Engranajes en máquinas de propósito general de 5 ejes
Que la fabricación de esta clase componentes en máquinas de propósito general se presente como un tema de actualidad se debe principalmente a la mejora continua que están sufriendo tanto los CNC multieje, como las máquinas 5 ejes/’multitasking’, como los software CAD/CAM a lo largo de la última década. Las principales ventajas que aporta el uso de una máquina de propósito general 5 ejes para el mecanizado de esta clase de componentes son:
- Reducción de inventario. Permite el uso de herramienta estándar.
- Especialmente indicado para el mecanizado de engranajes ‘únicos’ y con tiradas muy reducidas, como es el caso de los engranajes cónicos.
- Aporta una enorme flexibilidad en el mecanizado, tanto en términos de geometría como de tamaño, además de permitir la posibilidad de incluir micro correcciones de flanco como son el ‘tip relief’, ‘root relief’, ‘angular profile variance’, ‘profile crowning’, ‘angular lead variance’, ‘end relief ‘y ‘lead crowning’.
- Ecológico. No se necesitan aceites de corte.
- El pretratamiento y el postratamiento de la pieza se pueden realizar en la misma máquina.
- Piezas complejas pueden ser mecanizadas en una sola atada, por ejemplo piezas que presenten engranajes internos y externos.
- Obtención de un producto de calidad elevada (hasta DIN 3 (AGMA 14**)), siendo factible la obtención de superficies tan lisas como las obtenidas mediante rectificado.
**according to AGMA A2000-A88 standards.
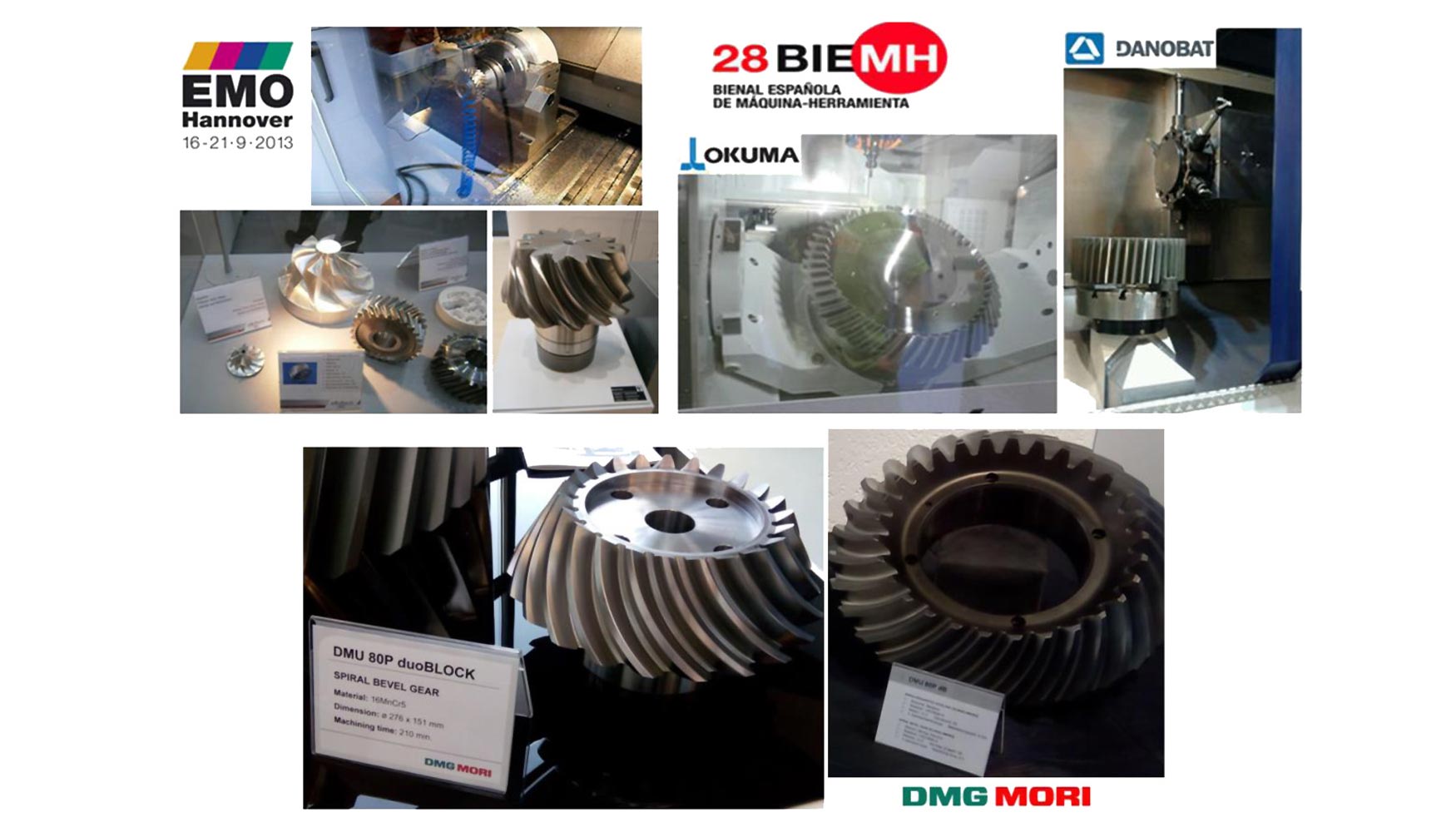
Como ya se ha comentado anteriormente, el uso de máquinas de propósito general nos permite mecanizar cualquier tipología de engranaje, pero es para el mecanizado de los engranajes cónicos de gran tamaño, y más concretamente los que presentan una mayor complejidad en su geometría, como es el caso de los cónicos-espirales (espirocónicos), en los que su utilización puede verse favorecida.
Los engranajes espirocónicos de gran tamaño son frecuentemente utilizados en aplicaciones donde se requiera una elevada transmisión de potencia, y donde esta transmisión debe ser lo más suave y silenciosa posible, como es el caso de aplicaciones de generación de energía térmica, sistemas de propulsión de barcos, turbinas eólicas o la transmisión de potencia en el sector aeronáutico, entre muchas otras.
Los engranajes espirocónicos son generados en su mayoría mediante procesos de corte continuos en máquinas específicas, clasificadas en función del método de fabricación utilizado. Existen diferentes métodos de fabricación, como son: a) Generación mediante ‘hobbing’ con fresas de plato con cuchillas de corte perimetral (sistema Gleason); b) Generación continua mediante hobbing espiral con fresas de plato con cuchillas de corte perimetral (sistema ‘Cyclo-Palloid de Klingelnberg’ y sistema Oerlikon); y c) Generación continua mediante hobbing espiral con fresa-madre del tipo cónica (sistema ‘Palloid de Klingelnberg’). En la figura 2 se puede observar cada uno de los métodos descritos anteriormente.
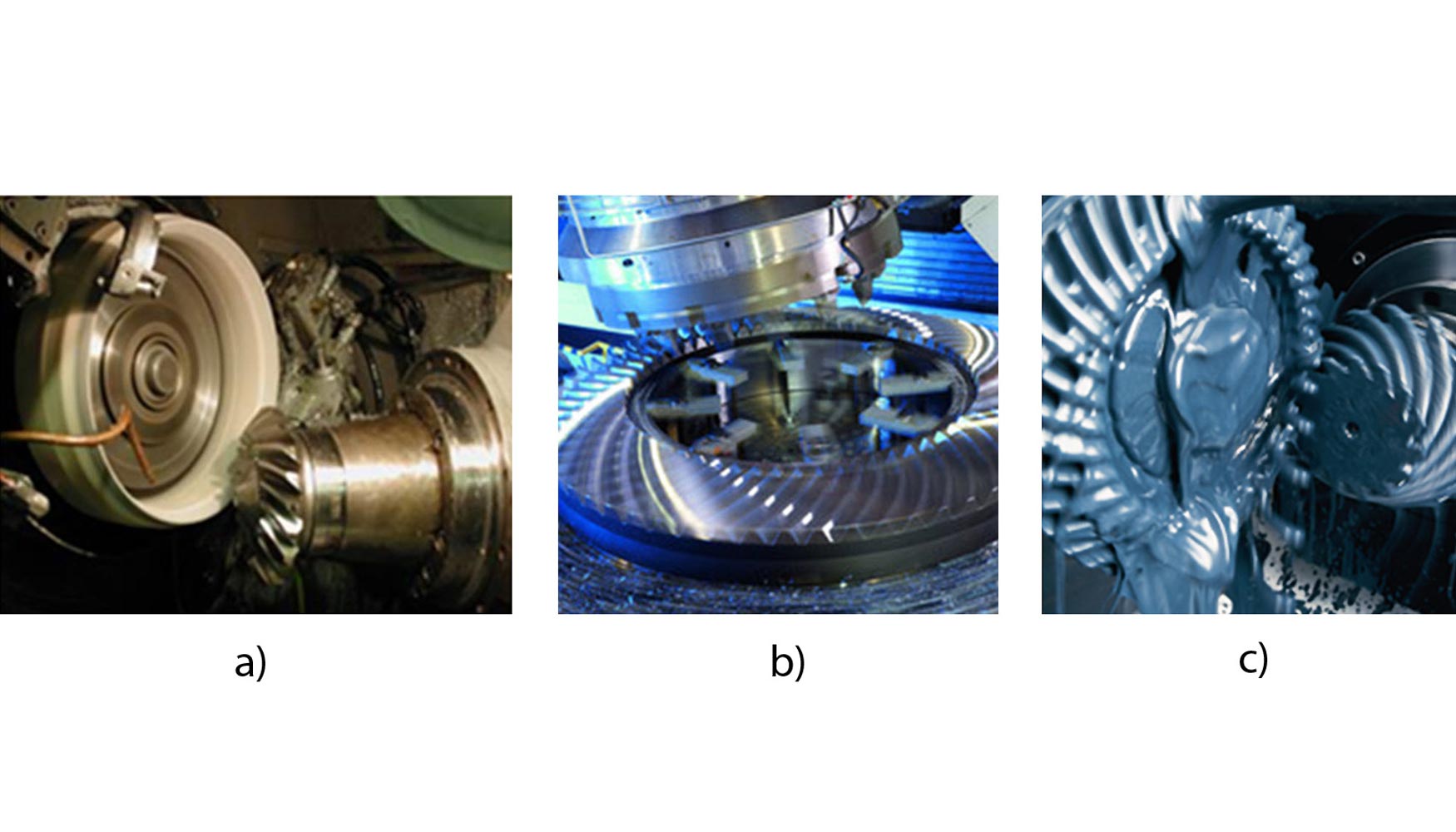
Para llevar a cabo el mecanizado de los engranajes espirocónicos, se precisa de modelos sólidos viables de los mismos. Sin embargo, hay que ser conscientes de la complejidad de la geometría cinemática de los engranajes espirocónicos, en conformidad con la variedad de métodos de corte existentes (Gleason, Klingelnberg, Oerlikon). Tampoco es fácil de generar el modelo 3D necesario para el mecanizado.
Existe una gran variedad de software de cálculo comerciales útiles para generar la geometría 3D. Una vez se tiene la geometría 3D del engranaje se precisa de un software CAM el cual permita programar cada una de las estrategias de mecanizado necesarias para lograr el engranaje final a partir del ‘blank’ de partida.
