Asfalto nuevo para el aeropuerto de Francfort del Meno: las tecnologías del Wirtgen Group garantizan un saneamiento exitoso
La Fraport AG, la empresa operadora del aeropuerto de Francfort, cambia casi cada siete años la capa superior de las pistas de despegue y aterrizaje, al igual que la de la pista central, el tramo más utilizado. Razón suficiente para otorgarle las posiciones claves a las máquinas del Wirtgen Group en este proyecto.
Los trabajos, en este caso el fresado y el extendido de la capa superior, son, en realidad, tareas estándares, si no se estuviera bajo tanta presión debido al corto plazo de trabajo, además de las altas exigencias de calidad. Al fin y al cabo se trata de la pista central (4 km de longitud, 60 m de anchura) del tercer aeropuerto más grande de Europa. Para restringir el tráfico aéreo lo menos posible, el trabajo tuvo que llevarse a cabo de una manera extremadamente rápida y fiable. El contratista principal de movimientos de tierras y construcción de carreteras ‘Heitkamp Erd- und Straßenbau GmbH’, solo tenía un plazo de 60 horas a su disposición para realizar todos los trabajos de asfaltado. Durante este trabajo, fue necesario mover un total de alrededor de 20 000 t de material.
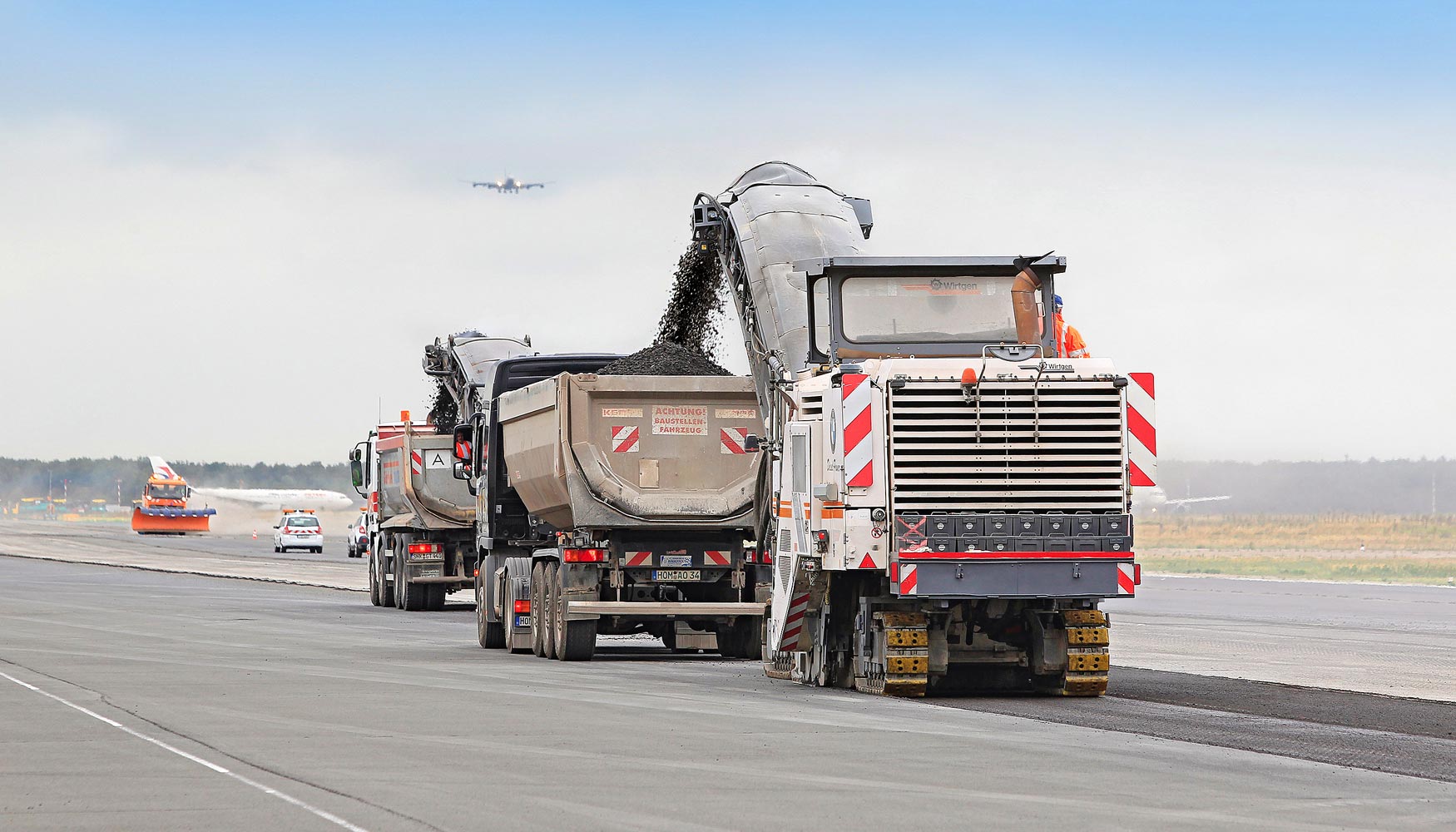
4 fresadoras de alto rendimiento de Wirtgen con 3500 CV de potencia
Con el fin de realizar el fresado en el menor tiempo posible, la empresa de saneamiento de carreteras ‘GMS Fahrbahnsanierungen GmbH’, llevó cuatro fresadoras grandes de Wirtgen de 2 m o 2,20 m de anchura de fresado a la pista de despegue y aterrizaje. Con una