Hibridación de procesos aditivos y convencionales para mejorar la productividad en la fabricación de componentes aeronáuticos
Más allá de la implementación de procesos de manera aislada, la hibridación de procesos de fabricación aditiva con procesos de fabricación convencionales es una línea de investigación que debería explorarse en mayor profundidad. Mediante la identificación de sinergias entre distintos procesos de fabricación se podrían explotar las ventajas de la FA, a la vez que se superan las limitaciones de procesos convencionales. Es por esto que, en el presente artículo, se describen, por una parte, las ventajas de los principales procesos de FA metálica. Por otra parte, se analizan una serie de procesos de fabricación convencionales (forja, fundición y mecanizado) y se estudia su compatibilidad con las tecnologías de FA. Por último, se presenta una evaluación crítica de la hibridación de dichos procesos, así como potenciales casos de aplicación.
1. Procesos de fabricación aditiva: L-DED Y L-PBF
La fabricación aditiva se refiere al grupo de procesos que se basa en la generación de piezas añadiendo material sobre un sustrato capa a capa, partiendo de un diseño digital en 3D. Este enfoque permite generar elementos con geometría y dimensiones similares a los de la pieza final, minimizando así el postprocesado necesario y permitiendo un ahorro de material. Además, la FA ofrece la posibilidad de fabricar piezas de mayor complejidad geométrica, al igual que ofrece una gran flexibilidad en cuanto a materiales procesables.
Este trabajo se centra principalmente en la FA metálica. Esta tecnología ha experimentado un desarrollo muy acelerado en los últimos años, gracias a su aplicación en la industria. Dada la gran variedad de materiales y fuentes de energía empleados en FA metálica, procesos muy distintos son englobados dentro de este término. Entre las categorías de FA definidas por la norma UNE-EN ISO/ASTM 52910:2020 [1], para la fabricación de componentes metálicos se emplean los procesos basados en Proyección de Aglutinante o Binder Jetting (BJ), el Laminado de Hojas o Sheet Lamination (SL), la Fusión de Lecho de Polvo o Powder Bed Fusion (PBF) y el Aporte Directo de Energía o Directed Energy Deposition (DED). Sin embargo, este artículo se centra en las dos últimas, ya que son los procesos de FA metálica más extendidos a nivel industrial.
1.1. Fusión de lecho de polvo
La fusión de lecho de polvo o Powder Bed Fusion (PBF) se utiliza en la fabricación de componentes metálicos de tamaño reducido. En este proceso una capa fina de polvo es pre-depositada sobre la plataforma de fabricación, donde una fuente de energía concentrada funde selectivamente el polvo de aquellas regiones que se corresponden con la geometría del diseño digital (Figura 1). Cuando el material fundido se solidifica, el lecho de polvo se recubre nuevamente de material virgen, y mediante la repetición sucesiva de este proceso se fabrica la geometría final.
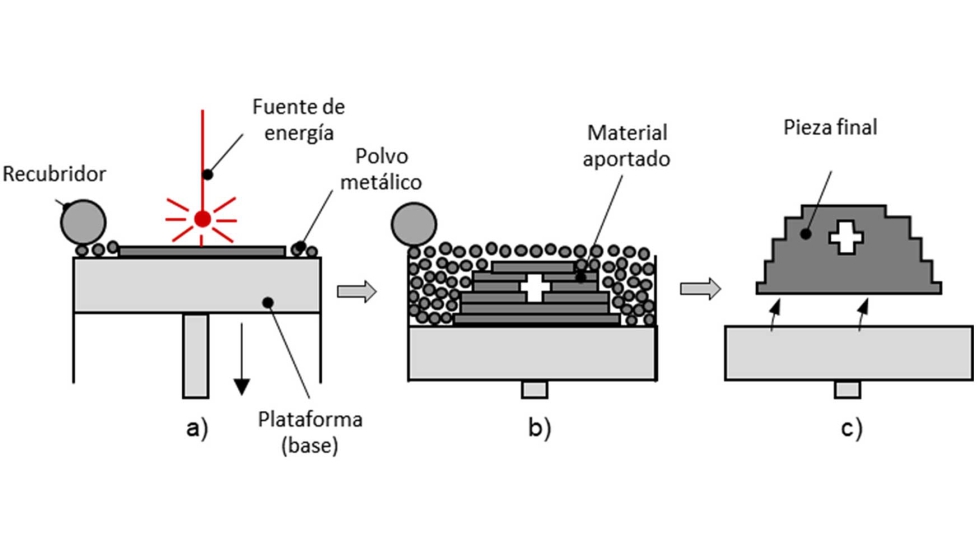
El resultado es una pieza de densidad superior al 99,5%, con buenas tolerancias dimensionales y un acabado superior al resto de tecnologías de FA. Para el caso de emplear una láser como fuente de calor, L-PBF, gracias a su aporte térmico altamente localizado y su relativamente baja afección térmica, permite fabricar piezas de geometrías complejas, paredes muy finas o que integren estructuras de celosía o lattice. Por su parte, la mayor limitación del PBF es que el proceso debe llevarse a cabo en una cámara inerte, lo que limita las dimensiones máximas de las piezas a fabricar.
