Entrevista a Jaime Cuesta, ingeniero de Nikon SLM Solutions
Jaime Cuesta, ingeniero de Nikon SLM Solutions, empresa representada por Delteco, analiza en esta entrevista la estrategia de la compañía en el sector de la impresión 3D en metal y su impacto en la industria. Con innovaciones como la tecnología LPBF y sistemas de fabricación aditiva de múltiples láseres, Nikon busca consolidarse como un referente en fabricación avanzada, ofreciendo soluciones para sectores como el aeroespacial, la automoción y la defensa. Cuesta participó como ponente en una de las jornadas de Aitiip Tech Days.
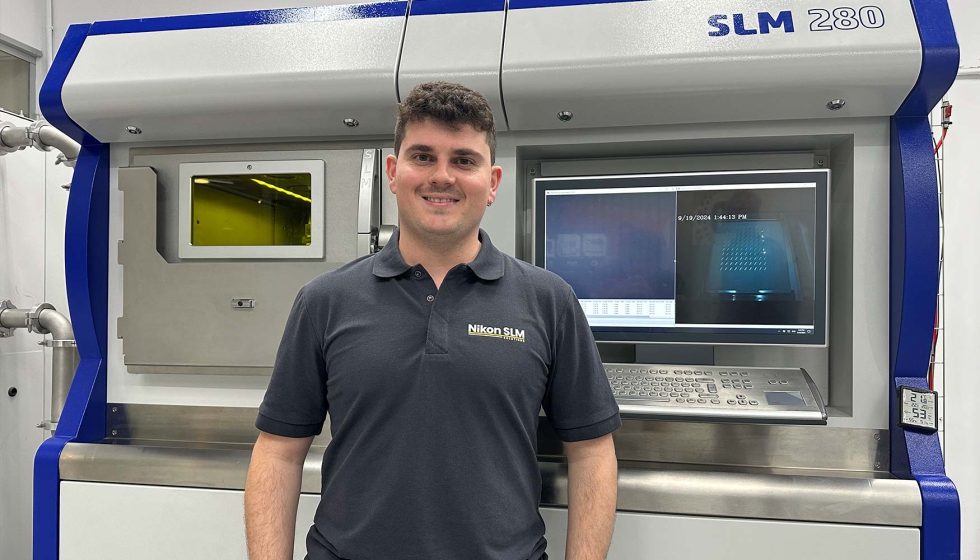
Nikon es ampliamente conocida en sectores como la metrología y los equipos de precisión. ¿Qué impulsó a Nikon a entrar en el sector de la impresión 3D en metal y cómo describiría su propuesta de valor en este mercado?
Nikon decidió entrar en el sector de la impresión 3D en metal como parte de su estrategia de diversificación y crecimiento en mercados avanzados de manufactura. Esta incursión se alineó con su experiencia en óptica de precisión, control de calidad y metrología, áreas críticas para la fabricación aditiva en metal. En este sentido, Nikon tuvo la intención de agrandar su compromiso con la fabricación avanzada y expandir esta línea de negocio.
Motivaciones para entrar en el mercado de impresión 3D en metal:
- Demanda en manufactura avanzada: la impresión 3D en metal ha experimentado un crecimiento significativo en sectores como la aeroespacial, automotriz y médica, donde la precisión y calidad son esenciales
- Sinergia con sus capacidades existentes: Nikon ya tenía un sólido historial en metrología, óptica avanzada y equipos de precisión, lo que facilitó su incursión en la manufactura aditiva con un enfoque en alta precisión y calidad
- Expansión estratégica: la compañía busca reducir su dependencia de mercados más tradicionales, como las cámaras fotográficas, y expandirse en industrias de alto valor agregado.
Propuesta de valor de Nikon en la impresión 3D en metal:
- Precisión extrema: aprovecha su experiencia en óptica y metrología para garantizar piezas con alta fidelidad dimensional
- Calidad y confiabilidad: sus soluciones se enfocan en minimizar defectos y asegurar la repetibilidad en procesos industriales
- Innovación en tecnología LPBF: gracias a SLM Solutions, Nikon ofrece sistemas de fabricación aditiva con múltiples láseres y mayor eficiencia
- Integración con manufactura tradicional: sus soluciones están diseñadas para complementar y optimizar procesos industriales ya existentes.
