19 Congreso de Maquinas-Herramienta y tecnología de fabricación, Donostia-San Sebastián
Medida de la precisión de posicionamiento en máquinas-herramienta de grandes dimensiones
Hoy en día la fabricación de piezas de gran tamaño es una fuerza impulsora en la industria de las máquinas-herramienta. Esta demanda ha desafiado a los fabricantes a materializar diseños a una nueva escala y es más, a mantener la precisión de estas máquinas al nivel de las de máquinas más pequeñas. Por otro lado, los constructores carecen de las herramientas apropiadas para evaluar la precisión de posicionamiento de las grandes máquinas de una manera práctica. El conjunto de instrumentos clásicos utilizados para la puesta a punto de la máquina tales como niveles, escuadras o interferómetros lineales se está quedando obsoleto para medir esta nueva familia de máquinas. La tecnología de medición más adecuada para esta tarea parece ser la interferometría láser. Otros dispositivos tales como el BallBar son capaces de proporcionar mediciones precisas aunque en un rango demasiado pequeño como para verificar máquinas de grandes dimensiones.
Actualmente cada vez más talleres tienen acceso a dispositivos de láser tracker. Estos son muy útiles durante el montaje y puesta a punto de la máquina; sin embargo carecen de la precisión suficiente para verificar la precisión de posicionamiento de la herramienta.
La manera de superar estas dificultades parece estar basada no tanto en el desarrollo de nuevos instrumentos como en la manera en la que se pueden utilizar los existentes.
Últimamente han surgido varios enfoques que aprovechan la alta precisión del interferómetro láser y la capacidad de seguimiento. La idea básica consiste en la combinación de las medidas lineales de los interferómetros tomadas durante mediciones secuenciales siguiendo un esquema de multilateración [1]. La norma internacional ISO 230-1 para la verificación de máquinas herramienta, ha sido revisada en 2012 para incluir la metodología de multilateración en verificaciones volumétricas [2].
Sin embargo, cuando se trabaja con máquinas-herramienta de gran tamaño se hacen evidentes algunas limitaciones. Los experimentos realizados han demostrado que el principal obstáculo para alcanzar el límite teórico de la precisión de este método es la inestabilidad de las condiciones ambientales y el comportamiento térmico de la máquina. Debido a estos factores, las precisiones esperables de una multilateración pura se desvanecen.
En este trabajo se ha desarrollado una aproximación intermedia, donde se fusionan las mediciones mediante multilateración laser y medidas de inclinación mediante niveles electrónicos de precisión, de manera que se obtienen medidas muy precisas en un tiempo muy ajustado.
Por un lado, son necesarias menos mediciones por lo que el tiempo de medición total se reduce. El beneficio es doble, ya que la máquina sufre menores desviaciones térmicas durante la medición y además la medición resulta más económica.
Por otra parte, se logra una incertidumbre de medida real muy por debajo de las desviaciones que la máquina sufre durante su uso normal. De esta manera la técnica es idónea para proporcionar un mapa de errores de posicionamiento lo suficientemente preciso que puede utilizarse para mejorar el rendimiento de la máquina en la retroalimentación del diseño así como en compensaciones futuras.
Descripción del método
Históricamente la medida de los errores geométricos de posicionamiento de las máquinas-herramienta se ha hecho en diferentes pasos, separando para cada eje los errores de posicionamiento, las rectitudes y perpendicularidades entre ejes. Este procedimiento se ha seguido tradicionalmente debido a las herramientas que había disponibles. La verificación de máquinas mediante esta metodología está regulada por estándares internacionales [2]. Desde la introducción de las técnicas de multilateración se ha podido medir la posición espacial con la suficiente precisión de forma que el procedimiento anterior ya no resulta necesario. Además las técnicas de multilateración son lo suficientemente prácticas como para obtener información en el volumen de trabajo completo de la máquina y no solamente en puntos de ciertas líneas seleccionadas.
Existen diferentes métodos para medir movimientos traslacionales y rotacionales [3,4]:
Por una parte, se puede obtener información completa en los 6 grados de libertad (gdl) de la máquina midiendo distancias desde puntos fijos en los que se coloca el equipo laser hasta los puntos en los que se sitúa el reflector situado en la punta de herramienta dentro del volumen de trabajo. Se puede demostrar matemáticamente que son necesarias 8 posiciones del interferómetro láser para medir los 6 gdl en la punta de herramienta.
