Sin periféricos, no hay transformación
Plásticos Universales ha entrevistado a diferentes empresas suministradores de periféricos del país para que nos den su impresión de cómo ven el sector de los periféricos para la transformación en un año en el que todas ellas presentarán sus últimos desarrollos e innovaciones en su feria en España por antonomasia, Equiplast.
Todos los entrevistados coinciden en que actualmente las necesidades de periféricos en la industria de transformación de plásticos, y más concretamente en el sector de inyección, se centran en la máxima automatización de los procesos productivos, la reducción de costes y la búsqueda de una flexibilidad que permita una rápida readaptación de esos periféricos a cada cambio de producción. La evolución de los equipos es muy variada, y depende de su función en el proceso. La empresa Centrotécnica destaca como periféricos más demandados en estos momentos a los robots o manipuladores para extracción de coladas y/o piezas, la incorporación de sistemas de reciclado en línea para coladas y ocasionales piezas defectuosas, mediante un triturador a pie de máquina y una válvula proporcional que gestiona la reutilización triturado en el porcentaje adecuado respecto al material virgen de forma automática, mediante un alimentador neumático individual o un sistema de alimentación centralizado...
Al automatizar y limitar al máximo la intervención humana, el objetivo de cualquier periférico es estabilizar el proceso productivo, mantener constantes los tiempos de ciclo de las máquinas y controlar la producción de un modo preciso. Son, por tanto, también cada vez más necesarios periféricos como las cintas transportadoras que evacúan las piezas y/o coladas desde las máquinas a un punto de recogida; o de separación e incluso de montaje, y, también, los sistemas de refrigeración de agua a circuito cerrado, que se pueden suministrar en forma de grandes equipos centralizados o pequeñas unidades para una máquina o un grupo de éstas.
Eurotecno señala que en su caso los periféricos más demandados son los molinos y los silos mezcladores. Alboex, por su parte, destaca como equipos más solicitados los molinos y los atemperadores, aunque también tienen un gran consumo las instalaciones centralizadas, así como los detectores de metales, que últimamente han experimentado un gran auge.
Desde Wittmann se matiza que en cualquier proceso es muy importante mantener las mejores condiciones de producción y calidad, por ello resulta imperativo apoyarse en más de un periférico. “El uso de robots y la fácil automatización de los procesos con nuestras actuales tecnologías, ofrece óptimas ventajas sobre cualquier proceso de fabricación, al permitir una mayor rentabilidad y un control sobre el mismo.”
Los equipos de inspección, selección y clasificación son también, en los últimos años, uno de los periféricos más demandados. Así por lo menos lo afirma la empresa Proyecma que representa y comercializa a la marca francesa Proditec. “Bajo nuestro punto de vista y sobre todo dentro del sector de la alimentación, y debido posiblemente a un considerable incremento en los últimos años de número de empresas dedicadas a la fabricación de tapones de plástico -comentan en Proyecma-, parece detectarse un incremento de la competencia a la hora de situarse como proveedor de las grandes marcas. Por un lado, en la lucha por ser proveedor de esas marcas se ha adoptado como un activo comercial más (más que por necesidad industrial real o por exigencias cada vez más elevadas del consumidor final) dotar al proceso de inyección de soluciones de visión artificial que garanticen el 100 por cien de la calidad en el producto suministrado. Por otro lado, una reducción cada día más necesaria del coste de la no calidad (pérdida de producción por fallos en el proceso, devolución de lotes, etc.), el fabricante de tapones se ve más obligado a introducir en su proceso posterior a la inyección este tipo de sistemas de verificación.”
Otra de las empresas entrevistadas, Equiper señala como periféricos más solicitados por el sector de inyección los alimentadores de granza, dosificadores de todo tipo, molinos y elementos de transporte con soluciones en estocaje.
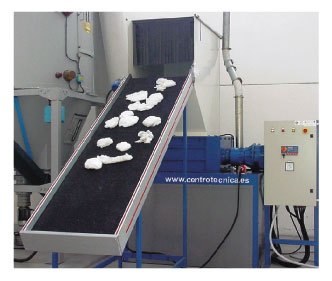
¿Junto con la máquina o por separado?
Desde Wittmann, por ejemplo, se señala que ocasionalmente se venden algunos robots con la inyectora, aunque la mayoría de usuarios prefiere seleccionar la tecnología que mejor se ajusta a sus necesidades. Y esto se hace a través de un experto que le permite elegir ante una mayor gama de modelos y soluciones.