potencia de alrededor de 3500 CV (2600 kW), las máquinas de alto rendimiento fresaron 80 000 m² de asfalto sobre la pista de 2,6 km de longitud y 31 m de anchura a una profundidad de 5 cm. Después de 19 horas, el trabajo de fresado e incluso la limpieza de la superficie ya habían concluido.
Widrive se encarga de la productividad
Las fresadoras grandes tipo W 250i, W 210i y W 2200, que se emplearon para este trabajo, están diseñadas para alcanzar siempre el máximo rendimiento. “Los puntos neurálgicos en proyectos de este tamaño son casi siempre el transporte del material fresado y el suministro de agua”, aclara el director de la obra Klaus Kormann de GMS. Con el fin de reducir el tiempo invertido en recorridos de un lado a otro, se había instalado especialmente un depósito provisional en el aeropuerto para el material fresado. En cuanto al suministro de agua, se vieron claramente las ventajas del sistema de control Widrive de Wirtgen. Este control también supervisa y regula la instalación de agua, además del número de revoluciones del tambor de fresado yla velocidad de la cinta, según el avance y la profundidad de fresado. De esta manera, Widrive activa el suministro de agua de forma automática en el momento en que el tambor de fresado inicia su trabajo o lo desactiva al interrumpir los trabajos de fresado. Además, dependiendo de la carga del motor y de la velocidad de fresado, la presión de la bomba de agua aumenta o se reduce de manera automática. Estas funciones hacen que el consumo de agua disminuya notablemente y convierten el proceso de fresado en un proceso muy eficiente.
