Soluciones en FRP para el servicio con hipoclorito sódico
9 de diciembre de 2010
Las soluciones comerciales de hipoclorito sódico (generalmente con 9-15% de cloro activo) son estabilizadas con hidróxido sódico. Esto y su fuerte poder oxidante le hacen muy corrosivo para muchos materiales de construcción. Sin embargo, la estabilidad del hipoclorito sódico depende de varios factores, como la concentración, pH, temperatura, y las impurezas como los metales. Por ejemplo, si el agua dura se utiliza para la preparación del hipoclorito, este no será tan estable debido a la contaminación por metales como el hierro, calcio y otros metales, lo que lo hará que sea más agresivo frente a los materiales de construcción de tanques de almacenaje (2,18). El pH puede variar de forma significativa cuando se forma el hipoclorito, por ejemplo en los procesos químicos y en los lavadores de cloro. El diagrama siguiente muestra la composición química sobre el pH, como equilibrio del cloro, ácido hipocloroso (HOCI) y el hipoclorito sódico (NaOCI) versus el pH.
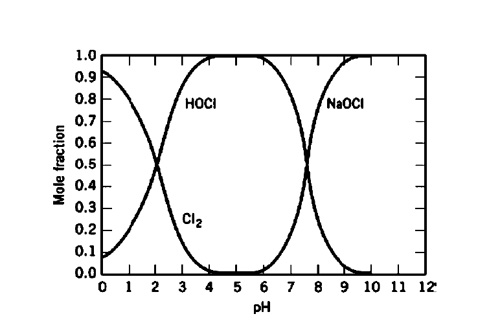
Cuando la estabilidad del sistema se ve comprometida, se pueden activar varios mecanismos. El ácido hipocloroso (HOCI) y el hipoclorito sódico (como ión ClO-)se descomponen a través de varias reacciones posibles que pueden ocurrir en función de la temperatura, incluso en ausencia de cualquier catalizador (3-8). La Tabla 1 resume estas reacciones y sus energías de reacción registradas, sin entrar en más detalles.
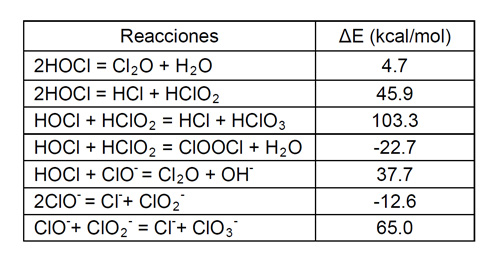
Se supone que cualquier producto intermedio que se forme durante las reacciones anteriores, puede tener efectos significativos sobre varios materiales. Por ello es muy importante conocer cuanto más sea posible las condiciones de operación, y de éste modo la estabilidad del hipoclorito, antes de seleccionar un material de construcción. Se debe dar prioridad a evitar la formación de productos inestables o para modificar los parámetros del proceso para mejorar la estabilidad del hipoclorito.
Perspectiva histórica
Los estudios de resistencia química de los FRP (según ASTM C581) frente al hipoclorito sódico, han sido realizados tradicionalmente a temperaturas elevadas, en un intento de detectar claramente las diferencias entre los sistemas probados. Esto llevó a la conclusión de que las resinas con una gran resistencia a los álcalis formuladas con un sistema libre de cobalto, en laminados con un doble velo sintético Nexus, se comportan mejor (9), según se puede ver en el apéndice I. Los sistemas de curado libres de cobalto continúan siendo la opción preferida mientras sea posible, y también las resinas epoxi vinilester bromadas, tal como veremos más adelante.
Además, han sido estudiadas las maneras de reducir la cantidad de cobalto (y de este modo el efecto perjudicial), en sistemas de curado estándar, bien sea debido a la sinergia con el potasio, o bien reemplazándole por vanadio. Ambos métodos han mostrado aspectos positivos, pero por el momento no se han usado en la práctica.
