Conceptos de utillaje para la mejora del mecanizado de componentes aeronáuticos de baja rigidez
Las funciones de un utillaje tradicionalmente incluyen la localización y la fijación de la pieza, junto con la capacidad para soportar las fuerzas existentes durante el proceso de fabricación[1]. La tendencia actual en fabricación es la utilización de utillajes que permitan un mayor grado de flexibilidad, reconfigurabilidad y automatización[2]. Habitualmente, los utillajes son diseñados como un subsistema[3], y de manera independiente a otros aspectos, como los tiempos de ciclo o el propio proceso de corte. Sin embargo, forman un mismo sistema máquina-utillaje-pieza-proceso, cuyas interacciones pueden llegar a influir de manera importante en el resultado final, afectando a la precisión, la calidad o el coste del componente fabricado.
En lo referente a los aspectos puramente técnicos, los procesos de fabricación cada vez demandan mayores grados de precisión y calidad, especialmente en sectores de alta exigencia como el aeronáutico/aeroespacial, energético, médico o el equipamiento científico. La capacidad de un proceso para garantizar un alto rendimiento depende de los elementos empleados, y aunque el elemento principal es la propia máquina, el subsistema utillaje proporciona la unión entre la máquina y la pieza y afecta a aspectos como la rigidez, la estabilidad del proceso, la dinámica o la precisión [3] que determinan el resultado del proceso de mecanizado.
En las series cortas o piezas unitarias, los requisitos del utillajes son más exigentes porque hay que asegurar su funcionamiento con fiabilidad y tiempos de configuración del utillaje reducidos, por lo que factores como las flexibilidad o adaptabilidad toman mayor relevancia.
Con el objetivo de solucionar estas limitaciones, se emplean cada vez más utillajes inteligentes basados en sensores, actuadores y algoritmos de control, que permiten la reconfiguración y la corrección de problemas como el desalineamiento, las deformaciones o las vibraciones mediante el control de la posición y de las fuerzas de amarre, de manera que se mejora la precisión. Sin embargo, estas soluciones son complejas como el concepto Swarmitfix [4], y tienen un coste elevado, comprometiendo la viabilidad económica de la inversión en muchas ocasiones.
En la fabricación de componentes en la industria aeronáutica son muy importantes la productividad de los procesos y la calidad final, principalmente en grandes componentes con baja rigidez estructural que suelen presentar problemas de vibraciones y deformaciones durante el mecanizado, limitando el resultado de las operaciones. El diseño y desarrollo de utillajes para el mecanizado de piezas de baja rigidez ha sido objeto de diversos análisis, debido a su influencia en la calidad de la pieza final y en el coste de producción [5]; buscando alternativas que permitan dar una solución a los problemas mediante un diseño de utillaje adecuado. Así mismo, los componentes esbeltos o con altas relaciones de aspecto varían significativamente su comportamiento dinámico durante el mecanizado debido a la eliminación de material; por lo que el comportamiento del utillaje debe ser capaz de adaptarse
a esas variaciones. En este trabajo se analiza el comportamiento de una carcasa de la turbina de baja presión (LPT, por sus siglas en inglés) de un motor de avión, de cara a analizar los puntos de mejora en el utillaje para reducir las vibraciones durante el mecanizado. La aparición de vibraciones limita las condiciones de corte reduciendo la productividad, y la calidad e integridad superficial del componente se ve afectada.
Inicialmente se realiza un análisis de las condiciones del utillaje actual evaluando las condiciones de contorno que afectan a la pieza durante el amarre, y se identifican la forma de trabajo y los aspectos de mejora.
A continuación se presentan diferentes alternativas para reducir y controlar el nivel de la vibración en el proceso mediante la introducción de elementos adicionales en el utillaje. Las alternativas analizadas se basan fundamentalmente en variar de forma controlada el comportamiento estructural del componente mediante los elementos de amarre del utillaje, variando las condiciones de amarre. Las soluciones planteadas incluyen:
- Ventosas de vacío para añadir rigidez al componente.
- Introducción de una deformación controlada en la pieza para mejorar sus condiciones de amarre y su comportamiento dinámico.
- Utilización de absorbedores de vibración.
Los resultados muestran que es viable la modificación del comportamiento de la pieza aumentado la rigidez y el amortiguamiento del conjunto mediante la introducción de elementos en el utillaje, permitiendo mejoras en el proceso de mecanizado.
1. Descripción de la problemática
El objetivo principal consiste en reducir las vibraciones durante el mecanizado de una carcasa de turbina como la mostrada en la Figura 1, que está hecha de Inconel 718 y tiene unas dimensiones características de 1.800 mm de diámetro máximo, 550 mm de altura y espesores entre 3 y 6 mm. La actividad se centra en el análisis del comportamiento de la pieza durante el proceso de torneado de acabado de la cara interior, que consiste en el copiado de la superficie y la realización de varias ranuras a diferentes alturas. La aparición de vibraciones en esta operación limita las condiciones de corte y reducen la vida de la herramienta, con el resultado de una baja calidad e integridad superficial en el componente.
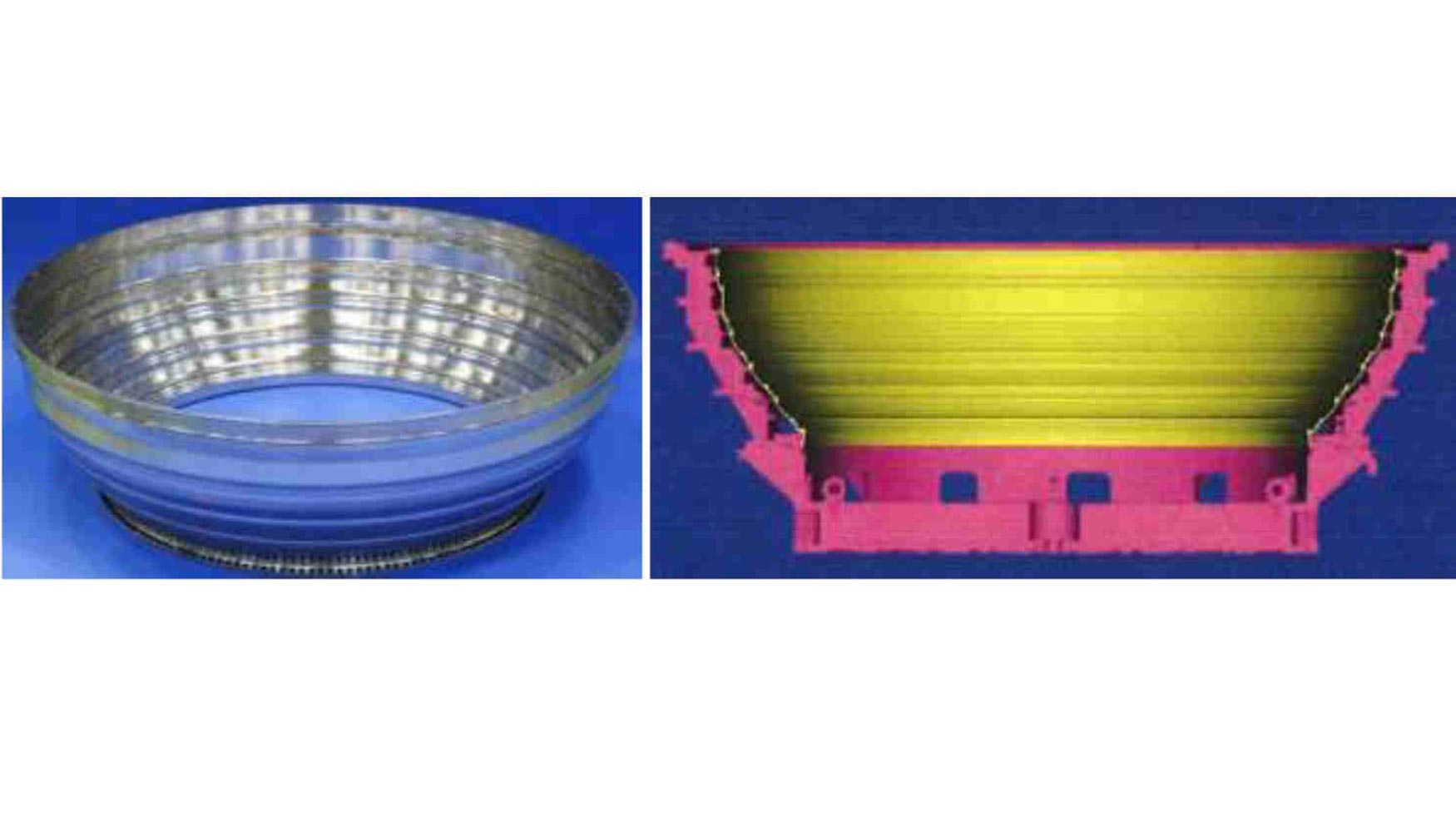
1.1. Utillaje actual y condiciones de amarre
La solución del utillaje empleado actualmente consiste en un receptáculo donde se encaja la carcasa que contiene una serie de elementos para posicionar y fijar el componente:
- Amarre con apoyos verticales en las bridas superior e inferior.
- Posicionadores radiales (aros metálicos de contacto) con apoyo en toda la circunferencia a diferentes alturas.
- Juntas tóricas radiales con apoyo en toda la circunferencia a diferentes alturas, para mejorar el amortiguamiento de la unión pieza-utillaje.
- Cámaras neumáticas radiales con apoyo en toda la circunferencia a diferentes alturas, para mejorar el apoyo y el amortiguamiento de la unión pieza-utillaje.
La solución actual con las cámaras neumáticas proporciona un soporte y amortiguamiento adicional a los elementos mecánicos convencionales del utillaje. Sin embargo, el problema que presenta este método está relacionado con la falta de fiabilidad de las cámaras neumáticas, y el elevado tiempo del ajuste manual de la presión de inflado para limitar la deformación provocada en el utillaje.
2. Análisis del comportamiento
La baja rigidez del componente implica que la pieza se ve sometida a deformaciones durante el proceso de amarre y el proceso de mecanizado. La siguiente figura muestra el criterio adoptado para describir la forma de trabajo de la pieza. El modo tensión implica que la pieza se deforma tendiendo a aumentar la presión de contacto con el utillaje; mientras que en el modo compresión la pieza tiende a separarse del utillaje perdiendo el contacto con este.
