Inspección mediante tomografía computerizada con rayos X de componentes fabricados aditivamente
En el proceso de la fabricación aditiva de piezas metálicas, los defectos interiores indeseados, como la porosidad y las grietas, se pueden formar debido a parámetros de procesamiento subóptimos o insuficientes, baja calidad del material de almacenamiento de alimentación o efectos medioambientales [1-3]. Los componentes estructurales de misión crítica requieren inspecciones minuciosas para defectos y precisiones dimensionales. La tomografía computerizada con rayos X (XCT en inglés) —basada en la inspección— está llegando a ser una opción viable para diversas industrias de fabricación. La tomografía computerizada con rayos X muestra una clara estructura interna tridimensional (3D) de la pieza en inspección. Se ha utilizado popularmente para entender la estructura y el comportamiento de los materiales [p. e., 4, 5]. Como la técnica se aplica a la configuración de inspección industrial, se deben establecer las directrices antes de la aceptación generalizada de la técnica.
Para establecer la tomografía computerizada con rayos X como una herramienta de evaluación fiable, no destructiva para las inspecciones de los componentes críticos a la fractura, es importante determinar la detectabilidad de la referencia de los tipos y tamaños de defectos de la fabricación aditiva utilizando la tomografía computerizada con rayos X. La probabilidad de detección (PoD en inglés) es una medida utilizada para determinar la capacidad de una técnica de evaluación no destructiva (NDE en inglés). Todavía hay aspectos indeterminados de probabilidad de detección (PoD en inglés) y tamaño mínimo de fallos detectables para los fallos típicos encontrados en las piezas producidas con fabricación aditiva utilizando la tomografía computerizada con rayos X. Solamente se han publicado hasta la fecha un puñado de documentos relacionados con este tema [6]. Uno de los pasos críticos a la hora de evaluar las técnicas de inspección no destructivas incluyendo la tomografía computerizada con rayos X será la capacidad de probar piezas con fallos simulados colocados de manera intencionada dentro de las piezas producidas por fabricación aditiva. Los artefactos fiables con características internas que son representativas de los defectos que se producen en la fabricación aditiva necesitan ser desarrollados. Sin embargo, construir una estructura interna es difícil con cualquier técnica convencional. Por otro lado, la fabricación aditiva, proporciona una oportunidad para incorporar estructuras internas complejas.
En este documento, se presenta tanto un enfoque para construir características internas utilizando la fabricación aditiva como para inspeccionar los resultados utilizando la tomografía computerizada con rayos X. Se construyeron tres piezas de pruebas que incorporaban características internas diferentes por medio de un proceso de fusión de polvo (PBF en inglés) basado en láser. Las calidades de estas construcciones se determinaron a partir de las digitalizaciones de la tomografía computerizada con rayos X. Las digitalizaciones metrológicas de la tomografía computerizada con rayos X midieron el tamaño de las características internas con más precisión. Las características interiores se compararon directamente con los modelos pertinentes de diseño asistido por ordenador (CAD). Tomando como base los resultados, se propuso un diseño de artefacto mejorado.
Contribución oficial del Instituto Nacional de Normas y Tecnología (NIST en inglés); no sujeto a derechos de autor en los Estados Unidos. Las descripciones completas de este documento requieren la identificación de ciertos productos comerciales. La inclusión de tal información de ninguna manera debería interpretarse como indicación de que tales productos están respaldados por NIST o están recomendados por NIST ni que sean necesariamente los mejores materiales, instrumentos, software o proveedores de los fines descritos.
Fabricación aditiva de muestras con características internas mediante tecnología de fusión de polvo por láser
Las piezas se produjeron utilizando los procesos de fabricación aditiva con fusión por polvo (PBF en inglés) basado en láser, con un sistema (EOS M270) disponible en el Instituto Nacional de Normas y Tecnología (NIST). Se utilizó el polvo de la superaleación con base de Níquel (Inconel 625) (entre 15 y 60 μm en tamaño de partículas tal como se midió por medio de tamices estándar). El tamaño del punto de láser es de aproximadamente 100 μm y se utilizó la configuración de parámetros de máquina por defecto para el material Se diseñaron tres muestras con características interiores que incorporaban tamaños y orientaciones diferentes de cubos y esferas, tal como se muestra en la figura 1. Se espera que los polvos no fundidos queden atrapados en los huecos. Los diámetros exteriores de las muestras son 10, 6 y 5mm, respectivamente.