Sin embargo, en los últimos años hemos podido ver cómo algunos –no muchos- fabricantes de máquinas de transformación, debido a la fuerte competencia existente entre ellos, están incluyendo equipamiento periférico como un argumento más; a veces puede ser política de empresa, otras, deseo del cliente... es una tendencia que, sin embargo, no se está generalizando. “Hay muchos usuarios que prefieren tratar la compra de periféricos de forma más libre y directa, sea por confianza en empresas más dedicadas a ello, o simplemente por mantener una línea de equipamientos similar a la iniciada en otro momento de su actividad”, destaca Equiper.
El presente económico del sector
¿Reajuste, crisis, nuevos actores implicados? La situación del sector es un tanto ambigua, por un lado se afirma que si se valora el año 2004 en su conjunto el consumo de periféricos aumentó, por otro se dice que los fabricantes de molde (sobre todo), maquinaria y periféricos están detectando una gran competencia desde los países asiáticos y sudamericanos (Brasil y Argentina), que ofrecen cada vez mayor calidad a menor precio; y por último se destaca que se está produciendo un reajuste positivo del sector.
Alboex resume la situación de la siguiente manera: “Aunque es verdad que existe una sensación de incertidumbre en cuanto a la situación del mercado, la realidad, es decir las ventas, contradicen esta sensación, ya que las cifras hablan por sí solas. No creemos estar ante una situación de cierta debilidad, sino que pensamos que hay un reajuste del sector industrial de transformación del plástico. Ya hemos dicho que si se valora el año en su conjunto el consumo de periféricos ha aumentado.”
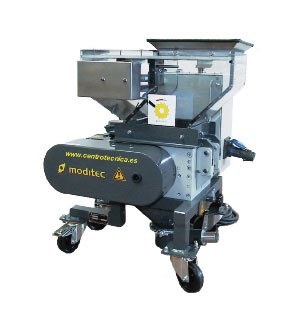
Perspectivas de futuro
Algunos de los entrevistados manifiestan un optimismo moderado “Está claro –dicen- que en Europa para seguir manteniendo la competitividad, será necesario evolucionar aún más en todos los procesos y ahí siempre hará falta un periférico sea de uno u otro tipo, que ayude a la rentabilidad de todo el conjunto.” Otros, al contrario, se muestran pesimistas, y hablan del futuro como “muy difícil”, dado que “la globalización de la que todos hablamos puede evidenciar una falta de competitividad en nuestras empresas que sólo las más flexibles o con más medios económicos puedan superar.”
Sea como fuere, el mercado no espera y los principales fabricantes de periféricos, si quieren seguir en primera fila, deberán, tal y como han hecho hasta ahora, mantener la evolución técnica, y hacerla dinámica, continua y flexible para poder seguir adaptándose a todas las novedades futuras en maquinaria, materiales plásticos, procesos, gestión integral, etc.
Los avances en esta materia estarán marcados, pues, por el aumento de las prestaciones, por la flexibilidad para adaptarse a diferentes necesidades de producción, por la reducción de consumos energéticos, y por supuesto, por el coste de la inversión en la compra de estos equipos.
Atemperador de moldes pequeño de gran capacidad
Entre las principales características del atemperador de moldes de Tool-Temp destacan el vaciado automático del molde, el sistema antifugas que permite al aparato trabajar con presión o por aspiración (el agua no sale de un molde defectuosos, sino que se puede seguir trabajando sin interrupción), control microprocesador con auto regulación y con indicación digital de los valores prefijados y reales, el llenado automático de agua (no para trabajar con aceite) o el intercambiador de calor libre de incrustaciones.
Es un aparato de larga duración y resistente a la corrosión (todos los elementos en contacto con el agua son de acero inoxidable o de bronce), calefacción en fases (conectable de 3 kW para trabajar con aceite a 9 kW para trabajar con agua) y dispositivos de seguridad: control automático de nivel evitando el funcionamiento en vacío; termostato de seguridad mecánico separado; limitador térmico montado en el regulador e interruptor protector de motor, transformador para el mando, aislamiento térmico. Además dispone de una bocina de alarma para señalar cualquier perturbación y de ruedas.
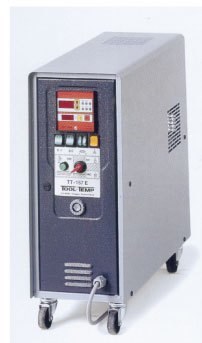
Deshumidificadores para la industria plástica
La serie 100 es una familia de máquinas muy compactas utilizadas para tratar las producciones pequeñas. El circuito de deshumidificación es monotorre con regeneración en contracorriente, mientras que el control de la temperatura se lleva acabo gracias a un microprocesador que utiliza el sistema PID y la calefacción es controlado por “relés solid state”. Un panel sinóptico con led facilita mucho el interfaz usuario.
