Compatibilidad del biobutanol con materiales poliméricos en motores de gasolina
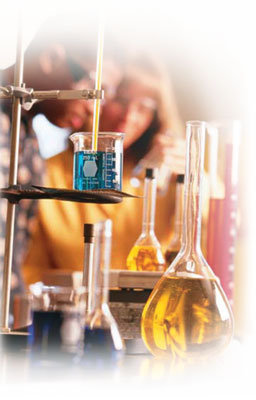
1. Introducción
El desarrollo de nuevos combustibles menos contaminantes es una prioridad en la actualidad debido principalmente a dos motivos: el primero es la necesidad de disminuir los productos contaminantes emitidos por los automóviles y el segundo disminuir la dependencia del petróleo, combustible fósil contaminante. En la actualidad esta dependencia por parte del sector transporte es prácticamente del 98% siendo además este sector responsable de un 25% de las emisiones de gases de efecto invernadero. Los biocarburantes constituyen la alternativa más factible a corto-medio plazo para lograr reducir la dependencia energética de los combustibles fósiles y las emisiones derivadas producidas por los mismos. La nueva Directiva de Energías Renovables marca como objetivo obligatorio para 2020 una cuota del 10% de biocarburantes que sustituyan a los carburantes fósiles en el transporte por carretera.
Tradicionalmente los dos biocarburantes más utilizados en el sector de la automoción han sido el bioetanol y el biodiesel para su empleo en motores de gasolina y diesel, respectivamente. Sin embargo la naturaleza química del bioetanol hace que presente una serie de limitaciones que hacen que sea necesario tomar ciertas precauciones tanto durante el proceso de mezclado, como en la distribución del producto final en las terminales de venta de combustible.
Un biocarburante que podría complementar e incluso sustituir al bioetanol es el biobutanol. El biobutanol se plantea como uno de los más prometedores biocombustibles de 2ª Generación ya que puede ser mezclado con gasolina y es perfectamente compatible con la tecnología de vehículos existente y con la infraestructura actual de distribución de combustibles.
En la actualidad se utiliza, como promedio, un 14% en peso de plásticos en la fabricación de un automóvil (Sector del plástico en España-Octubre 2008). El resto de materiales son el acero con un 60%, la fundición con un 9%, el aluminio con un 7%, los elastómeros con el 4% y el vidrio con el 3%.
Los plásticos son utilizados en la fabricación de sistemas de combustible ya que en comparación con los metales son más ligeros, lo que supone un ahorro de combustible, se ajustan fácilmente y hacen posible complicadas geometrías en las tapas de los depósitos, tanques, válvulas, juntas y otros componentes del sistema de alimentación del combustible.
Los materiales utilizados en la producción de piezas para los sistemas de combustibles tienen que cumplir una serie de requisitos que hacen que pocos materiales puedan ser utilizados en esta aplicación. Tienen que funcionar correctamente y no degradarse en un plazo de tiempo superior a diez años en presencia de productos agresivos como son el gasóleo, gasolinas y biocombustibles. Deben ser estables dimensionalmente, retener sus propiedades mecánicas de forma que soporten cargas físicas y vibracionales y evitar micropérdidas de combustible a través de pequeñas fisuras. Entre los materiales más utilizados figuran el PP, alrededor del 35% total de plásticos, la PA, el PUR, el PBT-PET, y el PC.
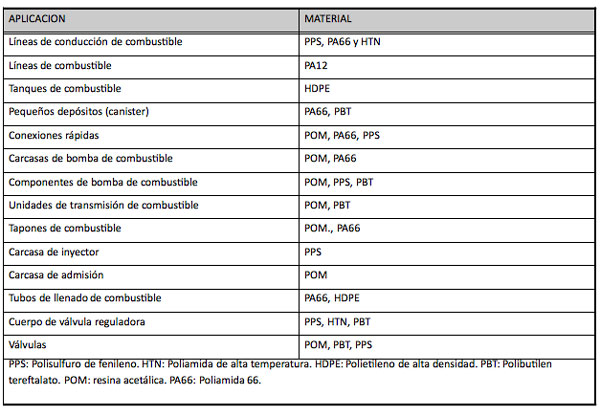
2. Procedimiento experimental
El desarrollo de estos nuevos combustibles nos lleva a la necesidad de probar su compatibilidad con los materiales que se utilizan en la actualidad en los sistemas de combustible de los vehículos.