Durante el proceso las distintas zonas de la pieza pueden estar trabajando en diferentes modos.
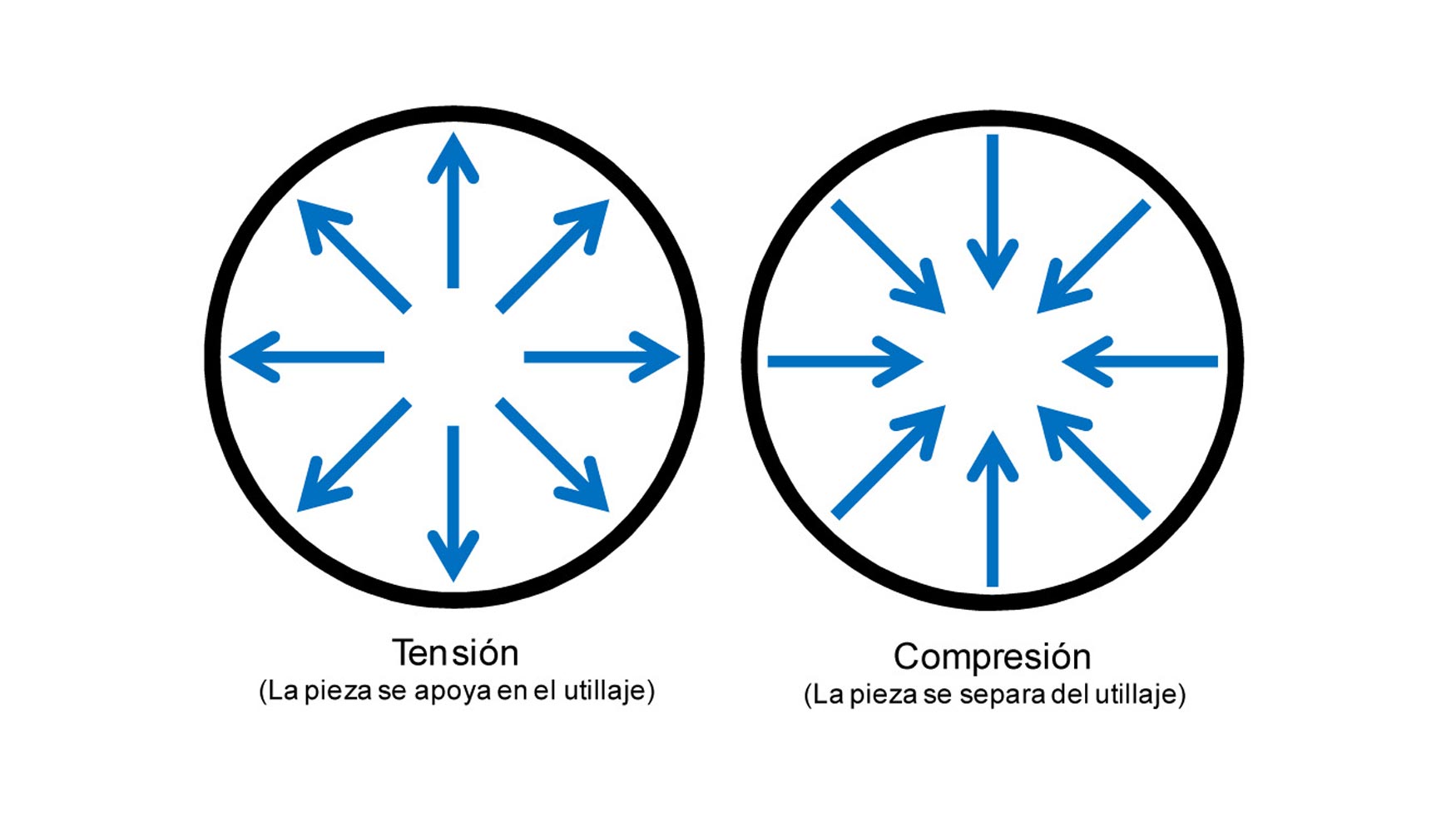
2.1. Análisis MEF
Se ha realizado un modelo de elementos finitos de la pieza con las condiciones de contorno impuestas por el utillaje, con el objetivo de identificar el comportamiento estático y dinámico. Las condiciones de contorno consideradas en el modelo son las siguientes:
- Amarre de la pieza en las bridas mediante fijaciones axiales (restricciones en los 6 grados de libertad).
- Restricciones de contacto en la zona periférica, representando el contacto entre la pieza y el utillaje en las zonas de posicionamiento radial.
- Introducción de la rigidez y el amortiguamiento proporcionado por las cámaras neumáticas y las juntas tóricas.
- Posibilidad de incluir las fuerzas de mecanizado que actúan sobre la pieza.
La rigidez del contacto entre la pieza y los posicionadores radiales se ha modelado como una rigidez no lineal, de forma que existe rigidez cuando la pieza empuja contra el utillaje (modo Tensión) y esta rigidez es nula cuando la pieza se separa del utillaje (Modo Compresión). Por un lado, el análisis estático muestra que la pieza sufre deformaciones durante el proceso que modifican las condiciones de contacto con el utillaje, la causa de esto es la baja rigidez de la pieza. Por otro lado, el análisis dinámico muestra que la forma modal del sistema (incorporando las cargas de mecanizado) tiene deformaciones locales y aparecen una serie de ondas.
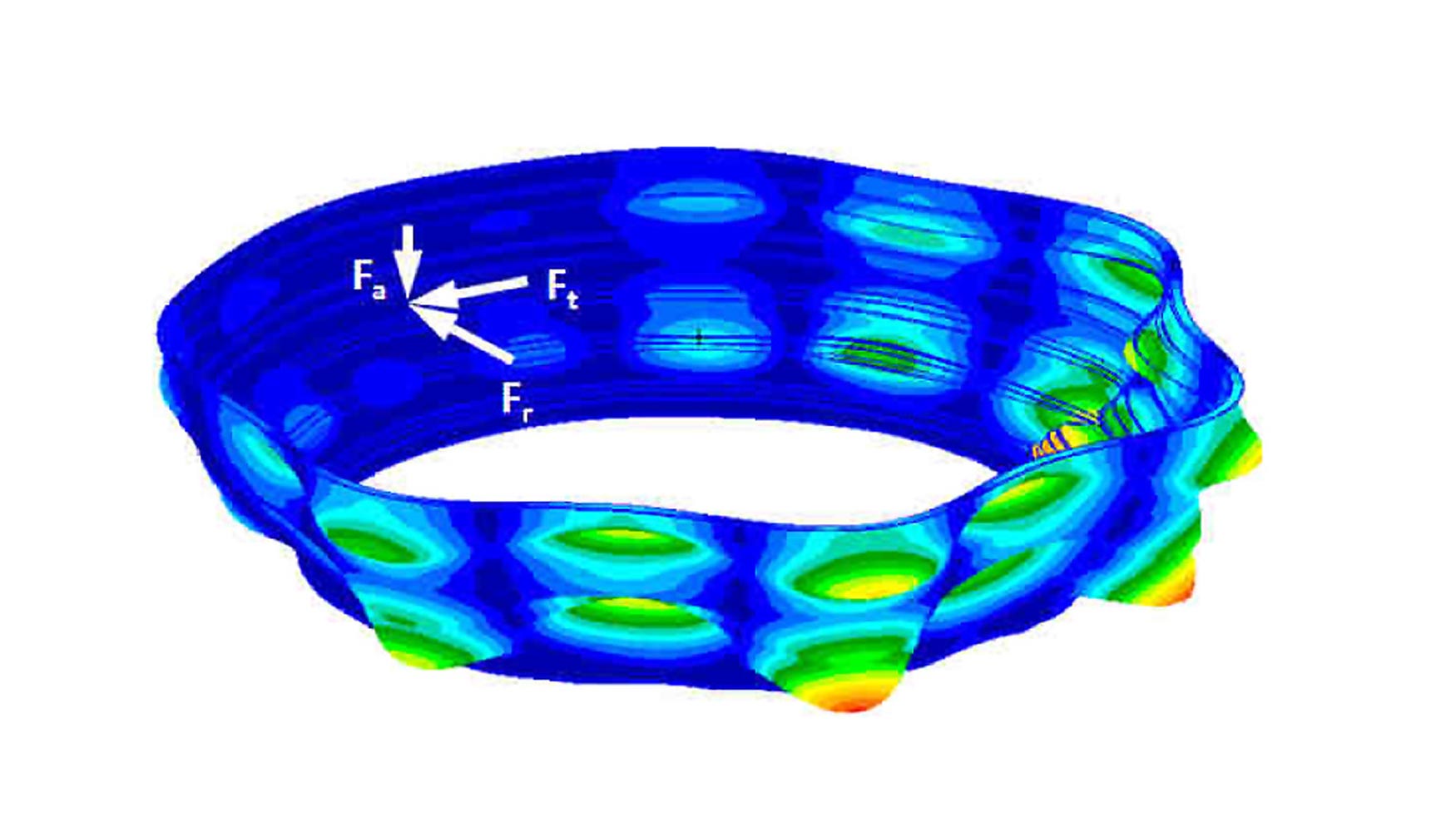
2.2. Análisis experimental
Los ensayos experimentales han consistido en un análisis modal para obtener las funciones de respuesta en frecuencia (FRF) en distintos puntos de interés. Con este análisis se ha evaluado la aportación de los diferentes elementos que actualmente se emplean en el utillaje, valorando la influencia de diferentes elementos que ahora se emplean en el utillaje: bridas de amarre superiores, cámaras neumáticas de apoyo, y juntas tóricas de apoyo.
El análisis modal se ha llevado a cabo con un martillo de excitación, varios acelerómetros triaxiales y un analizador de vibración.

El procedimiento de medida consiste en golpear los puntos de excitación establecidos previamente en la dirección (o direcciones) deseadas, de forma que el analizador registra por un lado el nivel de fuerza en el impacto del martillo, y por otro lado se registra la respuesta del acelerómetro en los puntos previamente fijados. Con la información obtenida se calculan las FRFs que determinan la relación entre la fuerza y la respuesta en función de la frecuencia.