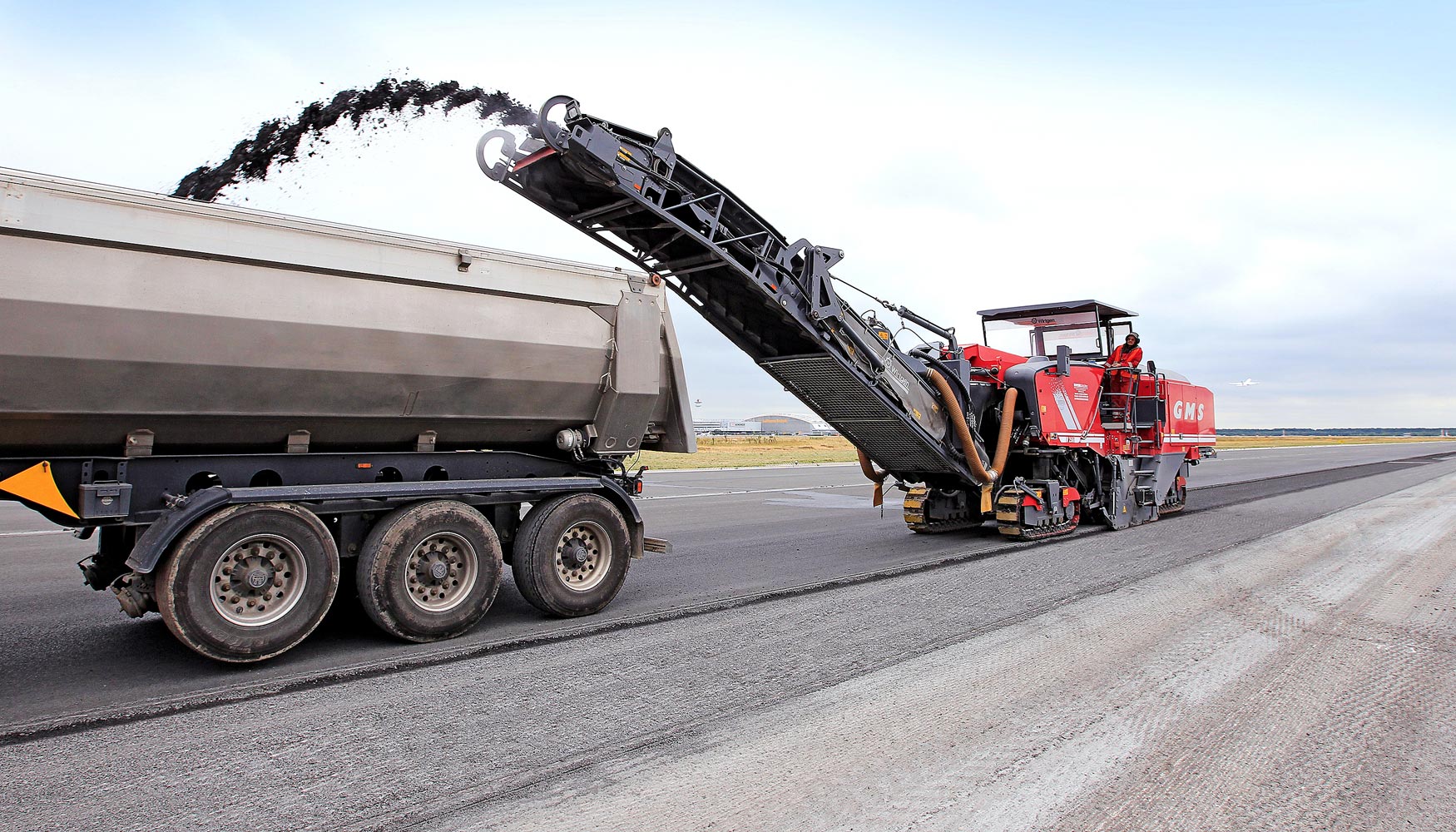
El concepto de motor doble propicia un rendimiento elevado
Especialmente la W 210i y la W 250i, debido a sus dos motores diésel separados, están en condiciones de alcanzar rendimientos de fresado extraordinarios. Asimismo, gracias a Widrive, estas fresadoras grandes hacen uso de la energía de forma muy eficiente y, a su vez, ecológica. Otro punto positivo: los motores están aislados contra vibraciones y ruidos, ya que se encuentran encapsulados en los llamados ‘bloques silenciosos’. De esta manera el operador de la fresadora no siente las vibraciones.