Con esta apuesta, Nikon no solo diversifica su portafolio, sino que también posiciona la impresión 3D en metal como una solución viable para la producción en masa con estándares industriales elevados.
Nikon SLM Solutions ha sido pionera en varias áreas, desde el desarrollo de la primera máquina de múltiples láseres hasta sistemas con 12 láseres. ¿Cuál considera que ha sido el hito más relevante de la compañía y cómo ha influido en la industria?
Uno de los hitos más relevantes de Nikon SLM Solutions ha sido el desarrollo del sistema SLM NXG XII 600, la primera impresora 3D en metal con 12 láseres de 1 kW cada uno. Este avance ha revolucionado la fabricación aditiva en metal, estableciendo un nuevo estándar en velocidad, productividad y escalabilidad para la manufactura industrial.
Impacto en la industria
1. Aceleración de la producción en masa:
- Con 12 láseres operando simultáneamente, la NXG XII 600 es hasta 20 veces más rápida que sistemas de un solo láser.
- Permite la fabricación de piezas grandes y complejas en horas en lugar de días, reduciendo los costos y tiempos de producción.
2. Expansión de la fabricación aditiva hacia la producción en serie:
- Antes, la impresión 3D en metal se utilizaba principalmente para prototipos o series pequeñas.
- Con esta máquina, se vuelve viable la producción a gran escala, especialmente en sectores como aeroespacial, defensa, energía y automoción.
3. Mayor accesibilidad para industrias exigentes:
- Empresas de aeronáutica y automoción pueden fabricar componentes críticos con una combinación de alta precisión, menor desperdicio de material y geometrías optimizadas.
- Esto ha impulsado la adopción de la fabricación aditiva como un proceso competitivo frente a la manufactura tradicional.
En su presentación en los Aitiip Tech Days mencionó su especialización en calidad y trazabilidad en fabricación aditiva (AM). ¿Podría explicar cómo Nikon SLM aborda estos aspectos y qué beneficios aporta a los clientes?
Nikon SLM Solutions se toma muy enserio el tema de la calidad. Contamos con la certificación TUV e ISO9001. Esta en nuestro día a día y en nuestra filosofía.
Todo empieza con nuestros proveedores, quienes tienen que cumplir ciertos estándares y condiciones nuestras de calidad para que lleguen a formar parte de nuestra lista de proveedores, tanto para el suministro de componentes de nuestras máquinas (láseres, ópticas, cableado, perfiles metálicos, tornillería, electrónica o paneles metálicos) como del suministro del polvo metálico para las impresiones nuestras y de nuestros clientes.
Al final, todos estos componentes son inspeccionados a su recepción para comprobar que cumplen nuestros estándares, son ensamblados en nuestra fábrica central en Lübeck, Alemania y a continuación se hacer controles de calidad de subgrupos y finalmente de la máquina. Posteriormente, se pone en funcionamiento la impresora y se somete a unas pruebas de estrés mecánico, software y electrónico. Después, se prueba la máquina con el material que el cliente va a utilizar fabricando impresiones con probetas de test para evaluar el rendimiento de la impresora y del material.
Fabricamos equipos complejos los cuales son verificados a diferentes escalas a lo largo del proceso de producción.
Y ya para terminar, realizamos la entrega, instalación y puesta en marcha de las impresoras en la sede de nuestros clientes para asegurarnos un correcto funcionamiento. Tras la instalación, siempre realizamos calibraciones de la misma e imprimimos una fabricación de test para comprobar todo el funcionamiento.
De todas formas, a lo largo de los años, se da soporte constante de mantenimiento y ayuda.
Nikon SLM Solutions trabaja con sectores tan diversos como el aeroespacial, automotriz, energético y defensa. ¿Cuál de estos sectores presenta el mayor potencial de crecimiento para la impresión 3D en metal, y por qué?
