Refuerzo de la viga flotante de la nueva base de contenedores Super Post Panamax en el puerto de Santa Cruz de Tenerife
La Autoridad Portuaria de Santa Cruz de Tenerife ha ejecutado durante los últimos años los trabajos correspondientes a una Nueva Base de Contenedores en la Dársena del Este en el puerto de Santa Cruz de Tenerife. Con esta nueva terminal, se han generado nuevas superficies para contenedores dentro del puerto. Para habilitar dichas zonas, se efectuaron diversas obras, entre ellas la transformación de las vigas carril para grúas Super Post Panamax (Figura 1). Tras unos años de uso, se detectaron ligeros asientos en las cimentaciones recalzadas de las grúas, obligando a su recalce.
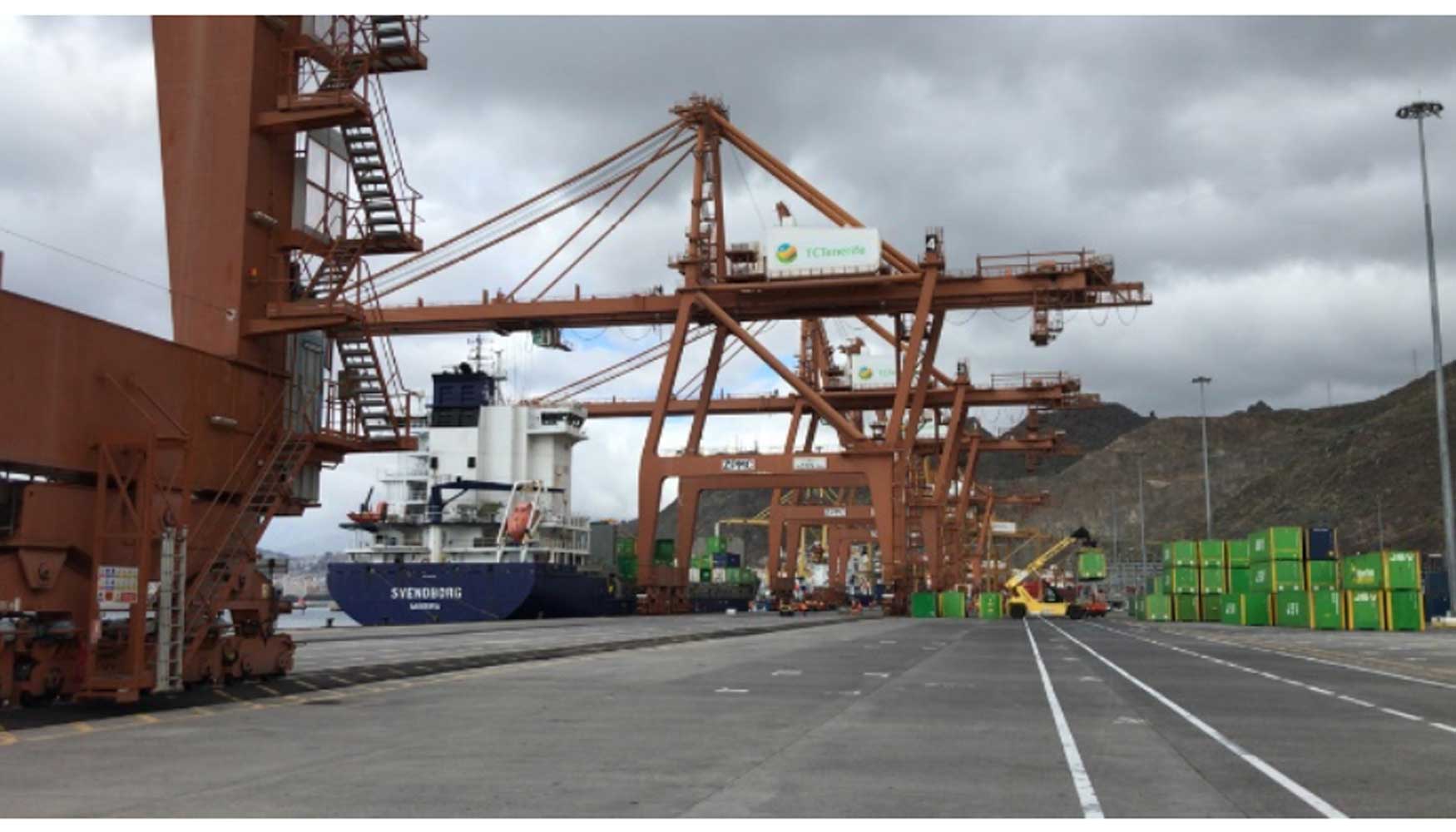
1.- Datos de la obra
La obra de Refuerzo de la viga flotante de la Nueva Base de Contenedores Super Post Panamax en el puerto de Santa Cruz de Tenerife fue adjudicada por la Autoridad Portuaria de Santa Cruz de Tenerife a la UTE SITE-SITESUR, con la finalidad de reparar y complementar el recalce existente.
El proyecto fue elaborado por Acciona Ingenieria, siendo designada directora de Obra Laura Fernández del Castillo Gil y la asistencia técnica de Fernando Alsina Basterrechea. El presupuesto base de licitación fue de 3.040.991,04 €, IGIC incluido.
El plazo de ejecución definido inicial era de seis meses, con fecha de inicio del 11 de marzo de 2021 y finalización el 30 de octubre de 2021 para ejecutar el recalce mediante 310 unidades de micropilotes de longitud unitaria 30,50 m, para un total de 9.455 metros lineales.
2.- Solución adoptada
Para subsanar dicha patología, la solución elegida fue reparar y complementar el recalce existente con nuevos micropilotes, manteniendo el mismo sistema de transferencia de carga. Se buscó con esta solución la máxima sencillez de los procesos constructivos limitando los futuros asientos.