Extendido de asfalto en dos turnos de noche
Allí, donde las fresadoras grandes habían terminado su trabajo y después de que se efectuara la limpieza de la superficie de fresado, se extendió una capa adhesiva como base para la capa nueva de asfalto. A continuación, se realizó el extendido de asfalto en dos turnos de noche, entre las 17 y las 7 horas. En este periodo de tiempo, el suministro del asfalto, para el cual se emplearon 35 semirremolques, se ejecutó independientemente de los embotellamientos típicos alrededor del aeropuerto de Francfort.
En cada una de las dos noches, el equipo de Heitkamp extendió 40 000 m² de hormigón asfáltico rico en gravilla AC 11 D S. El ingeniero diplomado Axel Konrad, director del proyecto por parte de Fraport AG, explica las razones: “El material con gran cantidad de gravilla ofrece una seguridad elevada contra el desprendimiento de agregados. Un aspecto muy importante para los aviones, ya que los áridos sueltos podrían deteriorar las sensibles turbinas. Otra razón es la siguiente: las marcas que los neumáticos de los aviones dejan en el suelo, se pueden eliminar fácilmente de este material”.
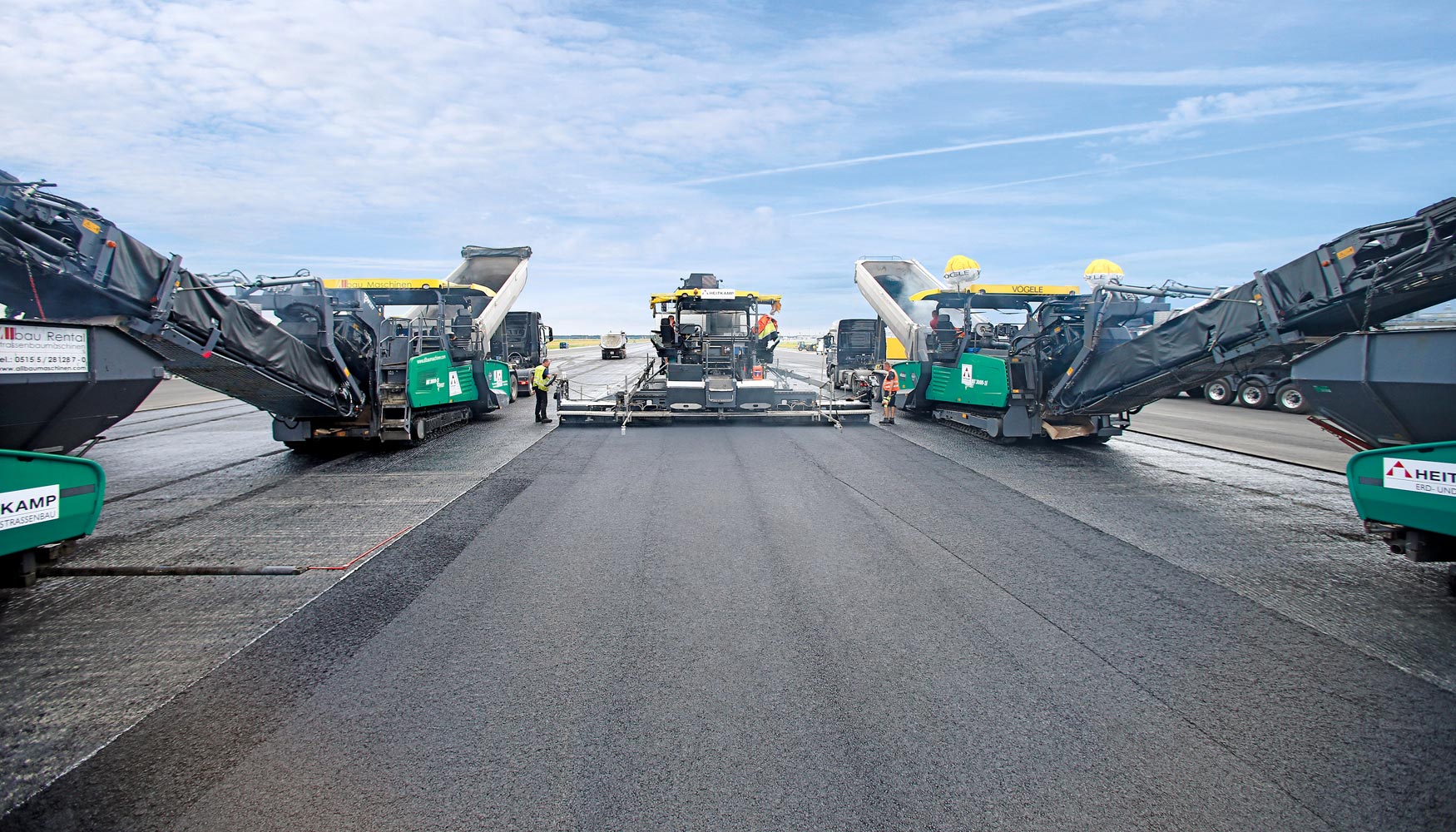
4 alimentadoras de Vögele aprovisionan a 4 extendedoras de Vögele
4 trenes compuestos de extendedoras y alimentadoras de Vögele se encargaron del extendido de la superficie; juntos lograron extender casi 500 t por hora. También aquí, la presión de tiempo era enorme. Fraport había especificado el extendido con alimentadoras, ya que para los operadores del aeropuerto era de gran importancia que la superficie de la pista central fuera absolutamente llana. “En este caso, las alimentadoras son simplemente ideales, puesto que no causan juntas ni salientes en la superficie asfaltada”, esto lo sabe muy bien el señor Konrad, director del proyecto. Por esta razón, el ingeniero diplomado Jörg Pigorsch, jefe de la obra en Heitkamp, llevó cuatro alimentadoras de gran rendimiento de Vögele tipo MT 3000-2i a la obra. Estas máquinas están en capacidad de recibir la carga completa de 25 t de un camión de transporte de aglomerado en solo 60 segundos.