Transporte y almacenaje del hipoclorito sódico
Se han utilizado muchos materiales de construcción para transportar y almacenar el hipoclorito sódico a temperatura ambiente, por ejemplo grados especiales de polietileno (LHPDE, PEX), CPVC, FRP y titanio. El titanio está considerado como el mejor, pero su elevado coste y disponibilidad son factores que limitan su uso. El PE puede durar entre 7 y 11 años. Como ha sido confirmado por un estudio industrial en el 2004 (1), los FRP basados en resinas epoxi vinilester especiales, son los materiales de construcción más comunes utilizados para el transporte y el almacenaje, basados en casos históricos de más de 20 años de servicio. Un tanque fabricado en FRP, bien especificado y construido, puede durar de 20 a 30 años o más, con inspecciones regulares de la barrera química cada dos años y con la necesidad de pequeñas reparaciones. Un diseño y fabricación inapropiados pueden conducir a un fallo de la barrera química y daño en la estructura en menos de 5 años, lo que requerirá la sustitución del tanque (1, 2, 18). Un caso especial son los recubrimientos en FRP de las cisternas de transporte fabricadas en acero o acero inoxidable. La vida de servicio de estas soluciones, dependen de la integridad mecánica del tanque para prevenir la separación entre el laminado y el acero, o el agrietamiento de la superficie.
La experiencia nos indica los siguientes elementos clave para un buen resultado del FRP frente al hipoclorito sódico a temperatura de servicio ambiente:
-Utilizar una resina epoxi vinilester adecuada, preferiblemente bromada.
-Diseñar adecuadamente la barrera química (por ejemplo con un doble velo de superficie, sin el uso de cargas, aditivos, ni pigmentos), y un buen diseño estructural.
-Una formulación sin cobalto (o muy baja en cobalto).
-Un buen curado de la resina (sería deseable un post-curado siguiendo la recomendación DIN 18820).
-Realizar inspecciones regularmente.
-Soluciones estables de hipoclorito sódico (pH>11, T< 40°C), sin metales contaminantes y agua blanda para la dilución, protección del sol directo sobre el tanque (especialmente la fase de vapor), recubrimiento externo de las tuberías, etc.
Estudios
Los estudios aquí indicados incluyen probetas utilizadas en laboratorio, así como en el interior de tanques de almacenaje de hipoclorito, en dos plantas de tratamiento de aguas en Colorado, y durante 12 meses. El propósito de estos estudios fue la identificación del mejor sistema de resinas y la construcción de la barrera química para obtener la mayor vida en servicio de estos tanques (2).
Se incluyen estudios posteriores realizados con sistemas alternativos de resinas y a temperaturas más bajas.
Procedimiento experimental
Estudios de laboratorio a 50 y 65 °C seguidos del estándar ASTM C-581 sobre Pruebas de Resistencia Química en FRP. Los laminados de prueba consistieron en 3 capas de Mat de 450 gr/m2 con un velo por cada lado. Los paneles fueron curados a temperatura ambiente durante la noche, seguido de un postcurado a 94 °C durante 8 horas. Después de cortados a la medida, los bordes de los paneles se recubrieron con resina para evitar el ataque químico a la fibra. Los paneles se sumergieron en una solución de hipoclorito del 10 al 15%, y entre 50 y 65 °C. La solución de hipoclorito fue cambiada una vez por semana para mantener la concentración de cloro sobre el 9% en todo momento durante la prueba. Después de 1, 3, 6 y 12 meses, los paneles fueron sacados y se evaluó la dureza Barcol, la resistencia a la flexión, el módulo de flexión, y también visualmente.
Los laminados también se colocaron en el interior de dos tanques de almacenaje de hipoclorito, en la planta de tratamiento de agua. Estos laminados se extrajeron de los tanques y se enviaron para su evaluación después de una exposición de 3, 6 y 12 meses.
Las pruebas de laboratorio y las de los dos tanques de almacenaje se hicieron con la resina epoxi vinilester DERAKANE 1 411-350 (EVER 1), HETRON 1 922 (EVER 2) epoxi vinilester, HETRON FR992 epoxi vinilester bromada (BREVER1), DERAKANE 510A-40 epoxi vinilester bromada (BREVER2), y DERAKANE MOMENTUM 470-300, una epoxi novolaca vinilester (NEVER). La resina BREVER1 se probó con 2 capas de velo de poliéster, 1 capa de velo de poliéster y 1 capa de velo de vidrio C. Los sistemas de curado evaluados incluyeron un sistema de peróxido de metil etil cetona (MEKP)/Cobalto (Co) y uno de peróxido de Benzoilo (BPO)/Dimetil anilina (DMA). Las otras resinas fueron probadas solamente con una capa de velo de vidrio C, y curadas con BPO/DMA. Todas las probetas fueron post-curadas durante 8 horas a 94 °C.
