La estabilización a la luz de films agricolas y beneficios de una nueva forma física de aditivo
Great Lakes Technology15/10/2003
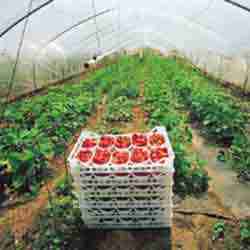
Esta mejora de comportamiento puede llevar a una reducción en el nivel de concentración de los aditivos, para conseguir las mismas prestaciones, y por lo tanto, a una reducción de costes.
Film Agrícola
Los requisitos de un filme de invernadero son altamente exigentes, debido al relativamente largo tiempo de exposición a la luz UltraVioleta (a menudo hasta 4 campañas) en combinación con las duras condiciones ambientales, tales como el aumento de temperatura dentro del invernadero, la exposición a agentes químicos agresivos (pesticidas, insecticidas,…), alta humedad, y exposición a otros factores climáticos como son la lluvia, el viento, el granizo, el rocío [3].
Además de la resistencia a estas severas condiciones, el film de invernadero debe ofrecer una combinación de propiedades como, buenas propiedades mecánicas, propiedades ópticas, fotoestabilidad, resistencia al calor, resistencia a los agentes fitosanitarios, repeler el polvo, antigoteo, retención del calor, favorecer el cultivo y reducir las enfermedades. Estas características deben mantenerse durante todo el tiempo de servicio de la cubierta de invernadero.
En general, se usan varios aditivos para lograr las propiedades deseadas. Estos aditivos a su vez, deben tener unas propiedades físico-químicas específicas. Por ejemplo, en el caso de un estabilizante a la luz, éste debe tener una estabilidad intrínseca a la luz, baja volatilidad, alta compatibilidad con la resina y dar lugar a interacciones indeseadas con los otros aditivos de la formulación. Además, el estabilizante a la luz no debe interaccionar con especies ácidas y debe ser químicamente inerte, especialmente cuando se usan altas concentraciones de fitosanitarios en el interior del invernadero.
Factores que influyen en el tiempo de vida de una película de invernadero
Factores de la Formulación
La resistencia intrínseca a la radiación UV del polímero o de la mezcla de polímeros usada (LDPE, LLDPE, EVA etc.) y la compatibilidad con los estabilizantes UV conducirá a distintos tiempos de duración del filmen la aplicación. Típicamente un film de EVA tendrá una duración ligeramente más larga que un film de PE como se muestra en la figura 1.
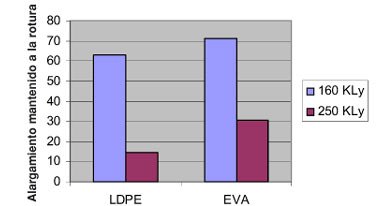
Film monocapa (150µm)
Polímero:
LDPE o EVA (14% VA)
Formulación:
0,5% HALS
Exposición:
soporte de Aluminio – Bandol (Francia)
Evaluación:
% Retención del alargamiento a rotura después de 160 y 250 KLy
Tipo de Película:
Los filmes coextruídos, principalmente LDPE-EVA, permiten aprovechar las propiedades que cada capa constitutiva del film ofrece (coste, elasticidad, propiedades térmicas…) . Además, los aditivos con diferente funcionalidad pueden añadirse directamente a la capa de film donde su función es necesaria (ej. Antiniebla en la capa interna, antipolvo en la exterior,…)
Espesor del Film:
Aumentando el espesor de la película, para una determinada formulación del sistema estabilizante, aumenta la duración del film (como se muestra en la figura 2).
![Figura 2: Efecto del espesor de la película [7] Figura 2: Efecto del espesor de la película [7]](https://img.interempresas.net/fotos/36327.jpeg)
Los estabilizantes a la luz UV y los niveles de aditivación, influyen claramente la duración de un film de invernadero. La figura 3 muestra el efecto de la concentración de aditivos en la duración del polímero, como era de esperar, ésta aumenta con la concentración de aditivo hasta llegar a un valor constante debido al efecto de saturación en el filme.