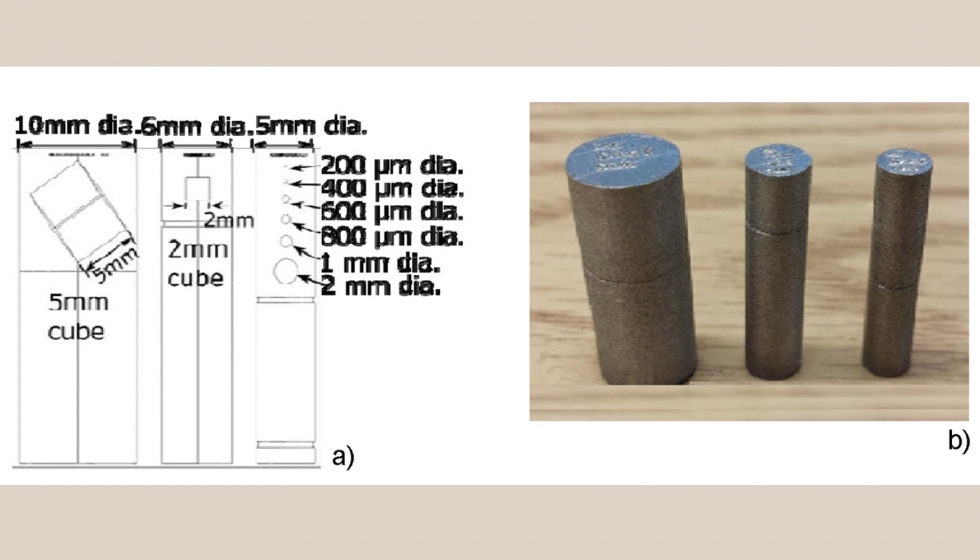
Inspección por tomografía computerizada con rayos X metrológica
Las mediciones metrológicas de la tomografía computerizada con rayos X (XCT en inglés) se obtuvieron utilizando un sistema Nikon XT H 225 ST. Una de las principales ventajas dela XCT es el uso del tamaño del vóxel calibrado. Las técnicas típicas de la XCT estiman el tamaño del vóxel basándose solamente en el factor de aumento. Sin embargo, existe potencial para errores dimensionales con este enfoque debido a errores de posición del eje, error en el alineamiento geométrico del hardware del sistema de la tomografía computerizada y error de desplazamiento del punto focal del rayo X. Además, la calidad de la imagen se puede ver afectada por factores físicos tales como el endurecimiento del haz o la dispersión de los rayos X, lo que se necesita evitar por medio del filtrado del hardware o compensar con correcciones de posprocesamiento tras la reconstrucción de la tomografía computerizada.
Para la medición actual se realizaron una calibración del tamaño del vóxel y una corrección del endurecimiento del haz. La calibración del tamaño del vóxel se llevó a cabo de manera similar a las directrices de [7] ejecutando una digitalización de tomografía computerizada de un objeto de calibración (figura 2) con configuración de digitalización idéntica a las utilizadas en la medición de las piezas de prueba. El objeto de calibración es un cilindro de aluminio hueco que se midió con una máquina de medición de coordenadas (MMC) para obtener dimensiones de referencia. Los parámetros de digitalización de la XCT se muestran en la tabla 1. Se observan ligeras diferencias entre el tamaño de vóxel efectivo calculado basándose en el aumento geométrico no calibrado y el tamaño del vóxel calibrado.
Para las mediciones de tomografía computerizada, las muestras se montaron en un ángulo de 20º desde el eje vertical para evitar artefactos con haz de cono.
