Maquinaria de inyección de más de 400 T de fuerza de cierre
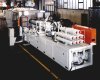
El moldeo por inyección es la técnica más conocida y utilizada en la transformación de plásticos. En esencia, la relación entre los principales parámetros de moldeo es común a todas las máquinas horizontales, cualquiera que sea su fuerza de cierre.
Sin embargo, al pasar la frontera de los 4.000 kN se plantea una serie de alternativas constructivas que intenta aumentar el volumen del producto con la misma fuerza de cierre o reducir el espacio ocupado por la máquina con distintos sistemas de carrera del plato portamoldes móvil.
Predominio de cierre por rodillera
En la mayoría de las máquinas actuales continúa utilizándose el sistema de cierre por rodillera, comandado hidráulicamente, que presenta la ventaja de proporcionar una velocidad lenta y gran entrega de potencia en el momento del cierre y una carrera rápida una vez se ha efectuado la apertura.
De todas maneras, el tamaño de los moldes utilizados y la separación necesaria para el desmoldeo hacen que este sistema precise de una gran ocupación de espacio longitudinal en la zona posterior de la prensa.
Además, en las grandes máquinas, los sistemas de rodilleras ya no pueden ser simples, sino que se emplean dobles e incluso triples, siendo estos últimos los que proporcionan una carrera mayor para el mismo espacio ocupado.
La firma italiana BMB dispone del sistema especial kW de rodillera en el que el desplazamiento del miembro más largo se hace por el exterior, a la inversa del sistema habitual, con lo que se consigue una mayor velocidad de carrera y una presión de cierre más equilibrada en los cuatro extremos del plato móvil.
Figura 1 El sistema de placas de cierre sandwich de Krauss Maffei, que se deslizan sobre patines, con sistema expulsor incorporado asegura un reparto homogéneo de la presión de cierre.
Se han desarrollado diversas alternativas que reducen el espacio necesario, aunque requieren, en unos casos, un incremento de la potencia hidráulica y, en otro, una reducción de la presión de inyección. Entre los primeros, se usa un sistema de columnas que atraviesan el plato fijo y que se bloquean mecánicamente detrás de éste al final de la carrera del molde, aplicándoseles entonces presión hidráulica mediante cuatro cilindros que actúan desde estas columnas sobre el plato móvil. El recorrido de apertura y cierre del molde se efectúa mediante un par de cilindros auxiliares de carrera larga.
Figura 2 Las cuatro barras solidarias a la placa portamoldes movil tienen unos rebajes en sus extremos sobre los que actúan los sistemas de enclavamiento.
Figura 3 Las cuatro barras solidarias a la placa portamoldes movil tienen unos rebajes en sus extremos sobre los que actúan los sistemas de enclavamiento.
Otra alternativa mecanohidráulica consiste en efectuar el recorrido mediante rodillera y la presión final de cierre con un gran cilindro hidráulico de recorrido muy corto que actúa sobre una oclusión central escamoteable del plato móvil.
Un sistema adicional, totalmente hidráulico, consiste en una combinación de movimientos de dos juegos de cilindros; los de gran recorrido son de baja potencia y se bloquean al final del mismo para que actúe un gran cilindro de recorrido corto que proporciona la fuerza de cierre.
Estas soluciones ponen de relieve el hecho de que el cierre mecánico por si mismo sólo actúa como posicionador de cierre del molde y soporta la reacción de la presión de inyección, pero no aporta presión de cierre. El uso de presión hidráulica sobre las cuatro columnas bloqueadas de cierre puede tener una especial utilidad cuando han de moldearse piezas que por su forma o reparto de espesores causen una reacción desequilibrada sobre uno de los extremos del molde.
Un sistema menos conocido es el desarrollado por Hettinga, en el que el que incluso el propio molde puede efectuar el cierre.
Reducción de la presión de inyección
En este último sistema se combinan velocidad y presión para obtener un llenado completo del molde; el perfil de la presión tiene la forma de una U invertida, con una baja presión inicial y final de inyección, como en las antiguas máquinas manuales de émbolo, incrementando la velocidad cuando conviene aumentar la temperatura del fundido.
Figura 4 Máquina de 2.500 T de fuerza de cierre de MIR, en fase de pruebas y con robot de extracci¢n de piezas, que será exhibida en funcionamiento en la Plast’97 de Milán.