![Figura 3: Efecto de la concentración de los estabilizantes UV [7] Figura 3: Efecto de la concentración de los estabilizantes UV [7]](https://img.interempresas.net/fotos/36332.jpeg)
Fílme de LDPE – Espesor: 170µm
Formulación:
1:1 NiQ-1:UVA-1 Mezcla en polvo
Exposición:
WOM Ci65, 63°C BPT, 0,35 W/m2, 50% RH
Evaluación:
Tiempo para una disminución del 50% del valor inicial del Alargamiento a rotura.
Cargas, Pigmentos:
Las cargas usadas para obtener una disminución de la transmisión en el IR lejano, que se emplean para evitar el descenso de temperatura en el interior del invernadero durante la noche, pueden afectar a la estabilidad del film frente a la luz. Esto también puede ocurrir con el empleo de ciertos pigmentos (para proteger el cultivo de un exceso de radiación o para seleccionar ciertas longitudes de onda importantes para el crecimiento de la planta).
Muestra:
Fílme de LDPE -Espesor: 150µm
Formulación:
0,5% HALS
Exposición:
Soporte de Aluminio – Bandol (Francia)
Evaluación:
% de retención del alargamiento a la rotura después de 160 KLy
Otros Aditivos:
Debido al mecanismo de acción, aditivos como antiniebla, antiestáticos, coadyuvantes de procesado, etc., pueden afectar a la duración del film generalmente de forma adversa [5].
Producción:
Para evitar posibles puntos débiles, el film debe tener un espesor homogéneo y un alto nivel de dispersión de los aditivos.
Factores Ambientales
La estructura debe resistir las condiciones climáticas y soportar la cubierta, la cual a su vez debe estar fijada adecuadamente al soporte. Debido a la retención de calor, absorción de luz y corrosión del soporte, el film frecuentemente se desgarra en el punto de contacto con la estructura. Este problema puede minimizarse, cubriendo este punto de contacto con varias capas de film de PE o pintándolo con una capa fina de pintura vinílica-acrílica. (Figura 4).
![Figura 4: Efecto de las cargas en el tiempo de vida de un film durante exposición al natural (Bandol, Francia) [6] Figura 4: Efecto de las cargas en el tiempo de vida de un film durante exposición al natural (Bandol, Francia) [6]](https://img.interempresas.net/fotos/36338.jpeg)
Fílme de LDPE – Espesor: 150µm
Formulación:
0.5% Estabilizantes a la luz
Exposición:
Soporte de Aluminio – Bandol (Francia)
Evaluación:
KLy para una disminución del 50% del valor inicial del alargamiento a rotura
Diseño:
Cuanto más cerca estén las plantas a la cubierta del invernadero, mayor será el efecto de rociado de pesticidas sobre el filme, causando una mayor degradación. Algunas estructuras están diseñadas para aumentar el calor al interior del invernadero, lo cual influirá también en la duración del film si el sistema estabilizante no ha sido elegido correctamente.
Radiación solar:
El nivel de radiación solar (J/m2, KLy) es uno de los parámetros que más afectan a la duración del film agrícola. Debido a la amplia variación sobre la superficie de la Tierra, se pueden esperar diferentes tiempos de servicio dependiendo de las diferentes regiones y diseños del filme. (Figura 6).
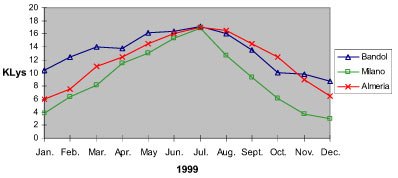
Temperatura, lluvia, viento, granizo, etc., también tienen su influencia en la duración de la cubierta de filme.
Tipo de cultivo:
La naturaleza del cultivo tendrá influencia en la selección del tipo y frecuencia de aplicación de los compuestos agroquímicos usados, por lo tanto afectará a la duración del filme.
Fitosanitarios:
Los pesticidas más agresivos son los que contienen azufre, y en menor medida los compuestos halogenados, debido a la producción de ácidos en su descomposición, los cuales pueden interaccionar de forma adversa con los aditivos de la formulación del film agrícola, por ejemplo con los HALS, lo que dará lugar a un efecto de antagonismo con una importante disminución de la duración del material de cubierta.
