Visión artificial en la industria alimentaria
Lo primero que uno acostumbra a pensar cuando se habla de una cooperativa agrícola donde se clasifica y almacena fruta, es que se trata de un lugar poco sofisticado con gran cantidad de polvo y con cientos de personas clasificando la fruta de forma manual. Evidentemente, este concepto, poco tiene que ver con la realidad. Este tipo de industria, actualmente, es altamente sofisticada, con sistemas de control automático de humedad y temperatura, así como con mecanismos de control de niveles de oxígeno, normalmente situadas en grandes naves del tamaño de un hangar de aviación y, por supuesto, con sistemas de visión en color para clasificar los distintos tipos de frutas y hortalizas.
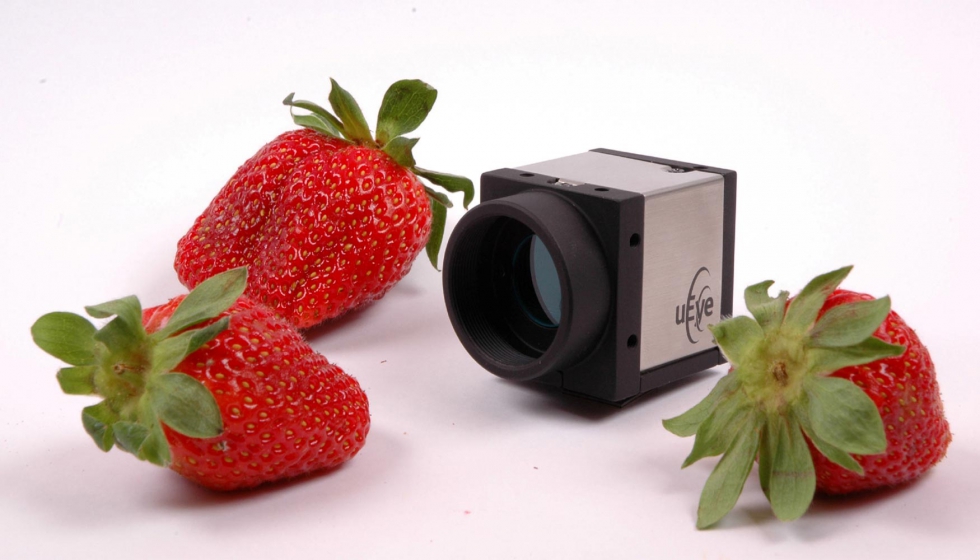
Los sistemas de visión artificial que se utilizan en estos entornos están dispuestos en una zona de la instalación, donde capturan las imágenes de las frutas que se desplazan sobre la cinta transportadora. El sistema de visión es capaz de clasificar la fruta según su forma o tamaño, y determinar su grado de maduración a través del color.
Los sistemas de inspección de alimentos frescos en Europa tienen una gran aceptación y difusión. La adopción de estos sistemas ha sido determinada principalmente por dos factores: el envejecimiento de los trabajadores, que tiene como resultado el hecho de que haya menos personas disponibles para este tipo de trabajo de clasificación, y los altos costes laborales en los países desarrollados.
Consecuentemente ha habido, en los últimos años, un gran número de compañías, que han fabricado máquinas de clasificación de alimentos en los países desarrollados, pero que a su vez empiezan a exportarlas a los países en vías de desarrollo, ya que el producto clasificado, habitualmente, tiene su mercado en Europa y Estados Unidos y estos países solicitan la máxima calidad.
