Integración de procesos multitarea para la producción de álabes
La fabricación de componentes rotativos de alto valor añadido es crítica dada la complejidad de su geometría. La presencia de estos componentes se extiende a varios sectores como el aeronáutico, el automovilístico o el de la energía. Algunos ejemplos claros de este tipo de geometrías rotativas son las palas de hélice, álabes para turbo-maquinarias, levas forjadas o ejes de levas de fundición que deben ser mecanizados, etc. Hoy en día existe una firme tendencia a la realización de todas las operaciones que conforman una pieza en la misma máquina, el denominado como mecanizado multitasking o multitarea. La mayor ventaja es que no se pierde en ningún momento el sistema de referencia de la pieza a lo largo de todas las operaciones y se minimiza la posibilidad de errores al mismo tiempo que se reduce el tiempo final total. El concepto de máquina-herramienta está evolucionando hacia el nuevo concepto de multitarea, e incluso procesos no tradicionales como el temple por láser, láser cladding o bruñido se llevan a cabo en la misma máquina sin alterar el montaje inicial.
En este artículo se define un proceso híbrido para la fabricación de una pala de una hélice en una máquina multitasking. El mecanizado de la pala se lleva a cabo mediante la aplicación sucesiva de tres técnicas. En primer lugar se realizar una operación de torno-fresado (turn-milling) para definir la preforma. En segundo lugar se torno-fresa la superficie a punta de bola (turn-ball end milling) para el contorneado de la superficie y finalmente se bruñe (burnishing) para mejorar la rugosidad y aumentar la resistencia a fatiga de la pieza. Estos procesos se modelizan para determinar sus parámetros óptimos.
Este proceso permite la obtención de piezas complejas funcionales con alta integridad, calidad y cortos tiempos de proceso. La visión integral de los procesos puede suponer producir piezas de elevado valor añadido que además posean características funcionales interesantes, en lo referente a precisión, resistencia a la fatiga, etc. En definitiva, se muestra como las posibilidades de una máquina multitarea abren nuevos procesos de elevado valor añadido.
1. Introducción
La fabricación de álabes es cada vez más frecuente en sectores como el aeronáutico y el energético. Su geometría la componen una serie de superficies complejas sometidas a duras condiciones de trabajo. Para su correcta fabricación es necesario tener en cuenta la aerodinámica de la pieza y los esfuerzos a los que se encuentra sometido, ya que es necesario cumplir con todos los requerimientos para obtener la pieza final.
1.1 Aerodinámica y fuerzas actuantes sobre el álabe
Este tipo de álabes están formados por dos superficies alabeadas unidas en su extremo final a buje. Como puede observarse en la Figura 1, las fuerzas qué actúan sobre este tipo de álabes son:
- Empuje de la fuerza del viento sobre el alabe de forma paralela a la dirección de avance introduciendo un esfuerzo de flexión sobre la superficie del álabe.
- Fuerza centrífuga debida la rotación del propio álabe y tiende a empujar el álabe de su punto central.
- Torsión que tiene lugar sobre el álabe a consecuencia de las posibles fuerzas que puede ejercer el viento y tiende a retorcer los alabes contra un ángulo de empuje menor.
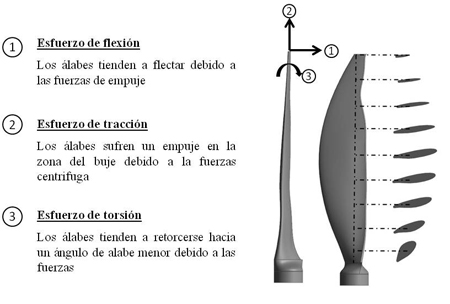
Figura 1. Esfuerzos sobre la sección de un álabe
2. Proceso de fabricación los álabes
El proceso de fabricación de álabes estudiado en el artículo se basa el denominado concepto multitasking que agrupa todos los procesos de fabricación requeridos por el alabe en la misma máquina. Como consecuencia de la agrupación de los mismos en una sola máquina y por lo tanto, una sola atada de la pieza, se reduce considerablemente la posibilidad de errores debida a los constantes traslados de pieza entre una máquina y otra. Se reducen de esta forma también los plazos de fabricación. Asimismo, la misma atada permite mantener el mismo sistema de referencia y evitar así posibles problemas debidos a los constantes cambios de referencia.