![Figura 2. imágenes de (a) estructura lattice, y (b) aplicación en carcasa de motor aeroespacial [2] Figura 2. imágenes de (a) estructura lattice, y (b) aplicación en carcasa de motor aeroespacial [2]](https://img.interempresas.net/fotos/3413669.jpeg)
1.2. Aporte directo de energía
El aporte directo de energía o Directed Energy Deposition (DED) se basa en alimentar y fundir el material de aporte directamente en aquellas zonas del sustrato donde se quiere generar la pieza (Figura 2). Las trayectorias que forman cada capa se generan mediante el movimiento relativo del cabezal de aporte (fuente de energía y material a aportar) respecto del sustrato. En este caso, el proceso de fusión también se realiza bajo una atmósfera protegida, que puede ser tanto local como global. Durante el proceso de fabricación, la fuente de energía funde una región del sustrato, creando lo que se conoce como baño fundido o melt pool. El material de aporte es inyectado en el baño fundido, donde se funde y se une al material del sustrato.
La protección local del material aportado evita la oxidación de las piezas sin la necesidad de trabajar en una cámara inerte, lo que facilita el acoplamiento del cabezal de aporte a una máquina cartesiana de 5 ejes o a un brazo robótico. De esta manera, se pueden aportar superficies de mayores dimensiones, lo que posibilita su aplicación a la reparación de troqueles o a la fabricación de piezas complejas de grandes dimensiones, como piezas aeronáuticas.
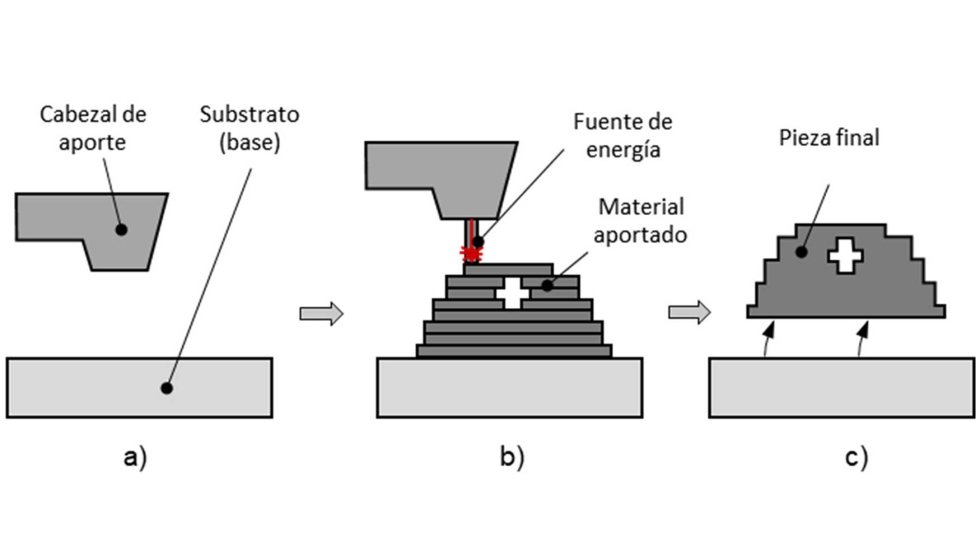
Los procesos que utilizan un láser como fuente de energía se conocen como aporte directo de energía mediante láser, o Laser Directed Energy Deposition (L-DED) en inglés. En estos casos el material puede ser alimentado en forma de polvo o hilo, mientras que los procesos de Fabricación Aditiva por Arco Eléctrico, o Wire Arc Additive Manufacturing (WAAM) se alimentan únicamente por hilo.
