En la tecnología médica, el gasto desde la idea del producto hasta la producción en serie es especialmente elevado, ya que se requieren pruebas y documentación exhaustivas para la validación de todos los pasos del proceso en la producción
Validación de procesos de moldeo por inyección mediante parámetros de proceso
Matthias Schöll, investigador asociado Moldeo por inyección | Control de procesos de Institut für Kunststoffverarbeitung (IKV) in Industrie und Handwerk an der RWTH Aachen
13/03/2023En la tecnología médica, todos los pasos del proceso cuyos resultados no se comprueban totalmente deben validarse para la fabricación de productos. Para la validación de los procesos de moldeo por inyección, se suele definir una ventana de proceso sobre la base de los parámetros de ajuste de la máquina. La desventaja de los parámetros de ajuste es que no garantizan unas condiciones de proceso reproducibles y sólo se correlacionan hasta cierto punto con la calidad del componente debido a las fluctuaciones. Por lo tanto, se analiza la idoneidad de los parámetros de proceso para la validación. Con el fin de mantener el esfuerzo de validación lo más bajo posible, se investiga si los límites de la ventana de proceso de los parámetros de proceso también se pueden reajustar mediante la variación específica de los parámetros de ajuste de la máquina sin cambiar la correlación entre los parámetros de proceso y la calidad de la pieza.
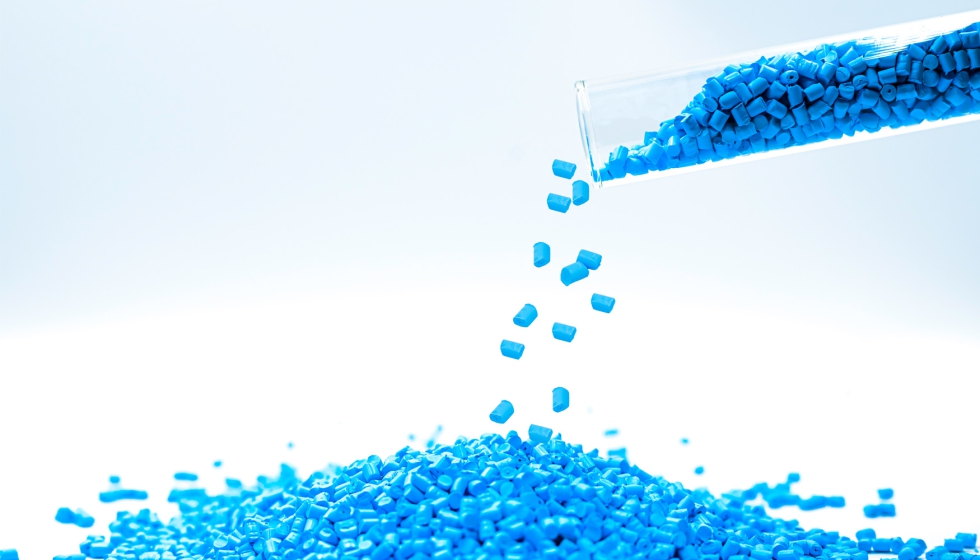
Las investigaciones muestran que las correlaciones entre los parámetros del proceso y las características de calidad pueden transferirse a la variación de los parámetros de ajuste de la máquina en el caso de variaciones en el proceso. Sin embargo, en el caso de las características de calidad, se producen diferencias en los factores de correlación de los parámetros de proceso. Una posible razón de ello puede ser que el comportamiento del material se ve influido de forma diferente por la variación de los parámetros de ajuste de la máquina que por las fluctuaciones.
2 Introducción
En la tecnología médica, el gasto desde la idea del producto hasta la producción en serie es especialmente elevado, ya que se requieren pruebas y documentación exhaustivas para la validación de todos los pasos del proceso en la producción. Diversas normas y directrices exigen la validación de procesos cuya calidad no puede verificarse por completo a posteriori. La validación sirve como prueba de que tanto el producto como el proceso se ajustan a las especificaciones previstas. Dado que el proceso de moldeo por inyección es un método de producción en serie, un control del 100% de los componentes a menudo no tiene sentido desde el punto de vista económico. En este caso, la validación tiene que demostrar que se ha identificado una ventana de proceso en la que la calidad de los componentes fabricados cumple las especificaciones del producto. En la producción posterior, la ventana de proceso validada no debe abandonarse.
Hasta ahora, se han utilizado parámetros de ajuste de la máquina para determinar la ventana de proceso del proceso de moldeo por inyección. Sin embargo, éstos no representan las condiciones del proceso y no pueden identificar las fluctuaciones del mismo, como el procesamiento de diferentes lotes de material. Por lo tanto, en esta contribución se investigará la posibilidad de validar un proceso de moldeo por inyección con la ayuda de los parámetros del proceso.
3 Estado de la técnica
En el estado de la técnica se presentan en primer lugar los requisitos para la validación, así como el procedimiento establecido para la misma, y se identifican los retos. Por último, se analizan distintos parámetros del proceso que describen su comportamiento.