Inicialmente, la pieza necesita someterse a un proceso de torno-fresado para realizar el desbaste de la misma hasta obtener una pieza lo más cercana a la pieza final. Posteriormente, se realiza el acabado del alabe mediante torno fresado con fresa de punta esférica. En algunos casos, la aplicación de un mecanizado equilibrado o pinch milling permite obtener procesos de fabricación más rápidos gracias a la ejecución de dos operaciones al mismo tiempo. Finalmente, se bruñe la pieza para mejorar la rugosidad final y mejorar la vida a fatiga de la misma.
2.1. Torno-fresado
El torno-fresado es un concepto relativamente nuevo dentro de las tecnologías de fabricación en máquinas multitasking de 4 ó 5 ejes. Para realizar esta operación es necesario dotar de una rotación simultánea tanto a la pieza como a la herramienta. Este proceso, en función de la posición espacial de los ejes de rotación, se puede clasificar como torno-fresado coaxial u ortogonal [1]. Se denomina coaxial cuando el eje de rotación de la herramienta y el de la pieza son paralelos entre sí. El proceso se denomina ortogonal cuando el eje de giro de la herramienta es perpendicular al de la pieza.
2.1.1. Torno-fresado coaxial
En este tipo de torno-fresado (Figura 2), la herramienta ataca en todo momento a la pieza con el flanco de la herramienta. Una correcta elección de la fresa a emplear es crítica para que la técnica proporcione resultados satisfactorios, por eso las fresas de escuadrar, debido a su diseño, son las que mejor se adaptan a este proceso.
Esta opción es adecuada tanto para el mecanizado tanto de exteriores como de interiores cuando se trata de una pieza de revolución o no. Para la ejecución de esta técnica la rotación de la pieza de trabajo es relativamente lenta en comparación con la velocidad de rotación de la herramienta. Esto conlleva una serie de ventajas como que debido a la cinemática del proceso se producen virutas cortas, incluso cuando se trata de mecanizar materiales dúctiles. En el caso de mecanizar piezas cilíndricas muy esbeltas, la velocidad de rotación baja evita excitar la pieza a altas frecuencias como en el torneado convencional.
Para utilizar esta técnica de torno-fresado es necesario que la máquina herramienta sea capaz de interpolar 3 o 4 ejes en continuo. La cinemática de esta técnica se presenta en la siguiente figura. Debido a que la rotación de herramienta se debe realizar siempre en el mismo sentido, como consecuencia de la disposición espacial de los filos de corte, hay que poner atención en el sentido de giro de la pieza. Será el sentido de giro de ésta la que determine si el mecanizado es oposición o en concordancia. Ambas operaciones reflejadas en la figura son en concordancia, por tratarse de la estrategia que mejores resultados proporciona en cuanto a tolerancia dimensional y acabado superficial.
Algunas características particulares de esta técnica son:
- Mediante el Empleo de una fresa adecuada se pueden realizar mecanizados interiores sin necesidad de que exista un agujero previo
- Se pueden generar superficies no cilíndricas como se aprecia en el ejemplo práctico de anterior figura
- Se pueden mecanizar canales estrechos
- La técnica en idónea para el mecanizado de roscas interiores y exteriores con fresas de roscar
- La principal desventaja de la técnica radica que para cavidades profundas es necesario un alto voladizo de la herramienta.
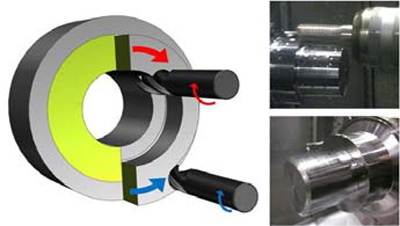
Figura 2. Esquema cinemático de la operación de torno-fresado coaxial y ejemplo de aplicación.
2.1.2. Torno-fresado ortogonal
El proceso se denomina ortogonal (Figura 3) cuando el eje de giro de la herramienta es perpendicular al de la pieza, siendo aplicable únicamente para el mecanizado de exteriores. Esta técnica proporciona una serie de ventajas:
- Se obtienen buenos resultados cuando se mecanizan piezas de pared delgada, ya que los esfuerzos se corte son menores que en el torneado convencional.