A continuación, el aglomerado se convierte en una mezcla homogénea pasando a través de sinfines cónicos transversales, especiales, situados en la tolva receptora de la alimentadora de Vögele, durante el abastecimiento para el proceso de extendido. El material frío que se encuentra en las paredes de los sinfines cónicos se mezcla con el material más caliente y el material segregado procedente de la descarga del camión, se homogeneiza de forma mecánica. Adicionalmente, un radiador de superficies de rayos infrarrojos mantiene la cinta transportadora a una temperatura elevada, evitando así la adhesión de aglomerado.
Detrás de las alimentadoras se encontraban en acción cuatro extendedoras de Vögele: dos SUPER 1800-3i, una SUPER 1900-3i y una SUPER 2100-2i extendieron la capa superior con la anchura considerable de 31 m ‘caliente sobre caliente’. Durante este proceso, la SUPER 1900-3i hizo las veces de extendedora conductora. Especialmente durante el trabajo nocturno, fue posible ver con gran rapidez y claridad las ventajas de su nuevo concepto de manejo intuitivo ErgoPlus 3. Así, por ejemplo, el tablero de mando del operador dispone de una pantalla en color de gran tamaño, que ofrece una imagen de alta resolución, incluso con una luz deficiente.
Calidad durante el transporte de material
Otro aspecto importante de la SUPER 1900-3i y la SUPER 1800-3i es el transporte del material: en estas extendedoras, gracias al suministro de aglomerado regulado de manera proporcional con control permanente de la cantidad, se obtiene un material a extender a la medida exacta. Además, la altura del sinfín de distribución se puede ajustar de forma hidráulica en hasta 15 cm a lo largo de toda la anchura de trabajo, incluyendo los soportes y las chapas en U. Gracias a ello, se logra una distribución óptima del aglomerado, incluso durante el extendido de capas delgadas, así como en el caso de espesores de extendido variables dentro de un tramo de obra. El gran diámetro de aleta de 400 mm del sinfín de distribución, se encarga de una distribución óptima y libre de segregaciones del aglomerado, también en grandes anchuras de trabajo. Por la anchura de extendido de 7,5 a 8 m esto era de gran relevancia en el aeropuerto de Francfort.