Hoy en día el sector defensa puede ser el que más potencial tenga por la fabricación aditiva, metal y polimérica, ya que es un sector que desde siempre ha exigido necesidades e innovación. Demanda el uso de la última tecnología, de materiales exóticos, nuevas aplicaciones y componentes con gran respuesta mecánica. Por otro lado, el sector defensa implica desarrollo y rapidez en suministro; desde la fase de prototipado a la de producción. Además, al necesitar series cortas para piezas tan complejas y específicas, la impresión 3D en metal tiene mayor sentido como método de fabricación que otros métodos convencionales.
Este sector defensa al final abarca otros sectores según las diferentes aplicaciones: sector aeroespacial, energético o automoción.
Las principales barreras que limitan el crecimiento de la fabricación aditiva en este sector de defensa son:
1. Regulaciones y Seguridad Nacional
- La fabricación de piezas para defensa está altamente regulada y requiere cumplir con estrictos estándares militares
- La impresión 3D implica riesgos de propiedad intelectual y ciberseguridad, lo que hace que la adopción sea más lenta
- Exportar o compartir diseños impresos puede estar restringido por leyes como el ITAR (International Traffic in Arms Regulations) en EE. UU.
2. Reducido volumen de producción
- A diferencia de la industria aeroespacial comercial, que produce miles de aviones y motores, el sector defensa suele operar con volúmenes más bajos
- La impresión 3D es ideal para prototipos y repuestos, pero el reducido volumen de producción de equipos militares, no siempre justifica su uso en producción masiva.
3. Resistencia a la adopción
- Las fuerzas armadas y contratistas de defensa suelen confiar en procesos tradicionales con materiales probados
- Aunque la impresión 3D puede mejorar el rendimiento de armas, blindajes y vehículos, su adopción depende de largos ciclos de prueba y certificación.
En su intervención destacó la amplia compatibilidad de materiales de sus máquinas. ¿Qué materiales han mostrado ser más exitosos en las aplicaciones de los clientes y cuál es el proceso para añadir nuevos materiales compatibles?
Dependiendo de la industria y su aplicación final, los materiales exitosos son muy diversos.
Titanio (Ti-6Al-4V)
- Industria: aeroespacial, médica, automotriz
- Beneficios: alta relación resistencia-peso, resistencia a la corrosión, biocompatibilidad
- Ejemplo de aplicación: componentes estructurales para aviones y prótesis médicas.
Aleaciones de aluminio (AlSi10Mg, AlSi7Mg, CP1, Scalmalloy o A2024-RAM2C)
- Industria: automotriz, aeroespacial
- Beneficios: ligereza, buena conductividad térmica y mecánica
- Ejemplo de aplicación: partes de motores y chasis para vehículos eléctricos.
Superaleaciones de níquel (Inconel 718, Inconel 625)
- Industria: aeroespacial, energía, defensa
- Beneficios: resistencia a temperaturas extremas, alta durabilidad
- Ejemplo de aplicación: turbinas de aviones y sistemas de generación de energía.
Acero inoxidable (316L, 17-4 PH)
- Industria: energética, médica, industrial
- Beneficios: alta resistencia mecánica y química
- Ejemplo de aplicación: piezas de equipos industriales y dispositivos médicos.
Cobre y aleaciones de cobre (CuCr1Zr, CuNiSiCr)
- Industria: electrónica, automotriz, aeroespacial
- Beneficios: alta conductividad térmica y eléctrica
- Ejemplo de aplicación: intercambiadores de calor y componentes de motores eléctricos.
¿Y en cuanto al proceso para añadir nuevos materiales compatibles?
Nikon SLM trabaja continua y estrechamente con fabricantes pulvimetalúrgicos en la investigación, creación y desarrollo de nuevos materiales metálicos para su uso en fabricación aditiva. Estos nuevos materiales son primeramente demandados por nuestros clientes para sus aplicaciones actuales o futuras y segundamente demandados por nosotros mismos, Nikon SLM, donde evaluamos qué materiales tienen mayor potencial para la industria a nivel general para así empezar a colaborar con los fabricantes de polvos metálicos.
