Tecnologías químicas y electroquímicas para el posprocesado de componentes de fabricación aditiva
La fabricación aditiva implica un grupo de tecnologías de fabricación de piezas poliméricas, cerámicas o metálicas, mediante la unión de materiales, capa sobre capa, a partir de datos de un modelo en 3D de la pieza. Las tecnologías de Fabricación Aditiva pueden dividirse en tecnologías de Deposición Directa y tecnologías de Lecho de Polvo, siendo estas últimas las que permiten fabricar estructuras rígidas y ligeras, con geometrías más complejas.
En el caso de las tecnologías de lecho de polvo, las fuentes de aplicación de energía para la unión de capas pueden ser la radiación láser, un haz de electrones o la temperatura, pero su característica principal es que la materia prima está en forma de polvo extendido en un lecho o cama. La fuente de energía es dirigida selectivamente y de forma programada sobre el lecho de polvo de tal manera que el material se funde y tras enfriarse se obtiene una capa sólida. Entonces, un mecanismo hace descender la superficie de trabajo y extiende otra capa de polvo virgen sobre la anterior. Este proceso se repite sucesivamente y así se forma, capa a capa, la pieza final.
Una vez fabricada la pieza, ésta requiere de una serie de etapas o posprocesos para dotarla de la geometría y propiedades requeridas para su uso. Según el informe anual de la empresa americana PostProcess Technologies sobre las tendencias de posprocesado en fabricación aditiva [2], las etapas de posprocesado consumen hasta un 25% del tiempo total de producción. El informe también indica que cuanto más se utilice la fabricación aditiva como método de producción a gran escala, mayores serán los desafíos asociados al postratamiento. Por este motivo, las soluciones automatizadas tienen una gran demanda. El documento también refleja que la mejora de la calidad de las piezas es cada vez más prioritaria para los usuarios de este tipo de componentes. Por todo ello, las etapas de posprocesado están adquiriendo un gran protagonismo en fabricación aditiva, debido a la necesidad de dotar a las piezas de una calidad óptima y reducir tiempo y costes globales del proceso. Estas etapas comprenden, entre otras, la retirada de soportes, la reducción de rugosidad y la protección superficial.
Estructuras soporte
Las estructuras soporte son necesarias cuando se fabrican piezas con ciertas tecnologías de fabricación aditiva como SLA, EBM, SLM, FDM. Estas estructuras tienen dos funciones principales; en primer lugar, evitar la deformación de la pieza uniendo la pieza de trabajo a la plataforma de construcción y, en segundo lugar, actuar como caminos para la disipación del calor generado durante el proceso. Una vez fabricada la pieza, estas estructuras deben ser eliminadas.
Rugosidad superficial
La alta rugosidad de las superficies de las piezas obtenidas por fabricación aditiva de lecho de polvo se debe al efecto escalera provocado por las sucesivas capas de material que conforman las piezas, a las partículas de polvo parcialmente fundidas en superficie y a las salpicaduras o defectos generados durante el proceso. La rugosidad depende de la tecnología de fabricación empleada (ver ejemplo en la figura 1), de los parámetros de fabricación aplicados y la orientación del componente durante la fabricación.
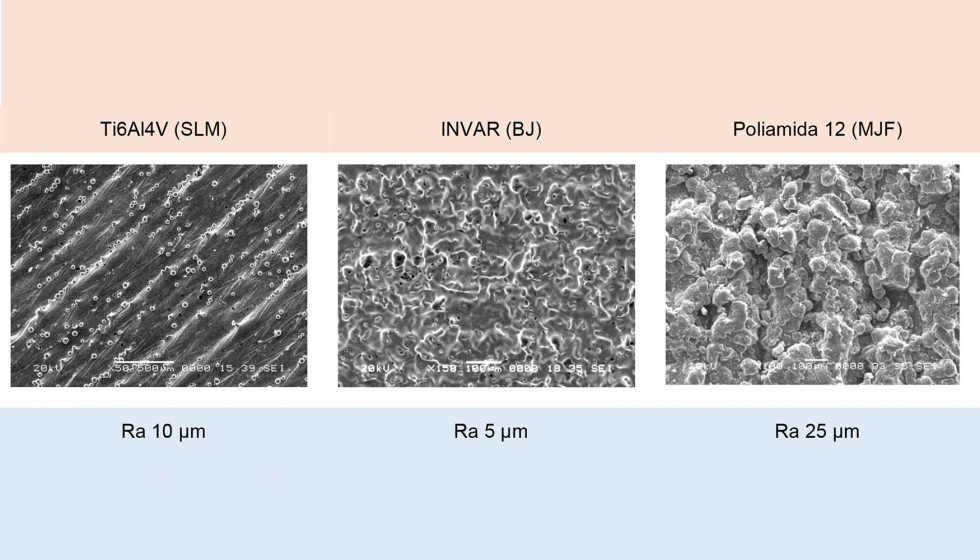
Además, la rugosidad puede variar también en función del lugar en el que esté colocada la pieza en la plataforma de fabricación. En la figura 3 se observa una plataforma de SLM con diferentes probetas planas de In718, y los valores de rugosidad medidos en las probetas coloreadas en amarillo. Como se puede comprobar, a pasar de que se han aplicado los mismos parámetros de fabricación, los valores de Ra de las diferentes probetas varían entre 12 y 19 µm.