Las características de los micropilotes (fig. 2) eran las siguientes:
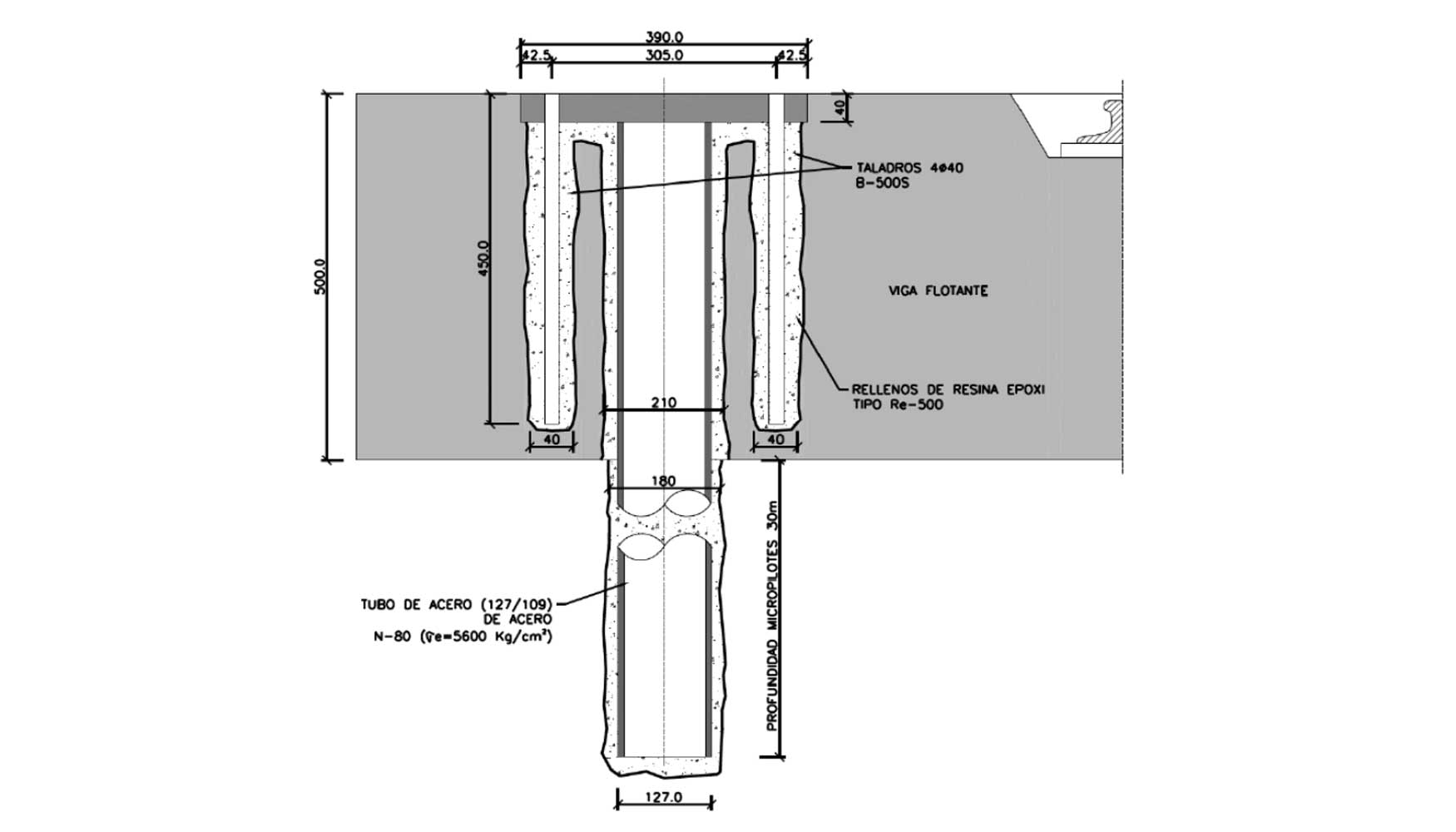
- Diámetro de perforación: 180 mm.
- Armadura tubular: Acero tipo N-80 (límite elástico=560 N/mm2) Φext/e 127/9 mm.
- Resistencia característica de la lechada: 35 N/mm2, sulforresistente e inyectada con el sistema de Inyección Repetitiva (IR) mediante válvulas antirretorno.
- Longitud de los micropilotes desde la base de viga de cimentación: 30,0 m.
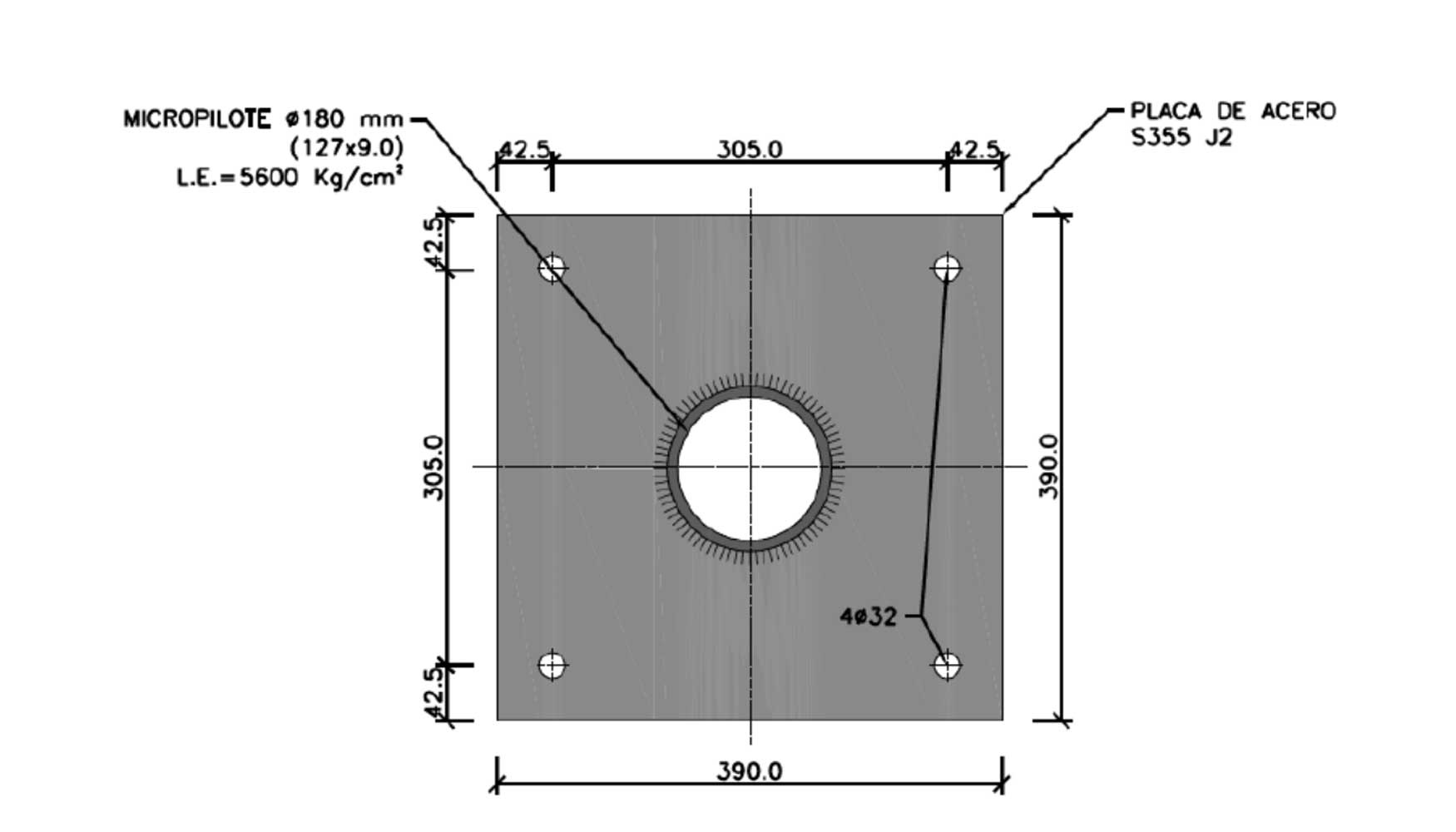
