Verificación volumétrica en MH mediante técnicas de multilateración
1. Introducción
La verificación geométrica en MH es uno de los aspectos importantes para garantizar que una maquina se posiciona con precisión. La normativa que se emplea para dicha verificación es la ISO 230 que define en sus diversos apartados como verificar la precisión de diferentes arquitecturas de máquinas. Desde posicionadores lineales, angulares y hasta la combinación de los mismos. Históricamente la verificación se ha establecido eje a eje o incluso por planos y analizando unos pocos grados de libertad. Además, la preparación de estas medidas es costosa y exigente desde el punto de vista del usuario. El conjunto de tecnologías empleada es diverso: interferómetros laser, niveles, ball-bar, artefactos lineales y planos, etc.
Una tendencia del mercado reside en la verificación rápida del estado de las MH. Estos chequeos rápidos permiten verificar de manera rápida el estado geométrico de la maquina sin la necesidad de procedimientos completos y complejos. La normativa ISO 230-6 [5] es un ejemplo claro de este tipo de metodologías que mediante la medición diagonal del volumen permite diagnosticar el estado de la máquina. Esta verificación se realiza nuevamente con tecnología láser o artefactos calibrados y palpador integrado en máquina. El resultado es una desviación del posicionamiento de la máquina. Este tipo de medidas también sirven para estimar el comportamiento de la MH bajo cargas térmicas, pero existen múltiples aproximaciones descritas en la ISO 230-3 [6].
Por otra parte, en los últimos años existe una tendencia creciente a sistemas [3,4] y metodologías volumétricas que permite cubrir volúmenes de trabajo y rangos superiores ofreciendo precisiones elevadas (unas pocas micras) e información completa del comportamiento de la máquina-herramienta, a diferencia de las verificaciones rápidas. Por ejemplo, la norma internacional ISO 230-1 [2] para la verificación de máquinas-herramienta, ha sido revisada en 2012 para incluir la metodología de multilateración en verificaciones volumétricas [1]. Los equipos de tipo Laser Tracker o Laser Tracer, permiten llevar a cabo las medidas necesarias con comodidad. Estos disponen de interferometría láser, actuadores angulares y software de control permite apuntar y medir distancias a los puntos de interés. La tecnología Laser-tracker, normalmente empleada para la medición de piezas y la verificación de sistemas de baja precisión, mejora sustancialmente las prestaciones cuando es utilizada siguiendo un procedimiento de multilateración. Un inconveniente del procedimiento de multilateración secuencial reside en las variaciones que sufre la máquina-herramienta durante el tiempo que duran las medidas. Este puede extenderse a 3 ó 4 horas. Aún, cuando estas medidas son muy válidas para conocer los errores de posicionamiento de la máquina en detalle, están contaminadas por las derivas térmicas. Además, el procedimiento de multilateración secuencial estándar, no es lo suficientemente ágil para capturar el comportamiento térmico, a no ser que se implementen soluciones muy específicas para automatizar completamente el proceso [7].
2. Descripción del método
La verificación volumétrica tradicionalmente se ha llevado a cabo mediante un procedimiento secuencial en el cual el dispositivo laser se ubica en diferentes posiciones (94) respecto al volumen de trabajo (Ilustración 5) de la máquina (3.000 x 2.000 x 1.200mm). La definición de estas posiciones se determina simulando la medición a priori. Desde cada ubicación se miden distancias a los mismos puntos programados para la verificación y mediante algoritmos de multilateración es posible determinar la posición XYZ de dichos puntos con mayor precisión que el indicado por el control de la MH. De este modo es posible determinar cuál es el error de posicionamiento de la maquina en puntos distribuidos por planos a lo largo de su volumen y compensar dicha desviación bien mediante tablas de compensación o modelos geométricos que estiman para cada punto la corrección a aplicar al CNC.