De hecho, cabría distinguir entre dos tipos de mercados: uno relacionado con los alimentos frescos, y otro con los alimentos elaborados donde se incluye algún tipo de valor añadido, como la congelación, enlatado, empaquetado, precocinado…
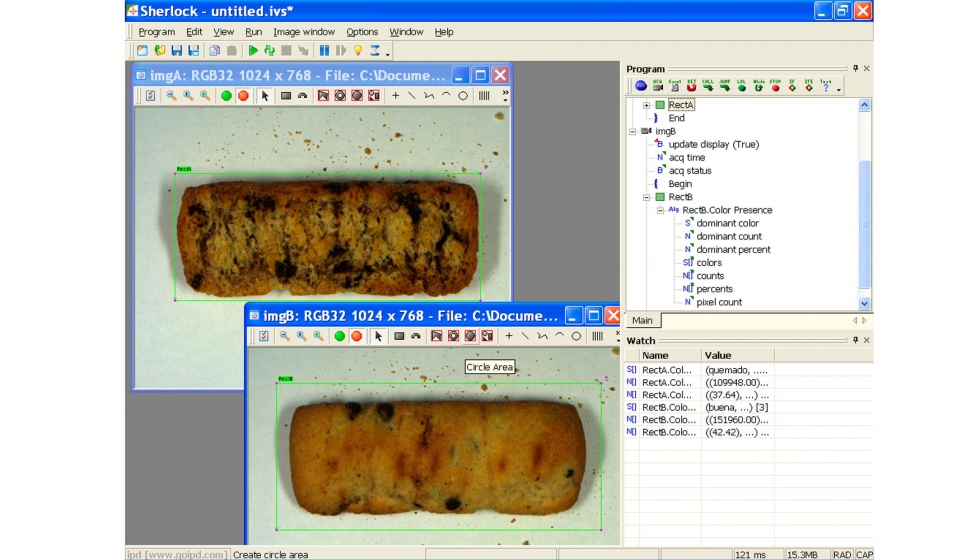
La inmensa mayoría de las compañías relacionadas con la alimentación utilizan sistemas de visión artificial en color, mientras que en otros mercados, donde tradicionalmente se ha utilizado estos sistemas, como el de la automoción o el de los semiconductores, se usan mayoritariamente sistemas basados en cámaras monocromas.
La inspección en la industria alimentaría se lleva a cabo, tanto con cámaras lineales como con cámaras matriciales, dependiendo del tipo de fabricante y del tipo de clasificación. Algunos fabricantes de maquinaria para la industria alimenticia ofrecen también versiones basadas en cámaras infrarrojas, que pueden detectar la presencia de hueso en las frutas o determinar características no visibles en su superficie.
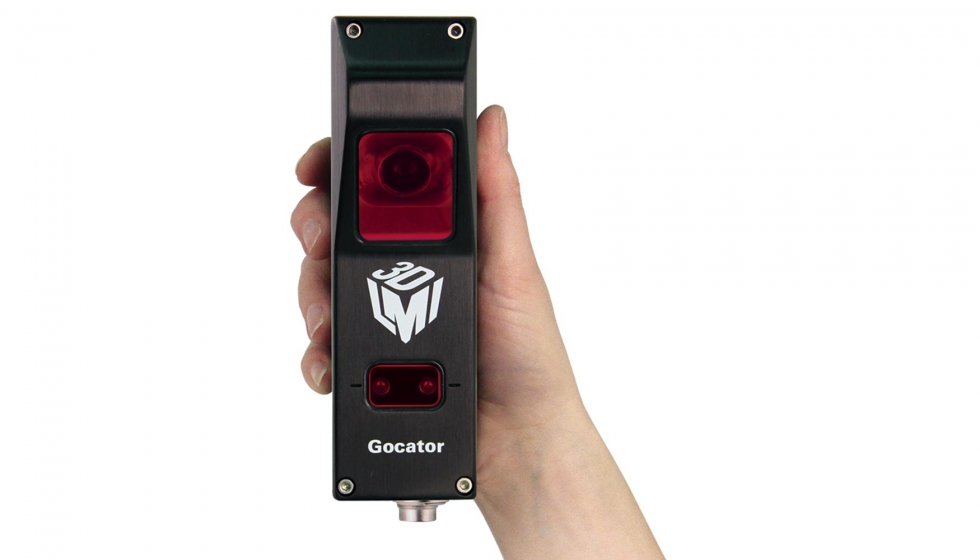
Los sistemas de clasificación están constituidos frecuentemente por cintas transportadoras, sin embargo otros están basados en mecanismos de clasificación por gravedad, que se utilizan típicamente con productos secos, como arroz o legumbres. Las compañías especializadas en frutas o verduras, generalmente canalizan los productos en varias líneas, utilizando copas o recipientes especiales, que pasan bajo las cámaras de visión.
