La firma reconstruye este equipo, fabricado en 2008, para una empresa del sector eléctrico
Euromaher da una segunda vida a la granalladora de túnel Lauco 60 FAC de OMSG
Uno de sus últimos trabajos ha sido la reconstrucción de una granalladora de túnel de la marca OMSG modelo Lauco 60 FAC del año 2008 y cuyo destino ha sido una empresa española especialista en el sector eléctrico. Es una máquina de túnel específica para el granallado de chapas y perfiles que se desplazan sobre rodillos en plano. La máquina se va a emplear en la mayoría de componentes de torres eléctricas y de comunicación que requieren de un acabado especial con unos criterios muy concretos. Una amplia tipología de piezas con un tamaño que va desde los 600 mm. de anchura hasta los 300 mm máximo de altura que conforman las torres.
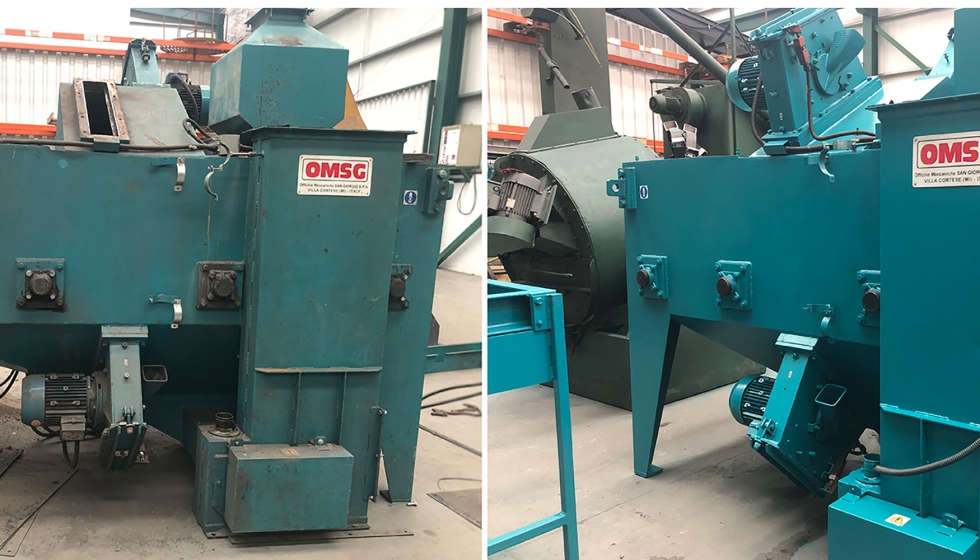
Antes y después del cuerpo principal de la máquina reconstruida en Euromaher.
Además de limpiar las superficies, debe de conseguirse en los contornos de todas las piezas una rugosidad y grosor determinados para que la adherencia de las siguientes etapas de tratamiento y pintura sea máxima y duradera en la vida útil de las piezas. Es importante que en este paso se consiga la máxima rugosidad para poder realizar los pasos posteriores de recubrimiento y pintura con el objetivo de que el resultado final cumpla con la normativa vigente y certifique los criterios de calidad y medio ambiente relativos al sector.
El reacondicionamiento de esta granalladora permite un aumento del 20% en la producción y supone un ahorro considerable para el cliente, en torno al 40-50% respecto a un modelo nuevo.
A continuación, se detallan los diferentes procesos realizados para obtener una granalladora competitiva.