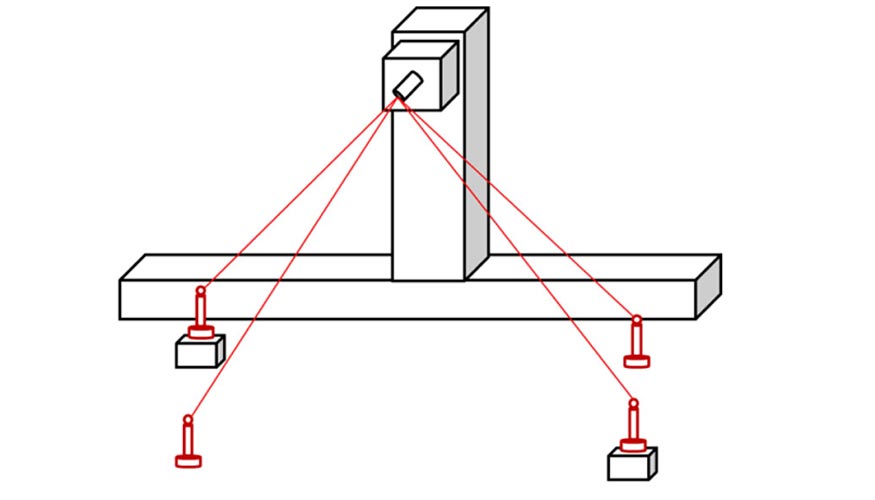
Una de las limitaciones de este procedimiento es la precisión obtenida por el procedimiento secuencial. Un indicador de esta precisión es el residuo (misfit) obtenido entre las distancias medidas y las ajustadas mediante el algoritmo de multilateración para los resultados establecidos. Este misfit puede ser debido a muchas causas, como por ejemplo: la falta de repetibilidad de la máquina, la deriva temporal de la máquina, la deformación térmica de la máquina, la incertidumbre de medida del láser, etc.
Con objeto de resolver esta problemática y mejora los resultados de la verificación volumétrica, se ha desarrollado una metodología que mide de manera simultánea la posición de la maquina empleando varios dispositivos de medida de manera sincronizada. Para poder medir la posición XYZ de un punto mediante distancias es necesario utilizar un mínimo de 3 equipos. Para garantizar una redundancia y por lo tanto mayor precisión, IK4-Tekniker ha utilizado diversas tecnologías que permiten establecer dichas distancias. Básicamente se han utilizado tanto interferómetros como distanciómetros disponibles para ejecutar las medidas. Mientras que la interferometría es relativa, los distanciómetros son absolutos. En la propia medición no es necesario tener en cuenta esta diferencia, pero sí se corrige en el procesamiento de las medidas. Este procesamiento no es en tiempo real, pero a futuro se prevé disponer de dicha capacidad.
Además de los dispositivos láser (laser-tracker, laser-tracer), ha sido necesario colocar 2 reflectores tipo Cat-eye sobre el cabezal de la máquina para poder asegurar la visión conjunta de todos los dispositivos en relación al punto de interés. Se considera que ambos reflectores se mueven con la misma precisión y como un sólido rígido.
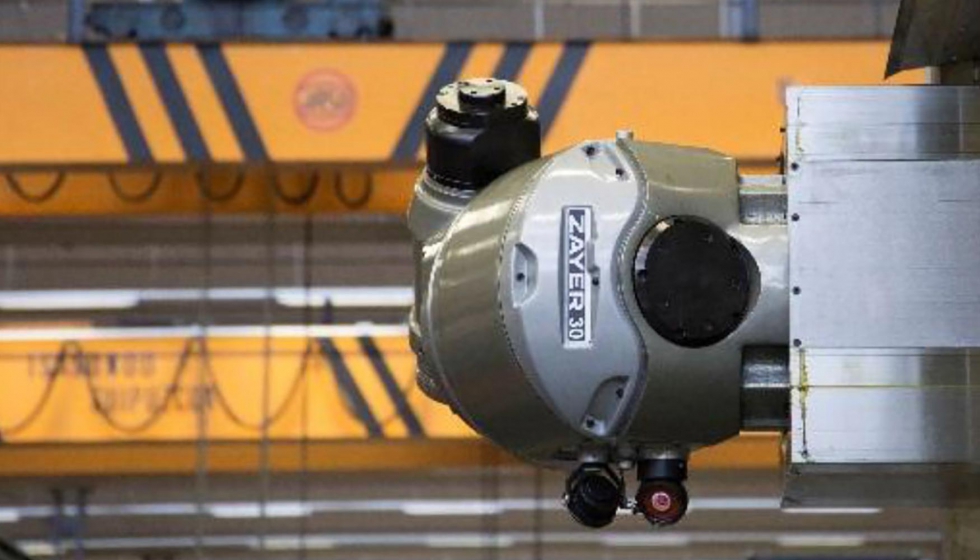
El modelo empleado a posteriori para extraer los parámetros geométricos de las coordenadas XYZ, es un modelo que contempla los errores de posición, rectitud y perpendicularidad. Para introducir otros parámetros geométricos es posible completar la medida con más estaciones de medida o incluso combinar otros sensores para la verificación angular.