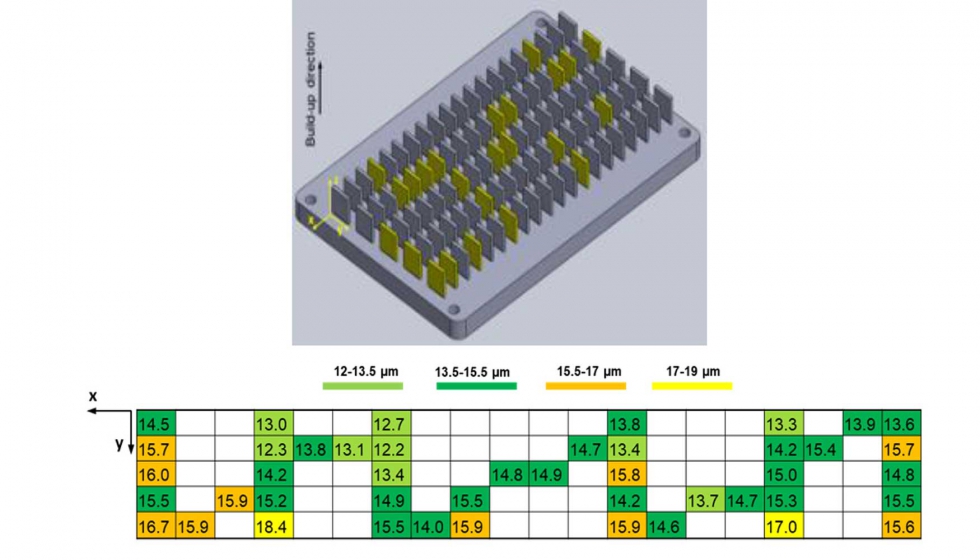
Teniendo en cuenta estas variaciones en la rugosidad inicial de las piezas, es necesario disponer de tecnologías de post-procesado que permitan obtener la rugosidad requerida por todas las piezas fabricadas bajo un mismo modelo, independientemente de los parámetros de fabricación utilizados, su posicionamiento en la plataforma de fabricación y la geometría de la pieza.
Protección superficial
Los componentes producidos mediante fabricación aditiva, al igual que los fabricados por métodos convencionales, en ocasiones y en función de sus requerimientos finales, tienen que protegerse frente a la corrosión, desgaste, u otro tipo de agentes externos que pueden deteriorarlos. Para ello, pueden emplearse diferentes tipos de tratamientos y/o recubrimientos que necesitan ser adaptados para su óptima aplicación en estas nuevas superficies.
Tecnologías de post-procesado para eliminación de soportes, reducción de rugosidad y protección
Hoy en día, existen numerosos procesos para reducir la rugosidad, eliminar soportes y proteger superficies de fabricación aditiva. En la figura 3 se presenta un esquema que recoge las diferentes tecnologías que pueden aplicarse para este fin.
![Figura 3. Tecnologías de post-procesado para la reducción de rugosidad, protección superficial y eliminación de soportes [3]... Figura 3. Tecnologías de post-procesado para la reducción de rugosidad, protección superficial y eliminación de soportes [3]...](https://img.interempresas.net/fotos/3010003.jpeg)
Cada uno de estos procesos posee ventajas e inconvenientes y es necesario seleccionar el más adecuado para cada tipo de componente, en función de sus requerimientos, así como del coste del proceso.
Como se puede observar en el esquema, las tecnologías químicas y electroquímicas pueden emplearse para reducir la rugosidad, proteger o eliminar soportes. Es importante destacar que las principales ventajas de este tipo de tecnologías frente al resto es su bajo coste, permiten el tratamiento simultaneo de muchas piezas y no generan ningún tipo de tensión y/o deformación de la superficie tratada.
Las tecnologías químicas de modificación superficial se basan en la inmersión de la pieza a tratar en un electrolito a una temperatura determinada. En función del electrolito empleado, este proceso puede provocar la oxidación controlada de la superficie de la pieza sumergida dando lugar a su pulido superficial o a la eliminación de estructuras delgadas, como pueden ser las estructuras soporte. Los procesos químicos, además, pueden emplearse para modificar la composición y topografía de las superficies de las piezas tratadas de cara a favorecer la aplicación de capas posteriores. Asimismo, es posible obtener recubrimientos metálicos por vía química (siendo los recubrimientos de Ni-P los aplicados más habitualmente por esta tecnología), a través de reacciones de oxidación-reducción entre el electrolito y la superficie de sustratos tanto conductores como dieléctricos.
