La tecnología Custom-Fit hacia la personalización masiva
18 de marzo de 2009
El nuevo proceso de fabricación integra tecnologías de escaneado, sistemas de CAD (Diseño Asistido por Ordenador) recientemente desarrollados y Tecnologías de Rapid Manufacturing: el escáner obtiene las características geométricas del cuerpo humano, en base a estos datos el software CAD realiza automáticamente el diseño del producto que las herramientas de Rapid Manufacturing imprimen estas partes sin necesidad de costosas herramientas, inasequibles para la fabricación de productos exclusivos como los que tratamos.
Este nuevo paradigma de fabricación ha sido ensayado sobre cinco casos de estudios: alguno de ellos relacionados con componentes personalizados en el ámbito médico – implantes de rodilla y mandíbula y prótesis transfemorales– y algunos productos de consumo particulares en que lo ‘hecho a medida’ aporta un valor añadido relevante, como los cascos de motoristas y los asientos para motocicletas.
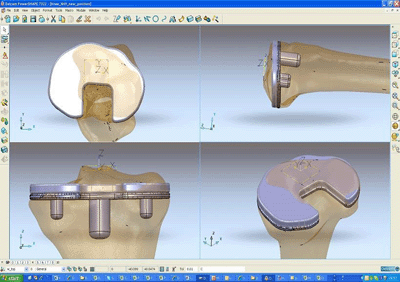
Esta nueva tecnología ha resultado un éxito en la fabricación de elementos personalizados. El proceso consiste en lo siguiente: se ha conseguido ajustar perfectamente los componentes de implantes de rodilla y mandíbula a la geometría del hueso al que tenían que adaptarse, por medio del uso de herramientas CAD que pueden operar con hueso. El escaneado CT (Tomografía Computerizada) los transforma en un formato CAD 3D estándar (denominado STL, Lenguaje de Triangulación Estándar) –véase la figura 1.
La mandíbula se imprimió con un material bio-absorbible desarrollado con una nueva tecnología denominada Impresora de Tinta de Alta Viscosidad: implante que es reemplazado en 12 meses por hueso regenerado – véase la figura 2.
El implante de rodilla se personalizó adecuándose no sólo a la forma sino también a la mezcla de material utilizado, graduado a partir de Titanio compatible con el hueso y Co-Cr de alta resistencia con la mezcla establecida según condiciones particulares del paciente. Una nueva herramienta de diseño se ha desarrollado para mantener la optimización de este material graduado (el MPTO o ‘Optimización de Topología Multi Fase’) y una nueva tecnología de Rapid Manufacturing, el Proceso de Impresión en Polvo de Metal, que es capaz de imprimir Titanio y partes de Co/Cr.
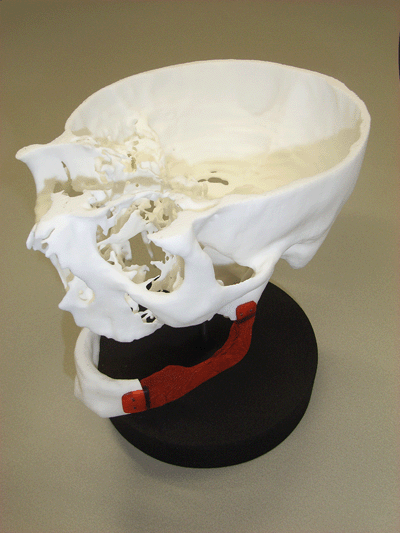
Una aproximación ligeramente diferente fue utilizada para el casco y el asiento de moto. El proceso este de personalización observaba la forma corporal externa, no los huesos escaneados con CT. En el caso del casco, se utilizó un escáner corporal láser para obtener la geometría de la cabeza del motociclista y se diseñó un recubrimiento que se ajustase perfectamente a ella; se pretende integrar la misma en el ámbito de seguridad estándar del casco, que obviamente no puede ser modificado por causas de certificación –véase figura 3.
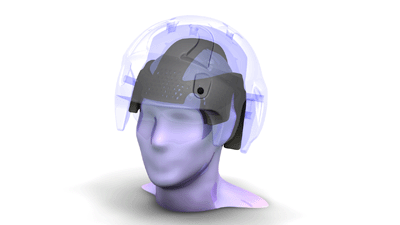
Para obtener la almohadilla con compresión graduada ha sido ideado un nuevo concepto de almohadilla, con una estructura interna constituida por elementos en forma de muelle cuya medida depende de la compresión local de la almohadilla. Esta estructura graduada ha sido posible gracias al concepto de fabricación por capas y resulta esencialmente imposible realizarla con tecnologías de fabricación tradicionales, véase figura 4.
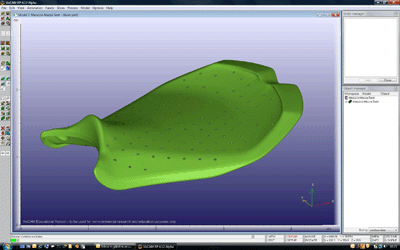