La verificación de la maquina se ha repetido hasta 9 veces con lo que ha sido posible no solo ver la precisión volumétrica, sino su estabilidad temporal en función de las condiciones térmicas del entorno productivo. Con la finalidad de correlar la variación térmica con la deriva de la maquina se ha monitorizado la temperatura ambiente. Además, se han utilizado unas referencias fijas sobre el suelo para garantizar que entre medida y medida los dispositivos de medida no se han medido.
3. Medidas experimentales
Las medidas han consistido en registrar para un volumen determinado las distancias entre los dispositivos de medida (AT402, AT901 y Laser-tracer) y los reflectores para cada posición de la máquina. Para ello es necesario sincronizar los equipos y asegurar que las medidas corresponden a un mismo punto e repetición.
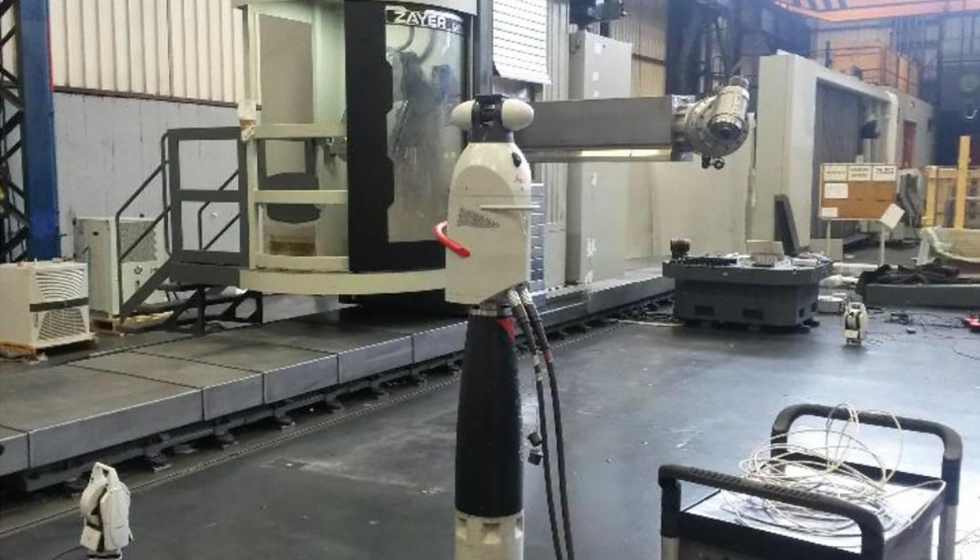
Una vez desarrolla la metodología de adquisición y aplicada correctamente, se repite este proceso tantas veces como se quiera caracterizar la máquina. En este caso se han ejecutado 9 repeticiones consecutivas durante una jornada de 6 horas. Cada medida puede llevar en torno a 20-30 min y se considera que durante este tiempo la maquina es al menos estable.
La metodología empleada ha consistido en:
- Activar la monitorización térmica de manera continua
- Verificación de referencias del suelo de manera automática
- Verificación volumétrica simultanea
- Repetir los pasos 2 y 3 (8x)
- Procesamiento de las medidas
- Interpretación de resultados
En paralelo se ha monitorizado térmicamente el ambiente durante el tiempo de ejecución de las medidas y se han medido varios puntos fijos sobre el suelo entre cada medida con objeto de asegurar que los dispositivos laser no derivan en el tiempo.