La conexión de los micropilotes (fig. 3) a la viga se consiguió utilizando la misma solución del recalce existente, mediante barras de acero ancladas con resinas especiales y soldadas estas a una placa de acero.
Para el desarrollo de las obras, según proyecto, se definieron tres fases (ver fig. 4) con el fin de no interferir sobre la operación de la terminal, dándole prioridad absoluta.
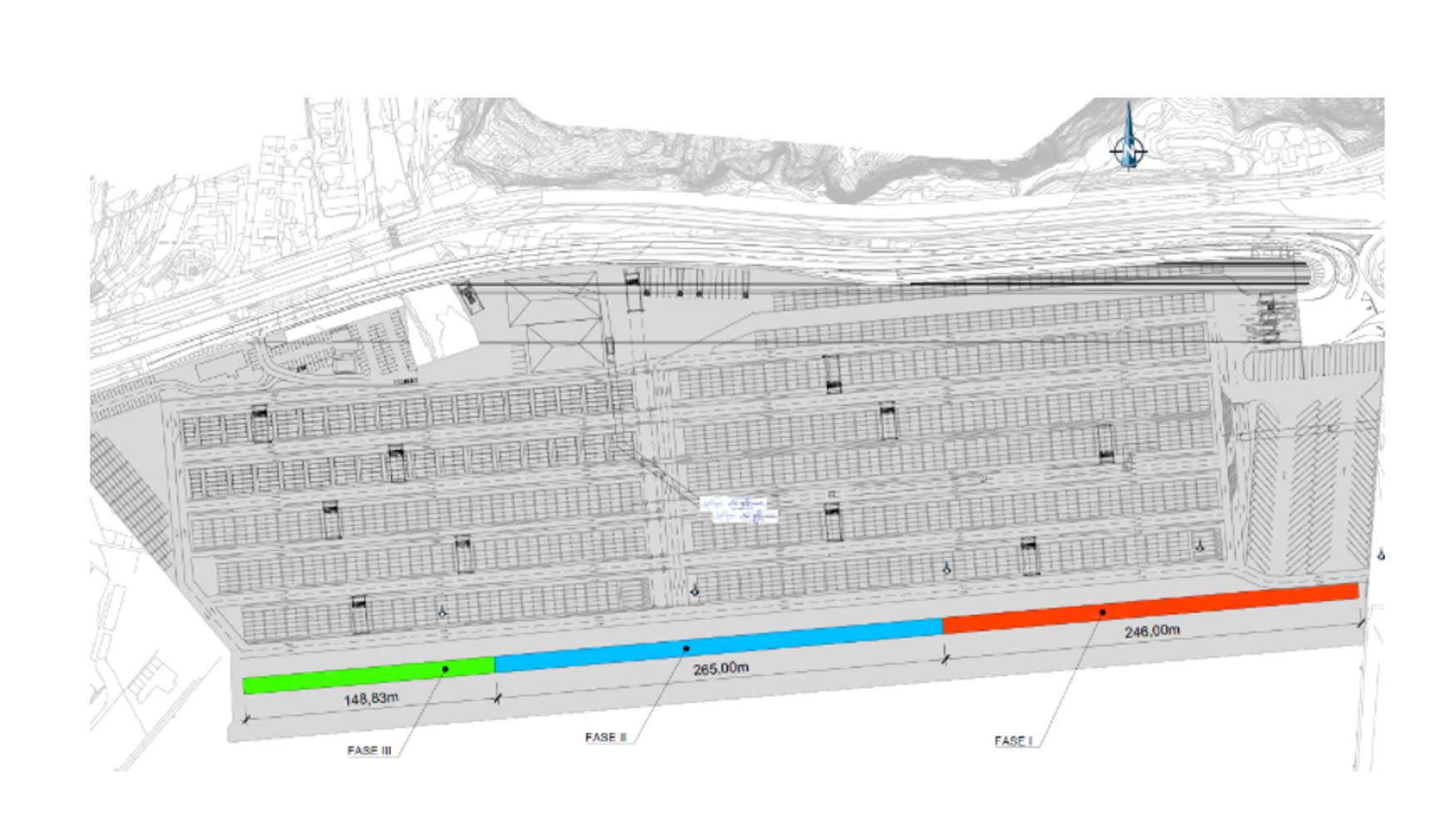
- Fase 1, bolardos 31 a 21 A. Este tramo, de 240 m de largo aproximadamente, es el más crítico para la Terminal, puesto que es el que dispone de atraque en rampa RO-RO.
