Incremento de la disponibilidad de máquina a través del diagnóstico de la condición de rodamientos
Entre los requerimientos de los fabricantes de máquina-herramienta siempre encontramos el incremento de la productividad, del rendimiento y la fiabilidad de las máquinas. Garantizar una mayor disponibilidad de máquina es posible mediante la monitorización del estado de los componentes más críticos. La experiencia de Schaeffler tanto en el desarrollo de componentes y soluciones específicos para la máquina-herramienta, en sistemas de condition monitoring para procesos continuos, en ingeniería de aplicaciones y la propia experiencia como usuarios finales de máquinas-herramienta, nos ha permitido adentrarnos en la monitorización de aplicaciones de máquina-herramienta. Esta estrategia de mantenimiento permite identificar los daños incipientes en aplicaciones de máquina-herramienta, en un estado temprano. Ello permite sustituir, por ejemplo, los componentes dañados durante una parada programada. Se evitan las paradas no planificadas, disminuyendo los costes de operación. Esta ponencia se centra en los sistemas y las estrategias de monitorización relevantes en aplicaciones de máquina-herramienta, teniendo en cuenta las causas de los fallos y sus consecuencias, demostrando su potencial con ejemplos prácticos.
1. Motivación y enfoque
Las necesidades relacionadas con el rendimiento y la fiabilidad de las máquinas-herramienta siguen en aumento ante el contexto de la situación de competencia en el sector de las máquinas-herramienta. Además de adoptar medidas constructivas para conseguir su optimización, la aplicación de sistemas de diagnóstico para monitorizar los componentes durante el funcionamiento gana en relevancia.
En el presente artículo, el concepto de monitorización del estado o condition monitoring comprende el registro del estado de los componentes críticos de la máquina-herramienta, de manera continua o a intervalos regulares, para medir unas variables significativas. Para ello se registran las vibraciones que suele generar el ruido propagado por la estructura mediante la instalación posterior de sensores (sensores externos). Normalmente se emplean sensores de aceleración piezoeléctricos. En el análisis posterior de señales, trata de localizar la señal útil que es iniciada por el componente a monitorizar y extraerla de la señal restante. La tarea principal consiste en detectar, desde el punto de vista técnico, los daños o cambios en los componentes
1.1 Estrategias de monitorización
La monitorización del rodamiento debe basarse en una estrategia eficiente. Es importante definir claramente los objetivos y el valor añadido que se pretende durante la fase de preparación.
Los objetivos adecuados podrían ser:
- Control de calidad
- Registro de datos de medición (historial durante el período de garantía)
- Prevención y limitación de daños (evitar el fallo total y los daños secuenciales)
- Mantenimiento orientado al estado (reducir los costes de mantenimiento y aumentar el ciclo de vida).
Ante todo, debemos distinguir si se trata de una modificación o un daño que se agrava continuamente o si cabe esperar un fallo espontáneo del rodamiento. Este es un aspecto importante a tener en cuenta, sobre todo en velocidades elevadas, y requiere un análisis muy preciso. Asimismo, las propiedades de la aplicación y/o del rodamiento montado desempeñan un papel importante en el sistema de monitorización. En función de las mismas deberán incluirse la selección y la posición de los sensores, los límites de alarma y las interfaces con la unidad de mando de la máquina. Tras haber definido los objetivos y considerado el comportamiento de fallo del rodamiento, debe planificarse el registro de los valores medidos. De ello se deriva la selección del sistema correcto de monitorización.
1.2 Objetivos de los usuarios de condition monitoring
Para definir los beneficios de las soluciones de condition monitoring, parece indicado distinguir entre los diferentes usuarios del sistema: Aumentar la disponibilidad técnica y garantizar la calidad de los productos acabados, especialmente en la producción, son objetivos importantes para los usuarios finales (MRO). En cambio, el objetivo principal de la organización de mantenimiento consiste en reducir los costes de mantenimiento y del ciclo de vida (costes durante la fase de servicio).
Los fabricantes de maquinaria (OEM) deben facilitar cada vez con mayor frecuencia modelos operativos para poder adoptar la decisión sobre la inversión en base a los costes del ciclo de vida de un equipo. Los sistemas de condition monitoring ayudan a definir mejor los costes del ciclo de vida. Apoyan al fabricante durante el período de garantía en relación con las posibles optimizaciones constructivas necesarias.
