El mecanizado por ultrasonidos rotatorio y el mecanizado mixto fresado/láser
El mercado actual exige el lanzamiento de productos cada vez más novedosos y competitivos, por lo que se necesita realizar un esfuerzo añadido para fabricar productos tecnológicos avanzados mediante procesos de fabricación “tradicionales”, lo que no siempre permite obtener el resultado esperado. Por otra parte, la introducción de “materiales avanzados” en sectores como la medicina, óptica, aerospacial o automoción está suponiendo un obligado desarrollo de procesos de fabricación alternativos para dar respuesta a las nuevas necesidades. El coste considerablemente superior de estas técnicas limita su uso exclusivamente a los casos en los que no se puedan emplear los métodos tradicionales.
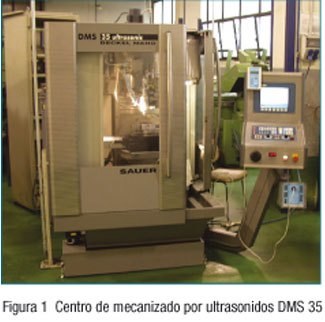
El mecanizado por ultrasonidos rotatorio ante el reto de los materiales duros y frágiles
El creciente desarrollo de los materiales avanzados con propiedades superiores como alta dureza, gran resistencia mecánica al desgaste, baja densidad y resistencia a la abrasión a altas temperatura, como es el caso de las cerámicas técnicas, ha introducido la necesidad de su procesado. Sin embargo, el alto coste de mecanizado, que oscila entre el 30-60% e incluso el 90% del coste de producción, ha frenado claramente su expansión comercial.
En este punto, cabe subrayar que sólo los comúnmente denominados procesos no convencionales de mecanizado, como el mecanizado por ultrasonidos rotatorio, pueden llegar a ser útiles, aparte de algún proceso abrasivo convencional.
Para alcanzar este reto Tekniker ha adquirido un centro de mecanizado por ultrasonidos DMS 35 Ultrasonic de la casa Sauer integrada en Deckel Maho Gildemeister. Dicha máquina incorpora la tecnología RUM (Rotary Ultrasonic Machining) para el mecanizado de materiales duros y frágiles.
El proceso del mecanizado por ultrasonidos rotatorio (Rotary Ultrasonic Machining-RUM) es un avance tecnológico del clásico mecanizado por ultrasonidos (Ultrasonic Machining-USM). Se basa en la eliminación de material mediante la combinación de giro y vibración en dirección axial de una herramienta, generalmente de diamante que, a su vez, se alimenta con una corriente interna-externa de fluido de corte.
El término “ultrasonidos” es debido a que la vibración se produce a una frecuencia próxima a los 20kHz (vibra unas 20.000 veces por segundo), frecuencia que está en el rango de los ultrasonidos. Se emplean regímenes de giro de entre 1000 y 6000rpm, y la vibración axial tiene unas pocas µm de amplitud (1-35µm).
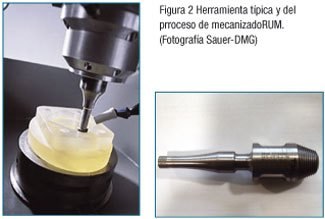
Así mismo, la máquina de Tekniker incorpora una serie de algoritmos de control que mejoran aún más la efectividad del proceso preservando la integridad de la herramienta y de la pieza; así, el control ADC (Adaptive Control) monitoriza el par y el ACC (Acoustic Control) monitoriza la fuerza en dirección axial.
El ámbito de aplicación del RUM está dirigido fundamentalmente al mecanizado de materiales duros y frágiles como las cerámicas técnicas, los vidrios, metales endurecidos, Silicio, piedras preciosas, etc.
Todo ello aplicado a:
- Industria del automóvil: discos de freno, toberas de inyección, insertos de moldes de inyección…; en materiales como Nitruro de Silicio, Alúmina, metal duro, acero templado (55HRc)...
- Industria de los semiconductores: plaquitas (Wafer), elementos de refrigeración…en materiales como Silicio, Cuarzo Hialino…
- Industria óptica: lentes cóncavas y convexas, espejos…; en materiales como Zafiro, Silicio, Zerodur y vidrios varios.