Otra alternativa la propone MIR, que utiliza dos unidades de plastificación paralelas que inyectan simultáneamente por dos puntos distintos del molde, reduciendo la potencia necesaria en un 20% en comparación con la inyección multipunto efectuada con una sola unidad de plastificación. La razón para ello es que, en el último caso, la unidad de plastificación debe proporcionar potencia para llenar la totalidad del molde, cuando en el primero cada unidad debe llenar sólo la mitad.
La alternativa más común para aumentar la dimensión de las piezas que pueden fabricarse con una máquina dada es la co-inyección de gas, que puede reducir hasta cerca de un 50% la presión de cierre necesaria para un tamaño dado de molde/pieza.
Figura 5 Esta máquina Battenfeld, una de cuatro unidades en construcción, de 27.000 kN de fuerza de cierre, pesará 220 toneladas cuando esté lista para su embarque, es decir, el peso de un jet Jumbo.
Nuevamente debemos citar a Hettinga, al que hemos denominado a veces el maverick de los constructores de maquinaria, en cuyo proceso Helga no se inyecta el gas, sino que se incorpora al fundido un líquido que gasifica dentro del molde, permitiendo fabricar piezas de muy grandes dimensiones y embutisaje profundo a muy baja presión de inyección.
Subcontratación de piezas auxiliares
En general, los fabricantes de maquinaria de inyección no construyen las unidades de plastificación, que adquieren de constructores especializados. Las barras cilíndricas tratadas y los elementos hidráulicos pueden ser también de mercado, por lo que su actividad se centra en tres campos principales.
Por una parte, se presta una atención especial a la electrónica de mando del equipo, así como a los correspondientes periféricos, visualizadores y mandos, que deben funcionar en condiciones a menudo difíciles, por lo que muchos constructores diseñan y construyen sus propios sistemas a partir, actualmente en general, de procesadores 486 u otros de menor potencia pero más específicos para esta aplicación. Estos medios controlan no sólo los parámetros de inyección sino también la temperatura del circuito hidráulico y de los medios de refrigeración, e incluyen los medios de conexión y relación con los elementos periféricos y con controles remotos para la estadística de la producción.
Donde se utilizan medios más espectaculares es en la mecanización de los platos y rodilleras, dado el tamaño que pueden alcanzar los primeros. Recientemente hemos presenciado en Sandretto la mecanización de un plato de aproximadamente 3.030 x 3.030 x 600 mm, cuyo peso debe estar en el orden de las 42 toneladas y esto es sólo una pequeña parte de la máquina, que no es la mayor que produce la firma. Por tanto, la cimentación que ha de recibir equipos de este tamaño debe estar seriamente considerada.
Las máquinas-herramientas utilizadas para mecanizar estas grandes unidades suelen estar también construídas a medida del fabricante de las prensas de inyección y son equipos que en algunos casos permiten trabajar hasta con 120 herramientas distintas que se seleccionan y cambian automáticamente. En algunas empresas mayores se realiza también la mecanización y tratamiento térmico de los elementos cilíndricos.
Finalmente, el montaje y la puesta a punto en fábrica, que se reproducirá luego en casa del cliente, porque estas máquinas hacen necesario desmontarlas para el transporte, son las operaciones que consumen un mayor número de horas-hombre.
Amortización en grandes series
Los fabricantes de estas máquinas de inyección se encuentran en un momento delicado porque han precisado efectuar inversiones muy importantes en equipamiento, que incluyen almacenes robotizados y células de producción complejas, con sistemas de fabricación integrados informáticamente, para mantenerse al nivel de calidad que exigen sus clientes.
La amortización de estos sistemas sólo puede conseguirse manteniendo unos niveles determinados de producción y, en este momento, no es fácil alcanzarlos, amén de que la competencia consiguiente presiona sobre los precios de venta.
Los costes de transporte y montaje de estas máquinas son muy elevados, incluyendo los del material en bruto, que proviene de acererías como Thyssen o similares, que pueden estar alejadas, y que exigen con frecuencia un transporte especial.
Otra consecuencia de la competencia expuesta es la necesidad de presentar continuamente nuevas mejoras en sus productos, obligando a destinar medios importantes a la I+D y al mantenimiento de oficinas técnicas extensivas.
No es de extrañar la concentración de empresas que se está produciendo actualmente y que probablemente continuará, tanto en la formación de grupos como en acuerdos de colaboración entre empresas para efectuar economías de escala en fabricación y diseño de estos equipos y de sus componentes.