Resultados
Los resultados de las pruebas de laboratorio en hipoclorito sódico estabilizado a 50 °C se muestran en la Tabla 2.
Ninguna de las pruebas sobre las probetas mostró una significativa reducción de las propiedades de la flexión después de 12 meses. El ataque superficial de las probetas varió, y se determinó por una inspección visual. La superficie de las probetas hechas con resina NEVER y curada con BPO/DMA fue la que sufrió más. El sesenta por ciento del recubrimiento de los bordes desapareció durante las pruebas. Estas dos observaciones indican un ataque químico por lo que ésta resina no se considera como la mejor para un largo tiempo de vida. La probeta basada en la BREVER1 con dos velos de poliéster y curada con 0,15% de Co 6% / MEKP también mostró ataque superficial.
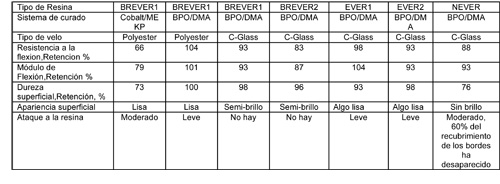
Si bien hubo alguna pérdida de brillo, el análisis al microscopio mostró el ataque al velo de poliéster. Algunas de las fibras de poliéster habían desaparecido dejando canales huecos en su lugar. Ello indicó que las fibras de poliéster habían sido atacadas por el hipoclorito sódico a 50 °C. Las probetas hechas con BREVER1 y un velo de poliéster curado con BPO/DMA retuvieron un mejor aspecto superficial frente a las mismas curadas con Co / MEKP. El Cobalto tiene un efecto catalítico sobre el hipoclorito sódico que aumenta con la temperatura. Los productos de la descomposición del hipoclorito se cree son perjudiciales para la resina y el velo de poliéster. Los laminados basados en BREVER1 Y BREVER2 con un velo de vidrio C y curados con BPO/DMA retienen una terminación superficial de semi-brillo, y no se observa ataque a la resina después de 12 meses. Las probetas hachas con EVER1 y EVER2 y un velo de vidrio C, curadas con BPO/DMA tienen una terminación más plana de la superficie después de 12 meses. Ellas mostraron un menor ataque que el visto con el sistema de curado basado en cobalto, pero ligeramente superior al de las probetas hechas con BREVER1 y BREVER2.
Las mismas probetas fueron colocadas en tanques de almacenaje en Thornton, Colorado, USA (Tabla 3) y en la ciudad de Westminster, Colorado, USA (Tabla 4), para comparar los resultados del laboratorio con los de la vida real.
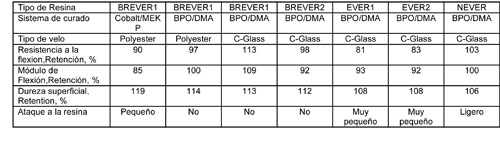
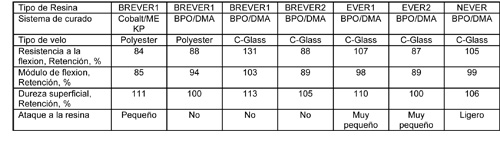
NEVER perdió brillo superficial y mostró ligeros signos de ataque a la resina. No se encontraron diferencias en las otras probetas que fueron evaluadas en estos tanques. Esto es probablemente debido a las temperaturas más bajas donde las probetas fueron expuestas.
Estos datos fueron comparados con los resultados de un estudio realizado en laboratorio durante 2 años a 40°C y en una solución estabilizada de hipoclorito sódico al 8% (5,25% durante los últimos 18 meses de exposición debido a la dificultad de encontrar NaOCl comercial del 8%). Las resinas utilizadas fueron las siguientes:
EVER3 = DERAKANE MOMENTUM 411-350 Epoxi Vinilester.
BREVER3 = DERAKANE MOMENTUM 510C-350 Epoxi Vinilester.