En este artículo se discutirá otro factor de gran importancia en la duración del film de invernadero como es la forma física de los estabilizantes a la luz. Para ello se compararán los resultados obtenidos sobre la duración de los filmes para invernadero cuando los estabilizantes a la luz se incorporan como mezcla en polvo o en forma de mezcla libre de polvo (No Dust Blend – NDB).
![Figura 5: Efecto del material de la estructura del invernadero [8] Figura 5: Efecto del material de la estructura del invernadero [8]](https://img.interempresas.net/fotos/36401.jpeg)
Introducción a los aditivos NDB (No Dust Blends)
El consumo de los estabilizantes en polvo ha pasado de un 60% en 1995 a menos del 40% hoy en día. Aunque ha habido un pequeño aumento del consumo de productos granulados (aditivos individuales y mezclas binarias) la mayor contribución a este menor crecimiento se ha debido al importante crecimiento de las mezclas libres de polvo (NDB), las cuales han pasado de un 8% a más del 25% durante el mismo período.
A primera vista, se podría concluir que este aumento del uso de NDBs es una simple consecuencia de la tendencia del mercado a usar aditivos en forma física libre de polvo o con bajo contenido en polvo. Si este fuera el caso, entonces seria de esperar un aumento similar de otras formas físicas con bajo polvo como las escamas, pastillas, gránulos, etc. En realidad, existe un gran número de ventajas técnicas y comerciales asociadas al NDB, algunas obvias y fáciles de medir, otras menos obvias y más difíciles de cuantificar, las cuales han sido las verdaderas directrices de este rápido aumento [14-17].
¿Qué es una Mezcla Libre de Polvo - No Dust Blend (NDB)?
Además de Antioxidantes y Estabilizantes a la luz, existe una amplia gama de aditivos usados en la formulación de polímeros. Estos pueden ser de bajo punto de fusión, higroscópicos, de baja estabilidad térmica, pulverulentos, irritantes e incluso tóxicos. Todas estas características dan lugar a inconvenientes que pueden traducirse en diversos problemas como una pérdida física del aditivo, adherencia, deterioro del ambiente de trabajo, aumento del tiempo de cambio de formulación, problemas de alimentación, bloqueo, segregación de la pre-mezcla, disminución de actividad, etc.
El NDB no sólo supera las dificultades mencionadas anteriormente , sino que además introduce un número de ventajas inicialmente menos obvias. Para determinar la composición de un NDB es necesario conocer el nivel final de cada aditivo individual en el polímero. Una vez conocida, hay que calcular la composición del NDB mediante un procedimiento relativamente simple (ver tabla 1).
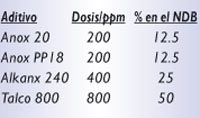
Características y Ventajas de las Mezclas Libres de Polvo
No es el objetivo de esta publicación el discutir en detalle todas las ventajas presentadas en la tabla 2, sin embargo, algunas de ellas que son de relevante importancia para la producción del film agrícola, serán brevemente examinadas seguidamente.
Características | Ventajas | Principal Contribución |
Producto Poco Polvoriento | Reduce riesgos de explosión
Más limpio, menos nocivo,medioambiente Rápido cambio de grados/Menor tiempo de limpieza Mínima pérdida de producto por extracción Reduce el riesgo de contaminación entre productos |
Seguridad
Confort en el trabajo Productividad Menor consumo de aditivos Calidad de polímero |
Alta Resistencia a la Abrasión | Simplicidad en el manejo
Menor riesgo de compactación durante el almacenaje Retención de las propiedades de fluidez |
Productividad
Productividad Productividad |
Buena Fluidez | Reducción de los problemas de alimentación
Precisión en el dosificado Fácil empaquetado y descarga |
Productividad
Menor consumo de aditivos Manejo |
Alta Velocidad de Fusión | Fácil incorporación en el polímero
Buena dispersión en el polímero |
Productividad
Menor consumo de aditivos |
Efecto de la Mezcla ("Alloy) de los Aditivos | Amplio rango de utilización de los aditivos
Fácil incorporación en el polímero Buena dispersión en el polímero Mejora del comportamiento de aditivos |
Amplia elección de formulación
Productividad Menor consumo de aditivos Reducción de costes |
Amplio Rango de Formulaciones | Posible disminución del nivel de aditivos
Posibilidad de formulación óptima |
Aumento de beneficios
Óptimo Costes-Comportamiento |
Composición del NDB constante | Menos polímero fuera de especificación
Reducción de sobredosificación de aditivos Propiedades del polímero estables Menor costes en control de calidad Menor tiempo de homogenización Menor posibilidad de error humano |
Aumento de beneficios
Menor consumo de aditivos Menos reclamaciones Mayor calidad de producto Aumento de beneficios Productividad |
Inclusión de Aditivos "Difíciles"
Productos de Baja Fusión Productos Líquidos Aditivos no fundentes |
Menos problemas de aglutinamiento
No alimentación especial para líquidos Reducción del polvo Dispersión |
Productividad
Productividad Higiene Comportamiernto |
Formulación en un único grano | Menor volumen de almacenaje que en polvo
Un producto reemplaza muchos Reducción del error humano Contacto con un único distribuidor Reducción del capital/equipo necesario Reducción del mantenimiento necesario Simplificación del proceso de producción |
Costes de operación, Logística, Admin, Compras,...
