Con este equipo… sí hay futuro III/IV - Relación de cómo se imprime a como se mecaniza (SLM)
La rigidez de los componentes ha sido tradicionalmente controlada a partir del uso de utillajes convencionales o especiales, fijos o automatizados que permiten disminuir la deformación elástica de los componentes en las zonas de interés para el mecanizado. Adicionalmente muchas investigaciones recientes han mostrado como el control de la rigidez dinámica [1] permite aumentar la confiabilidad y productividad de los procesos de mecanizado.
Todo lo anterior ha permitido que el mecanizado de componentes obtenidos a partir de componentes forjados o fundidos hoy en día tenga niveles de control de la calidad importantes. Sin embargo, los componentes obtenidos a partir de fabricación aditiva como es el caso de los del tipo LPBF, del inglés Laser Powder Bed Fusion, representan retos adicionales dadas sus caracteristicas especiales. Dentro de estas características se destacan las siguientes: la condición de ‘near net shape’, esto es, la similaridad entre la geometría impresa y la fnal; la presencia de paredes delgadas; diseños con topología de forma optimizada, que se representan mediante geometrías de baja masa, con formas esbeltas y complejas, y o formas tubulares y huecas entre muchas otras. Todos estos aspectos sumados al hecho de que los tiempos de fabricación por aditivo aún son elevados en comparación a otros procesos de orden primario hacen que el posprocesamiento por mecanizado de estos componentes incluya retos adicionales al mecanizado de materiales más convencionales.
El uso de utillajes como medida para el aumento de la rigidez en los componentes fabricados por aditivo parecería ser en primera instancia una solución a los problemas previamente mencionados. Sin embargo, la realidad es que el uso de utillajes convencionales en piezas de aditivo es una tarea casi imposible en muchas aplicaciones, lo que conlleva a pensar en el uso de utillajes especiales, diseñados cuidadosamente para cada tipo de componente o fabricación. Esto a pesar de ser una solución viable, constituye sin duda alguna una reducción de flexibilidad del sistema de utillaje, ya que se reduciría a un tipo de fabricación y diseño de pieza muy concreta, lo que hace que el utillaje especial pierda su efectividad si hay pequeños cambios en el diseño de los componentes o de la distribución de los mismos en la placa base. Adicionalmente la instalación de utillajes especiales o convencionales requiere de tiempo considerable que hace que la productividad de la cadena de proceso disminuya considerablemente.
Todos estos aspectos han llevado a que, en el CFAA, Centro de Fabricación Avanzada Aeronáutica, se consideren soluciones alternativas para la mejora del posprocesamiento de componentes de fabricación aditiva por mecanizado. Una de estas iniciativas consiste en la mejora del diseño de la pieza por aditivo desde la concepción del diseño a partir de la predicción de las propiedades mecánicas del material. Una de estas propiedades es el módulo de Young, la cual tiene incidencia directa sobre el aumento de la rigidez [2]. Otra forma es a través de la predicción de la tendencia de los coeficientes de corte [3] en función de las características microestructurales lo que permite estimar la mejor estrategia de mecanizado que se adapte a la reducción del nivel de las fuerzas de corte, de esta manera tanto el aumento de la rigidez del componente como la disminución del coeficiente de corte permitirán un aumento en la estabilidad del proceso y por ende de la calidad superficial de los componentes impresos. En ambos casos se requiere un conocimiento de la interacción entre los parámetros de fabricación laser, la respuesta del material en lo relacionado con su ‘huella’ metalográfica y la relación de los parámetros físicos del material (granos, textura, fases, etc.) con la respuesta plástica y elástica del componente fabricado ante las fuerzas que demanda el mecanizado.