- Fase 2, bolardos 21A a 10, con una longitud aproximada de 265 m.
- Fase 3, bolardos 8 a 1, con una longitud aproximada de 145 m.
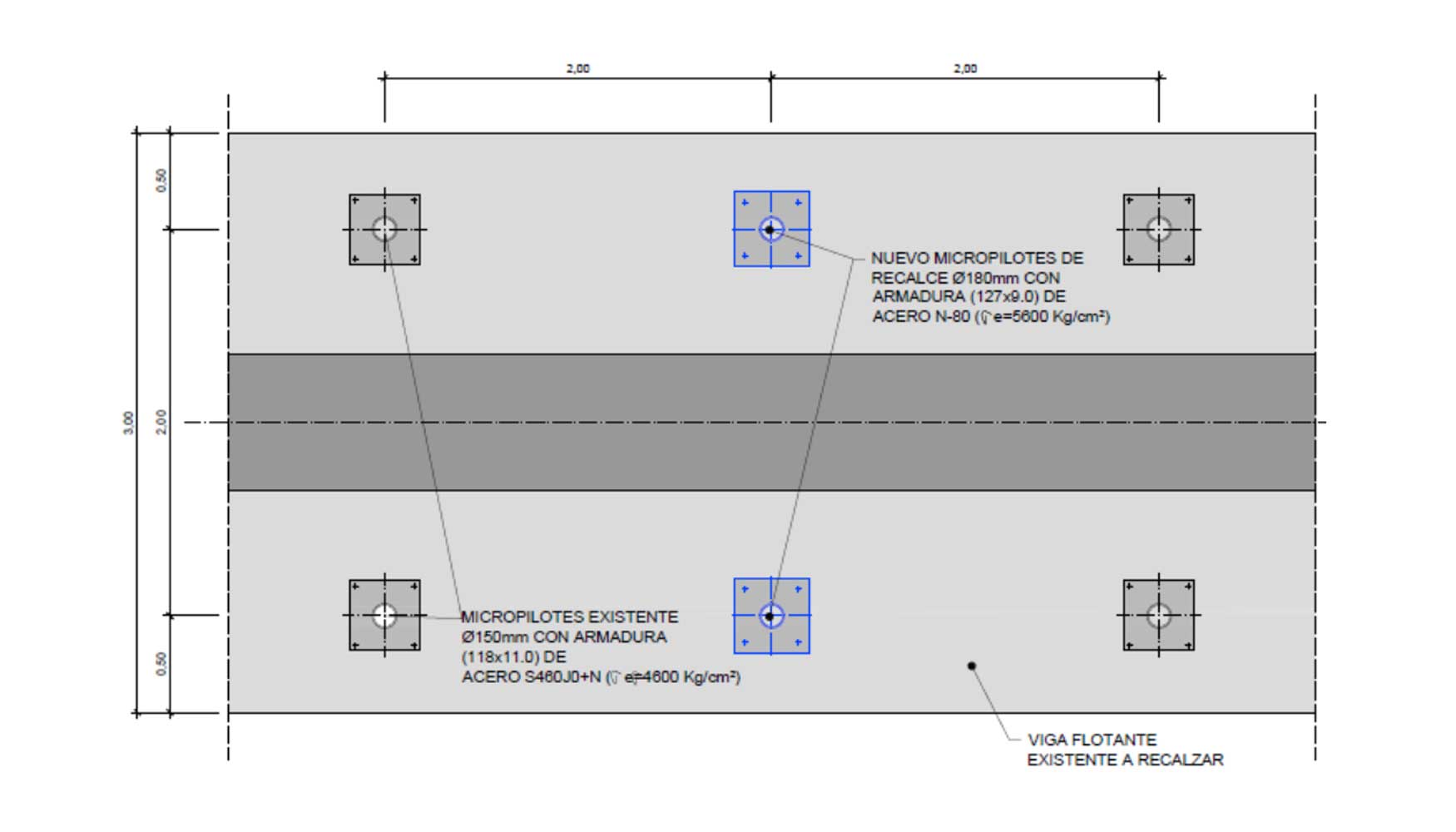
Se dispusieron nuevas parejas de micropilotes, distribuidos entre los 4,0 metros de separación que hay entre las parejas de micropilotes existentes (fig. 5). De esta forma los esfuerzos de cabeza de micropilote se reducirían ostensiblemente y por tanto serían admisibles con un coeficiente de seguridad aceptable, tanto desde el punto de vista estructural como geotécnico, los micropilotes existentes. Con dicha distribución a lo largo de la viga se ejecutaron las 310 unidades de micropilote.
3.- Descripción de las obras
Para la ejecución de los micropilotes, la UTE SITE-SITESUR movilizó tres equipos de perforación para alcanzar los plazos de obra establecidos (Figuras 6 y 7).
