Ejecución de pilotes de gran diámetro en el viaducto sobre el río Ulla en la ría de Arousa (1ª Parte)
El Eje Atlántico constituye un corredor ferroviario de alta velocidad situado a lo largo de la costa Oeste de Galicia, que permitirá conectar directamente las ciudades de Vigo, Santiago de Compostela y A Coruña. Como consecuencia de la orografía irregular de la zona, se han previsto 37 túneles (59,2 km de longitud acumulada, que supone un 38% del recorrido total) y 32 viaductos (14,9 km de longitud acumulada, que supone un 6% del recorrido total) (I).
El viaducto sobre el río Ulla en su desembocadura en la ría de Arousa (entre las localidades de Catoira y Rianxo, en Galicia), presenta un vano de luz máxima de 240 m, que es la mayor de todos los viaductos del eje. Sus apoyos quedan dentro de la ría, y debido a la presencia de depósitos aluviales de gran espesor, hace necesario cimentar mediante pilotes de 1,5m de diámetro empotrados en el macizo granítico subyacente. Las complejas condiciones de trabajo requirieron de un control en obra muy intenso, a fin de poder obtener las condiciones estructurales de diseño.
En esta primera parte del artículo se describe la ejecución de estos pilotes: criterios de diseño, investigación geotécnica específica, procedimientos de perforación, aceptación de la longitud del empotramiento en obra, labores de limpieza de la punta, y hormigonado, así como una breve descripción de las medidas adicionales que se adoptaron.
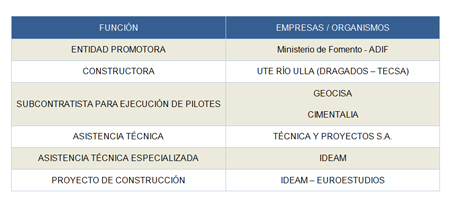
Descripción del viaducto
El viaducto presenta una tipología de tablero metálico en celosía de doble acción mixta. Tiene una longitud total de 1.620 m, cuyos tres vanos centrales tienen una distribución de 225 m+240 m+225 m (II). En total, el viaducto tiene 11 pilas, de las que las pilas 5, 6 y 7 se proyectaron dentro del cauce (III) (Fig.1).
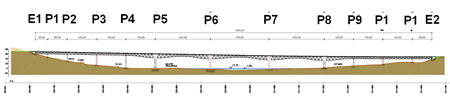
Durante los años 2009 a 2011, se llevaron a cabo las actividades necesarias para la ejecución de las cimentaciones diseñadas en proyecto para el viaducto sobre el río Ulla. Las cimentaciones se apoyaron todas en roca. Todos los apoyos se realizaron mediante zapatas cimentadas en un macizo rocoso granítico sano, excepto las pilas 5 y 6 (Fig. 2), que se cimentaron mediante pilotes empotrados en roca (Foto 1).
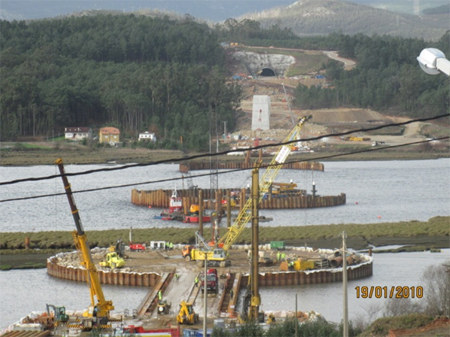
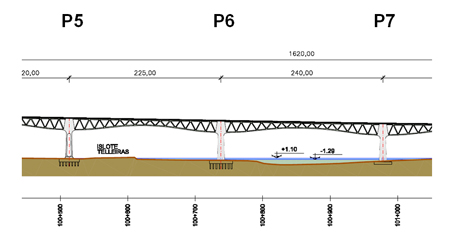
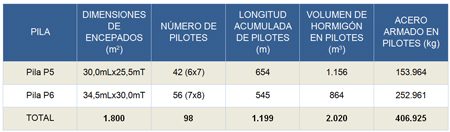
Las cimentaciones profundas consisten en encepados de grandes dimensiones apoyados en pilotes de 1,5m de diámetro. Los pilotes se empotran en el substrato rocoso de la ría un diámetro (IV) (Tabla 2). El proyecto establecía empotrar los pilotes dos diámetros (V), pero se concluyó (VI) que las condiciones geotécnicas del substrato rocoso y la rigidez del viaducto permitían reducir este valor.