- Posibilidad de emplear herramientas de menor voladizo, lo que confiere al proceso una mayor estabilidad cuando la tasa de arranque de material es grande.
- Si se dota a la herramienta de una alta velocidad de rotación y se emplean los parámetros geométricos adecuados, es posible obtener una calidad superficial muy buena, comparable incluso con el rectificado [2].
- La evacuación de la viruta es más sencilla, lo que mejora la refrigeración de la zona de corte evitando así los problemas derivados del exceso de temperatura [3].
- Al rotar la pieza de trabajo a baja velocidad es difícil que se experimenten problemas en el mecanizado generados por fuerzas centrífugas.
Otra variante del torno-fresado ortogonal es la posibilidad de situar la fresa de manera tangencial a la pieza. Esta técnica ha inspirado investigaciones enfocadas a analizar y obtener los parámetros de mecanizado que optimicen la rugosidad superficial de la pieza de trabajo. En este caso las herramientas empleadas son fresas de acabado, herramientas integrales de metal duro [4, 5].
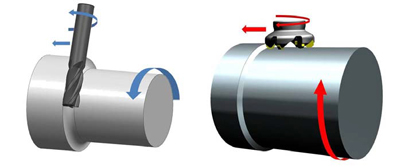
Figura 3. Torno-fresado ortogonal dependiendo de la herramienta utilizada.
2.1.2.1. Fundamentos teóricos torno-fresado ortogonal
A la hora de definir la operación de torno-fresado ortogonal se parte de las condiciones que impone el proceso de fresado, de manera que se calcula la velocidad de giro, Ec. (1) y la velocidad de avance de la herramienta, Ec. (2), como si de un proceso convencional de fresado se tratase. La herramienta no es capaz de moverse alrededor de la pieza, por lo que la velocidad de avance radial lo proporciona la pieza a mecanizar. El cálculo de la velocidad de rotación de la pieza de trabajo se obtiene a partir de las dos relaciones anteriores y del diámetro de la pieza, Ec. (3).

Donde N (rpm) es la velocidad de rotación de la fresa, Vc (m/min) es la velocidad de corte y ØT (mm) es el diámetro total de la herramienta de corte.

Donde Vf (mm/min) es la velocidad de avance en fresado convencional, Zn es el número de filos de la herramienta empleada y fz (mm/rev) es el avance por diente.

Donde (grados/min), es la velocidad de giro de la pieza y Øp es el diámetro de la pieza. A la hora de programar la operación, puede resultar más interesante disponer de la velocidad de rotación de la pieza en revoluciones por minuto, como se expresa en la Ec. (4).

Para el cálculo de la velocidad de avance axial, es necesario determinar lo que en fresado se denomina profundidad de pasada radial, ae (mm). En la Ec. (5) se muestra la expresión para el cálculo de la velocidad de avance axial.

2.1.2.2. Compensación en eje Y de la herramienta
La operación de torno-fresado ortogonal genera en la superficie de la pieza una forma en media luna característica, provocado por la geometría de la herramienta empleada y por la acción combinada de la rotación de la herramienta de corte y de la pieza. En la dirección de avance axial, también se genera una forma geométrica peculiar, dependiente en este caso, de la geometría de la herramienta y del valor de la compensación en el eje Y de la herramienta, a la que se denominará Ew (mm). En la Figura 4 y Figura 5, se reflejan los casos extremos.
Uno de los dos casos extremos es cuando Ew=0% Øef, siendo Øef (mm) el diámetro efectivo de la herramienta de corte. Este posicionamiento espacial de la herramienta genera una superficie convexa en la pieza mecanizada, como se aprecia en la Figura 4. El empleo de esta posición está recomendado para las operaciones de acabado de ranuras, para generar el acuerdo entre la pared y el fondo de la ranura. La forma en la que se realiza el corte, es similar a una operación de torneado en ramping, en la que los insertos de corte mecanizan con la parte inferior, generándose altos esfuerzos axiales.
