Renishaw organiza la I Jornada Anual sobre Fabricación Aditiva para Empresas del Sector Aeroespacial
El pasado 3 de abril Renishaw celebró la I Jornada Anual sobre Fabricación Aditiva para Empresas del Sector Aeroespacial en las instalaciones del Centro de Fabricación Avanzada Aeronáutica (CFAA, Zamudio, Bizkaia) y con la participación de ITP Aero, Madit y CiTD. Durante la jornada las empresas participantes expusieron sus actividades en el sector de la fabricación aditiva para cerrar la jornada con una mesa redonda que dio paso a una visita por el CFAA.
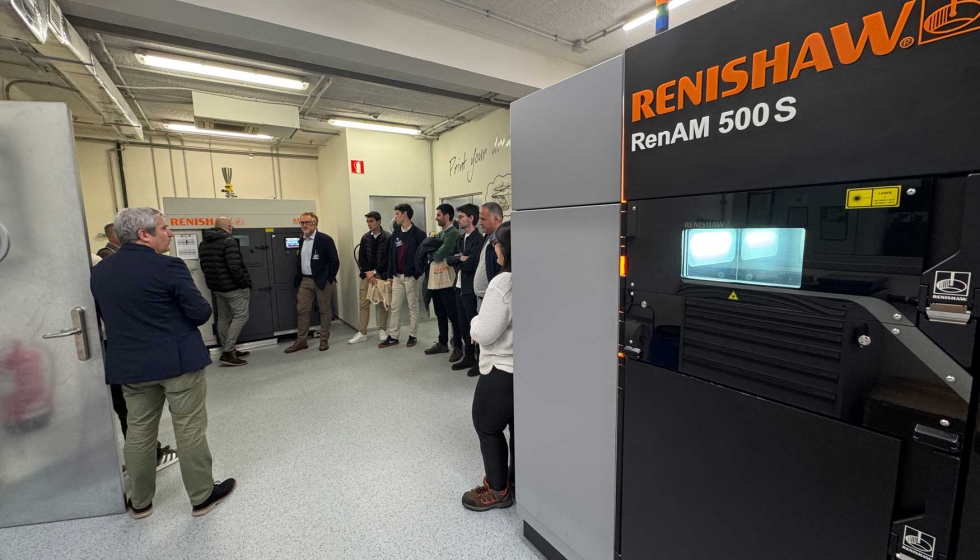
El escenario elegido por Renishaw para esta jornada fue inmejorable. El CFAA trabaja con un enfoque directo a las aplicaciones finalistas y apuesta por la generación de nuevo conocimiento en tecnologías avanzadas de fabricación. Uno de los terrenos en los que actúa es la fabricación aditiva para la que cuenta, entre otros equipos, con una máquina Renishaw AM400 y una RenAM500.
Condujo la jornada Aitzol Lamikiz, del CFAA y la Universidad del País Vasco y experto en fabricación aditiva (AM – Additive Manufacturing), quien introdujo el papel de la fabricación aditiva en el sector aeroespacial. Según informó, las diversas previsiones apuntan a la fabricación de más de 40.000 aeronaves nuevas para el año 2024, a lo que se suma el crecimiento exponencial del número de objetos lanzados al espacio. En los últimos cinco años se han lanzado más objetos que en todo el resto de la historia. En definitiva, la demanda de piezas es inmensa.
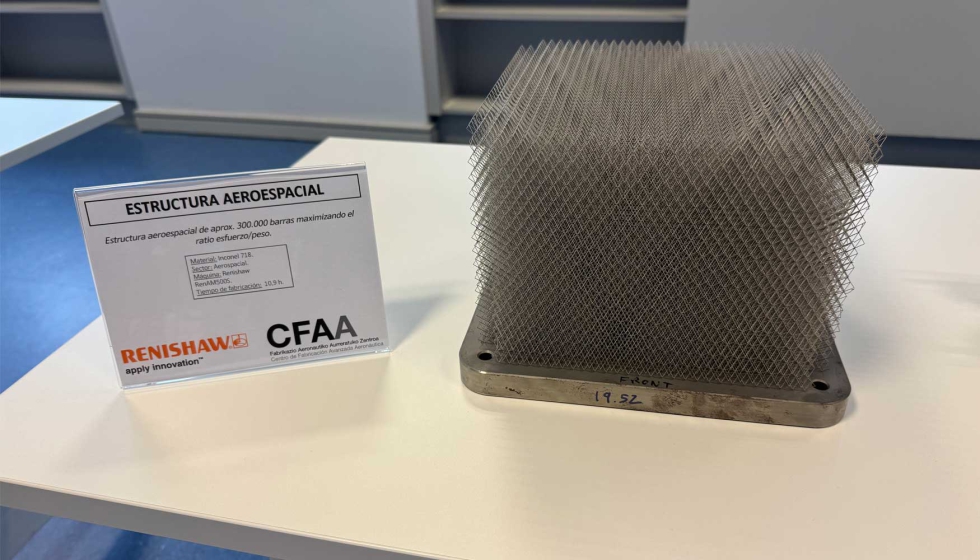
Como reto principal del sector, en términos generales, destacó el desarrollo de aeronaves más sostenibles y con mayor eficiencia, lo cual eleva la complejidad del motor. “Hay que fabricar muchas piezas -dijo- y cada vez más complejas. Aquí la fabricación aditiva es clave”.