Debido a las características de la pieza y las dificultades de excitación y medición en el análisis modal, se ha obtenido un ancho de banda efectivo de 0-400[Hz]. Dentro de dicho ancho de banda se han identificado varios modos en cada una de las configuraciones. Se han analizado cinco configuraciones distintas. Para todas ellas, se ha realizado el amarre axial en la brida inferior y se han variado el resto de elementos del amarre, resultando las cinco configuraciones siguientes:
- C1 - Cámaras de aire desinfladas y sin atado superior con bridas.
- C2 - Cámaras de aire desinfladas y con atado superior con bridas.
- C3 - Cámaras de aire infladas y con atado superior con bridas.
- C4 - Sin cámaras de aire y con atado superior con bridas.
- C5 - Sin cámaras, sin tóricas y con atado superior con bridas.
Se han fijado los siguientes puntos de medida respecto a un sistema de coordenadas de referencia seleccionado de forma arbitraria, considerando los puntos de medida mostrados en la Figura 5.
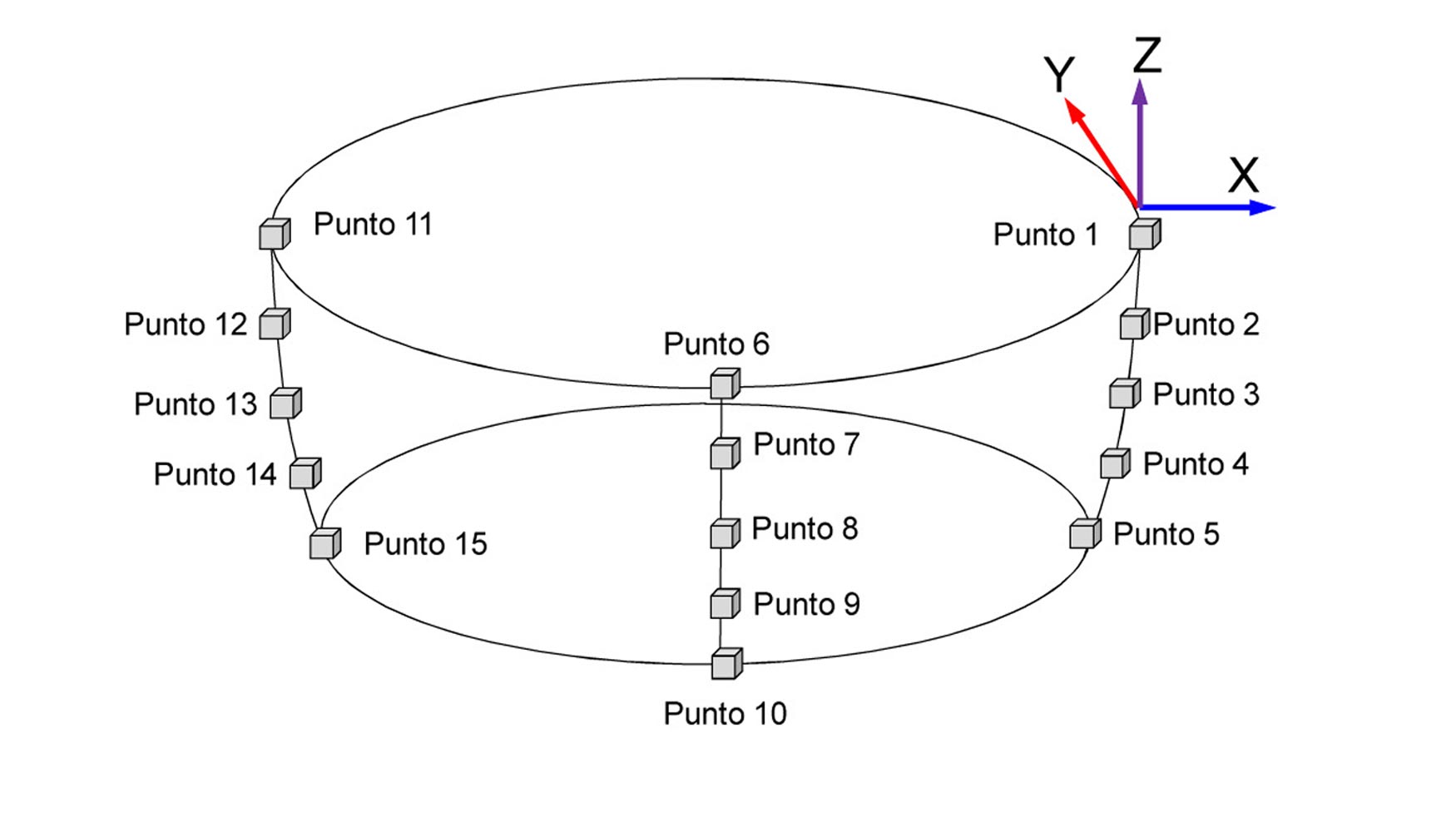
Los resultados del análisis modal muestran que el comportamiento entre las diferentes configuraciones es similar en los diferentes puntos medidos. La dirección más significativa es la radial, se puede ver una de las mediciones en la Figura 6. De forma general se observan tres efectos principales.
- La utilización de cámaras neumáticas provoca que la frecuencia natural y la rigidez sean ligeramente inferiores a las otras configuraciones. Se atribuye a que las cámaras provocan una deformación en la pieza, separándola de los posicionadores.
![Figura 6: FRFs 0-400[Hz] para Respuesta en el punto 3 y excitación en el punto 1, en ambos casos en la dirección radial Figura 6: FRFs 0-400[Hz] para Respuesta en el punto 3 y excitación en el punto 1, en ambos casos en la dirección radial](https://img.interempresas.net/fotos/1140968.jpeg)
2.3. Identificación de características
En base a los resultados del modelo de elementos finitos y los ensayos experimentales se han identificado la forma de trabajo del utillaje actual y sus características:
- El utillaje (posicionadores radiales) proporciona fundamentalmente rigidez trabajando en el modo tensión.
- Las cámaras neumáticas provocan una pre-compresión que hace que la pieza se despegue ligeramente de la pieza.
- Las cámaras proporcionan cierto amortiguamiento, pero es despreciable.
- El amarre de la pieza se realiza con las fijaciones axiales en las bridas (superior e inferior) de los extremos.
La principal conclusión es que el utillaje no proporciona rigidez a la pieza en el modo de trabajo a compresión. Esto permite formular la hipótesis de trabajo que relaciona esta falta de rigidez con los problemas dinámicos, en forma de choques entre la pieza y el utillaje que excitan dinámicamente la pieza produciendo la vibración. Las hipótesis establecidas son:
- Forma de trabajo con fuerzas de mecanizado: algunas áreas de la pieza trabajan en modo tensión (contacto con el utillaje) y otras en modo compresión (se separan del utillaje).
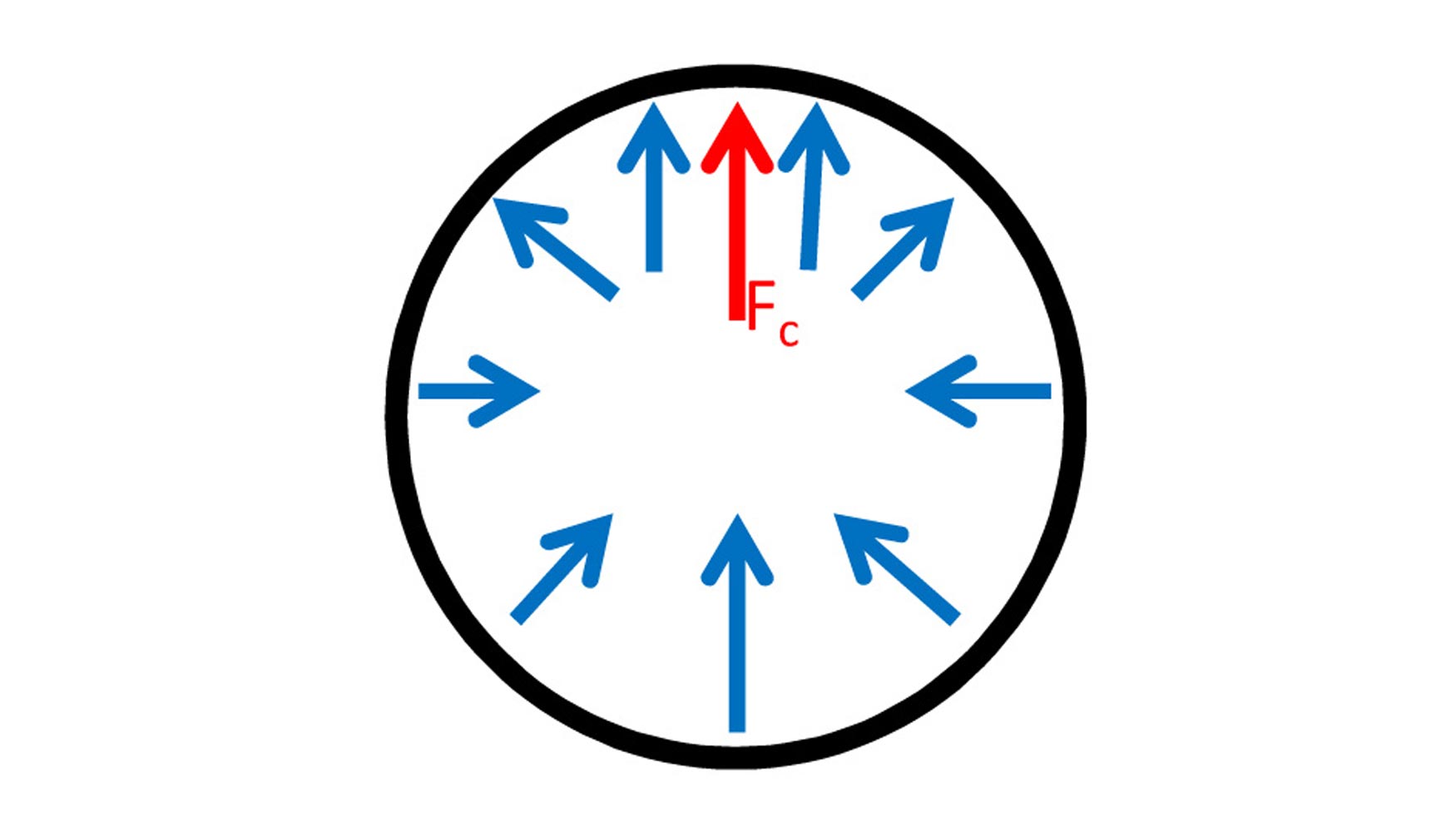
- La posición variable de la fuerza de corte produce deformaciones locales en la pieza que varían en el tiempo (cambio entre modo tensión y modo compresión), lo que conduce al golpeteo de la pieza contra el utillaje, que resulta en choques que son la principal causa de las vibraciones.