En el caso del L-DED, la alimentación de material en forma de polvo ofrece una mayor precisión y flexibilidad al proceso, ya que reduce los problemas de direccionalidad que presenta el hilo. De esta manera, se pueden generar trayectorias más complejas, aumentando así la libertad geométrica. En cambio, la eficiencia de material obtenida en el caso del aporte por polvo es menor que en hilo y, además, muy variable, siendo habituales valores de entre el 30 y 70% de aprovechamiento. Sin embargo, el aporte por hilo goza de una eficiencia másica cercana al 100% y tasas de aporte de material más altas, lo que aumenta la productividad del proceso.
2. Ventajas de la fabricación aditiva frente a procesos tradicionales
El gran interés que ha despertado la fabricación aditiva tanto a nivel industrial como de investigación se debe, indudablemente, a las múltiples ventajas que presenta frente a procesos de fabricación convencionales. Si bien esta tecnología aún está en proceso de maduración, el potencial que ofrece es inmenso, y aún mayor si se combina con otras tecnologías de fabricación. En este apartado se recogen los elementos clave de la FA que, a nivel general, posicionan estos procesos en una posición ventajosa en la industria. Además, se proporciona una visión crítica de cómo pueden ser explotadas por la industria.
En primer lugar, la FA ha supuesto un cambio disruptivo en la forma de entender la relación entre el diseño y la producción. Históricamente, el diseño de componentes ha estado altamente limitado por cadenas de producción poco flexibles. De esta forma, la etapa de diseño y la etapa de producción han sido tratadas de forma independiente. Sin embargo, en los procesos de FA, los rediseños son factibles una vez ha comenzado la producción. Esto se debe a que los procesos de FA no requieren utillajes individualizados. De esta forma, la FA permite una cierta interacción entre etapas de diseño y producción, dotando a la etapa de diseño de un mayor dinamismo y flexibilidad.
En segundo lugar, y ligado con lo anterior, la FA tiene potencial para la individualización de la producción en masa a un precio reducido. De esta forma, se puede obtener una mayor personalización del producto. Esta es una de las características más atractivas para la industria aeronáutica y de automoción. Asimismo, combinando la FA con procesos de fabricación optimizados para la producción en serie, se puede aprovechar aún mejor la posibilidad de customización. Por ejemplo, produciendo preformas básicas mediante técnicas de conformado, y añadiendo detalles individualizados mediante FA.
En tercer lugar, a priori, la FA permite un mejor aprovechamiento del material y una reducción de residuos de producción. Dada la naturaleza aditiva de estos procesos, y en contraposición con los procesos sustractivos, sólo se utiliza el material requerido por el diseño del componente. En el caso de diseños complejos y altamente aligerados, por ejemplo, en aplicaciones aeronáuticas o de automoción, esto supone un ahorro considerable de material. De hecho, se han estudiado varios casos prácticos en los que se ha logrado alcanzar buy-to-fly ratios del 1,2:1, cuando, en casos más extremos, llegan a ser del 10:1 en fabricación convencional. Además de la reducción de costes que esto supone, especialmente cuando los materiales son altamente costosos; en un contexto industrial absolutamente limitado por factores de sostenibilidad, la eficiencia del material supone una gran ventaja.
En cuarto lugar, la implementación de la FA tiene también un efecto favorable en la cadena de suministro. Debido a la descentralización de la producción, la alta automatización del proceso y necesidad reducida de equipos, los componentes pueden ser impresos por suministradores locales. De esta forma, se logra agilizar la cadena de suministro y reducir sustancialmente el plazo de lanzamiento o Time to Market. De hecho, esta característica fue una de las principales motivaciones iniciales para el desarrollo o industrialización de la FA.
Por último, la FA está ligada a una libertad de diseño superior frente a los procesos de fabricación convencionales. Por una parte, hay dos motivos principales detrás de la libertad geométrica de la FA. Primero, el carácter aditivo y la fabricación capa a capa. Segundo, el hecho ser una tecnología que no requiere de utillajes ni herramientas. Entre otras cosas, esta característica permite tanto su aplicación en la reparación de piezas individuales que hayan sufrido defectos durante la producción, como la implementación de herramientas de diseño avanzadas como la optimización topológica. Estas herramientas son cada vez más utilizadas en industrias donde el peso del componente es un factor diferencial. También es posible fabricar diseños que contengan elementos tales como cavidades o sistemas de refrigeración internos en una sola fabricación, sin que esto conlleve un aumento del coste de fabricación. Por otra parte, la FA también cuenta con una libertad mayor en lo que a diseño de materiales se refiere. Mediante la FA se pueden procesar una extensa cantidad de materiales, desde las aleaciones metálicas convencionales hasta polímeros y materiales cerámicos, pero también permite trabajar con materiales avanzados. Por ejemplo, materiales compuestos constituidos por una fase metálica y otra cerámica, aleaciones de alto rendimiento tales como superaleaciones base níquel o cobalto, e incluso aleaciones de alta entropía. Al mismo tiempo, es posible crear piezas con gradientes funcionales basados en una transición gradual de la composición o Functionally Graded Materials (FGM). De esta forma, se pueden diseñar componentes optimizando la composición de los materiales en base a los requerimientos de la aplicación.