- Industria médica: articulaciones, coronas dentales…; en materiales cerámicos varios como Zirconia, Alúmina…
- Varios: guías antidesgaste, pirometría, boquillas de soldadura, aisladores térmicos…; también en materiales cerámicos.
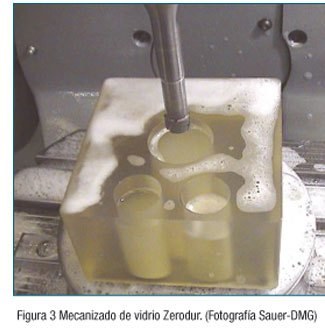
Mediante RUM se pueden mecanizar geometrías que difícilmente podrían conseguirse con otros procesos de fabricación como por ejemplo agujeros de Ø0.5 y 10mm de profundidad en Silicio, roscado interior en metal duro calidad H6, etc.
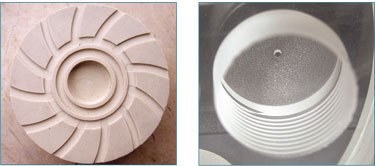
Figura 4 Ejemplo de mecanizado de alúmina y roscado en vidrio óptico.
- Reducción de los esfuerzos de corte, de la carga térmica a la pieza y con ello el desgaste de la herramienta debido al menor tiempo de contacto de cada grano abrasivo con el material de pieza, inherente al movimiento ultrasónico.
- La superposición de movimientos, rotación y giro, hace que se obtengan mayores tasas de arranque que en el caso de los procesos convencionales como el rectificado (hasta 5 veces mayores).
- Gran acabado superficial debido a las menores fuerzas del proceso, pudiéndose obtener superficies con rugosidades menores que 0.2 µm Ra hasta suprimir el pulido.
- El movimiento ultrasónico junto con el refrigerante interno y externo hace que la herramienta experimente un proceso de autolimpieza, evitando así el fenómeno de embotamiento y facilitando el regenerado de la misma.
- El proceso produce una capa superficial de tensiones residuales de compresión por lo que se aumenta la vida a fatiga.
- Se pueden tratar materiales duros y frágiles llevando a cabo pequeñas operaciones de corte, desde 0.5mm así como diversas operaciones en una sola máquina, a saber taladrado y fresado: agujeros de gran profundidad, contorneados, ranurados, planeados o superficies complejas.
Con todo ello, hay que concluir remarcando que el mecanizado por ultrasonidos rotatorio aparece como una clara solución para el procesado óptimo de materiales avanzados como cerámicas, metales endurecidos, vidrios, etc.
Mecanizado mixto fresado/láser: tecnología que posibilita nuevos retos
La necesidad de crear productos cada vez más precisos, y con un amplio rango de materiales, exige nuevas técnicas de procesado, para ir más allá de las actuales técnicas de procesado por arranque de viruta.
Con el objetivo de alcanzar este reto, Tekniker dispone de una máquina fresadora-láser DMU60L del fabricante DECKEL MAHO, que además de ser una fresadora de alta velocidad con un husillo que puede alcanzar las 18.000 rpm, dispone de un cabezal láser de Nd:YAG de 100 Wattios. La máquina adquirida por Tekniker incorpora la tecnología del mecanizado por láser.
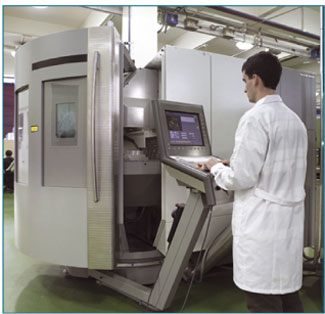
La tecnología del mecanizado por láser posibilita el mecanizado de figuras y piezas de pequeñas dimensiones, permitiendo obtener esquinas vivas y agujeros de pequeño diámetro, es decir, formas geométricas que no es posible o es muy costoso obtener mediante procesos convencionales.