Las opciones de las que dispone el usuario se pueden resumir en las siguientes:
1- Software diseño + Software CAM
- El diseño del engranaje se realiza en un software específico, y una vez generado se importa en un software CAM en el cual serán programadas cada una de las estrategias de mecanizado. El software de diseño más utilizado del mercado es KISSsoft AG (Figura 3).
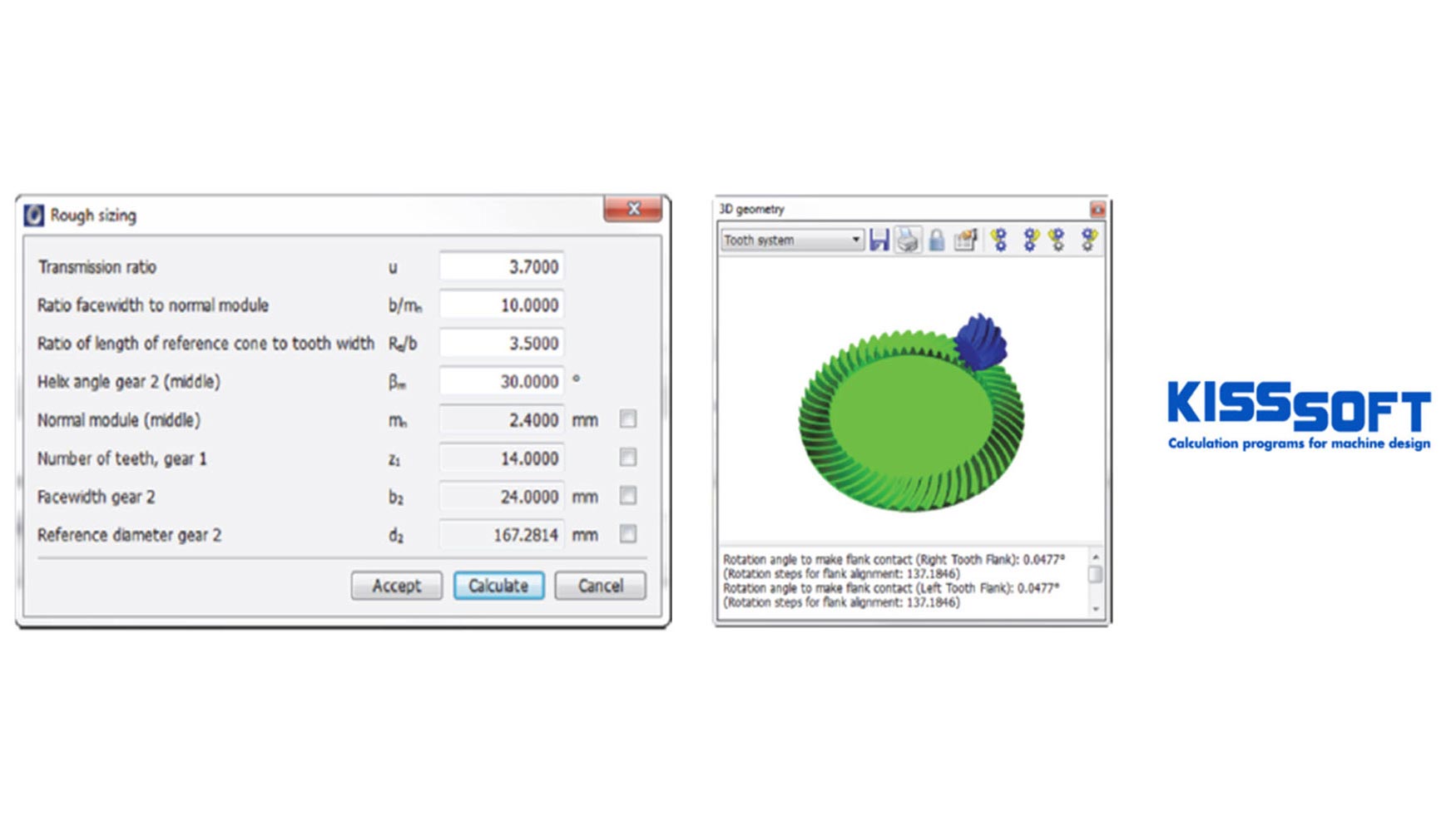
2- Software CAD con módulo diseño + Software CAM
- El diseño del engranaje se realiza gracias a la incorporación de un módulo de diseño de engranajes en el propio software CAD. Una vez generado el engranaje, este será importado en un software CAM en el cual serán programadas cada una de las estrategias de mecanizado. El módulo GearTrax (Figura 4), que muchos software CAD permiten su incorporación (Solid Edge, SolidWorks, Inventor, etc.), permite crear modelos sólidos de componentes de transmisión, como son los engranajes. Permite crear engranajes cilíndricos rectos, helicoidales y engranajes cónicos rectos.
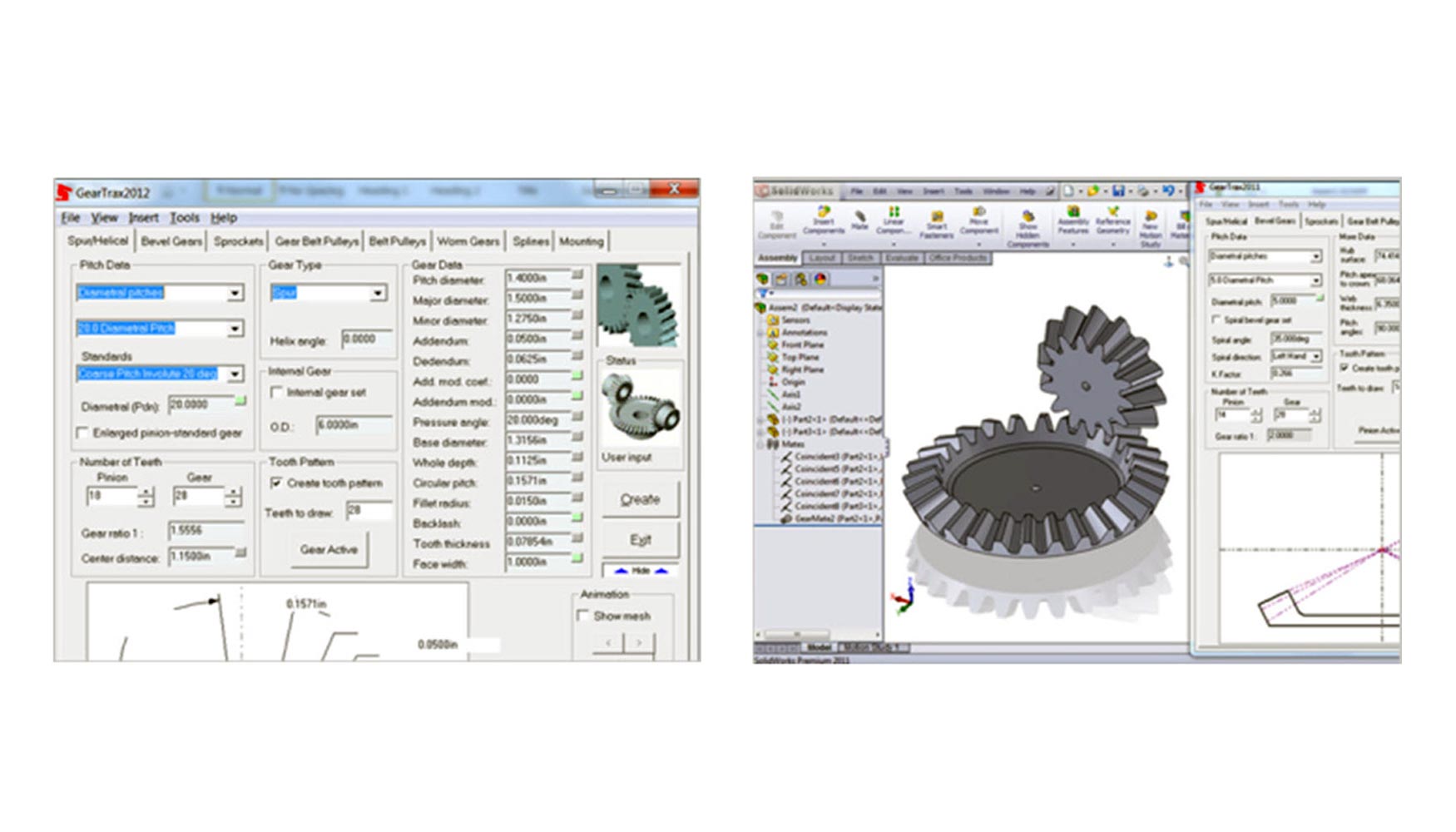
3- Software CAD/CAM específico para engranajes
- Tanto el diseño del engranaje como la programación de las diferentes estrategias de mecanizado se realizan en un mismo software. El proceso queda simplificado al ser sólo preciso un software, aunque este tipo de software específico suele conllevar un mayor coste de adquisición. A destacar el software EUKLID GearCAM (Figura 5).
