El reto del mecanizado de nuevos materiales
Con mucha seguridad dentro de la industria metalmecánica las familias de materiales más exigentes para el mecanizado lo constituyen las superaleaciones y los aceros endurecidos, estos últimos muchas veces hasta valores de dureza de 65 HRC, materiales enmarcados dentro de los grupos ISO de materiales S y H respectivamente. No conviene sin embargo olvidar otros materiales que aunque no presenten valores de dureza tan elevados, sí que poseen otras características que los hacen especialmente exigentes en su mecanizado. Estas características pueden estar relacionadas con su mala conductividad térmica, afinidad química con la herramienta, ductilidad, o presencia de partículas abrasivas por ejemplo, lo cual constituyen importantes amenazas para realizar un mecanizado de calidad. Materiales que presentan características de este tipo son la familia de los titanios, sus aleaciones y aluminatos de titanio, aleaciones de aluminio, aluminio-litio, o incluso bloques de arena utilizada en moldes para fundición.
El grupo S, siempre avanzando
La familia de las superaleaciones constituye una de las más exigentes en términos de su metalurgia. Estos materiales son generalmente aleaciones base Níquel, y tienen un uso generalizado en el sector aeronáutico por sus excepcionales características mecánicas de resistencia y tenacidad además de gran resistencia a la corrosión, todo a alta temperatura. Dentro de la clasificación ISO de materiales, se encuentran enmarcadas en el grupo S. Esta clasificación agrupa a los materiales en función de su naturaleza y sus características de mecanizado, siendo el grupo S uno de los que presentan un mecanizado más difícil.
El grupo S no solo se compone de materiales base Níquel, sino que también consta de aleaciones base Cobalto e incluso base Hierro, con altos contenidos de otros elementos de aleación que las dotan de características mejoradas para su uso en ambientes hostiles como el interior de una turbina de gas aeronáutica, marina o de generación de energía. Otras familias de materiales como los Titanios y sus aleaciones también pertenecen a este grupo de materiales, siendo el conocido Ti6Al4V el más ampliamente utilizado en componentes de turbina, sobre todo en las partes menos calientes del compresor, además de en componentes de estructura y tren de aterrizaje.
En los últimos años se han dado numerosos avances en el campo de las superaleaciones, tanto en lo relativo a su metalurgia como a métodos de procesado, sobre todo en lo relativo a su mecanizado, tanto en técnicas como en herramientas. Estos avances son la consecuencia lógica de la inversión e investigación continua en este tipo de materiales por parte de los motorizadores de aeronaves y fundidores, ya que las normas anticontaminación también están presentes en la industria aeronáutica, en la que se busca motores con un menor impacto ambiental, cada vez menos contaminantes y menos ruidosos, con restricciones importantes en la cantidad de gases CO2 y NOx, que pueden expulsar al ambiente, motores más verdes en definitiva.
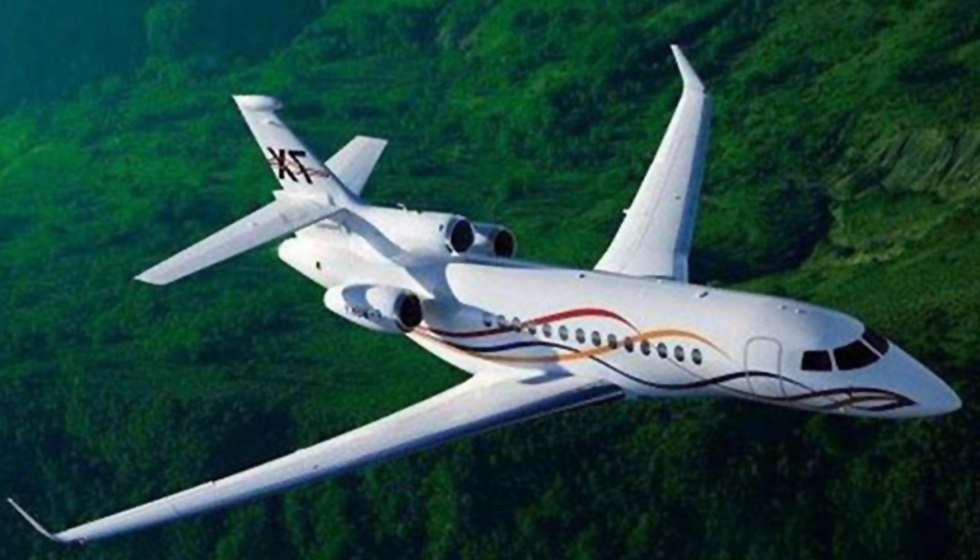
Respecto a los materiales, han sido varios los avances, surgiendo nuevas aleaciones con propiedades superiores respecto a sus hermanas pequeñas, ya sea bien por variaciones en su composición química que permiten diferencias en el tratamiento térmico lo cual hace posible su funcionamiento en servicio a temperaturas superiores a sus predecesoras, o por desarrollos nuevos. En este sentido cabe destacar la relativa nueva aleación Inconel 718 Plus, versión mejorada de la archiconocida Inconel 718, tan utilizada históricamente en la fabricación de componentes de turbina. Este nuevo material permite unas temperaturas de funcionamiento unos 50 °C superiores a las de su predecesor lo que redunda en unos rendimientos de la turbina mayores, pero también plantea dificultades añadidas en la fabricación de componentes, sobre todo en lo que atañe a su mecanizado, ya que materiales más resistentes a mayores temperaturas implica mayores dificultades en su mecanizado. Aun así resulta ventajoso su empleo en la turbina, ya que la reducción de costes que plantea el uso de la nueva aleación 718 Plus por su mayor rendimiento es mayor que el incremento de dificultades durante su mecanizado.