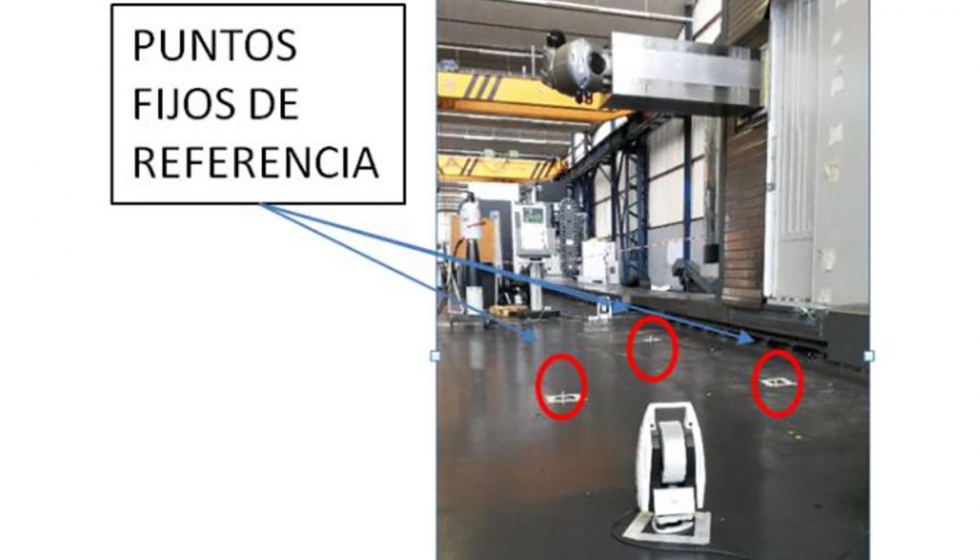
Los resultados obtenidos únicamente se han empleado para caracterizar la geometría de la MH y estudiar su comportamiento en función de la variación térmica ambiental. No se ha contemplado en esta actividad la compensación geométrica de la maquina MH.
Las medidas adquiridas por los diferentes equipos se han agrupado en tandas y se han tratado de manera independiente. Esto es, se ha obtenido un resultado del posicionamiento volumétrico de la máquina con cada grupo de cuatro medidas realizadas por los cuatro equipos de medida de manera simultánea. Cada tanda se ha procesado siguiendo el algoritmo de multilateración estándar. De esta manera, ha sido posible hacer una foto del comportamiento de la máquina cada 20/30 minutos.
4. Resultados de las medidas
Los resultados obtenidos tras el procesamiento son los siguientes:
- Precisión volumétrica
- Estabilidad geométrica de los errores
- Desplazamiento 3D de puntos de control
- Monitorización térmica durante las medidas
- Medición de los puntos de referencia del suelo
En la ilustración 5 se muestra la distribución de puntos medidos (en rojo) y puntos teóricos (en negro) a los cuales se ha enviado la MH. Dichos puntos son parte de diversos planos y rectas que a posteriori permiten ajustar el modelo geométrico.
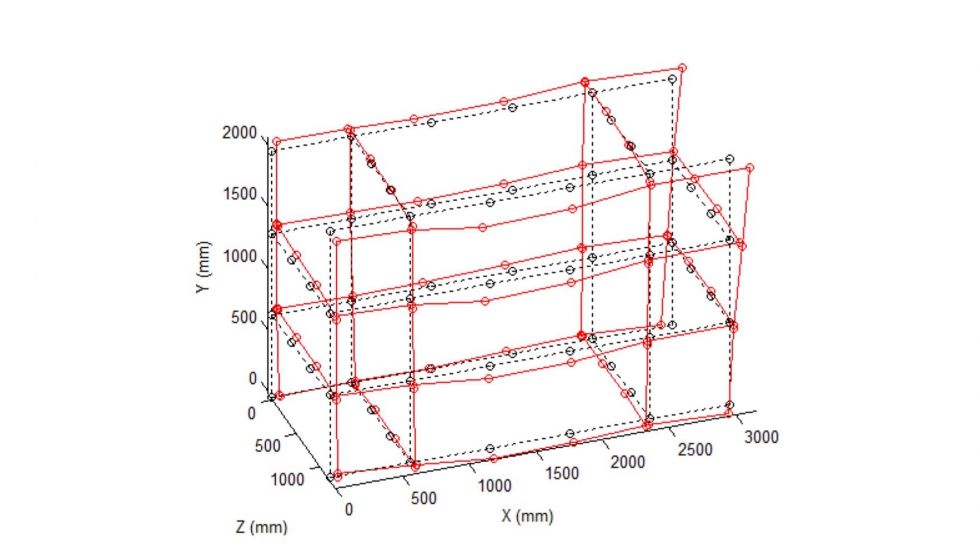
En la ilustración 6 se muestran los errores de posicionamiento en el eje X, eje Z así como las rectitudes correspondientes. Para el plano XZ y cota Y=0, también se estima la perpendicularidad entre los ejes (rectas) ajustadas. Estos resultados se obtienen para los distintos planos definidos en el volumen de trabajo.