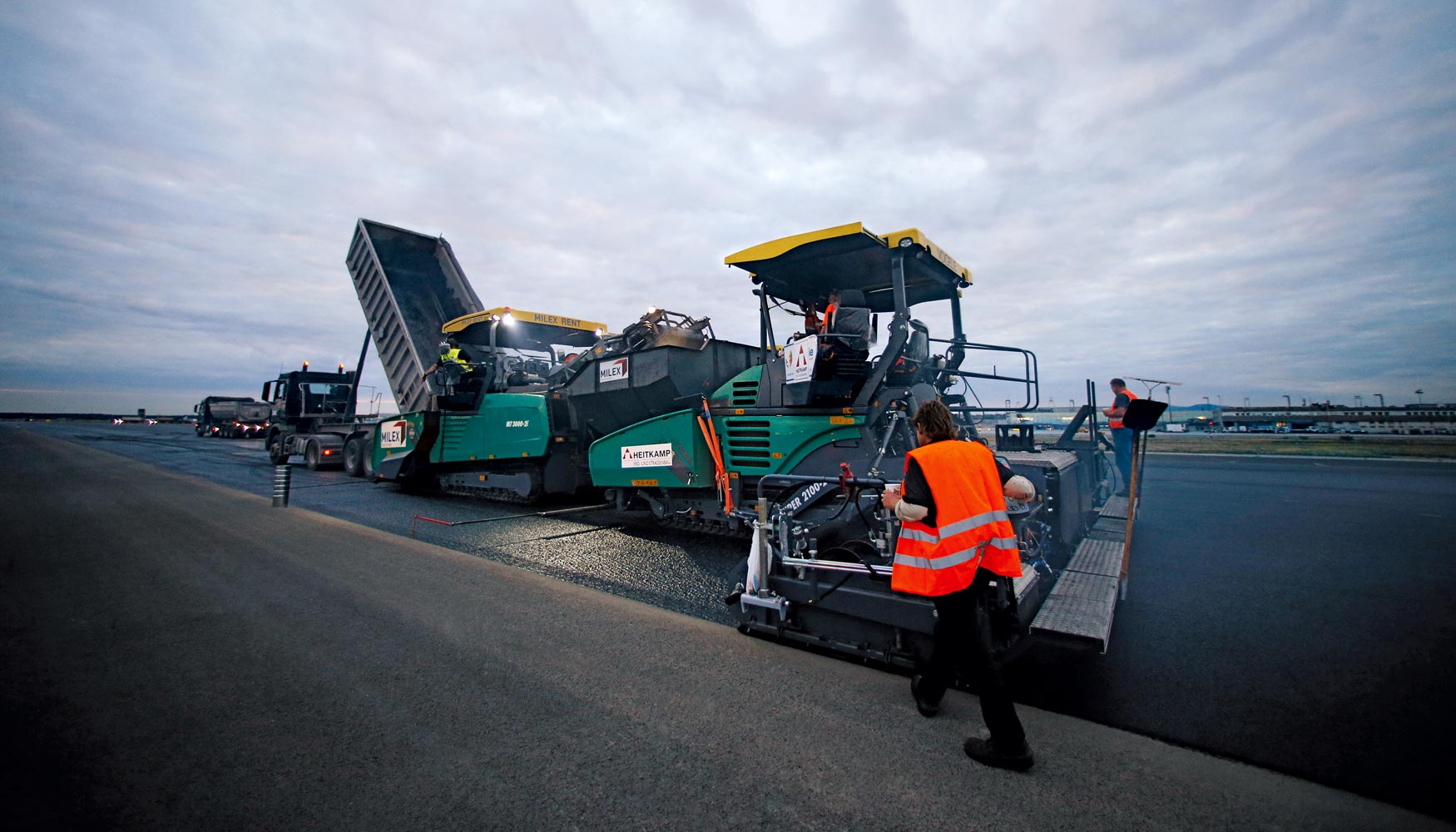
Los compactadores de Hamm son las máquinas ideales para la compactación final
Durante la compactación final e imprescindible, hicieron parte del equipo cuatro compactadores de Hamm tipo DV 85. Los compactadores con dirección por traviesa giratoria con más de 9 t de peso de operación ofrecen una excelente vista libre para que el operador pueda trabajar siempre de una manera muy segura y óptima. Desde la cabina panorámica y a través del vidrio de gran tamaño instalado en el suelo, eloperador ve todo el entorno de trabajo y los tambores. Además, desde el borde de la cabina también tiene una vista libre hacia los cantos de los tambores.