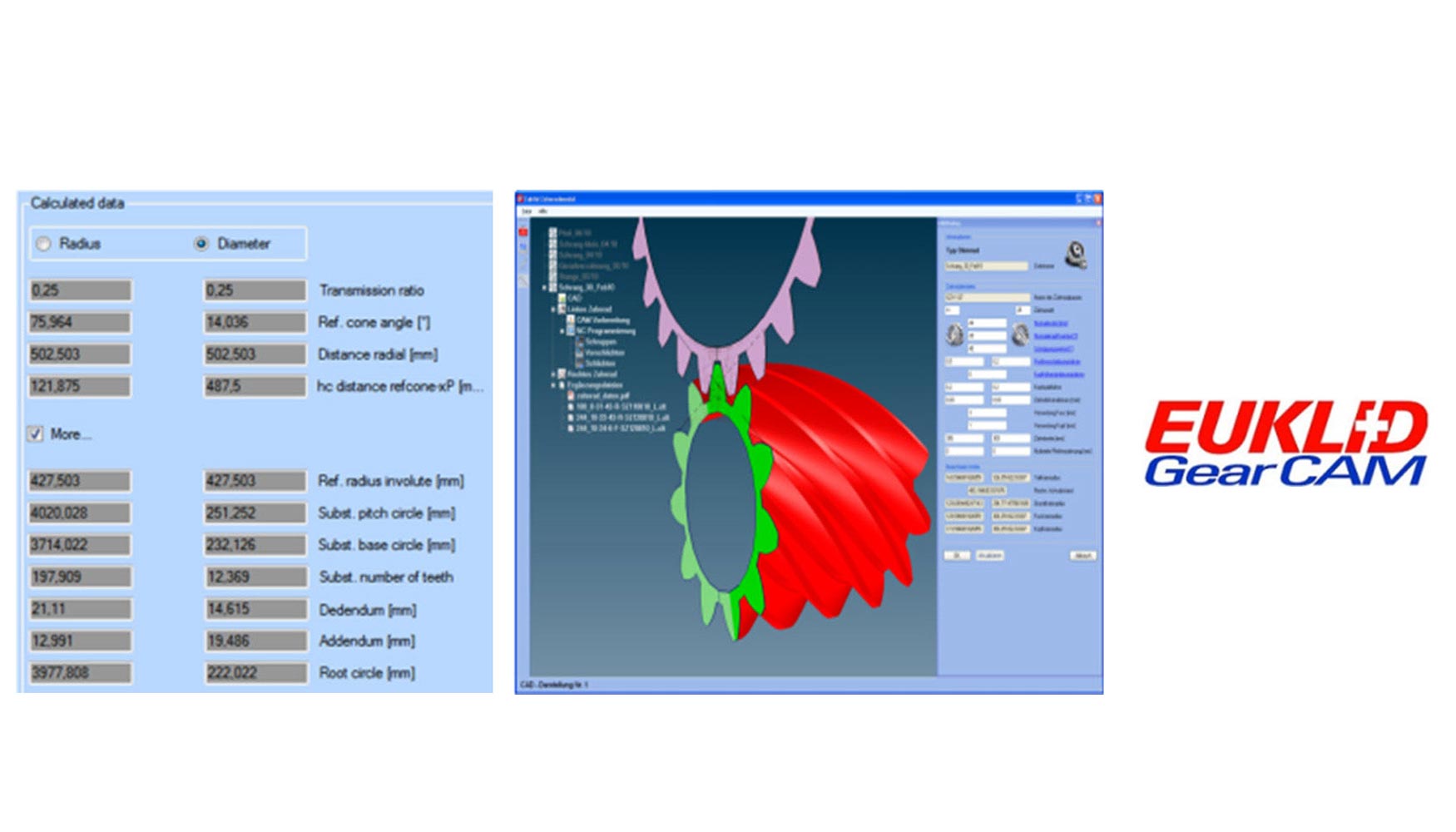
4- Software específico creado por fabricantes de máquina-herramienta
- Grandes e importantes fabricantes de máquina-herramienta han creado su propio software que permite el mecanizado de las diferentes tipologías de engranajes directamente desde máquina. Consiste en añadir un módulo al control numérico de la máquina, el cual permite, una vez se han introducido los diferentes parámetros de diseño del engranaje, optimizar tanto el diseño del mismo como la programación de las diferentes estrategias de mecanizado a llevar a cabo. Como ejemplos se pueden destacar tanto el gearMILL de DMG MORI (Figura 6) como el GearPro de MAG.
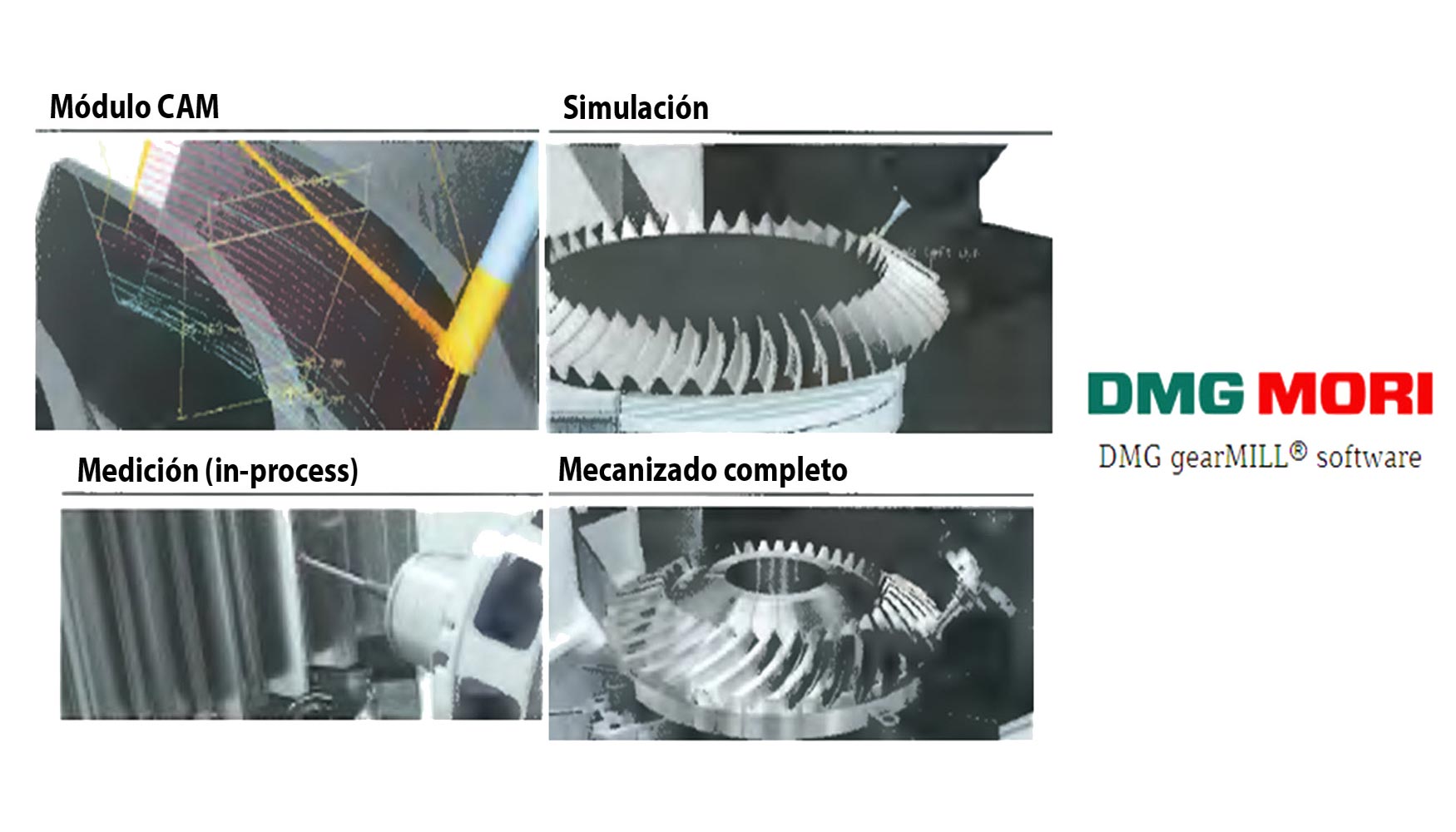
Esta opción supone un requisito esencial añadido, como es el de disponer de una máquina de uno de los fabricantes que ofertan el software específico de engranajes e incorporarlo a su control.
El mecanizado se puede hacer de principio a fin desde la propia máquina. El software permite realizar una simulación previa al mecanizado, detectándose así posibles colisiones herramienta-pieza, herramienta-máquina o máquina-máquina. Además permite la medición de diferentes parámetros relevantes a lo largo del proceso de mecanizado, lo que permite un mejor control del proceso.
La opción más económica es la primera, debido en parte a la existencia de un software CAD/CAM en casi la totalidad de las empresas dedicadas al mecanizado, por lo que sólo precisarían de la adquisición de un software de diseño. Además, existen en el mercado software de diseño a costes bastante económicos. Para el caso particular del diseño de engranajes espirocónicos, todo software existente permite la elección por parte del usuario del método de fabricación para la generación de los dientes, ya sea Gleason o Klingelnberg (Figura 7). Piñón y corona son generados al mismo tiempo debido a que los engranajes cónicos son siempre producidos en pares y a partir del mismo proceso de mecanizado con el fin de conseguir un buen patrón de contacto en la práctica.
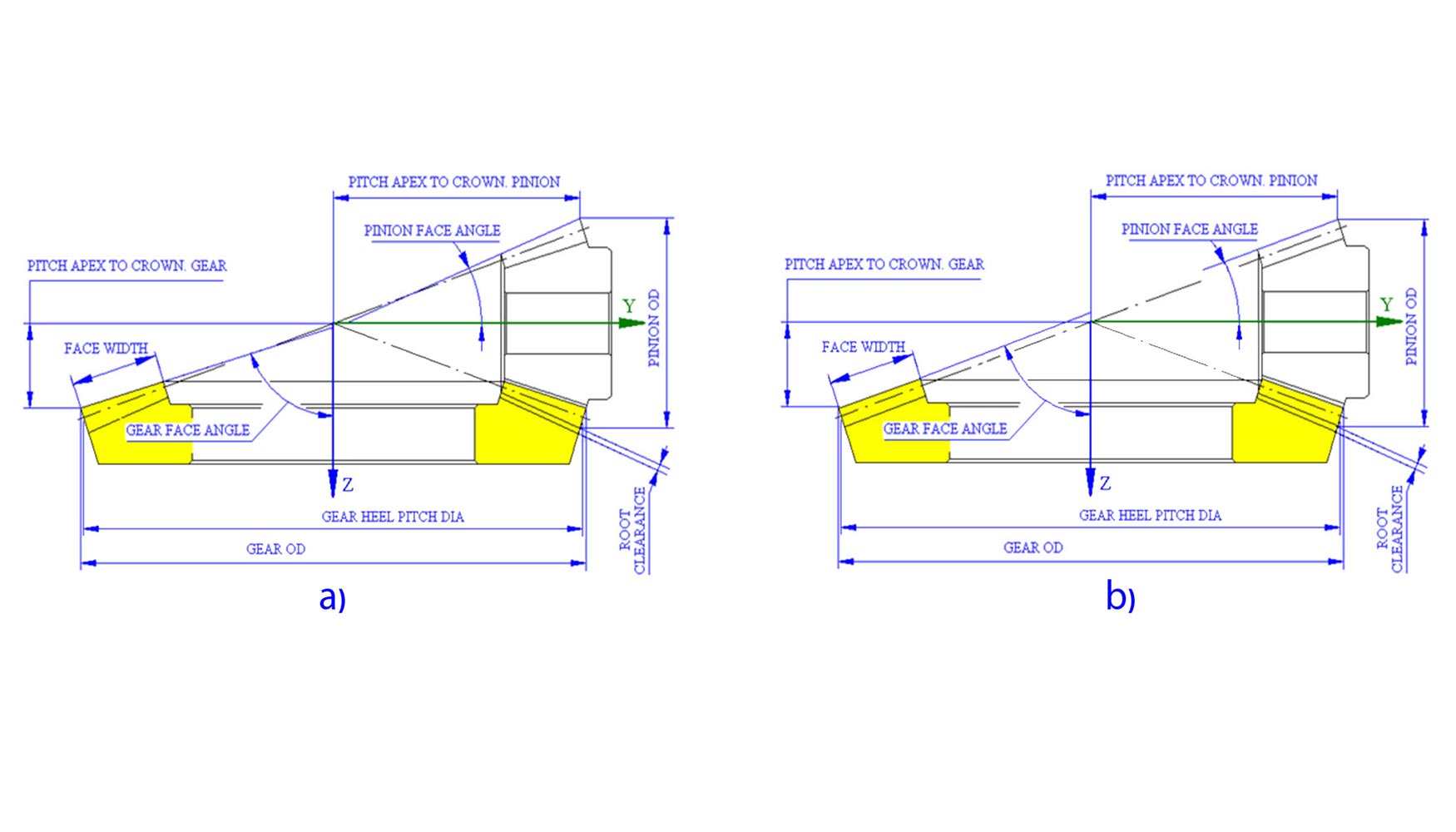
Otra de las ventajas que presenta esta opción es que permite realizar el mecanizado de estos componentes en cualquier máquina de propósito general de 5 ejes, indistintamente del fabricante de la misma.
