Potencial de mejora de la eficiencia a través del torneado en duro y rectificado
1 de febrero de 2011
Los beneficios de la combinación de torneado y rectificado incluyen el mecanizado completo, la mejora de la calidad y la gran flexibilidad. Estas tecnologías de combinación también pueden reducir el tiempo de ciclo. Si el mecanizado se lleva a cabo en una sola máquina, los tiempos de procesados, transporte y almacenaje intermedio se pueden reducir drásticamente. Además hay ventajas visibles en el tiempo y el esfuerzo de puesta a punto.
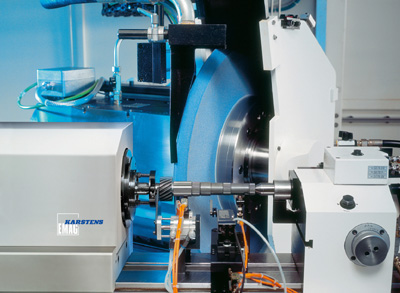
Puntos fuertes y débiles
Muchos procesos productivos hacen uso actualmente del rectificado cilíndrico externo convencional (Foto 1). Los métodos de rectificados convencionales están altamente optimizados, cosa que se transforma en un obstáculo a la hora de la innovar en este campo. Una característica clave del rectificado con CBN respecto al convencional es la drástica reducción del tiempo principal (Foto 2). Además de la reducción de este tiempo hay también una disminución significativa del de los tiempos secundarios conseguidos gracias a la gran vida de las herramientas CBN. Una desventaja del rectificado CBN es que el alto coste de las herramientas hacen de éste un procedimiento casi exclusivo para grandes series y producción en masa.
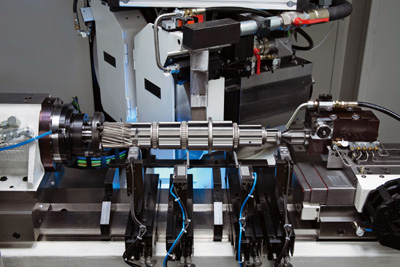
El rectificado cilíndrico externo de alta eficiencia de perfiles o descortezado es una variante del rectificado CBN en la cual muelas delgadas controladas generan el perfil de la pieza siguiendo un contorno controlado por control numérico. Este proceso, caracterizado por su alta flexibilidad, es ideal para el mecanizado cilíndrico externo de familias enteras de piezas. La desventaja radica en la inversión para el uso de tecnologías de alta velocidad y aceite de rectificado.
Un proceso que compite con el rectificado es el torneado en duro (Foto 3). El torneado en duro también se caracteriza por su alta flexibilidad. Este proceso es a menudo evaluado positivamente por el usuario ya se realiza en seco. La desventaja del torneado en seco sigue siendo inestabilidad del proceso: desintegraciones imprevisibles en la superficie de corte pueden conducir a fallas en el proceso. Por otra parte, la calidad de pieza alcanzable con máquinas estándar se limita al rango de IT6.
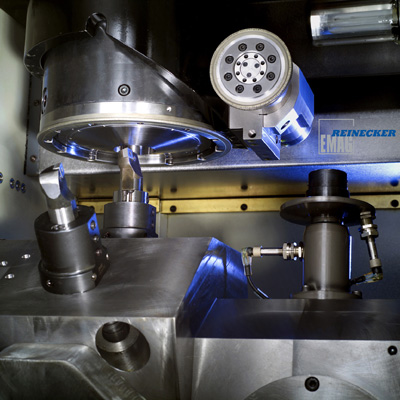
Soluciones óptimas con las máquinas combinadas
Esto deja claro que ningún proceso cumple con todas las necesidades del mecanizado en duro de precisión. Las máquinas combinadas ofrecen la posibilidad de un acercamiento al problema desde el punto de vista de la pieza y del requerimiento de mecanizado, para así llegar a una solución óptima para un caso en particular (Foto 4). La optimización puede hacerse en tres áreas importantes: productividad, calidad de pieza y costos de producción. Las máquinas combinadas, óptimamente equipadas, ofrecen la flexibilidad de poderse utilizar como una rectificadora o como un torno convencional.