Una vez se tiene fabricado el polvo metálico con propiedades y características adecuadas para su uso en nuestros sistemas SLM, se definen las características y propiedades a conseguir por los componentes fabricados. Después, se lleva a cabo el proceso de desarrollo de los parámetros de impresión de este nuevo material para lograr conseguir estas propiedades y características definidas en la fase anterior. Posteriormente, se define el parámetro y se empieza la certificación estadística, verificando su repetibilidad y estabilidad en la obtención de las propiedades definidas al inicio del proceso. Una vez el parámetro esta validado, se ofrece a nuestros clientes actuales y futuros.
¿Podría citar un caso de éxito?
Sí, el desarrollo del material C-103 en colaboración con Howco Metals Management LLC. El C-103 es una aleación de niobio desarrollada para aplicaciones que requieren alta resistencia térmica y mecánica en entornos extremos. Su composición incluye elementos como hafnio y titanio, lo que le proporciona excelente resistencia a la oxidación y estabilidad estructural a temperaturas superiores a 1.250 °C.
Gracias a estas propiedades, el C-103 se utiliza en sectores como aeroespacial y defensa, especialmente en motores de cohetes, cámaras de combustión y escudos térmicos, donde se requieren materiales ligeros y resistentes al calor. Su capacidad para mantener la integridad estructural bajo temperaturas extremas lo convierte en una opción clave para la fabricación aditiva de componentes avanzados.
Blog: Supersonic Rocket Chamber Manufacturing with Howco Group
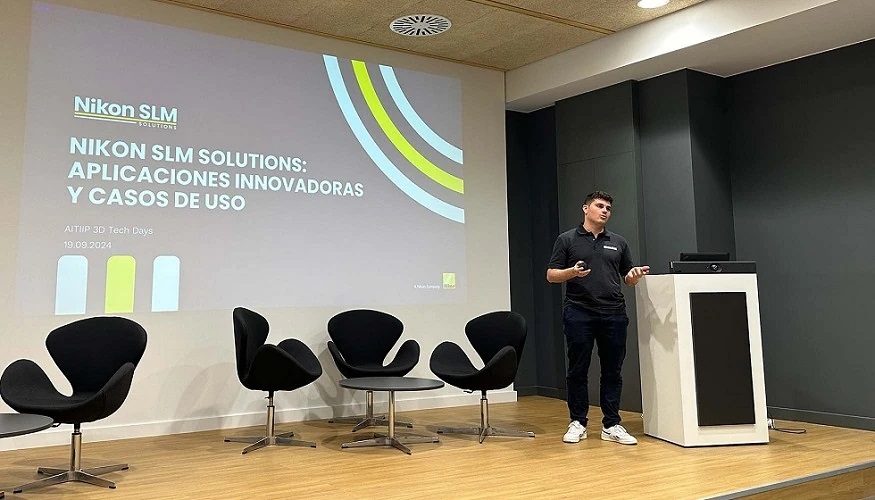
Nikon SLM promueve una arquitectura abierta en sus máquinas. ¿Cómo se traduce esto en ventajas para los usuarios y en qué se diferencia esta filosofía frente a otros fabricantes?
Nikon SLM Solutions adopta una arquitectura abierta, lo que permite a los usuarios elegir materiales de terceros, ajustar parámetros de impresión y utilizar software externo. Esto les brinda mayor flexibilidad, optimización y reducción de costos, en comparación con sistemas cerrados que restringen el acceso a consumibles y configuraciones.
A diferencia de otros fabricantes que limitan materiales y parámetros, Nikon SLM permite personalizar procesos para mejorar la calidad y productividad. Esto es clave para industrias como la aeroespacial y la automotriz, donde la innovación y la eficiencia son esenciales.
Además, esta filosofía fomenta la investigación y el desarrollo de nuevas aleaciones y aplicaciones, facilitando la integración de la impresión 3D en entornos de producción avanzada. La combinación de independencia y control hace que las soluciones de Nikon SLM sean ideales para quienes buscan máxima libertad y rendimiento en manufactura aditiva.
Uno de los casos mencionados fue la producción de una brida para flaps Krueger que implicó una reducción significativa de peso y coste. ¿Qué desafíos técnicos implica la impresión de piezas críticas como esta y cómo los aborda Nikon SLM?
La producción de una brida para flaps Krueger mediante impresión 3D en metal presentó varios desafíos técnicos, ya que es una pieza crítica en la aerodinámica de una aeronave. Entre los principales retos están la resistencia estructural, precisión dimensional y certificación aeroespacial.