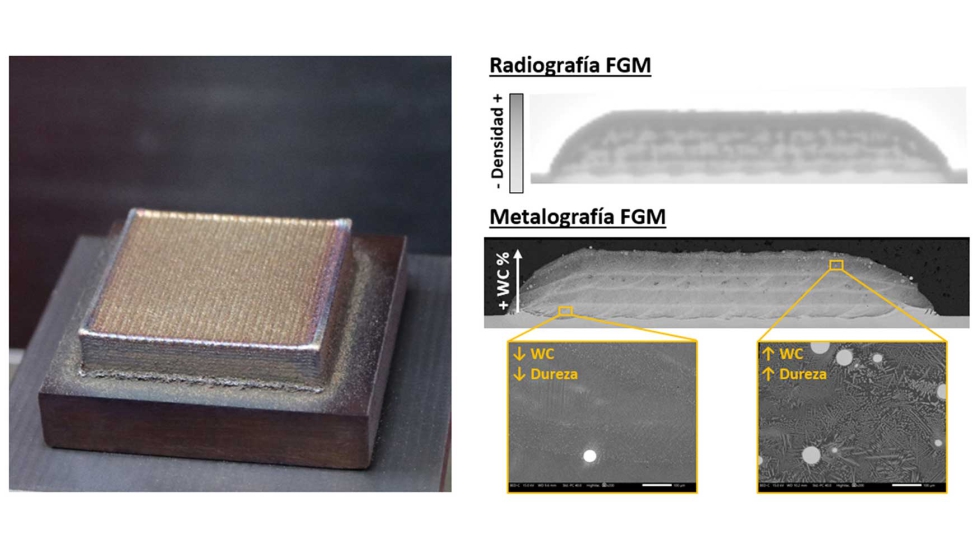
Sin embargo, la FA no está exenta de retos y hay numerosas limitaciones que tienen que ser afrontadas para agilizar su plena implantación en la industria. Por una parte, y debido la baja productividad de estos procesos, el coste por pieza es relativamente alto. Sin embargo, se están realizando avances en este ámbito, y, cada vez son más las compañías que presentan casos de éxito en la seriación de componentes fabricados por FA, en tiradas pequeñas o intermedias. En cuanto a cuestiones de calidad e integridad ser refiere, tolerancias dimensionales y acabado superficial, la FA no está a nivel de los procesos de arranque de viruta. Por tanto, las superficies funcionales deben ser acabadas una vez terminado el proceso de aporte.
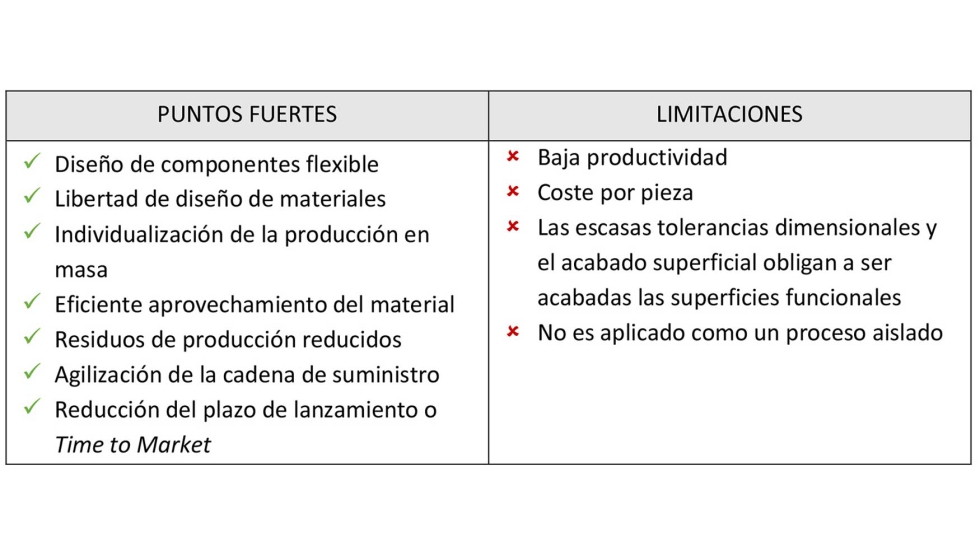
3. Análisis de procesos a hibridar
La hibridación de procesos de fabricación ofrece la posibilidad de combinar los puntos fuertes de distintos procesos, eliminando, a su vez, las limitaciones individuales de cada uno de ellos. Para ello, es preciso identificar sus beneficios e inconvenientes para determinar los procesos con los cuales se podría maximizar el potencial de la hibridación. Se busca combinar aquellos procesos en los que se aproveche al máximo el potencial de cada uno de ellos, mientras que suplan mutuamente sus carencias. Es por esto que, en este apartado, se analizan las ventajas y desventajas de diferentes procesos, en concreto, de los procesos de fundición, forja y mecanizado, con el fin de facilitar la posterior evaluación de la viabilidad de su hibridación con procesos de FA.