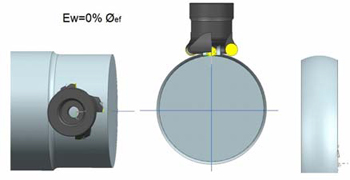
Figura 4. Caso extremo de corte Ew=0% Øef.
El otro caso extremo se obtiene cuando Ew=50% Øef. Este posicionamiento espacial de la herramienta genera una superficie cóncava, Figura 5. Con este desplazamiento se evita el efecto del corte en la parte inferior de los filos, reduciendo de esta manera los esfuerzos axiales generados en el mecanizado. Este posicionamiento permite evitar el peligro de que se produzca interferencia entre el centro de la herramienta y la pieza, independientemente de la profundidad de pasada (ap).
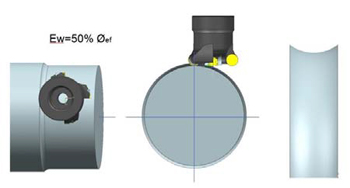
Figura 5. Caso extremo de corte Ew=50% Øef.
2.2. Torno-fresado de acabado con herramienta de punta de bola
Una vez se da por finalizado el desbaste de la pieza, es necesario ejecutar el programa de acabado para obtener la pieza final. En este caso, se aplica un torno-fresado de acabado con herramienta con punta de bola. Los usuarios de máquina herramienta están continuamente debatiéndose entre la necesidad de mantener una alta calidad en el mecanizado y la necesidad de reducir tiempo de mecanizado. Una solución a estos problemas son las máquinas equipadas con dos torretas. Estas máquinas permiten un mecanizado equilibrado, dos herramientas se encuentran cortando simultáneamente.
El corte simultáneo con dos herramientas es más rápido, y al mismo tiempo unas fuerzas de corte equilibradas contrarrestan la deformación que puede provocar en las piezas delgadas la presión de una sola herramienta [6]. El mecanizado equilibrado ha sido históricamente utilizado en las operaciones de torneado, pero desarrollos recientes en las maquinas y los software de CAM como Esprit están expandiendo la tecnología de mecanizado equilibrado a las operaciones de fresado. El mecanizado equilibrado en una máquina de torno-fresado puede resultar mejor que un centro de mecanizado tradicional para el mecanizado de ciertas piezas.
Las ventajas principales de este tipo de proceso simultáneo son ciclos más rápidos y fuerzas de mecanizado equilibradas.
Ciclos más rápidos
Cuando dos herramientas mecanizan la misma geometría simultáneamente con una herramienta por encima del eje de rotación y la otra por debajo, se puede duplicar la tasa de arranque de material sin afectar a la herramienta. Otra técnica a utilizar es empezar a mecanizar con una de las herramientas y mientras la segunda herramienta espera hasta que la primera haya recorrido una cierta distancia. La segunda herramienta sigue a la primera para realizar un mecanizado a diferente profundidad, de este modo se puede realizar dos operaciones en una sola pasada.
Fuerzas de mecanizado equilibradas
La flexión que se produce en piezas esbeltas y largas cuando se mecaniza con una sola herramienta es uno de los problemas con los que se enfrentan los fabricantes de este tipo de piezas. Si se aplica simultáneamente el mecanizado con dos herramientas se produce un equilibrio de las fuerzas de corte que reduce el riesgo de flexión de la pieza producido por el mecanizado con una sola herramienta. Indirectamente la solución del problema de flexión de pieza también reduce los ciclos de mecanizado al mejorar la calidad de la pieza.
Acabado equilibrado
Cuando el desbaste equilibrado se utilice únicamente para generar pasadas de acabado, se utilizan pasadas de contorneado en lugar de pasadas de acabado. Generalmente se deja un tiempo de espera entre el comienzo de mecanizado de la primera herramienta y la segunda para que puedan hacerlo a diferente profundidad de pasada. La primera herramienta puede realizar el semiacabado y la segunda el acabado hasta la forma final (Figura 6).