En los últimos años han adquirido cierta relevancia las máquinas de propósito general que se conocen como ‘multitasking’ (multitarea o multifunción). El ‘multitasking’ se podría resumir como ‘La combinación de operaciones/funciones/tareas de diferentes tecnologías en una máquina especialmente diseñada para ello’. El objetivo existencial de esta clase de máquinas, debido a que posibilitan la capacidad de que la pieza de trabajo pueda ser atacada por 5 caras, es conseguir reducir, con el objetivo de dejarlo en una, el número de atadas que necesita la pieza para ser mecanizada incorporando el mayor número de operaciones/funciones/tareas dentro de una misma máquina. En la figura 8 se muestra un centro de mecanizado de mesa fija y columna móvil con cabezal giratorio para operaciones de fresado y torneado de la compañía Ibarmia Innovatek S.L.U.
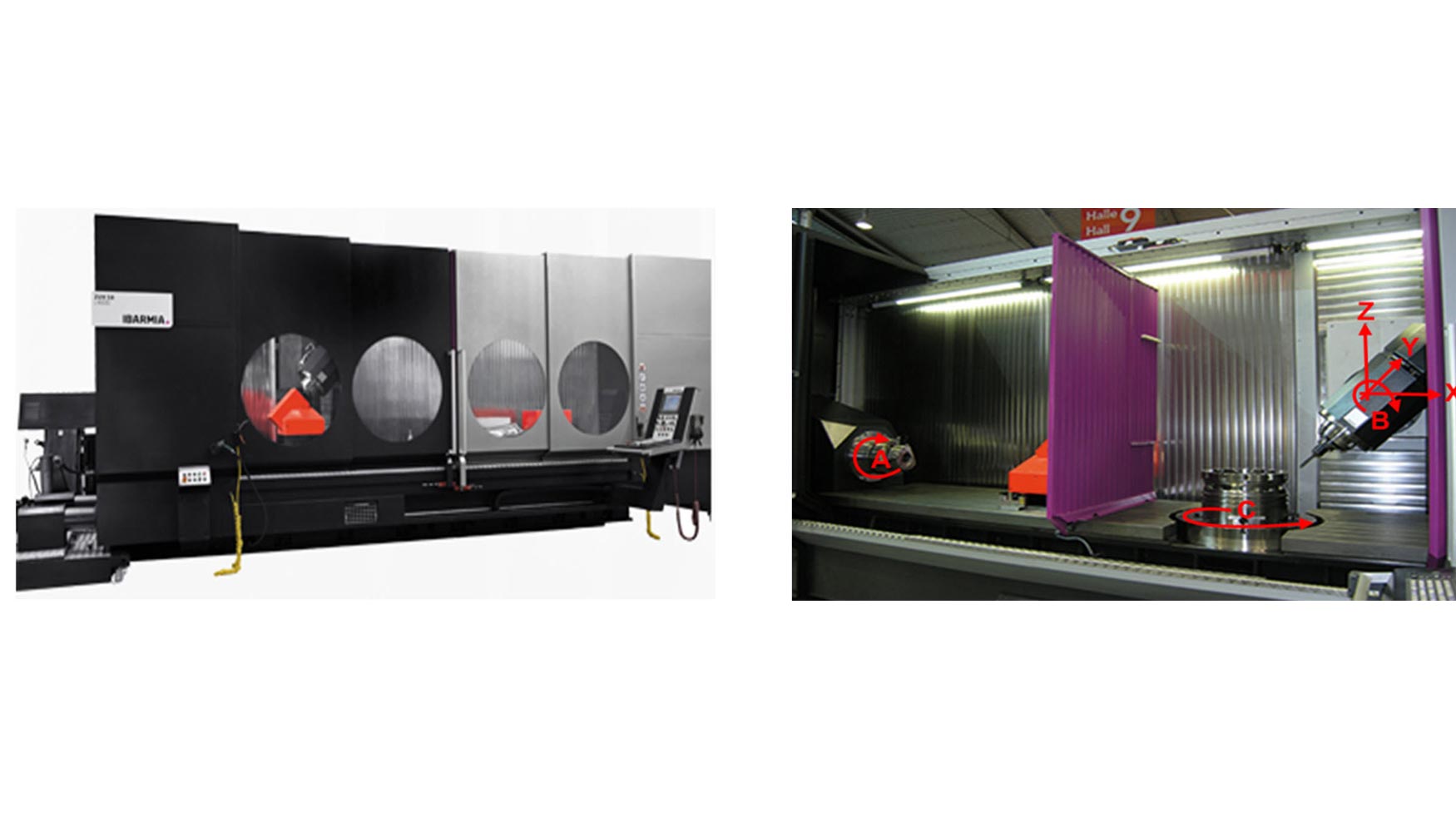
Las principales ventajas que presentan las máquinas multitasking respecto a los típicos centros de mecanizado 5 ejes se pueden resumir en los siguientes puntos:
- Al combinarse en una misma máquina diferentes operaciones, esto permite que la pieza sólo pase por una sola máquina para su mecanizado. Esto garantiza un tiempo mínimo entre el pedido y la entrega al cliente, garantizándose un plazo óptimo, lo que repercute de forma directa en una ganancia de pedidos. Ahorro de costes asociados a las máquinas, como mantenimientos, reparaciones, energía, etc.
- Reducción de stock. Se reduce el stock, los plazos se mejoran y, al ser un stock estándar, no hay riesgo de obsolescencia.
- Simplificación de utillajes. La mayoría de las máquinas ‘multitasking’ permiten la sujeción de la pieza de trabajo sin más que cambiar las garras del plato, mientras que un centro de mecanizado 5 ejes típico suele precisar de sistemas de amarre externos. La diferencia de coste de utillajes si una pieza se realiza en una ‘multitasking’ y en un centro de mecanizado es grande y obvia.
Otra de las ventajas de no ser necesarios sistemas de amarre externos, muchos de los cuales precisan de una pre-forma previa de la pieza de trabajo, es que el material sobrante tras el mecanizado puede ser utilizado para posteriores mecanizados, lo cual supone un ahorro tanto en material como en herramientas. También se podría interpretar como la no necesidad de un material de partida de tales dimensiones, reduciéndose así el coste en la adquisición del mismo.
En la figura 9 se muestra la realización de un mismo engranaje en dos máquinas diferentes y partiendo del mismo material de partida. Como bien se puede observar, en el engranaje realizado en el centro de mecanizado 5 ejes el uso de una mordaza autocentrante precisa de una preforma previa, inutilizando el material sobrante para futuros mecanizados, además de suponer un coste adicional en herramientas y tiempo a tener en cuenta.
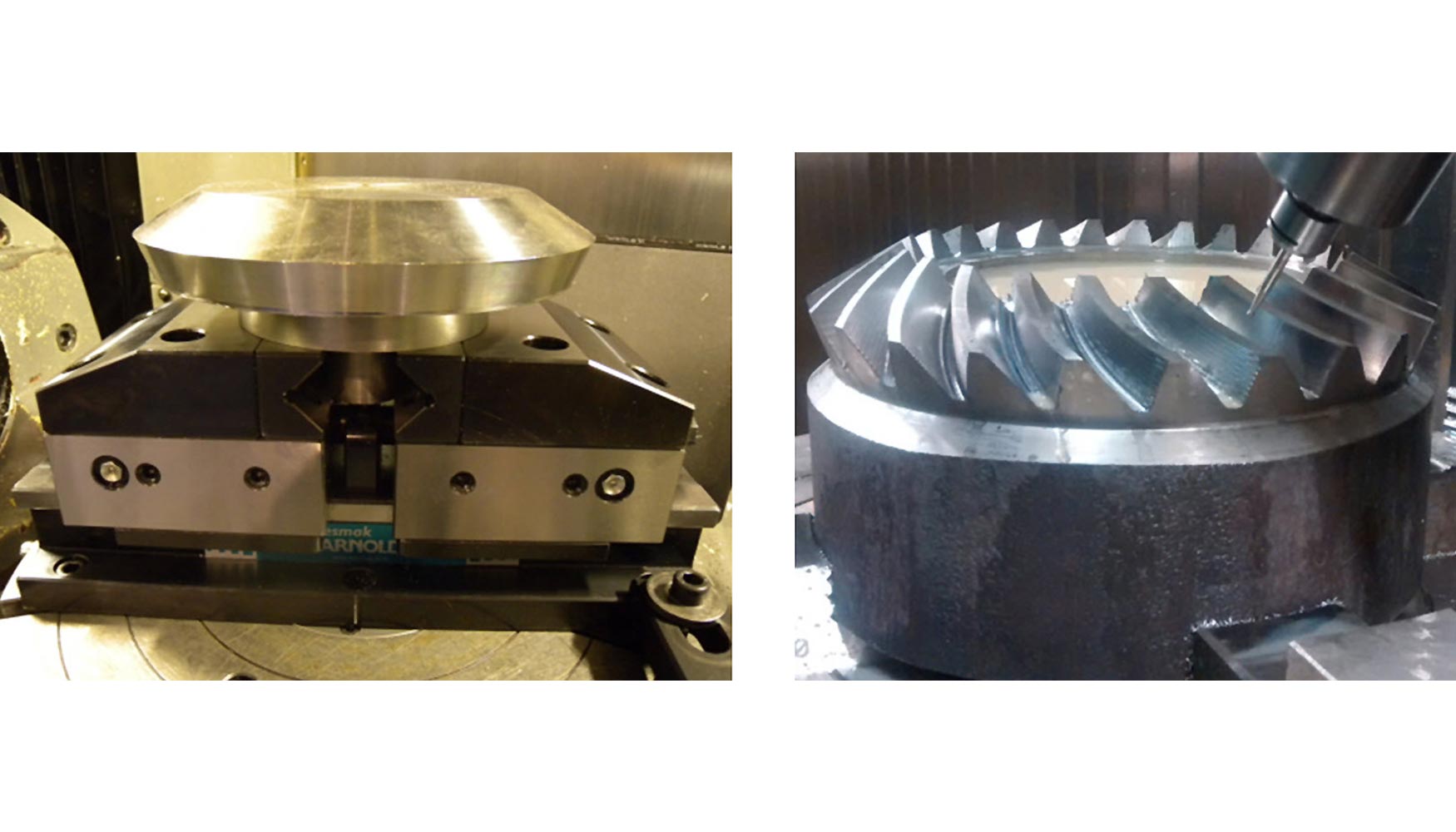
Figura 9. a) Sistema de amarre centro de mecanizado 5 ejes; b) Sistema de amarre máquina ‘multitasking’.
Al no precisarse de sistemas de amarre externos se evita una fuente de problemas y de incremento de plazos, debido a que el plazo de entrega del utillaje suele ser el mayor condicionante a la hora de establecer el plazo de entrega de nuevas piezas a un cliente.
- Menores tiempos improductivos. Menos máquinas, reducción de las puestas a punto y la eliminación de transferencia de piezas entre máquinas. Los movimientos en vacío quedan prácticamente eliminados. El transporte en fábrica pasa a ser no necesario debido a que la pieza se mantiene en la misma máquina. También se ven reducidos los riesgos, ya que en un cambio las máquinas tienen más riesgos de colisiones. Si los reducimos, ganamos en seguridad. En suma, se consigue una operación más limpia con un menor número de actividades que no aportan valor añadido al producto.