Estas fueron curadas con concentraciones de cobalto bajas y normales y con un sistema en base BPO/DEA en un caso, por comparación se aplicaron 2 capas de velo de poliéster NEXUSTM. Las probetas fueron post-curadas a 100 °C durante 5 horas.
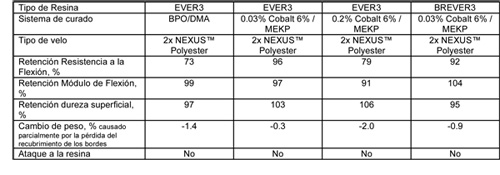
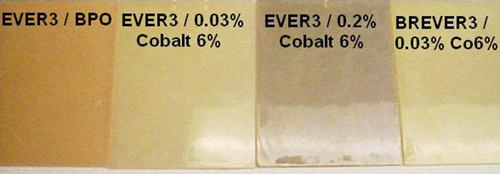
Todas las probetas de pruebas han mantenido una superficie brillante después de 12 meses y no se han deteriorado de una manera significativa. El estudio confirmó que, a 40 °C, el impacto del cobalto en el hipoclorito sódico es menos pronunciado. Sin embargo, se puede determinar que hay una diferencia entre un nivel de Cobalto 6% del 0,03%, frente al 0,2%. Ambos laminados con las resinas EVER3 y BREVER3 y curados con un 0,03% de Cobalto 6%, mantuvieron mejor el conjunto de propiedades. Por ello, podemos concluir diciendo que se pueden permitir pequeñas cantidades de cobalto en el almacenaje de hipoclorito sódico estabilizado a temperatura ambiente. El contenido en cobalto activo en un sistema de curado puede ser minimizado a través de sinergias con el potasio. Existen en el mercado mezclas comerciales de los promotores cobalto y potasio.
El efecto de la concentración de cobalto ha sido discutida en una publicación anterior (12). Se hicieron pruebas con hipoclorito sódico al 5,25% a 65 °C durante 10 meses. Se fabricaron tres probetas utilizando la resina EVER1 y curada con 0,1% de cobalto 6%/MEKP, 0,3% de Cobalto 6%/MEKP y BPO/DMA. La Figura 3 muestra el gráfico de la pérdida de peso frente al tiempo de exposición para los tres sistemas de curado. La pérdida de peso se relacionó directamente con la cantidad de cobalto. Así, mientras el sistema BPO/DMA solo perdió un 2% de su peso, el sistema curado con un 0,3% perdió un 18% y el sistema curado con el 0,1% de cobalto 6% perdió cerca de un 7%.
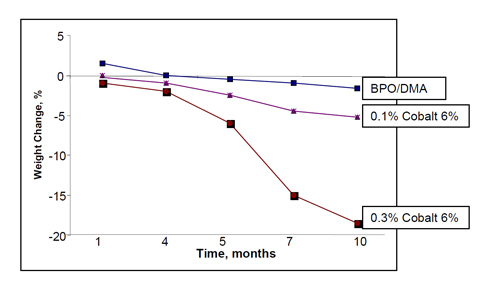
Con el fin de estudiar la influencia del tipo de velo, se hicieron probetas adicionales con la resina BREVER1 y se pusieron en contacto con hipoclorito sódico del 19% y a 65 °C. La primera probeta con una capa de velo de vidrio C fue curada con BPO/DMA, y la segunda con una capa de velo de poliéster sintético estandar y también curada con BPO/DMA. Los resultados se muestran en la Tabla 6.
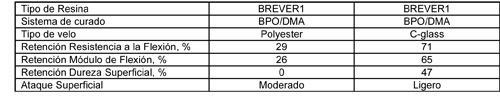
Las probetas hechas con velo de poliéster estándar, después de 12 meses se han quedado sin dureza superficial y mantienen un 28% de sus propiedades de flexión. Las probetas hechas con velo de vidrio C retuvieron un 47% de su dureza superficial y un 70% de sus propiedades de flexión. La temperatura elevada acelera la descomposición del hipoclorito sódico y hace que las pruebas sean más duras En las pruebas a 50°C, el velo de poliéster estándar fue visiblemente atacado por el hipoclorito sódico, lo que explica las diferencias vistas a 65 °C.