Por otra parte, se puede obtener una serie prácticamente completa de medidas conjugando la multilateración de cuatro estaciones laser con la que se obtienen las posiciones de la herramienta, junto con medidas de inclinación obtenidas con dos niveles electrónicos de precisión para obtener la rotación en la punta de herramienta en dos de los tres ejes cartesianos.
A continuación se muestran las ventajas de usar la técnica de multilateración para medir las posiciones y los niveles electrónicos para medir las dos rotaciones. En la práctica, las diferentes posiciones desde las cuales se toman las medidas con el equipo láser se llevan a cabo consecutivamente. Esto es debido al alto coste del equipo no siendo viable el uso simultáneo de varios interferómetros. De manera que la máquina se posiciona automáticamente en los puntos preestablecidos cada vez que se coloca el interferómetro en una estación diferente desde donde se toman las medidas. En la figura 1 se muestra un diagrama de la máquina y las diferentes posiciones de interferómetro laser.
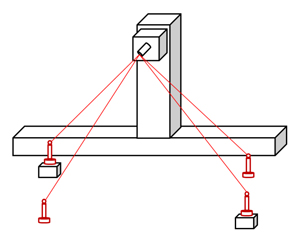
Si queremos obtener los 6 gdl de la máquina mediante multilateración pura, serán necesarias 8 estaciones, alargando sustancialmente el tiempo de medida que puede suponer varias horas. Esto conlleva que durante este tiempo la estabilidad de la máquina se puede ver afectada por las deformaciones térmicas y esto irá en detrimento de la incertidumbre de la medida. Además el tiempo invertido en realizar las medidas supone un gasto ya que la máquina no está produciendo.
Sin embargo, el uso de niveles electrónicos proporciona una medida directa de la magnitud de interés, esto es, las desviaciones angulares de la máquina en la punta de herramienta. Con ellos se puede medir la inclinación en dos de los tres ejes cartesianos. Los niveles de precisión comerciales que existen hoy en día proporcionan una resolución de hasta 1 micra/metro, y el funcionamiento inalámbrico del equipo permite registrar los datos a distancia en formato digital. Las medidas se toman en cada punto en el que se posiciona la máquina, durante todas las repeticiones sucesivas.
De esta manera los niveles no sólo proporcionan la medida de interés, sino que además son un valioso indicador de la estabilidad de la máquina durante el tiempo de medida. Este último punto es muy importante ya que como se ha mencionado anteriormente las medidas de multilateración sólo ofrecen una incertidumbre lo suficientemente baja si la máquina se ha mantenido estable durante el proceso. La otra gran ventaja de la utilización de los niveles consiste en poder reducir el tiempo total de medida, ya que sólo son necesarias 4 estaciones laser de medida frente a las 8 que habría que realizar sin ellos.
El tiempo es un factor crucial que afecta a dos aspectos diferentes de las medidas:
i) Tiempo de ocupación de la máquina: es conveniente sacar la máquina de su programa de producción el menor tiempo posible ya que cada hora que la máquina esté parada sin trabajar es dinero gastado.
ii) Estabilidad de la máquina: como los factores ambientales pueden cambiar durante las medidas (por ejemplo la temperatura del taller), hacer las medidas en el menor tiempo posible asegura que la desviación por efectos térmicos se mantiene dentro de lo aceptable y la incertidumbre de la medida no se ve afectada.
De esta manera, el utilizar los niveles electrónicos no sólo proporciona un indicador de la estabilidad de la medida sino que contribuye a la propia estabilidad de la misma.
En la figura 2 se puede ver una comparación entre los tiempos de medida de los diferentes métodos para medir el error de posicionamiento de la máquina. Se muestran también algunos perfiles de temperatura que corresponden a medidas específicas realizadas en máquinas reales. Puede verse cómo el método propuesto reduce a la mitad el tiempo necesario para la verificación de la máquina.