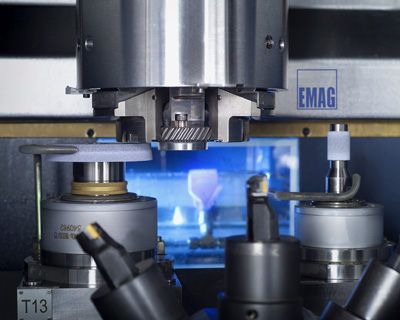
El cabezal de la pieza de trabajo está diseñado principalmente para los requisitos de torneado. La velocidad de rotación de éste es mucho más alta que en la mayoría de las rectificadoras convencionales. Cuando la máquina va a ser utilizada para el mecanizado en blando, hay mayores requerimientos en el torque máximo del cabezal que cuando se rectifica. Un requisito muy importante es la caída libre de la viruta. En el rectificado demanda más requerimientos. El mecanizado externo e interno, así como el mecanizado plano de talones, demandan diferentes requerimientos de velocidad, torque y rigidez. Para cubrir toda la gama de necesidades se hace necesario un cabezal modular.
Un requisito general para una máquina combinada es un control preciso de la temperatura. Por ejemplo, las operaciones de desbaste pueden producir temporal y localmente una gran carga térmica. El calor resultante se debe mantener bajo ciertos límites de manera que las siguientes operaciones de acabado no se vean afectadas. Por otro lado, para que el uso de máquinas combinadas sea una opción viable, la inversión económica debe ser mantenida dentro de un margen justificable cuando es comparado con la inversión en rectificadoras y tornos por separado.
Un excelente ejemplo de una máquina combinada para el mecanizado de piezas al plato es la plataforma VSC de Emag (Foto 5). El concepto de ‘pick-up’ responde perfectamente a las necesidades particulares de caída libre de viruta. La carga de la máquina a través de los ejes de la máquina es rápida y simple. Con la torreta de herramientas, el eje Y, el eje B y el cabezal de rectificado firmemente anclado en la bancada, la máquina cubre una gama muy amplia de aplicaciones.
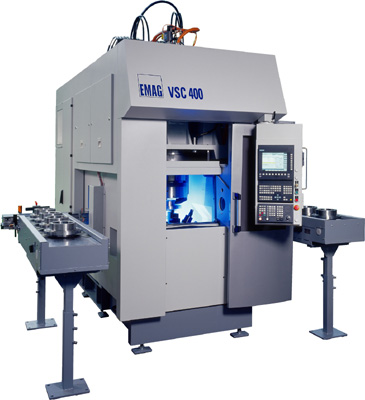
Un ejemplo de la combinación de procesos son las máquinas Emag de la serie VTC DS (Foto 6).Ya sea torneado, taladrado, fresado, rectificado o mecanizado de torneado/rectificado. La VTC integra todas las variantes de mecanizados de ejes. El modelo VTC 315 DS fue concebido para piezas de alta calidad que se producen en medias o grandes series, como por ejemplo, árboles de transmisión, ejes de rotor, ejes de bomba, ejes de motor o ejes de transmisión. Para cada uno de estos componentes hay una combinación de tecnologías apropiadas. Las piezas resistentes pueden mecanizarse mediante descortezado, mientras que piezas delgadas y frágiles hacen uso del rectificado. La máquina puede utilizarse tanto como una rectificadora, como un torno o como una máquina combinada (Foto 7).
