Innovaciones, requisito para un óptimo envasado en la industria de la alimentación
Illig Maschinenbau GMBH & Co.KG15/05/2006
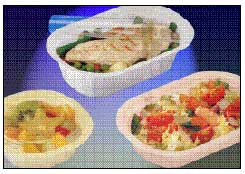
La creciente demanda de bandejas de menú de los últimos años empieza a mostrar signos de diferenciación. Hay que aplicar métodos de termomoldeo diferentes según las aplicaciones específicas al desapilar, llenar, sellar, y según las propiedades que se desee que tenga el envase cerrado, tales como transparencia, propiedades de barrera, capacidad de carga y duración. Por último, los lotes también determinan las diferentes soluciones para escoger la variante de método más económico.
Aprovechando la creciente concienciación ecológica de la industria alimentaria y de los consumidores, también se ofrecen envases fabricados con materiales biodegradables (fécula de maíz). Los envases tienen una buena barrera de aroma y son adecuados para un margen de temperaturas de 0 - 40ºC.
Últimamente las bandejas de fruta y verdura también se ofrecen en color negro con el fin de proporcionar un fondo contrastado respecto al alimento envasado. Una nueva tendencia es la marcación por color, por ejemplo el negro para la carne de cerdo; el amarillo para las aves, etc.
El mercado pide que la bandeja tenga cada vez más funcionalidades, tales como varios compartimentos para diferentes tipos de carne, o puentes (por ejemplo para shashlik). El termomoldeo también cumple los requisitos de calidad de la bandeja de carne en lo que se refiere a resistencia y aplastamiento.
La condición para la conservación del contenido son unos bordes de cierre completamente exactos y planos en todo el perímetro de sellado, lo cual se consigue con unos pisones refrigerados en el molde. Se logra prolongar la conservación mediante atmósferas de gas modificadas, que garantizan un aspecto apetitoso.
Al fabricar envases hay que tener en cuenta no sólo las propiedades del material deseado, sino también los gastos de eliminación. El A-PLA permite reducir los gastos de eliminación en los lugares donde existe la recogida selectiva de la basura. Otras materias primas se trituran en línea y pueden reciclarse limpiamente.
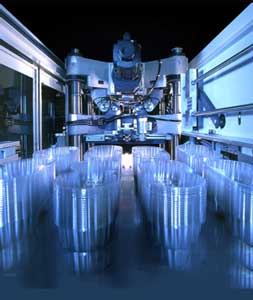
Desde hace décadas ILLIG viene ofreciendo varios conceptos de máquinas para proporcionar todas las soluciones convencionales de envasado, tanto para el moldeo y el troquelado separado, como para el funcionamiento del moldeo/troquelado.
Las máquinas para moldeo y troquelado separado siempre trabajan de igual modo. Después de desenrollar el plástico, éste es guiado a través de la estación de calefacción por ciclos. El proceso de moldeo y troquelado tiene lugar en estaciones separadas; el proceso de troquelado puede realizarse mediante corte con fleje de acero o un troquel y prensa desbarbadora. A continuación las piezas moldeadas se apilan y se transportan fuera de la máquina, ya contadas. El apilamiento A-B proporciona una buena posibilidad de desapilar las piezas moldeadas para su posterior procesamiento. Está disponible para el molde de moldeo o para la estación de apilamiento. El alto grado de automatización, en combinación con la madurada tecnología de moldes, permite la máxima disponibilidad.
Con la tecnología de moldeo por vacío es posible una producción económica, especialmente para lotes pequeños. El efecto económico mejora aún más combinando el moldeo por vacío con aire comprimido, lo cual da lugar a mejores resultados de moldeo en la mayoría de casos. Ambas máquinas tienen una tecnología de molde simple que proporciona una alternativa económica al termomoldeo convencional por aire comprimido. La amplia gama de aplicación incluye piezas de envasado, bandejas de menú o insertos y bandejas. Los moldes empleados son económicos gracias a su simple construcción y proporcionan las mayores ganancias en el caso de lotes pequeños. Unas características especiales (tales como matrices flotantes con centrado previo) dan lugar a una mayor precisión de corte durante el moldeo y el troquelado en estaciones separadas.
Las piezas moldeadas con entalladuras, bisagras moldeadas o botones de cierre pueden moldearse aún mejor combinando con aire comprimido. Directamente en el molde hay disponible una presión de moldeo de 2 bar.