Con este trabajo se va a estudiar la compatibilidad de los materiales poliméricos que se encuentran en el sistema de combustible tras introducirlos en mezclas gasolina, bioetanol y biobutanol a una temperatura de 30 °C y durante 2.000 horas de exposición. Para ello se han seleccionado los materiales que se utilizan en la actualidad en la fabricación de sistemas de combustibles y se ha procedido a analizar las muestras a 0 horas, 1.000 horas y 2.000 horas para poder estudiar los efectos de los combustibles en las diferentes propiedades de los materiales.
2.1. Materiales
Se ha valorado el comportamiento de materiales termoplásticos y elastómeros Los materiales termoplásticos estudiados para la realización de este trabajo son los siguientes:
• PA66
• POM
• HDPE
Estos materiales son los más utilizados en la fabricación de piezas para el sistema de combustible de los automóviles, el HDPE se utiliza en la fabricación del depósito de gasolina y la pipa de llenado, el POM se utiliza en la rampa de inyección y la PA66 en los enganches rápidos que unen los tubos de combustible con otros tubos o con distintos componentes del sistema de combustible.
En el caso de tubos de combustible y juntas se ha realizado una fase de prospección de materiales. En esta fase se han seleccionado los 5 modelos de coche más vendidos durante el año 2009 y hasta junio del año 2010 según los datos publicados por Aniacan.
Las juntas de los inyectores y tubos de combustible fueron adquiridos en los distintos concesionarios a partir de los modelos de automóvil seleccionados. Para la identificación de los elastómeros y termoplásticos se ha empleado un espectrómetro infrarrojo FT-IR (Spectrum 100 Perkin Elmer). La porción elastomérica se analiza por pirólisis siguiendo las especificaciones de la norma UNE 53 633:1991. Los resultados obtenidos para cada referencia se muestran a continuación
Tras analizar los resultados obtenidos se ha decidido utilizar las siguientes piezas en la realización del proyecto:
• Juntas de manguito pipe de FKM
• Manguera del evaporador de NBR
• Tubo de combustible de PA6/PA12.
El estudio se lleva a cabo con los siguientes combustibles:
• Gasolina calidad invierno
• BioButanol
• Bioetanol
Las mezclas de combustible a utilizar, basándose en diferentes estudios y análisis de estabilidad, fueron los siguientes:
• Gasolina 100%
• BU30. Mezcla de 30% de butanol con gasolina
• E10BU15. Mezcla de 10% de etanol, 15% de butanol y gasolina.
La primera condición servirá como testigo de una posible degradación, admitida por los fabricantes, de los componentes en el uso convencional, mientras que las dos restantes supondrían los ensayos a realizar sobre los componentes en situaciones más agresivas (BU30) y menos agresivas (E10BU15).
2.2. Métodos
Las propiedades a determinar han sido las siguientes:
2.2.1.1. Variación dimensional
El ensayo ha consistido en exponer las probetas de los distintos materiales de peso y volumen conocidos a la acción de las distintas mezclas. El porcentaje de variación dimensional fue calculado utilizando los valores previos a la inmersión y los valores tras la inmersión. Para ello se utilizó una balanza de precisión (METLER AT261 Delta Range) y un equipo de determinación de densidad de sólidos.
2.2.1.2. Resistencia al impacto Charpy
El método se utiliza para el estudio la fragilidad o tenacidad de los materiales en unas condiciones de ensayo definidas. La flexión Charpy se realiza sobre 3 puntos, aplicando la fuerza en el punto central de la probeta. Los parámetros obtenidos en ensayos de impacto permiten diferenciar entre plásticos en función de su distinta sensibilidad frente al impacto. El método consiste en que una probeta colocada horizontalmente entre sus apoyos, se golpea mediante una sola oscilación de un percutor, estando situada la línea de impacto equidistante de los apoyos, y se curva a una velocidad elevada y nominalmente constante. El ensayo se ha realizado con Péndulo de impacto Ceast 6963 siguiendo las indicaciones de la norma UNE EN ISO 179-1.