Otros materiales relativamente nuevos, en este caso desarrollados por el fabricante Haynes, son las aleaciones Haynes 282, Haynes 188, y Haynes 230. Las dos últimas han venido a sustituir a la aleación Haynes 25 ampliamente utilizada en componentes aeronáuticos, y en menor medida en otros componentes de la industria general como rodamientos. El material Haynes 282 es también una aleación de endurecimiento por precipitados del tipo gamma prima, la cual destaca por sus propiedades combinadas únicas de resistencia al creep, estabilidad térmica, soldabilidad y maquinabilidad, no presentes en aleaciones disponibles comercialmente como el Inconel 718 y Waspaloy, pero que según se ha demostrado en ensayos de torneado llevados a cabo por el Grupo de Fabricación de Alto Rendimiento de la Universidad del País Vasco presenta grandes problemas durante el mecanizado, resultando crítica la duración de las herramientas.
El caso del reciente material Haynes 230 constituye una novedad importante, que como ya se ha dicho ha venido han sustituir a las aleaciones 25 y a la posterior aleación 188, y tiene unas excelentes propiedades de resistencia a altas temperaturas, superiores a las de sus predecesores, así como a ambientes oxidantes. Tiene la ventaja de que es colable para realizar componentes por fundición además de tener una fácil fabricabilidad según el fabricante, aunque todavía hay muy poca bibliografía con ensayos de mecanizado que lo certifiquen, se centran más en aspectos de fatiga y creep combinados con oxidación y corrosión.
El caso del Inconel 706 es especial. No se trata de un desarrollo nuevo, en cambio sí que ha despertado de un largo sueño desde que fue desarrollada hace ya más de 30 años partiendo como base del Inconel 718, aunque con un contenido de hierro sustancialmente más elevado. Ha sido como consecuencia de avances en sus técnicas de producción y mejora de sus propiedades que se ha relanzado su uso en componentes aeronáuticos, sobre todo en discos de turbina, ejes, carcasas o soportes de motor. Las características de este material son muy similares a las del Inconel 718 con la ventaja de que tiene una maquinabilidad más elevada y su precio considerablemente inferior, lo cual la hacen apta para motores sujetos a regulaciones más laxas con una notable reducción de costes.
Un último caso del grupo S de materiales de relativa novedad lo constituye una variación de la aleación 718, denominada Inconel 718SPF, el cual es una versión hecha a medida especialmente para procesos de conformado superplástico, donde se requiere un material con altas capacidades mecánicas a alta temperatura, y a la vez que permita generar componentes de geometría compleja, aunque en este caso las tareas de mecanizado juegan un papel de menor importancia.
Son numerosos también los avances que continuamente se están dando en la generación de nuevas superaleaciones, en especial en las superaleaciones monograno o de cristal único, y de solidificación direccional, muy utilizadas sobre todo en la fabricación de alabes por sus excepcionales características anticreep, muy necesarias en estos elementos sometidos simultáneamente a una gran fuerza centrífuga y altas temperaturas. En este sentido se han desarrollado superaleaciones base Níquel y Cobalto como las M4706, DD9, PWA1484 y otras.
Las herramientas también tienen mucho que decir en lo que respecta al mecanizado de estos materiales. Se podría decir que es el metal duro el que casi exclusivamente ha permanecido como material utilizado en plaquita de torno, no tanto en herramienta de fresado donde también encuentra todavía alguna aplicación el acero rápido, aunque es residual en la industria aeronáutica que más uso hace de estos materiales. Tanto el metal duro como el acero rápido no han dejado de evolucionar surgiendo continuamente novedades en su estructura de grano, métodos de compactación y sinterización, así como en los recubrimientos aplicados a las herramientas para prolongar su vida en el mecanizado de materiales. En el caso de los recubrimientos, nuevos conceptos con disposiciones multicapa, con espesores incluso por debajo de la micra han hecho que las tareas de mecanizado se hagan más fáciles, logrando mejorar la integridad superficial del material mecanizado sobre todo en las aleaciones base níquel. Incluso las capas deformadas que surgen después del mecanizado ven reducido su espesor por esta mejora de las herramientas y recubrimientos.