Componentes de una máquina-herramienta: las máquinas-herramienta contienen una gran cantidad de puntos de apoyo que deben cumplir diversos requerimientos. Para garantizar la calidad de guiado, se utilizan elementos lineales y rotativos de precisión. A continuación, trataremos exclusivamente los sistemas de monitorización en el ámbito rotativo.
1.4 Evaluación de los componentes
Puesto que por motivos económicos no siempre tiene sentido realizar un diagnóstico amplio de todos los componentes individuales, recomendamos llevar a cabo una evaluación de los componentes en forma de matriz de riesgos. En ella se pueden considerar los riesgos de fallo (prioridad del equipo) y el alcance de los daños como parámetros relevantes. Como último paso, se debe valorar la aplicación de los sistemas de condition monitoring tomando en consideración los aspectos técnicos.
2. La duración del servicio de los rodamientos
1.1 Causas del fallo
Los rodamientos suelen tener una duración de vida útil calculada. Este cálculo se basa, por ejemplo, en la cantidad de acciones de los elementos rodantes y la carga. Las reflexiones del presente artículo se basan generalmente en los daños de las pistas de rodadura de los anillos exterior e interior, así como en el elemento rodante. La mayoría de los daños son ocasionados por influencias externas. Los daños por defectos de material y/o por fatiga son menos frecuentes.
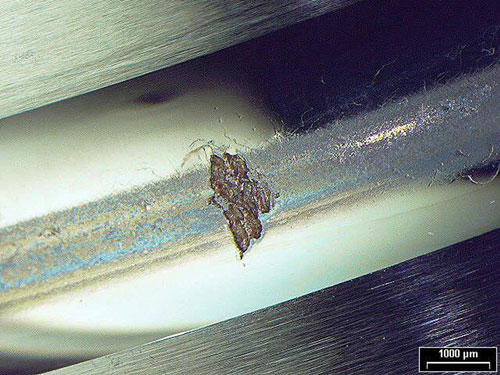
2.2 Indicaciones que apuntan a daños en el rodamiento
Los daños en los rodamientos se manifiestan de diferentes formas. Pueden producirse diversas anomalías en función de las condiciones de servicio. Se suele detectar una variación de la precisión de trabajo que se refleja en una calidad deficiente de la superficie y/o unos valores insuficientes de forma y medición. Los cambios o las curvas de temperatura son indicadores importantes de la variación del estado del rodamiento. Los daños locales y el desgaste de las pistas de rodadura y los elementos rodantes ocasionan unos ruidos de funcionamiento.
3. Parámetros de monitorización
Todas las variables de medición que se puedan asignar claramente a cambios del estado de los componentes son candidatas para convertirse en parámetros de monitorización.
Los requerimientos que deben cumplir las mediciones son, sobre todo, una elevada fiabilidad, un elevado valor informativo y la posibilidad de registrar los valores durante el funcionamiento. El momento de rozamiento del rodamiento depende del tipo, la velocidad y la carga. Además, en los rodamientos lubricados con grasa reacciona con especial sensibilidad según el tipo y estado de lubricación. No es fácil medirlo durante el funcionamiento. Una medida para el momento de rozamiento, por ejemplo, es el período de marcha en inercia de un cabezal que se puede determinar mediante un ensayo de marcha en inercia. La precarga variable y una inclinación no admisible influyen en el período de marcha en inercia.
Las curvas de temperatura permiten ilustrar muy bien el comportamiento en servicio de los rodamientos. Para ello se suele medir la temperatura del anillo estacionario. Los criterios de evaluación son el cambio de tiempo y el valor de temperatura en comparación con la temperatura del soporte. Se recomienda registrar la curva de temperatura, para lo que se deben realizar mediciones continuas.
4. El análisis del ruido propagado por la estructura y la generación de ruido en los rodamientos
Las vibraciones de la estructura suelen registrarse mediante sensores externos. Para ello, el dispositivo que registra los valores se monta en el exterior de la carcasa (estructura).
