Simulación de la inyección de un spolier posterior del automóvil
Mario Ordoñez (Gaiker) y Jon Ander (Maier Technology Centre)
En la transformación de plásticos por inyección son cada vez más altas las exigencias de calidad en las piezas obtenidas, a la vez que la fuerte competitividad obliga a la optimización de la producción y a la reducción de costes y tiempos de puesta en marcha de productos nuevos. Para asegurar el éxito técnico-económico en el desarrollo de un componente plástico nuevo debe recurrirse a un diseño integral del producto que contemple globalmente el problema: diseño del componente, elección del material, comportamiento mecánico de la pieza, diseño del molde, selección de la máquina y parámetros óptimos de procesado.
Los distintos programas existentes en el mercado para la simulación de los procesos de transformación y el análisis del comportamiento de piezas sometidas a solicitaciones constituyen una herramienta de trabajo de gran ayuda. A partir de datos geométricos relativos a la pieza, el molde y de las características reológicas del material se pueden evitar los defectos típicos de un diseño erróneo del molde, unos parámetros de transformación incorrectos o un material inadecuado para la aplicación considerada.
Desde Septiembre del 96 los Centros Tecnológicos GAIKER y MAIER TECHNOLOGY CENTRE colaboran en un proyecto para el desarrollo de nuevos componentes plásticos, destinados al sector de automoción y electrodomésticos, obtenidos por inyección convencional y otros procesos: film-in-mold, inyección secuencial, inyección asistida con gas, coinyección, sobreinyección. Para el análisis del proceso de transformación se dispone de los programas de simulación MOLDFLOW, C-MOLD y del paquete ANSYS para el cálculo de estructuras plásticas.
Como ejemplo de las posibilidades que ofrecen estos programas, a continuación se describe la simulación realizada con C-MOLD 97.1 de una pieza que actualmente se encuentra en fase de producción en MAIER S. COOP: el spoiler posterior del SEAT IBIZA CUPRA.
La pieza se transforma en ABS/PC BAYBLEND T45 MN de BAYER y está constituida por una cara vista y una tapa inferior. El conjunto se obtiene en un molde de dos cavidades (1+1) en una inyectora de 1500 Tm. Posteriormente la tapa, que hace de anclaje a la carrocería del automóvil, se sella con adhesivo. Además de la estabilidad dimensional, a esta pieza se le exige un alta calidad superficial porque sufre un pintado y esta operación acentúa los posibles defectos que presente.
Diseño del molde
Inicialmente el molde se diseñó con dos cámaras calientes y dos puntos de inyección para cada cavidad. Esta configuración da lugar a ráfagas en la superficie de la pieza y a líneas de unión muy marcadas porque los dos frentes se encuentran frontalmente al final del proceso de llenado (figura 1 y 2).
Figura 1
Avance del frente de llenado del molde. Tiempos de inyección en segundos.
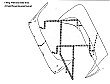
Posición de las líneas de unión.
Como solución se plantea incluir un tercer punto de inyección central en la cavidad mayor. Una modificación simple del molde consiste en crear un canal frío adicional entre las dos boquillas existentes hasta el nuevo punto de inyección. Sin embargo, la simulación muestra (figura 3) que no se consigue enviar suficientemente rápido el material hacia la zona central de la cavidad. El recorrido del canal adicional es demasiado largo, de manera que se completa antes el llenado de los extremos y se origina una línea de unión doble igualmente inaceptable (figura 4).
Figura 3
Avance del frente de llenado del molde. Tiempos de inyección en segundos.
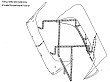
Posición de las líneas de unión.
Finalmente se estudia la inclusión de una cámara caliente central adicional. Como el recorrido del material por el canal central es menor que por los extremos, en la simulación se han optimizado los diámetros: todos son de 10 mm excepto en canal central que se ha reducido a 6 mm (figura 5). El resultado son tres frentes de llenado en la cavidad mayor de manera que las líneas de unión se sitúan en una zona de menor compromiso (cara inferior del spoiler) y son menos marcadas. Esta solución es la que se adoptó en el molde, con resultados satisfactorios.
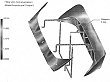
Avance del frente de llenado del molde. Tiempos de inyección en segundos.