Para superar el gran reto que supone el mecanizado de estos materiales tan avanzados, la parte del proceso también es objeto de investigación continua. De esta forma la aplicación de técnicas como el mecanizado con refrigeración a alta presión (High Pressure Cooling) es una alternativa muy adecuada con amplio uso en estos materiales, en los que además de suplir la demanda de refrigeración de la herramienta por la gran exigencia del mecanizado, favorece la fragmentación de la viruta. Otra técnica ya estudiada pero que está sufriendo una vuelta de tuerca es el mecanizado asistido por ultrasonidos, la cual por medio de movimientos de la herramienta generalmente de poca amplitud pero muy alta frecuencia, favorece el mecanizado, prolongando la vida de las herramientas e incluso preparando la superficie del componente con unas condiciones que la hacen adecuada para su posterior trabajo en servicio a fatiga.
Estas y otras técnicas que permitan mejorar el proceso deben ser aseguradas en términos de integridad superficial, realizando análisis exhaustivos del estado subsuperficial del material, analizando variaciones de su dureza interna, estado de tensiones residuales etc.
Todas estas técnicas, procesos y nuevos materiales serán objeto de estudio en el nuevo Centro de Fabricación Avanzada Aeronáutica (CFAA) recientemente constituido en el Parque Científico y Tecnológico de Bizkaia como modelo de relación entre Universidad y Empresa. Este centro se constituye como un centro mixto de la Universidad del País Vasco con un enfoque enfocado a la generación de nuevo conocimiento en tecnologías avanzadas de fabricación.
Aleaciones Aluminio-Litio
Como otro ejemplo de material con aplicaciones aeroespaciales que constituyen un gran reto se encuentran las aleaciones aluminio-litio (Al-Li), las cuales son aleaciones de aluminio a las que se ha añadido un porcentaje de litio entre 0,5 y 3,5% para reducir su densidad y aumentar sus propiedades mecánicas. Las aleaciones de aluminio-litio tienen como principales características, primero, que el litio es un metal más ligero que el aluminio (densidad de 0,54 g/cm3), por tanto al alearlo con el aluminio (densidad de 2,70 g/cm3) se obtiene una aleación con menor peso específico. La segunda razón es que, con excepción del berilio, cuyo uso está asociado a problemas de salud y fabricación, el litio es el único metal que mejora el módulo de elasticidad y rebaja la densidad cuando se alea con el aluminio.
Al añadir litio, cada 1% de litio añadido al aluminio, aumenta el módulo elástico en aproximadamente 3 GPa y disminuye la densidad en unos 0,08 g/cm3. Es por ello que las aleaciones Al–Li logran un elevado módulo de elasticidad y alta resistencia, lo que permite el diseño de estructuras más ligeras.
Otra ventaja de estas aleaciones respecto a materiales como los composites, y las aleaciones tradicionales de titanio, es que se pueden trabajar con equipamiento convencional. Su comportamiento es muy similar al de las aleaciones de aluminio tradicionales cuando se someten a operaciones como extrusión, forja, mecanizado, conformado y soldadura. Las superficies se pueden pintar y anodizar, y se pueden deformar plásticamente en ciertas condiciones, soportando temperaturas moderadas.
Aunque el litio es muy reactivo y tiende a quemarse, es relativamente fácil alearlo con el aluminio, por ejemplo en un horno de inducción en crisol de grafito y vaciándolo en un molde de hierro, ambas operaciones bajo atmósfera de argón. El intervalo de fusión está entre 500 °C y 600 °C.
El método más común para obtener estas aleaciones, es con el vaciado por enfriamiento directo (Direct Chill Casting), que es un proceso semicontinuo en el cual la aleación fundida se vierte en un molde refrigerado con agua que tiene una base retráctil. La base se va retirando a medida que el metal se solidifica en la periferia y se acaba de enfriar con agua pulverizada. Esta operación se puede realizar tanto de forma vertical como horizontal. Tecnologías como el ‘DC casting’ producen aleaciones hasta con un 3% de Li como máximo, pues las adiciones mayores de Li causan la formación de fases intermetálicas frágiles como resultado de la segregación, obteniéndose materiales no aptos para su utilización en aplicaciones industriales.
Se ha señalado que la principal ventaja de las aleaciones Al-Li es su baja densidad y por tanto la resistencia específica. Pero se ha visto que esto no es suficiente inicialmente para comercializar estos materiales para su utilización industrial, razón por la cual es fundamental enumerar las principales propiedades como son, las mecánicas (resistencia, fatiga y tenacidad), las térmicas (estabilidad), las químicas (respuesta a la corrosión) y la maquinabilidad, sobre todo la soldabilidad.
Al estudiar las aplicaciones actuales de las aleaciones Al-Li, podemos decir que todo comenzó en la década de 1980, cuando los fabricantes de aluminio, trabajaron en aluminio-litio como sustituto de los tradicionales aluminios; dando lugar a la aparición de las aleaciones comerciales 8090, 2090 y 2091 y la introducción posterior de Weldalite 049 y CP276.
Dentro de las aplicaciones comerciales, en primer lugar destaca la aeronáutica, donde se utiliza este material en grandes componentes como las alas (bordes, estructura y recubrimiento); fuselaje (armazón y cubiertas); pistas de asiento así como gran número de componentes de diversos tamaños que forman parte del avión. Además de los usos comerciales conocidos, no hay que olvidar que existen otras muchas para helicópteros, transporte, etc. que están en producción y estudio. Existe un importante capítulo de elementos que se encuentran bajo régimen de confidencialidad, lo cual limita su conocimiento y volumen real de utilización.