Aumento de beneficios Resolución de problemas Capital, costes de operación Costes de operación Costes de operación y mano de obra |
Así, desde el punto de vista de higiene y seguridad en el trabajo, no existen riesgos de explosión debida a la dispersión de polvo en el aire. Además, se consigue una mejora general en la higiene de la planta, el uso de NDB elimina la irritación y problemas de toxicidad que algunos trabajadores sufren debido a ciertas operaciones de manipulación de productos.
La reducción de los niveles de polvo en la planta tiene otras ventajas, tales como, el riesgo de contaminación de un tipo de aditivo con otro se reduce significativamente, con la consecuente reducción de problemas en el control de calidad del filme. La otra ventaja, derivada de la reducción de los niveles de polvo, es la reducción sustancial de los tiempos de limpieza del equipamiento (algunas veces menos de la mitad del tiempo necesario cuando se usan polvos). Esto lleva a una repercusión directa en la productividad debido a un menor tiempo de paro en los equipos.
La ventaja en coste cuando se utilizan NDBs en vez de polvos, o incluso gránulos,, es debida a la no existencia de pérdidas de producto debido al sistema de extracción de polvo durante las actividades de manipulación y alimentación. Dependiendo de la naturaleza del aditivo, normalmente, la pérdida en el sistema de extracción del aditivo en forma polvo está comprendida entre el 1 y el 7%. Debido al elevado precio de los aditivos con respecto al precio del polímero, el uso de un NDB producirá a un sustancial ahorro de costes.
Por ejemplo, tomamos el caso de una planta que usa 50 t/año de un complejo de níquel en polvo a un precio genérico de 25 $US /kg y que se pierde por extracción un 3% (1,5 t/año). El valor de la pérdida de producto en la planta es de 37.500 $US, que se resta directamente de los beneficios de la compañía. Como algunos aditivos se emplean en varias plantas de la misma compañía, cada una sufre su propia pérdida, el valor total de productos perdidos en la extracción será sustancialmente mayor. Además del coste directo de la pérdida física de aditivo en polvo, existe el coste de recuperación del material extraído.
Los problemas típicos asociados con la alimentación en polvo son diversos en los puntos críticos del sistema de alimentación e incluso en la fusión. Se puede llegar a la segregación de la mezcla de aditivos y consecuentemente a variaciones en la concentración final en el polímero. Esto puede dar lugar a polímeros fuera de especificación donde los niveles de aditivo son demasiado bajos y también sobredosificación en el polímero cuando la concentración de aditivo es demasiado alta. Ambas posibilidades de error tienen un efecto negativo en el coste asociado a ellos y con el uso de NDBs este problema se puede eliminar fácilmente.
Todos los beneficios señalados anteriormente en la tabla 2, contribuyen a una mayor productividad, incremento de la calidad del producto, en la higiene y seguridad de la planta y a significativas reducciones de coste.
A continuación, a título ilustrativo, se comparará el efecto de la forma física de los estabilizantes a la luz (polvo vs. NDB) en su comportamiento en el film de invernadero. En particular, se especificará el efecto de mezcla de los aditivos cuando se usan en forma NDB y se mostrarán los beneficios en el comportamiento cuando se usan en aplicaciones de invernadero.