El sensor debería estar fijamente unido a la estructura y su posición debe estar lo más cerca posible del componente a monitorizar, en este caso el rodamiento. Debe observarse detalladamente el comportamiento de transmisión de la estructura. Los valores característicos y las curvas de los mismos permiten detectar con antelación el desgaste y los daños locales.
El objetivo consiste en detectar los daños, justo cuando estén en la fase incipiente. El reto principal es extraer la señal útil iniciada por el componente defectuoso del resto de señales. El ruido propagado por las estructuras sólidas puede ser generado desde el exterior o por el mismo rodamiento. Las deformaciones elásticas, los efectos del rozamiento y las influencias del lubricante se consideran causas de las vibraciones y se pueden definir como vibraciones específicas del rodamiento.
Para que la señal del ruido propagado por las estructuras sólidas presente una modificación adicional, debe haber una variación en las pistas de rodadura de los anillos interior o exterior y/o en los elementos rodantes. Dicha variación se puede producir debido al desgaste o a daños locales. La curva de los valores característicos permite, mediante el análisis selectivo de frecuencias, detectar con antelación los daños y asignarlos a los diferentes componentes del rodamiento
4.1 El laminado de las superficies modificadas localmente
El laminado de daños locales genera los impulsos de choque, que se pueden registrar como secuencias de impulsos de choque mediante medición. Los métodos de análisis permiten separar estas secuencias de otras fuentes de vibraciones. A continuación, el análisis de las señales permite asignar los esquemas de secuencia generados a los componentes dañados correspondientes. Para detectar el desgaste, se calculan los valores característicos en el espectro de frecuencias (Fig.2) o a partir de la señal temporal. El valor característico puede, por ejemplo, representar la energía de las vibraciones.
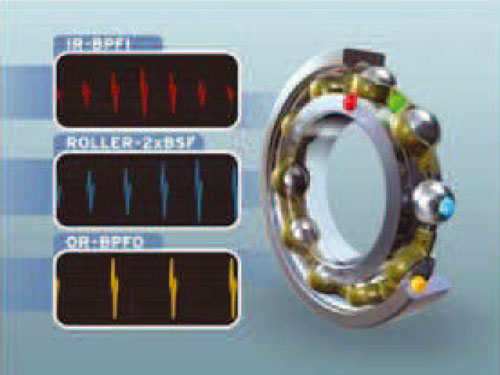
Para diseñar un sistema eficiente de monitorización se puede combinar el análisis de los valores característicos con el análisis selectivo de frecuencias. Un software especial de análisis de Schaeffler apoya al usuario en el análisis.
4.2 Impulsos de choque - frecuencias de defectos
El laminado de los daños locales en las pistas de rodadura de los anillos interior o exterior, o también en los elementos rodantes, genera un impulso de choque y/o una secuencia de impulsos de choque. A esta incidencia que se produce a intervalos equidistantes de tiempo se le puede asignar una frecuencia definida. De ello se derivan unas frecuencias específicas de laminado o defecto en función de los datos geométricos del rodamiento. Éstas pueden determinarse para cada componente del rodamiento, y resultan del movimiento relativo del anillo estacionario y el anillo en rotación, pero también de la rotación propia del elemento rodante. Estos esquemas de frecuencia sólo aparecen en el espectro en caso de daños. Dependen de la velocidad de la aplicación correspondiente.
4.3 Herramienta de análisis
Los software de análisis, como por ejemplo el Trendline de Schaeffler se basan en una base de datos para rodamientos estándar. Tras la selección de la referencia del rodamiento y la introducción de la velocidad, el software calcula automáticamente las características de diagnóstico en profundidad.
5. Sistemas de Condition Monitoring
En el ámbito de los dispositivos de condition monitoring podemos encontrar aparatos offline o de monitorización periódica y aparatos online o de monitorización en continuo.
La elección del sistema de condition monitoring se realizará en función de las características de la máquina y del proceso de acuerdo a la estrategia predictiva escogida.
6. Casos prácticos
Caso 1: Banco de ensayo para cabezales principales.