En estos ejemplos de aplicación juegan un importante papel requisitos tales como resistencia, rigidez, peso mínimo y comportamiento ante la corrosión. De todos los beneficios, el ahorro de peso es la más destacada en las aplicaciones aeronáuticas y espaciales. También se integran en estructuras rígidas básicas, depósitos y, como forma metalúrgica, construidas a partir de planchas, entre otras aplicaciones en la construcción de pantallas o barreras térmicas por su comportamiento criogénico.
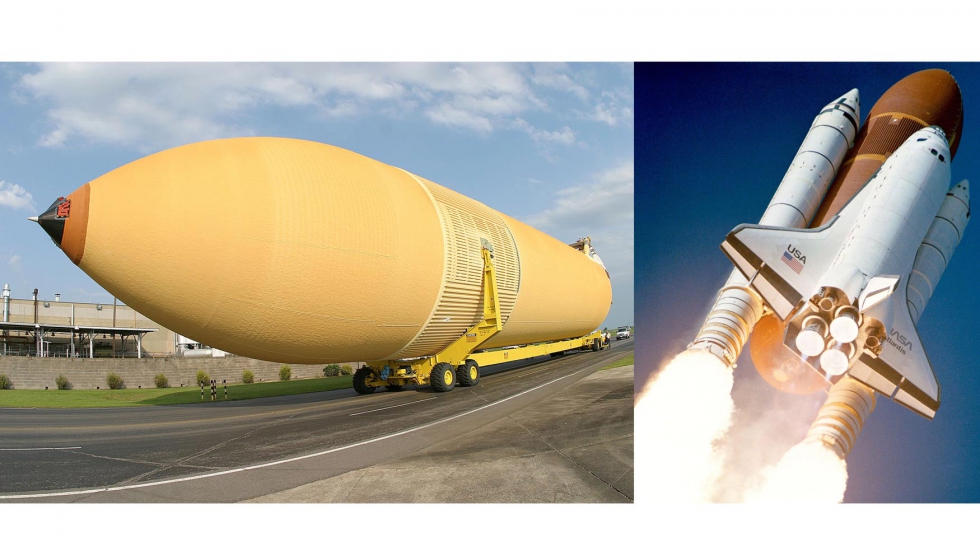
El reto de otros materiales
Pero no solo implican un gran reto materiales que involucran al mecanizado convencional. Existen otras formas de mecanizar no convencional como por ejemplo el biomecanizado con bacterias que son objeto actual de investigación. Se trata de mecanizar componentes de cobre utilizando microorganismos como herramienta para eliminar el material, las cuales van atacando el material. Esta idea surge como consecuencia de la búsqueda de la eliminación de los fluidos de corte para el mecanizado de cobre, y se plantea como una opción de futuro para ciertas aplicaciones.
Otro material poco común para ser mecanizado es la arena de moldes de fundición. El mecanizar un bloque de arena, que puede sonar raro en un principio, no lo es tanto cuando se piensa en series muy cortas, componentes únicos o prototipos, de forma que se reduce enormemente el lead-time de la fabricación de dicho componente. Mecanizar un material tan abrasivo como una mezcla compacta de arena pura y aglutinante, constituye un auténtico reto para las herramientas, que solo puede ser llevado a cabo por ciertos metales duros y herramientas de diamante sintético, ya que la duración de estas es un factor decisivo. Este proceso plantea retos añadidos, puesto que es necesaria una máquina preparada para soportar el ambiente generado durante el mecanizado. Partículas de menos de 100 micras de calibre son volátiles y viajan en suspensión por la máquina, pudiéndose introducir en los lugares más insospechados de la electrónica, o en los sistemas de accionamiento y guiado de la máquina.
Pero quizá el que mayor difusión y aplicación pueda tener en la industria, es el mecanizado de material aportado y fundido con láser (laser cladding), muy en boga recientemente por su gran expectativa de uso futuro para reparación de componentes aeronáuticos de alto valor añadido, aunque también se puede utilizar en otros ámbitos de la industria para fabricar piezas cercanas a su forma final, con poca carga de mecanizado posterior. La razón de su problemática radica en la falta de homogeneidad en su superficie después de haber realizado el aporte, lo cual se une al hecho de que generalmente los materiales utilizados en el aporte selectivo mediante laser son de difícil maquinabilidad (Inconel 718, Titanio, …) enfocados a la industria aeronáutica. Esta falta de homogeneidad puede desembocar en problemas de rotura de herramienta o similar a la hora de mecanizar el material para llegar a la forma final del componente, ya que la herramienta en sus trayectorias durante el mecanizado puede toparse con zonas de diferente espesor de material a mecanizar, lo cual no es solucionable a día de hoy en los modelos virtuales de aporte de material para la posterior generación de trayectorias de mecanizado, pero no es difícil aventurar que en unos años esto dejará de ser un problema.