2.2.1.3. Ensayos de resistencia a la tracción y alargamiento
En el ensayo de tracción las características del material se determinan aplicando una fuerza constante a velocidad elevada de forma que la tensión sea homogénea en el eje a lo largo de toda la sección. Los principales parámetros que se pueden determinar son:
- Resistencia a la tracción en el punto de rotura (r): Esfuerzo en tracción soportado en el momento de rotura de la probeta.
- Resistencia a la tracción (M): Esfuerzo máximo en tracción soportado por la probeta durante el ensayo de tracción.
- Deformación (): Incremento de la longitud por unidad de la longitud inicial de referencia, como relación sin dimensiones o en porcentaje.
Los parámetros obtenidos en el ensayo de tracción proporcionan aspectos importantes de la resistencia y el alargamiento de los plásticos. Los ensayos de tracción se han realizado en una máquina de tracción universal Zwick según ISO 5893 equipada con un extensómetro de contacto según ISO 5893 y mordazas de Autoapriete a una velocidad de ensayo de 50 mm/min según norma ISO 527-96 en el caso de los materiales termoplásticos y a una velocidad de 200 mm/min según norma UNE 53510:2001 en el caso de los elastómeros y de los tubos de PA6/PA12.
2.2.1.4. Determinación de la dureza
Se define como dureza Shore la resistencia contra la penetración de un cuerpo de forma determinada a fuerza de presión definida. La escala de dureza comprende un alcance desde 0 hasta 100, donde 0 corresponde a la menor dureza y 100 a la mayor.
En función de la dureza del material se determina la dureza Shore A o Shore D. Ambas se han determinado en un equipo Bareiss U72/80E según las instrucciones de la norma UNE-EN ISO 868:1998, con un tiempo de espera de 15 segundos. Las medidas se han obtenido directamente de las piezas. La dureza Shore A fue determinada en las probetas de las juntas de inyector de FKM y los tubos de caucho de NBR/CR. La dureza Shore D en el caso de los materiales termoplásticos (PA66, HDPE y POM) y tubos de PA6/PA12.
Las probetas de los distintos materiales fueron introducidas en botes de PE y cubiertas con el tipo de combustible correspondiente a cada ensayo (gasolina, BU30, E10BU15).
Los botes fueron introducidos en una estufa antiexplosiva(Thermo Scientific Heraeus) a la temperatura adecuada (30 °C).
A continuación fueron sacadas del líquido, limpiadas y acondicionadas durante 24 horas a las condiciones del recinto de ensayo (23 °C y 50% de HR) antes de ser ensayadas (0 horas, 1.000 horas, 2.000 horas).
Los ensayos han sido realizados en el laboratorio de materiales poliméricos de FUNDACIÓN Cetena-Cemitec (UNE-EN ISO/IEC 17025). Los materiales termoplásticos (PA66, HDPE y POM) fueron procesados por inyección y probetas del tipo 1A fueron obtenidas. Los tubos de PA6/PA12, los tubos de caucho NBR/CR y las juntas de FKM fueron troquelados en una prensa manual y se obtuvieron probetas del tipo 3 según la norma UNE 53510:2001.
3. Resultados
Una vez ensayadas las probetas en los distintos intervalos de tiempo en las siguientes gráficas se presentan los resultados obtenidos.