Normalmente estos sistemas incluyen múltiples cámaras para capturar las imágenes de toda la superficie del producto. Cuando los productos son más o menos redondeados, se usan mecanismos para hacer rotar el producto bajo el sistema automático de inspección visual. La clasificación por forma se establece a partir de los diámetros máximo y mínimo, perímetro, área, así como a partir de la relación entre los diferentes parámetros medidos. Las decisiones de color se basan en la superficie total escaneada. Para determinar las propiedades del color se utilizan parámetros como; relación simple de porcentaje, histograma de valor de intensidad, definición de áreas máximas o mínimas, etc.
Las tecnologías de visión artificial se han visto beneficiadas por los avances en los microprocesadores y DSP, la alta resolución de las cámaras tanto lineales como matriciales, el desarrollo de sistemas de iluminación especializados, así como por las investigaciones realizadas por especialistas en agricultura, conjuntamente con investigadores de automática y visión. El resultado es que los sistemas de visión actuales son capaces de resolver los requisitos que demandan la industria alimentaría.
La mayoría de sistemas se hacen prácticamente a medida, esto significa que a menudo incorporan iluminación cuyo espectro es específico para el tipo de alimento a inspeccionar, de forma que puedan mejorar la selección de estos tipos de productos. Estos sistemas son capaces de clasificar los alimentos con respecto a su apariencia, y por tanto, pueden identificar defectos relacionados con plagas, picaduras de animales, efecto de las heladas, oxidación o cualquier otro tipo de imperfecciones o enfermedades que pueden identificarse a través de la superficie.
Algunos fabricantes proporcionan sistemas de visión basados en rayos X, que son capaces de detectar defectos internos o condiciones que no podrían ser detectables tomando sólo la imagen de la superficie del producto.
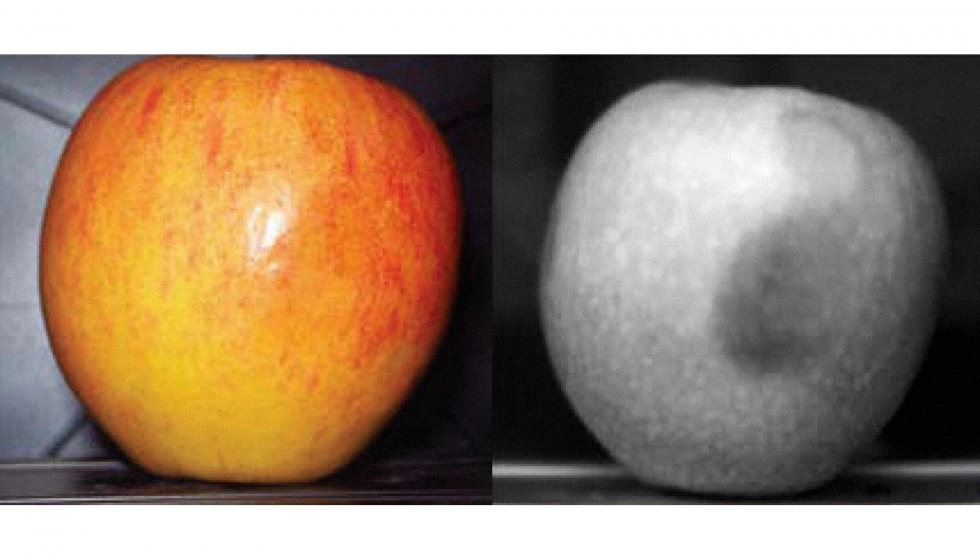
En algunas ocasiones, sistemas específicos de iluminación pueden proporcionar suficiente contraste y de esta forma clasificar mediante cámaras monocromas. Otros sistemas aprovechan las ventajas que pueden proporcionar la luz infrarroja o ultravioleta, u otras propiedades monocromáticas del espectro visible.
