Solución de CNC B&R: el corazón y el cerebro de la máquina
8 de octubre de 2010
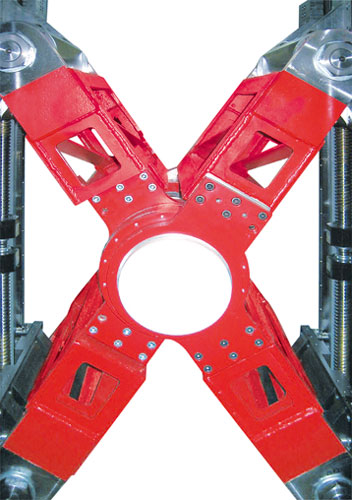
Los científicos son personas que miran más allá de las respuestas habituales y se hacen preguntas al respecto. Preguntas como “¿Por qué las máquinas-herramienta deben construirse siempre de la misma forma? ¿Solamente porque se ha hecho así durante décadas?”. Esta pregunta fue formulada por el equipo liderado el profesor Freidrich Bleicher en el laboratorio industrial del Instituto de Tecnología Industrial y Tecnología Láser de Alta Potencia de la Universidad de Tecnología de Viena. “El laboratorio resuelve problemas concretos a los que se enfrenta la industria mediante el enfoque científico”, explica el director de proyectos de mecatrónica del laboratorio Falko Puschitz. “Esto va desde la tecnología industrial y la producción automatizada hasta el dimensionado, la construcción y la implementación de la máquina-herramienta”.
Los clientes se encuentran en todas las ramas de la industria en las cuales los métodos de desarrollo convencionales no son capaces de solucionar los nuevos problemas que necesitan de un enfoque científico. Un ejemplo es un mecanismo usado cuando se perforan agujeros de gran profundidad en materiales muy duros, que permite la detección y corrección del movimiento lateral del taladro.
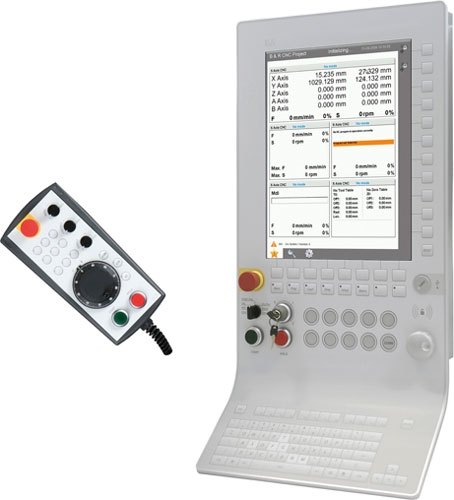
Nuevos enfoques para la fabricación de maquinaria
La búsqueda de nuevos enfoques para la fabricación de maquinaria nos conduce directamente a la X-Cut, una máquina cuyo eje principal tiene libertad completa de movimiento sobre dos ejes para posicionarse en el espacio disponible. Un tercer y un potencial cuarto eje pueden ser añadidos moviendo el cabezal de la herramienta lateralmente respecto el eje principal o bien moviendo la pieza a mecanizar.
Su nombre, X, proviene del alto nivel de la cinemática paralela, con dos grados de paralelismo para el posicionamiento del eje principal. El eje principal se encuentra en el vértice de un triángulo formado por dos brazos, cuyos extremos se mueven paralelamente sobre una guía común en dirección opuesta, moviendo de esta forma el eje principal en las direcciones x e y. Cuando este triángulo se estira hasta el límite (formando un ángulo o muy obtuso o muy agudo), los brazos llegan a ser casi paralelos —lo que los científicos lo llaman una singularidad— y la rigidez en una dirección se pierde. Por esta razón se usa un segundo par de brazos para convertir el triángulo en una X (véase la imagen). De esta forma, en cualquier punto la debilidad de una pareja de brazos es compensada por la fuerza de la pareja restante.
Esta construcción tiene cuatro ventajas sobre el enfoque convencional: por un lado, gracias a las guías verticales por las cuales se mueven los brazos se consigue que la maquina ocupe menos espacio en el suelo de la zona de producción. Por otro lado, la propia construcción de la máquina le proporciona una estabilidad mucho mayor en la dirección Z de la ofrecida por las soluciones convencionales. Tercero, la estabilidad en los ejes X e Y puede ser directamente controlada moviendo los dos triángulos de manera independientemente y ajustarlos para conseguir una rigidez extrema. Finalmente, comparado con máquinas basadas en una estructura en ejes cartesianos, la cinemática de traslaciones del X-Cut permite aceleraciones próximas a los 2G gracias a la baja cantidad de masa a mover, lo cual además incrementa la eficiencia energética.