Motivación: Control de calidad/Mediciones de referencia
Sistema: Registro manual de los valores medidos
Los valores de medición se registran en unas posiciones previamente definidas durante la puesta en funcionamiento de la máquina. En caso necesario, estos datos sirven de referencia para poder valorar el estado de un componente mediante unos valores comparativos. Gracias a la posibilidad de realizar un diagnóstico en profundidad y7o un análisis de frecuencias (Fig. 4 y 5) es posible detectar los daños en los componentes efectuando mediciones individuales. El método sirve para controlar la calidad.
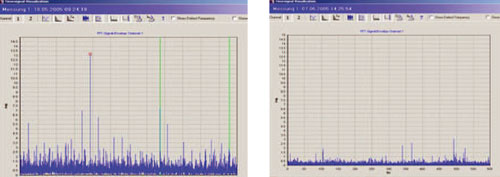
Fig. 3: Espectro de frecuencias de un husillo con comportamiento irregular. Fig. 4: Espectro de frecuencias después de reemplazar el rodamiento.
Caso 2: Monitorización continua de un cabezal principal
Motivación: Mantenimiento orientado al estado y garantía de calidad del producto final
Sistema: Registro automático de los valores medidos mediante sensores fijos
Los sensores se montan de forma permanente en las posiciones previamente definidas. El registro automático de los valores medidos se realiza durante las fases de marcha sin carga, no durante el proceso. Ello permite detectar con seguridad los daños de los componentes. El intercambio de datos y/o acceso a los sistemas locales de monitorización se realiza a través de la red interna de la empresa.
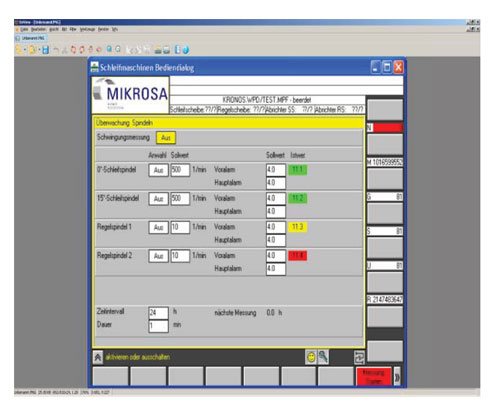
Fig. 5: Monitorización a través de la propia red de la empresa.
Para monitorizar con fiabilidad se deben de cumplir las siguientes condiciones:
- Registrar los datos únicamente durante la marcha sin carga
- Definir previamente los rangos de velocidad para la medición
- Durante el registro de los valores, las velocidades deben ser constantes.
La unidad de mando de la máquina facilita las señales necesarias, como la información sobre la velocidad y la señal de validación, a través de las interfaces. En caso necesario, se puede realizar una medición manual fuera del intervalo definido. El sistema dispone de una superficie de usuario para poder introducir los valores medidos. Se pueden ajustar los parámetros según necesidad.
Parámetros ajustables:
- Velocidad
- Intervalo de tiempo
- Duración de la medición y/o marcha sin carga
- Ajuste de los valores límite de alarma para el análisis de los valores característicos
7. Conclusiones
Los sistemas de condition monitoring juegan un papel fundamental en el incremento de la productividad y reducción de TCO de las maquinas herramientas actuales. Hasta la fecha estos sistemas han sido desarrollados principalmente para los procesos continuos de industria pesada como son papel, acero y cemento.
En el sector de la máquina-herramienta las variables de proceso y requerimientos son muy diversos. El conocimiento profundo de los diversos componentes y sistemas que integran la misma, y el estado de cargas de la misma a través de una experimentada ingeniera de aplicación es uno de los factores clave de éxito para la implementación de un sistema de condition monitoring.
Una combinación adecuada de un sistema de monitorización y una estrategia de vigilancia son claves para el éxito de un programa predictivo, orientado principalmente hacia la disponibilidad, fiabilidad y el ahorro de los costes del ciclo de vida (TCO).
El conocimiento de las necesidades de la aplicación y la experiencia en condition monitoring adquirida en procesos continuos nos permite definir la estrategia de condition monitoring y el sistema de monitorización más adecuado.
BibliografÍa
/1/ Dr. S.J. Lacey; The Role of Vibration Monitoring in Predictive Maintenance
/2/ Dr. M. Voll; Bearing Monitoring During Operation
/3/ Schaeffler KG; Publication nº TPI 214; Machinery monitoring for every machine