Una inyectora Allrounder 630 A para dos componentes produce mangos de PCR y TPE
Una inyectora instalación llave en mano en el contexto de una Allrounder 630 A para dos componentes fue una de las dos propuestas expuestas por Arburg en la feria K 2019, con la que demostró su competencia en cuanto a economía circular. A partir de material PCR (material reciclado posconsumo) y TPE, se produjeron mangos industriales en combinación duro-blando y para ello se combinaron los procesos de inyección de multicomponente y espumado Profoam.
La propuesta expuesta ilustró cómo el material reciclable obtenido a partir de residuos domésticos puede retornar al circuito de producción para procesar productos duraderos y de alta calidad. Arburg lo demostró en el certamen en concreto con el ejemplo de mangos industriales de material PCR espumado y TPE, que se emplean para puertas de protección de inyectoras Allrounder.
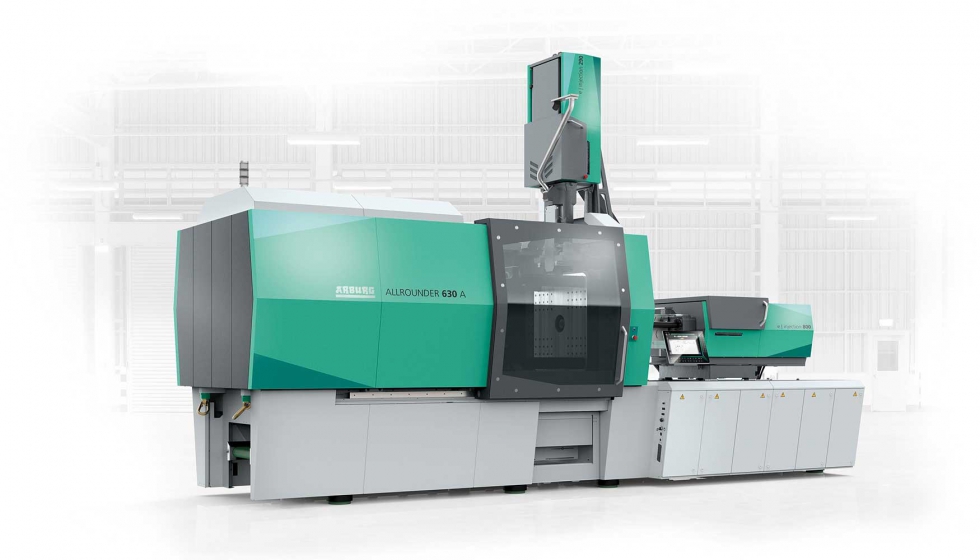
Mangos de dos componentes: un núcleo ligero, un tacto de alta calidad
Los mangos de dos componentes se inyectan en combinación duro-blando. Para ello, la inyectora Allrounder 630 A eléctrica para dos componentes con una fuerza de cierre de 2.500 kN estaba equipada con una unidad de inyección dispuesta en horizontal de tamaño 800 y una unidad de inyección vertical de tamaño 290. Para el espumado físico en el proceso ProFoam se utilizó una esclusa de granulado de 1 litro. La inyectora de diseño Clamp contaba además con un sistema de control Gestica. La manipulación la realizó un nuevo Multilift V 30 vertical. Para poder instalar la unidad de inyección vertical en la posición clásica, el sistema de robot se gira montado sobre el plato de sujeción móvil.
El Multilift V 30 tomaba inicialmente una pieza terminada de 1+1+1 cavidades de la empresa Weber Formenbau y posicionaba simultáneamente dos casquillos metálicos sobre los que luego se montó el mango terminado. Entonces el molde giraba 180 grados sobre una unidad indexíndice. Para fabricar ambas mitades del mango, se procesó PCR a base de PP (Dipolen) de la empresa mtm plastics (Borealis Group) en un proceso de inyección de espuma Profoam. Con el molde abierto, la parte superior del mango se encontraba en el lado del expulsor y la parte inferior en el lado de boquilla. Tras un giro de 90 grados, ambas piezas moldeadas se montaban directamente en el molde y se volvían a girar 90 grados. A continuación se sobremoldeaban parcialmente en la tercera cavidad con un componente de TPE (Queo) de dureza 84 Shore A de Borealis suave para mejorar el tacto. De este modo, en unos 62 segundos de tiempo de ciclo se obtenía una pieza ligera de PCR de 93 gramos con un acabado de tacto suave. El mango moldeado era aproximadamente un 10% más ligero en comparación con el moldeo por inyección con post-presión. El Multilift V 30 lo extraía y lo colocaba en una cinta transportadora.
Nuevo sistema de robot Multilift V 30
Con el nuevo Multilift V 30, Arburg amplía consecuentemente su oferta de sistemas de robot lineales. Con una capacidad de carga de 30 kilogramos, el robot vertical se ha concebido para la automatización eficiente de máquinas de inyección Allrounder de los tamaños 570 a 1120. Para un suministro de aire comprimido eficiente y de bajo consumo energético, el Multilift V 30 cuenta de serie con un dispositivo de vacío “inteligente” con función de ahorro de aire. La lubricación tiene lugar en función del rendimiento, es decir, los intervalos de mantenimiento se calculan según las velocidades, recorridos y tiempos programados. Esto supone un ahorro de tiempo de trabajo y recursos.
Espumado físico con Profoam
El proceso ProFoam destaca por la sencillez de regulación del proceso. El granulado plástico se enriquece con agente propulsor en una esclusa de granulado ya antes de la unidad de inyección. La estructura cerrada del sistema permite el empleo del dispositivo en diferentes versiones de Allrounder. En comparación con las piezas moldeadas por inyección compactas, los componentes fabricados con Profoam presentan, además de un peso inferior, menos irregularidades, deformaciones y tensiones interiores. También son posibles distintos espesores de pared Debido a la reducida viscosidad de la masa fundida cargada, las inyectoras se pueden hacer funcionar con una fuerza de mantenimiento y presión de inyección menores, lo que reduce la demanda de energía. A esto hay que añadir tiempos de ciclo más cortos. Además, se alcanza una reducción de peso significativa.
La propuesta expuesta ilustró cómo el material reciclable obtenido a partir de residuos domésticos puede retornar al circuito de producción para procesar productos duraderos y de alta calidad