Alstom adquiere tres fresadoras Correa para su planta de República Checa
La multinacional francesa Alstom ha adquirido tres fresadoras de pórtico Correa para su planta de Ceská Lípa, en la República Checa. Esta planta produce piezas para trenes de cercanías, tranvías, metro y otros vehículos ferroviarios; con casi 1.300 empleados, es uno de los mayores empleadores de la región.
El proyecto con un valor de varios millones de euros consta de una fresadora de puente fijo FOX-40 y dos fresadoras tipo gantry FOX M-80 y se ha realizado de manera conjunta con TGS, distribuidor de Correa en la República Checa.
La máquina FOX-40 cuenta con unos recorridos de X 4.000 mm, Y 3.000 mm, Z 1.000 mm y un cabezal universal automático UAD. Las dos gantrys FOX M-80 están equipadas con tres cabezales cada una, a parte de otros cabezales accesorios elegidos específicamente para el proceso particular del usuario final, y disponen de unos recorridos de 8.000 mm en el eje X, 4.250 mm en Y y 1.500 mm en el eje Z. El proceso de fabricación de las piezas era un aspecto crítico que con las nuevas máquinas Correa se ha conseguido optimizar, reduciendo los tiempos en torno a un 20% en las diferentes piezas que mecaniza Alstom.
El acto realizado con motivo de la puesta en marcha de las tres máquinas, el día 26 de abril, contó con la presencia de José Nicolás-Correa, presidente del Grupo Correa y José Manuel Revuelta, consejero jefe de la Oficina Económica y Comercial de la Embajada de España en Praga.
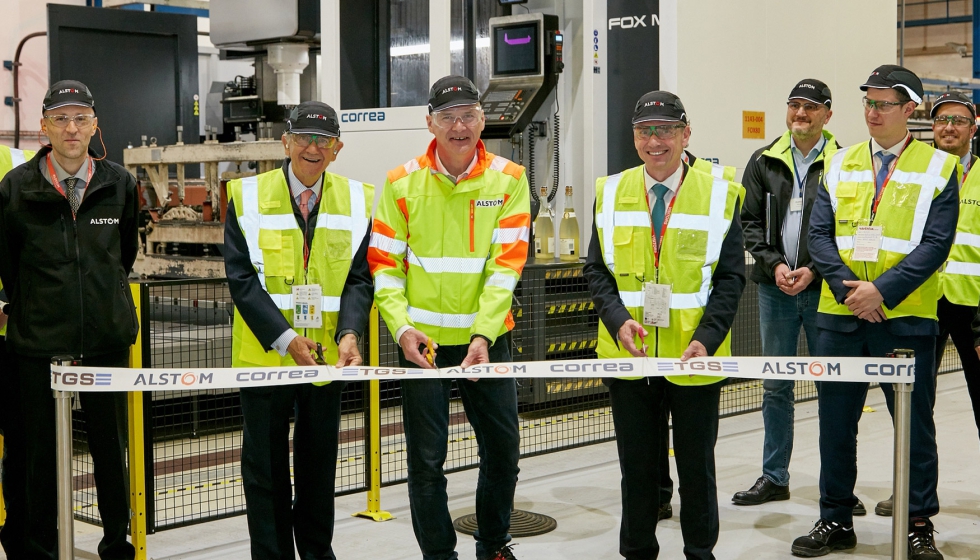
Colaboración estrecha con TGS
La empresa checa TGS es el proveedor local de Alstom y estaba en contacto permanente con su taller de mecanizado para cubrir sus necesidades tanto a nivel de herramientas de corte como de soporte técnico. En este proyecto era necesario conocer a fondo el proceso de mecanizado de las piezas para ser capaces de optimizarlo y crear una solución completamente adaptada a la aplicación del cliente. TGS mantuvo numerosas reuniones con el departamento de mecanizado de Alstom para realizar un estudio de tiempos y un diseño del proceso que mejoraba los tiempos de mecanizado que tenían con sus medios productivos.