3.1. Variación dimensional (%)
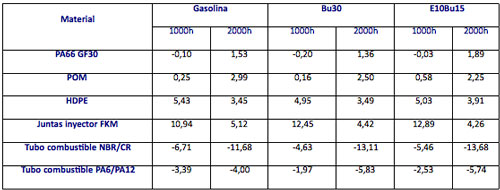
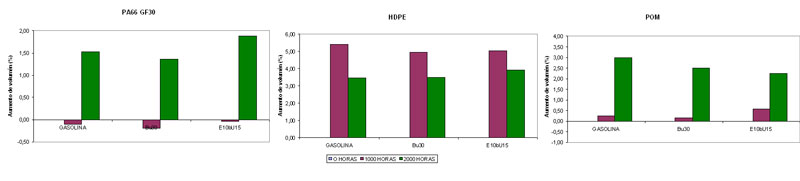

2.2. Resistencia al impacto Charpy a 23 °C (KJ/m2)
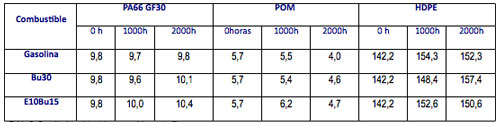
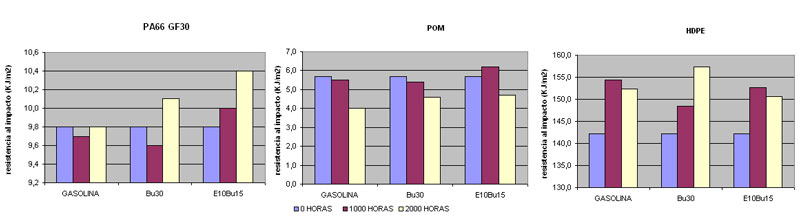
Figura 2.
2.5.2. Ensayos de resistencia a la tracción (MPa)

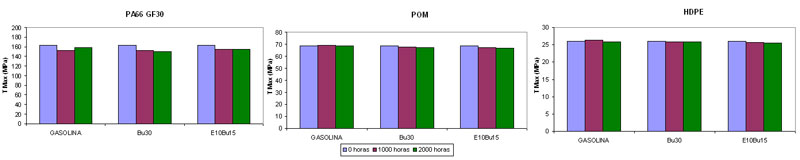
Figura 3.1.


Figura 3.2.
2.5.1. Ensayos de alargamiento en tracción (%)
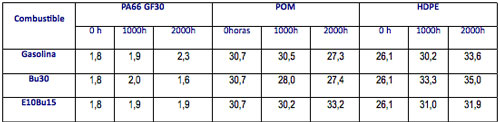
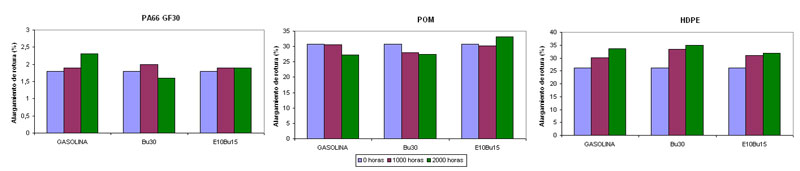
Figura 4.1.


Figura 4.2.
2.6. Determinación de la dureza shore (A y D)

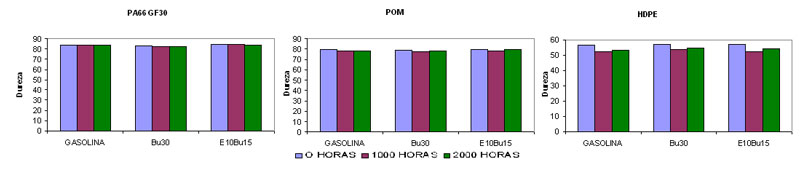
Figura 5.1.

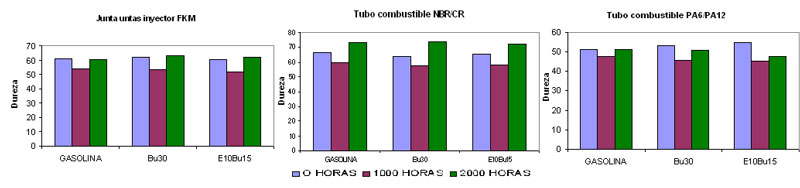
Figura 5.2.