En el CFAA se desarrollan tecnologías para fabricar estos componentes. Desde el principio la fabricación aditiva ha sido fundamental en el CFAA y, de hecho, la primera máquina que se instaló fue una Renishaw.
La siguiente intervención fue la de Fernando Lartategui, tecnólogo de fabricación aditiva en ITP Aero, una empresa de 1.612 M de euros de ingresos con 5.600 empleados repartidos por todo el mundo y que ofrece tecnologías de propulsión innovadoras, reforzando en la actualidad el mantenimiento de los motores ligado a la sostenibilidad. Si en el negocio de aviones comerciales funciona como un Tier 1, en defensa es una OEM, con ingeniería de motor completo y ensamblaje de motor, entre otras actividades.
En el campo de la AM la tecnología L-PBF (laser powder bed fusión) es la de más desarrollo en ITP. Lartategui mostró algunos ejemplos de reducción de peso y coste como la estructura TBH (Tail Bearing Housing) fabricado para el demostrador Ultrafan. El 80-85% del componente se ha fabricado por L-PBF. Otro ejemplo son los vanos del TEC (Turbine Exhaust Case) que motoriza el Airbus A400M.
Como oportunidades de la AM citó la mejora de diseños y su complejidad, la simplificación de procesos, la reducción de tiempos de industrialización, la simplificación y/o posesión de la cadena de suministro y la mayor utilización de materia prima comparado con procesos convencionales.
Como retos, citó la necesidad de diseñar para el proceso aditivo, la superación de las dudas de la implantación de AM tanto internamente en la empresa como en los reguladores de la industria, la gran cantidad de validaciones requeridas de componentes y controles de proceso, la necesidad de nuevos programas aeronáuticos para explotar el gran potencial del AM y que la tecnología debe estar lista cuando surjan las oportunidades.
Uno de los temas destacados de su presentación fue la digitalización de los procesos AM. Para que un diseño sea adecuado la fabricabilidad por AM es un punto importante.
En sus conclusiones afirmó que la fabricación aditiva es una realidad, pero que aún se requieren evidencias con la certificación de más componentes y su producción. Por otro lado, deben surgir nuevos programas aeronáuticos para explotar el gran potencial de AM. Señaló también la necesidad de reducir validaciones de componentes y de simplificar los controles de proceso y situó la colaboración de centros y universidades como factor clave.
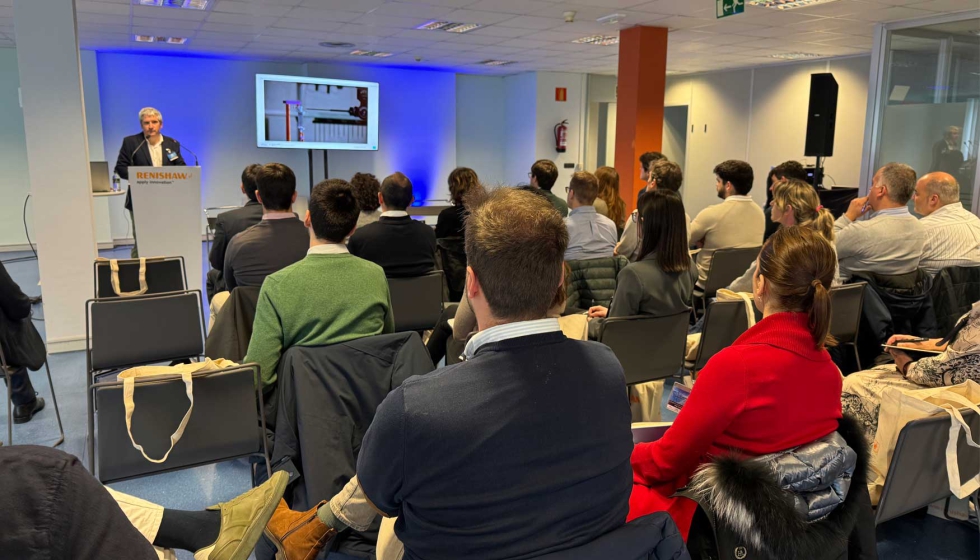
Madit baja la fabricación aditiva a tierra
Javier Díaz, CEO de Madit, fue el siguiente en intervenir. La empresa, situada en Zamudio (Bizkaia) realiza series cortas, prototipos y pre-series, piezas unitarias y componentes mejorados. Está especializada en tecnología SLM, y ofrece a la industria todo el proceso, desde el diseño y simulación, pasando por la fabricación y el postprocesado.