Las máquinas de clasificación se han venido utilizando en la industria de la alimentación desde la década de los 30, donde se utilizaban palpadores, pesadoras, y clasificadoras mecánicas. En los 90 muchas de las compañías que utilizaban estas metodologías empezaron a introducir sistemas de visión artificial en sus máquinas. Sin embargo, el gran auge ha llegado en el momento en que los precios de los sistemas de visión en color han sido realmente competitivos.
En la actualidad hay numerosos sistemas en el mercado desarrollados para clasificación de todo tipo de frutas: manzanas, cítricos (limones, naranjas, mandarinas, …), tomates, melocotones, peras, melones, frutas tropicales (mango, papaya, …), así como para legumbres, patatas, cebollas, ajos y otros tipos de hortalizas. Del mismo modo, existen máquinas para el mercado de alimentos en grano o procesados como: nueces, cereales, arroz, judías, lentejas, semillas de girasol, patatas fritas, aceitunas…
La utilización de estos sistemas ha ayudado a mejorar en gran manera la consistencia de la gradación. Uno de los grandes inconvenientes de la inspección manual realizada por personas, es la ineficiencia en las labores de inspección que requieren examinar productos aparentemente muy similares. Después de un periodo de tiempo relativamente corto la agudeza visual se deteriora, incluso en el caso de que la clasificación sea relativamente simple. Aunque no son perfectos, los sistemas de clasificación de alimentos basados en visión artificial son mucho más consistentes en la clasificación de productos buenos y malos, separación de productos correctos de extraños y en clasificación por gradación.
Valorando solamente estos factores ya justifican la adquisición de estos equipos. Si además se considera que cada vez es más difícil encontrar mano de obra especializada, que quiera hacer estos tipos de trabajos de inspección tan rutinarios, se llega a la conclusión que los sistemas de inspección por visión artificial son imprescindibles en este sector industrial.
Un gran número de compañías actualmente ofrecen sistemas de corte de porciones por chorro de agua, que incorporan sistemas de visión 3D para caracterizar el volumen del producto sobre el que se deben hacer las porciones. Esto incluye sistemas de porcionado para pescado, pollo, pavo, cerdo, ternera y todo tipo de carne.
Otras aplicaciones interesantes en la industria alimentaria son las relacionadas con inspección de huevos, clasificación de carne avícola (diferenciación y clasificación de muslos, pechugas, ..), inspección de sistema de ahumados, y control de alimento enlatado.
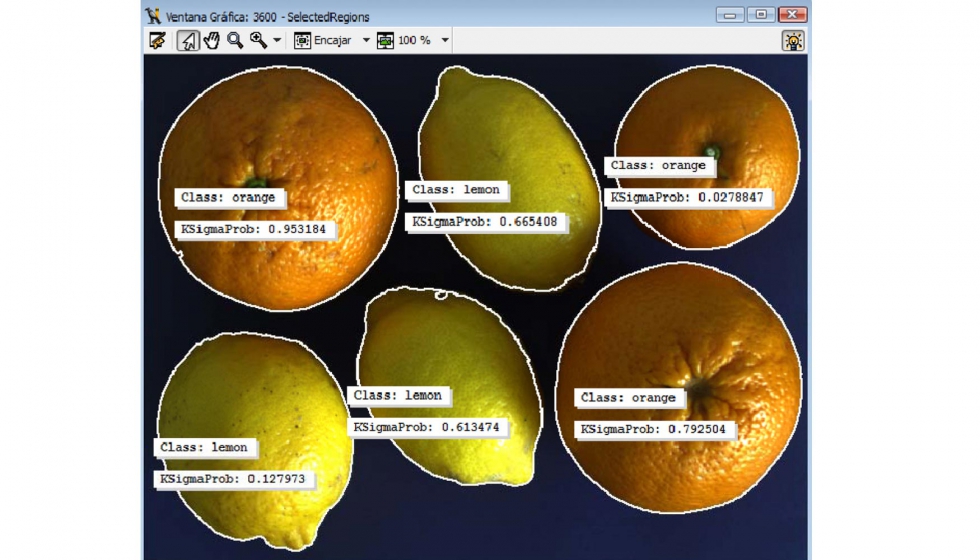
Otro sector alimentario donde la visión artificial está cada vez más presente es el de la panadería y bollería. Existen sistemas de monitorización en 3D de pan, pastas, crackers, y galletas. Como esta industria ya utiliza sistemas de empaquetado automático, la visión artificial se hace cada vez más necesaria para evitar cuellos de botella ocasionados por productos con tamaños erróneos. Las líneas de producción son cada vez más rápidas y por tanto las personas que clasifican este tipo de productos son menos capaces de controlarlas visualmente.