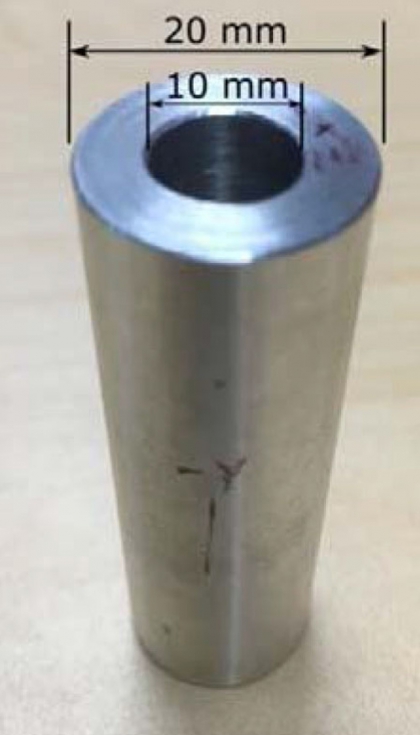
Viabilidad de construir. Características internas
Se muestran porciones interiores en aproximadamente la sección media de cada muestra en la figura 3. Se logró un contraste alto de las partes sólidas y los huecos llenos de polvos se pueden distinguir fácilmente de la estructura solidificada. El hueco atrapador de polvo parece más oscuro debido a la porosidad y a la resolución espacial bastante baja comparada con el tamaño del polvo. En la muestra de esfera no se construyó el poro esférico de 200 µm de diámetro. En la resolución espacial actual de la XCT, no se encuentra ningún poro visible en la zona. Tanto las esferas como el cubo pequeño experimentaron dificultades con la producción de superficies superiores precisas. Por otro lado, el cubo grande se construyó relativamente bien a pesar de las mayores dimensiones generales. Los orificios pequeños (100 µm de diámetro) se diseñaron e incorporaron para el fin de sacar posiblemente los polvos, pero tampoco parecían estar construidos. Los poros involuntarios no eran visibles en las imágenes de la XCT en la resolución espacial utilizada, lo que confirma que los parámetros de procesamiento de la fabricación aditiva utilizados eran óptimos para reducir la formación de porosidad.
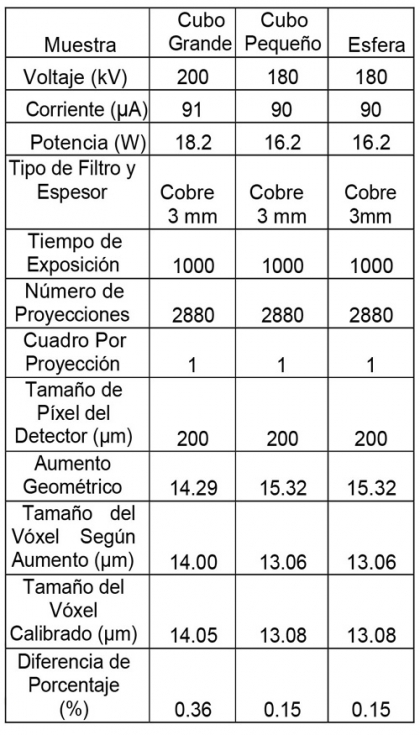
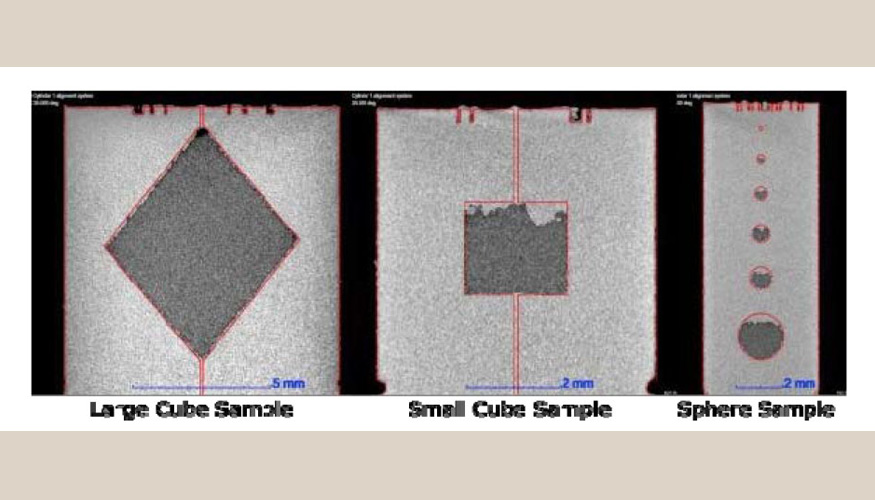
Comparación de CAD nominal contra real
Las imágenes de la XCT metrológica se compararon directamente con los dibujos de CAD tal como se muestra en las figuras 4, 5 y 6. La superficie de la XCT se registró en CAD a través de un algoritmo interativo de mejor ajuste. Las ubicaciones de geometría nominal se restaron de la posición real en las superficies determinadas desde los volúmenes de la XCT. Las desviaciones de la geometría nominal eran tan grandes como aproximadamente ± 100 µm, y las ubicaciones con desviaciones mayores de ±50 µm se destacaron en color rojo y magenta en las figuras interiores.