Parte experimental
Todos los films se prepararon usando los materiales, la maquinaria y las condiciones detallados a continuación.
- Polímero: LDPE (Escorene FC 20, densidad 0,922 g cm-3, MFI 0,25 g/10 min)
- Procesado: Brabender PL2000 extrusor monotornillo, 220°C
- Producción de film: Plasticisers, 220°C
- Espesor de film: 50, 100 y 170 mm
- Sistema UV*:
- 1:1 NiQ-1 : UVA-1
- concentración UV: 0, 0,25%, 0,5% y 0.75%
* - Los estabilizantes a la luz usados están detallados en el Apéndice I.
Envejecimiento acelerado:
Todos los films fueron soportados sobre plástico negro y sometidos a un envejecimiento UV acelerado en el sistema Atlas Ci65 Weatherometer, bajo las siguientes condiciones de irradiación:
- Radiación a 340nm: 0,35 W/m2
- Humedad Relativa: 50 %
- Temp. del panel negro: 63 °C
- Temp. de la cámara: 42 °C
Ensayos mecánicos:
La pérdida de las propiedades mecánicas se evaluó frente al tiempo de irradiación empleando un equipo universal INSTRON 4301 . Se tomó como criterio de evaluación el tiempo para obtener una disminución del 50% en el valor inicial del alargamiento a rotura.
Resultados
El efecto del empleo de un NDB en lugar de una mezcla en polvo de estabilizantes a la luz (0.25% NIQ-1+0,25% UVA-1) se presenta en la figura 8. Con el menor espesor de filme, los comportamientos del NDB y de la mezcla en polvo son virtualmente idénticos. Los films estabilizados con la forma física libre de polvo NDB presentan un mejor comportamiento UV que los filmes estabilizados con la mezcla en polvo al aumentar el espesor del filme. Hay que señalar que, como cabía esperar, independientemente del uso de la mezcla en polvo o en NDB, cuanto mayor es el espesor del film mayor es la estabilidad del mismo frente a la luz.
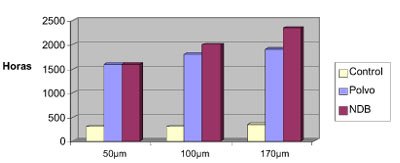
Película de LDPE
Formulación:
0,5% 1:1 NiQ-1:UVA-1
Exposición:
WOM Ci65, 63°C BPT, 0.35 W/m2, 50% RH
Evaluación:
Tiempo para una disminución del 50% del valor inicial del alargamiento a rotura
Los filmes producidos usando el NDB, de espesor 170 µm superan en fotoestabilidad a las producidas con las mezclas en polvo en un 25% aunque el paquete estabilizante a la luz añadido en cada caso fue el mismo (0,5% concentración total).
Los datos presentados en la figura 9 indican claramente que, para un mismo paquete estabilizante a la luz (por ejemplo 1:1 NIQ-1 : UVA-1), el uso del NDB lleva a una mejora de comportamiento con respecto a la mezcla en polvo. Esta diferencia en la duración, entre las mezclas libres de polvo y las mezclas en polvo, llega a ser mucho más significativa cuando la concentración total de estabilizantes a la luz se incrementa.
Cuando el film de mayor espesor y mayor concentración de la mezcla de estabilizantes a la luz, se estudió (170µm y 0,75% concentración total de estabilizantes UV) se obtuvo un aumento en la estabilidad de los filmes con NDB del 30% con respecto al mismo film aditivado con polvo. Esta mejora puede llevar a significativas ventajas en la reducción de la cantidad de complejo de níquel requerido para conseguir la misma estabilidad que cuando se usan los aditivos en forma de polvo.
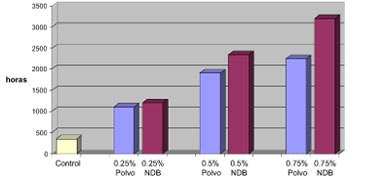
Película de LDPE – Espesor 170µm
Formulación:
1:1 NiQ-1:UVA-1
Exposición:
WOM Ci65, 63°C BPT, 0.35 W/m2, 50% RH
Evaluación:
Tiempo para una disminución del 50% del valor inicial del alargamiento a rotura.