Características principales del proceso de fundición
La fundición se engloba dentro de los procesos de conformado por moldeo, por lo que, en primer lugar, requiere de la previa fabricación del molde. La fundición consiste en la fusión de un material metálico y su posterior vertido a través de la cavidad del molde. Una vez solidificado, se extrae del molde y se obtiene el componente con la geometría impuesta por este. Mediante procesos de fundición se pueden obtener piezas de diverso tamaño y con geometrías de alta complejidad. Además, estos procesos son compatibles con la fabricación en serie y, para volúmenes de producción medios o altos, tienen un coste por pieza muy competitivo. Dentro de los procesos de fundición compiten numerosas tecnologías, siendo las propiedades mecánicas y tolerancias dimensionales muy dependientes del proceso específico empleado. Con carácter general, es habitual encontrar defectos metalúrgicos en piezas fabricadas por fundición. En efecto, el agrietamiento debido a fenómenos de dilatación y contracción, la contaminación por arrastre, o la porosidad son limitaciones típicas de este tipo de procesos. Por otra parte, la personalización del diseño no es posible, por lo menos, a bajo coste, dado que está altamente limitada por la geometría de los propios moldes.
Características principales del proceso de forja
La forja, por su parte, se engloba dentro de los procesos de conformado por deformación plástica. Se trata de un proceso de deformación realizado habitualmente en caliente, que consiste en la aplicación de presión a través de unas estampas o de sucesivos impactos a través de un martillo. Al igual que el proceso de fundición, tiene un gran potencial para su utilización en la producción en serie y en lo que respecta al coste unitario por pieza, se considera un proceso económico para la producción de tiradas altas. Sin embargo, cuentan con una libertad geométrica reducida. En lo que a restricciones dimensionales se refiere, es apto para la fabricación de piezas de tamaño diverso, desde pequeño-medio hasta grande (prensa hidráulica). En términos de calidad y propiedades metálicas, se pueden producir componentes con una integridad metalúrgica excepcional, ya que se pueden eliminar los defectos internos del material a través de grandes deformaciones plásticas. De esta forma, se obtienen componentes con propiedades excelentes, aptas para aplicaciones con grandes solicitaciones mecánicas.
Características principales del proceso de mecanizado
Por último, el mecanizado pertenece a la categoría de procesos de arranque de viruta. Este proceso consiste en la obtención de la geometría deseada mediante el arranque de material por medios mecánicos. En cuanto a la precisión, se pueden asegurar tolerancias geométricas y dimensionales muy estrechas. Asimismo, gracias al desarrollo de métodos avanzados para la planificación de trayectorias y la posibilidad de mecanizado con múltiples ejes, posibilita una gran libertad geométrica. En lo que a propiedades mecánicas se refiere, y siempre que se trabaje con parámetros óptimos de proceso y herramientas adecuadas, no tienen por qué afectarse las propiedades del material base. Por tanto, su rendimiento mecánico dependerá de las limitaciones del proceso de fabricación empleado para la producción del material de partida. En lo que a productividad se refiere, no es capaz de competir con los procesos de conformado, si bien, en general, son más competitivos que la FA en ese sentido. Sin embargo, una de las principales limitaciones del mecanizado es la generación de residuos y bajo aprovechamiento del material, debido a su naturaleza sustractiva.