Por lo tanto, la falta de rigidez en modo compresión provoca los choques que excitan dinámicamente la pieza y producen las vibraciones, por lo que la solución propuesta está dirigida a reducir este problema aumentando la rigidez a compresión de la pieza. La solución propuesta se basa en el uso de ventosas de vacío que proporcionan una fuerza de succión que tiende a aumentar la rigidez de la pieza a compresión, evitando la severidad de los choques entre está y el utillaje.
3. Ensayos de caracterización de la solución
La propuesta de solución basada en la utilización de ventosas de vacío se ha llevado a cabo en un banco de ensayos que trata de reproducir el comportamiento de la pieza real. Este banco de ensayos incluye los siguientes elementos: - Pieza flexible simplificada: Chapa de 350 x 250 x 3 mm de acero inoxidable. - 8 bridas de amarre. - De 4 a 6 elementos de soporte. - 1 o 2 ventosas de vacío: 140 N (@ 400 mbar).
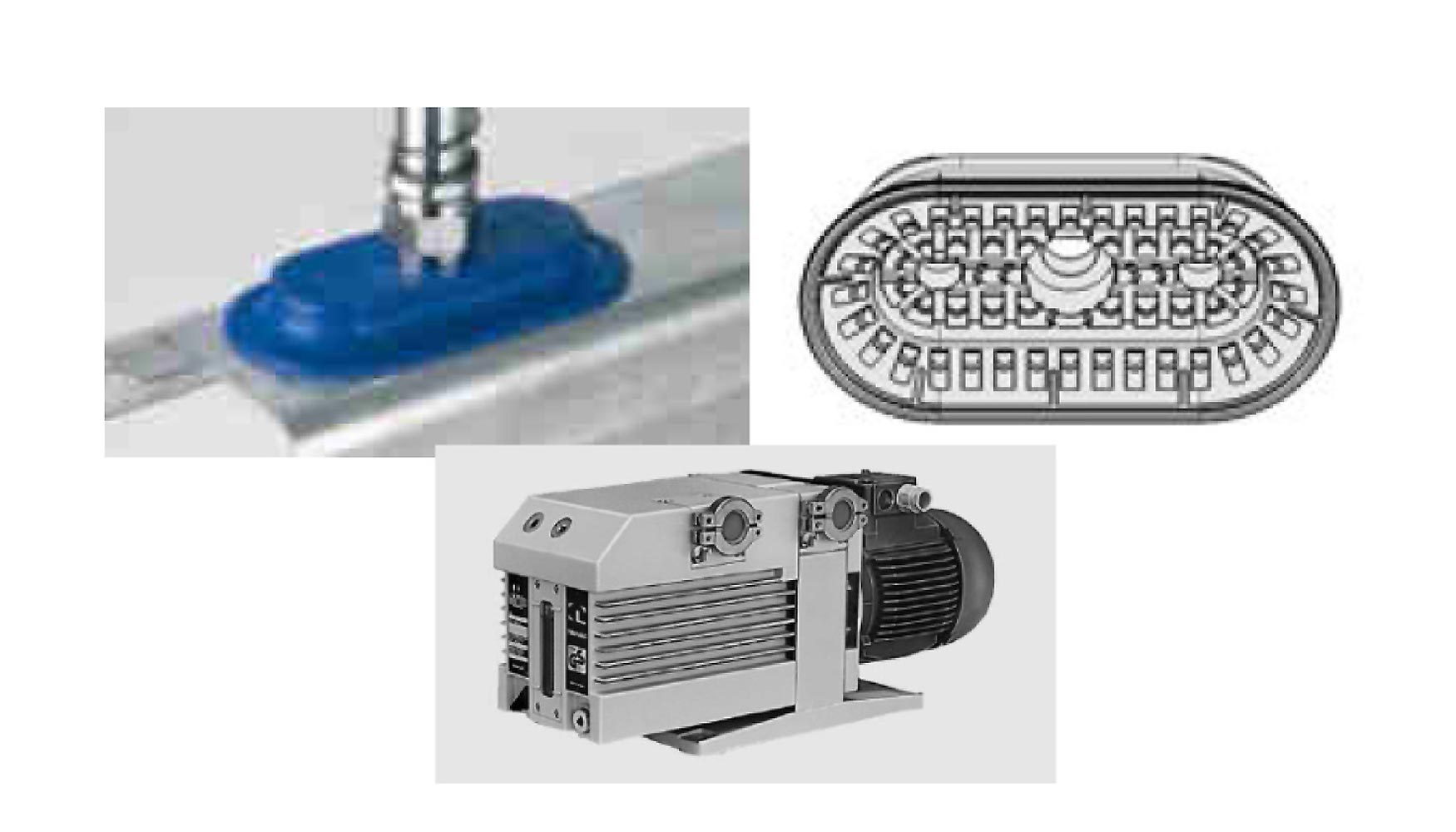
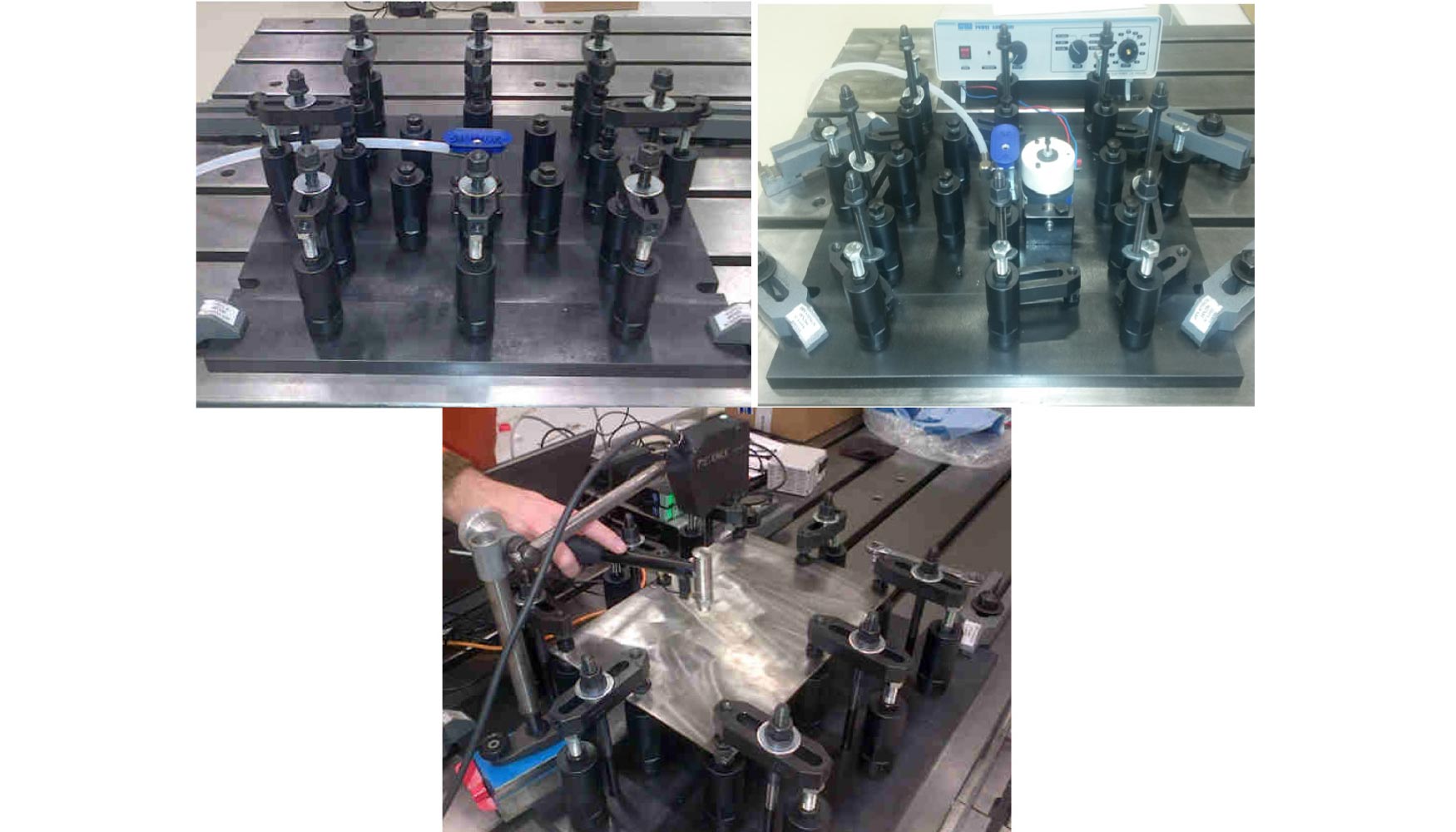
La siguiente tabla muestra esquemas de las diferentes configuraciones utilizadas en el análisis modal.
