Estado del arte de las diferentes aproximaciones al rectificado de caras
El objetivo de este trabajo es el de hacer una clasificación de las diferentes estrategias usadas en rectificado de caras, así como un análisis superficial de la cinemática de cada una y un examen de los requerimientos tecnológicos necesarios. Se considera este trabajo como el primer paso de un análisis más profundo para la definición del método y de los parámetros de corte óptimos para cada caso.
1. Introducción
El rectificado y la problemática que este proceso plantea han sido ampliamente estudiados por autores como Guo, Malkin o Marinescu entre otros [1] [2], aunque el caso concreto del rectificado de caras no ha sido aún explorado por completo en un sentido analítico.
Un primer intento en este sentido es un artículo de 2005 escrito por Oliveira [3] en el que centra la atención en el rectificado de caras. Oliveira plantea diferentes estrategias con el fin de evitar el dañado térmico de piezas, así como un desgaste excesivo de la muela. Las estrategias planteadas son, el avance axial, el avance axial por etapas y el avance radial o en plunge. Basándose en este trabajo Krajnik publica en 2016 un estudio sobre rectificado de ejes en el que se puede encontrar un apartado dedicado al rectificado de las caras laterales de cigüeñales [4]. Este estudio trata un caso práctico de una patente de Scania de 2015 [5] en la que se calculan los parámetros básicos de la cinemática del rectificado de caras. El rectificado de caras de cigüeñales con muela de CBN es una aplicación del rectificado de caras, aunque este proceso puede ser usado en muchas más aplicaciones.
Estos trabajos preliminares son de gran interés, puesto que plantean una comparativa entre diferentes estrategias para un mismo fin. De esta forma se asientan las bases que llevarán a una serie de experimentos que a su vez completen una guía de producción sobre este proceso.
Además, en este trabajo se trata de hacer una comparación entre las diferentes estrategias de rectificado de caras mediante un análisis descriptivo de cada una. Lo que se busca es poder generar un documento de referencia en el que se agrupen las características, cinemáticas, dinámicas y térmicas del proceso de rectificado de caras, así como características de flexibilidad de proceso y productividad. Las diferentes estrategias y técnicas analizadas en este trabajo se listan a continuación y se añade una lista gráfica en la tabla1.
- Rectificado angular de caras
- Avance axial
- Plonge angular
- Contorneado
- Rectificado recto de caras
- Plonge radial
- Plonge angular
- Avance axial
- Avance axial por etapas
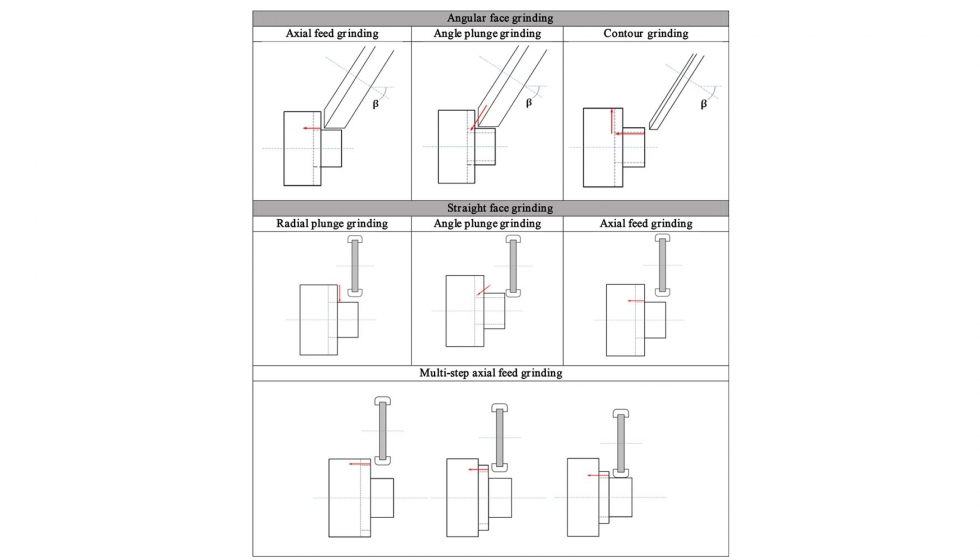
Los principales problemas a la hora de la clasificación son el riesgo de dañado térmico, el desgaste de muela, aunque se han de tener en cuenta otros factores como la flexibilidad del proceso, la productividad o la inversión necesaria.