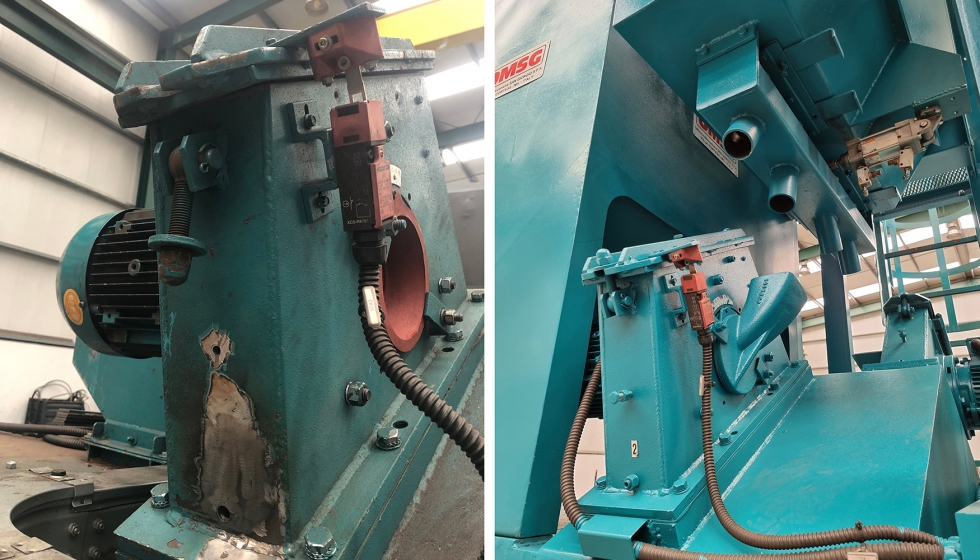
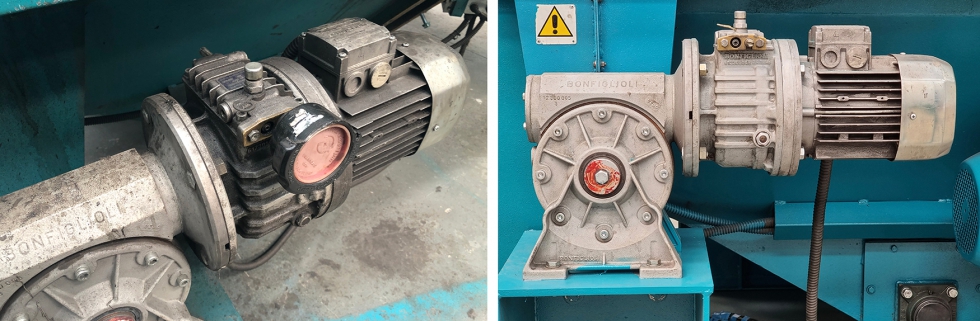
Análisis previo
Antes de proceder al desmontaje de las partes estructurales de la máquina se acondiciona la máquina mediante el lavado, desengrase y limpieza para poder realizar una inspección a fondo del estado de cada una de las partes que la componen.
El siguiente paso es detectar posibles fallos en el sistema eléctrico, mecánico y neumático que son los que determinan el funcionamiento de la máquina. En función de los resultados de este análisis inicial, se establece un plan de reconstrucción.
Por lo que se refiere a esta máquina granalladora, presentaba un aspecto externo bastante degradado. En la siguiente fase, se diagnosticó el estado de la parte interna y se tomaron las medidas pertinentes.
Proceso de reconstrucción
A continuación comienza con el desmontaje de la máquina para realizar la reparación de la parte estructural de la máquina y el desmontaje de los conjuntos y verificación de su estado. Todos los componentes deteriorados o en mal estado se reparan o sustituyen por elementos nuevos dependiendo del estado y grado de desgaste.
- Se sustituyen las turbinas por 4 turbinas de nueva generación y sus marcos de recepción de turbina. Las turbinas por las que se han cambiado son turbinas patentadas por el propio fabricante que las convierte en garantía de funcionalidad y duración. Son los elementos que realizan el lance de la granalla y el conjunto de la máquina que más esfuerzo realiza y que están expuestos a un mayor desgaste. Por esto, era importante ponerlas nuevas para comenzar desde cero con ese cuidado minucioso que necesitan y, a partir de ahí, revisarlas frecuentemente y someterlas a operaciones de mantenimiento habituales.
- También se sustituye el elevador de cangilones. La cinta de goma estaba algo deteriorada y para garantizar el perfecto transporte de la granalla que sale de los sistemas de recuperación al separador mediante esta cinta de goma con cangilones atornillados, la mejor opción era sustituirla.
- Se revisa el separador de granalla para que el resto de residuos queden aislados de la granalla. Si no presenta problema y realiza bien su función, se mantiene, como en este caso.