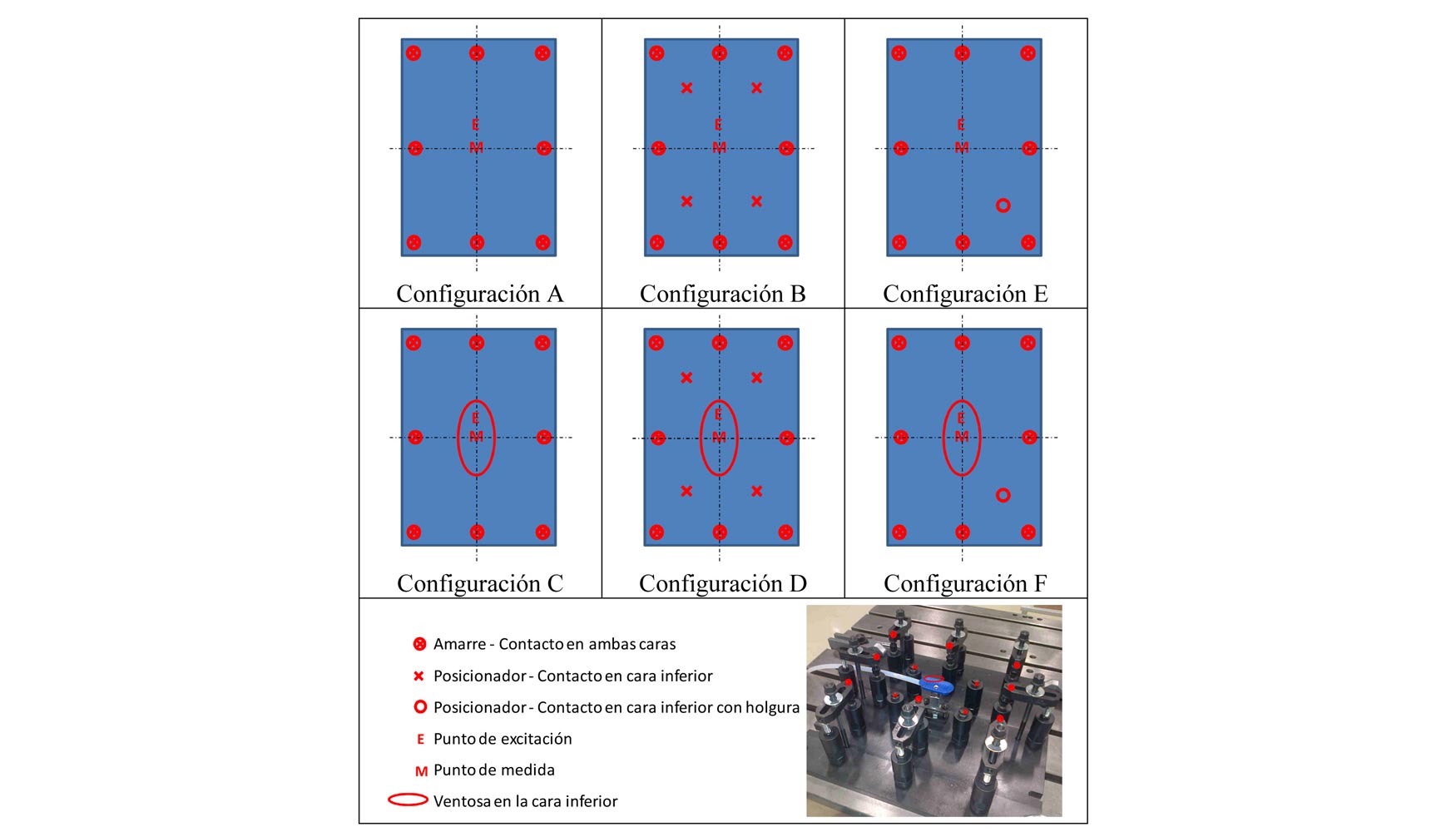
Las configuraciones A y C muestran el comportamiento de la pieza, con una baja rigidez al no disponer de apoyos intermedios, y permite evaluar el aporte de la ventosa al comportamiento de la pieza. Las configuraciones B y D permiten evaluar el efecto de la ventosa en una configuración de pieza con mayor rigidez de partida al incorporar apoyos intermedios. Y las configuraciones E y F permiten analizar el efecto que tiene la existencia de apoyos con holgura, que provocan choques entre el utillaje y la pieza cuando se producen deformaciones en esta última.
4. Resultados y discusión
4.1. Características modales
En lo referente al resultado obtenido en las diferentes configuraciones, en la Figura 11 se puede observar que el uso de posicionadores (Configuraciones B y D) aumenta la rigidez del conjunto, incrementando la frecuencia natural dominante, en comparación con la configuración base sin posicionadores (Configuraciones A y C) que se muestra en la Figura 10. Así mismo, se puede apreciar la influencia de la ventosa, reduciendo significativamente la amplificación dinámica (altura de los picos) e incrementando el amortiguamiento (anchura de los picos) notablemente. En las configuraciones con la ventosa se observa que las FRFs tienen multitud de modos secundarios, que indican un comportamiento dinámico no lineal debido a la ventosa.
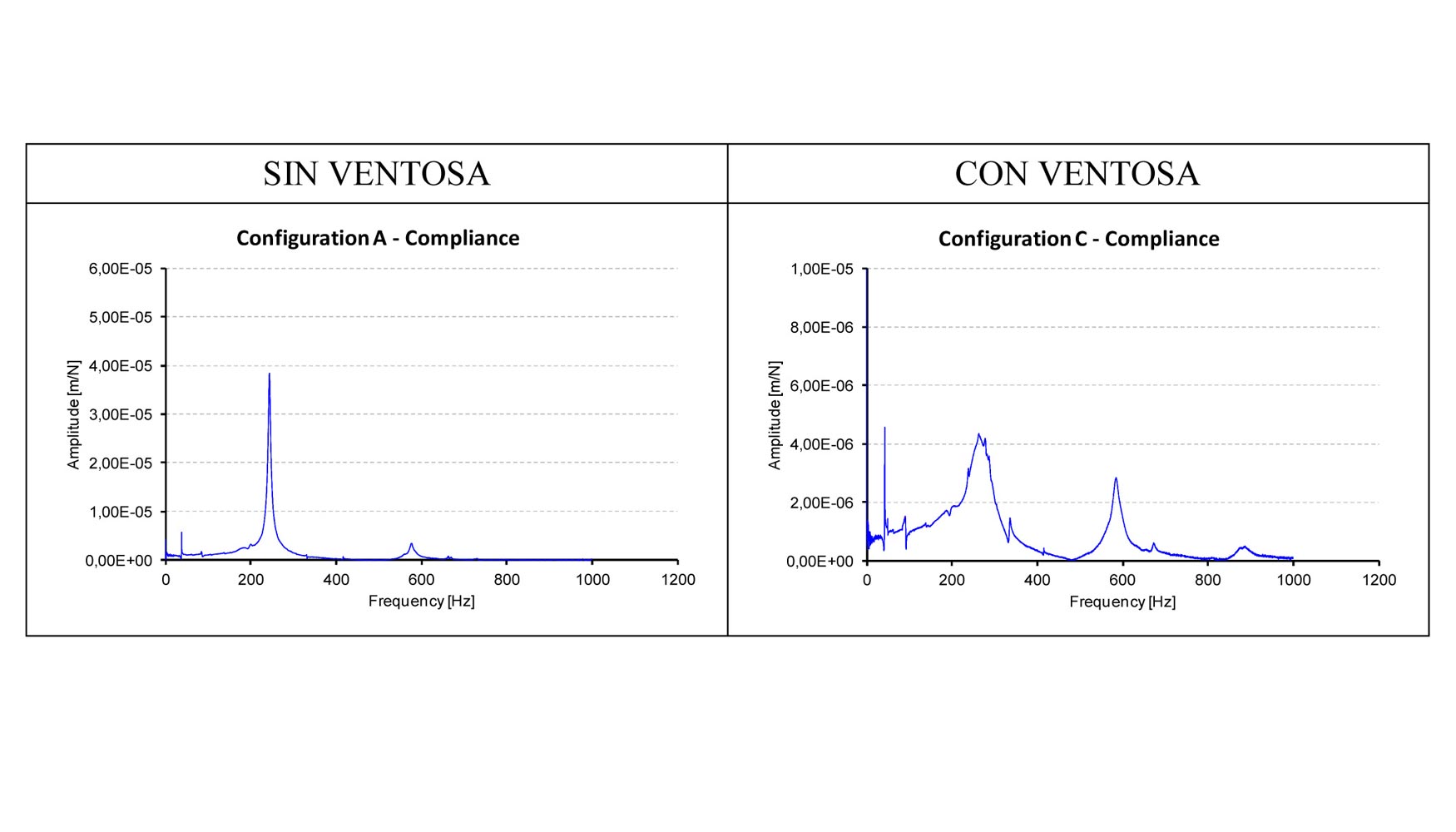
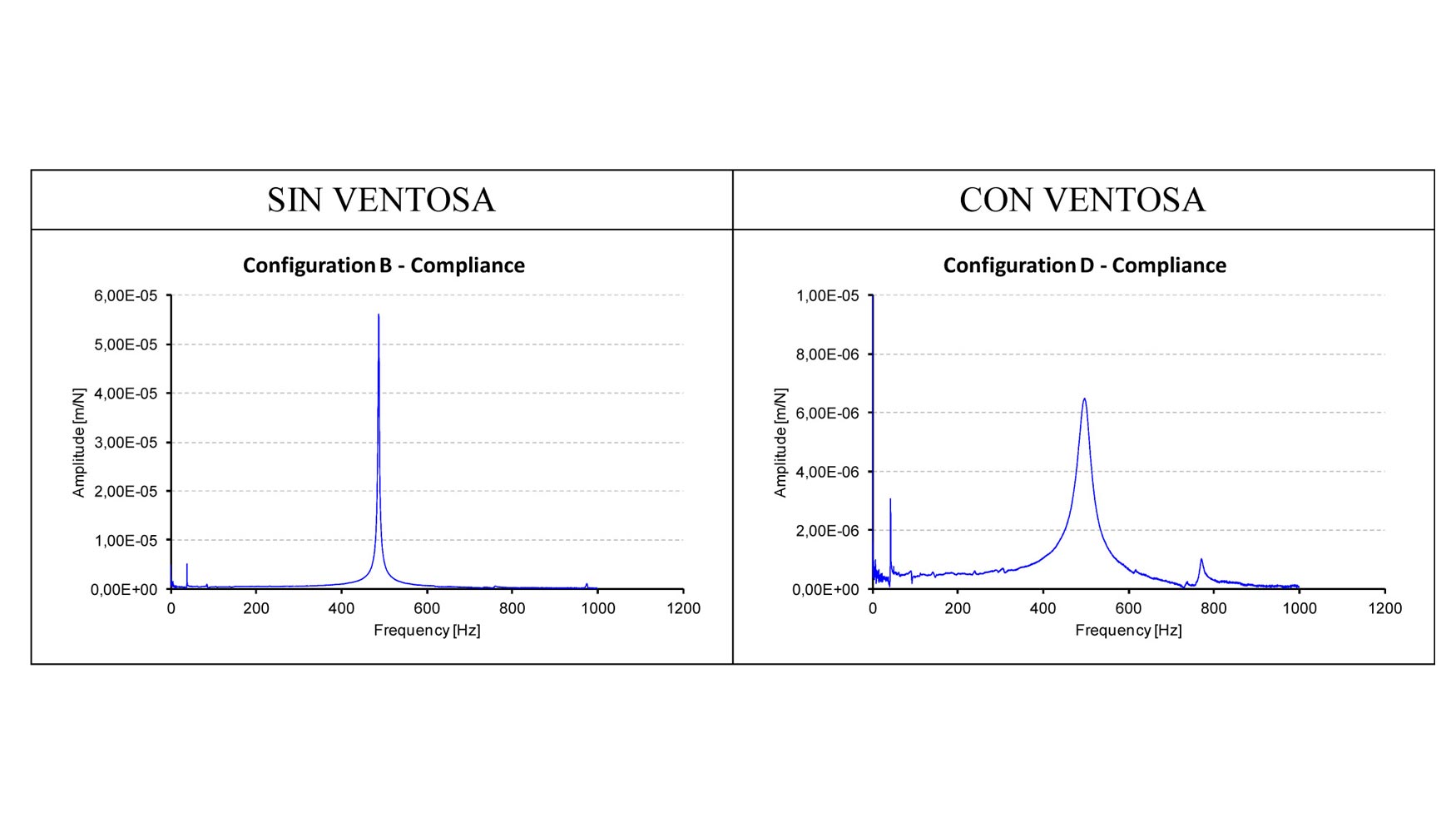
En lo que respecta a la caracterización del fenómeno de los choques entre la pieza y el utillaje, es otro factor adicional de no linealidad dinámica que se puede observar claramente en la asimetría del pico de 600 Hz en la configuración F de la Figura 12. Esta no linealidad se muestra en las señales temporales de la Figura 13. Se puede observar que, en la situación de interferencia, la vibración sólo se produce en un sentido, y que en el tiempo entre picos se produce ruido de alta frecuencia como consecuencia de los choques.