3.1 Validación de procesos de moldeo por inyección en tecnología médica
La fabricación y el aseguramiento de la calidad de los productos sanitarios están regulados por la Food & Drug Administration (FDA) de EE UU en el Code of Federal Regulations Title 21 Part 820 y por la norma DIN EN ISO 13485. La funcionalidad y la seguridad de un producto deben verificarse mediante una inspección al 100 por cien. Si esto no es posible, debe validarse el proceso de fabricación del producto. Debido a las grandes cantidades y a la comprobación parcialmente no destructiva de la funcionalidad, los procesos de moldeo por inyección suelen validarse. Según 21 CFR Parte 820 e ISO 13485, la validación tiene que demostrar con un alto grado de certeza y mediante métodos establecidos que el proceso de fabricación es capaz de producir productos seguros y funcionales. El procedimiento de validación debe documentarse y la capacidad del proceso debe comprobarse periódicamente. En ninguna de las normativas se define un procedimiento preciso. La Global Harmonization Task Force (GHTF), un consorcio de varias autoridades reguladoras médicas nacionales, como la FDA, recomienda un procedimiento de tres pasos que también se utiliza para los procesos de moldeo por inyección: Cualificación de la instalación (IQ), Cualificación operativa (OQ) y Cualificación del proceso (PQ).
La Cualificación de la Instalación indica que toda la maquinaria, equipos y sistemas necesarios para la fabricación están instalados y son totalmente funcionales en el lugar de fabricación de acuerdo con los requisitos del fabricante.
La Cualificación Operativa muestra los límites de los parámetros dentro de los cuales el proceso sigue siendo capaz de producir productos seguros y funcionales (pruebas en el peor de los casos). Si no se conocen ya por investigaciones anteriores, se examina primero qué parámetros del proceso influyen en los Atributos Críticos de Calidad (CQA). Los Parámetros Críticos de Proceso (CPP) así determinados se validan en el procedimiento posterior. En los procesos de moldeo por inyección, los parámetros de la máquina, como el cilindro de ajuste y la temperatura del molde, la altura de la presión de mantenimiento y la duración o la velocidad de inyección, suelen validarse como CPP.
En la cualificación de procesos, se examina la estabilidad a largo plazo del proceso en condiciones de producción en serie. La capacidad del proceso a largo plazo (cp, cpk) en el punto del proceso determinado en la OQ se demuestra en tres lotes de producción y, por lo general, debe ser cp, cpk ≥ 1,33.
Todas las fases de la validación del proceso deben documentarse. No hay especificaciones para el tamaño exacto de la muestra en la fase de validación respectiva. El productor debe elegir el tamaño de la muestra y justificarlo estadísticamente en un razonamiento. En caso de que se produzcan cambios técnicos en el proceso o se observen cambios en el CQA, deberá llevarse a cabo una revalidación del proceso. En el proceso en serie en marcha, debe comprobarse periódicamente que el proceso se encuentra dentro de los límites definidos.
3.2 Enfoques para acortar el procedimiento de validación
Una validación completa del proceso lleva mucho tiempo y es costosa. Si un molde de inyección se utiliza en varias máquinas de inyección diferentes, existen enfoques para llevar a cabo una validación abreviada en cada máquina de inyección individual en lugar de una validación completa del proceso. Para ello, la validación completa (IQ, OQ, PQ) se realiza primero en una máquina de moldeo por inyección. En el protocolo de validación se miden y registran parámetros independientes de la máquina, como presiones, temperaturas y movimientos del husillo. Los parámetros elegidos deben describir las propiedades de la masa fundida (temperatura, viscosidad, presión y comportamiento de enfriamiento), así como las operaciones del proceso. Por lo tanto, la validación se basa en las propiedades del material y las operaciones del proceso es independiente de la máquina de moldeo por inyección utilizada. Al utilizar el mismo molde en otra máquina de inyección, los ajustes de la máquina se seleccionan ahora de forma que las variables del proceso coincidan con las variables del proceso de la máquina totalmente validada anotadas en el protocolo de validación. La estabilidad del proceso se demuestra en una PQ abreviada de cuatro horas con un alcance de prueba menor. Esto puede suponer un ahorro de tiempo, personal, material y costes, pero hay un mayor esfuerzo de medición de temperaturas, presiones y movimientos durante el proceso de moldeo por inyección.
3.3 Variables del proceso en el moldeo por inyección
Las influencias que interfieren en el proceso de moldeo por inyección pueden dar lugar a que se produzcan piezas rechazadas incluso a pesar de que el punto de proceso sea estable. Debido a las condiciones cambiantes del proceso, como la fluctuación de las propiedades del material, no basta con reproducir únicamente los parámetros de la máquina. En su lugar, los parámetros de ajuste deben adaptarse a las condiciones de proceso modificadas.
Una posibilidad es utilizar indicadores de proceso. Los indicadores de proceso reflejan las condiciones actuales del proceso y suelen estar formados por varios parámetros de proceso o curvas de parámetros de proceso. Además de las condiciones del proceso, los indicadores se correlacionan con los criterios de calidad. Los indicadores suelen ser adimensionales, ya que sólo son una medida de las condiciones de proceso modificadas y no una cantidad física. A continuación, se explicarán los ratios del proceso que se considerarán en el curso posterior de esta contribución:
La integral de la presión de inyección PIInj es un indicador de proceso de gran relevancia, ya que se correlaciona directamente con la fluidez, porque la presión en la precámara del tornillo depende de los parámetros específicos del material, del molde y de la máquina. Se forma como la integral de la presión de inyección pM durante la fase de inyección Inj (cf. Ec. 3.1).