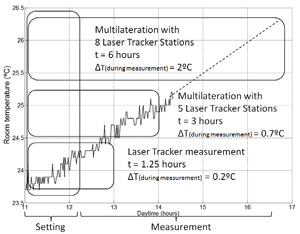
Medidas experimentales
Para realizar las medidas experimentales se ha utilizado el siguiente equipamiento comercial:
i) Leica Absolute Tracker AT901MR: el laser tracker es un equipo muy potente que combina un interferómetro laser que tiene capacidad de seguimiento con encóderes, de manera que se proporciona la posición del reflector en el espacio. Es muy utilizado para el montaje de máquinas, pero sin embargo tiene un punto débil que es no tener la suficiente precisión como para realizar verificaciones como las contempladas en este trabajo. Esta limitación proviene de la medida de los encóderes que no tienen la gran precisión de medida que posee el interferómetro láser. Sin embargo para la multilateración la medida de los encóderes no se utiliza, solamente se toman los datos obtenidos con el interferómetro.
ii) Wyler BlueLevel: estos son niveles electrónicos de última generación. Poseen una gran resolución de 1 micra/metro, y además siendo inalámbricos son capaces de enviar la medida remotamente por Bluetooth a un receptor que puede ser conectado a un PC para registrar las medidas. De esta manera al realizar medidas a grandes distancias no resulta un problema como es el caso de los volúmenes de trabajo de las grandes máquinas-herramienta. Por otra parte, el tiempo de estabilización del sensor de inclinación es de tan sólo 4 segundos, por lo que no se pierde un tiempo importante en cada medida individual.
En la figura 3 se muestra una fresadora de columna móvil modelo 30KCU2600R de la empresa Zayer, la cual fue utilizada para realizar unas pruebas experimentales en las que se utilizó la metodología descrita en este trabajo para realizar las medidas.
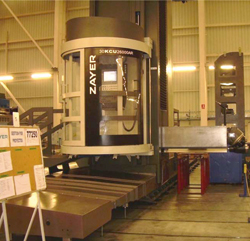
En la figura 4 se muestran dos fotografías del montaje utilizado durante las medidas. Se puede observar la máquina medida, el láser tracker, el reflector y los niveles de precisión colocados sobre el cabezal.
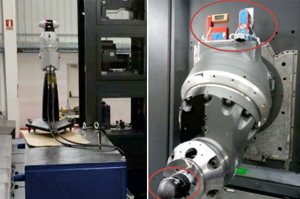
El volumen utilizado fue el siguiente:
- Eje longitudinal: 2.000 mm
- Eje transversal: 2.000 mm
- Eje vertical: 5.000 mm
Resultados de las medidas
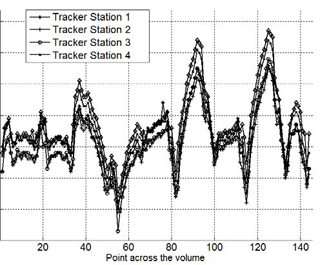
En la figura 6 se muestran en 3D los resultados de las medidas realizadas del posicionamiento de 144 puntos dentro del volumen del trabajo. Estos puntos estaban distribuidos a lo largo de 4 planos verticales. La magnitud de los errores ha sido amplificada para poder visualizarse (no a escala). Además para una mejor visualización se ha modificado también la escala de los diferentes ejes, siendo el vertical en la realidad mayor que el resto (5.000 frente a 2.000 mm).
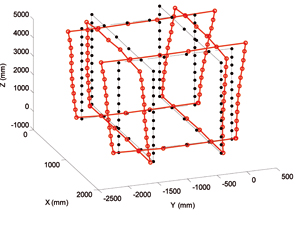
En la figura 7 se muestra la comparación de dos planos paralelos situados a 2.000 mm de distancia frente a las posiciones teóricas marcadas en negro.
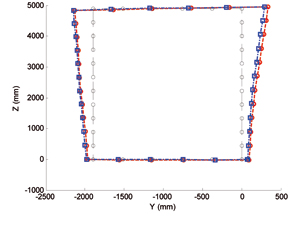
Existen varias fuentes que afectan a la incertidumbre de las medidas de multilateración:
i) Por el tipo de problema matemático en el que se basa, las medidas proporcionan una redundancia cuando se utilizan más puntos de medida que los estrictamente necesarios para poder resolver el sistema de ecuaciones asociado, en este caso para 4 estaciones el mínimo es de 6 puntos del reflector.
ii) La inexactitud inherente a las medidas del interferómetro láser: éstas dependen de las condiciones ambientales, como son la temperatura, presión y humedad del aire. Frente a cambios en estos parámetros la medida se vuelve menos precisa.
iii) La máquina no proporciona estabilidad perfecta a lo largo del tiempo: incluso siendo una máquina con una gran repetibilidad, el efecto en el tiempo de las deformaciones térmicas supone un factor limitante a tener en cuenta.