Condiciones de trabajo en la ría
La ejecución de estos pilotes estuvo condicionada por la posición de los apoyos dentro del cauce actual del río Ulla. Para posibilitar estos trabajos, fue necesaria la ejecución de islas artificiales temporales, consistentes en recintos doble-tablestacados rellenados con material granular vertido (Foto 2). Sobre estas islas se realizaron todas las labores para la ejecución de los pilotes.
Con este diseño de plataformas de trabajo se permitió la ejecución de la perforación y hormigonado de los pilotes en condiciones convencionales, ya que se realizaba desde la superficie de la plataforma, si bien en condiciones meteorológicas especialmente adversas, con bajas presiones, y mareas vivas, la lámina libre del agua alcanzaba una cota próxima a la de la plataforma de trabajo (Foto 3).
En el fondo de la perforación de los pilotes se acumulaba agua de infiltración, procedente de la ría, y que condicionaba la estabilidad de las paredes de excavación en los tramos de suelos y roca alterada. Mediante la hinca de entibación metálica, se redujeron los riesgos de contaminar el fondo por el desprendimiento de estos materiales, y de generar volúmenes de sobreexcavación importantes. Debido a la dificultad de empotrar la entibación en la roca sana no se consiguió evitar inestabilidades puntuales en la excavación de algunos de los pilotes.
Por su lado, las labores de excavación del relleno dentro del recinto interior de tablestacas, el descabezado de pilotes y la ejecución del encepado se hicieron en condiciones predominantemente secas, gracias a la impermeabilización del recinto interior mediante un anillo de jet-groting en la zona de contacto de la tablestaca con el estrato rocoso, controlando en todo momento mediante pozos de control y bombeo la aparición de pequeñas filtraciones de agua puntuales.
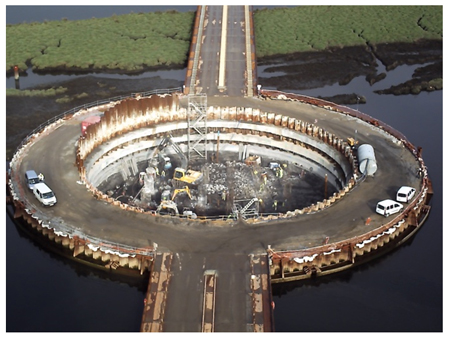
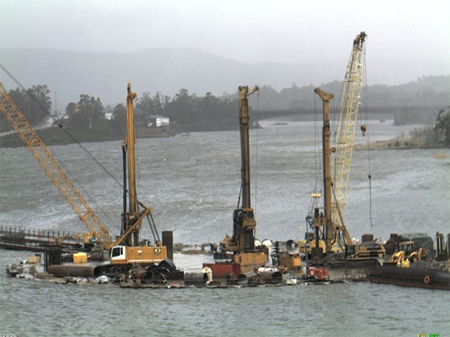
Especificaciones técnicas de los materiales estructurales
Los pilotes se construyeron con un hormigón tipo HA-35/B/20/IIIc/Qb y un acero para armar de calidad B500S (VII).
La necesidad de adoptar un hormigón de resistencia de 35MPa reside fundamentalmente en la necesidad de garantizar la durabilidad en estas condiciones de exposición. Pero, a su vez, también permite cumplir con las exigencias derivadas de los estados tensionales previstos por las cargas de diseño.
La carga máxima (VIII) estimada por pilote en proyecto es de 1.240Tn para un diámetro nominal de 1500 mm. Esto supone una tensión de trabajo del orden de 7MPa. El diámetro del pilote en el tramo de roca se redujo a 1400 mm por causas de ejecución. Esta reducción supuso un incremento en el valor de esta tensión de trabajo, que pasó a ser de 8MPa. Esta circunstancia redundó en la conveniencia de adoptar medidas adicionales que permitiesen reforzar las condiciones de ejecución y funcionamiento del pilote, fundamentalmente en la zona del empotramiento.