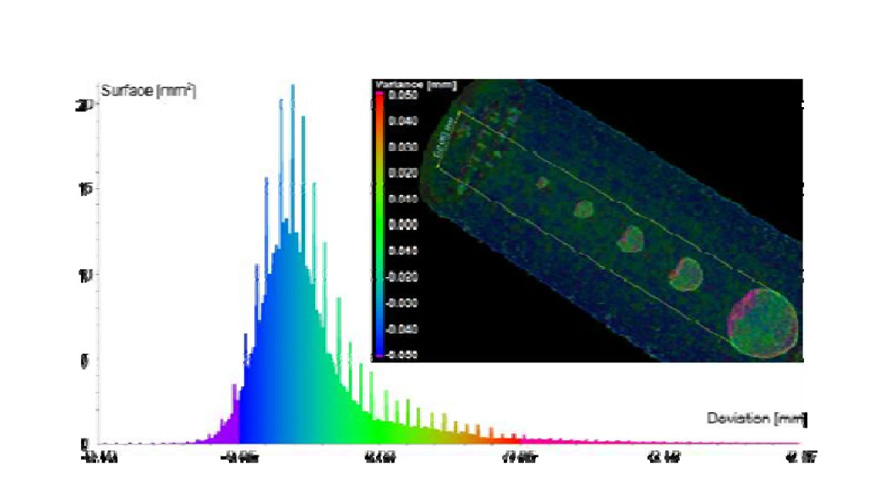
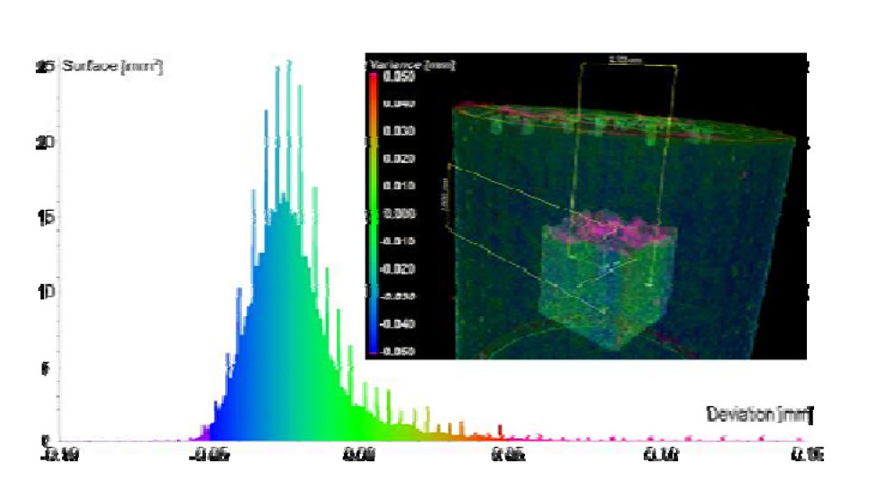
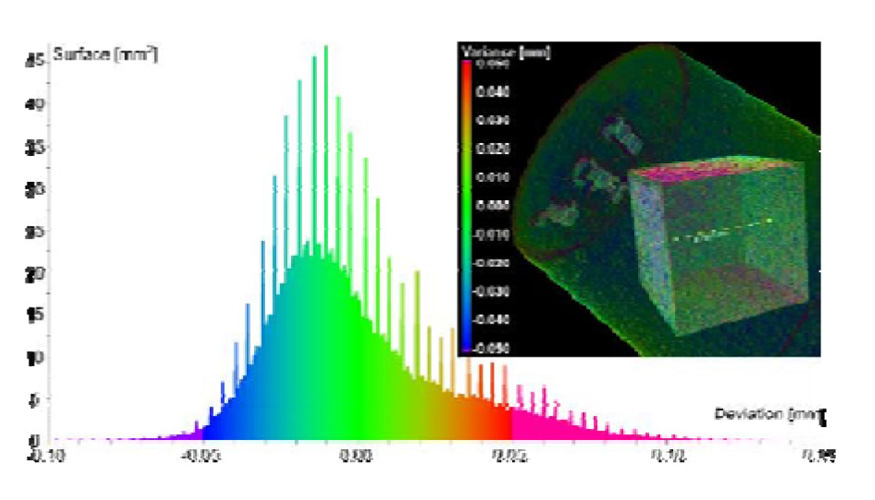
Los volúmenes nominales y reales de las características internas se comparan en la tabla 2. La diferencia entre los volúmenes nominales y reales aumentó según decrecía el tamaño de la característica interior. Los volúmenes reales fueron siempre más pequeños que los volúmenes nominales para los diseños escogidos debido a la producción inexacta de las superficies superiores.