Las tecnologías electroquímicas implican igualmente la inmersión de la pieza en un electrolito determinado, pero en este caso aplicando una corriente eléctrica entre la pieza y un contraelectrodo. Si la pieza se conecta al polo positivo (ánodo), en función del electrolito empleado y de las condiciones de proceso aplicadas, las piezas se pueden electropulir o anodizar. Cuando la pieza se conecta al polo negativo (cátodo), en función de las sales metálicas presentes en la composición del electrolito, se pueden obtener, por electrodeposición, recubrimientos metálicos homogéneos sobre la pieza (por ejemplo: Cr, Ni, Cu…).
Proceso electroquímico para la disminución de rugosidad
El electropulido es un proceso electroquímico que, a pesar de ser ampliamente conocido y utilizado industrialmente desde hace décadas, sigue vigente debido a los beneficios que aporta, como son, superficies de baja rugosidad, uniformes, brillantes y libres de defectos y fisuras superficiales, entre otros. Además, permite obtener superficies de bajo coeficiente de fricción y, ultralimpias en las cuales la suciedad tiene muy difícil adherirse.
En la tabla 1 se presenta una comparativa entre los valores del parámetro de rugosidad Ra y la composición química de superficies de Ti6Al4V obtenidas mediante SLM antes y después de aplicar tres tratamientos de superficie diferentes: granallado mediante esferas de vidrio, electropulido y la combinación consecutiva de ambos procesos.
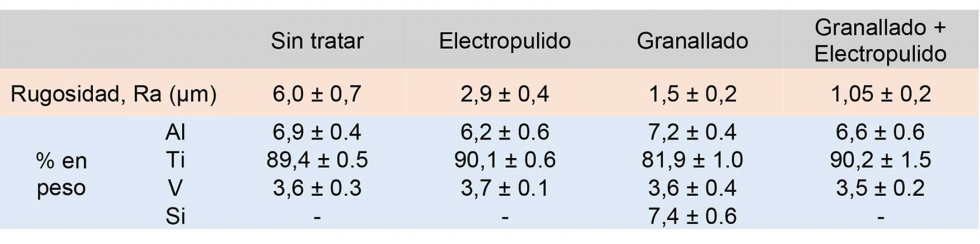
Como se puede observar, el electropulido consigue disminuir la rugosidad inicial en más de un 50%. Mediante granallado se consigue una disminución superior de la rugosidad, pero la superficie queda contaminada con Si proveniente de fragmentos de microesferas de vidrio incrustados en la pieza durante su procesado. No obstante, cuando a la superficie granallada se le aplica un posterior tratamiento de electropulido, se consigue disminuir aún más la rugosidad y además se eliminan las partículas incrustadas, dejando una superficie limpia.
El electropulido produce también superficies brillantes y puede aplicarse sobre geometrías relativamente complejas (figura 4).
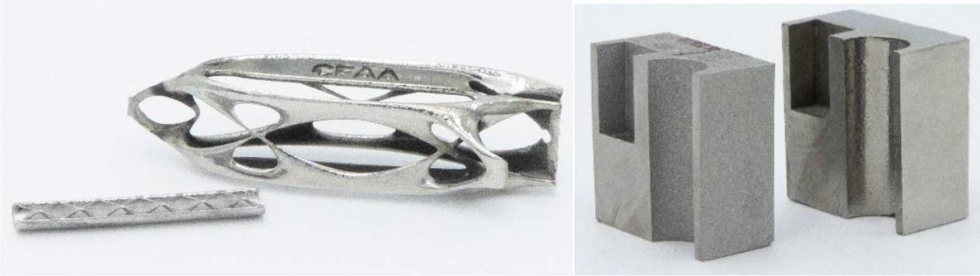
Proceso químico para la disminución de rugosidad
Al igual que el electropulido, el pulido químico es ampliamente empleado a nivel industrial ya que posee la gran ventaja de ser independiente de la forma, tamaño y estructura de la pieza a tratar. La inmersión de la pieza en el electrolito, contenido en cubas o tanques especiales, garantiza un procesado seguro. La eliminación de material está determinada por la concentración de los productos químicos, la temperatura de la solución y el tiempo del proceso. Las piezas con formas complejas se pueden pulir uniformemente con relativa facilidad.
La principal ventaja del pulido químico aplicado a los componentes de fabricación aditiva radica en que se pueden pulir superficies de piezas con geometrías complejas y canales internos estrechos, como los presentes en intercambiadores de calor.