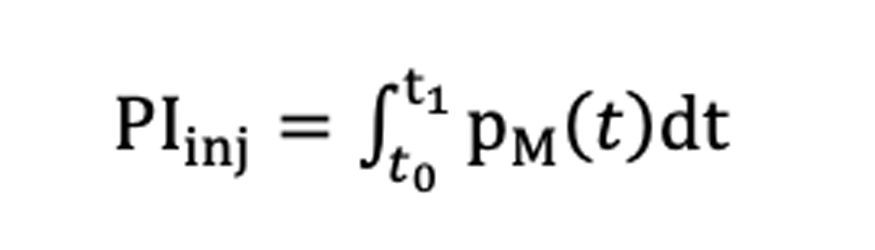
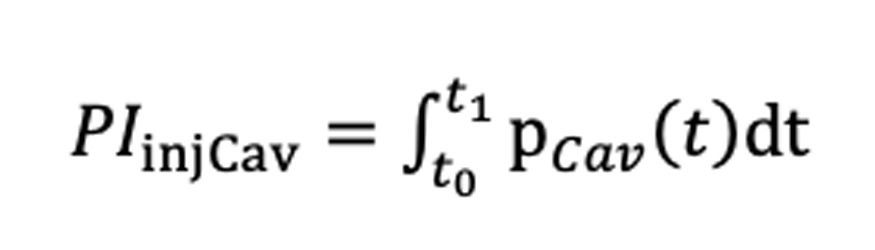
Otro indicador es el aumento integral de la temperatura en la posición del sensor en la fase de inyección TIInj. Se forma a partir de la integral de la temperatura de la pared del molde TCav durante la fase de inyección (véase la ecuación 3.3).
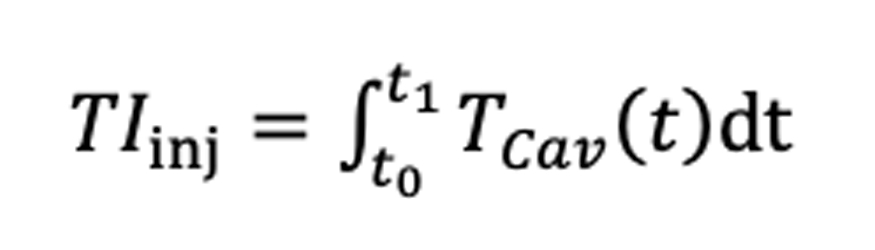
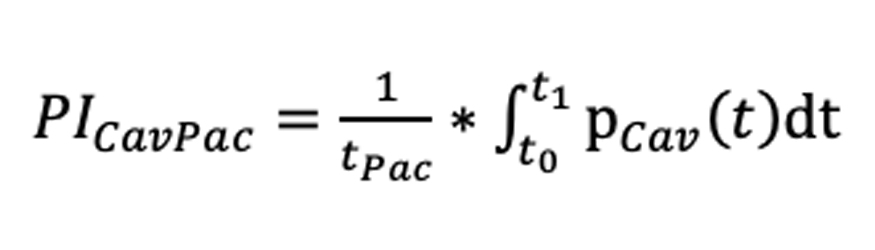
Al igual que la integral de la presión de inyección, este ratio también depende de la fluidez de la masa fundida. Como el gradiente de presión aumenta con una mayor viscosidad, la presión de la cavidad disminuye en condiciones por lo demás idénticas. Además, el parámetro de proceso también tiene en cuenta la temperatura del molde. Dado que la velocidad de enfriamiento depende directamente de la temperatura de la cavidad, este efecto también puede observarse en la presión de la cavidad. Con una temperatura del molde más cálida, la diferencia entre la temperatura de la masa fundida y la del molde es menor, por lo que la masa fundida se solidifica más lentamente.
4 Objetivos y procedimiento
Debido a las desventajas del procedimiento anterior para la validación de procesos de moldeo por inyección en el ejemplo de la tecnología médica, se va a investigar la posibilidad de validar el proceso con ayuda de los parámetros del proceso. Dado que no resulta rentable introducir deliberadamente en el proceso perturbaciones como, por ejemplo, fluctuaciones en el equilibrio térmico o fluctuaciones en la fluidez, se analizará si las perturbaciones pueden reajustarse mediante la variación dirigida de los parámetros de ajuste de la máquina.
Para ello, en un primer paso se investiga la influencia de las fluctuaciones del proceso en la calidad de los componentes. Por lo tanto, se identifican los indicadores del proceso que se correlacionan con la calidad del componente en este proceso. En un paso posterior, se investiga la influencia de una variación de los parámetros de ajuste de la máquina en los parámetros del proceso. Además, se considera el efecto sobre la calidad de la pieza. Al igual que en el primer paso, se analiza la correlación entre los parámetros del proceso y la calidad de la pieza. Por último, se evalúa si la influencia de las variaciones en la correlación entre los parámetros del proceso y la calidad de la pieza puede simularse variando los parámetros de ajuste de la máquina y si el proceso de moldeo por inyección puede validarse de forma significativa con ayuda de los parámetros del proceso.
5 Medios de explotación
Las pruebas de moldeo por inyección se realizaron con una máquina de moldeo por inyección hidráulica (véase la tabla 1). Para poder investigar adicionalmente la influencia de las fluctuaciones y las variaciones de los parámetros de la máquina en la calidad de la masa fundida, se utilizó una boquilla de medición especial. Con esta boquilla se puede medir la presión de la masa fundida mediante un sensor de presión. La temperatura de la masa fundida se mide con un termopar de inmersión que alcanza 1 mm en el canal de flujo y un sensor IR que tiene un termopar en el detector y en la superficie del sensor.