El mecanizado por láser permite el procesado de casi todo tipo de materiales, independientemente de su dureza o maquinabilidad. Los resultados obtenidos varían de un material a otro debido a sus propiedades físicas, pero en principio no se encuentra el obstáculo de la dureza. Se pueden obtener piezas a partir de fotografías, es decir, partiendo de una imagen se consigue un proceso parecido al grabado (tal y como se aprecia en la figura 6).
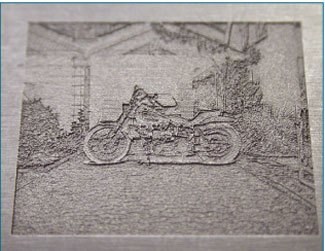
La alta densidad de energía que se obtiene en el punto de enfoque del haz láser permite llevar a cabo el proceso de ablación, es decir, el material es vaporizado directamente. Por otra parte, al ser una fuente de energía la que incide sobre el material, no se producen desgastes, roturas, ni colisiones de la herramienta de corte, lo que supone una gran ventaja al proceso de arranque de viruta tradicional. El valor del diámetro de haz en el punto de enfoque puede ser de 40 micras o de 100 micras.
El láser, es una fuente de luz coherente de alta energía cuyo significado es Amplificación de luz por Emisión de Radiación Estimulada, que en inglés forman las siglas LASER (Light Amplification by Stimulated Emission of Radiation). El sistema láser principalmente consta de tres componentes:
- Un medio activo que en nuestro caso es un cristal de Nd:YAG.
- Un medio de excitación que en nuestro caso es una lámpara.
- La óptica del resonador.
En la máquina disponible en Tekniker el sistema láser consta de una lámpara de 6000W que irradia una luz que tiene como propiedades que es divergente, multicolor e incoherente. Dicha luz excita el medio activo (cristal de Nd:YAG) produciendo un haz láser que en comparación con la bombilla tiene propiedades direccionales, monocromáticas y coherentes, siendo su longitud de onda l=1.064 micras, y una potencia media de 100W.
Este haz láser es reflejado al 100% por un espejo, y sólo parcialmente por otro espejo. El haz láser que no es reflejado es el que se utiliza para procesar el material. El haz láser esencialmente paralelo es fácil de transportar a largas distancias para llevarlo al sitio donde se necesita. En el área de procesado, el haz láser enfocado en un punto pequeño está provisto de la energía necesaria para calentar, fundir o hasta evaporar metales.
El dispositivo Q-Switch permite aumentar la potencia del haz, siendo la frecuencia de trabajo entre 5 y 50 kHz.
La obtención de los programas de mecanizado es semejante al del mecanizado por arranque de viruta. La aplicación LPSWin permite dibujar el volumen que se va a mecanizar, y crear estrategias de mecanizado con diferentes valores de los parámetros del proceso. La máquina permite mecanizar complejas figuras en 3D, siempre mecanizando capa a capa.
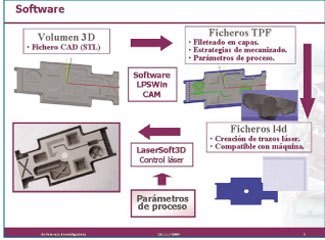
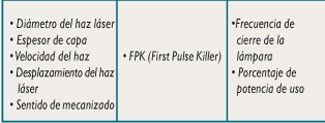
El ajuste de dichos parámetros permite obtener una pieza en menor tiempo pero con peor acabado, o viceversa, obtener un buen acabado a costa del tiempo de mecanizado, tal y como se puede apreciar en la figura 9.
(a) e=1µm, h=5µm: t=33’16’’ (b) e=3µm, h=20µm: t=6’06’’
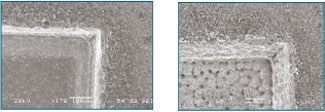
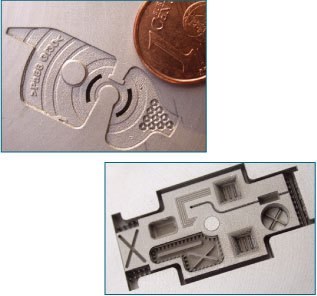