Ingeniería de procesos optimizada mediante Digital Twin
A medida que avanza la Industria 4.0, la visión digital gana cada vez más contorno y, sobre todo, relevancia práctica para la tecnología de fabricación CNC. Entre los desarrollos definitorios se encuentran el gemelo digital y las herramientas de inteligencia artificial y analítica avanzada. DMG MORI siempre ha marcado pautas en ambos sectores. En el curso de la Transformación Digital (DX) —uno de los pilares de apoyo en la Transformación del Mecanizado (MX) junto con la Integración de Procesos, la Automatización y la Transformación Verde (GX)— el desarrollo sigue avanzando.
La combinación de redes de extremo a extremo, gemelos digitales y herramientas de IA, así como sus interacciones, abren un amplio abanico de perspectivas para las empresas de fabricación. Los valores añadidos van desde máquinas-herramienta más eficientes hasta la mejora de la estabilidad de los procesos y el aumento de la calidad de los productos. También se fomenta la innovación y una producción más sostenible desde el punto de vista medioambiental.
DMG MORI demuestra cómo estas convergencias pueden dar forma al futuro de la fabricación con dos nuevos desarrollos actuales de su espectro de servicios digitales: tanto Digital Engineering como Digital Twin Test Cuts permiten la optimización de procesos incluso antes del inicio real de la producción.
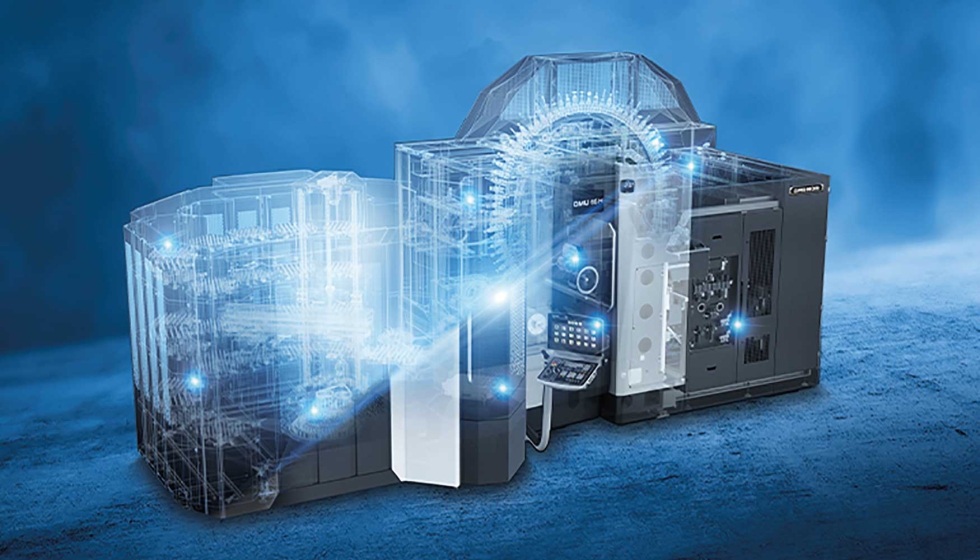
Ingeniería digital: aceleración de la producción en un 40
La ingeniería digital comienza antes del inicio real de la producción. Todo el sistema de fabricación se simula digitalmente, incluidos el programa y la automatización. Esto elimina la necesidad de realizar un rodaje de la máquina que requiere mucho tiempo y recursos. Incluso los nuevos procesos pueden configurarse digitalmente mientras la máquina sigue funcionando. La formación de los empleados también puede realizarse digitalmente. Daniel Niederwestberg, director de Digital Twin en DMG MORI, afirma que “el aumento de la producción puede acelerarse hasta en un 40%”, citando uno de los valores añadidos. Al mismo tiempo, los tiempos de preparación en la máquina real se reducen hasta un 80%. Además, la inspección digital completa y la optimización de la máquina y del proceso garantizan un mecanizado 100% libre de colisiones. “En la totalidad de sus funciones y capacidades, la Ingeniería Digital ofrece a los usuarios procesos más rápidos y, gracias a la utilización óptima de los datos y los nuevos conocimientos, un aumento de la productividad, así como una mejora de la eficiencia”, añade Niederwestberg.
Digital Twin Test Cuts evita el mecanizado de prueba
Incluso antes de adquirir una máquina, se plantea la cuestión de qué solución de fabricación es la óptima para las piezas de trabajo, cada vez más complejas y diversas. Hasta la fecha, parte del proceso de toma de decisiones ha consistido en realizar mecanizados de prueba en las instalaciones del fabricante. Su objetivo es definir los requisitos en términos de precisión y tiempo de producción y reducir el riesgo de la inversión. Daniel Niederwestberg añade: “Por muy probado que esté este enfoque, cuesta tiempo, dinero y recursos, sobre todo porque a menudo es difícil conseguir las máquinas, herramientas, útiles y materiales adecuados para un mecanizado de prueba representativo en poco tiempo”. Aquí es precisamente donde interviene el nuevo Digital Twin Test Cut de DMG MORI.

La principal ventaja del Digital Twin Test Cut Service es el importante ahorro de tiempo. Normalmente, los resultados de la simulación están disponibles en dos días laborables. Con los métodos convencionales, a veces se tardaban varias semanas. Además, los cortes de prueba digitales son respetuosos con el medio ambiente, ya que no se utilizan herramientas, materiales ni refrigerantes reales y el consumo de energía es mucho menor que en el mecanizado real.