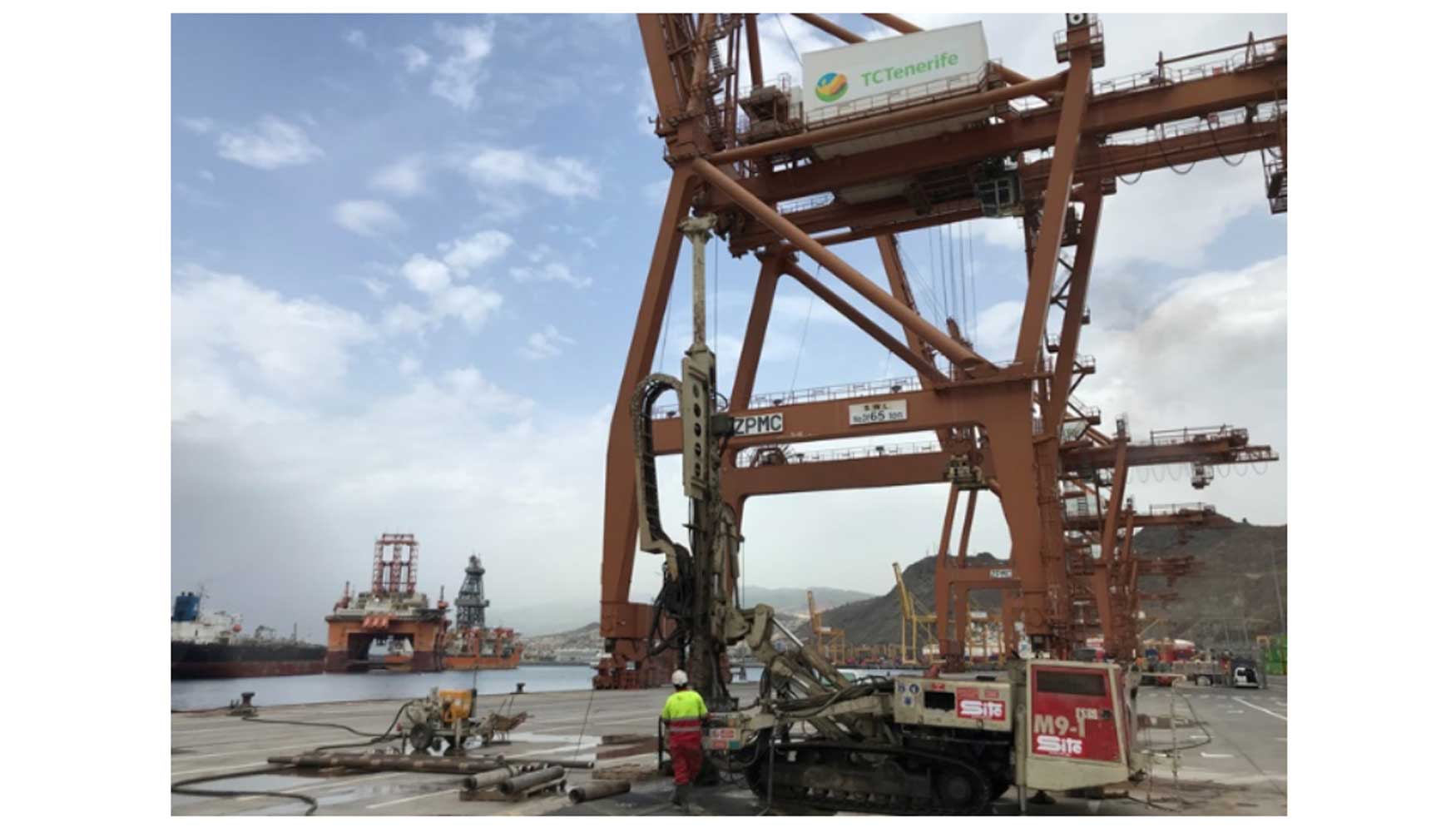
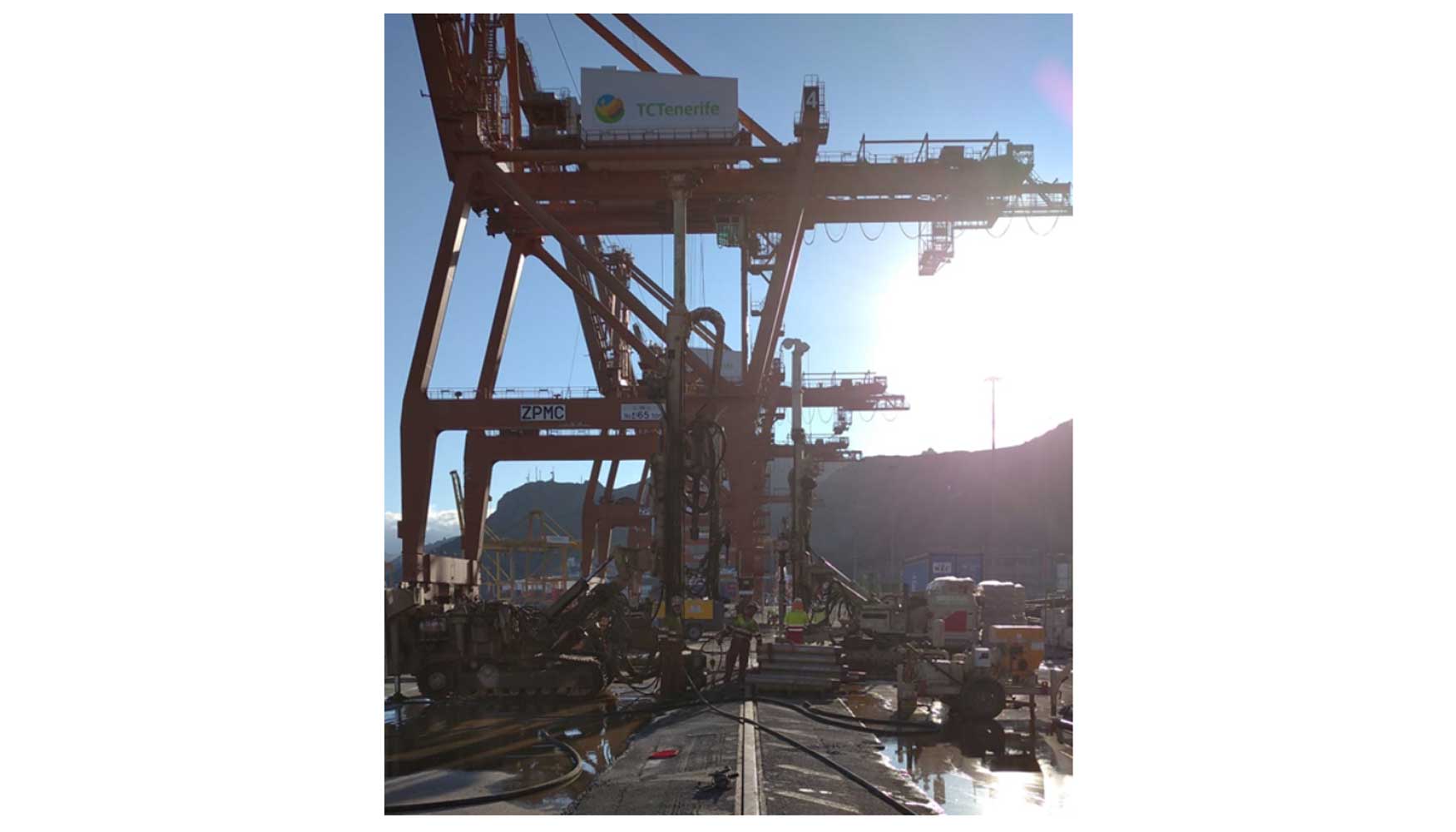
La perforación se realizó con diámetro 210 mm, mediante martillo de fondo de 6 pulgadas y en otros casos con brocas de policristalino, debido a la dureza y abrasividad de los rellenos basálticos, que permitieron perforar hasta dos micropilotes al día con cada equipo.