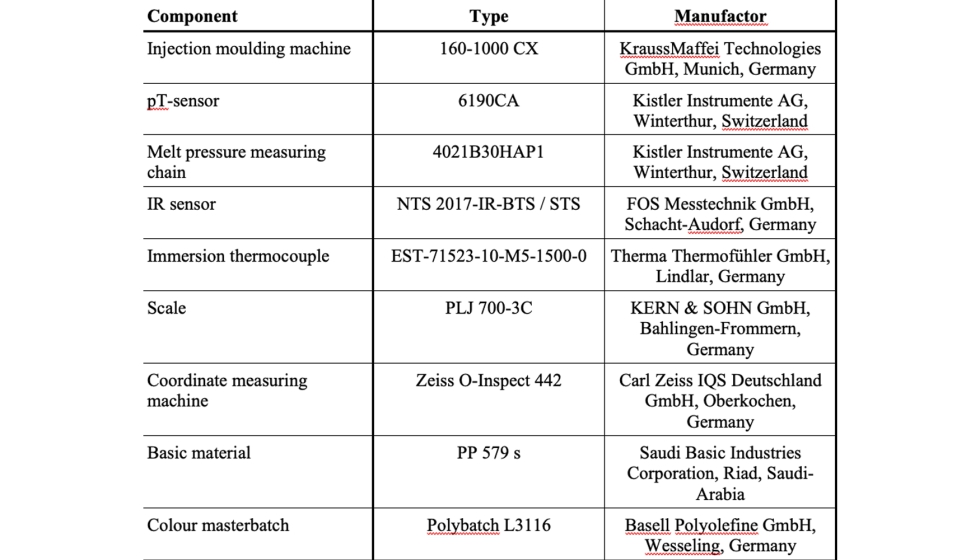
Cuadro 1: Recursos utilizados
Como pieza de ensayo se utiliza una geometría en forma de caja con nervaduras y aberturas adicionales. En el molde de inyección correspondiente se instala un sensor pT combinado. La figura 1 muestra la pieza de ensayo y la posición del sensor. Además, se marcan las dimensiones del componente, que se utilizarán para evaluar su calidad. Éstas se miden con una máquina de medición de coordenadas. Además de las dimensiones, también se tiene en cuenta el peso del componente
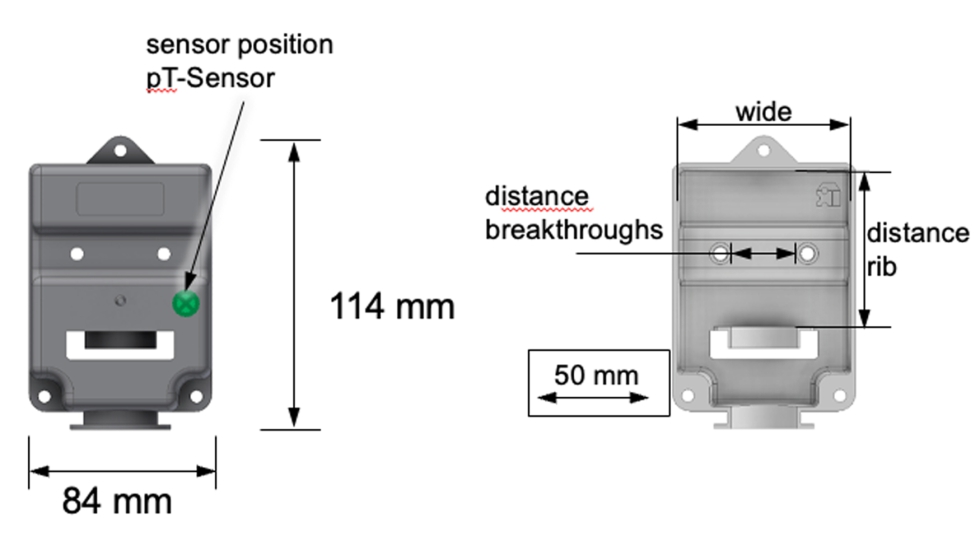
6 Análisis de validación de los procesos de moldeo por inyección en tecnología médica
En esta sección se investiga si la influencia de las perturbaciones en la correlación entre los parámetros del proceso y la calidad del componente puede simularse variando los parámetros de ajuste de la máquina. Para ello, en primer lugar se analizan los efectos de las perturbaciones en la correlación. A partir de ahí, se explora la correlación con una variación dirigida de los parámetros de ajuste de la máquina antes de comparar los dos enfoques entre sí.
6.1 Análisis de la influencia de las perturbaciones en el proceso de moldeo por inyección
En un primer paso, se analiza la influencia de las fluctuaciones en los parámetros del proceso y en la calidad del componente. Para ello, se manipula deliberadamente el proceso introduciendo fluctuaciones en puntos de prueba individuales. De este modo, se simula un cambio en la viscosidad mediante diferentes proporciones de masterbatch. Además, se procesaron dos lotes diferentes del material base. Las perturbaciones del equilibrio térmico se inician variando la temperatura del molde y el calentamiento del cilindro. Las perturbaciones y sus fases se resumen en el cuadro 2.