Durante los turnos de la noche en el aeropuerto de Francfort, fue posible constatar lo importante que es la buena iluminación del compactador. Heitkamp ha equipado las máquinas de Hamm con faros de trabajo muy luminosos de LED, así como con una iluminación para los tambores y sus cantos. Toda esa iluminación se encarga, de igual manera, de brindar seguridad y calidad durante los trabajos nocturnos.
Otro factor de calidad es la inversión cuidadosa del sentido de marcha, en donde los compactadores de Hamm asisten al operador, ya que el DV 85 frena y acelera el tambor automáticamente. Con rampas optimizadas, los compactadores evitan de manera eficaz las hendiduras o las distorsiones en el asfalto, logrando así producir una superficie muy plana. En este caso, también la dirección por traviesa giratoria, de mucha precisión, constituye un gran apoyo. A través de ello, la resistencia de la dirección cambia, según la velocidad, evitando así movimientos bruscos de dirección. No hay que olvidar que los compactadores disponen de una gran capacidad de desplazamiento desalineado, ajustable a voluntad. Esta hace posible, con los tambores de 1,68 m de anchura, una considerable anchura máxima de trabajo de 2,99 m.
Productivos y económicos gracias a Hammtronic
Durante la compactación, los compactadores de Hamm demostraron nuevamente que trabajan de una manera muy económica y, por ende, muy productiva. Una razón para ello se encuentra en Hammtronic, el sistema de manejo electrónico de la máquina para supervisar las funciones operativas y del motor. Este sistema adapta de forma automática el accionamiento de traslación, la vibración o la oscilación, así como el número de revoluciones del motor a las condiciones actuales de trabajo. La sincronización perfecta de la máquina garantiza una calidad de compactación óptima. Además, el consumo de combustible se reduce, al igual que las emisiones de gases y de ruidos.