“Hemos tratado el diseño y la solución tecnológica del proceso para que el comportamiento de las máquinas, los programas y todos los procesos de servicio sean seguros y no requieran intervenciones manuales de los técnicos. La continuidad de la producción es muy importante para los procesos posteriores y la logística de un producto tan grande como el chasis del tren”, dijo Pavel Diviš, director de TGS. Según él, las máquinas españolas están entre las mejores del mercado y TGS representa en exclusiva a este fabricante en la República Checa.
Cabezales robustos
La planta de Alstom Česká Lípa se dedica a la fabricación de bogies, piezas de mecano-soldado, de gran tamaño y formas complejas con salientes y orejas, lo que complica el proceso de mecanizado. Esta tipología de pieza es muy propensa a vibrar durante las operaciones de mecanizado. Estas vibraciones ocasionan un desgaste más rápido en los cabezales, entre otros inconvenientes y para Alstom era bastante habitual tener que realizar intervenciones en los cabezales de las máquinas que tenían de otros fabricantes. Estas paradas de máquina eran un factor crítico para Alstom ya que su producción está programada para los 7 días de la semana las 24 horas al día.
Para este tipo de operaciones, la tecnología de cabezales Correa se adaptaba muy bien ya que son cabezales muy rígidos, estables y 100% mecánicos, sin elementos delicados en su interior que puedan dañarse fácilmente durante operaciones de mecanizado exigentes. Entre otros aspectos, el eje principal del cabezal está soportado mediante 6 rodamientos para poder dar buenas prestaciones en este tipo de aplicaciones.
Para este proyecto se ha fabricado un cabezal específico para la aplicación del cliente. El cabezal Correa acodado estándar era de ISO 50 y no permitía acceder a algunas partes de la pieza. Sin embargo, los cabezales acodados comerciales tampoco eran una solución aceptable, ya fuese por falta de rigidez o porque las dimensiones de éstos no permitían mecanizar en las zonas de difícil acceso. La solución de Correa ha sido un cabezal acodado de ISO 40 directamente fijado en el carnero aportando una mayor rigidez y compatible con el sistema de cambio automático de cabezales.
Asimismo, se han incorporado en la máquina cabezales acodados comerciales para operaciones puntuales menos demandantes. El departamento de Ingeniería de Nicolás Correa ha preparado esta solución de tal manera que el acoplamiento de estos cabezales comerciales sea totalmente automático (adaptación en el sistema de cambio de herramientas y diseño de un ‘stop-block’ o bloqueo para la fijación de este cabezal más apropiado que los elementos comerciales estándar).
Soluciones a medida
Como todas las máquinas de Correa, se han adaptado al taller del cliente y a las exigencias de su trabajo; para garantizar una disponibilidad de máquina elevada se ha incluido un cabezal de repuesto para evitar paradas de máquina y condiciones especiales de servicio con un tiempo de respuesta breve.
“Alstom necesitaba las máquinas en un plazo de entrega breve y los plazos que se acordaron eran muy ajustados. Pese a las dificultades de los últimos meses Correa ha conseguido fabricar e instalar las máquinas respetando dichos plazos de entrega y haciendo frente a la crisis de materias primas, plazos de entrega de elementos comerciales mucho más largos, incremento de precios etc.” explica Raúl de la Peña, Área Manager de Nicolás Correa en República Checa.
En el pliego de condiciones de Alstom se incluían planos de varias piezas para la elaboración de estudios de tiempos, para los que debían garantizar una mejora en torno al 20% de los tiempos de producción de cada pieza. Hasta ese momento, los chasis de Česká Lípa se mecanizaban en varias máquinas.El requisito del nuevo proyecto era utilizar una sola máquina, mejorando notablemente los tiempos muertos entre máquinas y automatizando el proceso al máximo minimizando la mano de obra necesaria. TGS dispone de una fresadora FOX en sus instalaciones y los propios ingenieros de Alstom junto con los de TGS realizaron pruebas en esta máquina perfeccionando los proyectos de CAM, revisando operación por operación y detectando posibles mejoras. Por último, cabe destacar que para optimizar el proceso de mecanizado de los bogies se han diseñado utillajes especiales que han sido fabricados en las instalaciones de TGS utilizando también la fresadora FOX de marca Correa.
Con las nuevas máquinas Correa se han conseguido optimizar los procesos de fabricación, reduciendo los tiempos en torno a un 20% aproximadamente