Ventilación de moldes o salidas de gases: conceptos (Parte 1)
Ubicación de las salidas de gases o canales de ventilación
¿Dónde ubicar las salidas de gases o canales de ventilación? ¿Cuántos canales colocar? ¿Qué dimensiones aplicar en anchura y profundidad?
Las respuestas a estas cuestiones suelen determinarse en las plantas de inyección mediante el método empírico de prueba y error. Se realizan ajustes en el molde y, en función de los resultados obtenidos, se aplican las correcciones necesarias.
Dos ideas básicas que debemos tener en cuenta:
- Cuando el molde se cierra, no está vacío. Contiene un volumen de aire atrapado que debe ser desplazado para dar paso al plástico fundido durante el llenado de la cavidad.
- Las salidas de gases deben permitir la evacuación del aire sin dejar que pase el plástico fundido, ya que, de lo contrario, se generarán rebabas inevitables.
A modo de ejemplo, cuando un sistema de riego con aspersores comienza a funcionar, lo primero que se escucha es un silbido de aire presurizado saliendo por la boquilla hasta que el agua llega y desplaza completamente el aire. Lo mismo ocurre en el llenado de un molde con plástico fundido.
Consideraciones para determinar la correcta ventilación del molde:
- Velocidad o caudal de inyección.
- Volumen de la cavidad.
- Tipo de material.
- Cizalla aplicada en zonas complejas.
- Condiciones del proceso (temperatura de masa, de molde, tiempo de llenado, etc.).
Caudal y velocidad de inyección
La velocidad de inyección o caudal de inyección se mide en cm³ por segundo. En caso de utilizar mm por segundo, se debe calcular el volumen en cm³ por segundo multiplicando la velocidad de inyección por el área del husillo. Este caudal de plástico fundido en cm³ por segundo equivale al caudal de aire que debe evacuarse a través de todas las salidas de gases disponibles o mecanizadas.
Existe consenso en que, cuantas más salidas de gases haya disponibles, mejor será el rendimiento del sistema de ventilación, siempre evitando el riesgo de generar rebabas.
Como norma generalmente aceptada, el aire debe salir y evacuarse a la misma velocidad que el plástico fundido entra en la cavidad. Esto implica que, si se inyecta una pieza gruesa a velocidad lenta para evitar vacuolas, la necesidad de ventilación será menor. En cambio, si se inyecta una pieza delgada con un recorrido de flujo largo, la inyección será mucho más rápida y el aire deberá salir con alta velocidad a través de las salidas de gases.
Problemas típicos de una ventilación insuficiente
- Quemados o efecto diésel.
- Falta de compactación de la pieza.
- Piezas cortas.
- Poca definición superficial.
- Uniones débiles.
- Vacuolas internas.
- Variación dimensional.
- Brillos, ráfagas.
- Deformaciones.
- Marcas plateadas.
- Residuos en las salidas de gases.
¿Cuántas salidas de gases deben mecanizarse?
Existen diferentes reglas de taller o teorías al respecto. Una de ellas indica que las salidas de gases deben colocarse tantas como sea posible, con una separación de 25-30 mm entre ellas. Otra teoría sugiere mecanizar suficientes salidas de gases para que al menos el 30% de la longitud de la línea de partage esté ventilada.
Aquí surgen discrepancias entre inyectadores y moldistas. Los inyectadores, por lo general, preferimos contar con el mayor número posible de salidas de gases, mientras que los moldistas suelen optar por la mínima cantidad necesaria para evitar desajustes.
Personalmente, me inclino por esta última opción. Implementar ranuras de salida de gases conectadas a un canal secundario que rodee toda la cavidad es una buena solución, siempre y cuando se garantice la evacuación del gas hacia la atmósfera desde dicho canal.