Las máquinas automáticas de termomoldeo alimentadas desde la bobina que funcionan con aire comprimido están concebidas para una mayor producción y permiten velocidades de ciclo de más de 40 ciclos/min. Si se precisan tolerancias más estrechas, las piezas se moldean por medio de la tecnología RDK (moldear y troquelar en una sola estación) y se separan de la cinta de moldeo mediante líneas de corte con fleje de acero, integradas en el molde de moldeo.
La ventaja es la económica tecnología de moldes y la gran gama de formatos. La calidad de corte queda algo limitada por los botones de sujeción que se necesitan en este método para transportar las piezas moldeadas a través de la máquina.
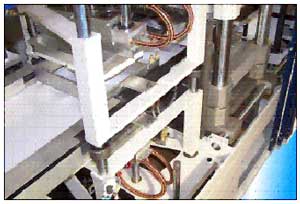
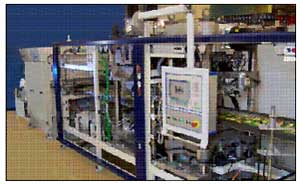
Para procesar PP es esencial el precalentamiento
Un equipamiento adicional de la máquina, esencial para procesar PP, es el dispositivo de expansión para el transporte del plástico. Este dispositivo compensa la comba del plástico y evita que se formen arrugas durante el proceso de moldeo. La aplicación de la tecnología de moldeo/troquelado (RDM, RDK) es ventajosa porque se evitan pasos de transporte adicionales y, por consiguiente, se obtienen óptimos resultados en lo que respecto a precisión de troquelado.
Todos los conceptos de la máquina garantizan un proceso de producción continua gracias a los parámetros que pueden guardarse en memoria y recuperarse en cualquier momento. En caso de repetir producto se recuperan las condiciones de fabricación, garantizando una calidad de producto uniforme. Durante el cambio de moldes se evitan los caros tiempos de inactividad como resultado de introducir datos en el sistema de mando. El uso de accionamientos por servomotor aumenta la capacidad útil de las máquinas de termomoldeo, mejorando decisivamente la dinámica y suavidad de marcha.
La estación de moldeo está postconectada a la estación de calefacción. Aquí se embuten las bandejas. Durante este proceso se preestira mecánicamente el material. Se consigue una óptima distribución del grosor de las paredes gracias a la servotecnología, la cual permite una sincronización exacta de la mesa de moldeo y los movimientos del pistón de preestirado. Una mejor distribución del material permite obtener la misma estabilidad del producto utilizando material más delgado, lo cual da lugar a una mayor calidad de los productos.
Se han tomado medidas para lograr una presión de aire de moldeo uniforme y controlable que permita velocidades de llenado más altas, una fase de moldeo más rápida y que la fase de refrigeración empiece antes, dando lugar directamente a mayores capacidades de producción.
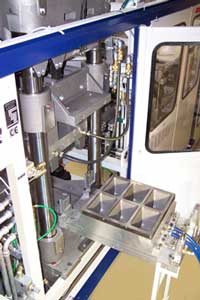
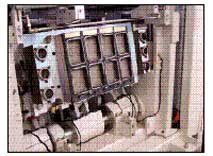
Según la producción y el material, hay que adaptar la temperatura de las resistencias a las diferentes temperaturas de procesado. El ajuste básico asistido por ordenador resulta útil para esto. Además de los datos de ajuste de la máquina, también presenta un calentamiento óptimo. Gracias a la regulación de temperatura mediante resistencias piloto no son necesarios sistemas de control adicionales.
ILLIG ofrece cada vez más sistemas integrados para la automatización de máquinas e instalaciones en el sector del termomoldeo.
La construcción modular permite aplicar diferentes técnicas de procesos para moldear, troquelar y apilar productos, pudiendo añadir un triturador de rejillas de troquelado para tener una instalación completa. Para introducir piezas de aspiración, decorar el envase o imprimir códigos de barras se utiliza un puesto vacío donde colocar estos dispositivos.
El uso de sistemas mayoritariamente electrónicos permite, por medio de desacoplamientos mecánicos, unas construcciones menos complicadas de máquinas y nuevos conceptos de instalaciones. Ésta es la base para llevar a cabo procesos de fabricación continuos y flexibles con elevadas velocidades de ciclo, garantizando al mismo tiempo una manipulación fácil utilizando piezas estándar.
Las soluciones procedentes de una sola fuente son muy ventajosas teniendo en cuenta la gran cantidad de máquinas y técnicas de procesos aplicables. Como fabricante líder, ILLIG ofrece tecnología punta en sus sistemas integrados.