Si se aplica como referencia el Código Técnico de Edificación (CTE), para pilotes in-situ con un hormigón de 35MPa de resistencia característica y entubado, el tope estructural obtenido con estas condiciones es del orden de 8,4MPa. Con un control de ejecución intenso, según esta norma se puede incrementar en un 25% adicional, por lo que alcanza valores del orden de 10,5MPa. En cualquier caso, estos valores son muy superiores a los tradicionalmente aplicados, que están comprendidos entre 4MPa y 6MPa.
Las cuantías de acero difieren entre los pilotes de la pila P5 y la P6. En la primera, la cuantía necesaria es del orden de 133 kg/m3 frente a 292 kg/m3 en la pila P6. Esta importante diferencia reside fundamentalmente en tres causas, relacionadas todas ellas con las diferencias de longitudes de pilotes que afectan de manera directa a la rigidez estructural de los mismos.
En primer lugar, la longitud promedio de los pilotes de la Pila 6 es del orden de 9,5m, muy inferior al promedio de 15,5m de los pilotes de la Pila 5. Esto es debido a que el substrato rocoso competente está más próximo a superficie en la Pila 6 que en la Pila 5.
Como segunda causa, en la pila 6 se detectó una variación de cota importante del techo del substrato rocoso, con un aumento de profundidad hacia el centro del cauce. Más adelante se incluyen los perfiles estratigráficos en sentido longitudinal de cada pila. Esta diferencia de longitudes en pilotes tan cortos hizo necesario el refuerzo mediante armadura en las tres filas de pilotes más cortos, situadas a menor PK, sin mayor repercusión ya que esta medida se adoptó antes del inicio de los trabajos.
Por último, a medida que se iban ejecutando cada uno de los pilotes, se hizo patente la irregularidad del techo rocoso, con unas diferencias de profundidades en pilotes adyacentes en la misma fila de hasta 6 metros. Ante esta situación, se realizó de nuevo un recálculo estructural en el que se comprobó la necesidad de reforzar algunos de ellos mediante la ejecución de micropilotes en el fuste.
Condiciones geológicas y geotécnicas de cimentación
Las excavaciones de las zapatas de las pilas del viaducto ubicadas en las orillas del río se realizaron con anterioridad a la ejecución de los pilotes, de tal manera que se pudo reconocer en detalle las características geotécnicas del macizo rocoso. Además, en fase de diseño se realizaron un total de 4 sondeos en la Pila 5, y 3 sondeos en la Pila 6, además de 16 ensayos de penetración dinámica para reconocer el espesor y la compacidad de los suelos. En fase de ejecución, se realizaron preforos monitorizados en los ejes de los pilotes de la Pila 5, previo al inicio de la perforación de los pilotes.
El macizo rocoso sano está formado por granitos de anatexia migmatizados. En las excavaciones de las zapatas, se identificaron claramente un granito sano de color azul (Foto 4) y un granito sano de color marrón (Foto 5). El primero predomina en la orilla Sur mientras que el segundo en la Norte. El contacto, que será irregular, se estima que está en la zona de inundación, por lo que no pudo cartografiarse.
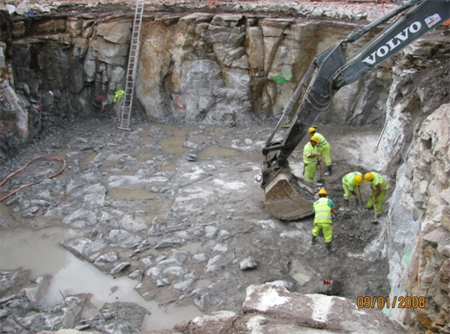
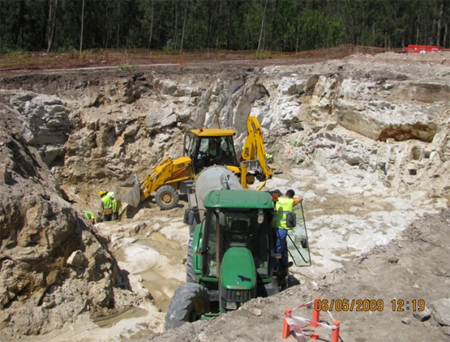
La campaña geotécnica que se realizó no demostró que la respuesta geotécnica de ambas rocas granitoideas fuera muy diferente, de tal manera que los parámetros geotécnicos adoptados en diseño fueron los mismos (Tabla 3).