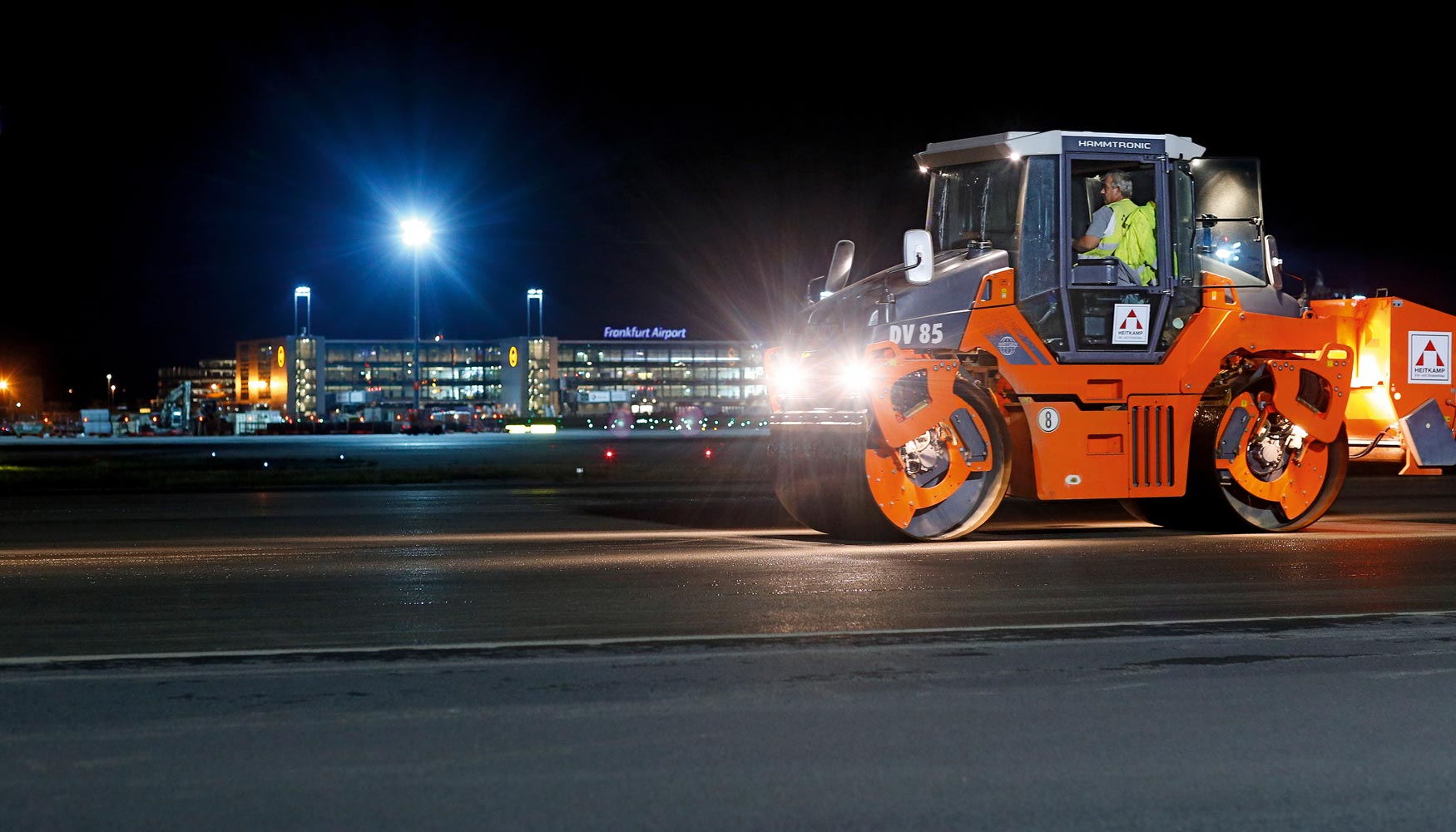
Wirtgen Group: fiable en todos los aspectos
Después de dos días y tres noches, el jefe de la obra Jörg Pigorsch pudo notificarle a su cliente sobre la conclusión de los trabajos de asfaltado, como se había planeado: “Ha quedado demostrado, una vez más, que las máquinas del Wirtgen Group son extremadamente fiables. Por eso, cuando se trata de proyectos a muy corto plazo, siempre utilizamos las máquinas de Wirtgen, Vögele y Hamm. Además, el servicio es excelente. En caso de que alguna vez falle un componente, las sucursales del Wirtgen Group ponen a disposición y al instante, máquinas de sustitución y piezas de repuesto o personal de servicio competente”.
Bajo mucha presión y después de realizar los trabajos de asfaltado, Fraport se encargó 12 horas más de la finalización de la pista central, cuya iluminación conbalizas luminosas se modificó en el curso del saneamiento de la capa superior, instalando un sistema con tecnología de LED, de larga vida y que ahorra mucha energía. Puntualmente, a las cinco de la mañana, la pista ya estaba lista una vez más para el paso de los aviones.