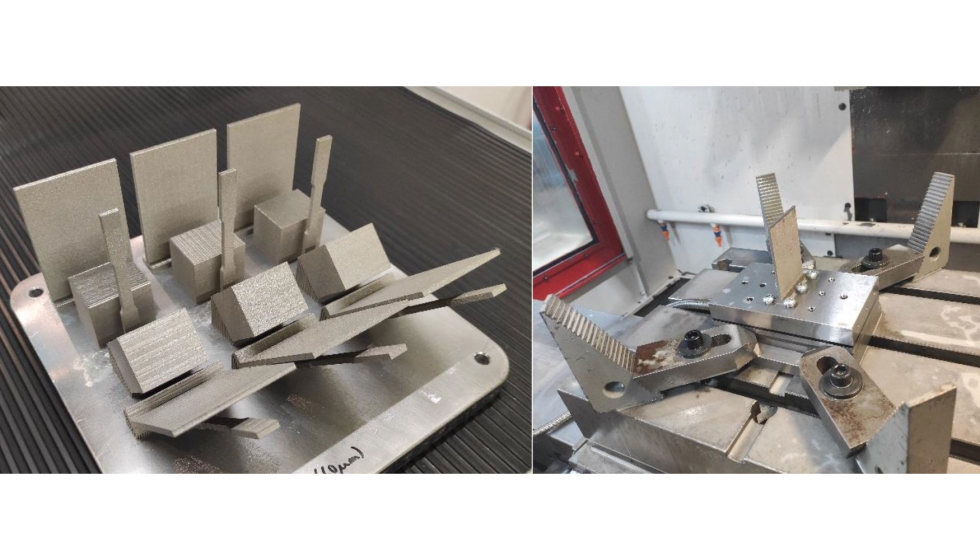
En este sentido el CFAA y la universidad del país vaso UPV/EHU aportan el gran potencial de sus instalaciones en lo relacionado con fabricación aditiva, análisis avanzado de materiales y modelamiento microestructural junto a la amplia experiencia de Ideko en el ámbito del mecanizado y control de las vibraciones durante el mecanizado. Esta sinergia ha permitido obtener componentes con aumento de rigidez en más del 50% solamente a partir del control de las propiedades mecánicas del material, por lo cual la primera fase del proyecto ha mostrado avances significativos en la dirección deseada. Una segunda etapa se encuentra actualmente en evaluación en lo correspondiente a la comparación de los niveles de chatter y estabilidad en diferentes muestras con el fin de analizar las estrategias de fabricación que sean más recomendables para este fin.
José David Pérez es investigador del CFAA en el área de fabricación híbrida (Aditivo + Mecanizado). Es un ingeniero mecánico por la universidad Industrial de Santander (Bucaramanga - Colombia), especialista en electrónica industrial y magister en ingeniería mecánica (Universidad del Norte, Barranquilla - Colombia). Actualmente está becado por el gobierno de Colombia para la realización de su doctorado en ingeniería mecánica en la universidad del País Vasco (Bilbao). Cuenta con más de 10 años de experiencia profesional en diferentes sectores industriales (oil&gas, Fabricación y automotriz) y experiencia docente e investigativa en las áreas de integridad estructural, modelización, simulación, fabricación hibrida, entre otros.
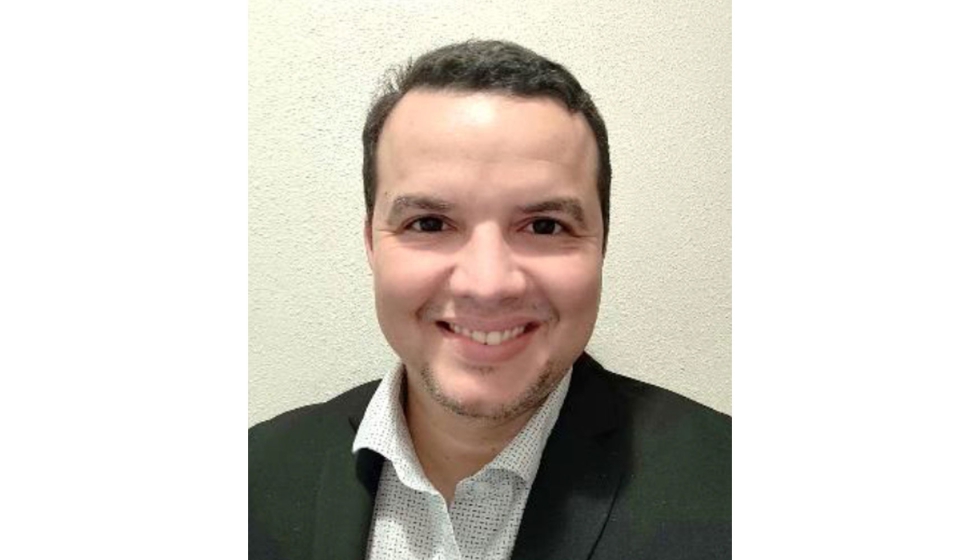