El reto de la resistencia estructural se resolvió con el uso de la aleación Ti6Al4V, material avanzado que aporta una gran resistencia mecánica, y mediante la optimización del diseño de la pieza para su reducir peso.
Dado que las piezas aeronáuticas requieren una precisión extrema para encajar en ensamblajes complejos, se realizó un proceso de iteraciones simulando la fabricación de la misma para minimizar las distorsiones de la pieza además de optimizar los parámetros de impresión.
Nikon SLM ofreció un proceso de validación y control de calidad avanzado para garantizar la repetición de las piezas cumpliendo la normativa de aviación.
¿Podría destacar algunos de los proyectos más disruptivos en los que trabaja Nikon SLM para estos sectores? Por ejemplo, ¿qué implicaciones tiene la impresión de componentes para UAVs y chasis de automóviles?
Nikon SLM Solutions está impulsando proyectos disruptivos en sectores como aeroespacial, automotriz y defensa, donde la impresión 3D en metal permite fabricar componentes más ligeros, eficientes y optimizados. En el caso de los UAVs, la tecnología nos permite producir estructuras más livianas y aerodinámicas, mejorando su autonomía y rendimiento sin comprometer la resistencia.
En automoción, estamos trabajando en chasis impresos en 3D y componentes estructurales optimizados para vehículos eléctricos, lo que reduce el peso y mejora la seguridad. Además, en el sector aeroespacial, la fabricación aditiva nos permite producir motores de cohetes y sistemas de propulsión con diseños innovadores, integrando canales de refrigeración internos para mejorar la eficiencia térmica. Estos avances están redefiniendo la manufactura en industrias donde cada gramo y cada milisegundo cuentan.
En el ámbito de la energía, su tecnología ha permitido reducir costes en la producción de piezas para turbinas y válvulas. ¿Cuál es el proceso para lograr estas optimizaciones y cómo contribuyen a la sostenibilidad?
Nuestra tecnología de impresión 3D en metal optimiza la fabricación de componentes para turbinas y válvulas, reduciendo peso, mejorando la eficiencia y disminuyendo costos. Mediante optimización topológica, creamos piezas más ligeras pero igual de resistentes, lo que mejora su rendimiento y prolonga su vida útil.
Además, la impresión 3D permite acortar significativamente los tiempos de suministro de piezas críticas, reduciendo el tiempo de mantenimiento y las paradas anuales en plantas de energía. Esto supone un gran ahorro operativo para el sector, ya que minimiza la inactividad de equipos esenciales.
También contribuye a la sostenibilidad al reducir el desperdicio de material frente a métodos tradicionales y permitir la fabricación bajo demanda y localmente, disminuyendo la huella de carbono asociada al transporte y almacenamiento.
Finalmente, mirando hacia el futuro, ¿qué cree que podemos esperar en la impresión 3D de metales en los próximos cinco años, y cómo se prepara Nikon SLM para estos avances?
En los próximos cinco años, la impresión 3D en metal evolucionará hacia la fabricación de componentes más grandes y la producción masiva en serie de piezas críticas. La demanda en sectores como aeroespacial, automotriz y energía impulsará el desarrollo de sistemas más rápidos, eficientes y capaces de producir a gran escala.
Nikon SLM Solutions se está preparando para este futuro con su tecnología de múltiples láseres, que permite fabricar piezas de gran tamaño con una productividad sin precedentes. Además, estamos enfocados en optimizar la producción en serie, asegurando que la impresión 3D sea una alternativa competitiva frente a la manufactura tradicional.
Una muestra clara de esta visión es la reciente apertura de dos nuevas sedes operacionales de Nikon Advanced Manufacturing, en Long Beach, California, para EE. UU., y en Japón, para todo Asia-Pacífico. Estas expansiones reflejan el compromiso de Nikon con la manufactura aditiva a gran escala.
La combinación de alta velocidad, precisión y escalabilidad marcará la próxima revolución en la impresión 3D de metales, y Nikon SLM Solutions está liderando este cambio con soluciones diseñadas para llevar la fabricación aditiva al siguiente nivel.