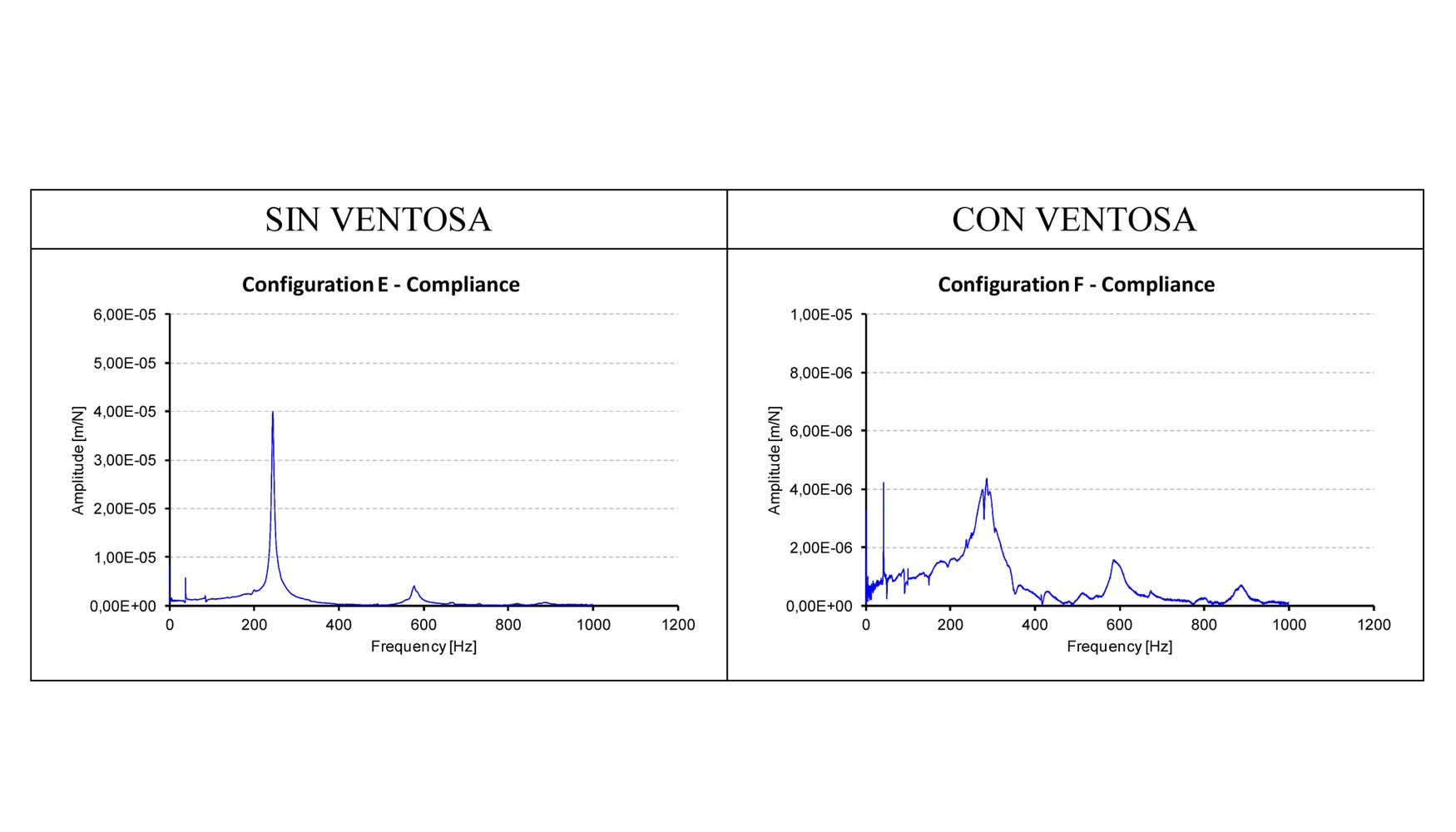
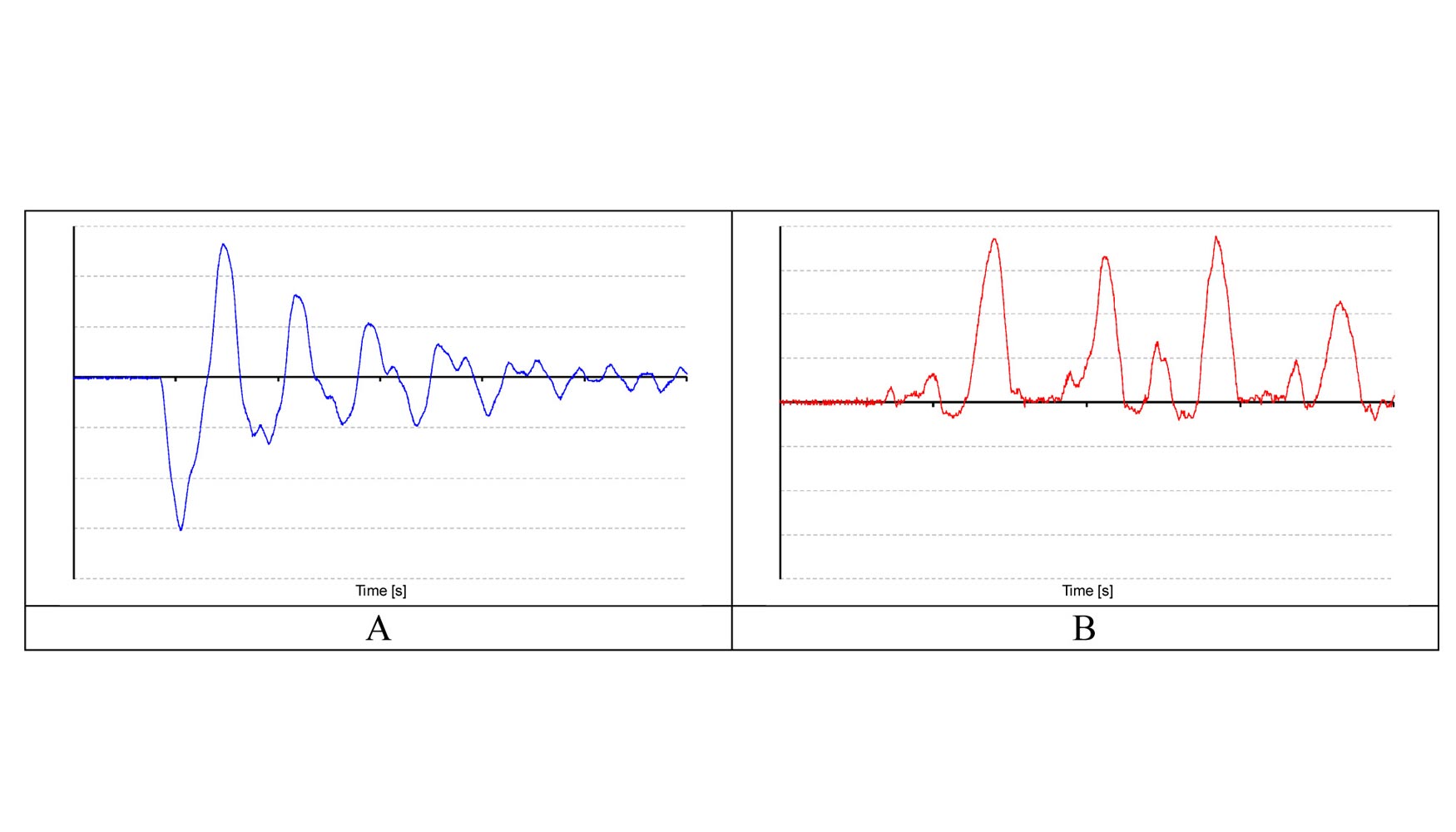
En lo referente al uso de la ventosa de vacío se ha comprobado que mejora el comportamiento del sistema reduciendo significativamente la amplificación dinámica. Esta mejora es de un orden de magnitud en el caso analizado. Esta mejora es consecuencia de la rigidez y el amortiguamiento aportados por la ventosa que están cuantificados en la siguiente tabla. Como se puede observar, en la configuración sin posicionadores el amortiguamiento aumenta significativamente desde el 1,09% al 7,83%; siendo el aumento más moderado en una configuración de pieza con posicionadores que resultan en una mayor rigidez y un menor amortiguamiento, de forma que la mejora aportada por la ventosa supone un 2,64% frente al 0,26% inicial.
