El nuevo sistema Flex Finishing de ABB revoluciona el sector de la robótica
15 de noviembre de 2008
de contacto y de bucles de realimentación que controlan la fuerza y la adaptan al movimiento del brazo del robot. Con estos robots de fuerza controlada trabajando con el controlador de robots S4Cplus, el tiempo de montaje de grupos propulsores se pudo reducir hasta en un 75 por ciento. Recientemente, se ha logrado dar un paso más en el uso de robots de fuerza controlada en una clase más compleja de aplicaciones: rectificado, desbarbado y pulimentado de unidades fabricadas, por ejemplo, en un taller de fundición. A diferencia del montaje de piezas, el control de las fuerzas del proceso en estas aplicaciones es mucho más exigente, y hasta ahora no era posible conseguirlo. Existen varias razones para esa mayor complejidad: el desgaste de las herramientas, las dimensiones variables de las piezas y la falta de una precisión total y repetible de los soportes, con el riesgo de grandes desviaciones de la posición y resultados irregulares. Tradicio-
nalmente, el proceso de acabado ha precisado mucha mano de obra, y la calidad del producto terminado no ha concordado con el rectificado, desbarbado y pulimentado manual. Hasta ahora, la posición de los robots utilizados para esta tarea se controlaba con herramientas y soportes adaptables, de acuerdo con trayectorias y velocidades definidas, ayudados a veces por un servomotor extra a fin de ajustar las variaciones en las dimensiones.
En este modo de operación, si el robot no puede alcanzar la trayectoria fijada porque la pieza no está colocada correctamente, seguirá tratando de cortar a través de ella. En consecuencia, el robot se para, la herramienta se rompe o la pieza se estropea.
Para limitar esos daños, los robots clásicos de limpieza de piezas de fundición funcionan a un ritmo más lento con una productividad limitada. Debido a la necesidad del control de posición, estos robots deben estar programados para ajustarse a una alta precisión en la trayectoria, un esfuerzo que exige mucho tiempo al ingeniero. Todos estos inconvenientes estaban frenando la expansión de las aplicaciones de los robots en esta industria.
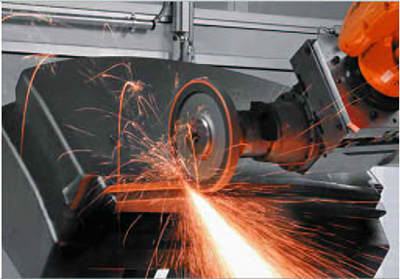
Pasos hacia una innovación sustancial
El IRC5 se construye sobre el sistema operativo más avanzado de la industria para control de robots y equipos periféricos. Con el lenguaje Rapid y el sistema operativo para robótica Motion Technology and Communication (tecnología de movimientos y comunicaciones) de ABB, constituye el sistema operativo de controlador más potente existente en la actualidad. IRC5 tiene dos canales Ethernet, uno para LAN y otro para conexión local, así como dos canales serie para comunicaciones punto a punto con los sensores. El ancho de banda proporcionado por el controlador IRC5 es crítico para las prestaciones globales y el tiempo de reacción del robot con vistas a corregir y ajustar su posición. Para alcanzar la tasa de muestreo adecuada para ajustar el posicionamiento dinámico del robot, el sensor debe estar estrechamente integrado con la electrónica del controlador si se quiere que esta innovadora aplicación arroje buenos resultados. El IRC5, equipado con Motion Technology MultiMove de ABB, es una referencia mundial que permite el control simultáneo de hasta cuatro robots (36 ejes). Los robots pueden compartir objetos de trabajo comunes, lo que permite configuraciones complejas coordinadas. MultiMove facilita asimismo el cambio dinámico entre movimientos independientes y coordinados. Esta característica única hace posible abordar las tareas complejas de rectificar, desbarbar y pulimentar. El entorno de programación que apoya al usuario de esta aplicación innovadora es el primero en ofrecer esta nueva dimensión de programación. Permite una programación sencilla y eficaz al utilizar el propio sensor de fuerza para definir la trayectoria del movimiento del robot. La programación se gestiona desde el FlexPendant y desde un módulo exclusivo de la aplicación para crear el programa para Force Control Machining (mecanización con control de fuerza). El concepto proporciona al operario la posibilidad de mover a mano el robot y enseñarle la trayectoria aproximada. Posteriormente, el robot utilizará automáticamente la información aproximada para seguir la pieza; al tiempo, registrará automáticamente la trayectoria exacta y creará un programa de robot. El bucle de realimentación FC Pressure permite que el robot rectifique, pulimente o pula objetos fundidos manteniendo una presión constante entre la herramienta y la superficie de trabajo. El software FC Pressure está destinado a procesos que requieran una superficie terminada de gran calidad. Permite que el robot 'sienta' efectivamente su entorno y siga la superficie de la pieza fundida, cambiando su posición para aplicar una presión constante en la superficie, incluso si no se conoce su posición exacta. Mientras haya un contacto continuo, las rebabas y otros sobrantes se eliminan hasta la misma profundidad.
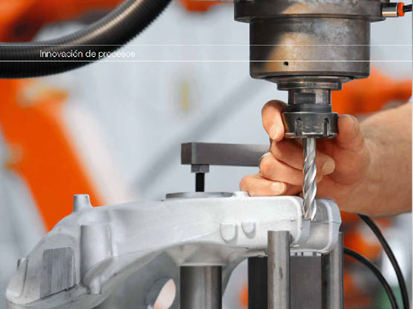
El producto final incluye un procesamiento avanzado de la señal del sensor, funciones matemáticas, solución lógica y una interfaz gráfica de usuario orientados a una programación rápida, fácil y precisa en la que se utiliza el sensor para que el operario guíe con la mano al robot con vistas a una programación directa e intuitiva. El producto de 'enchufar y utilizar' contiene todos los componentes necesarios, con el sensor, la electrónica y el cableado montados y probados en el robot, y sólo deja al integrador o al cliente el proceso de adaptación.
Una acción concertada para lograr el éxito
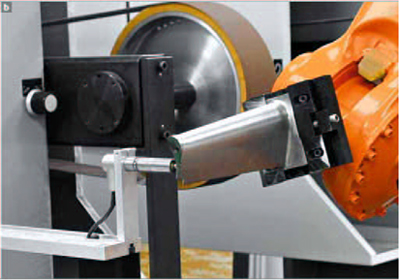
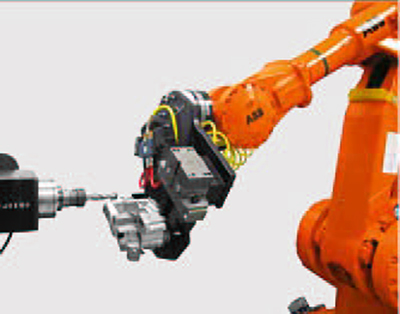
Un fuerte tirón en el mercado
Ahora, con RobotWare Machining FC, las operaciones de acabado de productos en las fundiciones son mucho más sencillas y permiten obtener piezas coladas acabadas mejor, más rápidamente y a mejor precio.