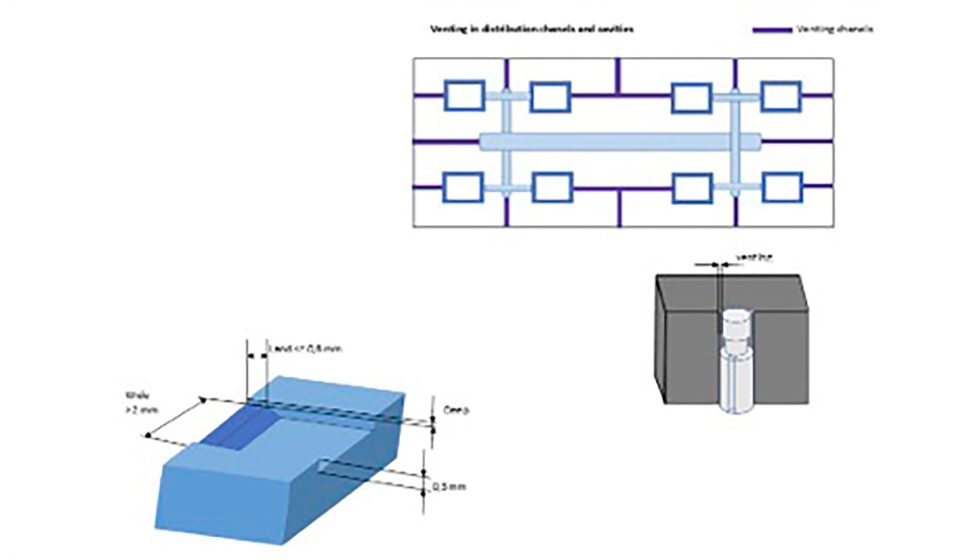
Dimensiones de las salidas de gases
Las características dimensionales de la salida de gases determinan su funcionalidad. Podemos diferenciar tres cotas clave:
Profundidad (Deep)
La profundidad de la ranura o deep (altura) debe ser lo mayor posible, siempre que no genere rebabas ni filtraciones de material indeseadas. Esta profundidad dependerá de diversos factores, como la geometría de la pieza (ya que los espesores determinan las velocidades de inyección adecuadas), el diseño del molde, los parámetros de inyección y, por supuesto, el tipo de material y su fluidez.
Por esta razón, los materiales más fluidos requieren profundidades de salida de gases más restrictivas en comparación con materiales más viscosos.
¿Cómo determinar la profundidad adecuada para el mecanizado del molde? La mayoría de los fabricantes de plásticos de prestigio ofrecen recomendaciones específicas para cada tipo y grado de material. Estas suelen oscilar entre 1.5 y 3 centésimas de milímetro, dependiendo del material utilizado.
Longitud del canal de ventilación (Land, Length)
Cuanto mayor sea la longitud de la salida de gases, mayor será la presión necesaria para expulsar el aire a través de ella. A su vez, cuanto mayor sea esta presión, mayor será la compresión del aire en la cavidad, lo que incrementará la presión de inyección necesaria para llenarla y, al mismo tiempo, aumentará el riesgo de efecto diésel o incineración del material, con el posible desgaste de los aceros del molde, pulidos, texturizados, etc.
Además, las longitudes de los canales de ventilación más cortas evitan la acumulación de residuos del polímero en la ranura, mientras que los canales más largos favorecen el depósito de restos del monómero y del paquete de aditivos en sus superficies.
A modo de analogía, si intentamos beber un refresco con una pajita muy larga, veremos que es más difícil succionar el líquido. En cambio, si la pajita es más corta, lo conseguiremos con mucho menos esfuerzo.
Se ha consensuado que la longitud idónea del canal de ventilación debe estar entre un máximo de 0,8 mm y 1 mm, aunque algunos manuales mencionan un límite de 0,03 pulgadas. También se establece una media máxima de 3 mm. En cualquier caso, hay quienes mecanizan las ranuras con una longitud de entre 2 y 3 mm, y, si aparecen efectos diésel o una presión de inyección excesiva, pueden reducir esta longitud.
Anchura del canal de ventilación (Wide)
La anchura del canal de ventilación suele depender principalmente del volumen de la cavidad. Se recomienda una anchura de entre 5 y 6 mm para piezas pequeñas y de entre 10 y 12 mm para piezas grandes.
En cualquier caso, es importante considerar que una menor anchura puede aumentar la frecuencia de limpieza, ya que la aparición de rebabas depende más de la profundidad de la ranura de ventilación que de su anchura.
En el proceso de inyección de plástico, los canales de ventilación excesivamente anchos no funcionan de manera óptima, no solo por las razones mencionadas, sino también porque pueden cerrarse parcialmente debido a la flexión de las placas del molde en superficies con grandes vaciados.
José Ramón Lerma es autor de los libros: 'Libro Manual Avanzado de Inyección de Termoplástico', que tiene como objetivo ser, por un lado, una herramienta para la formación y, por otro, un manual de ayuda para todo el personal de una empresa de inyección de plásticos y, del recientemente editado, 'Scientific Injection Molding Tools. Productividad a través del dominio del proceso'. Ambas publicaciones, comercializadas por Plásticos Universales / Interempresas (libros@interempresas.net), consta de detallados casos prácticos, amplia información de moldeo científico y un ‘pendrive’ con 20 hojas de cálculo y herramientas de SC Molding o Scientific Injection Molding, además de optimización y definición de proceso, lo que lo hacen único en el mercado. El libro Manual Avanzado de Transformación de Termoplásticos ha sido editado y comercializado en inglés a nivel mundial por la editorial Hanser Publications. Página web sobre Scientific Injection Molding: www.asimm.es