![Figura 6. Acabado equilibrado [DP Technology] Figura 6. Acabado equilibrado [DP Technology]](https://img.interempresas.net/fotos/871884.jpeg)
Figura 6. Acabado equilibrado [DP Technology]
Sincronizar operaciones de la torreta superior e inferior
La sincronización de operaciones sincronizadas es de vital importancia ya que evita colisiones y permite ahorrar tiempo gracias a acciones como la preparación de la herramienta correspondiente a la siguiente operación para una mayor optimización. Se puede arrastrar una operación hasta la posición de mecanizado deseada ya sea antes o después de un cambio de herramienta.
Fresado equilibrado
El fresado equilibrado con una herramienta en el cabezal de fresado y otra herramienta motorizada en la torreta inferior permiten mecanizar lados opuestos de la pieza al mismo tiempo. El fresado y el taladrado equilibrado son las operaciones más productivas cuando las dos torretas permiten realizar un movimiento en Y.
Fresado equilibrado en 5-ejes
Esta tecnología presenta uno de los mayores desarrollos en la programación CAM porque las herramientas superior e inferior siguen diferentes trayectorias de mecanizado y deben ser cuidadosamente coordinadas y sincronizadas en el gestor de operaciones para que no se produzca ninguna colisión. El mecanizado equilibrado en 5 ejes (Figura 7) requiere una máquina multitasking con eje B y una torreta inferior con herramienta motorizadas. Además se recomienda la utilización de dos husillos. Los husillos tienen eje C que proporcionan movimiento a la pieza.
Este tipo de fresado equilibrado es muy apropiado para la fabricación de alabes de turbinas ya que los alabes son unas superficies largas, delgadas y con tendencia a la flexión. Cuando el alabe se sujeta por los dos husillos, los husillos pueden agarrar y aplicar el par en los dos extremos de la pieza. Dado que la pieza es amarrada más rígidamente tiene menos tendencia a flectar. Esta configuración permite la utilización de herramientas esféricas sin inclinar la punta de la herramienta. Se la orientación de la herramienta durante el mecanizado simultáneo en 5 ejes, la maquina puede mantener una velocidad de corte constante. Este tipo de mecanizado es más rápido que un desbaste y un acabado. El corte simultáneo con dos herramientas permite aumentar las velocidades de avance y maximizar el rendimiento.
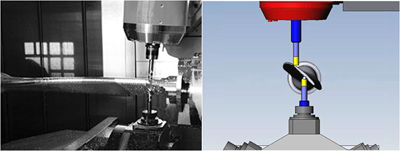
Figura 7. Fresado equilibrado en 5-ejes mecanizado en una Mori Seiki.
2.3. Bruñido con bola
El mecanizado de superficies complejas desempeña un papel importante en el proceso de introducir nuevos productos en el mercado. Gran variedad de productos, desde matrices para la industria del automóvil hasta los álabes de turbina, presentan superficies complejas. Este tipo de superficies suelen ser mecanizadas en máquinas multieje, realizando el copiado con fresas de punta esférica y posteriormente pulidas cuando un buen acabado superficial es necesario. El proceso de acabado y pulido a mano puede llegar a representar más del 75% del total del tiempo de mecanizado.
Entre los diferentes tipos de tratamientos mecánicos superficiales existentes, el bruñido con bola proporciona, además de un excelente acabado superficial, una mejora de las propiedades físico- mecánicas del componente [7]. Se trata de una operación sencilla, de bajo coste y que genera una superficie final de gran calidad. En este sentido, el bruñido con bola puede sustituir a procesos de acabado como el rectificado, el shot peening o el pulido a mano. Este proceso es de aplicación directa en máquinas multitasking.
El proceso se basa en provocar una pequeña deformación plástica en la superficie de la pieza. De esta forma se genera una capa de metal consolidada que puede alcanzar espesores de entre 2 a 10 µm. El ‘aplastamiento’ provoca los siguientes efectos sobre la superficie:
- Reducción de la rugosidad superficial en más de un orden de magnitud. El acabado final es del orden del rectificado [8].
- Generación de tensiones residuales de compresión en la superficie de la pieza, lo cual es beneficioso de cara al comportamiento a fatiga del componente. Además, la ausencia de calor evita cambios metalúrgicos en la superficie [9].
- Aumento de la dureza superficial entre 30-60% (HBN) partiendo de niveles propios de aceros comunes, es decir, 180-250 HBN. En materiales de elevada dureza, este incremento es despreciable.