Como ejemplo de su actividad en aeronáutica habló de su participación en el proyecto Brava con Morpheus Designs y Airbus, en el desarrollo de un intercambiador de calor avanzado. Para desarrollar un intercambiador se empieza por el diseño y la simulación, luego se desarrolla el core (el elemento más crítico del intercambiador) y se piensa en cómo se diseña para que sea fabricable. A continuación se realiza el desarrollo de parámetros y se pasa a la integración y la digitalización para llegar a la fabricación aditiva. Posteriormente es el momento del tratamiento térmico y el mecanizado y la soldadura, si se requiere. Por último está la validación con el control dimensional y la prueba de fugas, la tomografía y la validación funcional.
Javier Díaz también determinó como crítico el hecho de que hay que diseñar para el proceso SLM, un proceso complejo que requiere gran experiencia y en el que los post procesos son elementos clave.
Durante su intervención, muy centrada en proyectos reales, afirmó: “La fabricación aditiva es una tecnología de presente, no de futuro. Estamos fabricando para todos los sectores, no es una tecnología solo para altos valores añadidos. Si se hace todo bien es un procesos repetitivo, con menos costes y rentable para todas las partes”.
Tras el baño de realidad por parte de Madi fue el turno de Lidia Hernández, senior Stress Engineer de CiTD, una empresa que también ofrece soluciones para aeroespacial. Mostró aplicaciones que ya están volando, con tolerancias dimensionales muy críticas y destacó la importancia de la simulación para reducir riesgos y acortar plazos.
Mesa redonda
Moderada por Aitzol Lamikiz (CFAA), en la mesa redonda participaron Fernando Lartategui, Javier Díaz y Marta García-Cosío (CEO de CiTD).
El avance en los últimos diez años ha sido muy rápido, pero en los dos últimos años ya se ve que la tecnología se está asentando y se está centrando en la industrialización. Ya no hay saltos innovadores tecnológicamente hablando, pero la máquinas de hace años, siguen produciendo de forma rentable.
Como ya se había avanzado en las intervenciones anteriores, la necesidad de diseñar para el proceso aditivo volvió a acaparar la atención de la mesa redonda. Pero la libertad para diseñar no es total, todavía hay barreras. El conocimiento no es profundo y muchas piezas no están diseñadas para el proceso aditivo. Muchos productos llegan de otros procesos y aunque haya cierta flexibilidad, siempre hay limitaciones que condicionan. “Si desde el inicio la pieza se hubiera pensado en aditivo, sería todo mejor”.
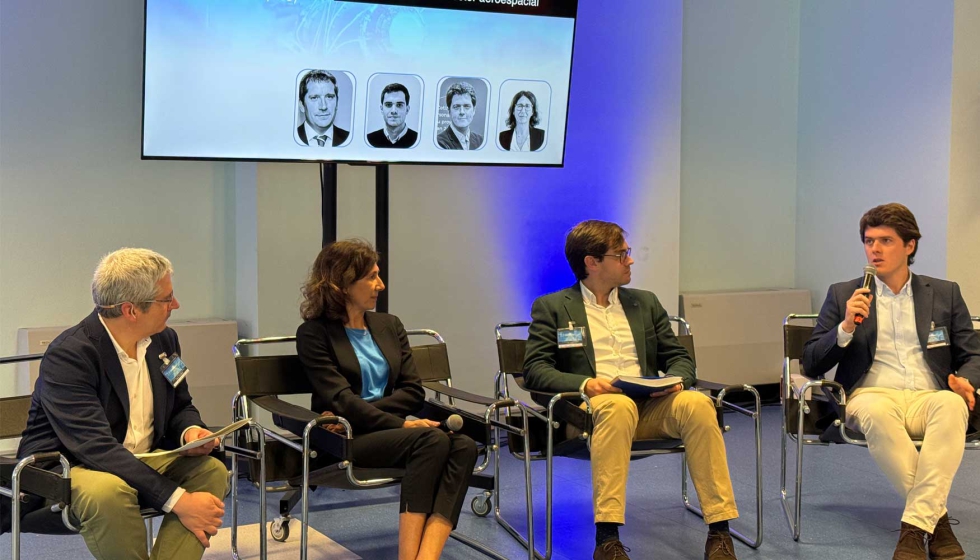
En la mesa redonda, moderada por Aitzol Lamikiz (CFAA), participaron Marta García-Cosío (CEO de CiTD), Fernando Lartategui (ITP Aero), y Javier Díaz (Madit).
Hay que educar mucho y saber lo que supone cada pequeño cambio de diseño. El cliente es muy reacio a cambios, algo todavía más acentuado en aeronáutica. La tecnología está lista, si para esas más de 40.000 aeronaves previstas se flexibiliza todo un poco y si los reguladores se adaptan, puede haber un crecimiento importante y supondría una explosión de la AM que va a requerir más equipos y más productividad (no solo en número de láseres).
Otra de las ideas interesantes surgida en el debate fue la de que las normas, al principio, impulsan la tecnología, pero hay un momento en que la ralentiza. Hay un exceso de normativa muy pensada en control de proceso. En ocasiones a las máquinas se les exige demasiada sensórica. “¡Están dopadas sin necesidad!”.
Otra reflexión interesante: la regulación tiene que tener en cuenta la criticidad de las piezas.