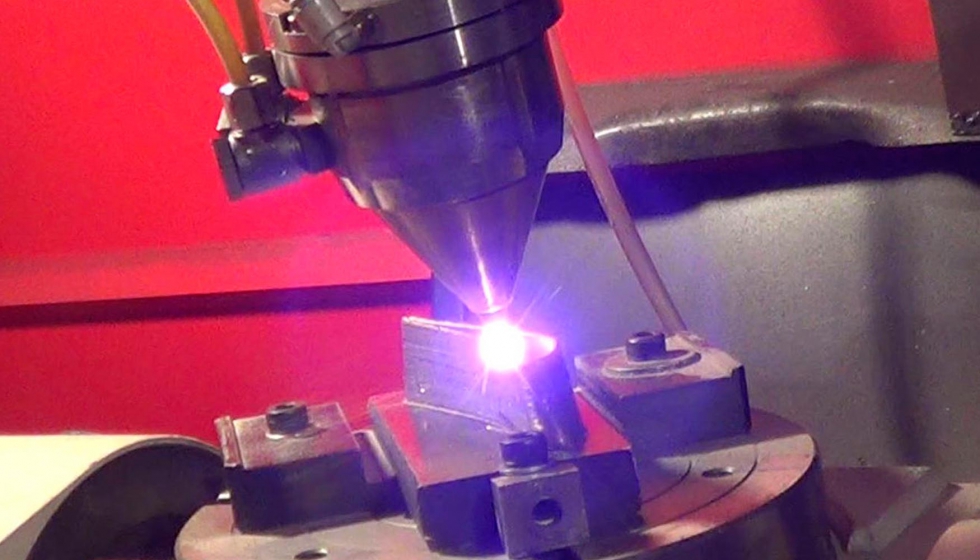
Superacabado de materiales de alto valor añadido
Las operaciones de superacabado son cada vez más empleadas en los procesos de fabricación de componentes de alto valor añadido. Se trata de operaciones de máxima precisión que se realizan al final del proceso de fabricación para la mejora de la calidad superficial del componente y dotarlo de unas propiedades mecánicas superiores.
Las operaciones de superacabado consisten en la eliminación de cantidades extremadamente pequeñas de material de la superficie, en algunos casos ni siquiera existe tal arranque de material sino una deformación de la superficie, en la que se aplastan los picos de rugosidad propia de procesos de mecanizado.
Existen varios procesos diferentes dentro de los denominados “procesos de superacabado” tales como el lapeado, superpulido, bruñido hidrostático, granallado… A continuación se expone una breve descripción de alguno de los utilizados en los principales sectores industriales.
Uno de los más empleados es el lapeado, un proceso de mecanizado abrasivo donde se consigue una precisión dimensional extrema de las superficies. Consiste en frotar la superficie a tratar con un plato giratorio o ‘Lap’ y una fina capa de partículas abrasivas suspendidas en un líquido viscoso (comúnmente aceite soluble, aceite mineral o grasa). Aunque es un proceso abrasivo, difiere del rectificado porque emplea abrasivo ‘suelto’ (en suspensión en un aceite) en lugar de abrasivo aglomerado como en las muelas. Con este proceso se alcanzan rugosidades superficiales de Ra=0,04 µm.
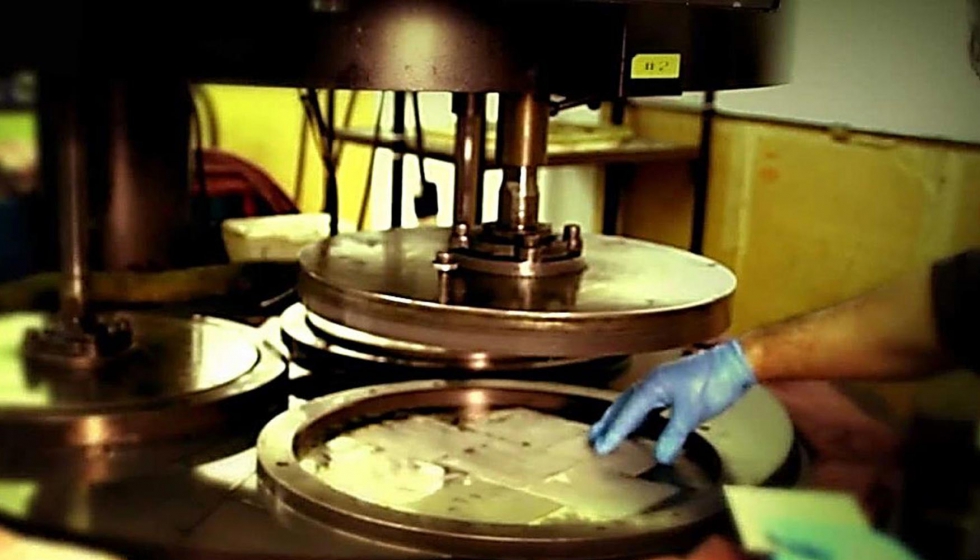
Menos conocidos son los procesos de superacabado isotrópico y acabado por vibración. Debido a las demandas cada vez mayores en cuando a durabilidad de los engranajes utilizados en grandes cajas de cambio, las compañías Osro y REM han desarrollado el superacabado isotrópico (ISF). Se trata de un proceso para mejorar la superficie de los engranajes de grandes dimensiones, componentes estos, de alto valor añadido.