El principio del bruñido hidrostático por bola, ilustrado en la Figura 7, está basado en el muelle hidrostático. La fuerza normal aplicada solo depende de la presión de la bomba. La bola tiene un movimiento libre de 6 mm que ayuda a absorber errores en las piezas y facilita asimismo la programación del proceso de acabado.
La aplicación de esta técnica de bruñido al álabe mejora su rugosidad y aumentar la resistencia a fatiga de la pieza.
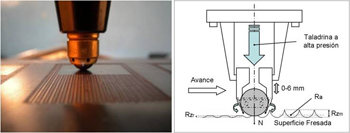
Figura 8. (Izda.) Principio de bruñido hidrostático con bola. (Dcha.) Detalle de la bola cerámica.
2.4. Ejemplos
En este ejemplo (Tabla 1) el álabe ha sido torno-fresado haciendo uso del sistema de amarre de herramienta denominado Capto. A continuación, se realiza la operación de acabado de torno- fresado con punta de bola. Esta operación es más duradera que la de desbaste. Finalmente, se aplica la técnica de bruñido para lograr un mejor acabado de la superficie y al mismo tiempo eliminar tensiones residuales.
Todas las operaciones se verifican virtualmente para evitar posibles colisiones o movimientos indeseados que pueden ser causa de errores.
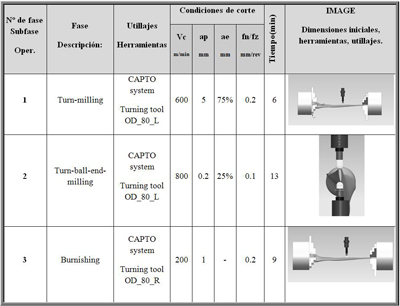
Tabla 1. Proceso de fabricación del álabe.
2.5. Conclusiones
El trabajo presenta la aplicación de una serie de técnicas para la fabricación de álabes. Incluye la aplicación de torno-fresado para operaciones de desbaste, torno-fresado a punta de bola para acabado de la pieza y bruñido.
2.6. Agradecimientos
Los autores quieren agradecer su apoyo al Departamento de Universidades, Investigación y Política Científica de Gobierno Vasco por su financiación y al Departamento de Industria, Innovación, Comercio y Turismo del Gobierno Vasco por su apoyo vía Etortek InProRet. Los autores agradecen también a la UPV/EHU (UFI 11/29).
Referencias
[1] H. Schulz, T. Kneisel (1994) Turn-milling of hardened steel and alternative to turning, CIRP, 43, 93-96.
[2] Ping Chen (1992), Cutting temperature and forces in machining of high performance materials with self-propelled rotary tool, JSME Int. J. Ser., III, 35, 180-185.
[3] S.K. Choudhury, J.B. Bajpai (2005) Investigation in orthogonal turn-milling towards better surface finish, Journal of Materials Processing Technology, 170 487–493.
[4] V. Savas, C. Ozay (2008) The optimization of the surface roughness in the processof tangential turn-milling using genetic algorithm, Int J Adv Manuf Technol, 37, 335–340
[5] In a Pinch: Using 2 Tools to Balance Cutting Forces: www.dptechnology.com (2012).
[6] Golden P.J, Shepard M.J. (2007) Life prediction of fretting fatigue with advanced surface treatments, Materials Science and Engineering, 15-22, 468-470.
[7] López de Lacalle, L.N., Rodriguez, A., Lamikiz, A., Celaya, A., Alberdi, R. (2011) Five-axis Machining and Burnishing of Complex Parts for the improvement of surface roughness, Materials and Manufacturing Process, 26, 997–1003.
[8] Prevéy, P., Ravindranath, R., Shepard, M., Gabb, T. (2003) Case Studies of Fatigue Life Improvement Using Low Plasticity Burnishing in Gas Turbine Engine Applications, Proceedings of ASME Turbo Expo, Atlanta, GA, 16-19.
[9] Rodríguez, A., López de Lacalle, L.N., Celaya, A., Lamikiz, A., Albizuri, J. (2012) Surface Improvement of Shafts by the Deep Ball-Burnishing Technique, Surface & Coatings Technology, 206, 2817–2824.