2. Técnicas de rectificado de caras
Para plantear las diferentes estrategias del rectificado de caras se ha de comenzar por establecer los parámetros geométricos principales además de describir las partes involucradas en el proceso y fijar los movimientos implicados. Una vez expuestos los parámetros cinemáticos se analizarán las fuerzas, las potencias y las temperaturas.
En primer lugar, se van a diferenciar las dos técnicas analizadas, el rectificado con muela recta y con muela angular (ver figura 1). Ambas técnicas se usan para rectificar la cara plana de un eje, representada en este trabajo como la pieza mostrada en la figura 3 en la que ????1 es el radio interior y ????2 es el radio exterior. El rectificado recto usa una muela recta y el eje de la pieza y el de la muela serán paralelos durante el proceso. Por otro lado, el rectificado angular usa una muela con sus facetas en ángulo y los ejes de muela y pieza no serán paralelos. Este simple hecho es de vital importancia ya que tiene un efecto directo sobre la longitud de corte, que será mucho mayor en el rectificado con muela recta. Longitudes de corte diferentes implican una situación térmica diferente que requiere un análisis diferente.
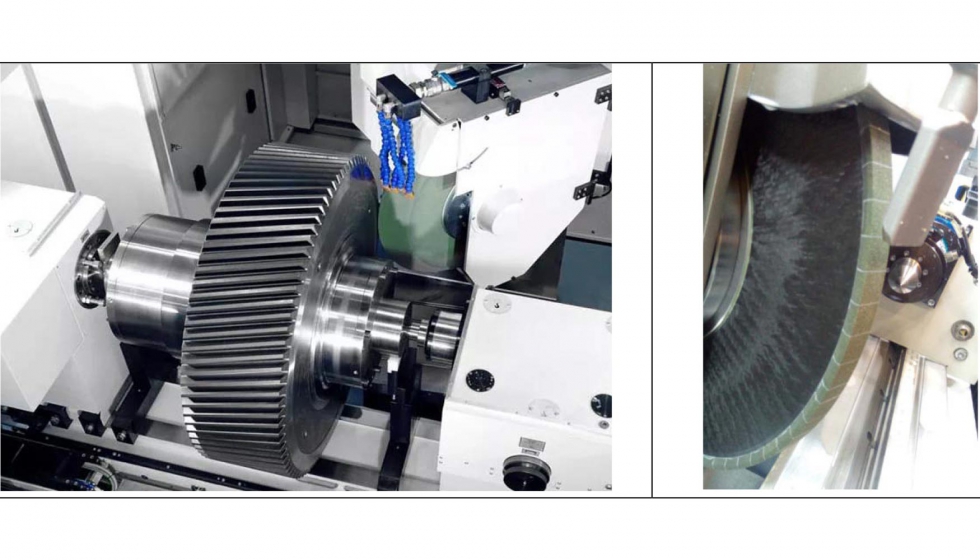
Tres parámetros para definir un proceso de rectificado son el grosor de viruta indeformada ℎ𝑐𝑢, la longitud de contacto 𝑙𝑐 y el caudal de viruta 𝑄. La longitud de contacto caracteriza el contacto entre pieza y muela, en el área de contacto se va a producir un intercambio de calor y el tamaño de esta área es un factor de mayor importancia en la temperatura que alcanzará la pieza. Si toda la acción de corte está concentrada en una pequeña área, también será así con el calor transmitido a la pieza mientras que si esta área es mayor el calor se esparcirá. El caudal de viruta es un parámetro que representa el proceso en sí ya que indica la cantidad de material que se está arrancando por la muela por unidad de tiempo. Por último, el espesor de viruta indeformada es el espesor previsto del material arrancado en cada contacto de la muela con la pieza. La relación entre el espesor de viruta indeformada y de la longitud de corte da una idea de la eficiencia del corte, una longitud de contacto larga, con un espesor pequeño, hacen un corte poco eficiente mientras que una viruta corta pero profunda indican que el corte es más eficiente.
Se puede definir un nuevo parámetro cinemático, 𝑄′ o tasa de arranque, que representa la cantidad de material arrancado por unidad de tiempo y por unidad de ancho del perfil de la muela. Este parámetro permite comparar entre distintas técnicas y estrategias de rectificado y muestra la eficiencia de todo el proceso en conjunto. El problema viene cuando los parámetros de corte no son constantes a lo largo de la longitud de contacto, la tasa de arranque no tiene un valor único que se pueda tomar como representativo de todo el proceso.