En la figura 5 se muestra, como ejemplo, el interior de canales internos de 2 x 2 mm2 de piezas obtenidas por SLM en una aleación de aluminio, antes y después de ser tratadas empleando un proceso de pulido químcio basado en ácido fosfórico. Como se puede observar en las micrografías, el polvo parcialmente fundido en la superficie interna de los canales es eliminado por el proceso químico y la rugosidad superficial disminuye en torno a un 50%.
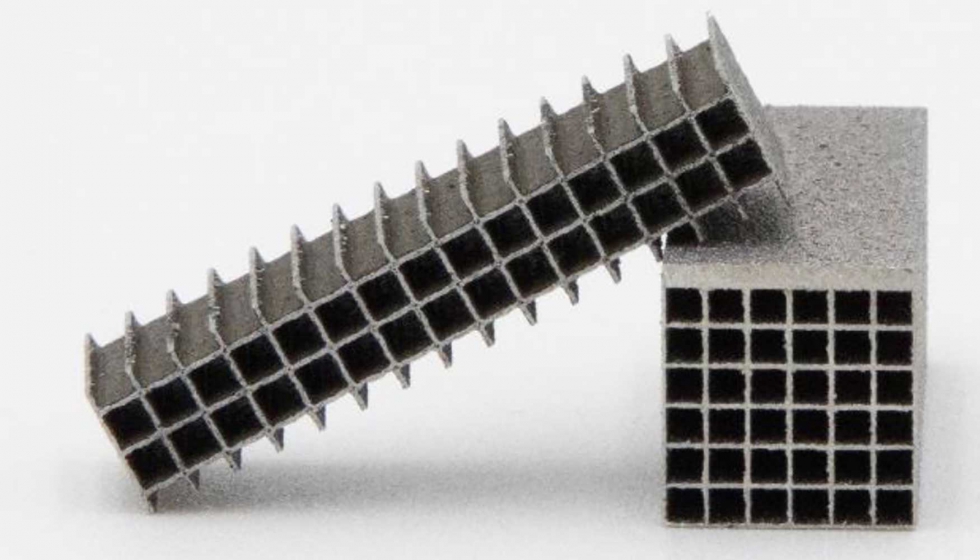
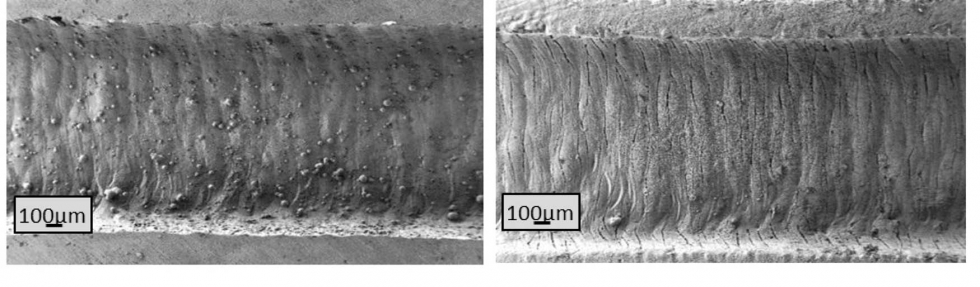
Figura 5. Probetas de aluminio con canales internos de 2 x 2 mm2 obtenidas por SLM y micrografías de los canales antes (izq.) y después (dcha.) de aplicar un proceso de pulido químico en Cidetec. Proyecto AMANECO (Clean Sky 2).
Por otro lado, el proceso de pulido químico, al contrario que el electroquímico, pueden emplearse también para tratar piezas poliméricas. Existen dos métodos principales de pulido químico para este tipo de materiales, el suavizado por vapor y la inmersión en líquido. Al igual que para materiales metálicos, es imprescindible seleccionar la química más adecuada, basada principalmente en disolventes, para el tratamiento de cada tipo de material polimérico a tratar.
Como ejemplo, en el caso de componentes de poliamida 12 (PA12), entre los disolventes estudiados destacan los compuestos orgánicos como son el cloruro de metileno (diclorometano), cresol, HFIP, combinaciones de ácidos orgánicos o combinaciones de diclorometano y ácido acético.
Cidetec ha llevado a cabo recientemente el desarrollo de un tratamiento químico para el pulido de piezas de PA12 mediante inmersión. En la figura 6, se muestran, respectivamente, los valores de reducción del parámetro de rugosidad Ra y del espesor de las muestras tratadas en un electrolito basado en ácidos orgánicos empleando diferentes tiempos y temperaturas del proceso. Para un mismo tiempo de tratamiento, la mayor efectividad en la reducción de la rugosidad se obtuvo para una temperatura de 80 °C, con valores de reducción de Ra comprendidos entre el 75 y el 95%. En la misma gráfica, se observa como una reducción de unos pocos grados en la temperatura del electrolito (tratamientos a 75 y 70 °C) comporta un pronunciado descenso de la efectividad del electrolito a la hora de reducir la rugosidad de las muestras de PA12. Para los tratamientos a 80°C, la mayor reducción de rugosidad se obtuvo con 50 minutos de inmersión. No obstante, como se observa en la figura 6, bajo estas condiciones se produce también la mayor eliminación de material (0,8 mm), por lo que para aquellas aplicaciones en las que se requieran tolerancias dimensionales menores, se puede optar por utilizar tiempos de tratamiento más cortos para los que se obtiene, todavía, una aceptable reducción de rugosidad.