- Se recuperan los sinfines. Como el diámetro y el espesor de la hélice no estaban deformados ni reducidos en exceso, se ha realizado una limpieza exhaustiva y se han cambiado los anillos de retención y los rodamientos para el posterior montaje.
- Se revisan cada uno de los soportes y rodillos de los caminos de entrada y salida. Se han desmontado y revisado uno a uno todos los rodillos. Los que sufrían de un desgaste excesivo se han sustituido. Del resto, a los que presentaban pequeñas deformaciones o alguna imperfección, se les han cambiado los rodamientos, soportes y piñones. Posteriormente, se ha realizado la limpieza superficial del rodillo y preparado la superficie para el acabado final. La calidad de los rodillos determinará el giro uniforme de la pieza por lo que es importante que todos estén en buen estado, sobre todo, cuando muchos de los componentes son pesados, como en el caso de las torres eléctricas y de comunicación.
- Se realiza la revisión y sustitución de las tres unidades filtrantes de manera que cumplan las normativas vigentes con los sistemas de aspiración y depuración de polvo.
Una vez revisados todos los componentes y sustituidos todos los que eran necesarios para un funcionamiento óptimo de la granalladora, se procede al montaje completo de la máquina.
Tras el montaje, se realiza una prueba general de la máquina para comprobar que todo funciona adecuadamente y no se produce ningún error a nivel de programación. A continuación, con la seguridad de que todo funciona de manera correcta, se pasa a la fase de pintado.
Un trabajo manual y delicado al detalle con el color elegido por el cliente o los propios de la marca. Las partes internas que no se ven, se han ido pintando tras su revisión o recuperación.
El proceso de reconstrucción termina con la parte eléctrica y, según los resultados del análisis inicial, se repara o se sustituye por un cuadro eléctrico nuevo. En este caso, estaba bastante bien, se realizaron los retoques y sustituciones de los elementos y seguridad deteriorados y el funcionamiento era perfecto. No fue necesario sustituirlo por uno nuevo.
El resultado es una máquina a la que se ha realizado un retrofitting con una infinita mejora tanto de la productividad del equipo como de la calidad del producto a granallar con una inversión muy inferior al de una máquina nueva y con la garantía de una nueva.
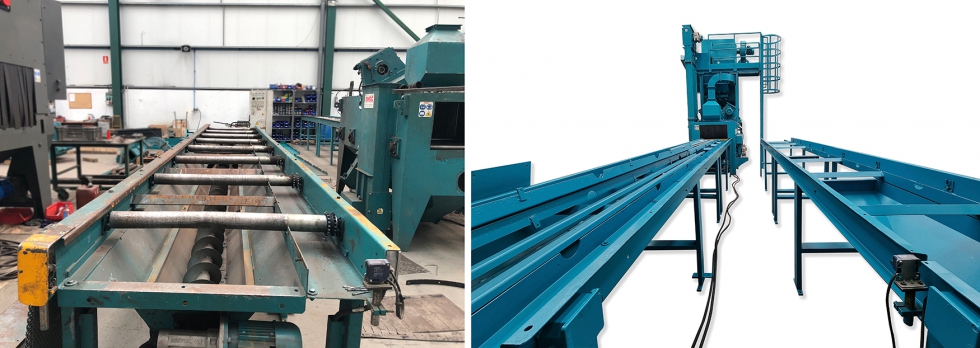
Recepción
Una vez terminado todo el proceso de construcción y comprobado que todo funciona correctamente, se realiza la recepción de la máquina para mostrar al cliente el resultado final. En este caso, debido a la complejidad de las piezas a granallar, la prueba final se realizó una vez montada en la empresa del cliente.