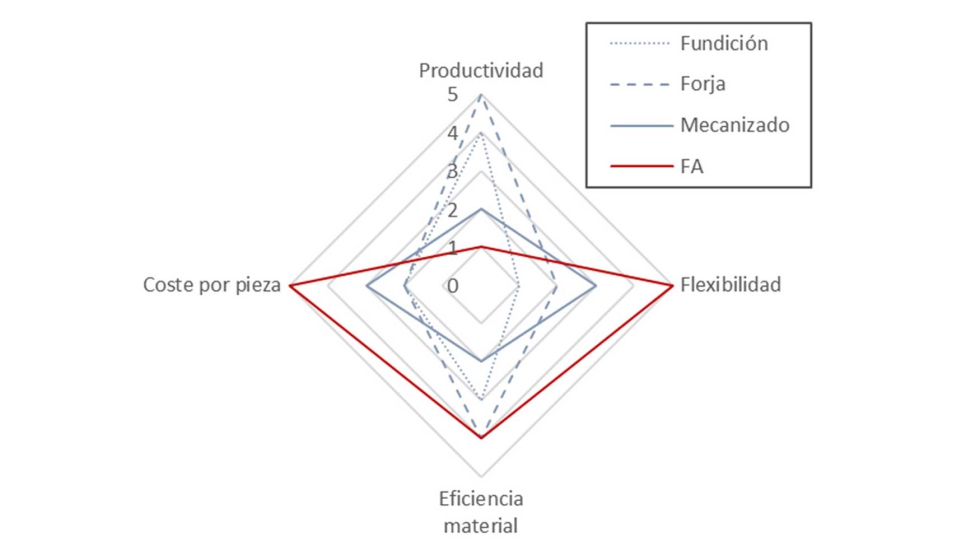
Los procesos de fundición, forja y mecanizado son, indudablemente, más competitivos que la FA mayormente en cuestiones relacionadas con la productividad, coste y, en el caso del mecanizado, en acabado superficial y tolerancias dimensionales (Figura 3). Sin embargo, la evolución de la FA ha dejado en evidencia inconvenientes tales como el aprovechamiento del material, la falta de agilidad y flexibilidad en la cadena de suministro o las limitaciones geométricas de procesos convencionales. Potencialmente, estas limitaciones se podrían eliminar mediante la hibridación de procesos convencionales y aditivos. Dada la alta capacidad de automatización de la FA, existe la posibilidad de incorporar técnicas aditivas a cadenas de producción existentes. Asimismo, la industria podría beneficiarse de las ventajas de la FA y volverse más competitiva, para poder afrontar los retos actuales de una forma eficiente.
4. Análisis de la viabilidad de la hibridación de procesos aditivos y convencionales
Con el fin de facilitar la hibridación de procesos de fabricación, es indispensable llevar a cabo un análisis de compatibilidad de los procesos. Asimismo, se requiere de una evaluación de la viabilidad de las posibles combinaciones, así como un estudio crítico de los potenciales beneficios derivados de ellas. En la siguiente tabla se resumen las principales características de los procesos de fabricación seleccionados para el presente estudio.
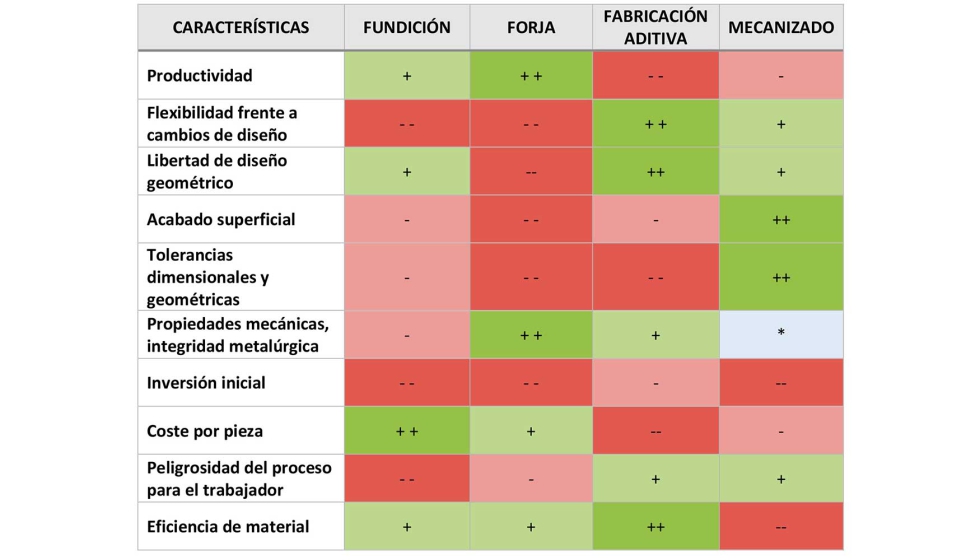
En la tabla se observa que existe una compatibilidad alta entre la fabricación aditiva y el resto de procesos convencionales estudiados. Comparando la FA con el resto de procesos, resulta evidente que hay una correspondencia casi perfecta entre algunos de los puntos fuertes de la FA, como la flexibilidad ante cambios de diseño, libertad de diseño geométrico o la eficiencia del material, y los puntos débiles de otros procesos de fabricación. Inversamente, características como la productividad y el coste por pieza, que se consideran cuestiones limitantes en la FA, son algunos de los puntos más fuertes de los procesos de fundición y forja. Se concluye, por tanto, que mediante la hibridación de procesos de FA con otros procesos de fabricación tradicionales, se podrían complementar las posibles carencias y, simultáneamente, maximizar sus beneficios.