Ambos procesos, denominados químico-mecánicos, consisten en introducir dentro de una cuba de trabajo las piezas a tratar, aditivos químicos y unos abrasivos que pueden ser de base cerámica, metálica o polimérica. Después, dicha cuba se pone en movimiento mediante un sistema vibratorio provocando un movimiento relativo de los abrasivos y las piezas. La acción de frotamiento constante entre abrasivos y piezas causa la eliminación de los picos de rugosidad de las piezas.
Entre sus muchas ventajas, estos procesos reducen la fricción y el desgaste de la superficie, aumentan la durabilidad y mejoran la resistencia a la corrosión. Además del sector de fabricación de engranajes, también han demostrado ser eficaces en otras aplicaciones industriales, incluyendo el sector aeroespacial, de automoción, sector médico y la generación de energía.
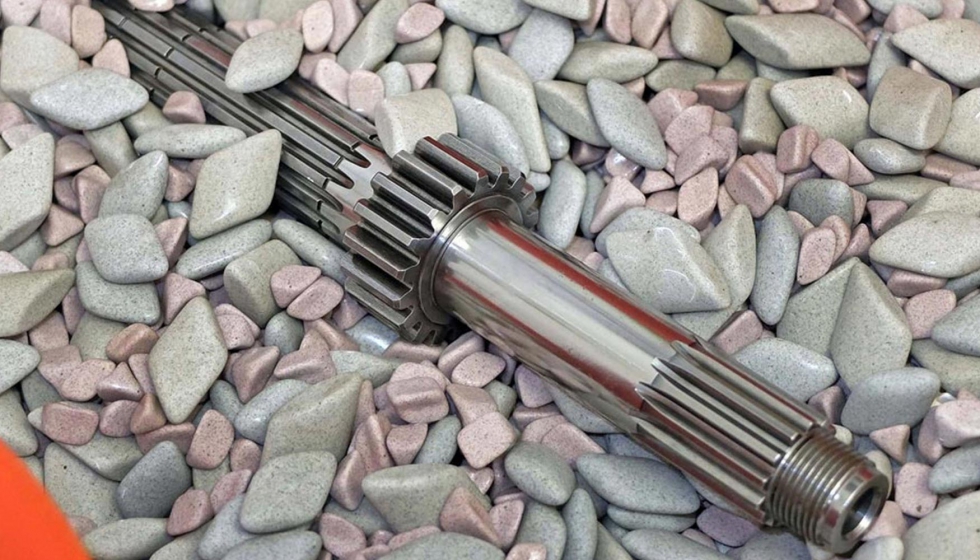
Otros procesos como el granallado (Shot peening) o el bruñido hidrostático con bola (Ball burnishing) además de conseguir un acabado superficial excelente también producen cambios en las propiedades mecánicas del material.
El proceso de bruñido consiste en presionar una herramienta de bruñido, sobre las microirregularidades de la superficie y generar un deslizamiento y/o rodadura sobre la superficie a tratar. De esta forma se consigue una capa de material endurecido por deformación que presenta mejores características tanto físicas como mecánicas respecto al material base. Los efectos del bruñido sobre la superficie son la mejora de la rugosidad final, el aumento de la dureza superficial y la introducción de tensiones residuales de compresión. Estos efectos, a su vez, hacen que el componente mejore sus propiedades en cuanto a vida a fatiga, corrosión y resistencia al desgaste.
Aunque con peores resultados de rugosidad superficial, mediante el granallado se produce un efecto similar en la superficie del material. En este caso, el proceso se realiza ‘disparando’ partículas esféricas a gran velocidad sobre la superficie. Las partículas, que varían entre 0,1 y 2 mm de diámetro, pueden ser de acero, cerámica o cristal.