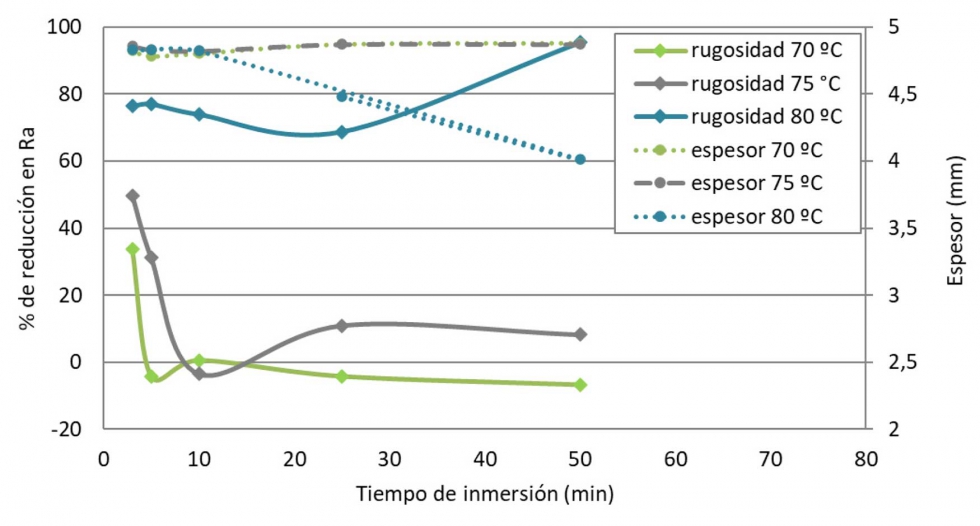
Además, ajustando las condiciones del proceso, principalmente el tiempo, es posible mantener los detalles y la geometría inicial de la pieza, tal como se muestra en la figura 7.
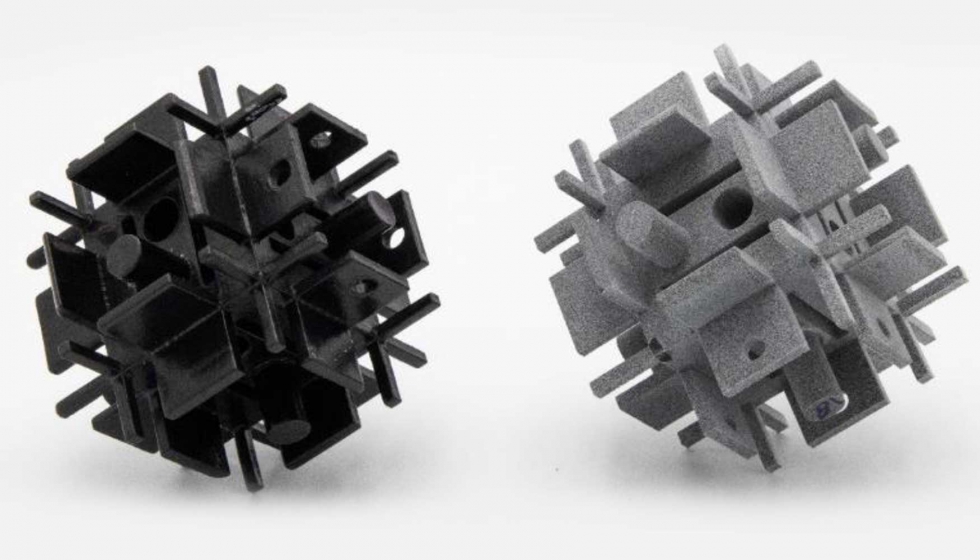
Proceso químico para la eliminación de estructuras soporte
Tal como se detalla en la figura 3, existen diferentes métodos para eliminar las estructuras soporte presentes en las piezas de fabricación aditiva, sin embargo, por lo general, los soportes se retiran manualmente o mediante mecanizado.
Empleando tecnologías químicas y electroquímicas, es posible disolver estas estructuras soporte, pero es necesario encontrar las condiciones de proceso, principalmente el tiempo, necesario para disolver cada tipo de soporte sin modificar las dimensiones de la pieza.
En la figura 8 se muestran piezas de In718 obtenidas por SLM, donde se han colocado estructuras soporte de diferente tipo. A estas piezas se les ha aplicado un tratamiento químico desarrollado por Cidetec y se ha comprobado el estado de los soportes después de 15 min de tratamiento. Finalmente, se ha calculado el tiempo necesario para eliminar cada una de estas estructuras y como se puede observar es muy dependiente del tipo de soporte presente en la pieza.