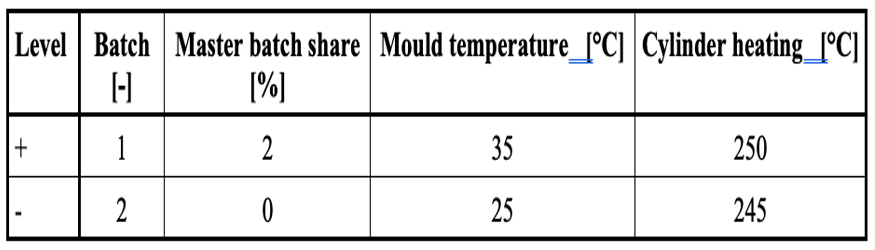
Cuadro 2: Interferencias introducidas
Para evaluar la influencia y las conexiones entre las variables individuales, se calcula la correlación de Pearson. Ésta describe la correlación lineal entre dos variables. Los factores de correlación pueden asumir valores entre -1 y 1. Una correlación de 1 / -1 describe una relación lineal perfectamente positiva / negativa entre las variables, mientras que una correlación de 0 describe una relación no lineal.
La influencia de las fluctuaciones en la calidad de la masa fundida (por ejemplo, temperatura y presión) puede medirse con ayuda de los sensores adicionales de la boquilla de medición. Tanto el lote (0,73) como el masterbatch (0,51) pueden identificarse con la presión máxima en la boquilla. Dado que ambas fluctuaciones afectan a la viscosidad, se requieren diferentes cantidades de energía para inyectar la masa fundida en la cavidad.
La variación de la temperatura de la masa fundida se correlaciona con la temperatura máxima de la masa fundida medida con el sensor IR (0,99). La variación de la temperatura del molde no tiene una influencia significativa en la presión y la temperatura en la boquilla.
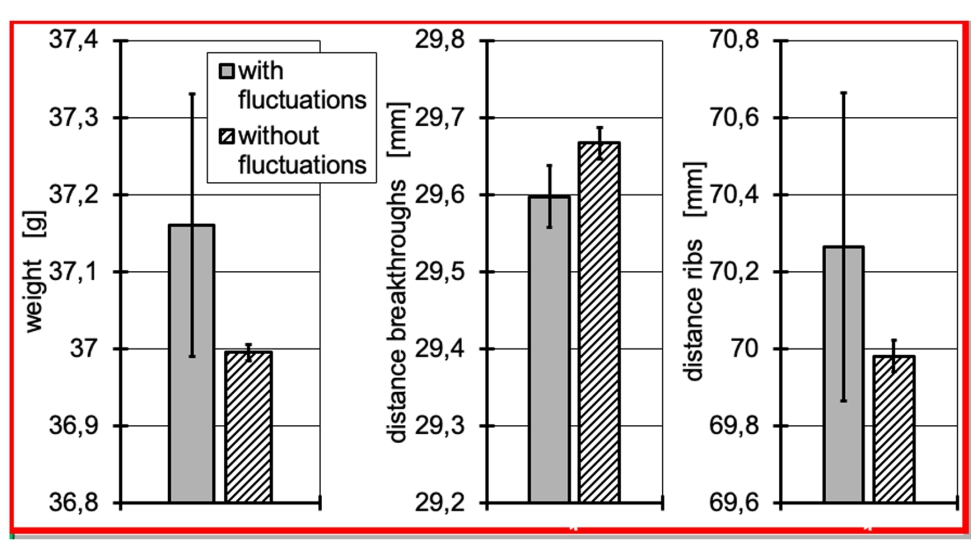
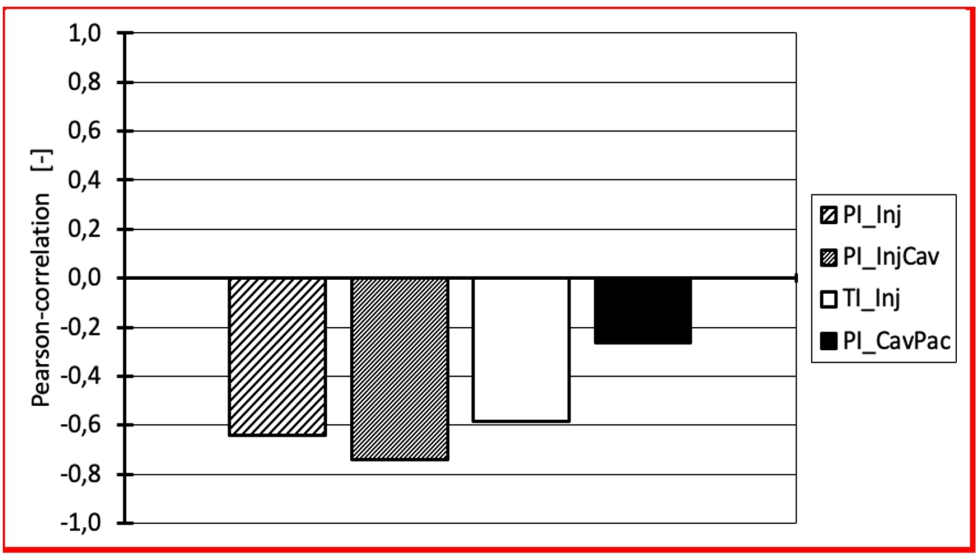
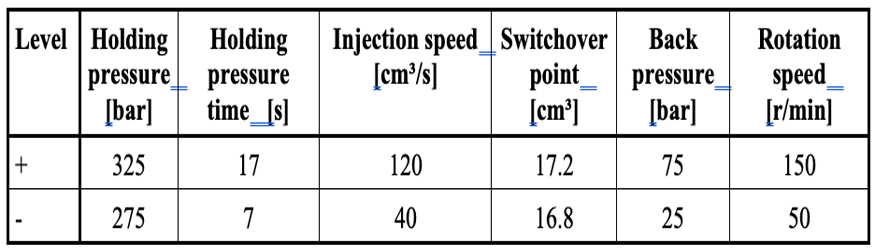
Los parámetros del proceso pueden utilizarse para identificar cambios en las condiciones imperantes en el proceso. Además, ofrecen la ventaja de que también se correlacionan con la calidad del componente debido a su dependencia de las condiciones de producción. A continuación se analizarán con más detalle las correlaciones entre los parámetros de proceso y los fallos, así como la calidad de los componentes. Para ello, se tendrán en cuenta los parámetros de proceso del apartado 3.3.