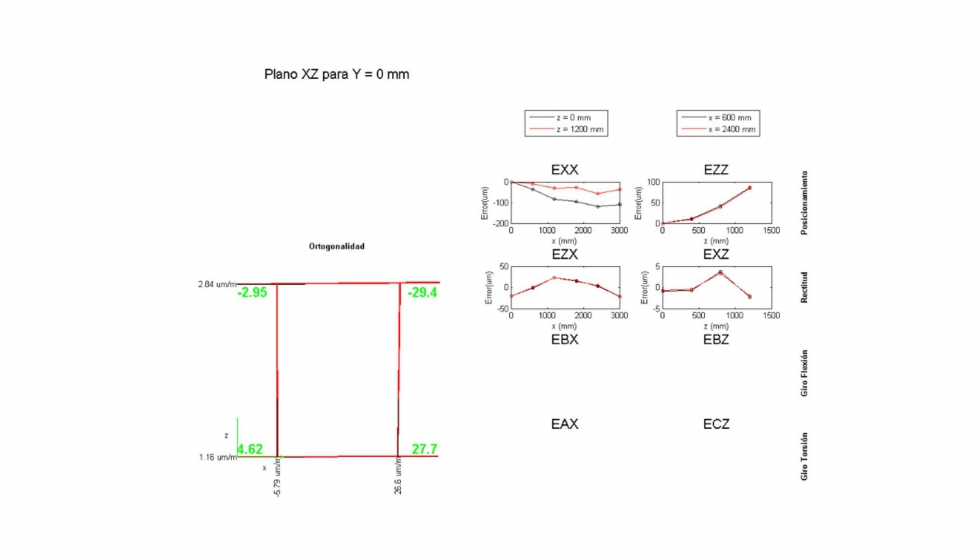
En la ilustración 7 se observa la variación para los parámetros de posicionamiento y rectitud mostrados en la ilustración 6. Se observa que la repetibilidad para distintas posiciones es alta pero que hay diferencias. El parámetro geométrico más estable y robusto frente a la variación térmica es la rectitud de los ejes ajustados.
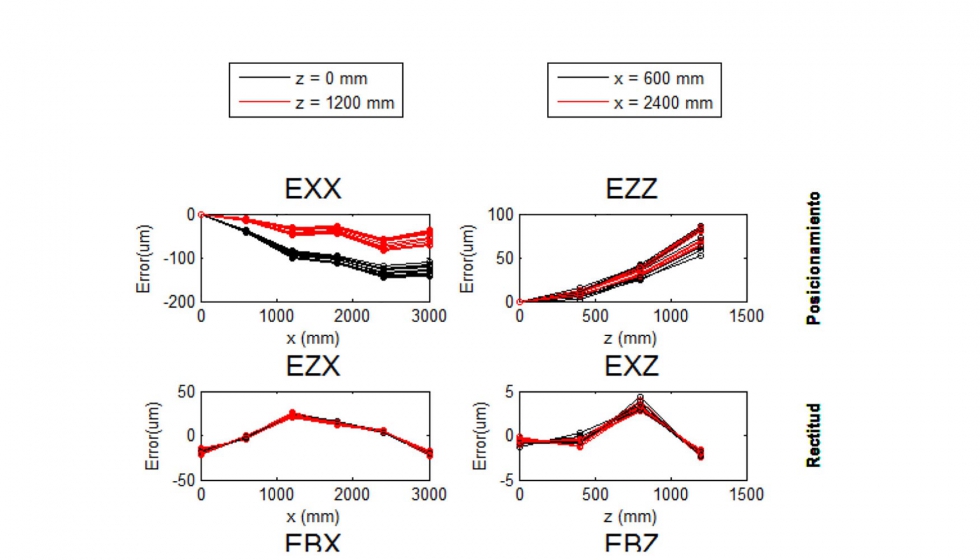
En la ilustracion 8 se muestra la variación espacial (3D) de algunos puntos del volumen de trabajo para las distintas medidas. Los resultados muestran para las medidas consecutivas que los cambios de punto a punto son progresivos (dos puntos cercanos se parecen más que dos distantes), y entre planos también hay tendencias similares. Sin embargo, no se aprecia que haya un modelo espacial determinista.