Por su parte, la gama Sincro 200 es una seria avanzada. EL circuito de deshumidificación doble-torre con regeneración en contracorriente, junto con un microprocesador Sincro, asegura un sincronismo perfecto entre el rendimiento y dotación de la máquina que llega hasta -55º C en Dew Point. El puerto Modbus es serie asegura el control del proceso. EL Master 200 completa la flexibilidad de su gracias a la autoconfiguración de sistema, que incluye una lista de materiales, “password superuser” y manutención programable.
Sincro 400 es una serie de máquinas de doble bomba. Como es la serie 200, el control está asegurado por un potente microprocesador Sincro, además de la bomba utilizada durante el proceso, hay una bomba dedicada exclusivamente a la regeneración. Los circuitos, entonces, son independientes y hacen que la producción sea constante, especialmente en las máquinas medio-grandes.
La serie Sincro 600 está diseñada para las aplicaciones más difíciles. El circuito de deshumidificación es del tipo a doble torre y doble bomba con la implementación del sistema a doble circuito. Como en la serie 400, los circuitos de proceso y regeneración son separados. Además, esta serie tiene un circuito que completa la regeneración o circuito cerrado con un “cooler” que enfría la torre que está regenerando . Este mecanismo permite elevar los rendimientos de la serie Sincro 600 hasta -75º C en Dew Point. Para usos más complicados, como el PET, esta serie utiliza una cámara de calefacción externa.
La serie 700 es la hoja de la gama entera, ya que presenta todas las características y las prestaciones de la serie Sincro 600 pero con un interfaz usuario muy avanzado y un panel touch screen muy intuitivo. En la pantalla se puede ver en tiempo real el estado de funcionamiento de la máquina, mientras que todos los parámetros están disponibles en forma gráfica. Además, el programador semanal está en serie.
Soluciones para la industria del tapón
El sistema automático de medición de tapones Visilab Caps de Proditec que proporciona en tiempo real datos de altísima precisión aumentando la eficacia del proceso (inyección o compresión): diámetros, altura, flecha, peso del tapón. permite la cualificación instantánea de los moldes y proceso hasta 90 tapones por cuarto de hora (30/25, 28 mm o similares).
Por otro lado, Visicaps Compact es un sistema de clasificación de tapones de alta velocidad que permite controlar y seleccionar el 100 por cien de su producción, en línea o fuera de línea, expulsando los tapones defectuosos automáticamente. Permite quince operaciones de control simultáneas (inspección dimensional, defectos de aspecto, microporos, defectos de forma). Es fácil de uso y de integrar en sus instalaciones existentes. Tiene una cadencia de verificación de hasta 120.000 tapones por hora (28 mm) hasta 50 mm de diámetro, una máxima flexibilidad para la manipulación de varios tipos de tapones y es totalmente adaptable y ampliable a la necesidad del cliente.
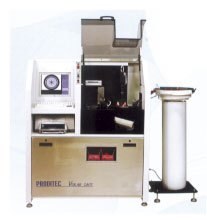
Molino
La bancada del molino dispone de una cuchilla fija en cada lado, inclinada respecto al plano horizontal del rotor, que al incidir con las cuchillas del rotor produce un verdadero corte tipo tijera, evitando el desgarro que producen los molinos clásicos.
Las cuchillas son un prisma afilado sin ningún tipo de taladro, realizadas en acero indeformable al cromo, templado y revenido. Se fina mediante cuñas a presión , lo que permite un fácil reglaje y sustitución.
al no tener taladros de fijación, no se producen roturas por concentración de tensiones de temple, se abarata el coste de las cuchillas y aumenta su duración.
La especial concepción y diseño de este sistema de corte, permite ahorrar hasta un 30% de la energía consumida en la molienda.
El rotor, cerrado o abierto, está construido en acero aleado al cromo-níquel, y se sostiene sobre rodamientos aislados y el sistema de refrigeración por agua del rotor, rodamientos y cuchillas laterales. Tiene una tolva modificable según las necesidades del cliente y el trabajo a efectuar; el tamiz es fácilmente intercambiable; el diámetro mínimo de los taladros es de 5 mm y dispone de una insonorización integral, parcial o mediante cabina.
Entre los modelos de molinos de Eurotecno destacan: MGV-80502 y MGV- 120653, concebidos para tritura piezas de gran volumen de materiales plásticos en general y ene especial cajas, botellas bidones, etc. sean de polietileno, polipropileno, ABS, PVC o PET; MEV-26151, para moler la colada que expulsan las inyectoras y, MEC-26151 y MEC-30201, para moler la colada caliente, que desecha la extrusora al principio del ciclo.