La evaluación de los parámetros del proceso con respecto a su correlación con la calidad de la masa fundida muestra que reflejan las condiciones del proceso. Además, la integral de la presión de inyección (0,99) y la integral de la presión de la cavidad durante la fase de inyección (0,42) se correlacionan con la presión de la masa fundida en la boquilla. Además, la integral de aumento de temperatura TIInj se correlaciona significativamente (0,42) con la temperatura de fusión del plástico medida con el sensor IR.
La figura 3 muestra la correlación de los parámetros del proceso con la distancia de las roturas. La integral de presión de inyección (-0,64) y la integral de presión de cavidad durante la fase de inyección (-0,74) se correlacionan fuertemente con los criterios de calidad.
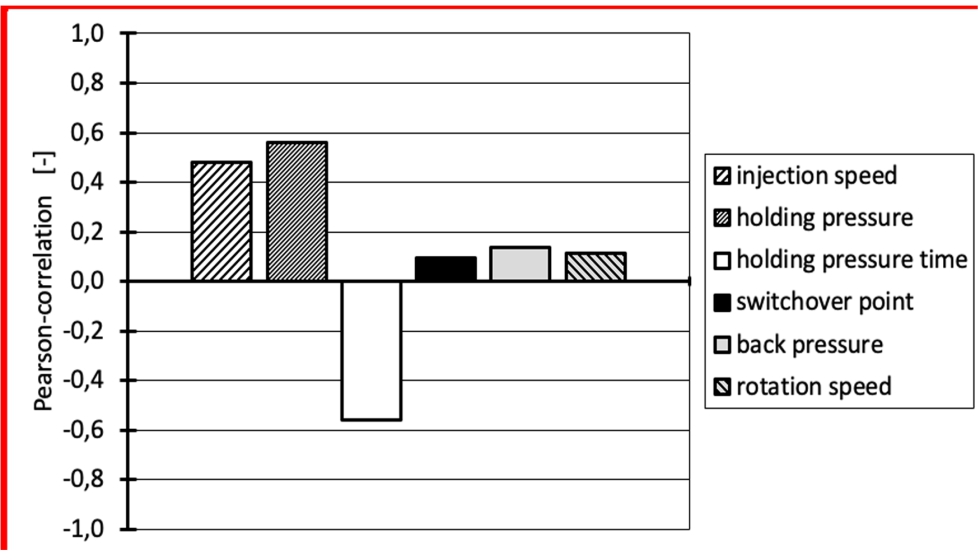
El aumento integral de la temperatura de la pared del molde sólo se correlaciona significativamente con la velocidad de inyección (0,87). Debido a la mayor velocidad de inyección, el material se cizalla con más fuerza, lo que se traduce en un aumento de la temperatura. La mayor temperatura de la masa fundida también da lugar a un menor gradiente de presión en la masa fundida. Por lo tanto, la integral de presión de la cavidad del molde de inyección también aumenta con la velocidad de inyección. La integral de presión también se ve ligeramente influida por el punto de cambio (0,21), la contrapresión (0,23) y la velocidad de rotación. Variando el punto de conmutación, varía la cantidad de plástico que se introduce en la cavidad durante la fase de inyección. Los parámetros de ajuste velocidad de rotación y contrapresión influyen en el cizallamiento y, por tanto, en la temperatura de la masa fundida durante la dosificación. Así lo pone de manifiesto la ligera pero significativa correlación de la contrapresión (0,14) y la velocidad de rotación (0,17) con la temperatura máxima de la masa fundida medida con el sensor IR.
La evaluación muestra que las variables del proceso se ven influidas por la variación selectiva de los parámetros de ajuste de la máquina. Además, los parámetros del proceso están correlacionados con la calidad del componente. La figura 5 muestra un ejemplo de la correlación de las variables del proceso con la distancia de las penetraciones cuando se varían los parámetros de ajuste de la máquina. La dimensión del componente se refleja con mayor intensidad en la integral de la presión de inyección (-0,51) y en la integral de la presión de la cavidad durante la fase de inyección (-0,61). También la presión media de la cavidad se correlaciona significativamente con la distancia. Las demás características de calidad también se correlacionan con algunos de los parámetros del proceso. Esto demuestra que las correlaciones entre las características del proceso y la calidad de la pieza también pueden establecerse variando los parámetros de ajuste de la máquina.