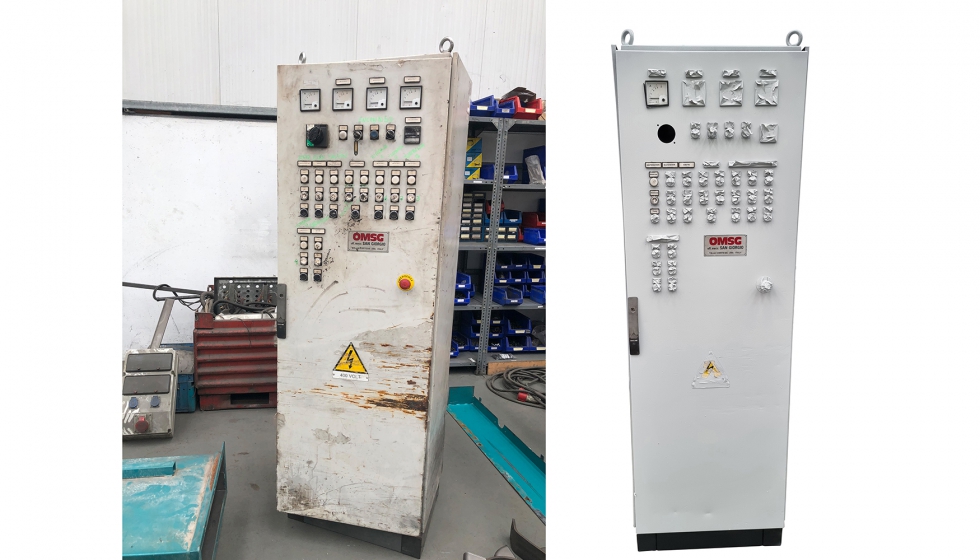
Euromaher, especialistas en el retrofitting para el acabado de superficies
Representaciones Euromaher, gracias a su ‘know how’ de más de 20 años, ha logrado que la reconstrucción y reacondicionamiento de maquinaria se convierta en uno de los puntos fuertes de su empresa. Una opción muy ventajosa que permite adquirir una máquina con la garantía de una nueva y con un precio mucho más competitivo.
Este tipo de venta goza de gran éxito entre los clientes de Euromaher que conocen su eficiencia en este campo y llevan más de una década con el tema del reacondicionamiento para optimizar los procesos de producción de las empresas. Además de la maquinaria de ocasión, completan su oferta con una amplia gama de maquinaria nueva para el tratamiento de superficies, estampación en frío e inyección de aluminio. Las soluciones integrales de Euromaher tienen como objetivo permanecer con el cliente desde el primer contacto hasta realizar la integración de la máquina en la producción y continuar con asistencia técnica y recambios toda la vida útil de la maquinaria.
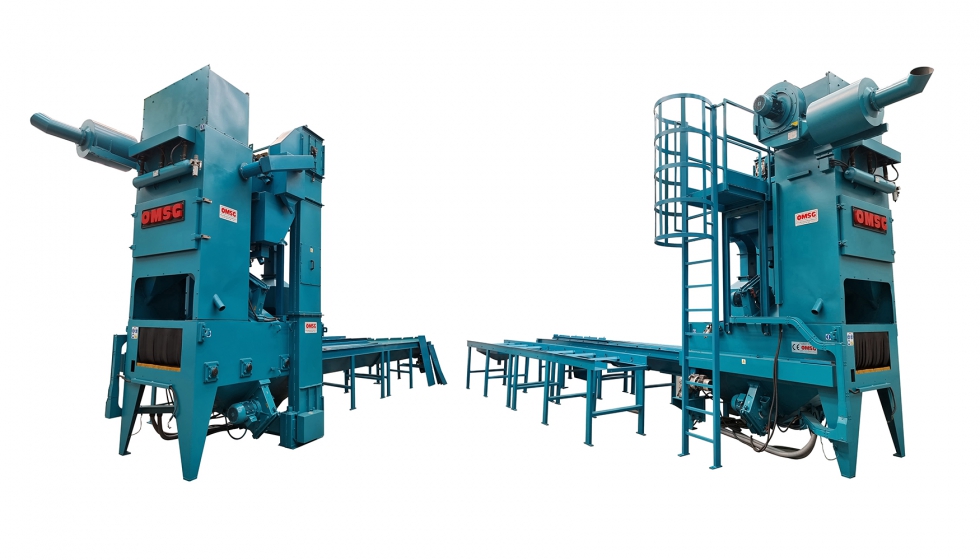