Existen otras razones por las cuales la forma física del NDB puede ofrecer una mejora sobre la simple mezcla en polvo. Entre estas se puede mencionar, el conseguir una proporción constante de NIQ-1 : UVA-1 y distribución homogénea en el film cuando se usa un NDB, a diferencia de la variación que se produce cuando se emplea una mezcla en polvo. El comportamiento mecánico de este tipo de film es reflejo de esta mejor actividad estabilizante derivada de la estequiometría constante y de la homogeneidad de la distribución de los aditivos. Además, menor cantidad de producto se perderá en forma de polvo con el NDB que con el polvo, por lo tanto, se obtendrá un ligero aumento del nivel de estabilización en el polímero. Una de las mayores contribuciones a la estabilidad y a la diferente actuación es el denominado efecto de mezcla, "alloy", observado en algunos NDBs. Este efecto, será discutido en la próxima sección.
El efecto de mezcla ("Alloy") de los aditivos en forma NDB
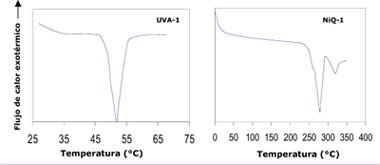
Cuando se prepara una mezcla libre de polvo de NIQ-1+UVA-1, el comportamiento de fusión de los dos componentes cambia debido a la disolución de un componente en el otro o simplemente por un efecto de disminución del punto de fusión.
La figura 11 muestra los termogramas de DSC obtenidos con un NDB 1:1 NIQ-1:UVA-1, donde el pico a aproximadamente 270°C desaparece y sólo queda el de baja temperatura (debido al UVA-1).
![Figura 11:Análisis DSC del NDB [NiQ-1 + UVA-1] (50:50)Velocidad de calentamiento: 10°C/min Figura 11:Análisis DSC del NDB [NiQ-1 + UVA-1] (50:50)Velocidad de calentamiento: 10°C/min](https://img.interempresas.net/fotos/36389.jpeg)
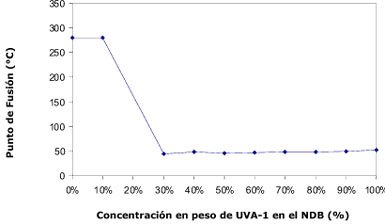
En general, puntos de fusión superiores a 210°C se consideran problemáticos para el procesado de poliolefinas, especialmente en el caso de polietileno, ya que estaría a temperaturas superiores y por encima de las temperaturas típicas de procesado. En dichos casos se obtiene una dispersión de "partículas" ya que los aditivos se encuentran en forma de partículas separadas, como pigmentos, en la matriz polimérica. Por el contrario, si el punto de fusión de los aditivos está por debajo de la temperatura de procesado, se obtendría una dispersión del tipo "disolución" (homogénea). Para un valor determinado de cizalla, debería ser más fácil obtener una dispersión homogénea de aditivos cuando las características de fusión de los aditivos están por debajo de la temperaturas de procesado (como en el caso del NDB) y será más difícil con aditivos que fundan a temperaturas superiores alas temperaturas de procesado (como en el caso del NIQ-1 en polvo).
El comportamiento de fusión del NIQ-1 se ve afectado cuando forma parte del NDB, tal y como se muestra en la figura 12, dando lugar a una disminución del punto de fusión del NIQ-1. Con el menor punto de fusión de un NDB, se consigue la homogeneización del sistema de aditivos en las condiciones de procesado de las poliolefinas.Aunque este efecto pueda tener lugar con algunas proporciones de la mezcla de NIQ-1+UVA-1, éste será más pronunciado en el caso del NDB. Por consiguiente, bajo ciertas condiciones experimentales, será más fácil obtener una dispersión homogénea con un NDB [NIQ-1+UVA-1] (50:50 o 67:33 que son las proporciones más frecuentes) que con la correspondiente mezcla en polvo. Por lo tanto, se puede asegurar una mayor eficiencia de actuación en la estabilización del NDB, tal y como se ha puesto de manifiesto en los resultado anteriormente mostrados.
La aditivación de un NDB [NIQ-1+UVA-1] ofrece distintas ventajas al usuario en términos de incorporación, dispersión y uniformidad en el filme:
- Un comportamiento uniforme de fusión de los dos componentes.