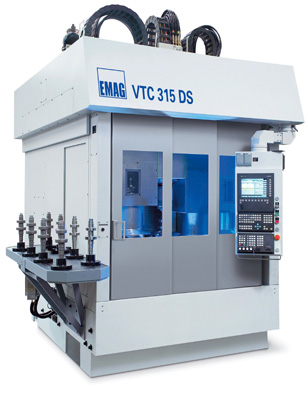
Un ejemplo típico del proceso de mecanizado de combinación son los engranajes. El torneado plano final de los escalones se realiza torneando en duro. Debido a los estándares de calidad de agujeros y conos, se desbastan y acaban con rectificado. Con este fin, la máquina está equipada con dos cabezales de rectificado. Un cabezal portamuelas es para el rectificado de los agujeros; el otro para el mecanizado externo. Debido a que sólo unas centésimas de milímetro deben ser rectificadas, las herramientas de rectificado están diseñadas para el acabado. Este proceso ha desplazado actualmente en gran medida el uso rectificadoras puras, y por lo tanto se debe entender esta tecnología como de vanguardia.
Otro ejemplo del uso apropiado de la tecnología de combinación es la producción de tuercas con surcos para recirculación de bolas, los que se utilizan en los husillos de bolas. En las tuercas se debe mecanizar la rosca interna, la cara frontal, el diámetro exterior y el escalón. Para el proceso presentado, la cara frontal, el diámetro exterior y la superficie plana son torneadas en duro y la pista para las bolas de la rosca interior fue rectificada. Para ello se puede utilizar una máquina de la serie VSC equipada adicionalmente con un eje B y un eje Y. El ángulo de avance de la rosca se controla con el eje B, muy preciso. El eje Y se utiliza para el posicionamiento en el mecanizado de pista de bolas. La máquina está equipada con dos cabezales de rectificado, que a su vez pueden equiparse con diferentes herramientas para operaciones tanto intermedias como de acabado. Un dispositivo de reavivado de muelas diamanta el perfil con un rodillo de diamante. La máquina es apropiada tanto para la utilización de muelas de CBN como convencionales. Una palpador de 2,5-D se utiliza para la determinación precisa del ángulo de la pieza amarrada y puede ser utilizada para el control ‘post-process’ de las superficies torneadas en duro.
La ventaja de este enfoque en contraste con la secuencia convencional de procesos es que todas las superficies determinantes de la calidad son mecanizadas en un solo amarre. Con ello se pueden evitar errores debidos al amarre, especialmente la alineación de la superficie plana, del diámetro externo y del eje central de la pista de las bolas.
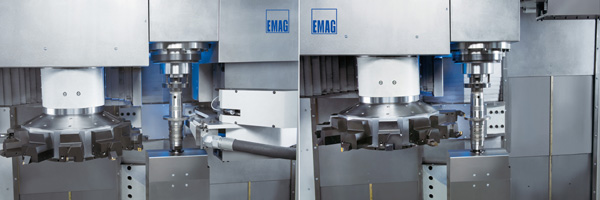
La tecnología y las máquinas en la práctica
En mecanizado de piezas al plato, la combinación de torneado y rectificado es tecnología punta. El potencial de racionalización de los procesos es todavía muy importante, ya que aún estamos lejos de implementar los procesos de combinación en todos los casos en los que se justificaría. En el futuro, además de los procesos de torneado y rectificado, también se fortalecerá la integración de procesos como el bruñido, el fresado y el escariado, ambos en duro.
Para el mecanizado de ejes ya se encuentran máquinas en el mercado que posibilitan la integración de procesos. El uso de estos sistemas todavía no está muy difundido como en las piezas al plato, ya que existen sistemas altamente productivos basados en procesos convencionales de rectificado, CBN y tecnologías modernas de torneado. Sin embargo, hay signos de que en el futuro se utilizarán las ventajas de los procesos combinados también para el mecanizado de ejes.
En general, se puede decir que los procesos combinados ya no se tratan de métodos exóticos, sino que de tecnologías y máquinas probadas. A través de una aplicación coherente de procesos de combinación y la integración futura de otros procesos de fabricación pueden alcanzarse mejoras considerables potencial de racionalización.