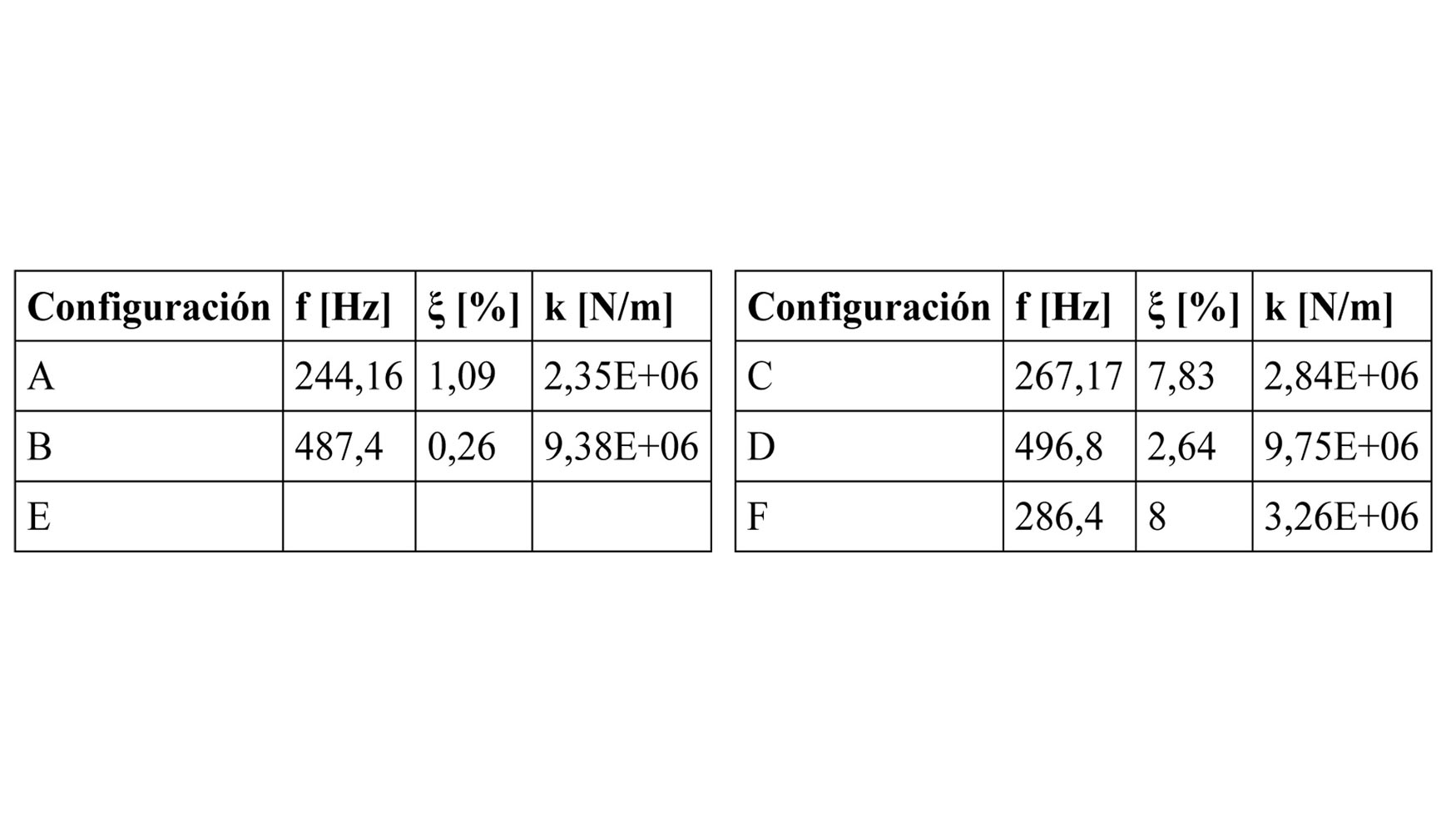
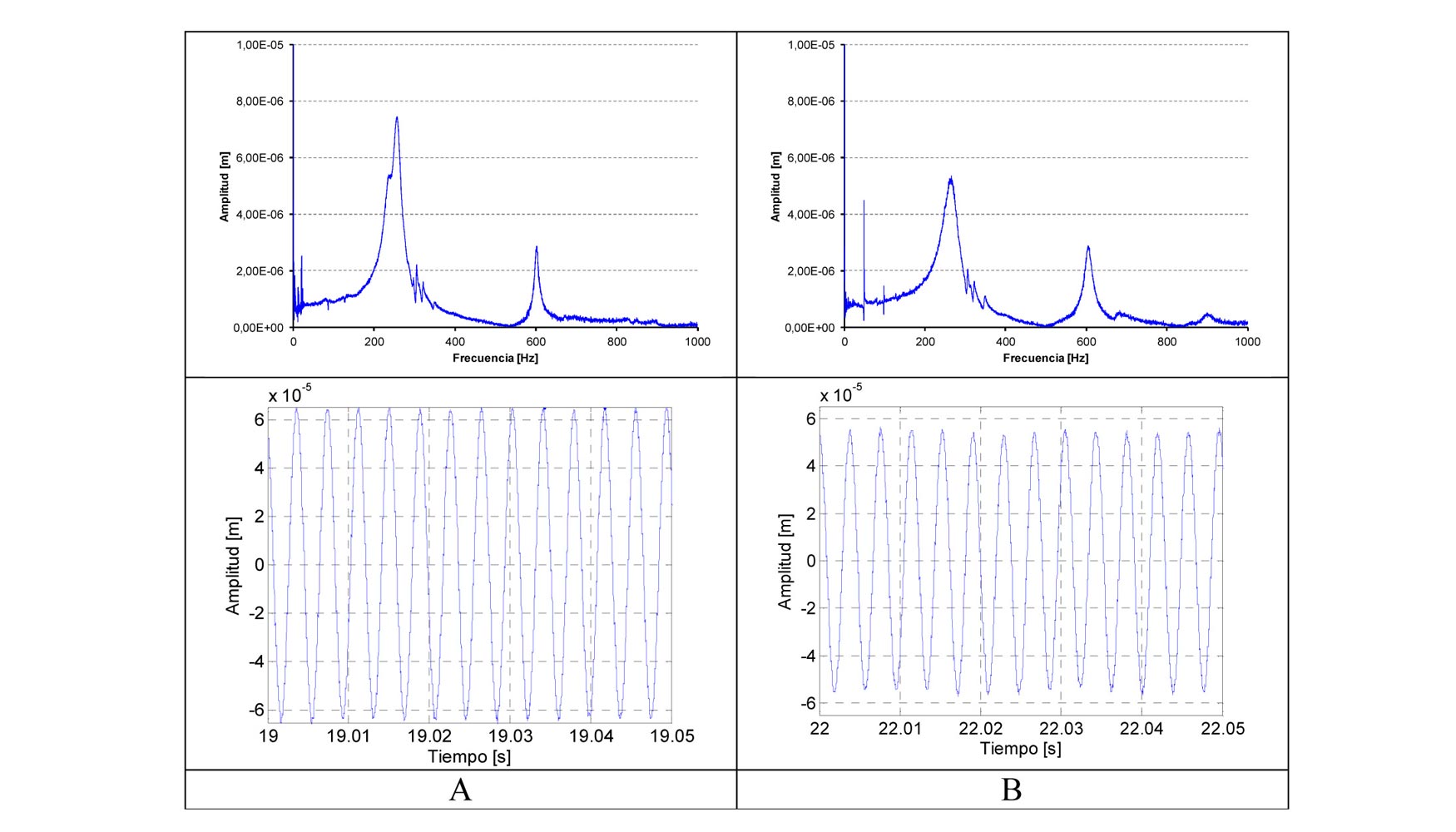
Figura 14. FRF y desplazamiento en el centro de la chapa. A. Sin ventosa de vacío. B. Con ventosa de vacío.
5. Propuestas de solución
Las posibilidades de mejora del utillaje de la pieza en estudio, es decir la carcasa de la turbina pasaría por la construcción de bloques de vacío integrados en el utillaje actual
sustituyendo el lugar ocupado por las cámaras neumáticas. Estos bloques introducirían una fuerza de succión para aportar rigidez ante deformaciones radiales, y provocarían el apoyo de la pieza contra los posicionadores del utillaje. Un ejemplo de estos bloques se muestra en la Figura 8, que consiste en un bloque para un sector que abarca 15º de la circunferencia y proporciona una fuerza de succión de aproximadamente 430 N. Se utilizarían diferentes sectores en toda la circunferencia de la pieza y a diferentes alturas. Al tratarse de una operación de torneado, la solución al problema del giro de la pieza y el utillaje durante el mecanizado pasaría por la utilización de un acumulador de vacío montado en el utillaje para mantener la presión en el sistema.