La UTE apostó por las brocas de diamante sintético policristalino, usualmente conocidas como PCD (Poly-Cristalline Diamond) y empleada en minería, que permiten trabajar en terrenos con una alta heterogeneidad estratigráfica sin necesidad de extracción de maniobra. Ese hecho supuso una reducción considerable en los tiempos de perforación de cada taladro ya que no era necesario cambiar el útil de perforación y por tanto, extraer y reintroducir toda la sarta de perforación para cada una de las perforaciones. Los rendimientos medios de perforación obtenidos fueron de 50 m/día.
El perfil geotécnico del terreno estaba constituido por un primer nivel de suelo seleccionado con SPT 12 de espesor 1,50 m, un segundo nivel de rellenos heterogéneos con SPT 8 y espesor aproximado de 17,50 m y un tercer nivel de arenas de SPT 15 con aproximadamente 10,0 m de potencia. Se utilizó agua para el barrido y fue necesario revestir la perforación debido a la litología presente, ya que prácticamente en su totalidad las perforaciones atravesaban rellenos de bolos y arenas, exceptuando los metros finales donde se encontraba roca basáltica.
Dada la existencia de una capa importante de rellenos, se optó por el sistema de Inyección Repetitiva, de forma que la adherencia terreno-micropilote se mejorase ostensiblemente respecto a las consideradas en proyecto con el sistema de inyección global única (IGU). Para evitar las perdidas de lechada en los primeros metros, donde la carrera de marea se llevaba la lechada inyectada, se opto por colocar una tubería de PVC que permitiera retener la lechada y poder constituir en esos metros el fuste del micropilote.