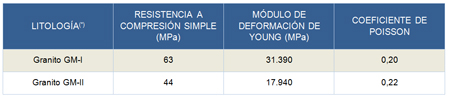
De los resultados de la campaña, se constató que los niveles de mayor alteración del macizo rocoso parecían haber sido arrastrados por la acción erosiva del río, de tal manera que bajo los depósitos aluviales afloraba prácticamente roca sana, en grado GM-II a GM-I. Con estas condiciones geotécnicas, la resistencia por punta en el terreno para un pilote aislado puede asumirse igual a 10MPa. Por tanto, podría considerarse admisible la tensión de trabajo transmitida por los pilotes.
La interpretación de los resultados de la investigación geotécnica permitió elaborar una serie de perfiles estratigráficos en detalle, tanto en sentido longitudinal como transversal, de cada pila. En la Pila 5 (Fig.3) se concluyó que los pilotes tendrían una longitud, hasta empotramiento, comprendida entre 12 m y 20 m, mientras que en la Pila 6 (Fig.4) serían más cortos, entre 5 m y 14 m.
Los niveles de suelos están formados por intercalaciones limoarcillosas de consistencia blanda. En la Pila 5, además, se detectó la presencia de un nivel de gravas de densidad media a alta, que originó ciertas dudas de cara a la hinca de la camisa del pilote. No obstante, el proceso de hincado de tablestacas y camisas metálicas pudo penetrar, en general, este nivel de grava, hasta alcanzar aparentemente el techo del substrato rocoso sano.
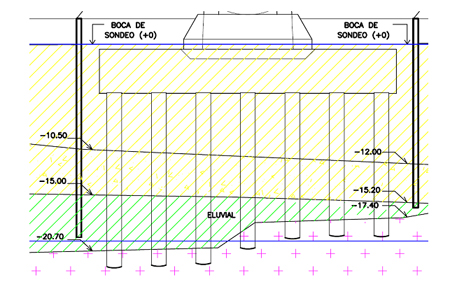
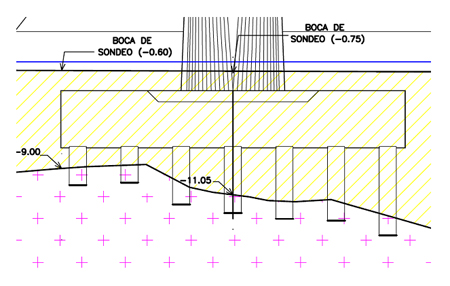
Cabe destacar que la previsión en fase de diseño de la longitud de los pilotes fue, en general, menor que la realidad, por lo que fue necesario perforar algo más de longitud de pilote que la inicialmente prevista. Las diferencias en algunos casos fueron métricas, quedando generalmente el substrato a una cota inferior de lo esperado.
Como también se había podido reconocer en detalle el fondo de excavación de las zapatas de las otras pilas, y con la información obtenida durante la campaña geotécnica, se concluyó que el techo del macizo rocoso presenta una geometría intensamente irregular, que habría precisado de una inversión en investigación geotécnica mucho mayor a la realizada para alcanzar un grado de conocimiento detallado. En cualquier caso, la aproximación alcanzada permitió un correcto diseño de la obra, que pudo absorber como tolerancia de ejecución las irregularidades en el emplazamiento de cada pilote.
Procedimiento constructivo
Dado que se trataba del camino crítico en esta fase de la obra, se consideró conveniente que dos máquinas trabajasen simultáneamente, con una tercera máquina como refuerzo puntual (Foto 6). Las máquinas perforadoras tenían un par comprendido entre 250 kNxm y 360 kNxm, que permitió perforar el empotramiento en roca en las condiciones descritas.
Por otra parte, se tuvo en cuenta que el área de trabajo era muy reducida (2.250 m2 en la Pila 5 y 3.160 m2 para la Pila 6) y que había otras actividades que se estaban realizado a la vez (fundamentalmente inyecciones de jet-grouting perimetrales en las islas, hincado del tablestacado interior, tránsito de maquinaria para la ejecución del pantalán provisional, etc.).
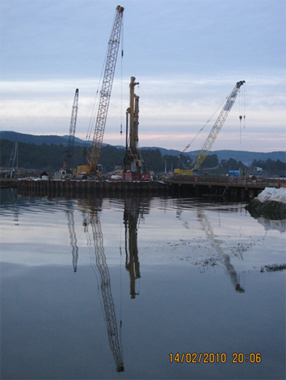
Los trabajos de perforación y hormigonado se organizaron en turnos continuos, días laborables y festivos, que supuso la dedicación del orden de 1 mes por pila para la ejecución de todos pilotes.