Posición de las líneas de unión.
Optimización de las condiciones de procesado
Además del diseño del molde, la simulación mediante el programa C-MOLD permite la selección de las condiciones óptimas de procesado. Así por ejemplo, se observa el efecto de la velocidad de inyección sobre el llenado de las cavidades. Suponiendo una temperatura de transformación de 2701C y una temperatura del molde de 801C, la simulación predice que un tiempo de llenado inferior a 4 s dará lugar a una cizalla excesiva del material que provoca su degradación. Por contra, la simulación de un tiempo de inyección superior a 5 s predice un enfriamiento excesivo del material en las zonas que se llenan en las fases iniciales del proceso. El aumento de viscosidad resultante desequilibra el llenado entre ambas cavidades. El tiempo de llenado real obtenido en producción es de 4.6 s.
Figura 7
Presión de inyección (MPa) soportada por el material a los 4.00 s.
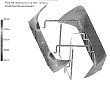
Temperatura (ºC) del material en la cavidad a los 4.21 s.
La simulación permite definir la duración de las fases de compactación y de enfriamiento, óptimizando el tiempo total de ciclo, con la consiguiente mejora de calidad y producción. Al cabo de 7.62 s los puntos de inyección se encuentran a 1901C, mientras que el resto de la cavidad está a una temperatura superior (figura 10). Aunque se mantenga más tiempo la presión de compactación ésta no tendrá efecto sobre la pieza porque los puntos de inyección se encuentran solidificados. Este enfriamiento prematuro, junto con la distribución de tensiones de cizalla observada (figura 9), indican que el diámetro (2 mm) de los puntos de inyección debe aumentarse, con la consiguiente reducción en la presión de inyección requerida, de la fuerza de cierre, y de las tensiones de cizalla inducidas. Esto a su vez se traduce en un menor recalentamiento del material y una distribución de temperaturas más uniforme a lo largo de las cavidades.
Figura 9
Tensión de cizalla (MPa) del material en la cavidad a los 4.21 s.
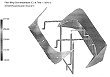
Temperatura (ºC) del material en la cavidad a los 7.62 s.
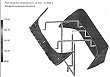
Temperatura (ºC) del material en la cavidad a los 22.54 s.
La duración de la fase de enfriamiento se obtiene de la figura 11 donde se observa que a los 22.54 s el material en las cavidades se encuentra por debajo de 120 ºC, es decir que puede procederse al desmoldeo de la pieza.
La simulación realizada nos permite predecir el comportamiento de la pieza tras el desmoldeo. Así la figura 12 muestra una contracción volumétrica del material muy uniforme en ambas cavidades por lo que en este caso no son previsibles problemas de alabeos.
Figura 12
Contracción volumétrica (%) del material en la cavidad a los 48.79.
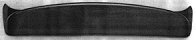
Spoiler posterior SEAT IBIZA CUPRA tras la operación de pintado.
Simulación de procesos de inyección no convencionales
Finalmente se ha procedido a la simulación de la inyección del spoiler suponiendo la utilización de boquillas provistas de válvulas con control de apertura/cierre (inyección secuencial). Se ha supuesto un tiempo de llenado de 5 s, manteniendo las demás condiciones de procesado como en el caso anterior (figura 14). Las válvulas 1 y 3 se abren a los 2.5 s de comenzar el llenado y todas se mantienen abiertas hasta el final de la fase de compactación. Se aprecia que cuando se abren las válvulas 1 y 3 los frentes de llenado han superado los puntos de inyección correspondientes por lo que no existen líneas de unión (figura 15). Las distribuciones de presiones de inyección, temperaturas del material y tensiones de cizalla calculadas son equivalentes a las observadas con una inyección convencional (figura 16).
No obstante, se optó por no considerar esta técnica de inyección dado el alto coste económico de la modificación del molde requerida.
Figura 14
Avance del frente de llenado del molde. Tiempos de inyección en segundos.
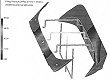
Presión de inyección (MPa) soportada por el material a los 2.50 s.
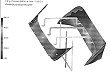
Presión de inyección (MPa) soportada por el material a los 5.00 s.