Ante la pregunta de porqué algo similar no ha sido ya inventado hace tiempo, Falko Puschitz nos ofrece una respuesta sencilla: “El Instituto de Tecnología Industrial y Tecnología Láser de Alta Potencia de Viena ha estado trabajando durante años en la concepción de nuevas máquinas-herramienta, incluyendo la prueba y el desarrollo de cinemáticas especiales como la cinemática paralela. El Quickstep y el Quickstep Neon son dos estructuras trípodes que ya han sido presentadas en la feria EMO junto con Krause & Mauser Machine Tools. La sofisticada estructura paralela del X-Cut hace uso de la extensa experiencia del instituto para situarse un paso por delante en relación con las estructuras convencionales”.
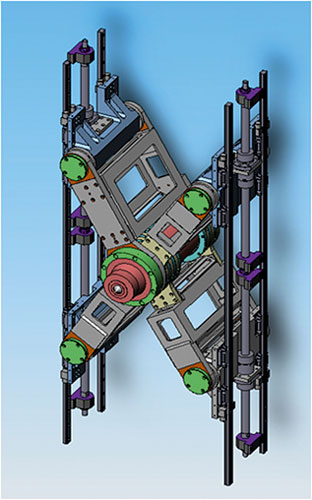
Control de la máquina como una tarea matemática
El control de la cinemática paralela del X-Cut es de esta forma una tarea que va más allá de la programación secuencial de un movimiento individual por pasos. “Más que programar los movimientos de los ejes lineales, es mejor usar el modelo matemático de la cinemática inversa, y hacer uso de éste también para todas las correcciones necesarias” —explica Falko Puschitz—. “Esta es una de las razones por las cuales hemos decidido usar la tecnología de automatización que ofrece B&R, ya que el entorno de desarrollo de B&R, Automation Studio, permite al programador desarrollar estas cinemáticas inversas”. Esto parece trivial, pero realmente no lo es: con la mayoría de los fabricantes de hardware de control tradicionales, estas funciones deben ser programadas en el sistema operativo. Así, los algoritmos generalmente están ya programados en el hardware por el fabricante. “Esto hubiera sido inaceptable para nosotros” —dice Puschitz— “porque no solamente hubiera retrasado cada paso del proyecto, sino que además hubiese dado como resultado que nuestro conocimiento habría pasado al fabricante de los controladores”.
Ya que la producción de complejos componentes de forma individual de la máquina es caro y la financiación pública es limitada, el equipo del Laboratorio de Tecnología de Producción de la Universidad Tecnológica de Viena, realizó simulaciones previas a la construcción del prototipo. Esto se aplica a la construcción de maquinaria, donde es necesario probar la distribución de fuerzas bajo todos los posibles escenarios de cargas usando el análisis de elementos finitos. También se aplica al control en lazo abierto y lazo cerrado, que se prueban usando Matlab/Simulink antes de programar la máquina. La nueva herramienta de B&R Automation Studio Client for Simulink proporciona la posibilidad de generar el código de un programa directamente a partir del modelo de simulación y transferirlo luego al controlador. “Esto nos ahorra tiempo e incrementa la seguridad” reconoce Puschitz. “Cuando hay cambios, podemos tener el programa final en la máquina pocos minutos después de haber llevado a cabo una simulación satisfactoria. Y lo hacemos sin la potencial introducción de nuevos errores en el resultado de la simulación durante la programación”.
Tecnología de automatización B&R
“Otra motivación de nuestra decisión para trabajar con B&R fue la solución de una automatización completamente integrada", informa Puschitz. “Desde la CPU hasta los motores, todo el control es común y los distintos equipos trabajan perfectamente integrados. No nos tenemos que preocupar por la comunicación interna entre componentes, y además solo tenemos una persona de contacto”.