Para evitar el desprendimiento del material de las paredes de excavación, se procedía previamente a hincar una camisa metálica mediante vibrador. La perforación siempre avanzaba por encima de la cota inferior de entibación. Normalmente, a medida que la perforación progresaba en los depósitos cuaternarios, ésta se paraba momentáneamente para hincar a mayor profundidad la camisa metálica (Foto 11). La potencia de este sistema y las características de los materiales que se perforaban, permitió aparentemente hincar la entibación de manera efectiva hasta alcanzar el substrato rocoso en la mayor parte de los pilotes, donde las paredes de excavación ya parecían estables. La elección de entibación metálica frente a la recirculación de lodos, tuvo en cuenta los posibles riesgos de afectar medioambientalmente la ría.
La perforación de los pilotes se realizó con una hélice convencional para excavación en suelos (Foto 9), una hélice reforzada con dientes de widia en los tramos en roca (Foto 8), un carotiere (Foto 7) para los tramos de roca más resistente, y un cazo de limpieza para el fondo (Foto 10).
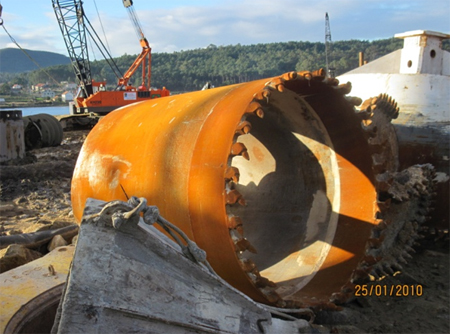
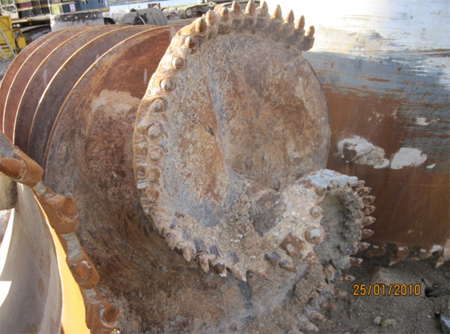
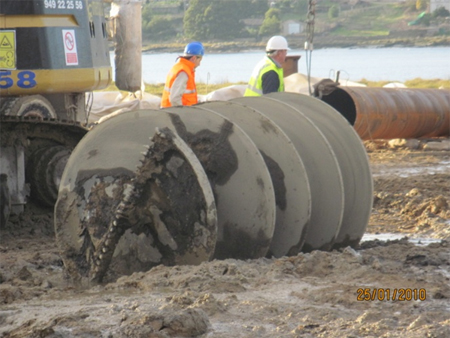
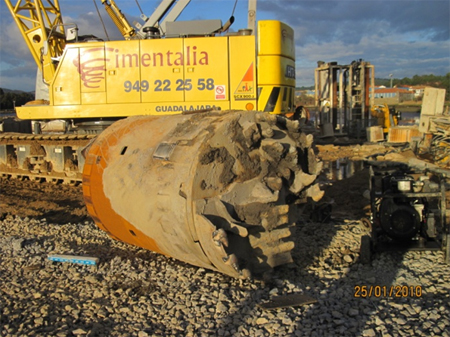
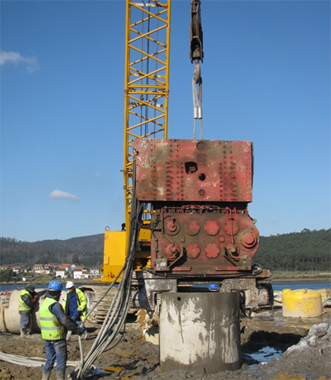
Durante la fase de perforación y hormigonado de los pilotes, se realizó un control de ejecución intenso, siendo ejemplo de trabajo en equipo y colaboración del personal de la Constructora y de la Asistencia Técnica junto con la Dirección de Obra. Más adelante en este artículo se describe en detalle los aspectos que se revisaron de manera conjunta.