Conclusiones
La conclusión principal es que los materiales presentan un buen comportamiento a lo largo del ensayo manteniendo sus propiedades mecánicas y estabilidad dimensional en las condiciones establecidas.
Las variaciones de las propiedades que se producen no son significativas por lo que estos materiales pueden seguir siendo utilizados en la fabricación de piezas y componentes para el sistema de combustible de los automóviles. En los casos en los que las propiedades tienen una variación apreciable ésta se debe al efecto de la gasolina. La adición de biobutanol y bioetanol no produce variaciones significativas.
En los ensayos de variación dimensional en el caso de los termoplásticos el material que presenta un mejor comportamiento es la PA66 que sufre variaciones inferiores al 2%. De todas formas ninguno de los tres materiales analizados supera el 4% de variación dimensional. El polietileno presenta un comportamiento más complejo ya que el aumento de volumen a 2.000 horas es inferior al aumento a 1.000 horas. Probablemente a 1.000 horas se produce un hinchamiento del material base, y posteriormente el fluido provoca la extracción de fracciones de bajo peso molecular y/o aditivos que causan una ligera disminución en el hinchamiento.
En el caso de los elastómeros FKM, NBR/CR y PA6/PA12 las variaciones que se producen son mayores. En el caso del FKM se producen variaciones de hasta un 13% al ser expuesto a E10Bu15 y del 11% en las probetas expuestas en gasolina. El comportamiento del FKM sería similar al del polietileno, con un hinchamiento inicial y una posterior disminución debida a la extracción de fracciones de bajo peso molecular y/o aditivos.
En el caso de los tubos de NBR/CR se produce una contracción del material debida a la extracción de los aditivos que alcanza el 14% en su valor máximo en E10Bu15. Su comportamiento es similar en los otros dos combustibles, ya que en la gasolina la pérdida es del 12% y del 13% en Bu30.
En los tubos de combustible PA6/PA12 se produce una disminución continua. El comportamiento del material en los tres combustibles es similar. Tras 2.000 horas de ensayo la disminución del volumen no superaba el 6% para ninguno de los tres combustibles.
En los ensayos de resistencia al impacto Charpy en el caso de la PA66 se produce un ligero aumento en las probetas sumergidas en Bu30 y E10Bu15. En el caso del POM a pesar de que se producen ligeras variaciones, éstas son similares en los tres combustibles. La máxima variación se produce tras 2.000 horas de exposición a gasolina y en menor medida a las probetas sumergidas en Bu30 y E10Bu15, por lo que se concluye que la pérdida de propiedades se debe a la gasolina y que este material es adecuado para su uso en contacto con Bu30 y E10Bu15. En el caso del HDPE las variaciones que se producen son similares en todos los combustibles utilizados por lo que podemos concluir que si el material es adecuado para su uso en gasolina también será adecuado para su uso en contacto con Bu30 y E10Bu15. Las variaciones producidas mejoran en muchos casos la resistencia al impacto del material lo que se explicaría por un efecto plastificante producido por el combustible.
En los ensayos de tracción en el caso de los termoplásticos PA66, POM y HDPE las variaciones que se producen en las distintas propiedades medidas nunca superan el criterio de rechazo de un material. En el % alargamiento del POM las variaciones producidas son más significativas. En este caso la muestra sumergida en gasolina también sufre una variación importante. Esta disminución en alargamiento estaría relacionada con la disminución que sufre la resistencia a impacto. No obstante las piezas fabricadas en POM no sufren deformaciones apreciables, siendo la resistencia a tracción el valor más crítico que en este caso no presenta variación apreciable.
En el caso de los elastómeros y del tubo de combustible de PA6/PA12 también se producen disminuciones superiores al 50%. En algunos casos, aparecen disminuciones apreciables en las propiedades, pero son en todos los casos debidas al efecto de la gasolina.