Otras aplicaciones
Otras aplicaciones implicando al hipoclorito sódico o derivados a pH variable (ver Figura 1) incluyen lavadores cáusticos para eliminar el cloro de los residuos o gases de combustión Mientras que los típicos lavadores para la reducción del cloro, por ejemplo en las plantas de cloro-álcali están trabajando de manera satisfactoria con la química bien definida (hidróxido de sodio, cloro, hipoclorito sódico), los gases de combustión, por ejemplo, de los incineradores de residuos industriales hacen a menudo necesario estudiar y encontrar soluciones individuales para una larga vida útil. La instalación clásica para tales sistemas de depuración de gases de combustión consiste en un enfriador, un lavador de ácidos para absorber el HCl con ácido clorhídrico, seguido de un lavador cáustico para neutralizar el HCl residual y eliminar el cloro. Sin embargo, el pH en esta segunda etapa se ajusta a 8-9 para limitar el consumo de NaOH (un pH más alto también eliminaría el CO2).Como consecuencia de ello, el cloro no se convierte completamente en hipoclorito sódico estable, con una muy alta agresividad química, actuando especialmente en la fase gas y los anillos Raschig del interior del lavador. Una temperatura elevada (>50 °C) puede además aumentar la agresividad. Un ejemplo del sistema de lavado se muestra en la Figura 4.
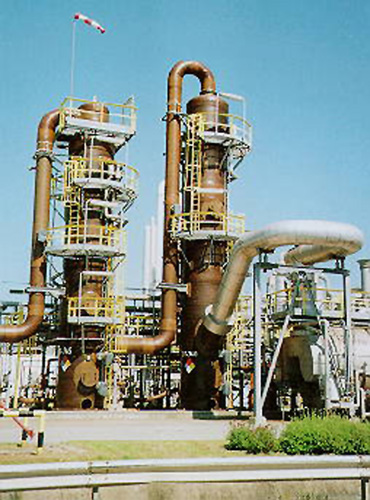
Mientras que el curado con BPO puede ayudar a mejorar la vida de servicio frente a un laminado curado con cobalto, puede requerirse y se acepta una renovación ocasional de la barrera química. Sin embargo en muchos casos se utiliza la adición de un agente reductor tal como el bisulfito sódico, para prevenir la inestabilidad química y mejorar la eficiencia del lavador. Las referencias 15, 16 y 17 revisan la química implicada en esta reacción de “decloración”. El agente reductor más efectivo en función del coste es el metabisulfito sódico. Se sugiere disolver el metabisulfito sódico en agua para obtener una solución de bisulfito sódico y dosificarlo a razón de 3 gramos de metabisulfito por 1 de cloro, aunque en teoría la relación requerida sería de tan solo 1,34: 1. Usando un agente reductor, la vida en servicio del lavador alcalino en FRP aumentará notablemente y normalmente evitará la necesidad de renovar la barrera química durante la vida del equipo.
Resumen y conclusión
Las pruebas a temperatura ambiente en un tanque de almacenaje de hipoclorito sódico y en laboratorio, muestran muy poca diferencia entre una resina epoxi vinilester bromada y una epoxi vinilester de bisfenol A estandar. Una resina vinilester de epoxi novolaca mostró algunas señales de ataque..Las pruebas de laboratorio realizadas a 50°C, aceleraron el ataque y revelaron una ventaja de las resinas epoxi vinilester bromadas sobre las vinilester en base bisfenol A. Un velo de poliéster estándar no tuvo ninguna ventaja frente al velo de vidrio C en la prueba, mientras que un velo sintético unido térmicamente tal como el NEXUS, superó de forma repetida al velo de poliester sintético y al velo de vidrio C. Esto puede ser también atribuido a la relativamente gruesa capa rica en resina que se consigue con éste velo especial.
Los principales factores que influyen en la vida de servicio de los tanques de almacenaje de hipoclorito sódico son:
- La cantidad de cobalto disponible en la resina, especialmente cuando la temperatura aumenta.
- El grado de curado como se demostró en estudios históricos y experiencias en campo.
- Las condiciones de servicio que impactan sobre la estabilidad del producto (pH, contaminantes, temperatura, luz del sol...).