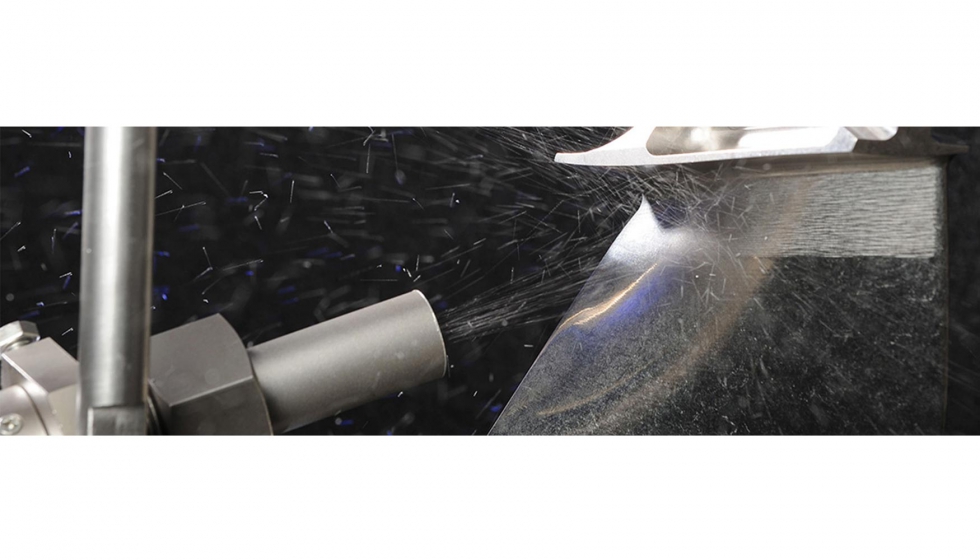
Otro proceso es el superpulido, quizá más enfocado a sectores como la óptica y la fabricación de lentes. Este proceso otorga una rugosidad superficial extremadamente baja (Ra≈1Å) al componente donde se aplica, comúnmente en materiales como el cristal de silicio, zafiro, YAG, etc. Son casos de especial aplicación en los que se trabaja con longitudes de onda corta como en las ópticas de rayos X y en aplicaciones de fotolitografía.
Como se ha podido vislumbrar de los párrafos anteriores, el mecanizado general de los materiales está muy lejos de haber sido resuelto. Es un hecho que se han realizado grandísimos avances desde que se empezó a mecanizar allá por el Siglo XIX, pero la continua evolución de la técnica y con ello el avance en nuevos materiales, hace que el proceso no se detenga nunca, y la evolución de técnicas y herramientas de mecanizado discurra paralela a la propia evolución de los materiales que todos los ámbitos de la industria demandan. Para ello, instituciones y centros de investigación en fabricación avanzada como el mencionado CFAA vienen a tratar de dar solución a esta problemática.
El MRL, nuevo paradigma del desarrollo
El conocido como MRL (Manufacutirng Readiness Level) surge de la necesidad de crear un criterio uniforme de evaluación del nivel de desarrollo o madurez de un producto o proceso de fabricación. El objetivo es adaptar la escala tecnológica TRL (Technology Readiness Level) al ámbito de la fabricación, y los 10 niveles de la escala MRL están relacionados con su equivalente tecnológico que consta de 9 niveles. El nivel de madurez de un proceso de fabricación requiere de un nivel mínimo de desarrollo tecnológico, y es por ello que estas dos escalas son complementarias.
Por medio de esta escala se pretende dotar de un conocimiento relativo acerca del desarrollo del proceso, y por consiguiente de los riesgos que van asociados a cada nivel. A medida que se ascienden niveles en la escala, la viabilidad de implantación en la industria del proceso aumenta, puesto que se encuentra más cerca de su ámbito de actuación, tal y como se puede observar en la figura, la cual refleja la transición desde el ámbito de la investigación hasta la implantación del proceso desarrollado dentro de la industria.
Tal y como refleja la imagen, la escala evoluciona desde un nivel TRL 1, con el menor nivel de madurez tecnológica que recoge los principios básicos observados, hasta un nivel TRL 9, donde la tecnología ya se encuentra en funcionamiento con éxito en producción, plenamente implantada por tanto en la industria. La zona intermedia constituye una zona de vacío conocida como el ‘valle de la muerte’ donde se produce la transición desde la investigación básica de las universidades y centros tecnológicos, hacia la investigación aplicada que se realiza en las empresas. Es en este punto donde instituciones como el mencionado Centro de Fabricación Avanzada Aeronáutica (CFAA) vienen a dar solución a esta problemática, como un nuevo modelo de relación en el eje universidad-empresa. Los trabajos que se realizan en este centro se orientan a trabajar y desarrollar los ‘MRL 6-7 o su equivalente ‘TRL 5-6’, donde se requieren pruebas de validación en entornos representativos, con máquinas muy parecidas o en ocasiones idénticas en cuanto a tamaño y características.