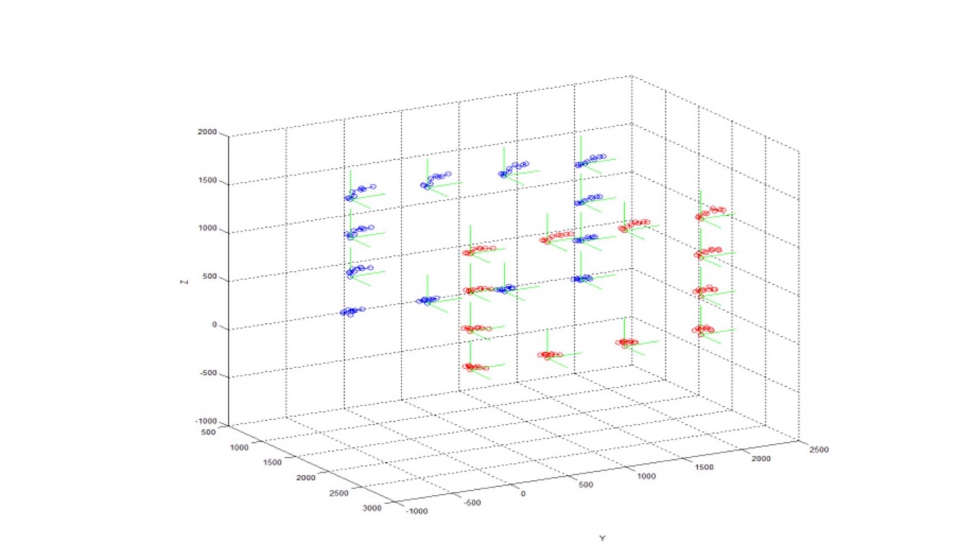
En la ilustración 9 se muestra la monitorización térmica del ambiente en el entorno productivo durante la ejecución de todas las medidas. La variación a lo largo de los ensayos es inferior a 1 °C.
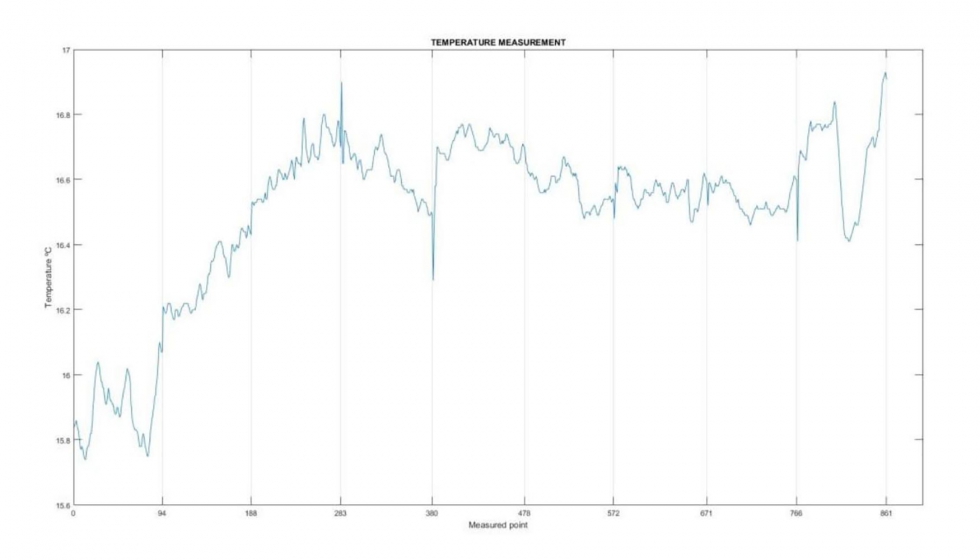
En la ilustración 10 se observa para los 3 puntos de control (1, 2, 3) la variación por cada coordenada en las distintas medidas repetidas a lo largo de todos los ensayos. La magnitud de la variación es del orden de la repetibilidad de los dispositivos empleados.