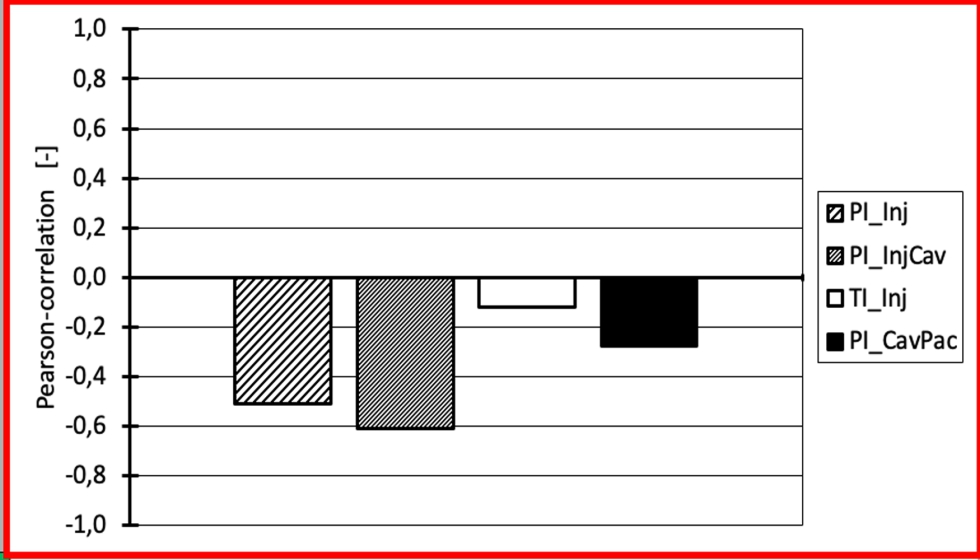
6.3 Comparación de la correlación entre las variables del proceso y la calidad del componente en caso de variaciones del proceso y en caso de variación de los parámetros de ajuste de la máquina
Con el fin de poder recrear las perturbaciones para la validación mediante la variación de los parámetros de reglaje de la máquina, en este apartado se analiza si las características de calidad individuales se correlacionan por igual con los parámetros del proceso, independientemente de las fluctuaciones debidas a las variaciones o a los parámetros de reglaje de la máquina.
La figura 6 muestra las diferencias en los factores de correlación de las características de calidad individuales. Puede observarse que los factores de correlación del criterio de calidad anchura son casi idénticos. La situación es similar en el caso del peso del componente, pero el factor de correlación de la integral de presión de la cavidad difiere en 0,21 puntos. Asimismo, en el caso de la costilla de distancia, los factores de correlación de la integral de aumento de temperatura y de la presión de cavidad media durante la fase de presión de mantenimiento al introducir las perturbaciones coinciden con los que se obtienen al variar los parámetros de ajuste de la máquina. Sólo la influencia de la integral de la presión de inyección se desvía en -0,19. Los factores de correlación de la integral de aumento de temperatura difieren para el espaciado de las rupturas. Los demás parámetros del proceso son iguales.
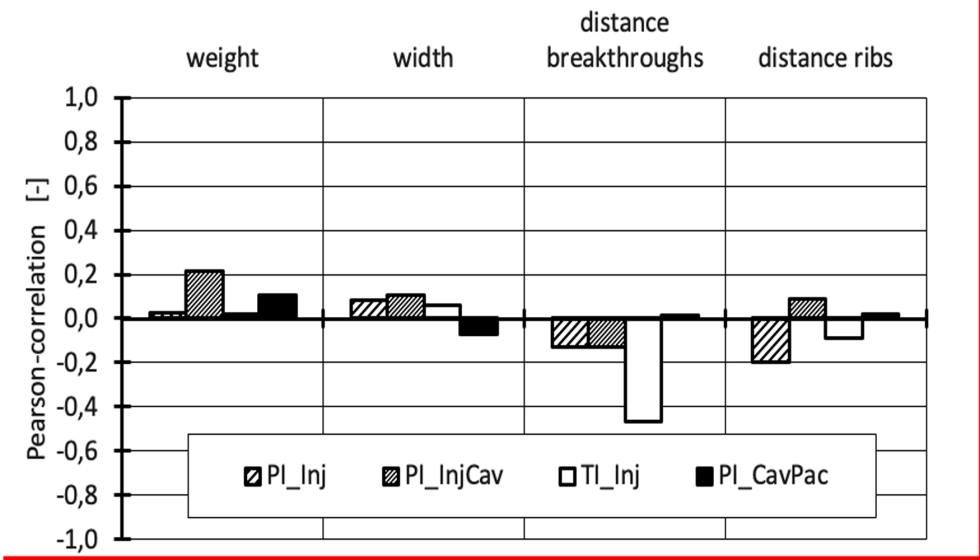
7 Conclusión y perspectivas
Las investigaciones demuestran que mediante el uso de parámetros de proceso se pueden describir las condiciones imperantes en el proceso. Además, se demostró la correlación entre la calidad de la pieza y los parámetros del proceso, lo que pone de relieve la ventaja de los parámetros del proceso sobre los parámetros de ajuste de la máquina.