Una vez finalizada la perforación de cada pilote, se procedía a limpiar el fondo con el cazo, mientras se terminaba de montar la armadura y se programaba el hormigonado. La armadura se acopiaba en el tajo parcialmente montada, en base a la información de partida, pero no era hasta la determinación de la cota de inicio de empotramiento cuando se podía finalizar el montaje de la misma con la longitud adecuada (Foto 13), incluso todos los elementos auxiliares (fundamentalmente, cuatro tubos de acero negro de 4’’ colocados en sentido longitudinal del pilote para la posterior realización de ensayos de integridad del pilote, separadores para garantizar el recubrimiento necesario de la armadura y elementos para descabezado).
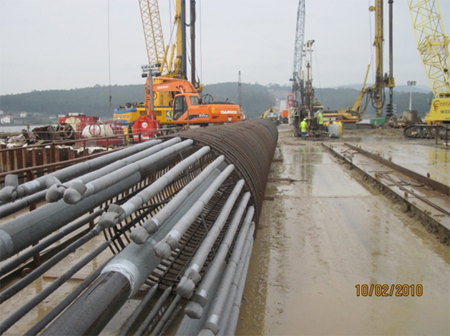
Por condiciones de ejecución, se optó por ejecutar los pilotes desde la cota superior de la plataforma de trabajo. Aunque eso supuso excesos de longitud de pilote de unos 2 m que posteriormente habría que eliminar, se consideró que este descabezado permitiría realizar además un saneo recomendable del hormigón. Para facilitar estas labores, se protegieron los extremos superiores de las barras longitudinales con vainas de material sintético (Foto 12), que evitaban que la armadura y el hormigón entraran en contacto.
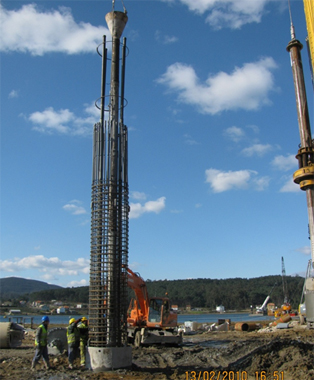
Una vez que la limpieza con el cazo se consideraba finalizada (ya no se extraía material), se procedía a introducir la armadura junto con el tubo de hormigonado. Para evitar que la armadura se descolocara durante el proceso de hormigonado, se anclaba a la camisa (Foto14).
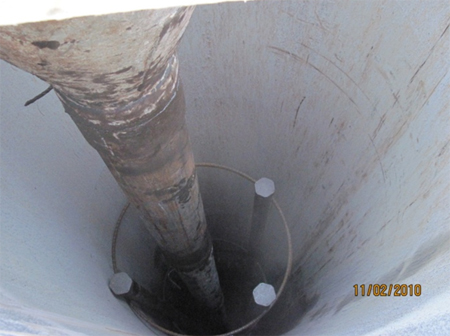
El proceso de hormigonado era continuo, mediante camiones hormigoneras sucesivos. Se vertía directamente al tubo tipo Tremi (Foto 15), que iba en retirada a medida que progresaba el hormigonado. El tiempo de espera entre camiones se controlaba escrupulosamente, si bien normalmente el único tiempo de parada era el necesario para cambiar el camión hormigonera.
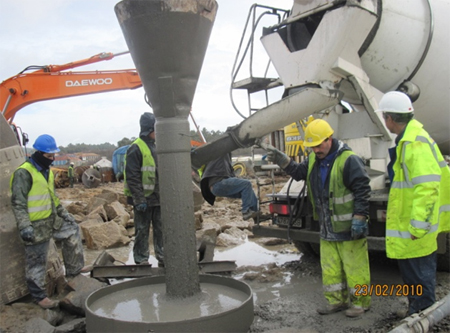
Una vez que se tenía parcialmente hormigonado el pilote, se paraba momentáneamente para retirar tramos de entubación (Foto 16), garantizando en todo caso que la cota inferior de la entubación estaba unos 2 diámetros por debajo de la cota superior del hormigón fresco.
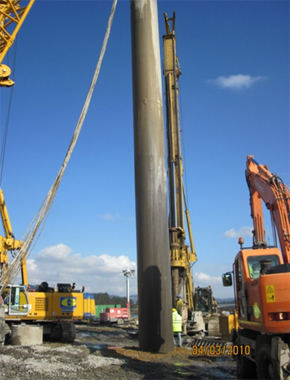
Una vez finalizado el hormigonado y retirada la entubación, se procedía a tapar la cabeza del pilote mediante una cama de zahorra y se vallaba la zona. De esta manera, se evitaban accidentes y se recuperaba la zona para trabajo una vez pasaran 24 horas de fraguado del pilote ya hormigonado.
