Engel en la feria Fakuma 2018: pabellón A5, stand 5204
Producción flexible de lotes pequeños
Desde vehículos hasta aparatos electrónicos, cada vez se ofrecen más productos en variaciones de diseño cada vez más diversas. Para la fabricación, esto se traduce en lotes más pequeños. En la Fakuma 2018, del 16 al 20 de octubre en Friedrichshafen, Alemania, Engel Austria, firma representada por Helmut Roegele, muestra cómo se pueden reproducir lotes pequeños en el moldeo por inyección con la eficiencia y la rentabilidad de la producción a gran escala con dos innovadoras aplicaciones.
Fabricación de variantes con un cambio totalmente automatizado
Tres novedades a la vez
Con una célula de fabricación totalmente integrada, en la que se producen calibradores de dos piezas de ABS, Engel celebra tres novedades a la vez en la Fakuma 2018. Por primera vez, se presenta una solución totalmente automatizada para el cambio rápido de insertos de molde; al mismo tiempo, se presenta al público el nuevo tamaño constructivo 120 de la serie totalmente eléctrica y sin columnas e-motion TL, con una fuerza de cierre de 1.200 kN; en tercer lugar, se presenta el distribuidor de agua para ajuste de la temperatura electrónico e-flomo con una funcionalidad ampliada.
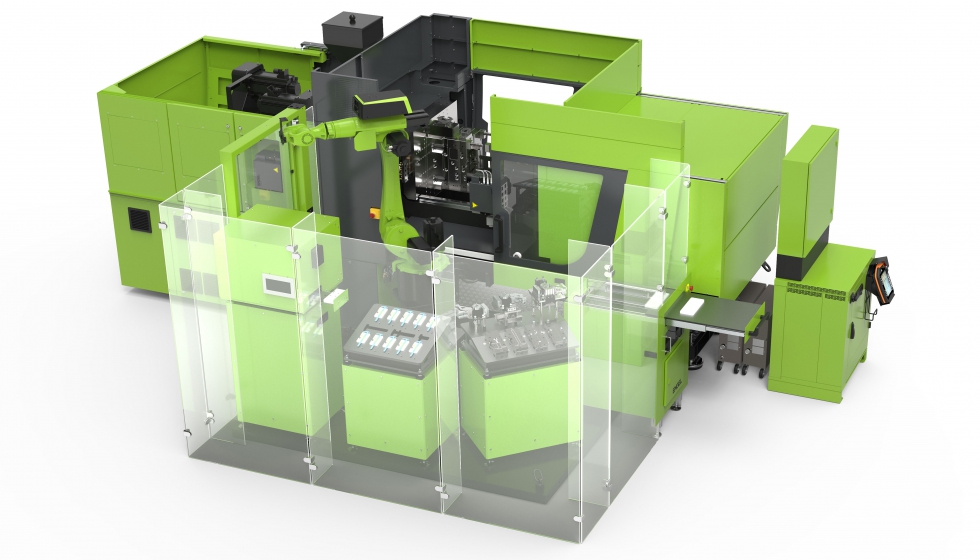
Las cantidades de menos de 1.000 unidades representan un reto especial en el moldeo por inyección. Para poder reproducir una gran cantidad de variantes de forma rentable, a menudo se emplean moldes con insertos intercambiables. Ahora, en la Fakuma, Engel da un paso más allá junto con Braunform (Bahlingen, Alemania) y otros socios de sistema. La solución de sistema que se presenta allí permite un cambio totalmente automatizado de los insertos de molde en tan solo un minuto. Para ello, la máquina de moldeo por inyección Engel e-motion 170/120 TL está equipada con un molde con el sistema de cambio rápido patentado de Braunform.
Con el fin de demostrar el potencial de la nueva solución, los dos componentes de geometría diferente del calibrador se fabrican de manera consecutiva con un cambio rápido. Después de solo tres inyecciones, la máquina de moldeo por inyección comunica al robot de brazo articulado integrado Engel easix que se ha alcanzado el lote y desbloquea los insertos de molde. En primer lugar, el robot toma el último componente que se ha fabricado; a continuación, cambia la pinza y cambia los insertos de molde. De pieza buena a pieza buena, este proceso dura tan solo un minuto. La comunicación entre la máquina de moldeo por inyección y los periféricos tiene lugar a través de authentig, el MES de TIG, una filial de Engel. El software facilita los registros de datos de las piezas a la máquina y al robot.