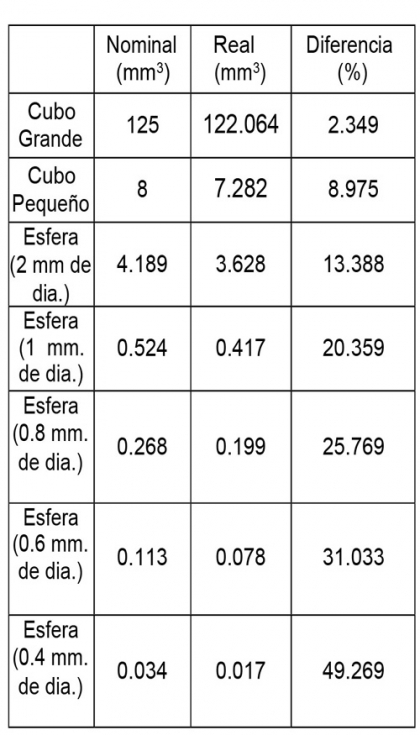
Diseño mejorado
Basado en las imágenes de la XCT de los prototipos iniciales, se propuso construir un diseño mejorado como artefacto para determinar la Probabilidad de Detección (PoD en inglés), y un diseño de ejemplo se muestra en la figura 7. El diseño incluye cubos de tamaños diferentes que están en orientaciones giradas. Se espera que los cubos en esta orientación se construyan próximos a los diseños nominales. Se planifican mediciones posteriores de XCT para el diseño nuevo.