En rectificado, la temperatura alcanzada por la pieza es un factor decisivo, la mayor parte de la energía necesaria se convierte en calor, un valor ampliamente aceptado en la bibliografía es que un 60-85% del calor generado es conducido a la pieza [6]. Esto es algo a tener en cuenta a la hora de diseñar un proceso de rectificado porque las consecuencias del daño térmico son, entre otras, cambios de fase y tensiones residuales. Una tasa de arranque que no es constante a lo largo de la longitud de corte significa que la distribución de calor a lo largo de esta tampoco lo es y por eso es importante conocer bien esta distribución, para poder proveer con precisión el daño térmico local. Para evitarlo es necesario conocer la cantidad de calor transportada a la pieza, el porcentaje de energía que se convierte en calor, las condiciones de corte, y la distribución del calor a lo largo de la longitud de corte. Estos factores suelen variar de una estrategia de corte a otra y es típico establecer condiciones límite para evitar el dañado térmico.
2.1. Rectificado recto de caras
Una característica representativa de esta técnica es la zona de contacto b la cual es muy reducida en comparación con una muela recta convencional. Esta reducción se da con el principal objetivo de reducir el roce excesivo de esta zona con la pieza ya que la muela y la pieza están en contacto total. Este término es una traducción del inglés ‘total contact’ el cual aparece en el libro [4] de Guo Malkin. En la figura 2 se puede ver una representación del perfil de una muela recta de avance axial. Entre la faceta para el rectificado con avance axial b y la faceta para el rectificado cilíndrico se puede observar r0 el cual representa el radio de esquina. En el trabajo realizado por Krajnik [2] se puede ver una división entre las tres zonas y los parámetros cinemáticos definidos para cada zona.
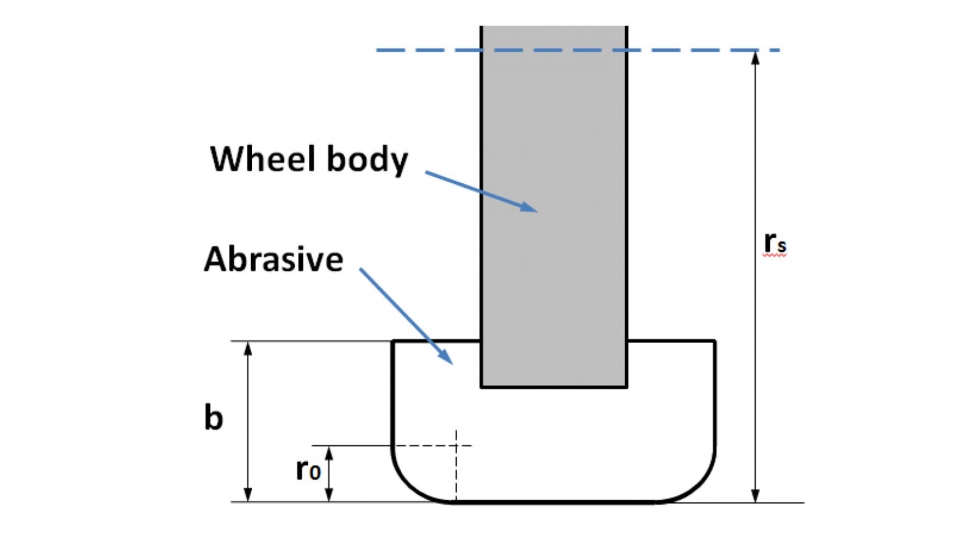
La longitud de corte en una operación con muela recta es claramente mayor que en otras operaciones de rectificado y puede ser calculada mediante el arco entre la muela y la pieza.
Como menciona Marinescu en su libro [2] el arranque de material en una operación de rectificado de caras con muela recta está concentrado en el borde de la muela. A esto se ha de añadir que si se tiene un radio de esquina como el de la figura 2 el corte estará concentrado ahí, de esta forma el resto de la faceta solamente está rozando la pieza.