Asistencia 4.0 para garantizar el máximo porcentaje de piezas buenas
Uno de los desafíos que plantea esta aplicación es que ambos componentes presentan pesos de inyección muy diferentes. Para producir una pieza buena ya desde la primera inyección después del reequipamiento, la máquina de moldeo por inyección se optimiza continuamente a sí misma con ayuda de tres sistemas de asistencia inteligentes del programa inject 4.0 de Engel. Mientras que iQ weight control reajusta el volumen de fundido para cada inyección, iQ clamp control calcula la fuerza de cierre óptima y la configura automáticamente. El tercer sistema de asistencia, iQ flow control, regula las diferencias de temperatura en el circuito distribuidor de agua refrigerante a partir de los valores de medición calculados por e-flomo y ajusta la potencia de las bombas en los atemperadores e-temp a las condiciones actuales del proceso.
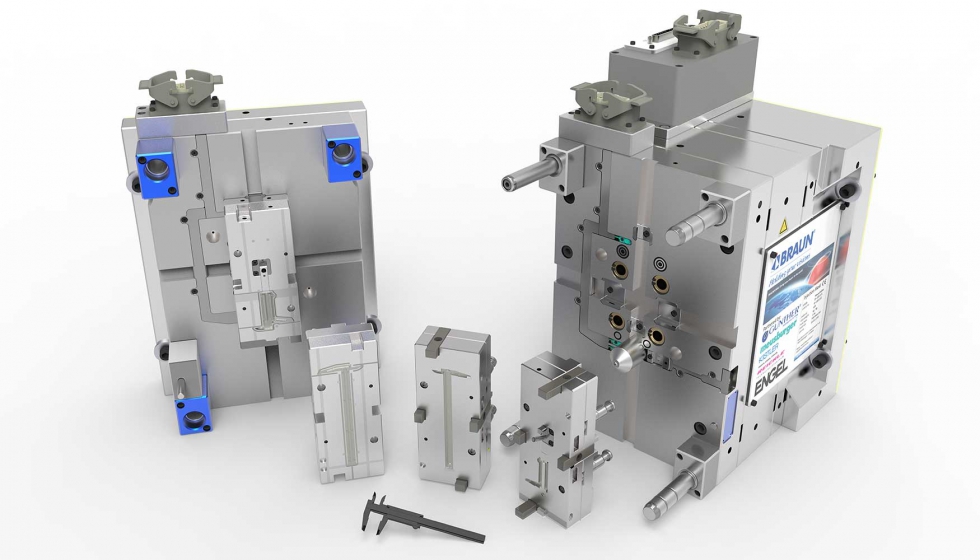
A su vez, el distribuidor de agua para ajuste de la temperatura electrónico e-flomo también contribuye a acortar los tiempos de equipamiento. El soplado automatizado y secuencial del circuito distribuidor en el molde garantiza que se elimine completamente el agua y, en su caso, la suciedad que se encuentre en los canales atemperadores antes de la retirada del molde o del inserto de molde. Por otra parte, esta nueva función también garantiza una ventilación óptima de los canales atemperadores en la instalación. El proceso automatizado ahorra tiempo con respecto al soplado manual convencional y, además, permite prolongar los intervalos de mantenimiento del molde. A menudo, en el método manual, el aire comprimido no fluye uniformemente por todos los canales, de manera que puede quedar agua residual en los canales y provocar corrosión. La automatización elimina este riesgo.
Todas las unidades integradas de forma compacta
Una gran atracción en la Fakuma es el diseño extremadamente compacto de la célula de fabricación, en cuyo centro se encuentra el robot easix. Este se encarga de toda la manipulación de los insertos de molde y los componentes, de la identificación de las piezas moldeadas por inyección y de su montaje, así como de la retirada de los calibradores. La máquina de moldeo por inyección, la estación para las pinzas y los insertos de molde, la impresora láser, el dispositivo de montaje y la unidad transportadora están dispuestos en forma de estrella alrededor del robot.