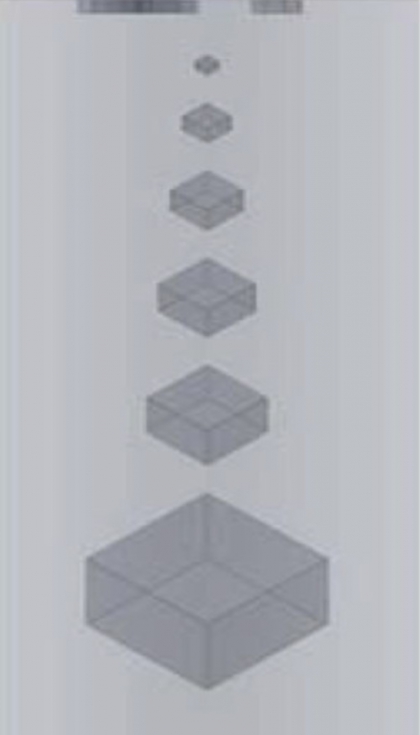
Conclusiones
Se construyeron las muestras que incorporan características internas y se obtuvieron digitalizaciones de XCT metrológicas para las muestras. Las digitalizaciones de XCT se alinearon con los dibujos de CAD nominales para una comparación directa. Se detectaron desviaciones de hasta ± 0,1 mm entre las dimensiones nominales y las medidas de las piezas producidas por Fabricación Aditiva utilizando la XCT. Las incertidumbres habituales de las mediciones de Tomografía Computerizada están en el orden de 10 μm, lo cual es un factor cinco más pequeño que la desviación medida. Por lo tanto, las tolerancias de ± 50 μm están relacionadas predominantemente con el proceso de Fabricación Aditiva más que con la incertidumbre de medición. La XCT tiene la capacidad de generar datos geométricos para la caracterización de las estructuras de materiales (características internas y externas) y detectar defectos de fabricación y desviaciones dimensionales del diseño de CAD. Para estudiar las estructuras complejas producidas por el proceso de fabricación aditiva, la XCT está llegando a ser una opción viable para extraer dimensiones de los componentes de las estructuras internas u ocultas de manera no destructiva. Las mediciones de XCT proporcionan además conocimientos sobre la construcción e incorporación de características internas utilizando los procesos de fusión de polvo (PBF en inglés). La XCT metrológica de las muestras controladas proporciona buenos datos de referencia para medir las características internas. Los resultados obtenidos se pueden utilizar finalmente para determinar cuantitativamente la detectabilidad de las características internas utilizando la XCT.
Los planes futuros incluyen la obtención de imágenes adicionales de XCT en sistemas diferentes para una comparación. Una vez que se hayan completado todas las digitalizaciones de XCT, se realizará una medición destructiva.
Reconocimientos
A los autores les gustaría agradecer al Sr. Mike McGlauflin del Instituto Nacional de Normas y Tecnología (NIST en inglés) por proporcionar consejo sobre el desarrollo de un diseño de muestra y al Dr. Jarred Heigel of NIST por producir las piezas con fabricación aditiva.
Referencia
[1] Ng GKL, Jarfors AEW, Bi G, Zheng HY. Formación de porosidad y retención de burbujas de gas en la deposición del metal por láser. Física Aplicada A. 2009;97:641-9.
[2] Thijs L, Verhaeghe F, Craeghs T, Humbeeck JV, Kruth J-P. Un estudio de la evolución microestructural durante la fusión con láser selectiva de Ti–6Al–4V. Acta Materialia. 2010;58:3303-12.
[3] Yadroitsev I, Thivillon L, Bertrand P, Smurov I. Estrategia de fabricación de componentes con estructura interna diseñada por fusión con láser selectiva de polvo metálico. Ciencia de Superficies Aplicada. 2007;254:980-3.
[4] Maire E, Withers PJ. Tomografía con Rayos X Cuantitativa. Revisiones de MaterialesInternacionales. 2014;59:1-43.
[5] Withers PJ, Preuss M. Fatiga y Daños en Materiales Estructurales Estudiado por Tomografía con Rayos X. Revisión Anual de Investigación de Materiales. 2012;42:81-103.
[6] Amrhein S, Rauer M, Kaloudis M. Caracterización de Escáneres de Tomografía Computerizada Utilizando el Método de Probabilidad de Detección. JNE. 2014;33:643-50.
[7] Lifton JJ, Malcolm AA, McBride JW, Cross KJ. La Aplicación de la Corrección del Tamaño del Vóxel en la Tomografía Computerizada con Rayos X para la Metrología Dimensional. 2ª Conferencia y Exposición Internacional de Pruebas No Destructivas de Singapur. Marina Bay Sands, Singapur 2013.