- Mejor utilización del personal. Si un operario lleva dos máquinas, y una de ellas es ‘multitasking’, en realidad es como si llevase 3 ó 4. El número de operarios se ve reducido al tiempo que lo hace el número de máquinas a utilizar.
- Ocupación de un menor espacio, que cada vez es más caro. El hecho de sustituir una serie de máquinas por una sola requiere una menor planta de taller. El espacio de trabajo generalmente se ve reducido a una simple configuración entre torretas, divisores y cabezales de mecanizado, que se mueven de una posición a otra en cuestión de segundos.
- Mejora de calidad por hacer las piezas en un sola atada. La calidad de la pieza mejora considerablemente ya que no está sometida a cambio de origen de referencia de cada programa de CNC. Toda la pieza se produce con un mismo cero de pieza. Esto permite abordar un mercado de piezas de mayor complejidad y valor.
- Reducción de gastos directos: El número de máquinas se puede reducir de cuatro a una y los utillajes de seis a uno.
- Reducción de gastos indirectos: El hecho de sustituir una serie de máquinas por una sola requiere menos planta de taller, se reduce el impacto ambiental y el movimiento de material por la planta es más eficiente.
- En definitiva, lo que se consigue es un mayor rendimiento de los sistemas productivos.
Como es lógico, las máquinas ‘multitasking’ precisan de una inversión inicial mayor que los centros convencionales de mecanizado 5 ejes, pero esta inversión es inferior a la necesaria para la adquisición de una máquina específica de generación, también conocidas como tecnologías tradicionales.
Además, estas tecnologías tradicionales presentan el hándicap de precisar herramientas especiales de características muy concretas. La figura 10 muestra alguna de estas herramientas especiales utilizadas en las tecnologías tradicionales de generación.
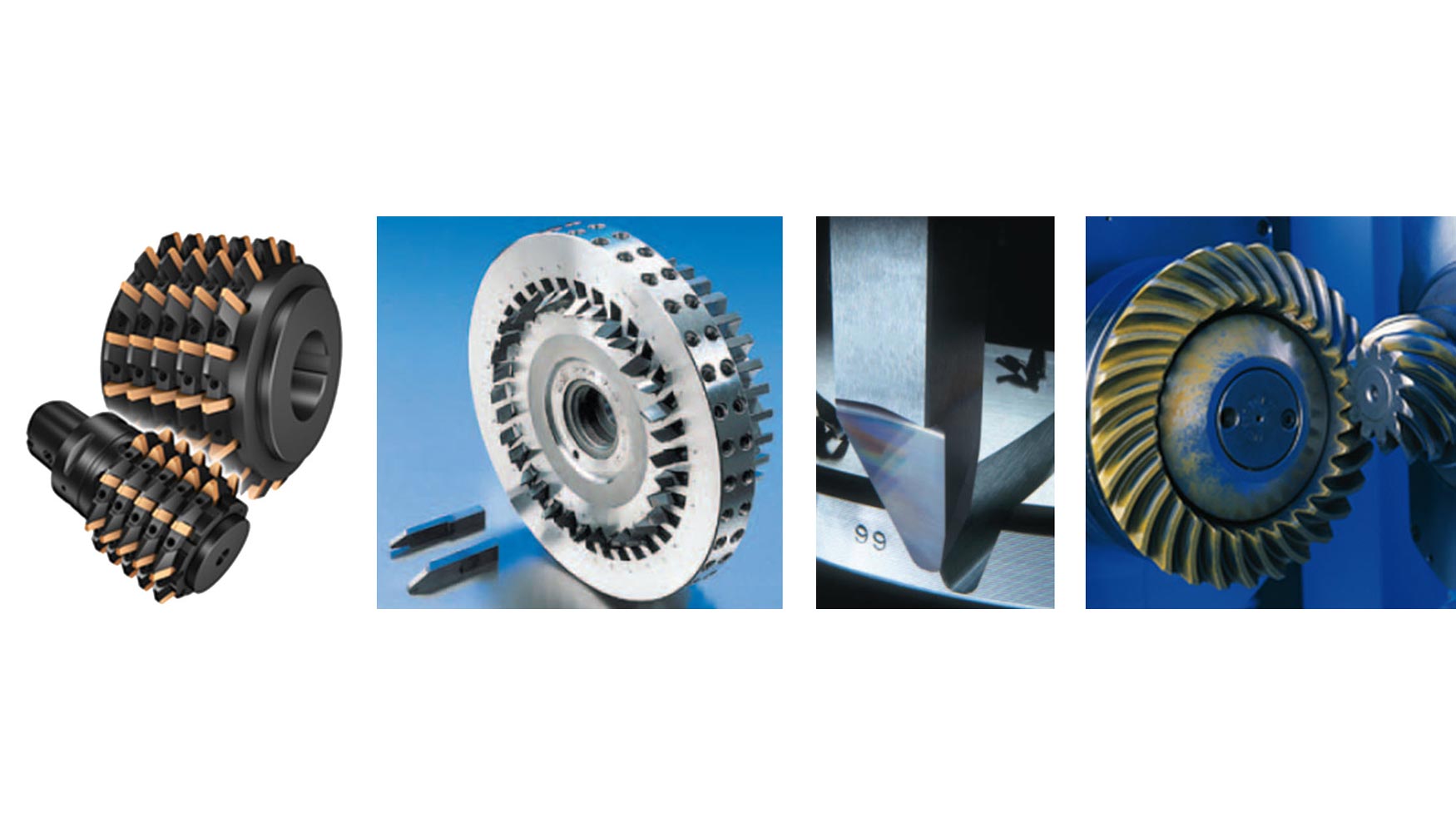
El reducido número de proveedores de esta clase de herramientas especiales en el mercado, además de la complejidad de las mismas, hacen que su coste sea bastante elevado, además de presentar abultados plazos de entrega. En lo que a herramientas se refiere, la utilización de las máquinas de propósito general para el mecanizado de engranajes conlleva ciertas ventajas. Este tipo de máquinas permiten la utilización tanto de herramientas estándar como de herramientas de las que consideramos especiales, como es el caso particular de las ‘fresas madre’ (‘hobs’).
La utilización de herramientas especiales en máquinas de propósito general precisa de un sistema rígido y el módulo de los mismos no debe ser superior a 6 debido a que las cargas generadas durante el proceso de generación del engranaje serían muy elevadas, viéndose afectada la calidad final de los mismos. Este tipo de herramientas, como ya se ha comentado anteriormente, llevan asociados abultados plazos de entrega, los cuales rondan de 8 a 12 semanas.
Por otro lado, la utilización de herramienta estándar presenta grandes beneficios. El elevado número de proveedores existentes en el mercado favorece la existencia de una mayor oferta del producto, consiguiéndose una reducción tanto del coste como de los plazos de entrega.
En la figura 11 se muestra el mecanizado de un engranaje en máquina de propósito general, tanto mediante el uso de una herramienta especial (‘hobbing’) como mediante el uso de una herramienta estándar.
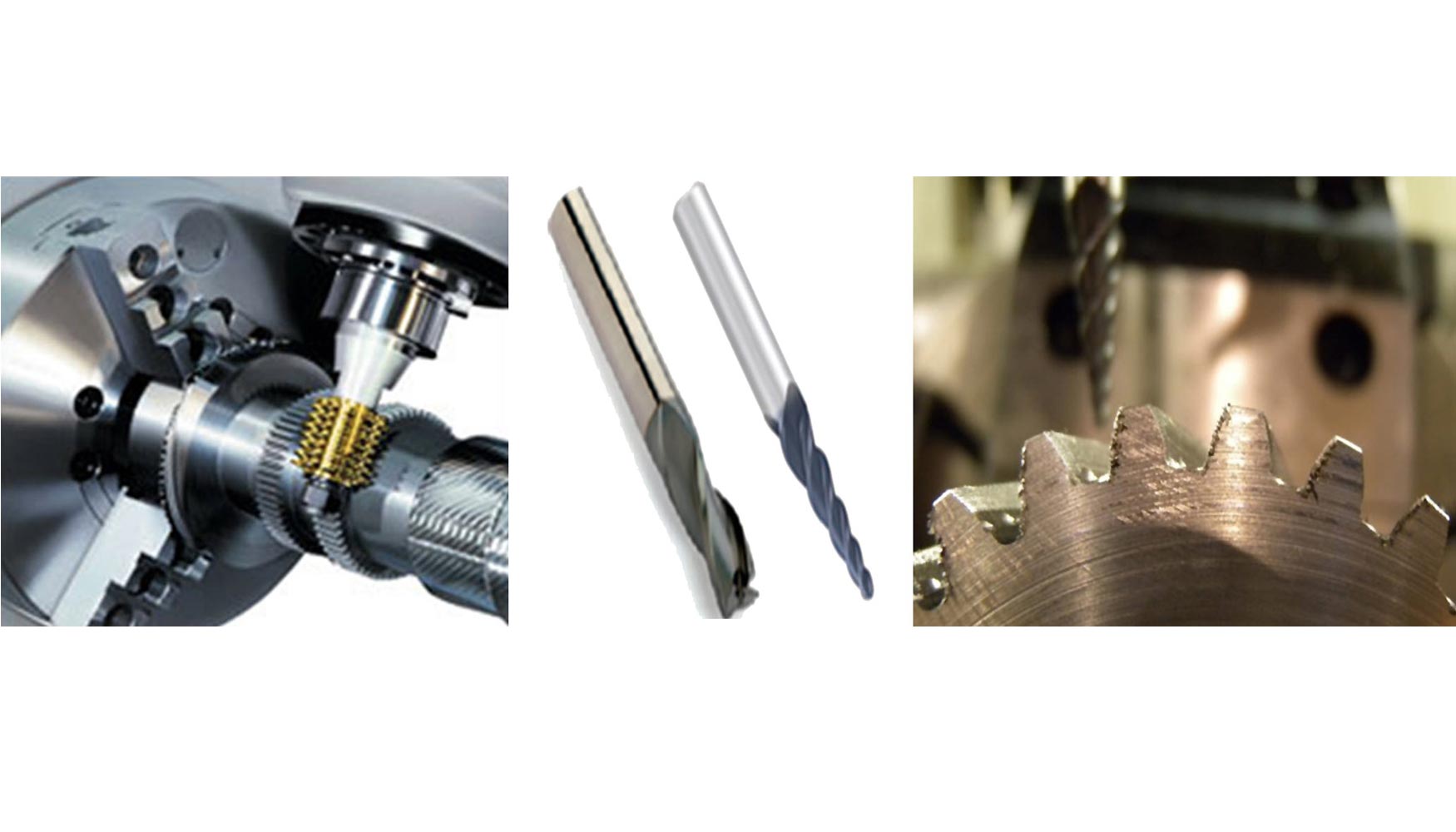
En los últimos años, en parte debido al volumen de mercado de estos componentes, que se estima en miles de millones por año, han surgido nuevas tecnologías en herramientas de fresado. Sandvik Coromant, empresa mundial en distribución de herramientas, ha desarrollado herramientas especiales tanto para el fresado de engranajes cilíndricos, tanto rectos como helicoidales, como para engranajes cónicos. Estas herramientas están diseñadas para ser utilizadas en máquinas de propósito general 5 ejes, independientemente del fabricante. Para el caso particular de los engranajes cilíndricos, Sandvik Coromant, con la colaboración del fabricante de máquina-herramienta DMG MORI, ha presentado InvoMilling. InvoMill utiliza herramienta frontal para interpolar la evolvente del diente del engranaje. El contacto entre el plano de la herramienta y la evolvente del diente es descrito por una línea. La trayectoria de la herramienta es radial, por lo general desde la cabeza a la raíz del diente. Por lo tanto, las principales variables del engranaje (módulo, ángulo de presión y ángulo de hélice) están determinadas por la trayectoria de la herramienta, no a la herramienta en sí, una característica generalmente asociada a herramientas de flanco o de boda, siendo diferente a lo que ocurre en los procesos de ‘hobbing’, ‘gashing’ o ‘shaping tools’.