Markel Sanz finalizó el grado de Ingeniería Mecánica en la Universidad del País Vasco (Escuela de Ingeniería de Bilbao) en 2017, recibiendo un premio al mejor expediente académico de su promoción. Continuó sus estudios en la Universidad del País Vasco, obteniendo en 2019 el título de máster en Ingeniería Mecánica. Al mismo tiempo, cursó el título de Especialista en Máquina Herramienta e Industria 4.0 en la Unidad de Máquina Herramienta de la Universidad del País Vasco. Durante los últimos meses de sus estudios, realizó prácticas en el departamento de Dinámica y Control de IDEKO, donde desarrolló su tesis de máster bajo la dirección del doctor Alex Iglesias en torno a dispositivos de acoplamiento modal y fresas de paso irregular para evitar el chatter en el fresado de piezas de pared delgada. Posteriormente, continuó trabajando en IDEKO, iniciando una tesis doctoral sobre técnicas de acoplamiento modal y mecanizado de paredes delgadas bajo la supervisión del doctor Jokin Muñoa.
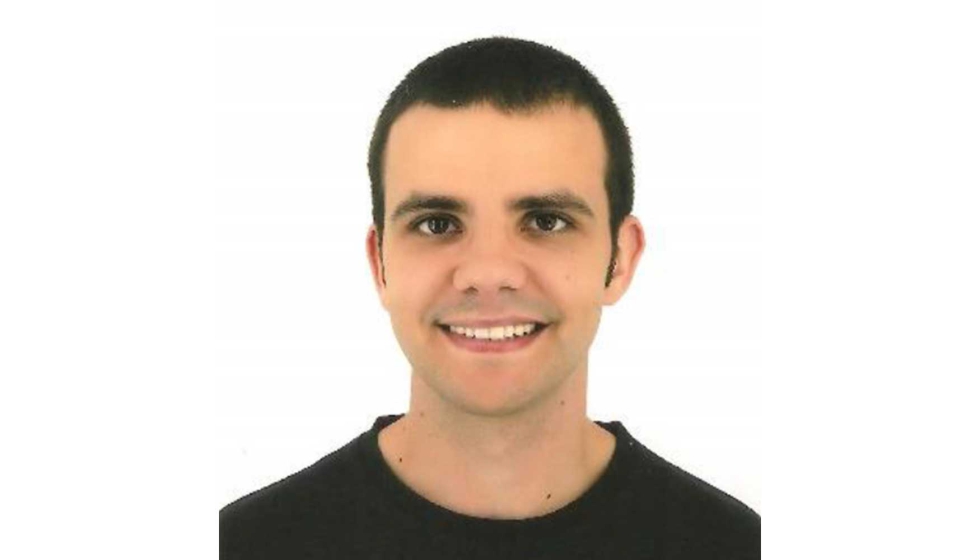
Referencias
[1] J. Munoa, A. Iglesias, A. Olarra, Z. Dombovari, M. Zatarain, G. Stepan, Design of self-tuneable mass damper for modular fixturing systems, CIRP Ann. 65 (2016) 389–392. https://doi.org/10.1016/J.CIRP.2016.04.112.
[2] J.D. Pérez-Ruiz, F. Marin, S. Martínez, A. Lamikiz, G. Urbikain, L.N. López de Lacalle, Stiffening near-net-shape functional parts of Inconel 718 LPBF considering material anisotropy and subsequent machining issues, Mech. Syst. Signal Process. 168 (2022) 108675. https://doi.org/10.1016/J.YMSSP.2021.108675.
[3] J.D. Pérez-Ruiz, L.N.L. de Lacalle, G. Urbikain, O. Pereira, S. Martínez, J. Bris, On the relationship between cutting forces and anisotropy features in the milling of LPBF Inconel 718 for near net shape parts, Int. J. Mach. Tools Manuf. 170 (2021). https://doi.org/10.1016/J.IJMACHTOOLS.2021.103801.