Las obras se desarrollaron manteniendo la Terminal operativa, con todos los condicionantes referentes a la explotación. Se trabajó en aquellas zonas donde no había barcos atracados; en caso de coincidencia en la escala de varios barcos, se ocupaba toda la línea de atraque y las obras se paralizaban temporalmente. La buena coordinación entre la operativa del puerto y la UTE fue determinante para no retrasar el plazo de ejecución de los trabajos (6 meses + 2 meses de ampliación de plazo). Dicha coordinación obligó a adaptar horarios, barriendo todas las franjas desde las 8:00 hasta las 22:00 de lunes a domingo.
4.- Control de calidad
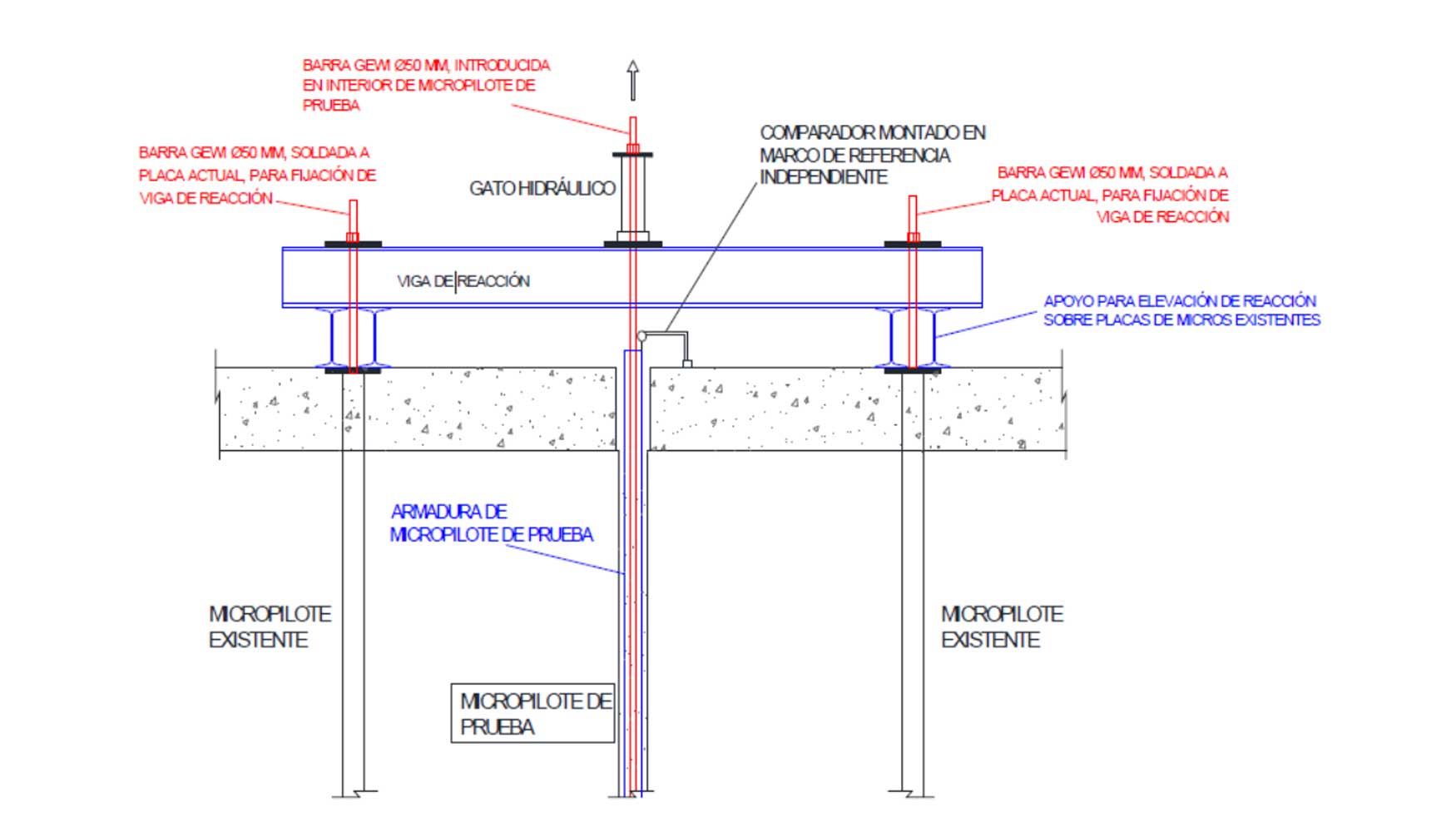
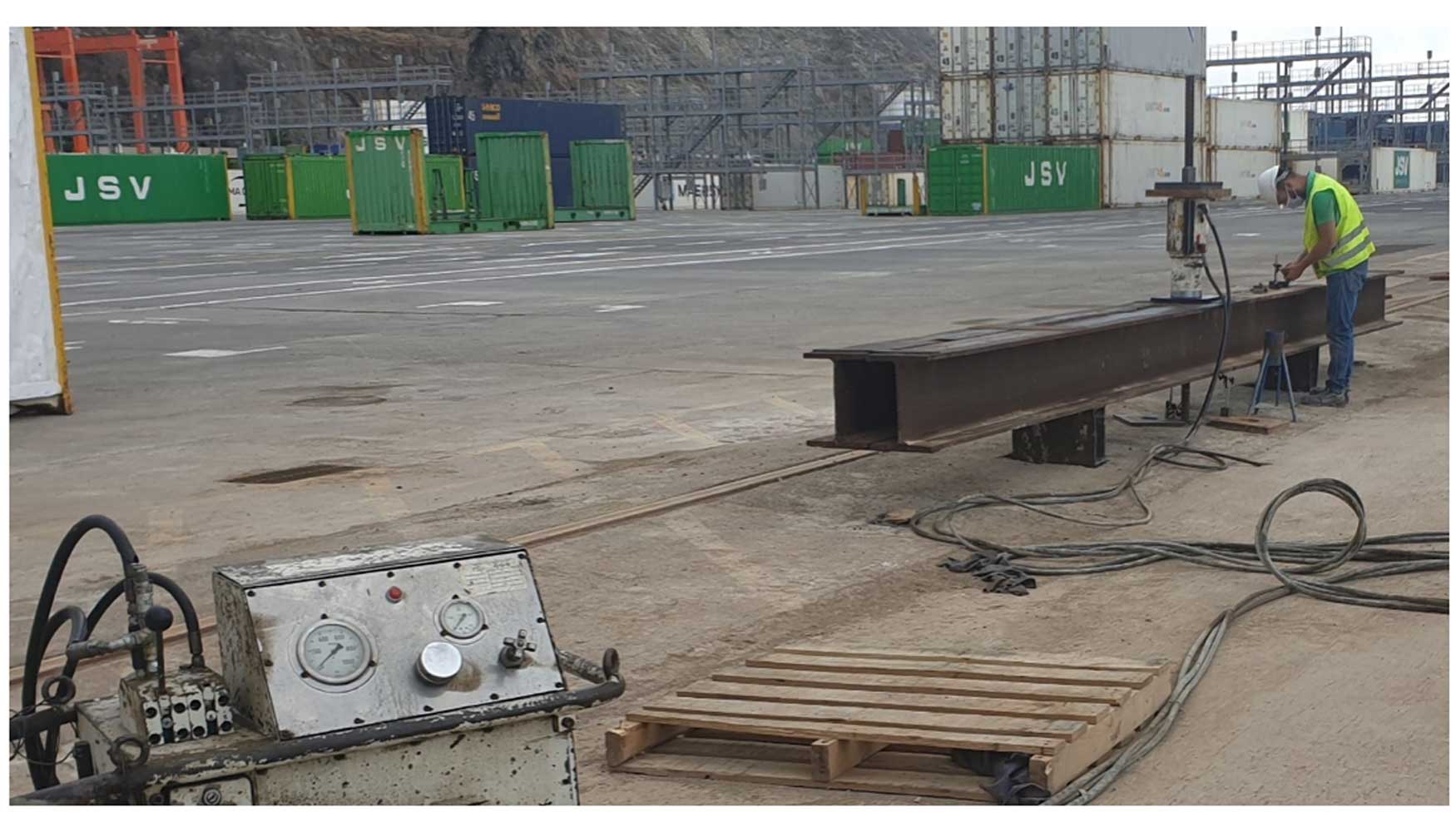
La carga se aplicó en escalones incrementales de un 25% de Pmáx, quedando por tanto los siguientes escalones de carga:
- P1 = 19 Tn
- P2 = 38 Tn
- P3 = 57 Tn
- Pmáx = 76 Tn
Cada escalón de carga se mantuvo hasta que se produzca alguna de estas circunstancias:
1º) En primer lugar se fijó el criterio de comprobación de la resistencia a las diferentes cargas del micropilote.
En cada escalón de carga, se comprobó la tensión aplicada y la resistencia del micropilote a dicha tensión, mediante lectura. Se incluyó un escalón inicial P0 = 10 Tn, con objeto de acoplar el conjunto de vigas, barras, tuercas, etc.