A diferencia del proceso de fresado convencional, donde la calidad superficial depende de los parámetros de ap y ae, es decir, que si se incrementan estos valores la rugosidad superficial tiende a empeorar, para el caso de InvoMill no existe tal correlación. Esta nueva tecnología permite diferentes profundidades axiales, gracias a la existencia de herramientas con anchuras que van de 5 a 15 mm para la mayoría de los engranajes comunes que comprenden el rango de módulo 3-6, no viéndose así afectada la textura superficial debido a que el contacto entre el plano de la herramienta y la evolvente del diente es descrita por una línea, como ya se ha mencionado anteriormente.
En comparación con el fresado convencional, la limitación de los parámetros de mecanizado (ap y ae) pasa de 0,1 a 0,3 mm. Como resultado, la productividad de InvoMill puede ser de una magnitud de uno a dos órdenes mayor que con el fresado convencional. En la figura 12 se muestra, de manera gráfica y en 4 simples pasos, el proceso InvoMilling.
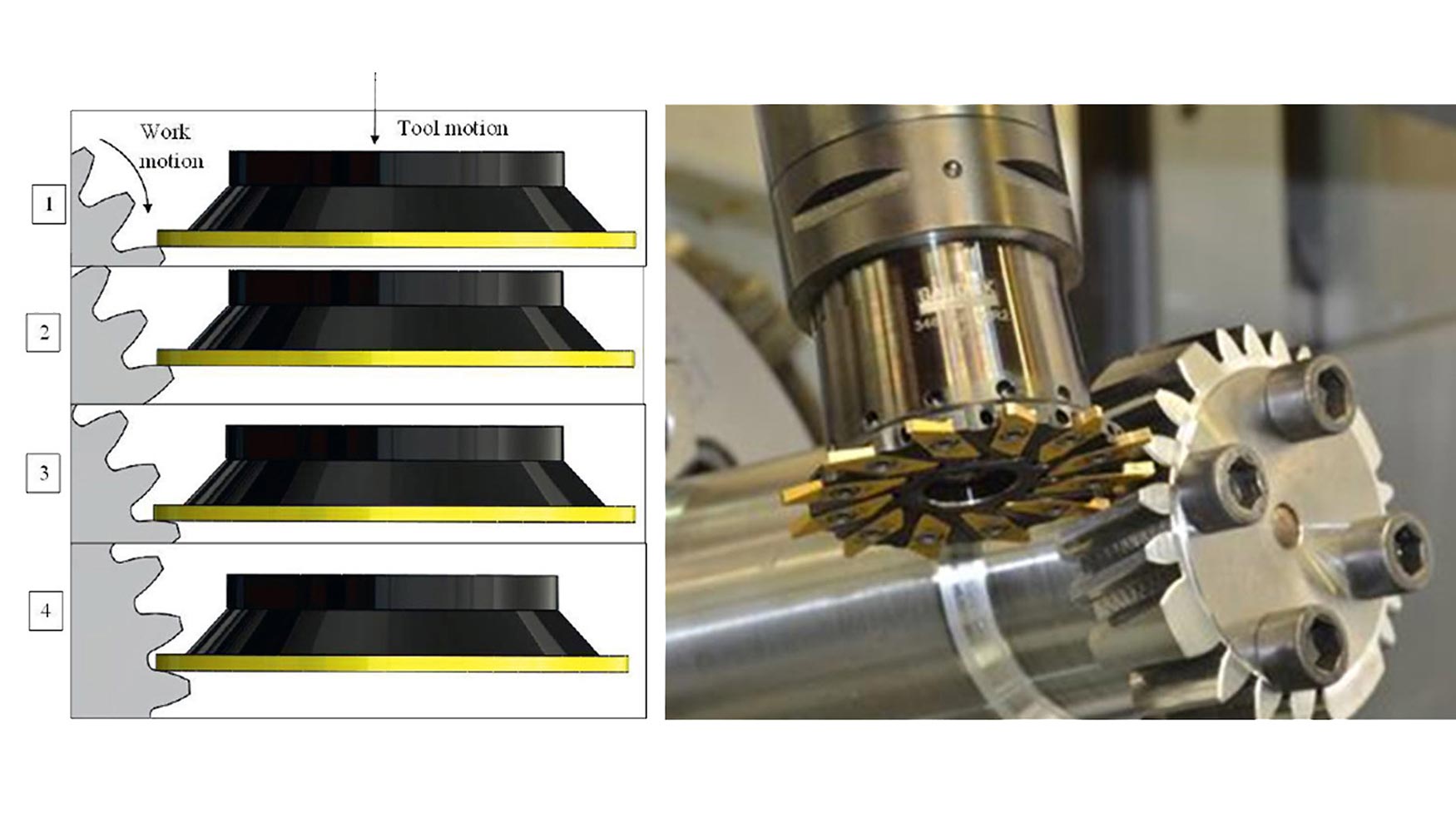
El proceso de InvoMill y el proceso de hobbing son procesos comparables porque ambos se utilizan principalmente para el mecanizado de engranajes cilíndricos. Se ha demostrado, utilizándose condiciones conservadoras en el mecanizado de engranajes del rango de módulo 3-6 para cada uno de los dos procesos, que InvoMill se vuelve más productivo que el proceso ‘double cut hobbing’ para engranajes de módulo 6. La misma tendencia se ha demostrado para módulos de tamaño superior a 6 y también para algunos módulos inferiores a 6.
Por otro lado, InvoMill comparte una restricción con el fresado convencional, que es la dificultad en la preparación de una trayectoria de la herramienta para el CNC. Las soluciones CAM tradicionales son inefectivas, igual que lo son los modelos sólidos de los perfiles de los engranajes existentes.
Este problema ha sido resuelto por el desarrollo de la superficie del engranaje basado en un modelo sólido generado por el software gearMILL de MORI. Este software permite la programación de los engranajes que carecen de modelos y de aquellos que han sido modelados de manera imperfecta.
Hasta el año 2014, debido a la colaboración previa entre Sandvik y DMG MORI en la obtención y continua mejora del producto InvoMilling, sólo las máquinas del fabricante DMG MORI disponían de licencia de exclusividad de utilización de este producto. En la actualidad, esta tecnología ya no presenta tal exclusividad, pudiéndose utilizar en cualquier máquina, independientemente del fabricante. Es por esta razón que Sandvik ha desarrollado su propio software, InvoMilling Software 1.0, el cual permite una programación CNC rápida y fácil del proceso InvoMilling patentado. Así, combinando el software con sus herramientas precisas de corte CoroMill 161 y CoroMill 162, se consigue una fabricación de engranajes realmente flexible. En la figura 13 se muestra un ejemplo de aplicación del InvoMilling Software.
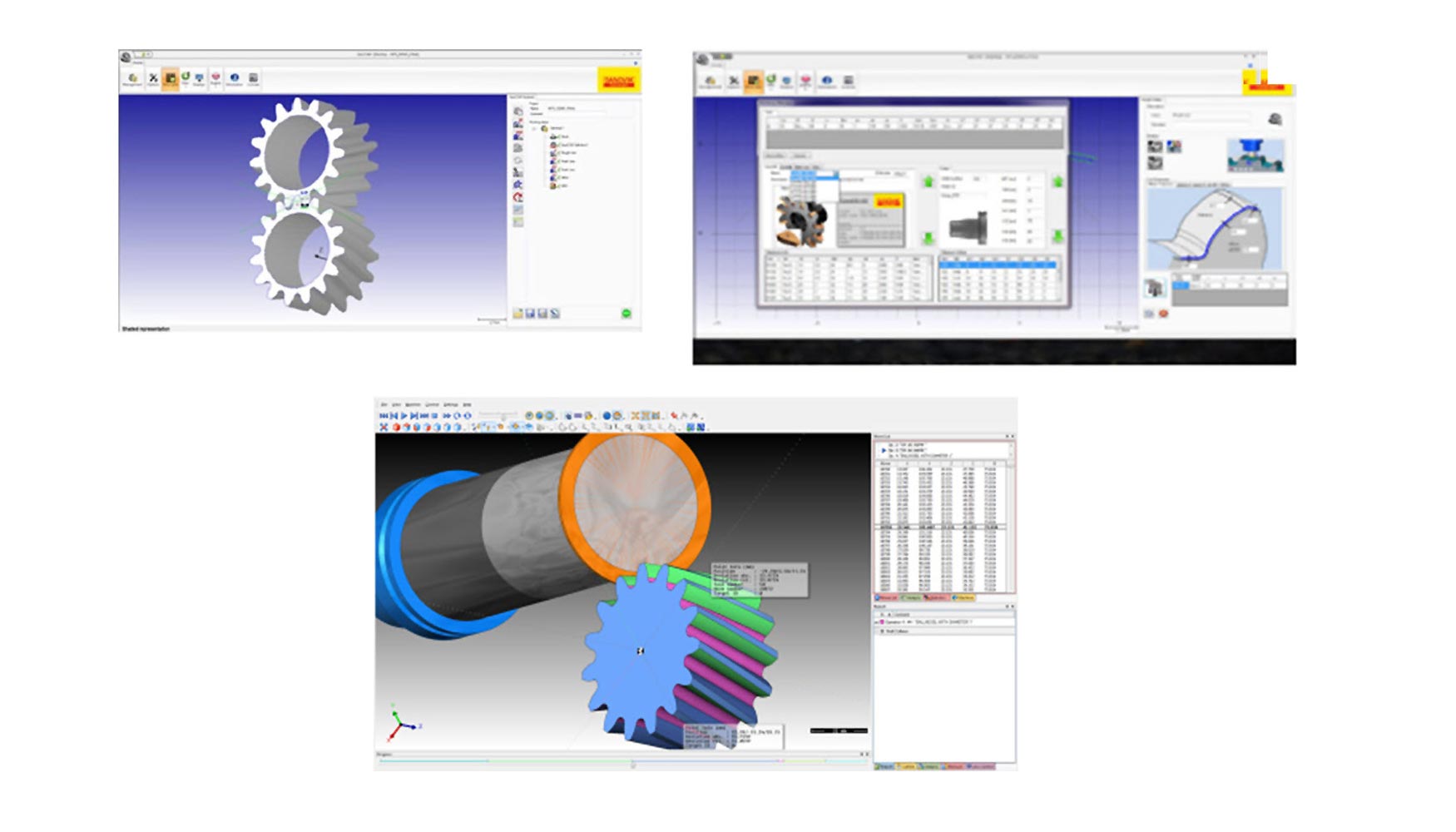
Los inconvenientes que presenta esta nueva tecnología frente al mecanizado con herramienta estándar se pueden resumir en los siguientes puntos:
- Permite realizar correcciones en el eje x, pero no otras correcciones como son el ‘crowning’ o el ‘tip relief’.