Para estimar la calidad de las medidas realizadas puede usarse un histograma de residuos del sistema de ecuaciones que proporciona una buena indicación de la misma. En la figura 8 se muestran los residuos de las medidas realizadas. Para poder proporcionar este indicador, se utilizaron 5 estaciones de interferómetro láser, uno más de los 4 que eran estrictamente necesarios para poder resolver el sistema de ecuaciones. Puede observar cómo todas las medidas muestran menos de 5 micras de discrepancia. Esto demuestra que en el caso analizado la repetibilidad de la máquina fue buena y que las condiciones ambientales las adecuadas.
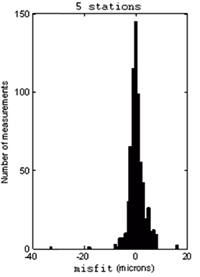
En la figura 8 se muestra una comparación de medidas de rectitud extraídas de las medidas en el espacio de los puntos analizados. Corresponden a dos movimientos de la máquina a lo largo del eje vertical en un recorrido de 5.000 mm en diferentes líneas. Puede versa cómo el comportamiento de la máquina es similar en los dos recorridos y que las medidas son lo suficientemente precisas como para estudiar errores de rectitud en un curso de 5.000 mm.
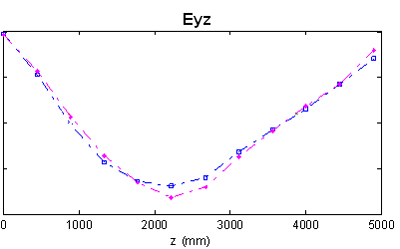
Próximos trabajos
Las próximas tareas a realizar se centrarán en el desarrollo de procedimientos de medida que permitan medir los grados de libertad rotacional mediante técnicas de multilateración que reduzcan el tiempo de medida respecto de las existentes actualmente. También se desarrollará la metodología para utilizar la información obtenida en este tipo de medidas para realizar una compensación vía software en la máquina.
Conclusiones
En este trabajo se han descrito las ventajas de complementar resultados de multilateración y medidas de inclinómetros de precisión a la hora de medir el posicionamiento lineal y rotacional de una máquina-herramienta de grandes dimensiones para realizar la verificación volumétrica de la misma. Los beneficios pueden resumirse como:
i) Al medir los gdl rotacionales con niveles electrónicos de precisión se reduce drásticamente el tiempo de medida comparado con medirlos mediante métodos basados en la multilateración, con dos beneficios principales:
- Mayor estabilidad de la máquina durante las medidas.
- Menor tiempo de máquina desocupada con menor coste asociado.
ii) La medida de los niveles proporciona adicionalmente una buena indicación de la estabilidad de la máquina y por tanto de la calidad de las medidas.
Las medidas realizadas presentan una incertidumbre suficientemente pequeña para poder verificar volúmenes de trabajo con cursos de máquina de varios metros. El tiempo de medida es más reducido que otros métodos existentes actualmente.
Por último, realizar la verificación volumétrica de la máquina proporciona información muy valiosa sobre el comportamiento de la misma en todo su espacio de trabajo. Esto proporciona una ventaja competitiva notable ya que de esta manera se pueden aplicar compensaciones mecánicas o numéricas durante la puesta a punto o recalibración periódica de la máquina.
Agradecimientos
Este trabajo de investigación se ha realizado gracias al Gobierno Vasco por los Programas Emaitek y Etorgai, dentro de los cuales se ha enmarcado el Proyecto Hiperion, al CDTI por el Proyecto Impeler y a Zayer en particular por permitir mostrar el método con una de sus máquinas.
Referencias
[1] 478E.B. Hughes et al. Design of a High-Accuracy CMM Based on Multi- Lateration Techniques. CIRP Annals - Manufacturing Technology, 2000; 49: 391-394.
[2] International Organization for Standardization, ISO 230-1:2012, Test code for machine tools - Part 1: Geometric accuracy of machines operating under no-load or quasi-static conditions.
[3] H.Schwenke et al. Geometric error measurement and compensation of machines. An update. CIRP Annals - Manufacturing Technology, 2008; 57: 660-675.
[4] H.Kunzmann et al. Error mapping of CMMs and machine tools by a single tracking interferometer. CIRP Annals - Manufacturing Technology, 2005; 54:475.