Control de calidad y de ejecución
En la segunda parte de este artículo (se publicará en el número 240 de Ingeopres) se presenta una valoración de los principales riesgos geológicos, geotécnicos y de ejecución, que parecen afectar las cimentaciones por pilotes. Se describen las medidas paliativas adoptadas en este caso y se exponen consideraciones acerca del concepto del Tope Estructural basadas en esta experiencia de obra.
Como resumen, en los pilotes de las pilas P5 y P6 del viaducto del Ulla, se consideró suficiente el control realizado en obra, la ejecución de las diagrafías en el 100% de los pilotes, y el testeo mediante reperforación bajo punta (entre un 30% y un 60%). En base a estos datos, se decidió tratar las irregularidades detectadas en los fustes, realizar la limpieza e inyección sistemática en la punta de todos los pilotes, y la ejecución de columnas de jet-grouting en las puntas de los pilotes de la pila P6.
Conclusiones
Las cimentaciones del vano central de 240m de luz del viaducto sobre el río Ulla en la ría de Arousa se ejecutaron mediante pilotes empotrados en el macizo rocoso granítico subyacente bajo depósitos aluviales. Al situarse estos apoyos en la zona de inundación de la ría, las condiciones de ejecución dificultaron las labores de limpieza del fondo, y ante las exigencias del diseño propuesto, se consideró adecuado realizar labores adicionales orientadas a intentar garantizar la respuesta estructural y geotécnica.
Gracias a la colaboración constante y permanente de las diferentes partes implicadas, se realizó un control de ejecución intenso que permitió identificar eventualidades, que pudieron ser reforzadas con técnicas específicas. Se destaca el esfuerzo en consensuar la cota de inicio del empotramiento, y la ejecución de columnas de de jet- grouting como medida de refuerzo en la punta de algunos de los pilotes.
Agradecimientos
Rubén Estévez Sánchez (Dirección de Obra del Ministerio de Fomento - Adif), Luis Conde Martínez (Jefe de Unidad de la Asistencia Técnica de Typsa).
I Página web de información del Adif (Ministerio de Fomento), que tiene la siguiente dirección URL:
http://www.adif.es/es_ES/infraestructuras/lineas_de_alta_velocidad/eje_atlantico.shtml
II Artículo “El viaducto sobre el río Ulla en el Eje Atlántico de Alta Velocidad: una celosía mixta de 240 m de luz”, redactado por Ideam (Francisco Millanes, Luis Matute Rubio, Miguel Ortega Cornejo, Carlos Gordo Monsó) para el V Congreso de ACHE.
III Artículo “Cimentaciones singulares del Viaducto sobre el río Ulla en la ría de Arosa, eje Atlántico de Alta Velocidad”, publicado en el 9º Simposio Nacional de Ingeniería Geotécnica sobre Cimentaciones y Excavaciones Profundas, por Ignacio Muñoz Sota, Germán Burbano Juana, y Rubén A, Estévez Sánchez (Sevilla, 2012).
IV Informe Específico “Longitud de empotramiento de pilotes en roca”, entregado a la Dirección de Obra por la Asistencia Técnica (Typsa) en marzo de 2009.
V Proyecto de Construcción del Eje Atlántico de Alta Velocidad, tramo: Viaducto del Río Ulla (A Coruña – Pontevedra), plataforma, redactado por Ideam-Euroestudios en enero de 2008.
VI Informe Específico “Cimentación de las pilas 5, 6 y 7. Tipología, profundidad, ejecución y alternativas”, redactado por la UTE Río Ulla (Profesor Francisco Román) en marzo de 2009.
VII Documento de obra “Criterio de ejecución de pilotes”, entregado a la Dirección de Obra por la UTE Río Ulla (Dragados – Tecsa) con fecha de enero de 2010.
VIII Estudio “Revisión del Cálculo de la Longitud de empotramiento de los pilotes en roca a partir de su control de ejecución”, editado por el Servicio de Geotecnia de DRAGADOS en febrero de 2010.