- Calidad obtenida asegurada DIN 6.
- Un único proveedor.
- Coste. El precio por licencia ronda los 45.000 €.
Para el caso del mecanizado de engranajes cónicos, Sandvik Coromant en colaboración con Gleason, líder mundial en ingeniería y tecnología del engranaje, y con el fabricante de máquina-herramienta Heller, ha desarrollado una herramienta especial, uP-Gear Technology. En la figura 14 se muestra un desbaste y un acabado realizado mediante esta tecnología.
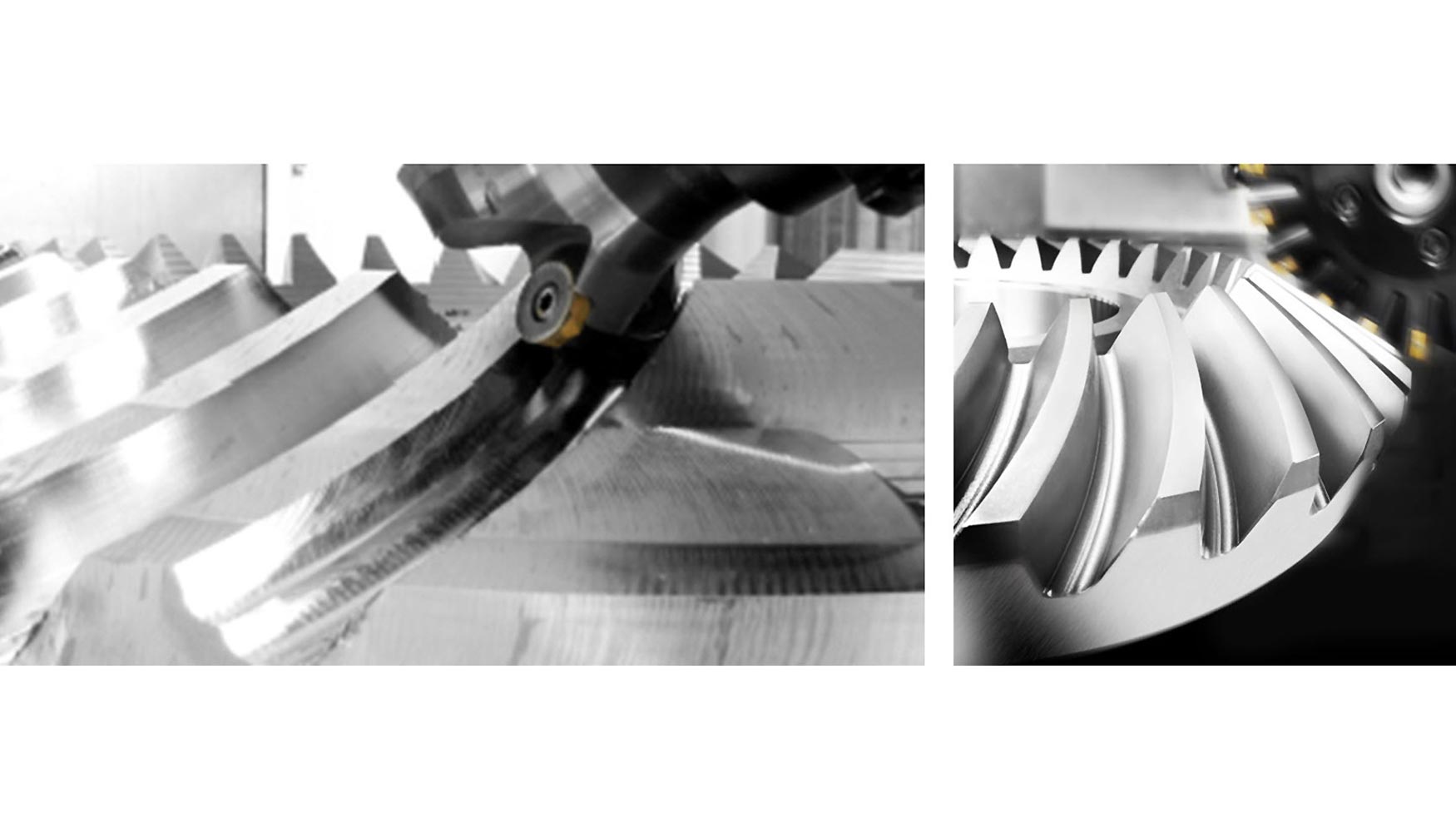
Una de las principales ventajas que presenta uP-Gear Technology es la reducción del tiempo de producción total. Al fabricar el componente en una misma máquina, se ahorra un tiempo considerable en comparación con el uso de una máquina de fabricación específica de engranajes cónicos al ser también necesario el uso de un centro de torneado. En comparación con el fresado convencional, uP-Gear Technology permite generar la geometría del diente terminado en menos de un tercio del tiempo. En la figura 15 se compara de manera visual las herramientas utilizadas en el fresado convencional frente a las utilizadas mediante uP-Gear Technology.
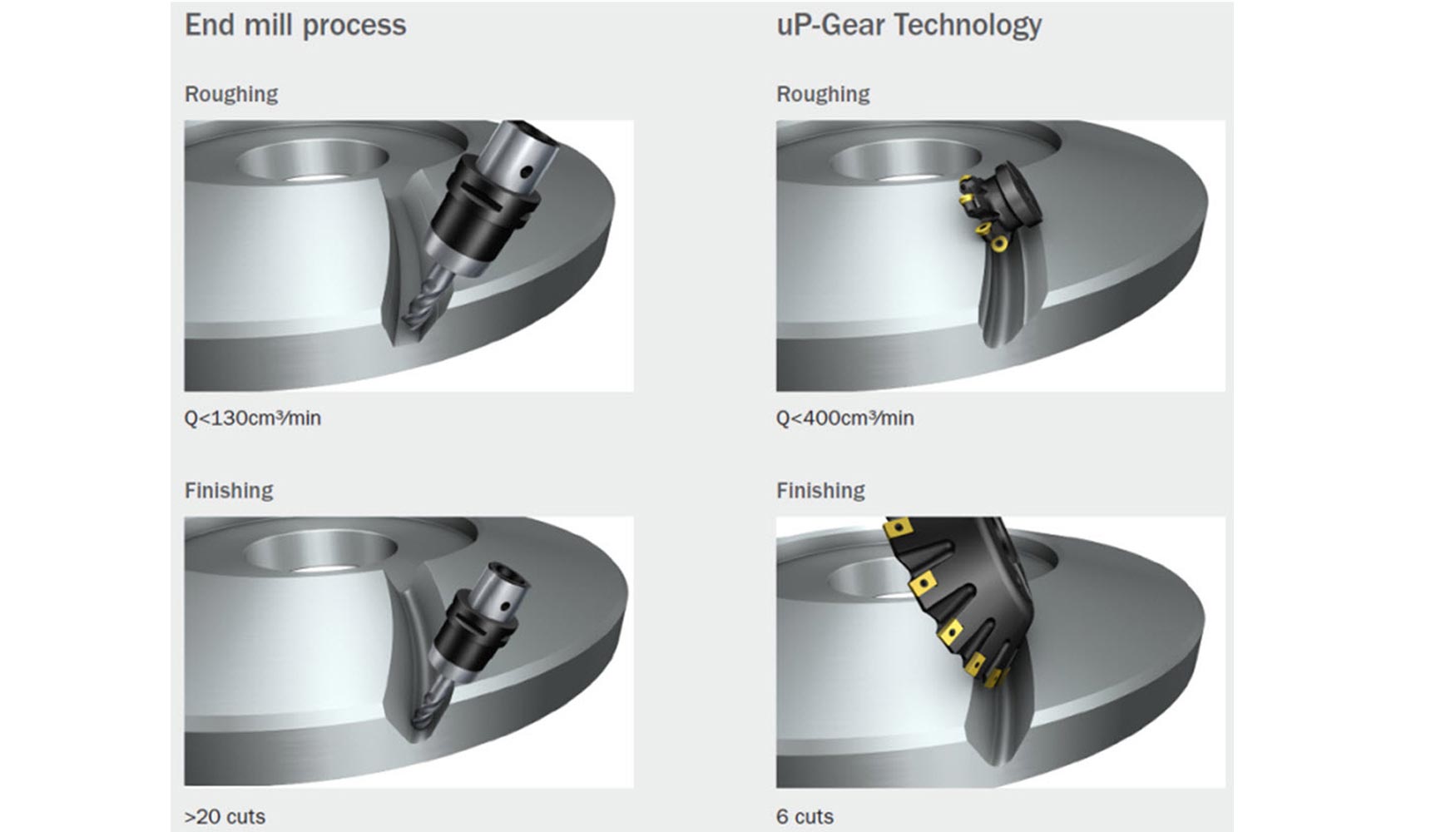
El conjunto de herramientas de alta precisión requeridas para el proceso uP-Gear Technology son usadas para el fresado de la geometría del diente del engranaje. Todas las herramientas están diseñadas para altas velocidades de eliminación de material, lo cual conduce a tiempos de ciclo muy cortos.
En vez de herramientas dedicadas y específicas, a menudo usadas en máquinas de engranajes cónicos, la tecnología uP-Gear nos permite utilizar herramientas y plaquitas estándares de fresado, las cuales ayudan a reducir los costes de las herramientas hasta en un 50%. Además, también es posible utilizar el mismo conjunto de herramientas para una gama diferente de perfiles de dientes y de tamaños.
La gama de herramientas de Sandvik Coromant para uP-Gear Technology han sido diseñadas para tres operaciones principalmente: obertura de la ranura del diente, mecanizado de la protuberancia y el acabado de los flancos de los dientes. Todas las herramientas se han optimizado para el mecanizado del engranaje antes y después del tratamiento térmico.
El tipo y el número de herramientas para el proceso de uP-Gear Technology dependen tanto del módulo del engranaje como de la estrategia de mecanizado seleccionada.
Como ya se ha comentado, esta tecnología nace tras una colaboración entre Sandvik, Heller y Gleason, líderes cada uno de ellos en un determinado sector. En un principio, y mientras no se rompa el acuerdo, hasta inicios del 2016 su licencia de exclusividad pertenece a Heller, siendo las máquinas de este fabricante las únicas en las que se puede mecanizar con uP-Gear Technology de Sandvik.
Para finalizar este estudio, comentar que el uso de máquinas de propósito general, ya sea un centro de mecanizado 5 ejes o una máquina ‘multitasking’, permite la implantación de nuevas tecnologías, hasta ahora nunca antes evaluadas, en el mecanizado de esta clase de componentes. El grupo de Fabricación de Alto Rendimiento, perteneciente al Dpto. de Ingeniería Mecánica de la UPV/EHU, está estudiando la viabilidad de una nueva tecnología para el acabado de engranajes, como es la turbina de aire.