La potencia de cálculo y de gestión es proporcionada directamente por un APC 620. Gracias a la ausencia de ventiladores y de disco duro, se trata de un PC industrial robusto y muy flexible que se conecta a los módulos X20 mediante el rápido bus de Poerlink. Los módulos de X20 son necesarios para controlar la máquina (encender la máquina, cambiar herramientas, activar el motor del eje principal, etc.). La máquina aun no tiene ningún tipo de equipamiento de protección montado, pero cuando llegue el momento, éste puede ser integrado usando los componentes Safe I/O de las series X20 de B&R, que se programan en el mismo entorno de desarrollo usando SafeDesigner.
“La red interna de Powerlink ha resultado ser muy eficaz en muchos sentidos” nos cuenta Puschlitz. “No solamente requiere de muy poco cableado y de poca cantidad de espacio en el armario eléctrico, sino que además puede manejar una gran cantidad de datos, necesarios para obtener una dinámica elevada y una alta precisión de la cinemática paralela, así como para la gestión del diagnóstico y del estado del posicionamiento, que se envían por la misma red”.
También conectado a la CPU a través de Powerlink se encuentran los servoaccionamientos ACOPOSmulti. Potentes y compactos, estos servoaccionamientos proporcionan máxima potencia en un mínimo espacio. Además están equipados con inteligencia propia, lo cual les proporciona una extensa lista de posibilidades de diagnóstico y funciones de seguridad sin ningún tipo de conexión externa.
La solución de automatización está completamente integrada incluso en los motores. Los cinco motores trifásicos síncronos de B&R de la familia 8LS, con un par nominal de 31,6 Nm y un par de bloqueo de 36,4 Nm, están diseñados para aplicaciones que requieren de unas excelentes características dinámicas y de alta precisión en el posicionamiento, todo ello en un tamaño compacto y un peso reducido.
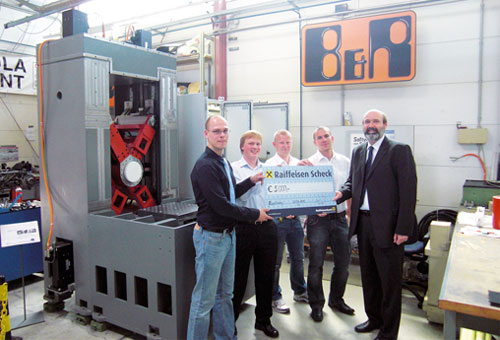
Visión de futuro
En un principio durante su desarrollo, la máquina se controló con un Automation Panel 900 de B&R, pero hace unos meses B&R proporcionó a la Universidad una versión preliminar de panel CNC con un mando de operación desarrollado para los centros de mecanizado. Equipado con funciones de operación diseñadas específicamente para el proceso de CNC, los elementos de control están personalizados para el proyecto de ejemplo de CNC, pero también son apropiados para la aplicación de visualización programada por el cliente.
Esta combinación ergonómica de panel de operador equipados con numerosos selectores de funciones y botones diseñados para operar en entornos desfavorables —incluso por trabajadores que lleven guantes— ya está disponible en el mercado tras haber sido probada con éxito en máquina real, como en el caso de la X-Cut.
Un centro de mecanizado no consiste necesariamente en ejes encapsulados dentro de un sistema de coordenadas cartesiano. La Universidad Tecnológica de Viena proporciona un nuevo enfoque que ha dado como resultado el desarrollo de la X-Cut, una máquina de procesado de tres ejes de altas prestaciones dinámicas y que presume de una estabilidad excepcional, una alta eficiencia energética y unas dimensiones compactas. Desde la CPU hasta los motores, el sofisticado concepto de control ha sido implementado usando la tecnología de automatización de B&R que demuestra de este modo ser apropiada para tareas poco corrientes.
Universidad Tecnológica de Viena
La Universidad Tecnológica de Viena —T.U. Viena— es una de las universidades técnicas con mayor éxito de Europa. Con más de 20.000 estudiantes y cerca de 2.000 investigadores, es la institución con mayor investigación técnica y ciencia aplicada y educativa de Austria.
El Instituto de Tecnología Industrial de la Universidad Tecnológica de Viena cubre un amplio rango de tecnología de producción y máquina-herramienta. En relación con el desarrollo de procesos y la relacionada ingeniería relacionada con las máquinas, el instituto es considerado como uno de más importantes en la investigación de tecnología de producción.