A continuación, se comprobó para cada escalón que el tonelaje se mantenía en un determinado período de tiempo (Fig. 10)
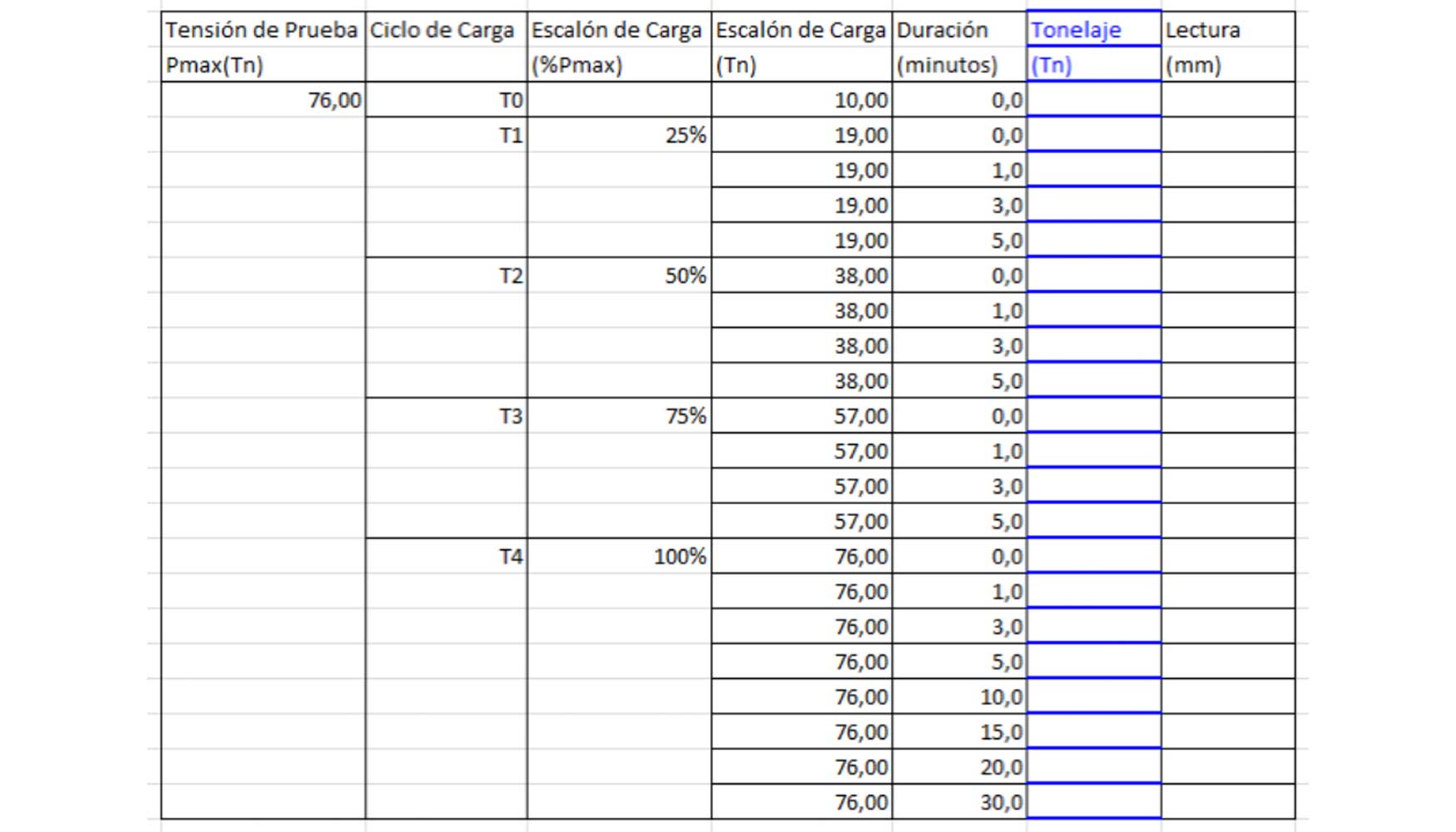
Fig 10.- Tabla tipo empleada en los ensayos de tracción.
2º) En segundo lugar se fijó el criterio relativo a límite de los desplazamientos del micropilote.
Al aplicar la carga en el micropilote de prueba, los alargamientos elásticos del acero se definen por la siguiente expresión:
ΔL= (La* ΔT)/(ATOT*E)
ΔL: Alargamiento
La: Longitud de micropilote que sufre alargamiento elástico
ΔT: Escalón de carga aplicado
ATOT: Área de acero del micropilote = 33,36 + 19,63= 52,99 cm2
E: Módulo de elasticidad del acero: 2.100.000 kg/cm2
De esta forma, la elongación máxima, suponiendo que toda la longitud del micropilote estuviese alargando de forma elástica, es:
La = 30,50 m
ΔLmáx= (3.500 cm* 76.000 kg)/(52,99 cm2*2.100.000 kg/cm2) = 2,39 cm
Como este alargamiento se ha obtenido para la carga máxima, el orden de magnitud para los escalones inferiores en los límites de sus correspondientes alargamientos sería:
ΔT1 = P1 = 19 Tn → ΔL1 = 0,597 cm
ΔT2 = P2 = 38 Tn → ΔL2 = 1,195 cm
ΔT3 = P3 = 57 Tn → ΔL3 = 1,793 cm
ΔTmáx = Pmáx = 76 Tn → ΔLmáx = 2,39 cm
Igualmente, de acuerdo a la Guía para el proyecto y la ejecución de micropilotes en obras de carretera, el desplazamiento máximo admisible en un micropilote viene definido por:
SMAX = 0,15D = 0,15*20,8 = 3,12 cm
5.- Conclusión
Este proyecto confirma la idoneidad de la ejecución de recalces mediante micropilotes en puertos, siendo posible atravesar terrenos de gran complejidad geotécnica (escollera y basaltos) mediante el empleo de nuevas técnicas de perforación que han mostrado su efectividad.
También ha quedado ratificada la posibilidad de eliminar las pérdidas de lechada en las zonas de carrera de marea mediante el empleo de camisas perdidas plásticas, que además contribuyen a mejorar la protección anticorrosión de los elementos enterrados.