Dada su naturaleza fundamentada en la adición de material, en el contexto de la hibridación con otros procesos, la FA adquiere inevitablemente el rol de añadir elementos de detalle, cuyo diseño, además, podría variar de pieza en pieza. La fabricación de la geometría base o preforma mediante procesos de forja o fundición facilita la producción seriada, y posteriormente esta se podrá personalizar el diseño según los requerimientos específicos de cada aplicación mediante procesos de FA. De esta forma, se fabrica la pieza base de forma productiva y con un coste por pieza bajo; mientras que mediante la FA se adquiere una mayor capacidad de customización individual, aumentando también la flexibilidad ante cambios de diseño. Esto se traduce en un mayor dinamismo de la cadena de suministro, así como una mayor interacción entre las etapas de diseño y producción.
En el caso del mecanizado, la necesidad de hibridación es evidente, dado que las piezas fabricadas mediante FA tienen que ser acabadas. Asimismo, la FA suple la falta de eficiencia de material de los procesos de arranque de viruta. De esta forma, la fabricación de componentes altamente aligerados y con geometrías extremadamente complejas, a menudo, diseñadas a través de la optimización topológica, resulta asequible y/o competitiva.
Teniendo en cuenta todo lo anterior, las combinaciones de hibridación con mayor potencial identificadas son las siguientes:
Forja + DED
Mediante la hibridación de estos procesos, se aprovecha la alta productividad que ofrece el proceso de forja, empleándose la FA para añadir ciertos detalles sobre la pieza final. De esta manera se optimiza el aprovechamiento de material y se confiere una mayor flexibilidad y dinamismo al sistema de producción.
Además de superar las limitaciones naturales de diseño del proceso de forja, las cuales ya han sido mencionadas previamente, la adición de material mediante el aporte directo de energía (DED) permite aumentar el valor añadido de las piezas forjadas (Figura 4). Gracias a la flexibilidad de la fabricación aditiva ante posibles cambios de diseño, será posible modificar la geometría final para ajustarse mejor a los requerimientos de cada aplicación específica.
![Figura 6. Pieza fabricada por hibridación de forja y L-DED, con mecanizado posterior [3] Figura 6. Pieza fabricada por hibridación de forja y L-DED, con mecanizado posterior [3]](https://img.interempresas.net/fotos/3413695.jpeg)
Fundición + FA
En el caso de la fundición, existen múltiples combinaciones posibles, en función del proceso de FA que se esté considerando.
En lo que a hibridación con procesos de fusión en lecho de polvo (PBF) se refiere, se ha estudiado la posibilidad de que elementos previamente fabricados por PBF encajen en el molde de fundición en forma de insertos modulares (Figura 5 a). De esta manera, tras el vertido del material en la cavidad del molde y su posterior solidificación, los elementos fabricados por PBF quedarían embebidos en la pieza. Lo que permitiría obtener una pieza de geometría más compleja y con un mayor valor añadido.
En el caso de hibridación con el proceso de aporte directo de material (DED) la sinergia identificada es similar al caso de forja + FA previamente descrita. Es decir, una vez fabricada la pieza de fundición, se emplearía el DED para añadir elementos de detalle sobre esta (Figura 5 b), dotando al diseño del componente de una mayor libertad geométrica y la posibilidad de fabricar componentes personalizados.
![Figura 7. Piezas fabricadas por hibridación de forja y (a) PBF y (b) L-DED. [4] Figura 7. Piezas fabricadas por hibridación de forja y (a) PBF y (b) L-DED. [4]](https://img.interempresas.net/fotos/3413696.jpeg)
FA + mecanizado
Como ya se ha mencionado anteriormente, todos los procesos de FA necesitan un mecanizado posterior, en mayor o menor medida, para poder lograr las tolerancias dimensionales y los acabados superficiales de la aplicación final. Sin embargo, mediante tecnologías aditivas se pueden fabricar piezas de geometrías muy cercanas a la final, lo cual resulta mucho más eficiente y sostenible que el mecanizado partiendo de un bloque rectangular.