Un sistema de curado libre de cobalto (BPO/Amina) en general requiere un post-curado para conseguir el mejor resultado. Por ello no es necesario escoger un sistema de curado, por ejemplo para el laminado de tanques de acero, si luego no es posible hacer un post-curado a 80 °C. Un sistema de curado clásico MEKP/bajo en cobalto, a menudo da un mejor resultado para esta aplicación, teniendo en cuenta que la solución de hipoclorito sódico esté estabilizada y por debajo de 40 °C.
El uso de un agente reductor tal como el bisulfito sódico en lavadores alcalinos de los gases de combustión de los incineradores de residuos conteniendo cloro, puede mejorar drásticamente la vida del equipo y eliminar la necesidad de la renovación de la barrera química.
Referencias
- Industry survey performed by Dow Chemical, 2004. Internal Information.
- Michael G. Stevens, ‘What is the Best Resin for FRP Sodium Hypochlorite Storage Tanks?’, NACE 2008
- Farr, J. P.; Smith, W. L.; Steichen, D. S. ‘Bleaching Agents, Survey’. Kirk-Othmer Encyclopedia of Chemical Technology. John Wiley & Sons, 1996. (Article online posting date December 4, 2000). See also references therein.
- Lister, M. W. ‘The Decomposition of Hypochlorous Acid’. Can. J. Chem. 1952, 30, 879-889.
- Lister, M. W. “The Decomposition of Hypochlorite: The Uncatalyzed Reaction” Can. J. Chem. 1956, 34, 465-478.
- Cotton, F. A.; Wilkinson, G.; Murillo, C. A.; Bochmann, M. Advanced Inorganic Chemistry. 6th ed. John Wiley & Sons, New York: 1999.
- Anbar, M.; Ginsburg, D. ‘Organic Hypohalites’. Chem. Rev. 1954, 54, 925-928. See also references therein.
- Abramovici, S.; Neumann, R.; Sasson, Y. ‘Sodium Hypochlorite as Oxidant in Phase Transfer Catalytic Systems. Part I. Oxidation of Aromatic Aldehydes’. J. Mol. Catal. 1985, 29, 291-297. ‘Part II. Oxidation of Aromatic Alcohols’. J. Mol. Catal. 1985, 29, 299-303.
- T. W. Cowley and M. A. Robertson, ‘The effect of pH and temperature on Fiberglass Reinforced Composites in Sodium Hypochlorite solutions’, NACE, 1991
- Sodium Hypochlorite General Information for the Consumer’, Odyssey Manufacturing Co., March 21, 2004.
- ASTM C-581 Standard Practice for Determining Chemical Resistance of Thermoset Resins used in Glass-Fiber Reinforced Structures Intended for Liquid Service, Annual Book of ASTM Standards, July, 2003.
- Don Kelley, ‘Fiberglass Reinforced Plastic Equipment for Treating Waste Incineration Gases’, Corrosion 2004 paper # 04617, (Houston, TX, NACE, 2004)
- Jonathon Mason, Paul Kelly, ‘Low Cobalt Initiated Glass Reinforced Plastic Systems for Bleach Service’, 10th International Symposium on Corrosion in the Pulp and Paper Industry (ISCPPI, 2001).
- DERAKANE Resin Case History E-131-2005, Ashland Inc.
- Richard Grubbs and Tom Ladshaw, ‘Low Cost Approach for Dechlorination’, Proceedings of the Georgia Water Resources Conference, 1991, University of Georgia
- Kinetic Systems Inc., ‘Technology Update: Use of Sulfites to remove Chlorine or Chloramine in High Purity Water’, June 28, 2002, www.kineticsgroup.com.
- Filmtec Membranes, ‘Water Chemistry and Pretreatment: Biological Fouling Prevention, Chlorination/Dechlorination’, Form No. 609-02034-1004, The dow chemical company, www.dow.com.
- Powell, ‘Sodium Hypochlorite Fiberglass Reinforced Plastic (FRP) Storage Tank Specification’ and ‘Sodium Hypochlorite General Information Handbook’, www.powellfab.com.
El presente artículo forma parte de la ponencia pronunciada por Michael Jaeger, de Ashland Performance Materials, en las XX Jornadas Internacionales de Materiales Compuestos, organizadas por el Centro Español de Plásticos (CEP), los pasados 23 y 24 de noviembre en Barcelona.