La integración estuvo terminada en tres semanas. Todas las mangueras y conexiones fueron preparadas durante la integración para acortar el tiempo de instalación en el sitio del cliente. Una vez instalado, el sistema funcionó a pleno rendimiento, bajo la supervisión de personal cualificado desde el primer momento. Se estima que se ahorraron tres semanas en el proyecto.
Dada la reducción del tiempo de ciclo, los ahorros de tiempo para alcanzar la producción total y una disminución de mermas gracias al desarrollo de una vasta ventana de operación, este cliente consiguió recuperar en 3 meses el importe de la integración del sistema.
Etiquetado dentro del molde
El motor principal de este crecimiento es la posibilidad de diferenciar mejor los productos mediante una decoración de elevada calidad. En algunos casos, el etiquetado integrado en el molde ha incrementado directamente el volumen de ventas de más de un 30 por ciento. Husky, junto con el suministrador Hekuma de equipos automatizados en el molde, ofrece ahora un enfoque automatizado llave en mano para el etiquetado incorporado en el molde.
Paredes gruesas para cosmética
Husky ofrece una solución llave en mano para la producción de envases de cosmética de pared gruesa, basada en sus máquinas Index de moldeo por inyección. Esta solución permite a los fabricantes acortar los tiempos de ciclo, reducir los desechos y alcanzar niveles de rendimiento más elevados.
El tiempo de ciclo típico de una máquina convencional con evacuación robotizada de la pieza de plástico de 50 ml de capacidad, (con un grosor de pared de 6mm), oscila entre los 55 y 60 segundos. En un sistema Dual Index de Husky, la evacuación de la misma pieza oscila entre los 25 y 30 segundos.
Moldes apilados
Husky ha implementado con éxito un programa de sistemas Hylectric 1000 en un importante fabricante mundial de productos domésticos. Entre ellos se encontraba una H1000 que utilizaba varios moldes apilados de dos niveles para la producción de recipientes y tapas. Para resumir, la H1000 utilizaba tres moldes para recipientes (dos de 2x6 cavidades y uno de 2x4 cavidades) y dos moldes para tapas (uno de 2x6 cavidades y uno de 2x4 cavidades). Se consiguieron ciclos impresionantes en menos de ocho segundos.
Aunque el sistema apilado con obturador es una opción económica, previamente estaba limitada a diseños que requieren cavidades desplazadas en todas las líneas de separación. Las nuevas boquillas Ultra de Husky con instalación simplificada de platos han permitido la utilización de diseños adosados.
Al igual que los sistemas apilados con obturador desplazado, los sistemas adosados pueden ser diseñados con las boquillas Ultra 500, Ultra 750 o Ultra 1000. Los sistemas varían entre 2x1 para piezas grandes con punto de inyección en el centro y 2x12 para componentes más pequeños.