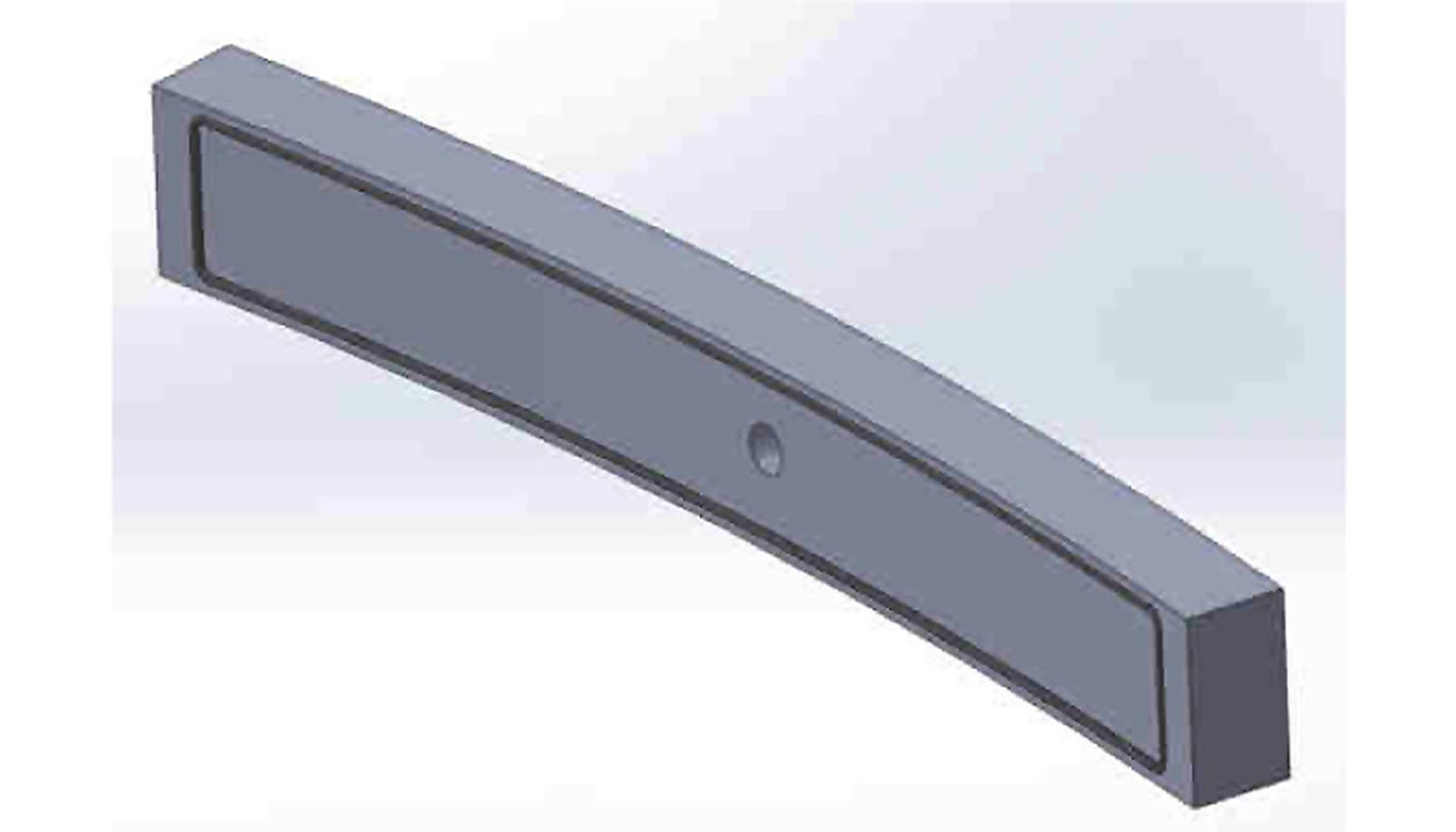
En el proyecto Intefix (VII Programa Marco, Contrato nº 609306) se han planteado soluciones adicionales que serán probadas en el marco del mismo proyecto. Se trata de soluciones más complicadas que tratan de verificar las posibilidades de nuevos conceptos de utillaje, para ser verificados como parte de la actividad del proyecto. En este caso lo que se trata es de mejorar el comportamiento frente a vibraciones por lo que se han propuesto dos soluciones adicionales:
- Absorbedores activos de vibración para reducir la amplificación dinámica de la pieza.
- Deformación controlada de la pieza (cuasiestática y rotativa) para mejorar las condiciones amarre, mejorando el contacto entre pieza y herramienta en la zona de interés (zona de corte).
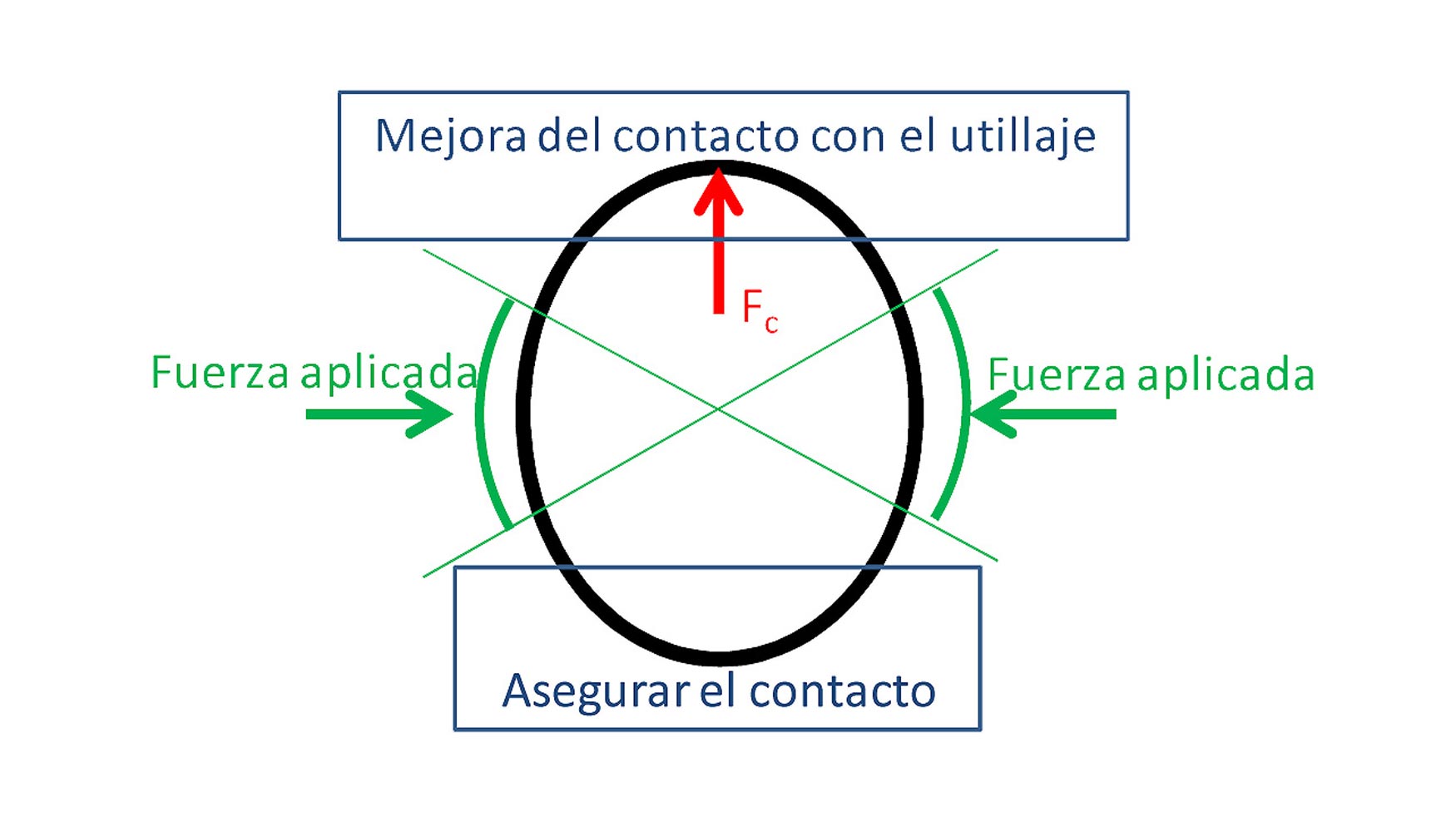
Estas soluciones implican la introducción de los sistemas necesarios en el utillaje actual de cara a modificar el comportamiento del conjunto. Esto supone una complejidad adicional que debe ser estudiada en detalle.
6. Conclusiones
El objetivo principal ha sido identificar las ventajas aportadas por la utilización de la ventosa de vacío en lo referente a rigidez y amortiguamiento, así como evaluar el efecto de las separaciones y choques entre la pieza y los elementos de apoyo del utillaje. Este trabajo ha permitido concluir que la mejora en el comportamiento de la pieza puede ser importante, y que sería interesante el desarrollo de esta alternativa para la carcasa de la turbina de baja presión, de cara a mejorar el comportamiento del utillaje actual. Se ha planteado una solución para incorporar el sistema analizado mediante unos bloques de vacío. Así mismo, se plantean otras alternativas que serán analizadas en el futuro en el marco del proyecto Intefix Las principales conclusiones del trabajo realizado se describen a continuación:
- El uso de la ventosa de vacío aumenta la rigidez del sistema, mientras que el amortiguamiento aumenta de forma importante. El aumento del amortiguamiento es menos relevante cuando la configuración del sistema inicial tiene una rigidez más elevada.
- La ventosa de vacío permite mejorar el comportamiento del sistema y reducir el impacto de los posibles choques entre la pieza y el utillaje, al aumentar la fuerza de contacto entre ambos elementos y reducir la amplificación dinámica en todo el espectro de frecuencia.
- De acuerdo al estudio realizado, las cámaras neumáticas de apoyo empleadas en el utillaje actual para el mecanizado de la turbina apenas aportan ventajas al comportamiento dinámico frente a una configuración sin estas cámaras.
Agradecimientos
Los resultados de este trabajo son parte de la investigación llevada a cabo en el proyecto Inproret dentro del programa Etortek, financiado por el Departamento de industria del Gobierno Vasco; y del proyecto Intefix del VII Programa Marco.
Referencias
[1] Bi, Z., Zhang, W.,2001.Flexible fixture design and automation: review, issues and future directions. Int. J. Prod. Res. 39(13), 2867–2894.
[2] Boyle, I., Rong, Y., Brown, D., 2011. A review and analysis of current computer-aided fixture design approaches. Robot. Comput. Integr. Manuf. 27(1), 1–12.
[3] Fleischer et al., 2006, “Workpiece and Tool Handling in Metal Cutting Machines”. Annals of CIRP Vol. 55/2, pp. 817-839.
[4] Swarmitfix Report Summary. Project reference: 214678. Funded under: FP7-NMP (2013) http://cordis.europa.eu/result/rcn/57171_en.html.
[5] X.-J. Wan, Y. Zhang, X.-D. Huang.Investigation of influence of fixture layout on dynamic response of thin-wall multi-framed work-piece in machining. International Journal of Machine Tools & Manufacture 75 (2013) 87–99.