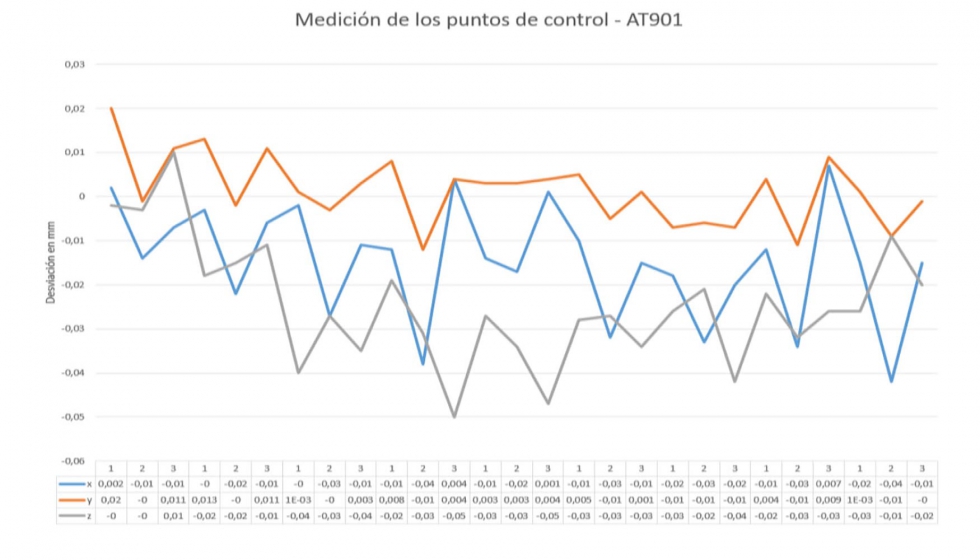
Las próximas tareas consistirán en automatizar el procesamiento de las medidas para poder disponer de un resultado justo después de la verificación. En paralelo, se prevé ajustar la deriva geométrica de la maquina a un modelo térmico que permita corregir las desviaciones de posición en el tiempo. Otra posibilidad es adaptar la metodología secuencial para que tenga en cuenta la deriva del proceso de verificación debido al efecto combinado de la propia máquina y el sistema de medida y así poder conseguir resultados más precisos. Finalmente se considerará la opción de medir en tiempo real. Para ello sin embargo es necesario llevar a cabo una primera medida volumétrica y utilizar sus resultados para triangular las distancias y determinar las posiciones de MH en tiempo real. Previamente habría que definir un alineamiento común.
6. Conclusiones
En este trabajo se han descrito las ventajas de utilizar una metodología simultánea en lugar de una secuencial. Este nuevo procedimiento es ventajoso no solo por la diferencia en tiempo requerida para la verificación, sino por los siguientes beneficios:
- Menor incertidumbre de medida
- Menor tiempo requerido para la parada de máquina (reducción de costes)
- Permite conocer la estabilidad geométrica de la máquina para condiciones térmicas variables
- Es posible repetir varias medidas en un tiempo reducido para asegurar los resultados
Las medidas realizadas en cada iteración presentan una misfit inferior a los resultados obtenidos mediante una aproximación secuencial, por lo que la metodología desarrollada con diferentes equipos de medida es válida. La redundancia de medidas incluso permite seleccionar los resultados más fiables de las distintas iteraciones. A priori las dimensiones y rango de la MH no suponen una limitación para este procedimiento.
Por último, realizar la verificación volumétrica de la máquina de manera repetitiva proporciona información muy valiosa sobre el comportamiento de la misma en función de las condiciones térmicas del entorno de trabajo. Esta información proporciona un indicador de la nobleza de la maquina en cuanto a su geometría. Incluso es factible aplicar compensaciones mecánicas o numéricas en función del rango de Tª a la que trabajaría la máquina.
7. Referencias
[1] 478E.B. Hughes et al. Design of a High-Accuracy CMM Based on Multi-Lateration Techniques. CIRP Annals - Manufacturing Technology, 2000; 49: 391-394.
[2] International Organization for Standardization, ISO 230-1:2012, Test code for machine tools - Part 1: Geometric accuracy of machines operating under no-load or quasi-static conditions.
[3] H.Schwenke et al. Geometric error measurement and compensation of machines. An update. CIRP Annals - Manufacturing Technology, 2008; 57: 660-675.
[4] H.Kunzmann et al. Error mapping of CMMs and machine tools by a single tracking interferometer. CIRP Annals - Manufacturing Technology, 2005; 54:475.
[5] International Organization for Standardization, ISO 230-6:2002. Test code for machine tools — Part 6: Determination of positioning accuracy on body and face diagonals (Diagonal displacement tests)
[6] International Organization for Standardization, ISO 230-3:2007. Test code for machine tools — Part 3: Determination of thermal effects
[7] Gomez-Acedo, E.; Olarra, A.; Zubieta, M.; Kortaberria, G.; Ariznabarreta, E.; de Lacalle, L. N. Method for measuring thermal distortion in large machine tools by means of laser multilateration. Int. J. Adv. Manuf.Technol. 2015, 80, 523–534.