Aleaciones Gamma Ti-Al
Las superaleaciones de tipo intermetálico Gamma TiAl, son aleaciones que ofrecen excelentes propiedades mecánicas, con bajos valores de densidad de 4 g/cm3, alta resistencia a elevadas temperaturas, alta conductividad eléctrica y térmica, resistencia a la oxidación, una tensión de rotura de 1.000 MPa, un módulo de Young de 160 GPa, siendo posible su mecanizado. Existen tres tipos fundamentales de aleación, el tipo TNB [Ti (44-45)Al-(5-10)Nb-(0,2-0,4)C] para aplicaciones a muy altas temperaturas, manteniendo altos valores de resistencia y oxidación, con aplicaciones aeronáuticas. El tipo MoCuSi [Ti (43-46)Al-(1-2)Mo-(0,2)Si-Cu] para utilización a bajas temperaturas, con alta resistencia por debajo de los 650 °C. El tercer tipo es el TNM [Ti (43-45)Al-(5-8)Nb-Mo-(0-0,4)B-C] para aplicaciones a altas temperaturas. Dos de los grandes inconvenientes que presentan este tipo de aleaciones, son su gran sensibilidad a las impurezas y su alto costo de fabricación. Existen dos formas para fabricar estas aleaciones, que son, como aleación solidificada en lingote, o como aleación extruida. Las propiedades mecánicas que presentan las aleaciones extruidas, son superiores a los materiales obtenidos en lingote. Como se puede ver en la Figura 9, las aleaciones fundidas y solidificadas en lingotera, presentan una estructura sin ninguna orientación preferente, típica de los materiales no laminados o extruidos, mientras que las aleaciones que posteriormente han sido extruidas, presentan una estructura orientada hacia la dirección de extrusión. Dos ejemplos de la utilización de estos materiales, se pueden ver en los motores de aviación y automoción. En los motores aeronáuticos, se utiliza principalmente en los alabes del compresor de baja presión, los más exteriores y cercanos al fan de entrada, mientras el sector de la automoción hace uso de estos materiales en las bielas de los motores de competición. Las características de ligereza y excelentes propiedades mecánicas de las aleaciones titanio-aluminio descubiertas hace ya unos años, han tenido sus limitaciones para su utilización comercial a gran escala, que ha sido posible únicamente en los últimos anos. Las razones principales del uso restringido de estas aleaciones ha sido la del elevado coste en comparación a otras aleaciones de aluminio con las que competía y la existencia de aspectos técnicos sin resolver en las aleaciones Ti-Al desarrolladas hasta entonces, tales como su pobre tenacidad y ductilidad, la falta de desarrollo de tratamiento térmicos y superficiales adecuados.
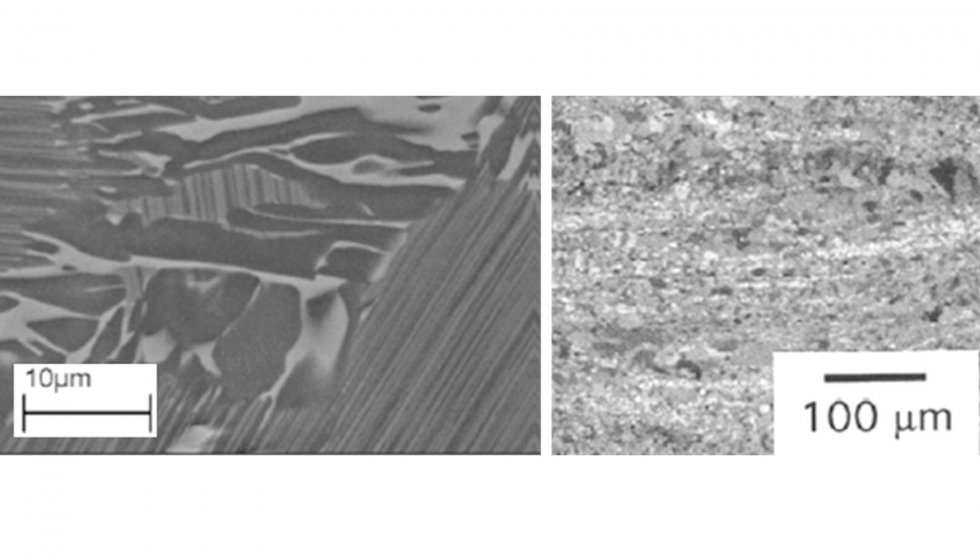
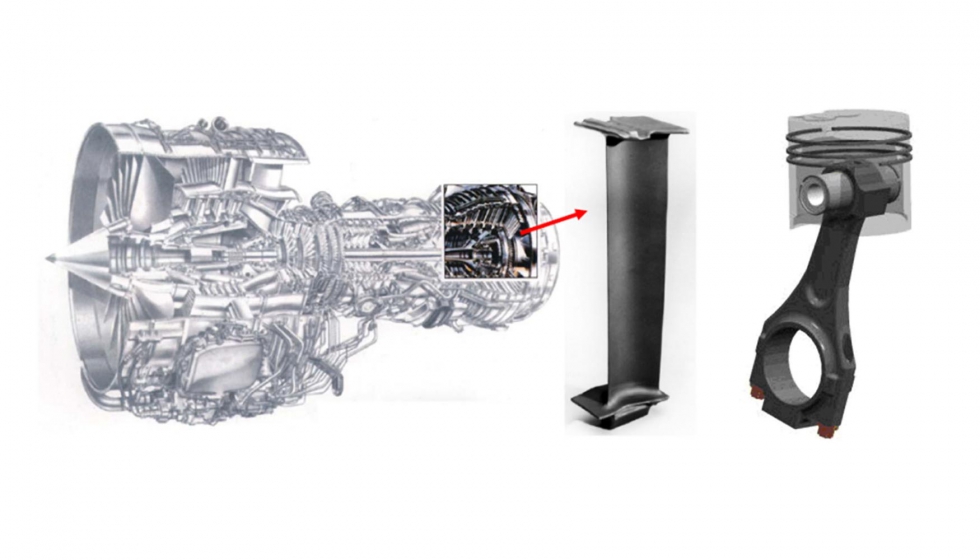