La determinación del volumen a través del análisis 3D se hace cada vez más importante a la hora de empaquetar los productos correctamente, dentro de bolsas o paquetes de unas dimensiones determinadas.
Infaimon es especialista en sistemas de visión artificial desde hace 23 años y ofrece soluciones basada en los sistemas de visión artificial que permiten visualizar continuamente los productos, obtener los datos de tamaño y forma en tiempo real, enviar esta información al sistema de control de la producción, y en el caso de no ajustarse a las condiciones predeterminadas, variar las condiciones de cocción y/o de suministro.
Se deben considerar distintos requisitos a cumplir para que un sistema de visión artificial en la industria alimenticia tenga éxito. Es fundamental, que tanto el usuario final como el fabricante de maquinaria estén íntimamente familiarizados con todas las características de la aplicación. También es sumamente importante, que la instalación convenza a las personas que están trabajando en la cadena de producción. Cuando se demuestra que la instalación de un sistema de visión mejora la forma de trabajo de los operarios, entonces el éxito del sistema está asegurado. La mejor forma de garantizar este éxito es entrenar correctamente a los operarios que utilizarán el sistema.
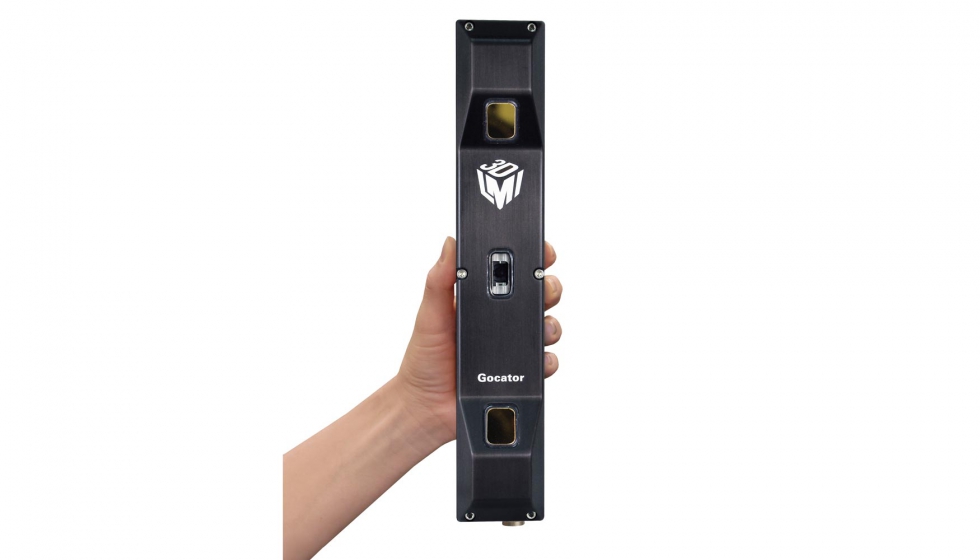