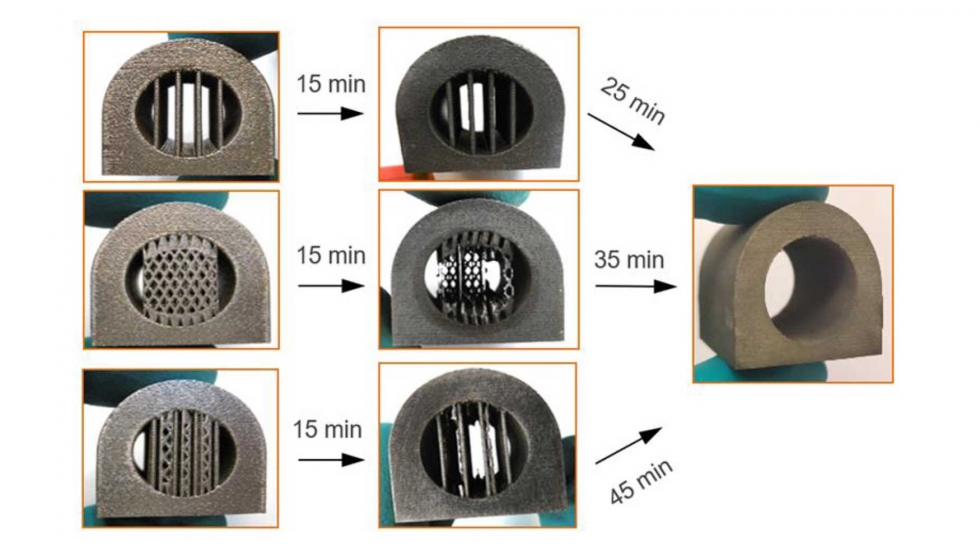
La principal ventaja de aplicar tecnologías químicas o electroquímicas para la eliminación de soportes es el hecho de que estos procesos pueden ser completamente automatizados, evitando así el coste de la mano de obra empleada hoy en día.
Protección electroquímica de aleaciones ligeras metálicas
El anodizado es uno de los tratamientos electroquímicos más empleados para proteger aleaciones ligeras (aleaciones de titanio, aluminio y magnesio). Durante el anodizado, la superficie del metal (ánodo) se recubre con una película estable, porosa y compleja de óxidos del propio sustrato metálico y de determinados elementos presentes en el electrolito, proporcionándole propiedades protectoras, decorativas y funcionales.
Para aleaciones ligeras obtenidas por tecnologías de fabricación convencionales, el anodizado es ampliamente conocido y aplicado a nivel industrial. Sin embargo, las aleaciones obtenidas por fabricación aditiva posen una microestructura totalmente diferente y en ocasiones, como es el caso de las aleaciones de aluminio, la composición y concentración de elementos aleantes también puede diferir. Este hecho puede provocar que la capa de anodizado no posea las mismas características y propiedades protectoras.
En Cidetec se ha trabajado en la aplicación del proceso de anodizado sobre aleaciones de Ti6Al4V obtenidas por diferentes tecnologías (convencional, LMD, SLM y WAAM), y en la caracterización de la resistencia a la corrosión de estas superficies mediante técnicas electroquímicas (curvas de polarización). Con el fin de disponer de superficies homogéneas con la misma rugosidad previo al anodizado, todas las piezas fueron electropulidas. Como se puede observar en la figura 9, las superficies electropulidas de todas las probetas de titanio analizadas poseen un comportamiento muy similar frente a la corrosión y el anodizado mejora esta respuesta. En todos los casos, comparando las curvas de las superficies anodizadas con las de las superficies electropulidas, el potencial de corrosión (Ecorr) aumenta y la densidad de corriente de pasivación disminuye. Sin embargo, se aprecian diferencias en esta respuesta dependiendo del tipo de superficie anodizada. Estas diferencias se deben principalmente a la microestructura de las superficies.