2.2. Rectificado angular de caras
La característica principal en rectificado angular es que el eje de la pieza y el de la muela no son paralelos. Esto tiene una influencia directa en los parámetros cinemáticos previamente mencionados. El diámetro equivalente en la zona de corte se ve influenciado por el ángulo ß, el cual se puede ver en la figura 3. En consecuencia, la longitud de corte también depende de ß la cual es significativamente menor que en un rectificado con muela recta. El rectificado angular es en cierto sentido similar al rectificado plano, la geometría de la zona de contacto está formada por una superficie plana, la pieza, y por la pieza que tendrá un diámetro equivalente mayor debido al ángulo al que está inclinado.
La tasa de arranque en este caso será la cantidad de material arrancado por la zona AB de la figura 3 en cada punto del perfil de la muela.
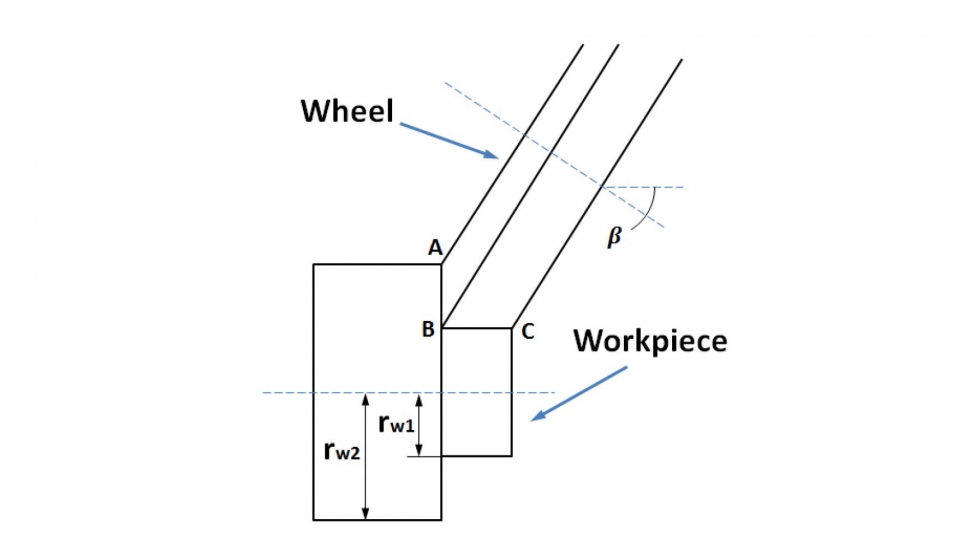
3. Estrategias de rectificado
En los experimentos llevados a cabo por Oliveira en [3] se comparan por primera vez diferentes estrategias para el rectificado de caras. El objetivo es analizar diferentes maneras de producir la misma pieza usando el mismo proceso, pero cambiando las condiciones de corte y optimizar el proceso de cara al daño térmico y al desgaste de muela. Estas estrategias están aplicadas únicamente al rectificado recto de caras, pero un experimento similar podría ser llevado a cabo incluyendo la técnica del rectificado angular en la cual la estrategia más usada es el avance axial. Como se ha mencionado antes la productividad y la economía del proceso también han de tenerse en cuenta.
3.1. Rectificado recto con avance axial
En esta estrategia se está rectificando toda la cara de la pieza al mismo tiempo. La muela se mueve en vacío hasta el interior de la pieza, rw1, y después en dirección axial rectificando la pieza. Es evidente que, aunque las condiciones de corte sean variables a lo largo de la longitud de contacto se mantendrán teóricamente constantes durante el proceso. En la tabla 1 se puede ver una representación esquemática del rectificado de caras con avance axial.
El problema principal con el rectificado con muela recta y avance axial es que las condiciones de corte no son las mismas a lo largo de la longitud de corte. Además, como el corte está concentrado en el radio de esquina el desgaste de muela es muy severo en una zona pequeña del perfil.
3.2. Rectificado recto con avance axial por etapas
La estrategia del avance axial por etapas consiste en realizar varios avances axiales de una menor profundidad radial hasta conseguir rectificar la totalidad de la cara. En la tabla 1 se puede ver un ejemplo en el que se realiza el rectificado de la cara en 3 etapas de una misma profundidad axial.
En comparación con la estrategia de una sola etapa, hacer varias etapas implica distribuir el material arrancado en los diferentes tramos, así como el calor generado por el corte. Un problema de esta estrategia es que si se subdivide el corte de la cara en tres etapas se tardará por lo menos tres veces más en completar la operación que si solamente se necesita avanzar una vez sobre la pieza.