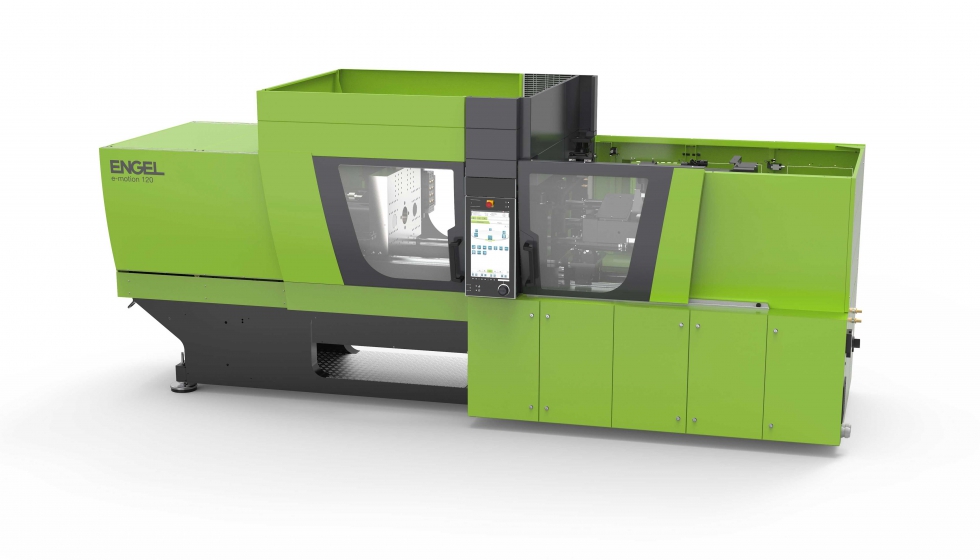
Dos factores contribuyen principalmente a la disposición extremadamente compacta de los distintos componentes. Por un lado, las áreas restringidas del robot easix, que se pueden definir libremente; por otro lado, la unidad de cierre sin columnas de la máquina de moldeo por inyección e-motion TL. El acceso sin barreras a la zona del molde hace que el robot pueda acercarse mucho a la unidad de cierre, sin limitaciones de movimiento.
Con la célula de fabricación totalmente automatizada, los socios de sistema Engel y Braunform se dirigen a los clientes que fabrican artículos parecidos en cantidades reducidas o bien con un gran número de variantes. Los productos típicos incluyen, por ejemplo, bienes de consumo como utensilios para escribir, piezas técnicas en la industria automotriz y eléctrica y una serie de productos en el sector de la tecnología médica.
Tecnología sin columnas y totalmente eléctrica: con una fuerza de cierre de 1.200 kN
La nueva e-motion 120 TL, con una fuerza de cierre de 1.200 kN, es la máquina más grande de su serie. Con esta ampliación, Engel sigue la tendencia de un creciente uso de moldes de cavidad múltiple. Sin columnas que molesten, las platinas de montaje de los moldes se pueden aprovechar al máximo, de modo que los moldes grandes caben en máquinas de moldeo por inyección relativamente pequeñas. Esto también representa una ventaja en la fabricación de componentes de geometría compleja, que requieren tiranoyos y correderas en el molde. El tamaño del molde ya no es el factor que decide el tamaño de la máquina, sino la fuerza de cierre que se necesita realmente. Esto supone un ahorro de costos tanto en la inversión nueva como durante el estado operativo.
Para garantizar una larga vida útil del molde y una calidad elevada constante del producto, las máquinas de alto rendimiento totalmente eléctricas y sin columnas de ENGEL están dotadas de un paralelismo entre platinas altamente sensible. Las máquinas de esta serie se emplean a menudo para la producción de piezas de precisión muy pequeñas en la industria de la electrónica y la tecnología médica.