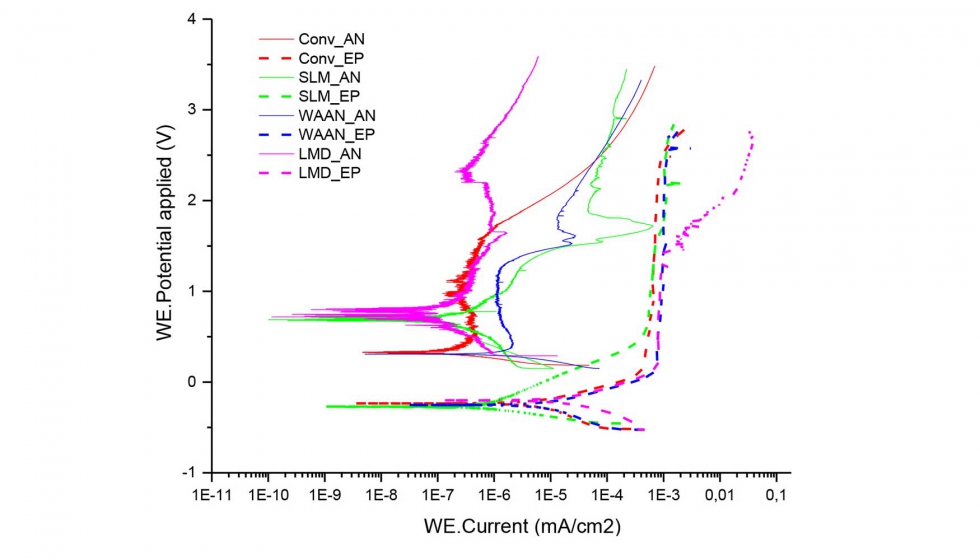
En este trabajo se comprobó también que las superficies de Ti6Al4V obtenidas por tecnologías de fabricación aditiva se anodizan de manera homogénea en diferentes tipologías de piezas. En la figura 11 se muestran, como ejemplo, dos piezas de Ti6Al4V por SLM, anodizadas en condiciones estándar empleadas por el sector aeronáutico.
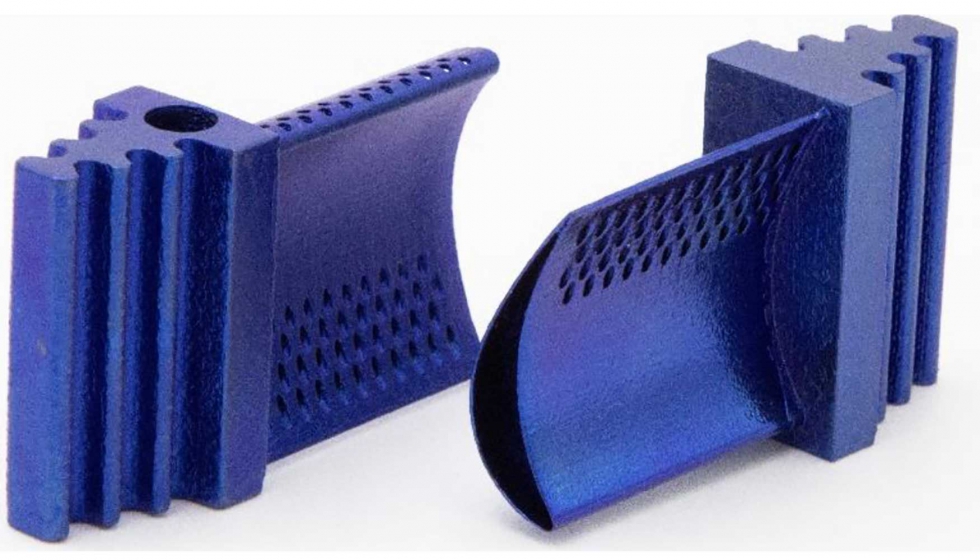
Protección (electro)química de polímeros
Los materiales plásticos pueden ser recubiertos con una capa fina metálica, buscando diferentes propiedades como conductividad eléctrica, conductividad térmica, resistencia a la corrosión, residencia a la abrasión o estética. El caso de las piezas con geometrías complejas la mejor técnica para el metalizado de estos materiales es el metalizado químico/electroquímico, ya que al sumergirse la pieza completamente en el electrolito, permite recubrir las zonas de difícil acceso de manera más eficiente que el resto de las técnicas.
El proceso de metalizado químico/electroquímico consiste en una serie de etapas: pretratamiento, metalización química y electrodeposición del acabado final. La etapa más crítica es el pretratamiento, en la cual se consigue una estructura superficial adecuada en el substrato para que la adherencia de las capas metálicas sea correcta. En el caso de las poliamidas, aun a pesar de existir procesos patentados, a nivel industrial se trata de procesos muy complejos y dependientes en gran medida del proceso de fabricación del substrato plástico (inyección, moldeado, laminado, fabricación aditiva…). Por ello, para facilitar el proceso de metalizado, se añaden aditivos en el material que lo favorezcan. Este es el caso de las poliamidas reforzadas con fibras, como la fibra de vidrio o la fibra de carbono. Estas fibras, además de aportar propiedades al propio polímero, se utilizan como puntos de ataque durante la etapa de pretratamiento, para generar los puntos de anclaje del recubrimiento metálico. Algunas de las tecnologías de fabricación aditiva actuales, permiten fabricar piezas con este tipo de material modificado.