Oliveira concluye en su artículo [3] que se puede tener un mejor control sobre el calor transmitido a la pieza usando esta estrategia.
3.3. Rectificado recto en plonge radial
En una operación en la que se utilice la estrategia de plonge radial la muela comienza a rectificar la pieza desde el diámetro exterior hasta el interior. Se posiciona la muela de forma que se rectificará todo el avance axial de una sola vez y se avanza en la dirección radial de la pieza. La zona de corte al usar esta estrategia de rectificado será similar a la de una cilindrado y evidentemente mucho menor que en
cualquier operación en la que se avance axialmente hacia la pieza. Una consecuencia de tener una longitud de corte mayor es que el calor estará más concentrado.
3.4. Rectificado angular con avance axial
Se trata de la estrategia más sencilla con una muela angular, la muela se mueve paralela al eje de la pieza a una cierta velocidad de avance.
Como se ha dicho la cinemática del rectificado angular es muy similar al del rectificado plano salvo que la longitud de corte y el diámetro equivalente están distorsionados por el ángulo ß [2]. La longitud de corte es significativamente menor que en un rectificado con muela recta y la tasa de arranque está distribuida de manera constante a lo largo del perfil de la muela. Esto significa que el calor generado también estará distribuido de la misma manera.
3.5. Rectificado angular por contorneado
El objetivo principal de usar una estrategia como el rectificado por contorneado es la de usar una muela más simple que reduzca el área de contacto y así flexibilice el proceso. Esta estrategia, también llamada peel grinding, contour grinding, o rectificado de forma, según el autor o el documento, trata de rectificar la pieza por completo en una sola atada según Klocke [8]. Esta estrategia es más adecuada para lotes pequeños de piezas con varios rectificados distintos y que necesiten de un proceso flexible manteniendo una cierta sencillez. Klocke afirma que con la misma muela de rectificado por contorneado se puede cilindrar, rectificar caras, chaflanes y perfiles cóncavos y convexos con un buen acabado superficial.
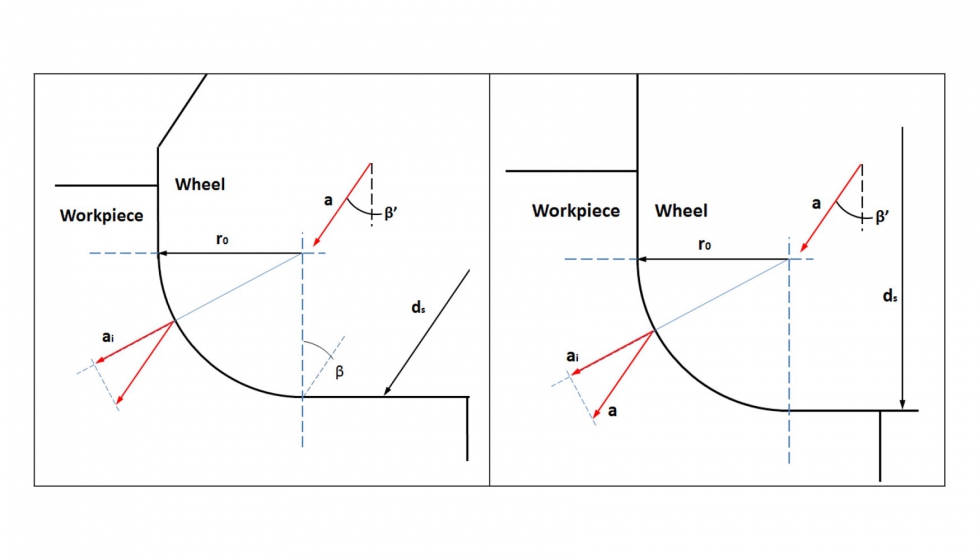
3.6. Rectificado de caras con avance angular
En una operación real es habitual querer rectificar el diámetro y la cara de una pieza al mismo tiempo y con la misma muela, para ello se usa un avance combinado entre el radial y el axial. En la Figura 4 se puede ver el perfil de ambos tipos de muela aquí analizados, el avance está inclinado un ángulo β' que define esta estrategia de rectificado.
Aunque todos los puntos del perfil se mueven de forma idéntica solamente se considera en cada punto el avance perpendicular a su superficie ai [4]. De esta forma en lo que a la cara respecta se tienen un avance perpendicular a la misma, la componente perpendicular de ai.