- Una disminución del punto de fusión de ambos componentes.
- Una proporción constante NIQ-1:UVA-1 en todo el material.
Se favorece la constancia en la concentración y distribución de los aditivos en la formulación, y se reducirá el número de "puntos débiles" en el film lo dará lugar a un aumento de las propiedades de estabilización frente a la luz.
Esto se ha confirmado en los resultados mostrados en la figuras 8 y 9 donde se observa una significativa ventaja en la estabilidad obtenida por el uso del NDB co respecto a la correspondiente mezcla en polvo. Considerando un productor de film que produce 10 t/año de film de invernadero estabilizado al 1% de NIQ-1:UVA-1 (1:1). Para obtener una estabilidad similar, el NDB puede ser dosificado un 20% menos que la correspondiente mezcla en polvo. Esto se traduce en una ahorro de costes del orden de 125.000 Euros por el uso de la mezcla libre de polvo (No Dust Blend). Estos ahorros pueden ser adicionales a los ahorros debidos a la reducción del producto en polvo perdido por extracción y también por los aumentos de precisión en la dosificación. Finalmente, también existe la ventaja en la higiene y seguridad cuando se usa la forma física NDB.
Conclusiones
Además, se ha presentado una nueva forma de aditivos, llamada mezcla libre de polvo (No Dust Blends-NDB).Se han puesto de manifiesto las ventajas que supone el uso del NDB a través de ejemplos de su comportamiento comparativo co respecto al uso de aditivos en polvo en films agrícolas. El uso del NDB en vez de polvos o gránulos, puede fácilmente llevar a la obtención de significativas ventajas en la productividad. También se consigue un aumento de la calidad del producto, mejoras en la higiene y seguridad en las plantas así como interesantes reducciones de costes. Se mostró también que la incorporación de aditivos de alto punto de fusión, como es el caso de productos NIQ, en un formulaciones de polietileno se puede facilitar por el uso del NDB. El aumento de la velocidad de fusión y la fácil dispersión en el polímero del NDB lleva a mejoras en la estabilidad del 20 al 30%. Este incremento en la actividad de los aditivos puede llevar a una reducción en los niveles de aditivo para alcanzar las especificaciones técnicas requeridas con la consiguiente reducción de costes.
Referencias
[2] J.P. Jouet, Plasticulture, No 120, pp 108 – 126, (2001)
[3] M. de la Cruz, B. W. Johnson, Great Lakes Polymer Additives Bulletin 002206, Jun 2000
[4] A. Lichtblau, M. Zah, Kunstoffe plast europe, pp 716-19, May 1998
[5] F. Henninger, E. Pedrazzetti, Arabian Journal for Science & Engineering, 13, 4, pp 473 – 486, Oct 1988
[6] M. de la Cruz, GLCC Applications Report AR 27.01, 2001
[7] M. de la Cruz, GLCC Applications Report AR 08.98, July 1998
[8] R. Farris, S. Costanzi, GLCC Applications Report AR 13.98, Nov 1998
[9] US Patent No. 5,240,642
[10] US Patent No. 5,844,042
[11] World Patent No. WO 99/55768
[12] World Patent No. WO 99/52977
[13] L. Pallini, Plastic Additives, No. 3, Oct 1992
[14] C. Callierotti, L. Pallini, G. Sandre, R. Lee, M. Wu, K. Keck-Antoine, B.W. Johnson, Addcon World 2000, paper 4, Basle, Oct 2000
[15] K. Keck-Antoine, B.W. Johnson, Polyethylene 2001, Zurich, Feb 2001
[16] B.W. Johnson, K. Keck-Antoine, R. Lee, C. Callierotti, Plastics Additives & Compounding, 3 (6) pp 14-21, June 2001
[17] B.W. Johnson, K. Keck-Antoine, R.E. Lee, O. Kuvshinnikova, C. Callierotti, J.W. Kim, Polyolefins Retec 2001, Houston, Texas, Feb 2001
Apéndice
UVA-1: Lowilite 22 2-hydroxy 4-octoxy benzophenone
NiQ-1: Lowilite Q84 2,2’-thiobis(4-tert-octyl-phenolate)–N– butylamine–Nickel (II)