Preparación química superficial de polímeros
Una vez reducida y controlada la rugosidad superficial de las piezas poliméricas obtenidas por fabricación aditiva es necesario preparar su superficie para un recubrimiento metálico electrodepositado posterior. Esta preparación puede llevarse a cabo mediante métodos químicos, empleando ácidos o base fuertes, disolventes orgánicos, modificación química superficial, deposición de vapores químicos o uso de soluciones oxidantes. Excepto la última opción, el resto de opciones tienen la desventaja de usarse disolventes inflamables, sustancias fuertemente reactivas, gases venenosos o de provocar un envejecimiento de los baños utilizados en etapas posteriores del proceso de metalizado. Es por ello que la alternativa más prometedora es el uso de soluciones oxidantes ya que producen un mordentado adecuado del substrato, generan grupos polares que facilitan la aplicación de las capas metalicas en las etapas subsiguientes y permiten trabajar en fase acuosa. Además, este tipo de pretratamiento elimina el uso de Cr VI, utilizado en procesos de metalizado de plásticos tradicionales.
Cidetec Surface Engineering lleva años investigando en el desarrollo de soluciones, principalmente a través de tecnologías químicas y electroquímicas, para el post-procesado de piezas metálicas y poliméricas obtenidas por fabricación aditiva, colaborando tanto con empresas como con centros de investigación. Actualmente, Cidetec trabaja en el control y automatización de estos procesos para que sean más precisos, sistemáticos y controlados. Asimismo, Cidetec está investigando en el empleo de electrolitos no convencionales y medioambientalmente más sostenibles tanto para los procesos químicos (eliminación de soportes, pulido de material metálico y polimérico, mordentado polimérico previo a metalizado), como para los electroquímicos (electropulido, anodizado, electrodeposición…).
Cidetec Surface Engineering dispone de 4.000 m2 de instalaciones equipadas con tecnologías avanzadas en las que se cubre desde la investigación básica, pasando por la adaptación de procesos y la obtención de preseries, hasta el ensayo en condiciones muy próximas a la realidad. El equipamiento disponible en Cidetec para el post-procesado de componentes de fabricación aditiva cuenta con un módulo de acabado superficial y eliminación de soportes por vía química y electroquímica, un módulo de aplicación de recubrimientos metálicos por vía química electroquímica, un módulo de chorreado a presión para texturizado y pulido a medida y equipamiento láser de nanosegundos (UV, IR, Cos y verde) para pulido y texturizado selectivo. Asimismo, Cidetec dispone de un equipo de fabricación aditiva de tecnología FDM (Stratassys Fortu 450 mc.).
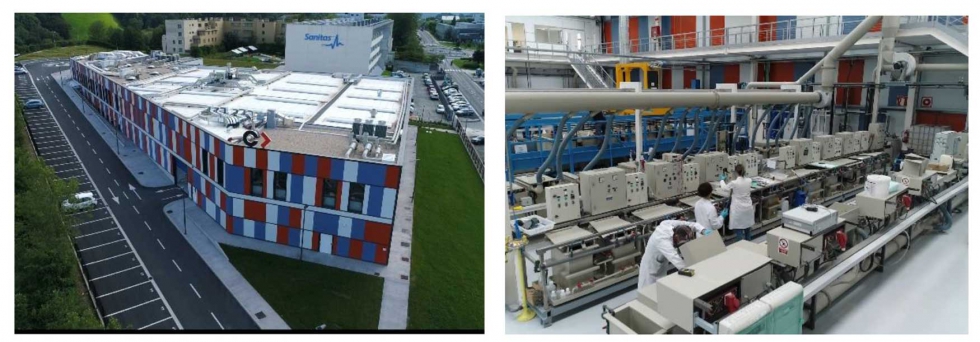
Referencias
[1] https://www.gminsights.com/industry-analysis/additive-manufacturing-with-metal-powders
[2] https://www.3dnatives.com/en/postprocess-trends-2020-020920204/#!
Cidetec es una organización de investigación aplicada que integra a tres centros tecnológicos de referencia internacional en Almacenamiento de Energía, Ingeniería de Superficies y Nanomedicina. Cidetec, fundada en 1997, tiene como objeto la aportación de valor a las empresas mediante la captación, generación y transferencia de conocimiento tecnológico. La misión de Cidetec es incrementar, a través del desarrollo de nuevos productos y procesos, la capacidad de innovación y la competitividad de las empresas. En Cidetec trabajan 190 profesionales, de los cuales un 95% son titulados superiores y un 44% doctores. Los investigadores y tecnólogos que integran Cidetec tienen como objetivo fundamental transformar el capital de conocimiento de la entidad en soluciones industrializables y sostenibles. En la actualidad, Cidetec dispone de 26 familias de patentes activas y su volumen de actividad alcanzó los 14 M€ en 2020. Cidetec cuenta con la acreditación ISO17025 y la acreditación NADCAP para Ensayos No Destructivos (END).