También se demostró que la calidad de la masa fundida se ve influida por la variación específica de los parámetros de ajuste de la máquina. Una vez más, quedó claro que los parámetros de proceso están correlacionados con la calidad de los componentes fabricados. Una comparación de las correlaciones entre los parámetros del proceso y los criterios de calidad cuando se aplican fluctuaciones y cuando se varían los parámetros de ajuste de la máquina muestra que la mayoría de los factores de correlación casi coinciden. Sin embargo, también se observan diferencias individuales, que pueden deberse a un comportamiento diferente de los materiales. Por tanto, para poder hacer afirmaciones generales sobre la posibilidad de validación con ayuda de los parámetros del proceso, debería investigarse más a fondo el comportamiento del material bajo la influencia de las variaciones.
Además, debería analizarse si los parámetros de proceso relevantes para los respectivos parámetros de calidad pueden predecirse con ayuda de simulaciones de moldeo por inyección. Además, también debería investigarse la predicción de los parámetros de ajuste de la máquina, con los que se puede influir en los parámetros de proceso correspondientes, con el fin de mantener la cantidad de pruebas durante la validación lo más baja posible.
8 Agradecimientos
El proyecto de investigación 21127 N de la Forschungsvereinigung Kunststoffverarbeitung fue patrocinado como parte de “industrielle Gemeinschaftsforschung und -entwicklung (IGF)” por el Bundesministerium für Wirtschaft und Energie (BMWi) alemán debido a una promulgación del Bundestag alemán a través de la AiF. Queremos expresar nuestro agradecimiento a todas las organizaciones mencionadas.
9 Abreviatura, símbolo de fórmula, índice
9.1 Abreviatura
Abreviatura Significado
CPP Parámetros críticos del procesoa
CQA Atributos críticos de calidad
GHTF Grupo de Trabajo de Armonización Global
IQ Cualificación de la instalación
IR-sensor Sensor de infrarrojos
OQ Calificación operativa
PP Polipropileno
PQ Cualificación del proceso
Sensor pT Sensor de presión-temperatura
9.2 Símbolo de fórmula
símbolo unidad Significado
cp, cpk [-] Capacidad del proceso
p [bar] Presión
PI [bar*s] Integral de presión
t [s] Tiempo
T [°C] Temperatura
TI [°C*s] Incremento integral de temperatura
9.3 Índice
Índice Significado
Cav Cavidad
Inj Fase de inyección
M Máquina
Pac Fase de embalaje
10 Literatura
[AB17] ANES, J.; BEAUMONT, J.: Process Validation for Injection Molding Medical Components. Plastics Engineering 73 (2017) 5, S. 38-43
[Gro00] GROLEAU, R.: Location Independent PPAP Streamlined Global Manufacturing. In: University of Michigan Automotive Conference, 2000
[Gue20] GUERRA, M.: Validation of the injection moulding process to produce the primary packaging of tissue heart valves. Politecnico di Torino, 2020
[Ham04] HAMAN, S.: Prozessnahes Qualitätsmanagement beim Spritzgießen. TU Chemnitz, Dissertation, 2004
[HW15] HEINZLER, F.A.; WORTBERG, J.: Qualitätsregelung beim Spritzgießen (Teil 2Adaptive, druckgeregelte Prozessführung. Zeitschrift Kunststofftechnik 11 (2015) 3, S. 157-179
[LBS+18] LUSARDI, G.; BROWN, R.; SMITH, B.; HARRINGTON, M.; BROWN, D.; SCULLY, S.; BUTLER, D.; VALLEY, E.; THERRIEN, M.: “Part Process” Transferability Using a Machine Independent Variable (MIV) Methodology for Multiple Machines. White Paper (2018), S. 1-13
[LGP83] LAMPL, A.; GISSING, K.; PAINSITH, H.: Kontrolle des Formfüllgangs beim Spritzgießen mit Hilfe der Einspritzarbeit. Plastverarbeiter 10 (1983), S. 1105-1108
[Mus00] MUSTAFA, M.A.-H..: Modellbasierte Ansätze zur Qualitätsregelung beim Kunststoffspritzgießen. Universität Essen, Dissertation, 2000
[NN04] N.N.: GHTF/SG3/N99-10:2004 – Quality Management Systems – Process Validation Guidance, 2004
[NN16] N.N.: Medizinprodukte – Qualitätsmanagementsysteme – Anforderungen für regulatorische Zwecke (DIN EN ISO 13485:2016), 16a
[NN17] N.N.: Food and Drug Administration - Code of Federal Regulations Title 21 Vol 8 Part 820, 2017
[Pet05] PETRETICH, C.: Development of a validation method for thermoplastic injection molding processes for the contract medical device manufacturer. Bowling Green State University, 2005
[RL19] RAZENBÖCK, J.; LHOTA, C.: Assistenzsysteme in die Validierungsstrategie einbinden. Plastverarbeiter / Medplast 70 (2019) 13, S. 18-21
[The17] THERRIEN, M.: ‘Part Process’ Development and Validation for Multiple Machines. Medical Product Outsourcing Magazine (2017), S. 156-161
[VRA12] VESELOV, V.; ROYTMAN, H.; ALQUIER, L.: Medical Device Regulations for Process Validation: Review of FDA, GHTF, and GAMP Requirements. Journal of Validation Technology (2012), S. 82-92
[Zöl03] Zöllner, O.: Grundlagen zur Schwindung von thermoplastischen Kunststoffen., Bayer Magazin (2003) 01
[ZSW17] ZHAO, Y.; SHENG, K.; WANG, Z.; ZHANG, X.; HengyiYang; MIAO, R.: Process Validation and Revalidation in Medical Device Production. Procedia Engineering 174 (2017) 5, S. 686-692