En cada caso concreto, se debe escoger el proceso de FA metálica más adecuado en base a las dimensiones, nivel de detalle y complejidad geométrica de la pieza a fabricar. El aporte directo de energía mediante láser (L-DED) es más adecuado para la fabricación de piezas de tamaño medio (Figura 6 a) y cierto nivel de detalle, debido a la resolución dimensional del mismo, condicionado por la altura de capa y dimensiones de los cordones. Por otro lado, la fabricación aditiva por Arco Eléctrico (WAAM) encaja mejor con la fabricación de piezas de gran tamaño (Figura 6 b), puesto que, en este caso, se alcanzas tasas de aporte de hasta 10 kg/hora.
![Figura 8. Piezas fabricadas por L-DED [5] (a) e WAAM [6] (b), antes de ser mecanizadas Figura 8. Piezas fabricadas por L-DED [5] (a) e WAAM [6] (b), antes de ser mecanizadas](https://img.interempresas.net/fotos/3413697.jpeg)
En el caso concreto de la hibridación de L-DED y mecanizado, se ha de tener en cuenta que, al poder trabajar en 5 ejes en ambos casos, las arquitecturas y cinemáticas de los centros de aporte láser y de mecanizado son muy similares. Esta sinergia facilita la integración de ambos procesos en una sola máquina híbrida, aprovechando mejor el espacio de planta, reduciendo el movimiento del material y permitiendo la generación de geometrías más complejas de las que se obtendrían realizando el aporte y el mecanizado secuencialmente. No obstante, el mercado de máquinas aditivo-sustractivas es muy joven aún y, a pesar de que se han comercializado algunas máquinas hibridas, todavía existen muchos retos que superar para que puedan ser integradas completamente en la industria.
Conclusiones
Tras analizar las posibles compatibilidades entre procesos de fabricación convencionales y procesos de FA metálica, se concluye que, las rutas de fabricación pueden ser optimizadas mediante la hibridación. En concreto, el estudio de viabilidad realizado demuestra que la FA es perfectamente compatible con procesos de forja, fundición o mecanizado. Así, a través de su hibridación, se podría aprovechar las ventajas de la FA, mientras que sus limitaciones se verían compensadas por el empleo de procesos de fabricación convencionales.
Más allá de la sinergia entre procesos de arranque de viruta y FA, la cual queda claramente evidenciada por la amplia oferta de sistemas híbridos por parte de fabricantes de máquina-herramienta, se han identificado posibles combinaciones entre procesos conformado y FA. En el caso de procesos de forja y fundición, por ejemplo, la FA podría emplearse para posibilitar la fabricación de geometrías complejas y la individualización del diseño en tiradas medias-altas. Además, mediante la fabricación seriada de preformas a través de procesos convencionales, se minimizaría el coste por pieza, una de las principales limitaciones de procesos de FA.
Referencias
[1] ‘ISO /ASTM 52910:2020 − Fabricación Aditiva. Diseño. Requisitos, directrices y recomendaciones’
[2] SLM SOLUTIONS, https://www.slm-solutions.com. Disponible en: https://www.slm-solutions.com/fileadmin/Content/Case_Studies/CaseStudy-Monolithic-Thrust-Chamber.pdf
[3] F. Meiners et al., New Hybrid Manufacturing Routes Combining Forging and Additive Manufacturing to Efficiently Produce High Performance Components from Ti-6Al-4V, Procedia Manuf., 2020, Vol. 47, pp. 261-267. (https://doi.org/10.1016/j.promfg.2020.04.215)
[4] Polenz, S., Oettel, M., López, E. et al. Hybrid Process Chain from Die Casting and Additive Manufacturing. Lightweight design worldwide, 2019, Vol. 12, pp. 44–49. https://doi.org/10.1007/s41777-019-0021-8
[5] ARRIZUBIETA, J.I., LAMIKIZ, A., UKAR, E. eta ORTEGA, N. 2019. Laser bidezko prozesu gehigarrietarako hauts-elikagailuen azterketa eta kalibrazioa; Ekaia, 2019, vol. 36, pp. 275-290. (https://doi.org/10.1387/ekaia.20749)
[6] ADDILAN, addimat.es 01 junio 2021. Disponible en: https://www.addimat.es/es/noticias/basque-fondo-de-capital-riesgo-spri-seed-capital-bizkaia-y-tecnalia-entran-en-el-capital-de-addilan.