En los ensayos de dureza no se aprecian variaciones significativas en los materiales termoplásticos estudiados (PA66, POM, HDPE)
En los dos tipos de elastómeros analizados (FKM y NBR/CR) se observa un comportamiento similar. En el caso del FKM la dureza disminuye en las primeras 1.000 horas y se recupera en las siguientes, llegando a los valores iniciales. El contacto del material con el combustible provoca un hinchamiento del material, provocando un aumento de volumen y la disminución de la dureza. En las siguientes 1.000 horas el combustible extrae aditivos de bajo peso molecular del material provocando la recuperación del volumen y un aumento en la rigidez, y por tanto en la dureza del material. En el caso del NBR/CR la dureza también disminuye en las primeras 1.000 horas de exposición. El NBR/CR disminuye de volumen debido a la extracción de aditivos durante la exposición. La pérdida de aditivos provoca en un primer momento el reblandecimiento del material, con la consiguiente pérdida de dureza. En las siguientes 1.000 horas de exposición el material se sigue contrayendo por la extracción de aditivos. Esta contracción provoca un aumento en la rigidez, lo que ocasiona que los valores de dureza obtenidos sean superiores a los iniciales.
Las variaciones en contacto con Bu30 y E10Bu15 son similares a las que se producen al estar en contacto con gasolina. Por tanto se puede concluir que estos materiales son adecuados para su uso en esta mezcla de combustibles y que las variaciones que se producen están relacionadas más con el efecto de la gasolina que con la adición de biobutanol. En el caso de las muestras de tubo de PA6/PA12 se produce un descenso de la dureza en las primeras 1.000 horas y una cierta recuperación de los valores en las siguientes. Las variaciones en los valores son similares en los tres combustibles por lo que se puede concluir que si el material es apto para su uso en gasolina también es apto para su uso con Bu30 y E10Bu15
Las especificaciones de dureza para un material de suministro son de +- 5 puntos shore, y la mayoría de las variaciones registradas tras las 2.000 horas de ensayo son inferiores a este margen, por lo que las variaciones de dureza registradas no se consideran como significativas.
Agradecimientos
Este proyecto ha sido llevado a cabo por Fundación Cetena-Cemitec dentro de un proyecto de investigación, desarrollo e innovación de tipo cooperativo de título ‘Valoración de la producción y uso de biobutanol en motores de gasolina’ y en el que han participado Acciona Energía, Centro Nacional de Energías Renovables Cener-Ciemat, Fundación L’Urederra y Fundación Cetena-Cemitec. Este proyecto ha sido subvencionado por el Gobierno de Navarra.
Referencias
Climate change and CO2.
Organisation Internationale des Constructeurs d’Automobiles (OICA), Geneva Motor Show, March 2008.
Status and perspectives of biomass-to-liquid fuels in the European Union. ISBN 92-894-9784-X.
B. Kavalov and S.D. Peteves
Plan de Energías Renovables 2011-2020. IDAE
Compatibility study of high density polyethylene with bioethanol–gasoline blends
C. Berlanga-Labari, A. Albistur-Goñi, I. Barado-Pardo, M. Gutierrez-Peinado,
J. Fernández-Carrasquilla Materials and Design 32 (2011) 441–446
[5]Mohammad Ibrahim AlHasan & Muntaser AlMomany (2008): The effect of isobutanol-diesel blends on engine performance, Transport, 23:4, 306-310
The Engine Performance and Fuel Properties of Biobutanol Blended Gasoline Jan. 21, 2010 SK ENERGY
Emission characteristics of a spark-ignition engine fuelled with gasoline-n-butanol blends in combination with EGR
Xiaolei Gu, Zuohua Huang, Jian Cai, Jing Gong, Xuesong Wu, Chia-fon Lee
Fuel 93 (2012) 611–617
Production of butanol (a biofuel) from agricultural residues: Part I – Use of barley straw hydrolysate
Production of butanol (a biofuel) from agricultural residues: Part II – Use of corn stover and switchgrass hydrolysates
Nasib Qureshi*, Badal C. Saha, Bruce Dien, Ronald E. Hector, Michael A. Cotta
biomass and bioenergy 34 (2010) 559 – 565; 566 – 571
Combustion of n-butanol in a spark-ignition IC engine
S. Szwaja J.D. Naber Fuel 89 (2010) 1573–1582