La razón principal por la que esta nueva tecnología de mecanizado ha sido evaluada, es porque es fácilmente integrable en cualquier máquina CNC, y puede presentar una mejora en el proceso de mecanizado de engranajes en máquinas de propósito general. La turbina de aire, debido a su alta velocidad y par constante (~40.000 rpm), va a permitir la evaluación de diferentes herramientas de acabado con el fin de obtener una mayor calidad de la superficie final del diente. Han sido evaluadas muelas de CBN de diferentes diámetros y fresas ‘multidiente’ esféricas de metal duro. La figura 16 muestra la turbina de aire, las herramientas especiales utilizadas en la misma, y una fotografía del mecanizado realizado en uno de los engranajes realizados por el grupo de investigación anteriormente mencionado.
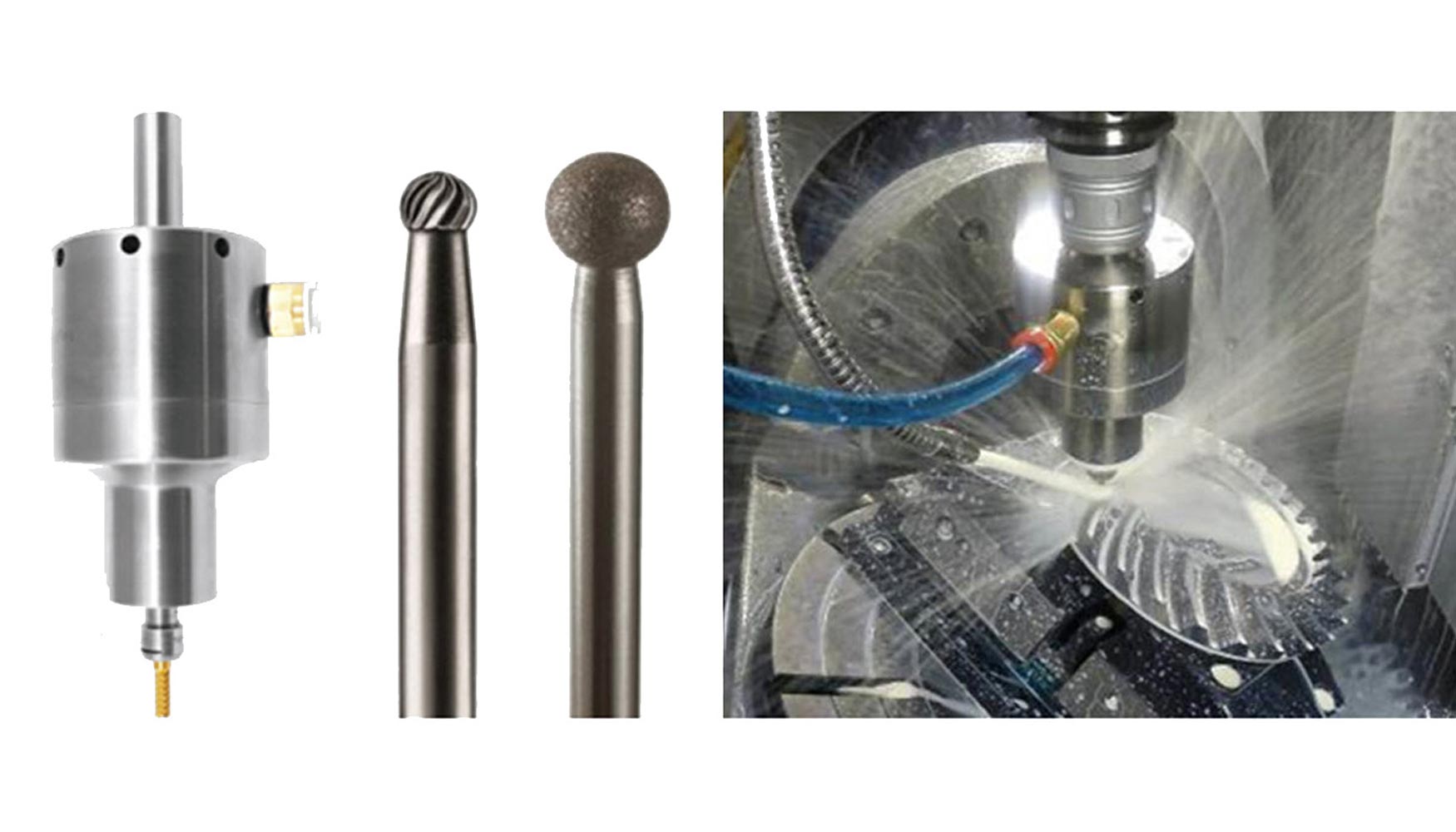
Como resumen, se puede afirmar que el mecanizado de engranajes en máquina de propósito general y con herramienta estándar se presenta como una opción totalmente factible y ventajosa respecto a las tecnologías tradicionales cuando se pretende obtener un ‘producto único’. Se conoce como producto único a aquel que precisa de una elevada flexibilidad en el proceso, ya sea en término de geometría o de tamaño, y del cual se precisa un número muy limitado de unidades.
Como ya se ha comentado, la fabricación de engranajes en máquina de propósito general está en una continua evolución, presentándose nuevos productos en el mercado con una cierta asiduidad.
Grupo de Fabricación de Alto Rendimiento de la UPV/EHU, cantera de talento
El mecanizado multieje de componentes complejos como son los engranajes espirocónicos, los impellers y los blisks, entre muchos otros, precisan de un amplio conocimiento del proceso, basado en una formación avanzada, y de una cierta experiencia previa. El mecanizado de este tipo de componentes, y más aún cuando se realiza en materiales de baja maquinabilidad (Inconel, Titanio, Waspalloy...), es un proceso de requisitos tecnológicos elevados. Para cumplir con éxito y generar pieza buena a la primera, es necesario tener un amplio conocimiento de los fundamentos del mecanizado así como de otras áreas de conocimiento, entre las que cabe destacar la tribología, el análisis de vibraciones, la programación de trayectorias óptimas, la monitorización de esfuerzos y la integridad superficial.
El Grupo de Fabricación de Alto Rendimiento, perteneciente al Departamento de Ingeniería Mecánica de la Universidad del País Vasco (UPV/EHU), se presenta como el nexo de unión ideal entre la universidad, fuente continua de conocimiento, y el entorno empresarial. Este Grupo, que se nutre anualmente de alumnos de último año de Ingeniería Industrial, Aula de Máquina-Herramienta, Grado, Másteres de Mecánica y otros, permite la formación continua de nuevos talentos en los diferentes procesos de fabricación. Gracias a la convivencia de alumnos, doctorandos, personal investigador contratado y personal docente, se genera un ambiente enriquecedor que facilita la adquisición de conocimiento día tras día, compaginándose aptitudes científicas e industriales. De esta forma, la gente de mayor antigüedad y de mayor experiencia se responsabiliza de que los nuevos integrantes del Grupo adquieran el conocimiento necesario para controlar cada una de las distintas tecnologías.
Las empresas del entorno son las primeras en ser conscientes y valorar la formación adicional que aporta la integración en el Aula de Máquina-Herramienta y en el Grupo de Fabricación de Alto Rendimiento, dando lugar, en muchas ocasiones, a contratos de cooperación educativa e integración de los recién titulados en la plantilla de las distintas empresas.
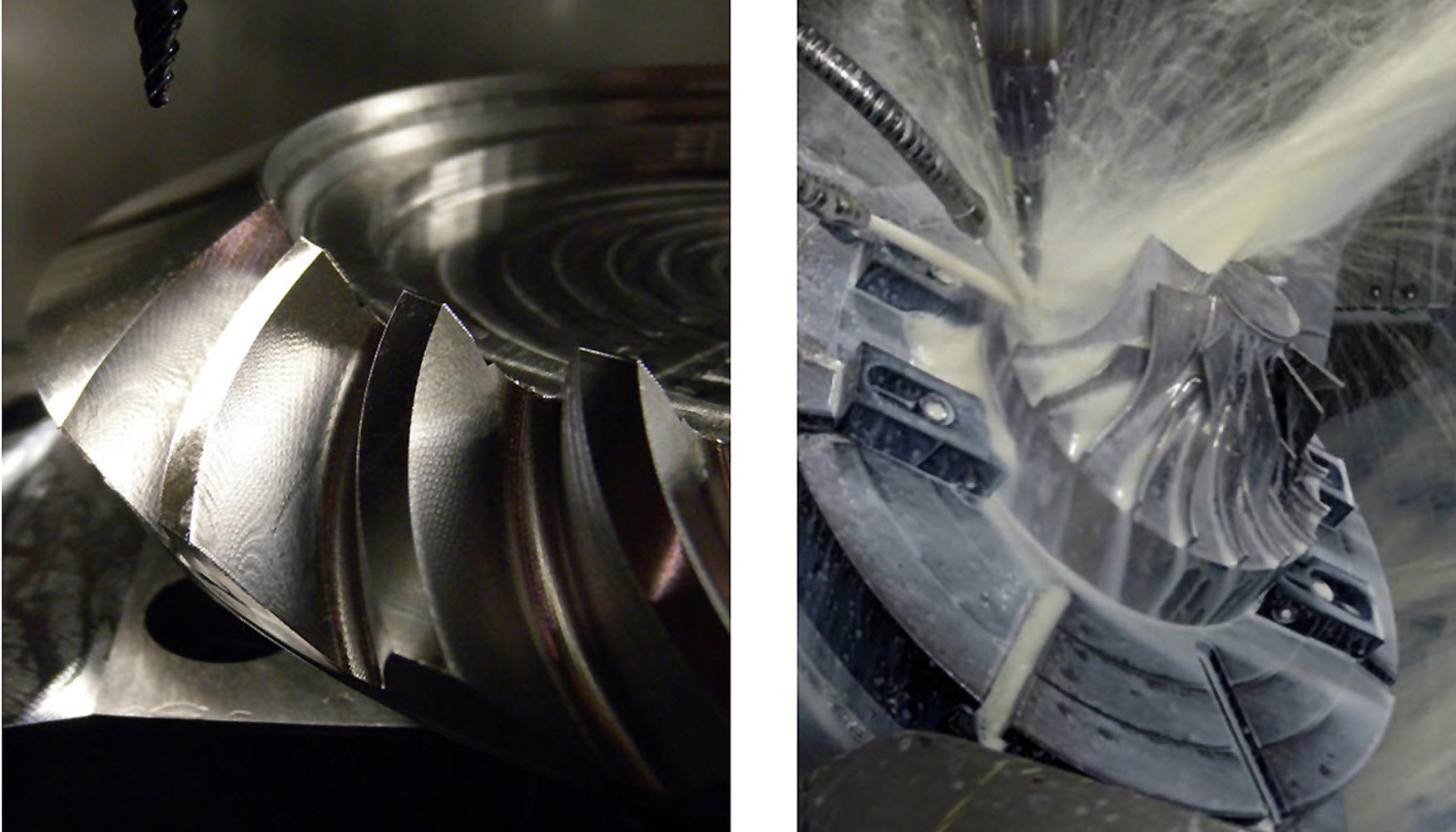