4. Consideraciones de máquina
Cada caso de producción debería llevarse a cabo usando la técnica que mejor se adapte a la situación teniendo en cuenta las variables concretas del proceso.
- El rectificado con muela recta es, por lo general más versátil que el angular. Esto es debido a que al ser los ejes paralelos y tener una faceta de corte vertical a cada lado es posible rectificar dos caras opuestas con la misma muela. Si se quiere usar una muela angular, la máquina debe estar equipada con un eje B que permita el giro de la muela permitiendo así un cambio de herramienta y así poder rectificar las dos caras opuestas.
- La misma muela recta es capaz de rectificar una multitud de geometrías de pieza distintas mientras que la muela angular está limitada por su propia geometría. Por ejemplo, una muela angular solo podría rectificar de una sola vez una cara de un tamaño menor o igual al de su faceta de dedicada a esta función. Por otro lado, una muela recta es capaz de rectificar caras de múltiples tamaños debido a la cinemática de la propia técnica.
- El rectificado recto es útil también a la hora de rectificar en una zona estrecha de difícil acceso mientras que el rectificado angular necesita un mínimo de espacio.
- Es posible flexibilizar aún más el proceso de rectificado si se usa una estrategia de rectificado por contorneado. Es recomendable buscar el equilibrio entre el tamaño de lote y el objetivo del rectificado a la hora de elegir qué tipo de rectificado se va a elegir.
- El diamantado de las muelas es algo a tener en cuenta porque se debe diseñar un diamantador capaz de diamantar las muelas que se vayan a usar. Además, la propia estrategia de rectificado puede ser que necesite de más grados de libertad para el propio diamantador. Aquí los factores clave son el perfil de la muela y la arquitectura del módulo de diamantado de la muela.
- En cuanto a la lubricación-refrigeración el rectificado con muelas rectas puede ser un problema. La posición de muela y pieza impide un acceso directo a la zona de corte, no así en rectificado angular. Además, la longitud de corte tan grande hace necesario que se usen muchas toberas de refrigeración. Para esto el rectificado por etapas puede ser una solución.
- Las dos técnicas de rectificado dejan un acabado superficial diferente, aunque es destacable que también lo son las marcas dejadas por la herramienta. En un rectificado con muela angular las marcas serán tangentes al punto de contacto y por el contrario en rectificado recto las marcas dejadas serán espirales que son dependientes de las condiciones del proceso [7].
5. Conclusiones
Como conclusión a este trabajo se han destacado los siguientes puntos.
- Se ha realizado una recopilación de información en torno al rectificado de caras en la que se han recogido las presentes técnicas usadas.
- Se han formulado los problemas principales a la hora de rectificar caras explicando los factores que afectan a estos problemas.
- Se ha realizado una clasificación de las posibles técnicas y de las diferentes técnicas existentes para así poder destacar sus ventajas e inconvenientes.
- Se ha proporcionado información sobre la arquitectura necesaria en las máquinas para cada una de las estrategias.
- Se ha dado un primer paso en el diseño de un guía de producción para el rectificado de caras el cual da pie a un análisis más exhaustivo de cada una de las arriba mencionadas estrategias.
Referencias
[1] S. Malkin, C. Guo. (1989). ‘Grinding technology: Theory and application of machining with abrasives’ Ellis Horwood Ltd.
[2] I. Marinescu et al. (2004) ‘Tribology of abrasive machining process’. William Andrew publishing.
[3] Oliveira, J. F. G. et al, (2005). ‘Analysis of grinding strategies applied to crankshaft manufacturing’ CIRP Annals, 54(1), 269-272.
[4] P. Krajnik, R. Drazumeric et al. (2016). ‘High-Performance Industrial Grinding: Recent Advances and Case Studies from the Automotive Engine Production’, ISAAT 2016.
[5] P. Krajnik, R. Drazumeric, R. Roininen. (2015). ‘Method of grinding a workpiece having a cylindrical bearing Surface and method for determining processing parameters’ EU Patent EP15175782.
[6] S. Malkin, C. Guo. (2007) ‘Thermal analysis of grinding’ Annals of the CIRP 56/2, 760-782.
[7] A. J. Shih, N. L. Lee. (1999) ‘Precision cylindrical face grinding’ Precision engineering 23 177-184.
[8] F. Kolcke. (2009) ‘Manufacturing Process 2, Grinding, Honing, Lapping’ RWTH edition.