Un proceso para un sinfín de opciones de diseño
Diseño, estructura, función en un solo paso del proceso
Con el perfeccionamiento de su tecnología foilmelt, Engel presenta en la Fakuma una aplicación de IMD rodillo a rodillo, con una flexibilidad nunca vista hasta ahora. El desarrollo conjunto de los socios de sistema Engel, Leonhard Kurz (Fürth, Alemania), Schöfer (Schwertberg, Austria) e Isosport Verbundbauteile (Eisenstadt, Austria) permite termoformar, inyectar y troquelar las estructuras superficiales más diversas de rodillo a rodillo con un cambio rápido en el molde.
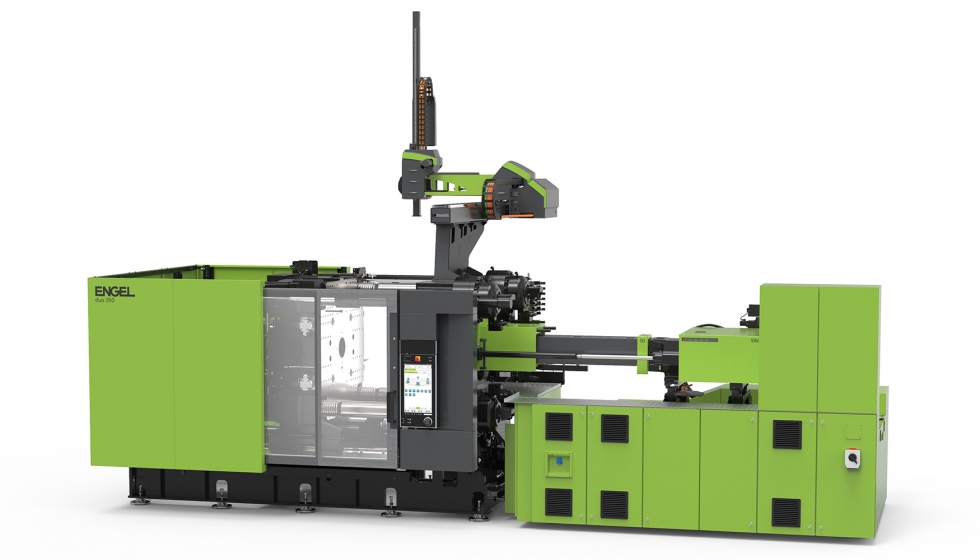
Destaca el amplio abanico de combinaciones de materiales posibles. Desde el rodillo se pueden tratar tanto sistemas de láminas multicapa con superficie pintada como sistemas estructurados, con retroiluminación o porosos como la madera, así como láminas funcionales con electrónica capacitiva. Para la inyección trasera entra en juego, además de materiales típicos como el ABS, el PC o el PC/ABS, también el PP. Para cambiar de decoración, estructura y funcionalidad solamente hay que cambiar el rodillo, sin cambiar el molde.
Con la fabricación de piezas de muestra complejas, tridimensionales y con decoraciones distintas en una máquina de moldeo por inyección duo 1060/350 con robot lineal viper 20 integrado, Engel demuestra la elevada flexibilidad del método para la producción en serie en su stand de la feria. El grupo destinatario son, entre otros, los fabricantes de componentes visuales para el interior de vehículos, así como la industria de la teletrónica y de los electrodomésticos.
A partir de enero del 2019, la célula de fabricación estará disponible en el centro tecnológico de Engel, en la planta matriz de Schwertberg, para demostraciones tecnológicas, pruebas de materiales y desarrollos específicos para clientes.
Cerramiento de protección modular y altamente flexible
Otra novedad que presenta la célula de fabricación foilmelt en la Fakuma es el nuevo cerramiento de protección desarrollado por Engel según EN ISO 14120, que estará disponible a partir de octubre para todas las máquinas de moldeo por inyección automatizadas y las soluciones de sistema integradas. De nuevo, en el desarrollo se hizo especial hincapié en una elevada flexibilidad combinada con una gran rentabilidad. El concepto modular permite una configuración y un montaje muy sencillos. La amplia variedad de paneles de protección y elementos funcionales, como vanos, puertas giratorias y puertas correderas, también permite realizar diseños individuales de forma rentable.